Dross is an inevitable and often unsightly by-product of laser cutting. It can cause many problems – from decreased accuracy and efficiency to dangerous fires. In this blog post, we’ll discuss the causes and prevention of dross in laser cutting. Stay safe and produce top-quality products with our tips!
What Is Dross in Laser Cutting?
Dross is the undesirable build-up of waste material generated from molten material. This waste material gets developed as a byproduct of the cutting process. Dross’s production is influenced by various factors, including torch speed, distance, voltage, and other factors.
The presence of dross during the laser cutting process always reduces the cut’s precision and leaves the material unpolished. Many firms spend time and money polishing items cut with the plasma laser machine, which generates significant dross. This procedure requires considerable time and effort, reducing your business’s efficiency.
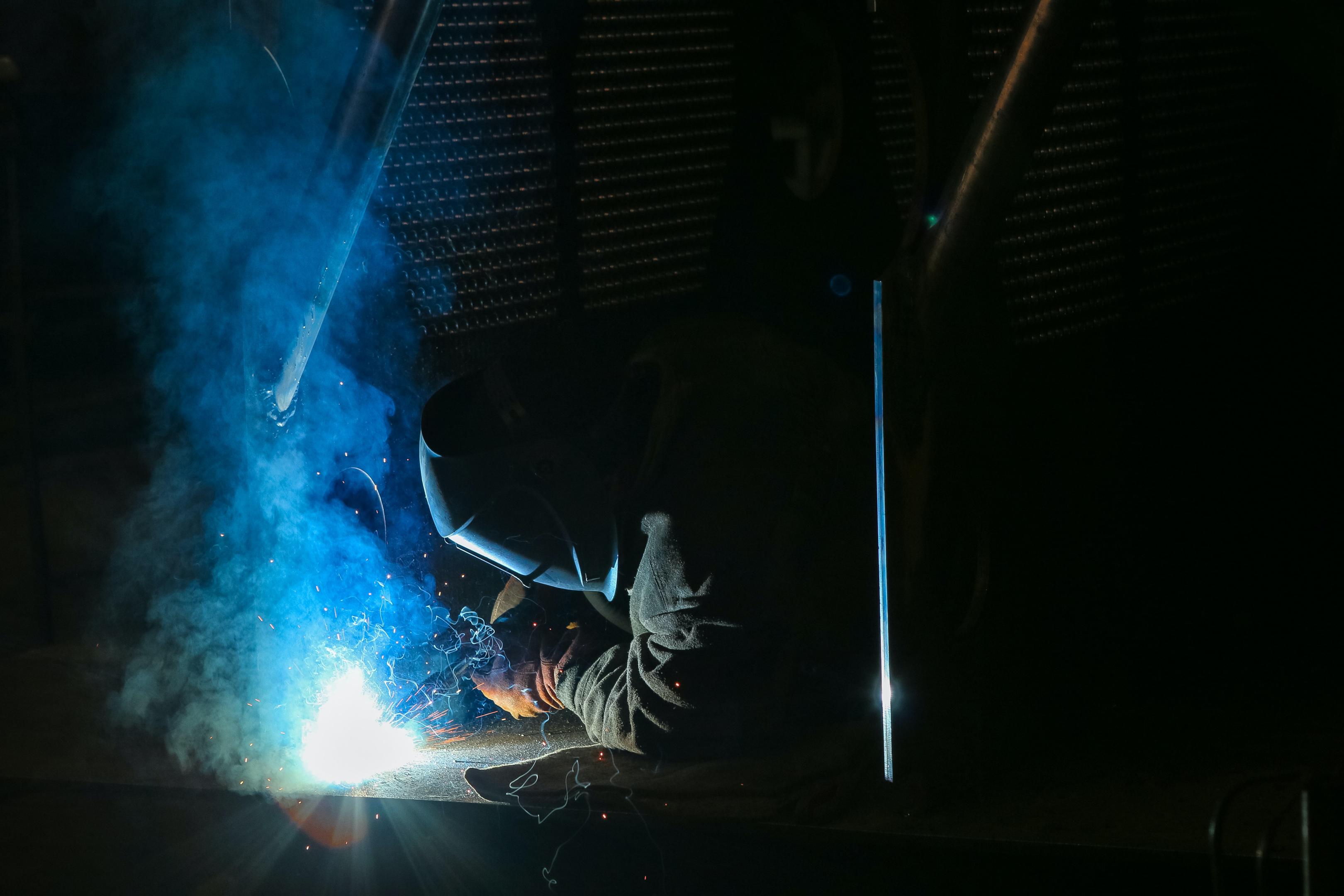
What Are the Effects of Dross on Laser Cutting Performances?
Dross can significantly affect your laser machine’s performance resulting in a loss of precision and accuracy, which reduces the machine’s efficiency. These issues can result in rough edges, striations, and an accumulation of unwanted materials on the laser, reducing the cutting efficiency.
There are many other problems, such as low-speed Dross, high-speed Dross, and top spatter dross, all of which can cause the performance of your laser-cutting machine to suffer. There are also a few effects that dross has on the machine, such as cut angularity, incomplete cuts, and difficulties with hole quality.

Main Causes of Dross Formation
Several factors might play a role in determining the amount of dross formed, a few of which were covered in earlier discussions.
The cutting parameters at stake here include but are not limited to, speed, standoff distance, voltage, thickness, and temperature. However, low-speed Dross, high-speed Dross, and top scatter Dross are the three primary causes that are most prominent overall.
1. High-speed Dross
When cutting the material, if your speed is too high, the arc will start to trail behind in the kerf, leaving uncut material on the bottom of the plate. The dross will start accumulating unwanted waste by proceeding in this manner, resulting in poor performance.
2. Low-Speed Dross
When cutting material, if the pace you are cutting at is low, the cutter will search for additional material to cut. The diameter of the arc continues to expand, which results in the broader kerf at the point when the high-velocity component of the plasma no longer disperses molten metal. Therefore, this molten material accumulates around the plate’s base.
3. Top Spatter Dross
This dross gets created when resolidified metals leave deposits on the surface, later showered with pieces cut from the metal. Most of the time, this is due to two factors: the speed is too high, or the nozzle does not have sufficient pressure. In contrast to the other two, getting rid of this dross requires very little work and can be done by anybody.
How to Prevent Dross Formation?
There are a variety of strategies that are used to prevent dross from accumulating in the laser-cutting machine. It is not always possible to utilize all of these strategies; for this reason, we will cover the seven best preventative measures that could assist.
1. Dross Inhibitors
Use a wide range of dross inhibitors that can be applied to the surface to stop the accumulation of other materials. However, you must ensure a solid understanding of the mechanism since a few steps must be carefully done to avoid harming the machine.
2. Nitrogen Blanket
Utilizing a nitrogen blanket is yet another method that could be employed to prevent the formation of dross. Nitrogen is employed as a blanket in this process, which protects the solder produced by the wave generator. Through the use of this procedure, the amount of dross added to the solder pot gets minimized.
3. Oil Coating
Eliminating interaction with air is the simplest method available for preventing dross. You could use the nitrogen approach, but it may be a bit pricey. Alternatively, you could try applying an oil coating to coat the uncovered solder, which works as a barrier in the production of dross.
4. High-pressure Gas
If you are working with a very high-powered laser beam, using a high-pressure nitrogen assist gas or high-purity nitrogen gas can help prevent dross. This method of high-cutting speed and high assist gas pressure can effectively cut through materials while simultaneously avoiding the production of dross.
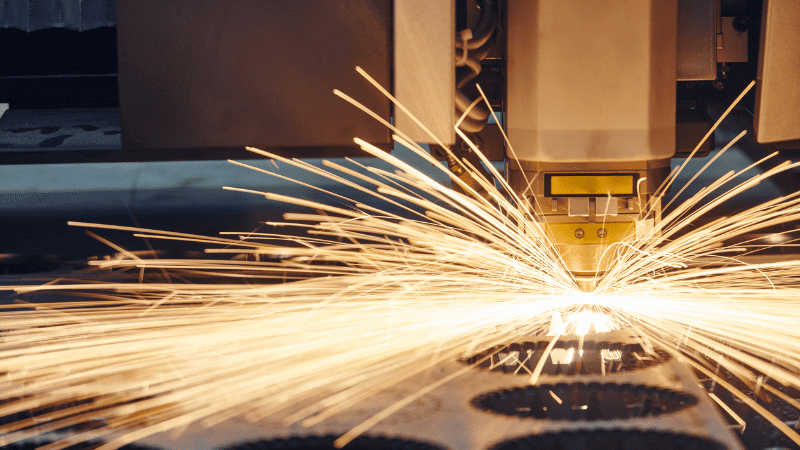
5. Material Composition
When it relates to determining the formation of dross, the material you use plays a vital function. Low-grade steel often contains impurities that are highly reactive during the heating process. During this stage, several heat reactions take place, which may affect the dross.
Moreover, the dross will get blown away if the material’s low viscosity. However, if the viscosity is high, the dross will cling to the material and need further cleaning. Remember that certain material thicknesses and viscosities have their advantages.
6. Laser Speed Management
Speed management is of the utmost importance when working with a laser cutter. Your cutter’s speed can lead the plasma arc to extend, resulting in dross formation. Therefore, it is best to use the laser technology at a speed that is neither too high nor too low. A wide variety of speed control tools comes with purchasing plasma lasers and fiber laser cutting.
7. Check the Laser Nozzle
When cutting through any material, the function of the nozzle is of the utmost significance. The quality of the nozzle has a substantial effect on the form of the arc produced.
If you use a nozzle worn out or defective, the plasma arc will become unpredictable, resulting in the production of cuts of poorer quality. As a result, changing out the nozzle of the laser machine is the most effective strategy for getting rid of dross within the machine.

Methods for Removing Dross from Laser-Cut Parts
It can be highly time-consuming to wash away the accumulated dross from the laser-cut parts. They tend to be sticky and prefer to remain in the area if the appropriate approach is not applied. Therefore, to overcome this problem, let’s look at some of the most prevalent methods for cleaning dross from laser-cut components.
1. Anti-Spatter Spray
This approach is likely the least costly of the available options. Make use of an anti-spatter spray that prevents spattering and simple to apply, is non-toxic, and does not cause the material to deteriorate. This procedure helps prevent the dross from clinging to the plate, making it simpler and quicker to clean. In addition, since it does not include any potentially harmful components, it is suitable for use in almost any environment.
2. Keep It Cool
Once the object has cooled down to the point where you can handle it safely, you should eliminate dross or get the dross removed completely.
In most cases, dross cools extremely fast and becomes quite simple to scrape away once it has solidified. We strongly suggest you only clean your dross after it has cooled down to avoid sustaining any form of injury and to complete the process as effectively as possible. The cooling method of the laser cutting machine is here.
3. Sanding System
Sandpaper is often used as the technique of choice when clearing dross from a laser machine. The dross will usually come off in readily removable chunks when using sandpaper. It is quick, and minimal effort is required to finish it. However, because they leave scratches on the sanded material, they are inappropriate to use with polished surfaces.
Tips for Improving the Quality of Laser-Cut Parts
Several elements might influence the quality of laser-cut parts. You must possess knowledge about these factors to make the quality better. Therefore, let’s look at the three most important factors to increase the quality of your laser-cut items.
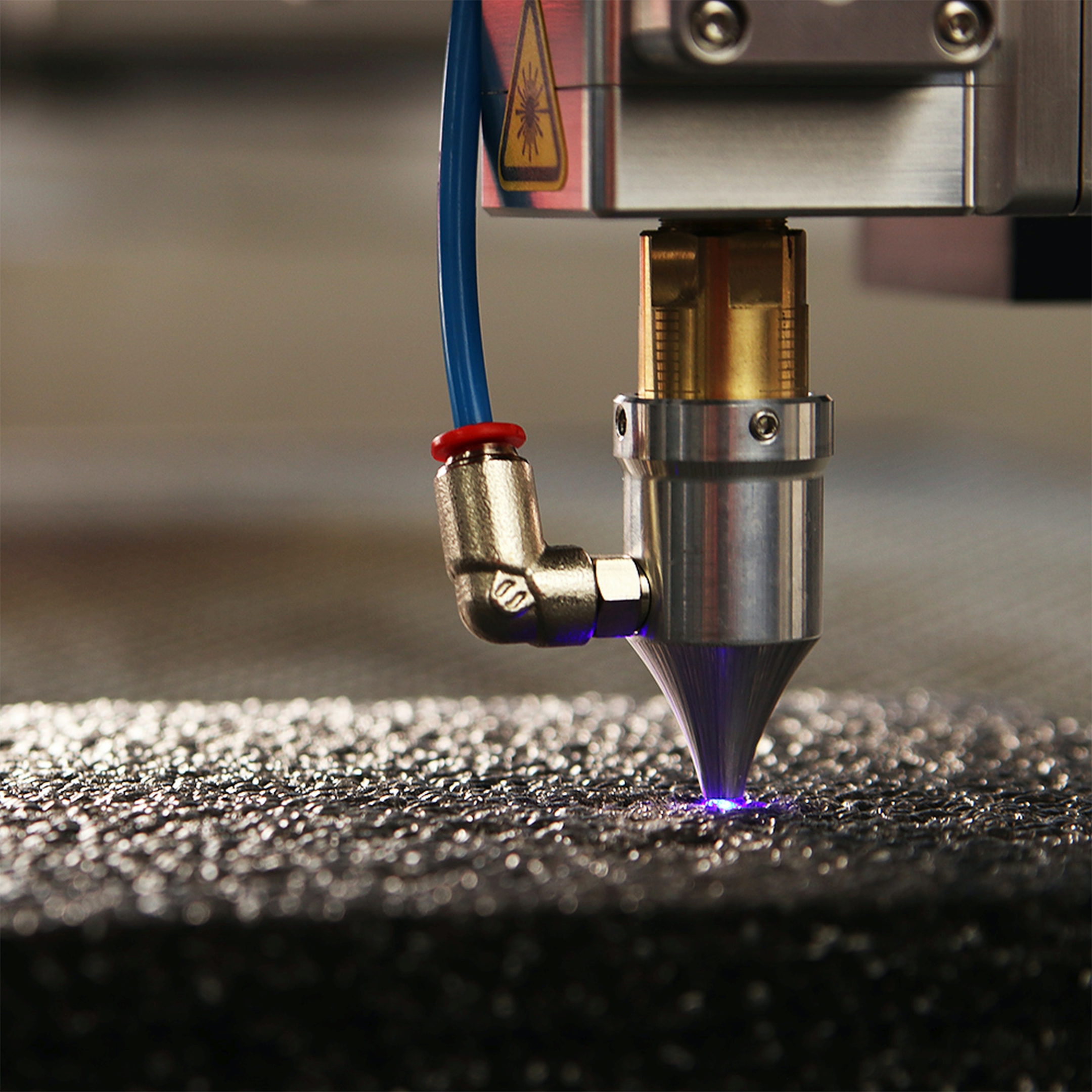
- Material Thickness: The thickness of the material also significantly impacts the quality of a laser cut. Thicker material will result in more striations on the material’s cut edge when cut. Therefore, try using thin materials to improve the quality.
- Material Quality: Keep in mind that the material’s surface finish could significantly impact the cut quality. For improved quality, we strongly advise utilizing clean, rust-free, and oil-free materials. Also, make sure to avoid low-grade materials.
- Laser Power: One can avoid problems such as striation and dross by utilizing a laser with extremely high power. Many different laser cutters, such as plasma and fiber lasers, are very effective. However, purchase the most high-powered laser regardless of its type.

Conclusion
Using these strategies to prevent dross may appear complicated, but once you get acquainted, they are straightforward to manage and operate. By following the tips and techniques outlined in this blog post and maintaining a clean and well-maintained laser cutting machine, you can significantly reduce the formation of dross and its negative impact on your workpiece.
If you still find these procedures confusing, don’t hesitate to contact us for assistance.
Achieve Flawless Cuts with Baison Laser!
Is dross giving you a headache? At Baison Laser, we’re not just about selling equipment; we’re about ensuring you get perfect, dross-free cuts every time. Partner with us for expert advice and top-tier laser cutting solutions. What are you waiting for? Click the link here to contact us now!