The same is the case with the use of pipe-cutting machines in the manufacturing process.
This blog will explain how a pipe-cutting machine can save time, reduce manufacturing companies’ costs, and make the process less time-consuming.
What Is a Pipe-Cutting Machine?
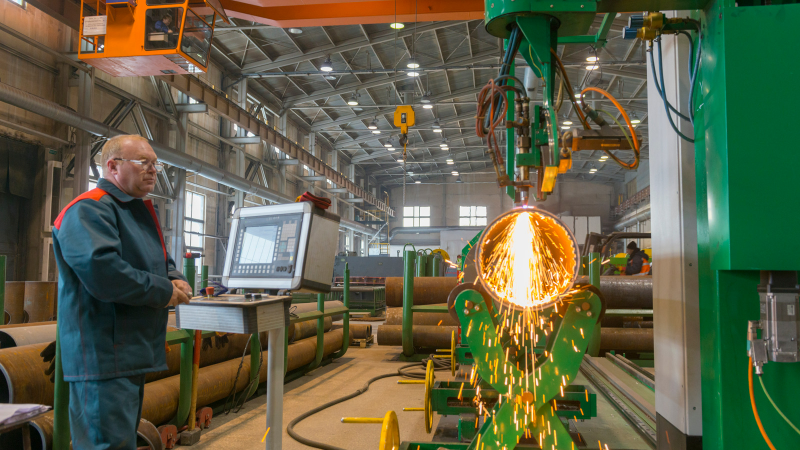
A pipe-cutting machine makes accurate and precise cuts and holes in pipes. The efficiency of the pipe-cutting machine depends upon the material of the pipe being cut. Consider, for example, a steel pipe and a copper pipe. The steel pipe will require a more precise cut than the copper pipe.
What Are the Advantages of a Pipe-Cutting Machine?
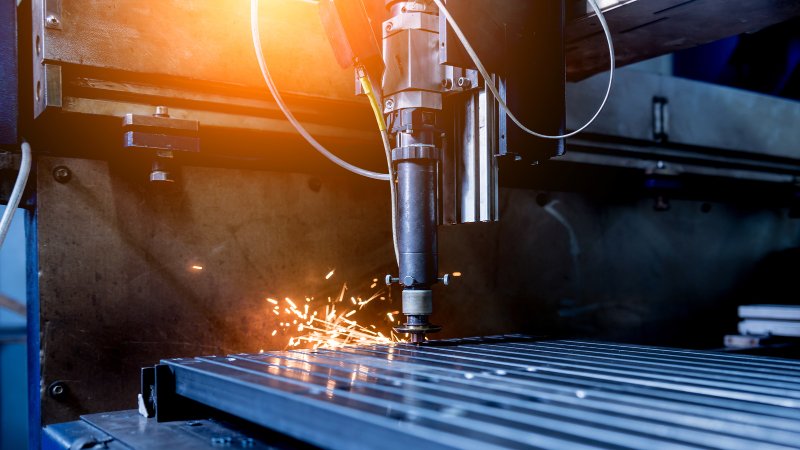
- A pipe-cutting machine has the ability to cut a variety of materials. Be it carbon, steel, or stainless steel, it can cut it all.
- A significant advantage is that it is less time-consuming. It takes just a few seconds to cut a pipe.
- This machine can cut pipes of any precision or diameter.
- Because of its high-speed piercing capability, it ensures accuracy in its functions.
- A major advantage of a pipe-cutting machine is that it does not produce hazardous waste. This makes the machine more environmentally friendly.
- It reduces overhead costs by being energy efficient.
What is Waste in Manufacturing Terms?
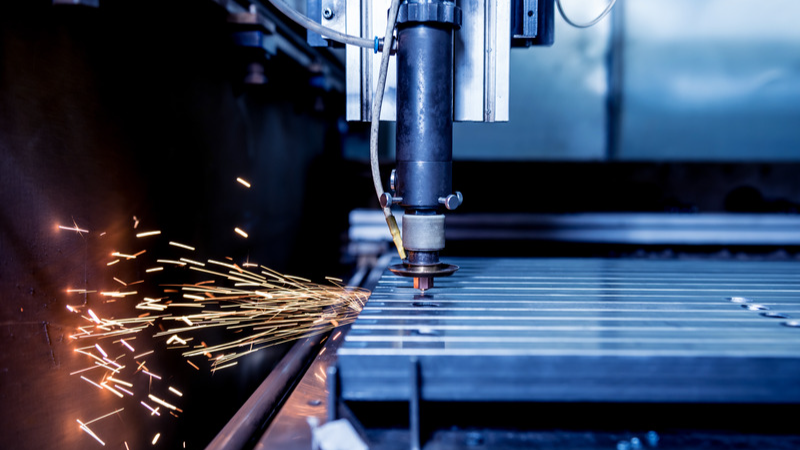
Anything that is not valuable from a customer’s perspective is called waste. Elimination of waste can lead to manufacturing cost reduction. Unfortunately, sixty percent of activities in manufacturing operations are part of the waste.
Therefore to cut down the manufacturing costs, companies can use lean manufacturing/production principles. The accurate identification of waste activities follows the elimination of waste. Following are some examples of waste activities in manufacturing operations:
- Unutilized talent or human resource
- inventory
- transportation
- overproduction etc
- Implementation of lean manufacturing/production principles can therefore reduce unnecessary costs and optimize the company’s manufacturing process.
How to Save Time?
1.Improve Manufacturing Efficiency
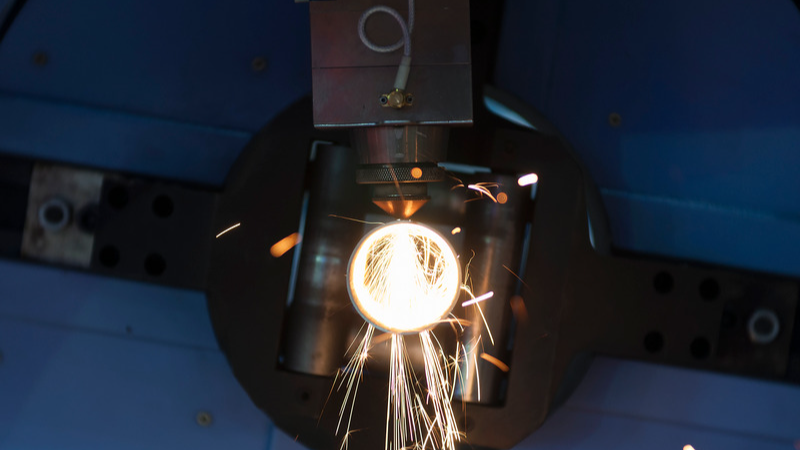
Manufacturing is all about producing the best quality product while maintaining cost. Efficiency in manufacturing pays attention to minimizing the risks and reducing the number of defects in the product.
A company can improve manufacturing efficiency by the purchase of high-quality materials. Good quality materials can cause fewer defects. The labor would also be able to carry out all the work manufacturing tasks easily.
Overall Equipment Effectiveness (OEE) is the metric used to measure manufacturing/production efficiency. It is a percentage of how many overall good products a company produces within zero downtime and at least cost.
Eighty percent of the errors in the manufacturing process are human errors. Standardization of the manufacturing process can reduce these errors and increase efficiency.
A manufacturing company should have a bird’s eye view of the data. It should be able to analyze everything related to labor, inventory, and production. Based on the findings, it should identify and eliminate the bottlenecks.
2.Get Consistent Results
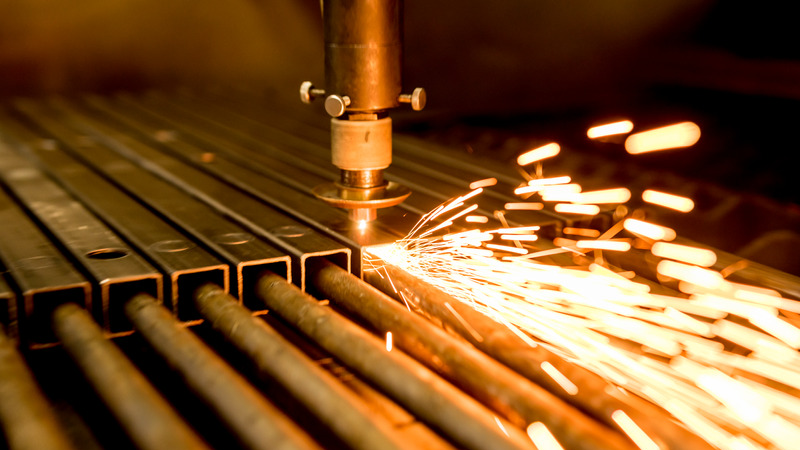
A manufacturing company often faces the challenge of dealing with variable results. Producing consistent results is crucial to the company’s success in this competitive environment.
But how can a manufacturing company ensure consistent product and service quality? The answer is simple: QUALITY MANAGEMENT. You can see the article we’ve written called “20 Tips to Help You Improve the Laser Cutting Quality” for more details.
Quality management focuses on preventive maintenance. It pays attention to eliminating errors or defects in the production process. It prevents reworks and overhead demands through standardization of processes across the supply chain, i.e., design, development, manufacturing, and distribution of the product.
How to Reduce Costs?
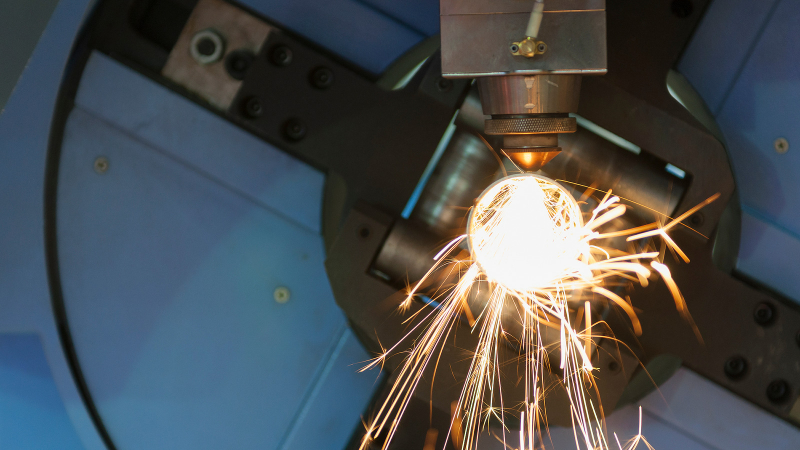
1.Reduce Material Cost
Cutting down the material costs is critical to the profitability of a manufacturing company. In order to reduce material costs, a company should always look for ways to set up something in which it can consume less material. However, it should also make sure that no compromise is made on production volume and product quality.
A company can use the following tools and strategies to reduce material costs:
- reviewing the entire supply chain process to identify, gather and utilize waste wherever possible
- process automation
- implementation of batch production
2.Adopt Strategic Production Plans
The present global business market has become smarter. To ensure manufacturing cost reduction, companies adopt strategic production plans. Implementation of lean manufacturing/production principles is one of those strategic production plans. A lot of companies have adopted lean manufacturing/production principles to stand apart from the rest of the market. It is their competitive edge.
What are lean manufacturing/production principles? Five key principles comprise the basis of lean manufacturing/production principles which are:
- identification of value
- mapping of value stream
- creation of flow
- establishment of pull and
- seeking perfection
Implementing these five principles leads to various advantages such as cost reduction, increased productivity, quality improvement, and increased profitability.
Doing more with less effort is the core concept of lean manufacturing. The basic objective of lean manufacturing is to reduce material waste.
3. Reduce Labor Costs
Labor cost is among the most important costs incurred by businesses. Labor cost refers to the ability of a business to convert its labor into profit efficiently. Labor cost is the sum of the payroll taxes, wages, and salaries paid to and for all the company’s employees. It is of two types, i.e, direct and indirect labor.
- Direct labor refers to the wages and salaries paid to the employees involved in the production and operations
- Indirect labor relates to the costs involved in increasing the productivity and efficiency of the production or manufacturing process
- Companies need to focus on balancing labor costs. An equilibrium state should be maintained between both man and machine activities. To optimize the use of labor, companies should take the following steps:
- Focus on work specialization
- Pay more attention to such tasks that enhance the company’s productivity
- Hire employees with various skill sets that are capable of multitasking
- Encourage the use of new techniques and work processes by motivating the employees to give their input
4. Replace the Obsolete Equipment
While investing in the company’s processes, one should always consider the cost-benefit analysis. Continuing operations with old and weary equipment can increase costs and compromise the quality of production. Result? Unsatisfied customers.
Obsolete equipment might halt production, make the process more time-consuming and increase overhead costs. A major overhead cost caused by a factory using obsolete equipment is maintenance cost.
Companies should make sure to invest in their equipment and increase the efficiency of their operations. While planning to purchase new equipment, companies should always consider the following factors:
- the new equipment would be able to speed up the production processes
- it will have a significant impact on product quality
- it will cause a reduction in material waste
- will lead to an increase in the volume of production in the near future and
- will lead to the smooth operation of processes in the long run
Features of Different Pipe-Cutting Machines
For a modern manufacturer who wants to attain a competitive edge in the market, our laser pipe-cutting machines are the best option to speed up their own fabrication processes.
Baison’s laser pipe-cutting machines offer a high range of precision and accuracy. The following table shows the significant features of each machine:
1.Small Tube Laser Cutting Machine
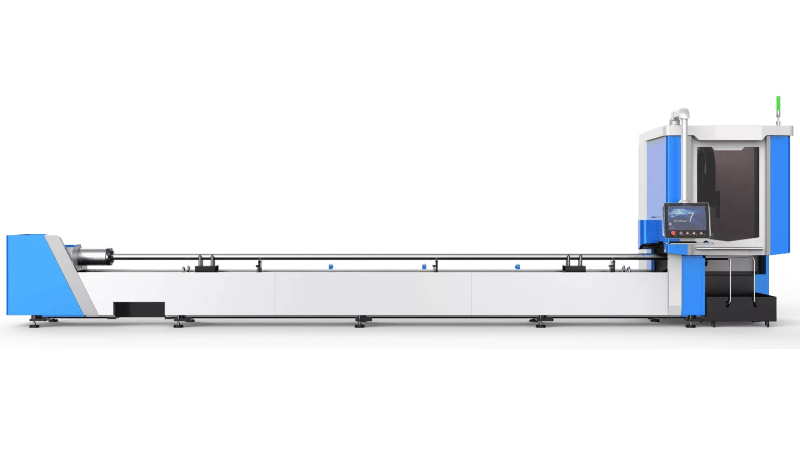
- The small tube laser cutting machine reduces the maintenance and operations cost to a maximum.
- The simple buttons on the machine make it easy to operate.
- It provides precise and stable pipe cutting through its servo follow-up support system.
2.All-Round-Tube Laser Cutting Machine
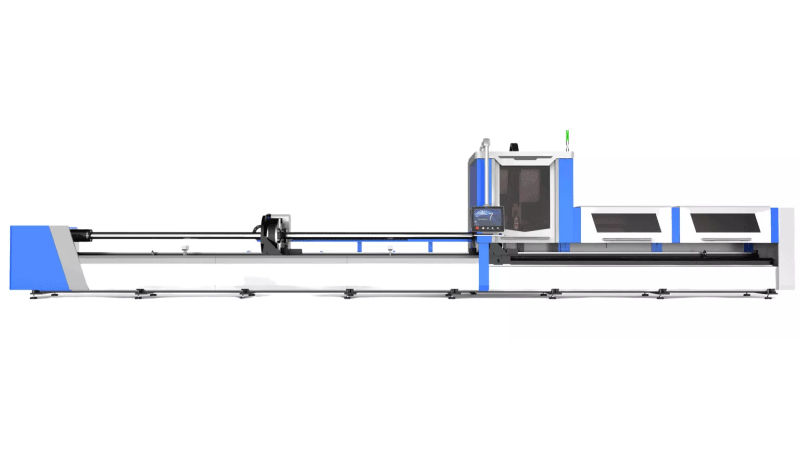
- The all-around tube laser cutting machine uses a solid-state laser to decrease the processing time and increase the production volume.
- It works perfectly on heavier material.
- It can be used on a wide variety of materials and diameters ranging from 10-20 mm.
- It provides more flexible cutting through a dynamic combination of chuck and laser head.
- It ensures accuracy in cutting through a pneumatic chuck.
- The three-chuck design produces minimum waste of material.
3. Heavy Duty Tube Laser Cutting Machine
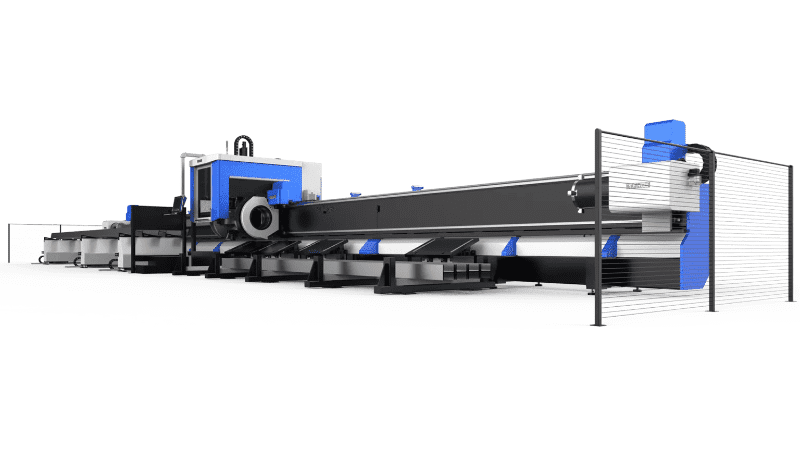
- The heavy-duty tube laser cutting machine is ONE MACHINE CUTS ALL tool.
- This machine is capable of cutting through heavy metals and tubes of all sizes.
- It offers high-quality bevel cuts with high precision.
- With up to four heavy-duty chucks, the machine offers more durability and an extended period of operation.
All these machines have three common features to offer the customer, i.e., precision, durability, and ease of use. The best machine for you is the one that best meets your manufacturing business requirements.
Conclusion
Baison Laser has enabled companies to take their manufacturing abilities to new heights through its laser pipe-cutting machines. With durability, ease of use, high precision, and accuracy, these new machines can be used on all sorts of materials and diameters.
With up-to-date technology and energy-efficient qualities, our machines and components can be used across various manufacturing processes and industries. Apart from laser cutting machines, Baison also offers laser welding, cleaning, and marking machines.
Get in touch with our team of experts and request an instant quote NOW!