Metal fabrication is a popular part of construction and other projects that use the various implementations of metal works for functionality and aesthetics. And it requires precise bends and shapes. We use different machines for different purposes when bending metal. Two prominent machines used for this purpose are panel benders and press brakes. Choosing between them can be crucial for maximizing efficiency and achieving the desired results in your projects.
This blog post will guide you through the detailed knowledge of what these two machines are, their functionalities, advantages, similarities and dissimilarities, and applications of both machines, ultimately helping you decide which one best suits your needs.
What is a Panel Bender?
A panel bender is a sheet metal working machine that utilizes a series of rollers and fingers to create bends in sheet metal. Bending sheet metal while doing creative metal works can enhance the craftmanship. The machine can be programmed to create complex shapes with high precision. Panel benders offer advantages like fast turnaround times, and minimal setup changes.
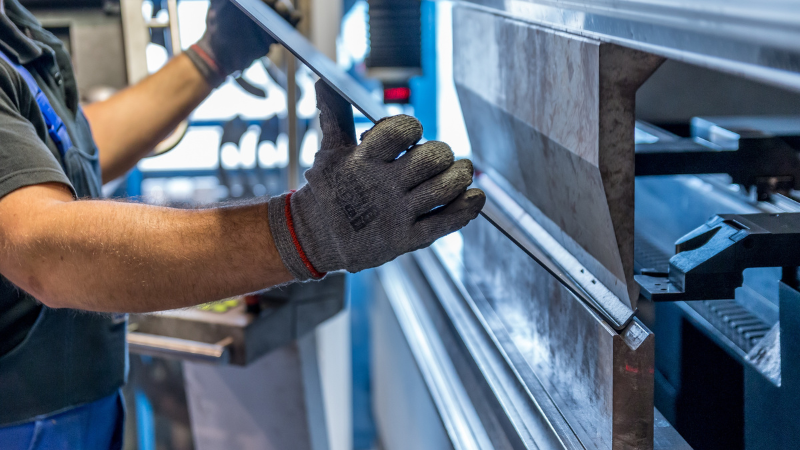
Not only that, it also has the expertise that enables the ability to handle intricate bends. It has upper and lower universal bending blades that help generate lateral force. However, the bending process might have limitations in terms of material thickness and overall working area compared to press brakes.
What is a Press Brake?
A press brake functions by clamping a sheet of metal between a punch and a die. The punch then presses down on the sheet, creating a bend along the die’s profile. A traditional press brake is known for its versatility in handling a wide range of material thicknesses and sizes.
Additionally, they can form various bend angles with the appropriate tooling. However, press brakes might require more setup time for complex bends and involve manual manipulation of larger sheets, impacting production speed.
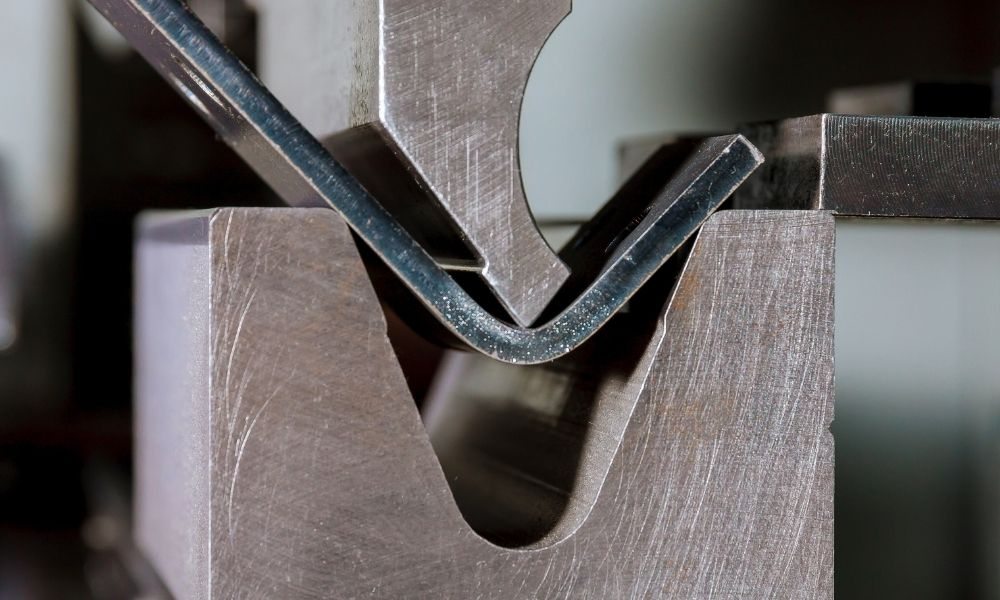
One of the earliest methods of mechanical metal deformation is press brake metal forming. A piece of metal is formed along a straight axis during this procedure. A punch and die set is used to achieve this forming. The shape of the set might be channel, “U,” or “V.” Although a CNC controlled press brake machine’s lifespan can extend well beyond 50 years from the date of creation, units older than 20 years may be very challenging to acquire spares and maintenance for.
Ready to Get Your Own Bending Machines?
Boost your operations with Baison Laser's advanced, customized technology!
Applications of Panel Bender
Panel benders are the go-to machines for specific industries due to their unique ability to handle complex bends with high precision. Here’s a deeper dive into why these industries leverage panel benders:
1. HVAC Systems
HVAC systems consist of numerous ductwork components with bends, angles, and offsets to navigate around obstacles and optimize airflow. Panel benders can efficiently create these intricate shapes with minimal tooling changes, ensuring proper air circulation within buildings.
2. Appliance Manufacturing
Modern appliances like refrigerators, washing machines, and ovens often have curved panels for aesthetics and functionality. Panel benders excel at forming these bends precisely, maintaining a sleek and uniform look for the final product.
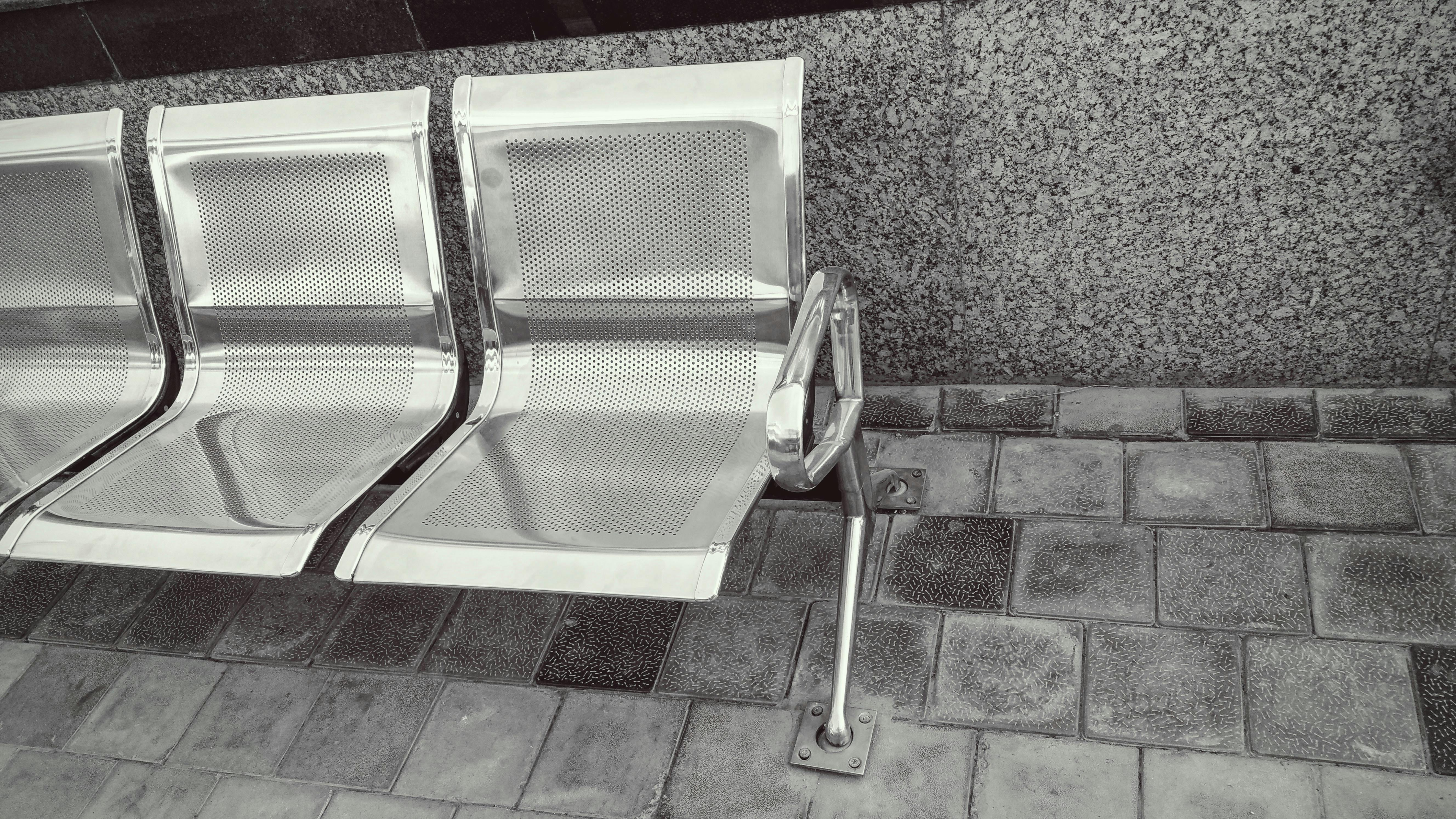
Additionally, intricate internal components within appliances can also benefit from panel bending’s ability to create folded shapes.
3. Electronics Enclosures
Electronic devices require protective housings with ventilation slots, access panels, and other intricate features. Panel benders can create these features with sharp bends and tight tolerances, ensuring a perfect fit for electronic components while maintaining a clean and professional appearance for the enclosure.
4. Architectural Cladding
Modern architecture often incorporates metal panels with complex folds and curves for a unique aesthetic. Panel benders allow for the creation of these custom cladding panels with high precision, enabling architects to bring their visions to life. The ability to handle larger panels also contributes to faster installation times for building projects.
Applications of Press Brake
Press brakes reign supreme in industries requiring large quantities of metal parts with various bend requirements. Here’s a closer look at some of the applications where press brakes truly excel:
1. Automotive Parts
Imagine the intricate shapes that make up a car’s body panels, chassis components, and brackets. Press brakes are the workhorses behind these parts. Their ability to handle a wide range of material thicknesses, from thin sheet metal for interior panels to sturdier steel for frames, makes them ideal for automotive production.
Additionally, the possibility of using various press brake tooling allows for the creation of diverse bends, folds, and flanges on these parts.
2. Roofing Panels
Roofs come in various shapes and sizes, and press brakes play a crucial role in shaping the metal panels used in their construction. From simple corrugated panels to complex standing seam profiles, press brakes can efficiently form these shapes with high precision. This ensures proper water drainage, weatherproofing, and a clean aesthetic for the finished roof.
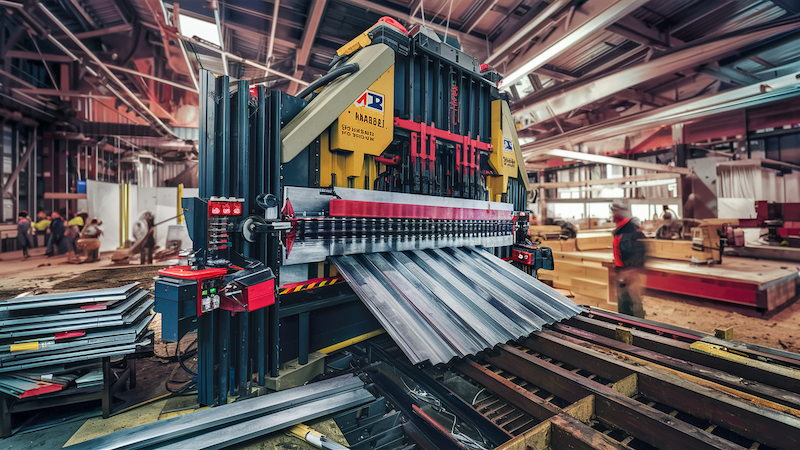
3. Ductwork
HVAC systems rely on a network of ducts to deliver conditioned air throughout a building. Press brakes are instrumental in creating the straight and angled sections of these ducts.
Their ability to handle larger sheet sizes allows for the production of longer duct sections, minimizing the need for joints and maximizing airflow efficiency. Additionally, press brakes can form flanges on the duct ends for secure connections with other components.
4. Building Components
The world of construction utilizes press brakes for a variety of purposes. From creating brackets for structural support to shaping metal cladding panels for building exteriors, press brakes offer the versatility needed for these applications. They can efficiently bend various metal elements used in walls, ceilings, and other building components, ensuring a precise fit and a sturdy final structure.
Ready to Get Your Own Bending Machines?
Boost your operations with Baison Laser's advanced, customized technology!
Similarities Between Panel Bender and Press Brake
Both the panel bender and press brake are used to bend sheet metal and can achieve precise results. The entire bending process requires the proper use of metal types and machines. These two types of machines are sometimes used interchangeably because of how similar they are.
The panel bender and press brake both have the function of bending the metal sheet to our design and functional needs. They offer the ability to work with various materials like steel, aluminum, and stainless steel. Additionally, both machines can be equipped with CNC (Computer Numerical Control) systems for automated operation.
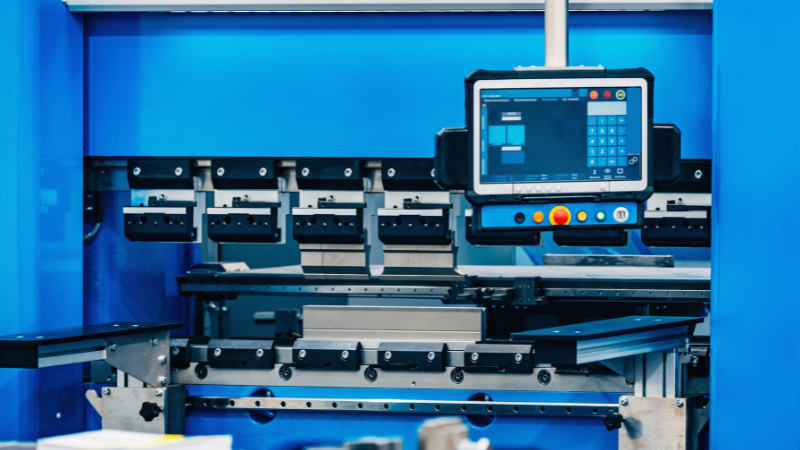
Differences Between Panel Bender and Press Brake
Even though panel benders and press brakes are all used for bending sheet metals to a needed shape and design, these have some differences in the actual forming process. You need to be careful while choosing between the two based on what you like. Some of these differences are such that:
- Working Principle: For panel benders, there is a set of rollers and fingers that bend the sheet. The material mass lies flat on the table and can get bent with the help of the rollers. And when it comes to pressing brakes, punch, and die to create the bends the material has to follow the action movement.
- Production Efficiency: Using panel benders is faster for complex shapes and for high-volume activities of metal sheet bending, press brakes are the best choice. When you need a faster approach even when the job is of high difficulty level, then you need to use panel benders. But otherwise, press brakes are the best option.
- Bending Quality: Panel benders have a higher precision for intricate bends than press brakes. On the other hand, the opposite is true for much simpler bends.
- Material Thickness: Even though you can use panel benders for a range of metal sheets with varied thicknesses, this works best with the thinner sheets. But press brakes handle a wider range of thicknesses.
- Working Area: While working with panel benders, you are okay with setting up in a smaller area, whereas a larger working area setup is needed for press brakes.
- Setup Time: When working with panel benders, the setup time and production line is minimal, even for complex bends, but a press brake may require more setup time.
- Operator Skill: The operator working panel benders requires much less skill level than the one operating the press brake.
Which One Should You Choose?
In the end, no matter what the pros and cons of using either of these bending and folding machines are, you need to choose the one best suited for your needs. The ideal machine for your project depends on several factors:
- Complexity of Bends: You need to ensure how complex the required job is. If the designs are more intricate, you need to plan as such. Panel benders are better suited for intricate shapes requiring multiple bends.
- Production Volume: It is also important to consider how much you need to prepare at a certain time limit. For high-volume production of simple bends, press brakes offer better speed and efficiency.
- Material Thickness: Make sure that you know just how thick the metal sheet you are working with is going to be. Consider the thickness of the sheet metal you’ll be working with. Press brakes handle thicker materials.
- Budget: Above all, you must be aware of your budget limit. Panel bender tooling generally has a higher initial cost than press brakes.
Above all, there are a lot of decisions to be made when choosing to buy machines for your business. You need to invest in a way that is profitable for the business and also adds new potential for expanded business opportunities.
Ready to Get Your Own Bending Machines?
Boost your operations with Baison Laser's advanced, customized technology!
FAQs
1. Why are panel benders easier to operate?
Panel benders tend to be fully automated, and there are different types of blades to ensure the best and safest outcome. Due to their automation features, panel benders often require less operator skill compared to press brakes.
2. Do I need a separate machine for flagging?
Press brakes are more suitable for creating internal flanges, while panel benders might require additional tooling for this purpose.
Conclusion
High-quality metal fabrication depends on the perfect execution of all the different operations in the whole process. The bending force from different machines has different outcomes. Understanding the strengths and limitations of panel benders and press brakes will empower you to make an informed decision for your sheet metal fabrication needs.
By considering the factors mentioned above, you can choose the machine that optimizes your workflow, production efficiency, and overall project success. For further guidance on metal fabrication equipment and techniques, explore Baison‘s website’s resources!
Ensure the Best Choice for Your Metal Fabrication Projects!
If you are trying to get the best machines for your next projects and to improve the serviceability of your metal fabrication business, you need to know all there is to know about various machines. Contact us at Baison now to get any type of help related to your machine choices, machine prices, and much more!