Welding is vital in the construction, manufacturing, and repair industries.
According to a market research report by MarketsandMarkets, the global welding equipment market size is expected to reach USD 32.5 billion by 2026, with a CAGR of 4.6% during the forecast period.
The report also highlights the increasing demand for portable and efficient welding machines, including hand-held laser welding machines, due to their cost-effectiveness, efficiency, and portability.
This blog post will provide a comprehensive review of the pros and cons of handheld laser welders so that manufacturers can make an informed decision.
What Is a Hand-held Laser Welding Machine?
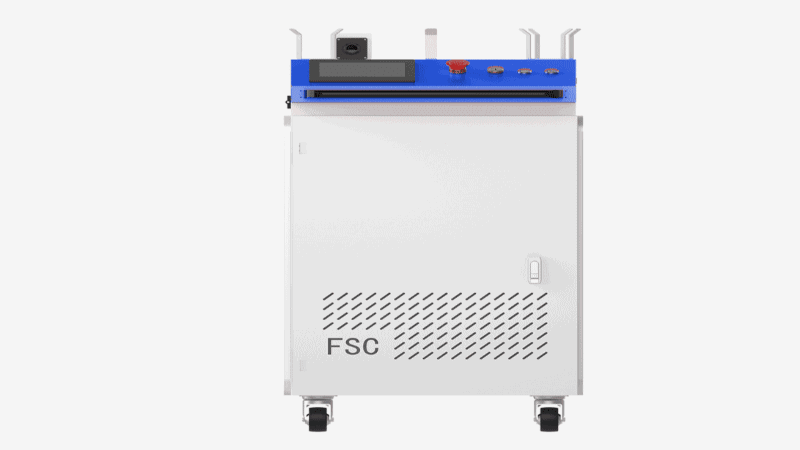
A hand-held laser welding machine is a welding tool that uses a laser beam to join two pieces of metal together. It is a “hand-held” device that can be carried and used in various locations and positions, making it more flexible and versatile than other welding machines.
They can weld various metals, including stainless steel, aluminum, and titanium, and are commonly used in automotive, aerospace, medical device manufacturing, and numerous other manufacturing, fabrication, and repair applications.
Like traditional hand-held welding machines, hand-held laser welding machines are durable, portable, efficient, and versatile, allowing welders to perform welding tasks in hard-to-reach areas or on-site. However, they are generally more expensive than traditional welding machines and require specialized training to operate safely and effectively.
How Does Hand-held Laser Welding Work?
Hand-held laser welding machines use a laser beam to join two pieces of metal together. The process works by directing a high-powered laser beam at the metal to be welded, causing the material to melt and fuse.
Here’s how it works in more detail:
1. Preparation:
The metal pieces to be welded are cleaned and prepared by removing any dirt, debris, or oxidation. The pieces are then positioned and clamped in place.
2. Laser beam generation:
The hand-held laser welding machine generates a laser beam using a high-powered laser diode.
3. Laser beam delivery:
The laser beam is then delivered to the workpiece through a delivery mechanism, usually an optical fiber or optic cable.
4. Focusing the laser beam:
The laser beam is focused by a lens, which concentrates the beam’s energy into a small spot size, typically a few millimeters in diameter. The machine’s ability to precisely control laser parameters minimizes the impact of heat distortion, thus even enabling untrained operators to perform the process.
5. Welding:
The operator uses the hand-held laser welding machine to direct the laser beam at the joint to be welded. The high energy of the beam causes the metal to melt and fuse.
The laser beam moves along the joint and creates a continuous weld. Incorporating the wobble function makes it unnecessary to weave the bead manually during welding, and in numerous scenarios, there is no need for wire feed.
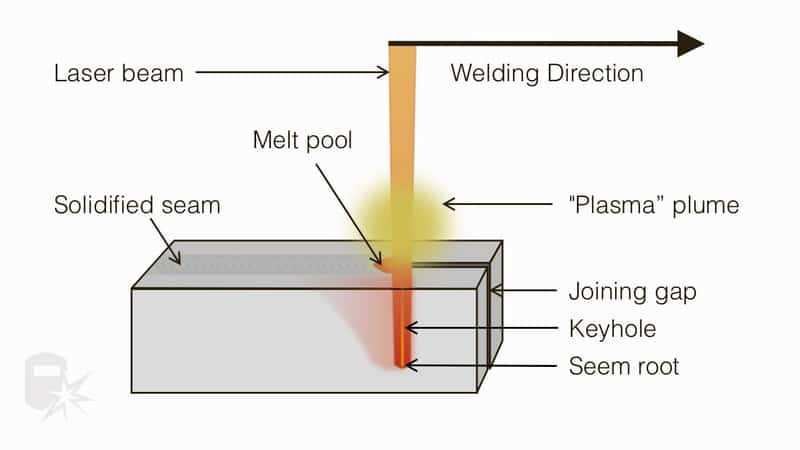
6. Cooling:
Once the welding is complete, the welded area is cooled either naturally or with the help of a cooling system.
The Pros of Hand-held Welding Machines
Hand-held laser welding machines offer several advantages over traditional welding machines, including:
Precision:
They offer high precision and accuracy, allowing small and intricate welds to be created with minimal distortion. This makes them ideal for use in applications where precision is critical, such as in the medical or aerospace industries.
Speed:
Laser welding is generally faster than other types of welding, and hand-held laser welding machines can be used to weld quickly and efficiently. This makes them ideal for production environments, where fast cycle times are essential.
Versatility:
These machines can be used to weld various materials, including metals, composites, and plastics. This makes them versatile tools that can be used in a wide array of applications.
Reduced Heat Input:
Laser welding machines deliver a high-energy beam that produces very little heat, reducing the heat input and minimizing the risk of damage to the welded materials.
Minimal Cleanup:
Hand-held laser welding machines produce minimal spatter, slag, or fumes, reducing the amount of cleanup required after welding.
Flexibility and Mobility:
Hand-held laser welding machines are small, lightweight, highly flexible, and mobile, allowing greater maneuverability and access to tight spaces. This makes them ideal for use in applications where traditional welding machines cannot reach or maneuver, such as in automotive or aerospace manufacturing.
Ease of Use:
Hand-held laser welding machines are relatively easy to operate and do not require extensive training or expertise. This makes them ideal for use in small workshops or by non-specialized personnel, which can further reduce labor costs.
Lower Labor Cost and Space Requirements:
These welding machines require less space than traditional ones, making them a space-saving alternative. Additionally, they are cost-effective; since the operation is effortless and does not require highly skilled personnel, labor costs can be significantly reduced.
Excellent Power Density:
Hand-held laser welding machines offer excellent power density, meaning they can deliver a lot of energy in a small area. This makes them ideal for welding small or delicate parts, where precise control of the heat input is crucial.
The high power density also creates deeper and stronger welds, which is particularly important for welding thick or difficult-to-weld materials.
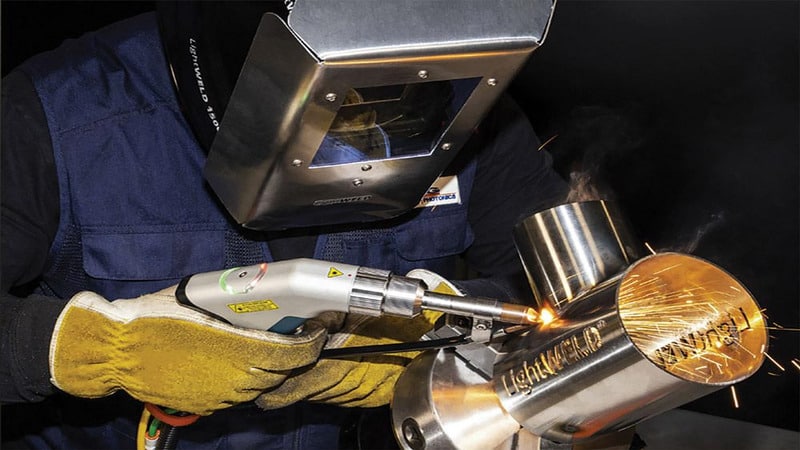
The Cons of Hand-held Welding Machines
While handheld laser welding machines offer many advantages over traditional welding machines, there are also some potential drawbacks to consider, such as:
Cost: Hand-held laser equipment can be expensive to purchase and maintain, especially compared to traditional welding machines.
Safety: Laser welding can be dangerous if proper safety measures are not followed. Exposure to the laser beam can cause eye damage or burns, and appropriate Personal Protective Equipment (PPE) must always be worn. Additionally, there may be a risk of fire or explosion if the materials being welded are not appropriately handled.
Limited Thickness Range: These machines may not be suitable for welding very thick materials, as the laser beam may not penetrate deeply enough to create a strong weld.
Material Limitations: Handheld laser welding machines can weld a wide range of materials, but they may not be suitable for all types. For example, some plastics may not be compatible with laser welding, and certain metals may require specialized techniques or equipment.
Maintenance Requirements: These welding machines may require regular maintenance to maintain their functioning. This can include cleaning the optics, replacing worn parts, and recalibrating the machine. Failure to perform regular maintenance can result in reduced performance or even machine failure.
Limited Power Output: Hand-held laser welding machines typically have a lower power output than traditional welding machines, which can limit their ability to weld thicker materials or larger parts. This can make them more suitable for welding smaller parts or conducting precision welding.
Strict Working Environment Requirements: These hand-held machines require a clean, controlled working environment to ensure optimal performance and safety. This means they are typically used in dedicated welding areas or clean rooms and require a specialized workbench or workstation.
Reduced Durability: Hand-held laser welding machines may have reduced durability compared to traditional welding machines, as they typically feature more delicate components and optics. This can make them more susceptible to damage from impacts or other external factors.
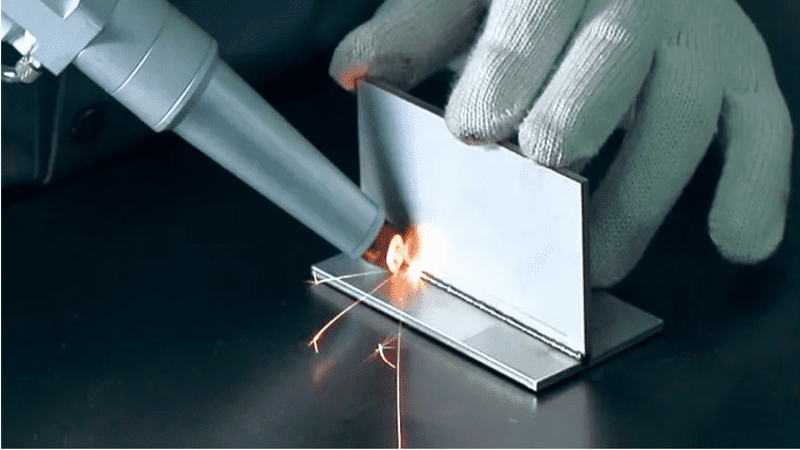
What’s the Difference between Hand-held Welding Machines and Stationary Welding Machines?
The choice between a hand-held laser welding machine and a stationary laser welding machine will depend on the specific needs and applications of the user.
The following table states give a side-by-side comparison to help you make an informed decision:
Features | Hand-held Laser Welding Machines | Stationary Laser Welding Machines |
Mobility | Highly mobile and flexible | Not very portable, fixed in place |
Application | Suitable for small-scale welding and repair jobs | Ideal for mass production, large-scale welding jobs |
Welding speed | Slower than stationary machines | Faster than hand-held machines |
Precision | Requires steady hand and skill | High-precision welding with automated control |
Cost | Lower cost than stationary machines | Higher cost due to automatic control and advanced features |
Maintenance | Low maintenance required | High maintenance required |
Operator safety | It can be more hazardous for operators due to direct exposure to laser beam | Operators are safer as the machine has safety features and automated controls |
Output power | Comparatively lower output power | Comparatively higher output power |
Power supply requirement | Maybe battery-powered | Requires a reliable power source |
Applications | Ideal for welding small and complex parts, repairs, maintenance, and on-site work | Ideal for welding large and complex parts, mass production, high-volume manufacturing, and research applications |
Applications of Hand-held Laser Welding Machines
Handheld laser welding machines are versatile tools commonly used in various industries for welding and repairing small, complex parts. Some typical applications include:
Jewelry Making: These welding machines are commonly used in the jewelry industry to weld and repair delicate jewelry. Laser welding allows for precise control over the welding operation, ensuring that the jewelry is not damaged during welding.
Medical Device Manufacturing: Medical device manufacturers often use hand-held laser welding machines to repair small, intricate medical device parts. The precision of the laser beam allows for high-quality welds that meet the strict standards of the medical industry.
Automotive and Aerospace Industry: hand-held welding machines are also used in the automotive and aerospace industries for welding and repairing small, intricate parts of engines, transmissions, and other mechanical components.
Laser welding can provide high-quality welds with minimal distortion and heat input, making it ideal for welding parts with tight tolerances.
Sanitary Ware Manufacturing: These welding machines commonly produce sanitary ware, such as sinks, faucets, and showerheads. Laser welding allows for precise and clean welds, which is essential in sanitary ware production.
Beer and Beverage Marking: Hand-held laser welding machines are used in the beverage industry for marking and welding beer cans and other beverage containers. Laser marking can provide high-quality markings with excellent contrast and durability, making it ideal for branding and identification.
What Factors should be Considered When Choosing a Hand-held Laser Welding Machine?
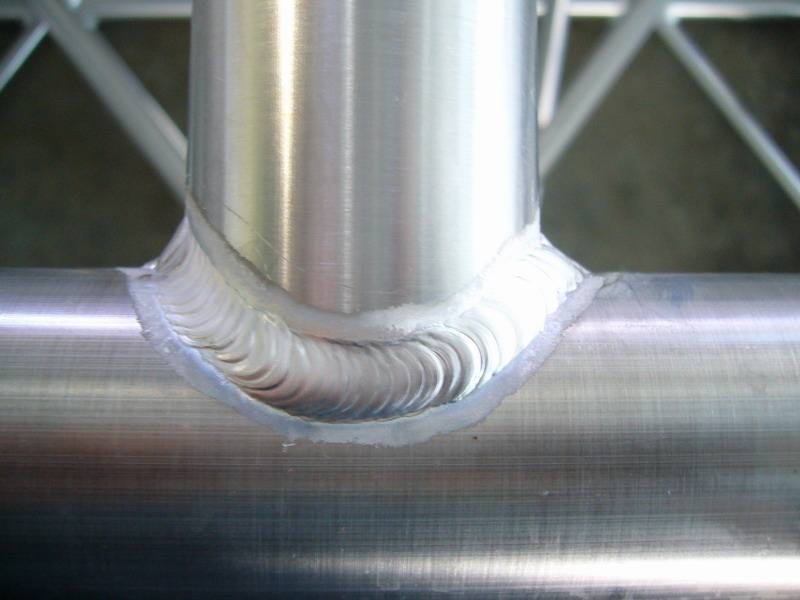
When choosing a handheld laser welder, there are several essential factors to ponder:
Power and Capability: The power and capability of a laser welding machine determine the thickness and type of materials it can weld. Consider the kind of materials you intend to weld and choose a laser welding machine with the appropriate power and capability.
Laser Type and Source: Several types of lasers are used in welding, including pulsed and continuous. Besides, you also need to ponder laser sources, such as CO2, fiber, and Nd: YAG lasers. Each has advantages and disadvantages, and you should choose a laser source and type that best suits your welding needs.
We discussed how to choose a fiber laser welding machine in the previous article. If you are also interested in the differences between CO2 and fiber laser technology, check out our articles on the website.
Portability: Consider the machine’s dimensions, weight, and overall portability, especially if you need to move it frequently or work in different locations.
Ease of Use: A user-friendly interface and easy-to-understand instructions are essential for a hand-held laser welding machine. Consider machines that are easy to set up and use, and have features like presets or automated settings.
Brand, Support, and Service: Choose a laser welding machine from a reputable brand/manufacturer that offers good customer support and service. This is important in case you need technical assistance or repairs.
Safety Features: Laser welding can be dangerous, and it is essential to choose a machine with adequate safety features, such as protective eyewear, shielding, and interlocks.
Duty Cycle: The duty cycle refers to a machine’s continuous operation duration before cooling down. Choose a device with a duty cycle that meets your welding needs and work requirements.
Price: You should choose a machine with the best budget value. Consider the initial cost and any additional costs associated with maintenance, repairs, and replacement parts.
Quality: The quality of the welding machine can impact its durability, reliability, and performance of the device. Choose a machine from a reliable manufacturer made from high-quality materials with a solid construction, good build quality, and in compliance with international safety and quality standards.
Welding Speed: Choose a machine with adequate welding speed to meet your production requirements.
Configuration: The configuration of the welding machine can impact its usability and versatility. You can choose a manual or automatic laser welding machine. You can also choose a machine with a flexible configuration that allows you to adjust settings and parameters to meet your welding needs.
Is Hand-held Laser Welding Machine Right for Me?
Hand-held laser welding machines are generally used for smaller welding applications or when moving a large piece of equipment to the welding site is impractical. They are handy for welding in tight spaces or on irregularly shaped parts, where traditional welding machines would be difficult to use.
A handheld laser welder may be a good choice for small-scale welding needs. They are beneficial for welding thin materials such as sheet metal or tubing.
Additionally, hand-held laser welding machines are typically more precise and produce less heat distortion than traditional techniques, such as stick welding and arc welding, which can benefit some industrial applications.
Hand-held laser welding machines require a certain level of skill and training to operate, so you should consider whether you or someone on your team has the necessary expertise to use this equipment effectively.
Finally, considering whether a hand-held laser welding machine is the right choice, you should consider cost, maintenance requirements, and after-sales support.
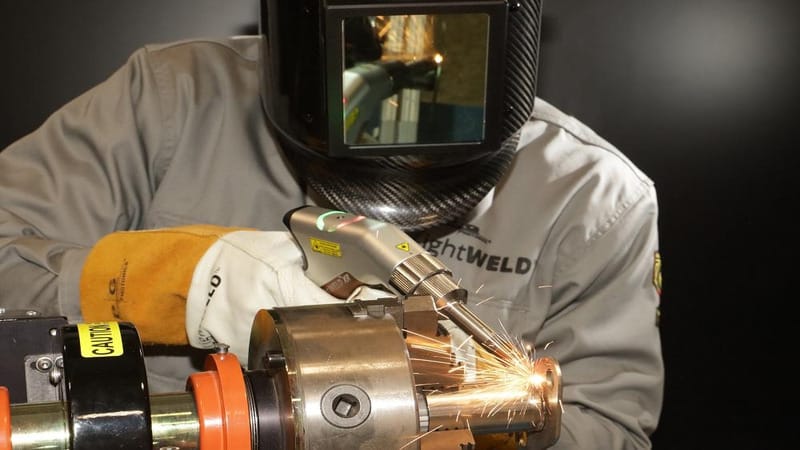
How to Maintain and Repair Hand-held Welding Machines?
Handheld laser welders require regular maintenance to ensure they function at their best and have a long lifespan.
Maintenance Procedures:
Keep the machine clean: Regularly clean the machine’s exterior and interior components using a soft cloth and a mild cleaner. Be careful not to scratch or damage any delicate parts. Don’t use water, any corrosive liquid, or pressurized air to clean the machine’s gun head.
Check the water cooling system: Make sure the water cooling system is functioning correctly and there are no leaks or blockages in the water lines. Changing the water in the cooling system every six months is recommended to ensure it is clean and contaminant-free.
Check the gas flow: Ensure that the gas flow of the protective gas system (shielding gas system) is steady and there are no leaks in the gas lines. Replace the gas filter every six months to prevent debris from clogging the gas lines.
Inspect the optics: Check the laser beam path and optics for dust, debris, or scratches. Clean the optics with a soft cloth and a cleaning solution designed for the machine. While replacing the optics, keep the environment clean, turn off A/C and fans, and seal the opening of the gun’s body with tape to prevent any dirt from entering.
Lubricate moving parts: Apply a small amount of lubricant to the machine’s moving parts to prevent them from rusting or seizing.
Common problems and solutions:
Loss of power: If your machine is losing power, check the power supply and make sure the machine receives the correct voltage. The problem may be with the laser diode or power supply module if the power supply is working correctly. Contact a professional for repair.
Overheating: If the machine is overheating, check the water cooling system and make sure the water flow is adequate. If the cooling system is functioning correctly, the problem may be with the power supply or laser diode. Contact a professional for repair.
Laser beam misalignment: If the laser beam is not correctly aligned, check the optics and ensure they are clean and debris-free. If the optics are clean, the problem may be with the laser diode or beam expander. Contact a professional for repair.
No output or weak output: If the machine is not producing any output or the output is weak, check the gas flow and make sure the gas lines are not clogged or leaking. If the gas flow is right, the problem may be with the laser diode or power supply module. Contact a professional for repair.
What Should You Pay Attention to When Using Hand-held Laser Welding Machines?
When using handheld laser welders, there are several essential factors to pay attention to ensure safe and efficient operation:
Eye protection: The laser beam emitted from the welding machine can cause severe damage to the eyes. Always wear appropriate eye protection, such as laser safety goggles or a welding helmet with a proper filter lens.
Ventilation: Laser welding produces smoke and fumes, which can be harmful if inhaled. Ensure proper ventilation in the work area, such as using an exhaust fan or working in a well-ventilated room.
Positioning: Proper positioning of the workpiece and the welding machine is critical to achieving a successful weld. Ensure the workpiece is aligned correctly and supported and the welding machine is held at the correct distance and angle.
Power supply: Use the correct power supply for the machine and ensure it is properly grounded. Avoid using extension cords or power strips; always follow the manufacturer’s instructions.
Materials: Laser welding suits many materials, but certain materials may require special attention. For example, highly reflective or conductive materials may require a different laser or welding technique.
Maintenance: Regular maintenance and inspection of the machine are crucial to ensuring its optimal performance and longevity. You must follow the manufacturer’s recommendations and maintenance schedule and address any issues immediately.
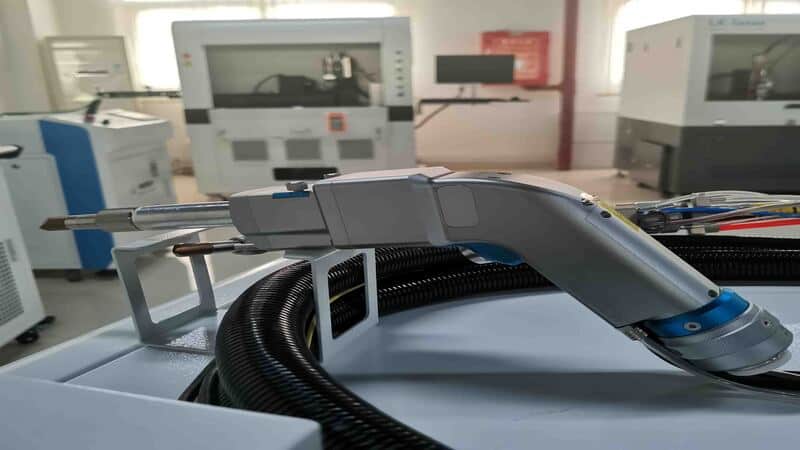
Sustainability and Environmental Impact of Hand-held Laser Welding Machines
Hand-held laser welding machines have several advantages regarding sustainability and environmental impact compared to traditional welding methods. Here are some of the reasons why:
Reduced Material Consumption: Laser welding requires less filler than other methods, such as MIG welding or TIG welding processes. This means less waste and reduced consumption of materials, making it a more sustainable option.
Energy Efficiency: Laser welding machines use less energy than traditional welding machines, such as MIG welders. The laser beam provides a concentrated source of energy that requires less electricity to produce, which results in lower energy consumption and lower CO2 emissions.
Reduced Emissions: Hand-held laser welding machines produce fewer emissions than traditional welding methods. This is because they use a smaller heat-affected zone, which means less material is burned off and less harmful fumes are produced.
Improved Precision: Hand-held laser welding machines offer precise control over the weld, wasting less material and reducing energy consumption. This precision also allows for better weld quality, reducing the need for repairs or rework and reducing waste.
Longer Machine Life: Hand-held laser welding machines have a longer lifespan than traditional welding machines. This is because they require less maintenance and have fewer parts that can wear out. This means fewer machines need to be manufactured and disposed of, reducing the overall environmental impact of the equipment.
In conclusion
Hand-held laser welding machines offer many benefits over traditional welding machines, including increased precision, speed, and flexibility. They are also easier to use and require less space and labor than conventional welding machines.
Ultimately, investing in a hand-held laser welding machine will depend on the application’s specific requirements and the available budget and resources.
If you want to learn more about hand-held laser welding machines and how they can benefit your business, we encourage you to request a quote from Baison Laser. Our team of experts can provide guidance and support to help you find the right solution for your welding needs.