Understanding Welded Machine Tools
Welded machine tools are typically made by joining different metal parts together using a variety of welding methods, including lathes, milling machines, drill presses, and grinders. Welding provides a strong and durable bond between components, ensuring the stability and reliability of the machine during operation.
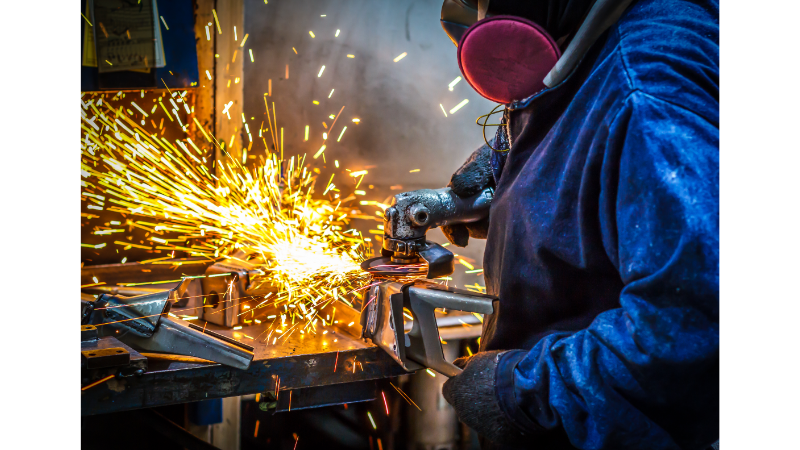
What Is Welded Machine Tool?
Welded machine tools are essential equipment used in various industries to cut, shape, and form metal parts through welding processes. These tools are constructed through welding processes, where metal components are joined together to create a sturdy and functional structure. These machines, such as welding robots, laser cutters, plasma cutters, and CNC machines, play a crucial role in manufacturing processes across sectors like automotive, aerospace, construction, and more.
Common Welding Techniques Used in Machine Tool Fabrication
Several welding techniques are employed in the fabrication of machine tools, each offering unique advantages depending on the application and materials involved. Some common welding techniques used in machine tool manufacturing include:
- Arc Welding: This technique utilizes an electric arc to generate heat, melting the metal components and creating a fusion between them. This technique is commonly used by welders to join and fabricate welded structures. Subtypes of arc welding include shielded metal arc welding (SMAW), gas metal arc welding (GMAW), and flux-cored arc welding (FCAW).
- Gas Welding: Gas welding employs a flame generated by burning a mixture of fuel gas and oxygen to melt the metal components. It is commonly used for non-ferrous materials and offers excellent control over the welding process. Gas welding is a preferred method for welders working on welded structural integrity, as it allows for precise welds. Additionally, gas welding can be used with the online weld technique to create strong and reliable joints.
- Resistance Welding: This technique involves passing an electric current through the metal components to create resistance and generate heat. The heat causes the parts to fuse together, and common forms of resistance welding include spot welding and seam welding.
- Laser Welding: Laser welding utilizes a high-energy laser beam to heat and melt the metal components, creating a strong bond. It is a precise and efficient welding method commonly used for small and delicate machine tool components.
By employing these welding techniques, manufacturers can ensure the reliable and precise fabrication of machine tools, meeting the application and customer requirements of various industries.
The Significance of Quality Control in Welded Machine Tools
By prioritizing quality control in metal fabrication, manufacturers can deliver high-quality welded machine tools that meet industry standards. The welding procedure and welding parameters play a crucial role in ensuring the reliability and performance of these tools in various industrial applications.
Improved Product Reliability
Consistently producing high-quality welded machine tools leads to increased reliability during operation. By implementing effective quality control measures and following the welding standard and welding procedure, manufacturers can ensure that they possess the necessary strength and durability for industrial applications. This among the actual welding typically includes evaluating factors such as fatigue strength to ensure reliable performance over extended periods.
Enhanced Safety Standards
Stringent quality control measures reduce the risk of accidents caused by faulty welds or weak joints. Welded machine tools undergo thorough testing and inspection to ensure their integrity and compliance with safety regulations. By adhering to strict acceptance criteria and quality standards, manufacturers prioritize the safety of both operators and end-users.
Increased Customer Trust
Delivering reliable and defect-free welded machine tools builds trust with customers. When businesses consistently provide high-quality products, customers have confidence in their performance and durability. This trust fosters long-term relationships, repeat purchases, and positive word-of-mouth recommendations.
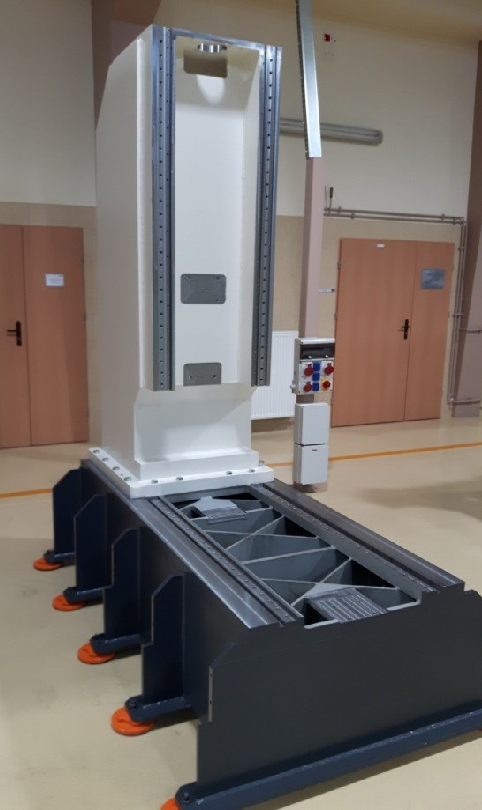
Cost Savings
In addition to enhancing product reliability, manufacturers can avoid unnecessary expenses associated with repairing or replacing faulty equipment. Effective welding quality control minimizes rework, warranty claims, and potential legal liabilities. By conducting rigorous testing and compliance checks during the fabrication process, manufacturers can ensure the high-quality design and steel construction of machine tools.
Adhering to industry standards and regulations for welding quality assurance in steel machine tools is not just a legal requirement but also serves the purpose of maintaining consistency and excellence in delivering products with quality welding at different quality levels.
Key Aspects of Quality Control in Welded Machine Tools
By implementing effective quality control measures throughout the manufacturing procedures, manufacturers can achieve consistent weld quality while meeting industry standards. This involves thorough material inspection, validation of welding procedures, non-destructive testing, and dimensional accuracy checks.
Material Inspection
- Ensure the use of high-quality materials suitable for actual welding processes in the fabrication and production of welded structures, meeting all the necessary requirements.
- Verify that the materials meet the required specifications for strength and integrity.
Welding Procedure Qualification
- Validate welding procedures to achieve desired strength and integrity.
- Follow established welding standards and welding parameters.
- Conduct welder qualification to ensure competency.
Non-Destructive Testing
- Conduct inspections using methods like visual inspection, radiographic testing and ultrasonic testing for welding quality assurance and weld quality assurance. Implement weld quality systems to ensure quality welding.
- Welding inspectors perform a thorough welding machine inspection to detect hidden defects or flaws in welded structures that may compromise their quality and fatigue strength. This inspection involves the measurement of various process parameters to ensure the integrity of the welds.
- Implement quality systems for non-destructive testing.
Dimensional Accuracy Checks
- Ensure the welding quality assurance by conducting a thorough inspection of the welding machine to verify its proper functioning and adherence to quality standards. Additionally, measure the dimensions of welded components to ensure they align with the design specifications.
- Use precision measuring tools to ensure accuracy.
- Implement welding quality control measures at every stage of the welding process.
Welding quality assurance plays a vital role in ensuring the durability and performance of welded structures. It involves adherence to established welding standards, meticulous weld preparation, proper execution of welding procedures, and comprehensive inspection processes.
Challenges and Solutions in Quality Control
In the process of making welding machines under strict quality control, some problems will inevitably be encountered. Common problems and their solutions are discussed below.
Common Challenges Faced in Welded Machine Tools
Ensuring quality control in the manufacturing of welded machine tools can be a complex and demanding task. Some common challenges that manufacturers often face include:
- Welding defects: Welding defects such as porosity, cracks, and incomplete fusion can compromise the integrity of the machine tool. Detecting and addressing these weld defects is crucial to maintaining quality control.
- Dimensional accuracy: Achieving precise dimensional accuracy in welded machine tools can be challenging due to the inherent complexities of the welding process. Variations in heat input, distortion, and shrinkage can affect the final dimensions of the product.
- Material selection: Selecting the appropriate materials for machine tool fabrication is essential to ensure durability and performance. However, identifying the right materials that meet the specific welds can be challenging.
Strategies and Solutions
To overcome the challenges in quality control in welded machine tools, manufacturers can implement various strategies and solutions:
- Robust inspection and testing: Implementing thorough inspection and testing procedures throughout the manufacturing process helps identify and address weld defects. Non-destructive testing techniques such as ultrasonic testing, radiography, and magnetic particle inspection can be used to detect flaws.
- Welding procedure qualification: Establishing and documenting welding procedures that meet industry standards and specifications is crucial. Conducting procedure qualification tests ensures that the welding processes used in machine tool fabrication are reliable and consistent.
- Training and certification: Providing comprehensive training programs for welders and ensuring their certification helps maintain a skilled workforce. Welders who are knowledgeable and experienced in the specific welding techniques used in machine tool fabrication can produce high-quality welds.
- Quality management systems: Implementing robust quality management systems, such as ISO 9001, helps ensure that quality control processes are in place and followed consistently. These systems provide a framework for continuous improvement and adherence to industry standards.
- Collaboration with material suppliers is crucial when selecting the appropriate materials for welding structures. Working closely with reputable suppliers who provide high-quality materials can greatly enhance the overall strength and weld geometry of the final product in machine tool fabrication.
By implementing these strategies and solutions, manufacturers can overcome the challenges in quality control and ensure the production of welded machine tools that meet or exceed customer expectations and industry standards. This will strengthen the system and structures, preventing fatigue.
FAQs
How does quality control impact the performance of welded machine tools?
Quality control plays a vital role in ensuring that welded machine tools perform optimally by minimizing defects and ensuring high levels of reliability.
What are some common challenges faced during quality control in welded machine tools?
Common challenges in welding quality assurance include identifying potential defects early on in the production process, maintaining consistency across multiple units, and meeting strict industry standards. Weld quality systems are essential for achieving weld quality levels.
How can effective quality control benefit manufacturers?
Effective quality control of the welding machine system leads to improved durability of welded structures, reduced downtime due to equipment failures or malfunctions, increased customer satisfaction, and enhanced brand reputation in terms of fatigue.
Conclusion
In order to stay ahead in today’s competitive market, businesses must recognize the value of implementing robust quality control measures for their welded machine tools. Effective quality control brings numerous benefits to both manufacturers and end-users.
It ensures that welded machine tools meet or exceed customer expectations in terms of functionality, safety, and longevity. By understanding the intricacies of welded machine tools and recognizing the significance of quality control, manufacturers can overcome various challenges and implement effective solutions.
Baison, Your Best Choice
If you are looking for the most efficient welding solution for your business, Baison is the best choice for you. Baison’s laser welding machines are designed to provide accurate, high-quality welding results in a fraction of the time required by traditional welding methods.
Check out our range of handheld laser welding machines and laser welding robots to choose the one that best suits your needs. We offer a free evaluation service to ensure you get the most out of our machines.