This blog post aims to provide valuable insights and guidance on these two popular cutting techniques, helping you make the best decision for your projects and business needs. Let’s dive into the world of precision cutting and explore the differences between a laser cutting tool and die cutting to determine which one is right for you.
Laser Cutting
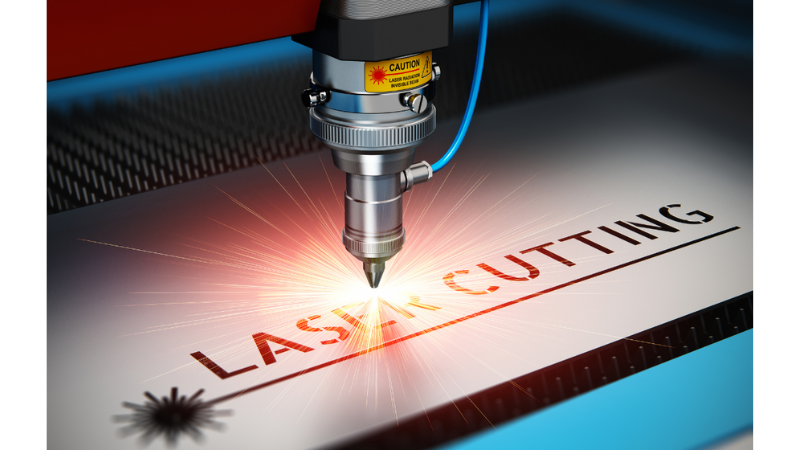
What is Laser Cutting?
Fiber laser cutting is a non-contact manufacturing process that uses a high-powered, focused laser beam to cut materials by melting, burning, or vaporizing the material. This advanced technology is widely used in industries such as aerospace, automotive, electronics, and textiles, among others, for its precision and versatility.
How Does Laser Cutting Work?
Laser cutting works by directing a high-powered laser beam at the material to be cut. The laser’s energy is concentrated in a small area, generating heat that melts or vaporizes the material.
The laser is guided along the desired cutting path using computer numerical control (CNC) technology, ensuring accurate and consistent laser cuts. A gas, typically nitrogen or oxygen, is used to blow away the molten material and debris, leaving a clean, precise cut.
Benefits of Laser Cutting
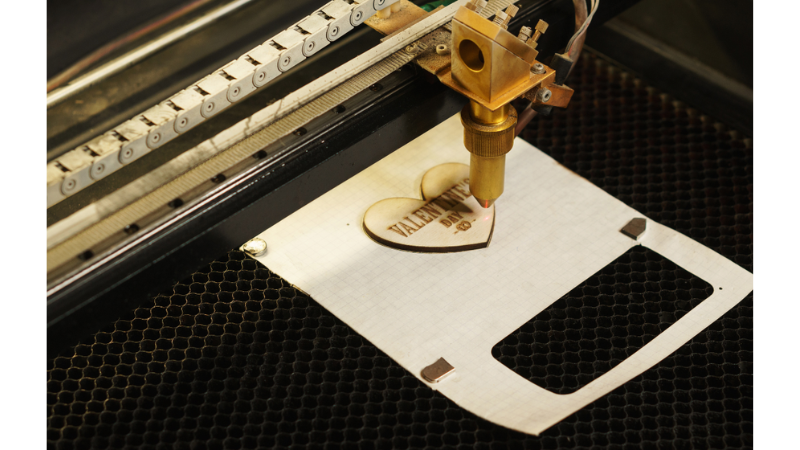
Laser cutting offers several advantages, including:
- Thin materials: Laser cutting is ideal for cutting thin materials, such as sheet metal, plastics, and textiles, with minimal distortion or damage.
- Complex shapes: The non-contact nature of laser cutting allows for intricate, complex shapes to be cut without the need for custom cutting tools or dies.
- Precise cuts: Laser cutting provides high precision and accuracy, resulting in clean, smooth edges and minimal material waste.
- Reduced setup time: Since laser cutting relies on CNC technology and doesn’t require physical tooling, setup times are typically shorter than with traditional cutting methods like die cutting.
Types of Jobs that are Well-Suited for Laser Cutting

Laser cutting is modern technology well-suited for various applications, such as:
- Prototyping and small-batch production: The flexibility and precision of laser cutting make it ideal for creating prototypes and producing small runs of custom parts.
- Intricate designs and patterns: Laser cutting can easily handle complex shapes and intricate designs, making it perfect for industries like fashion, signage, and electronics.
- Multi-material projects: Laser cutting can be used on a wide range of materials, including metals, plastics, textiles, and composites, making it suitable for projects involving multiple material types.
- High precision requirements: Industries that demand high precision and tight tolerances, such as aerospace and medical devices, benefit greatly from the accuracy offered by laser cutting.
Die Cutting
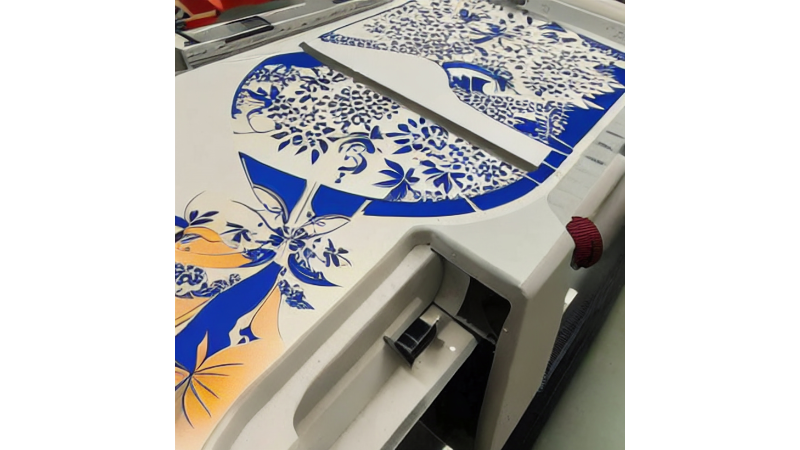
What is Die-Cutting?
Die cutting is a manufacturing process that uses custom-made cutting tools, called dies, to cut or shape materials such as paper, cardboard, plastic, foam, and fabric. Die cutting is widely used in industries like packaging, printing, and textiles for its efficiency and ability to produce consistent, uniform cuts.
Benefits of Die Cutting
Die-cutting offers several advantages, including:
- High-volume jobs: Die cutting is well-suited for high-volume production runs, as it can quickly and consistently cut large quantities of material with minimal waste.
- Uniform cuts: The use of custom-made dies ensures that every cut is consistent and uniform, resulting in a professional and polished final product.
- Easy replication: Once a die is created, it can be used repeatedly to produce identical cuts with minimal effort, making die cutting an efficient choice for mass production.
- Lower cost per unit: As production volume increases, the cost per unit typically decreases, making die-cutting a cost-effective option for large-scale manufacturing.
Different Types of Die-Cutting Machines
There are two main types of die-cutting machines:
1. Flatbed Die-Cutting Machines
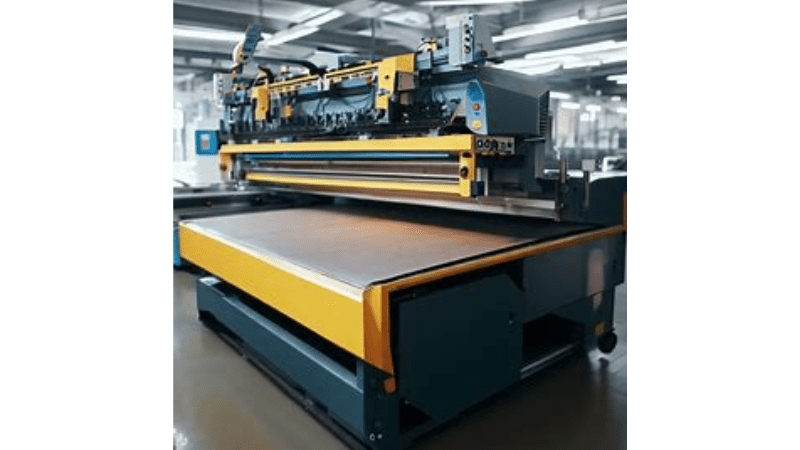
Flatbed die-cutting machines use a flat, stationary cutting surface and a custom-made die to cut materials. The material is placed on a flat surface, and the die is pressed down onto the material using hydraulic or other mechanical equipment or force.
Flatbed die-cutting machines are versatile and can handle a wide range of materials and thicknesses. They are ideal for short production runs, thick materials, custom shapes or projects requiring precise alignment.
2. Rotary Die-Cutting Machines
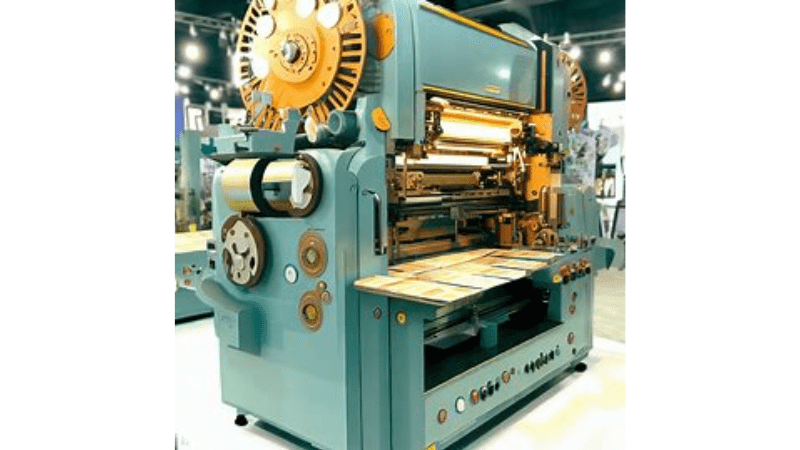
Rotary die cutters use a cylindrical die and a rotating cutting surface to cut materials. The material is fed through the machine, and the cylindrical die rotates against it, cutting it as it moves through it.
Rotary die cutters are well-suited for high-speed, high-volume production and can handle thinner materials more efficiently. Moreover, rotary die cutters are commonly used for projects involving continuous materials, such as rolls of labels, adhesive tapes, or flexible packaging materials.
Laser Cutting Vs. Die Cutting
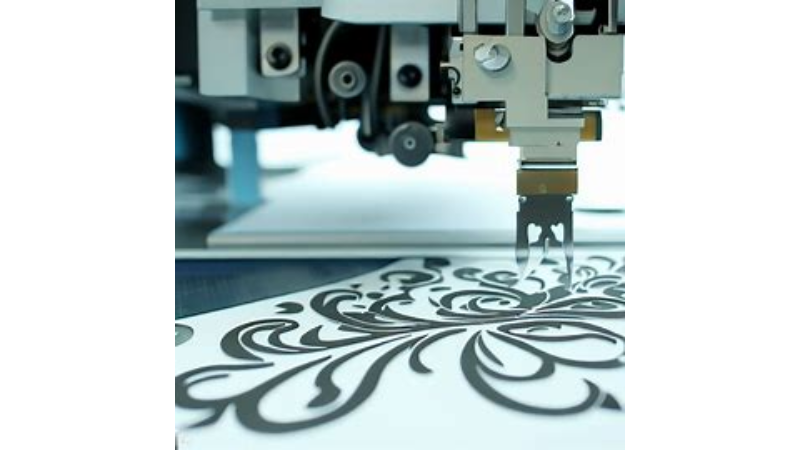
Difference Between Laser Cutting & Die Cutting
The following table highlights the primary differences between laser and die cutting, making determining which method suits a specific project easier. Factors like lead time, precision, speed, production volume, design complexity, cost, desired shape, edge smoothness, and finishing needs are crucial when deciding between these cutting methods.
Category | Laser Cutting | Die Cutting |
Lead Time | Shorter (quick setup) | Longer (custom die fabrication) |
Precision | High precision and accuracy | Good precision, but may vary |
Speed | Moderate to fast, depending on power | Faster for high-volume production |
Volume | Suited for low to medium volumes | Ideal for high-volume production |
Complexity | Capable of handling complex shapes | Limited by die design capabilities |
Cost | Higher initial cost, lower cost per unit for small batches | Lower initial cost, cost-effective for high volumes |
Specific Requirements for Certain Jobs
Laser cutting is highly versatile and can create any desired shape with smooth edges and minimal finishing needs. On the other hand, die cutting is limited by the die design and may produce rougher edges or require additional finishing steps.
The specific requirements of a job will determine which method is more suitable. Laser cutting offers a wider range of material compatibility, whereas die cutting is generally limited to materials like paper, cardboard, and foils.
Moreover, regarding environmental impact, laser cutting typically produces less physical waste than die cutting, as it vaporizes material instead of removing it as scrap. Depending on the specific application and material used, this can lead to a lower overall environmental impact.
Category | Laser Cutting | Die Cutting |
Desired Shape | Highly versatile (any shape possible) | Limited by die design (custom dies) |
Edge Smoothness | Smooth edges, little to no burring | Can have rougher edges o burring |
Finishing Needs | Minimal post-processing | May require additional finishing steps |
Material Compatibility | Wide range (metals, plastics, textiles) | Limited (mostly paper,cardboard. foils) |
Environmental Impact | Lower (no physical waste) | Higher (due to material waste) |
How to Choose?
When it comes to choosing between laser cutting and die cutting, businesses should consider several factors to determine the best method for their specific needs. Here’s a guide to help you make an informed decision:
1. Evaluate the complexity of your designs
If your project requires intricate shapes and designs, laser cutting is preferred, as it can easily handle complex patterns without needing custom dies. However, die-cutting can be more efficient if your project involves simple, repetitive shapes.
2. Consider the production volume:
For small to medium production volumes, laser cutting machines, such as those offered by Baison Laser, can provide cost-effective solutions with shorter setup times. On the other hand, die-cutting becomes more cost-effective as the production volume increases, making it ideal for large-scale manufacturing.
3. Assess material thickness and type:
Laser cutting is best suited for thin, flexible materials, while die cutting can handle a wider range of thicknesses. Consider the various materials you will be working with and choose the cutting method most compatible with those materials.
4. Analyze precision requirements:
Laser cutting is the way to go if your project demands high precision and accuracy. Like Baison Laser, laser cutting machines can deliver precise cuts with smooth edges, often requiring minimal finishing. Die cutting also provides good precision, but the results may vary depending on the die cutter being used.
5. Determine your budget:
Laser-cutting machines typically have a higher initial cost, but the cost per unit for small batches is lower. Die-cutting machines have a lower initial cost, but the cost-effectiveness increases with higher production volumes. Evaluate your budget and production needs to decide which method is more suitable for your business.
6. Consider the lead time and speed:
Laser cutting process offers shorter setup times and can be more suitable for quick turnarounds and prototyping. Die cutting offers faster cutting speeds for high-volume production while having longer setup times due to die creation.
By considering these factors and evaluating your specific project requirements, you can confidently choose between laser cutting manual machine and die cutting. Baison Laser’s laser and laser die-cutting and machines are an excellent choice for businesses seeking precision, flexibility, and cost-effectiveness for small to medium production volumes.
Conclusion
In conclusion, choosing between laser cutting and die cutting requires careful consideration of several factors, such as project complexity, production volume, precision requirements, material thickness and type, budget, lead time, and speed.
By understanding the differences between these cutting methods and assessing your project needs, you can make an informed decision and achieve precise, efficient results.
At Baison Laser, we offer a wide range of laser-cutting machines to meet your specific needs. Whether you need a laser cutter for prototyping, small-batch production, or high-volume manufacturing, we have the right laser cutter solution for you.
Transform your manufacturing process today with Baison Laser’s cutting-edge laser-cutting technology. Schedule a free consultation with our team to discover the perfect laser-cutting solution for your business needs. Don’t miss out on the opportunity to take your business to the next level. Contact us now to get started!
What Will You Get with Free Consultation?
During the free consultation, our experts will provide tailored guidance and support to help you find the best laser cutting machine for your specific requirements. We understand that every business has unique needs and challenges, so we take a personalized approach to every consultation.
Ready to take your manufacturing to the next level? By contacting us for a consultation, you can take the first step towards improving your manufacturing process and staying ahead of the competition.