In this post, we’ll explore the importance of laser cutting technology in shipbuilding, covering topics such as the benefits of using laser cutting machines in shipbuilding and how these machines are utilized to cut marine steel plate raw materials. Join us as we dive into the world of maritime construction and the power of laser cutting in the shipbuilding industry.
Laser Cutting Technology
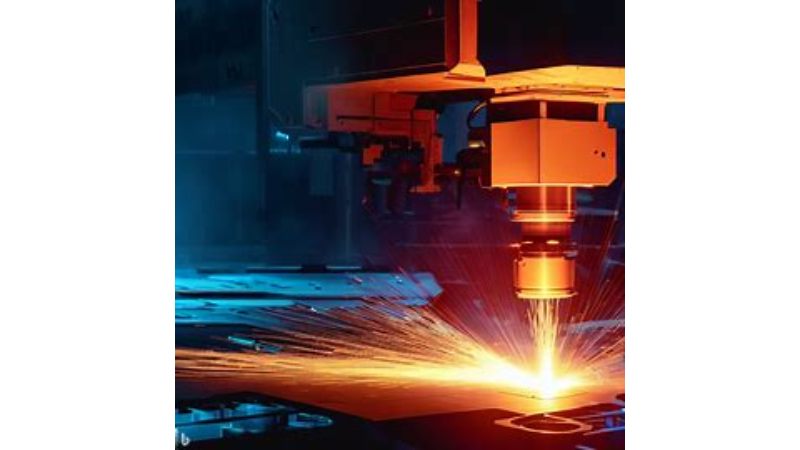
Laser cutting technology cuts, engraves, or etches materials through a highly concentrated laser beam. The beam is generated within a resonator and then directed onto the workpiece with mirrors and lenses.
As the laser beam interacts with the material, it rapidly heats, melts, or vaporizes along the cutting path, resulting in a precise and immaculate cut.
How Does Laser Cutting Machine Work?
A fiber laser cutting machine produces a precise cut by directing a potent laser beam onto a material. As a result, the material is melted, burned, or vaporized. A computer-controlled system guides the laser beam according to a digital design, ensuring that the cutting process is precise and uniform.
Since laser cutting is a non-contact procedure, it minimizes material deformation and produces high-quality edges. It is an adaptable and efficient cutting method that can be employed on various materials, including wood, plastics, metals, and more.
Do You Have Any Questions?
Let Us Solve Your Problem
Plasma Cutting vs. Laser Cutting
Here is a comparison between plasma cutting and laser cutting:
Feature | Plasma Cutting | Laser Cutting |
Cutting Principle | Uses electrically conductive gas to cut material | Uses a focused, high-intensity laser beam to cut material |
Precision | Moderate to good | High precision and accuracy |
Edge Quality | Rougher edges may require finishing | Smooth, clean edges, often with minimal post-processing |
Cutting Speed | Generally faster for thick materials | Faster for thin to medium-thick materials |
Material Thickness | Better suited for cutting thicker materials | Excels at cutting thin to medium-thick materials |
Heat-Affected Zone (HAZ) | Larger heat-affected zone due to thermal process | Minimal heat-affected zone, reducing distortion |
Material Compatibility | Limited to electrically conductive materials (metals) | Can process a wide range of materials, including non-metals |
Operating Cost | The lower initial investment, higher consumable cost | The higher initial investment, lower consumable cost |
Kerf Width | Wider kerf, resulting in more material waste | Narrow kerf, reducing material waste |
Noise and Debris | Generates more noise and debris | Quieter operation and less debris production |
Both plasma cutting and laser cutting have advantages and disadvantages. The choice between the two technologies depends on factors such as material type, thickness, required precision, budget, and production volume.
The shipbuilding sector often favors laser cutting for its precise cuts, clean edges, and minimal heat-affected zone. This particularly applies when working with marine-grade steel plate materials and complex shapes.
Benefits of Using Laser Cutting in the Shipbuilding Industry
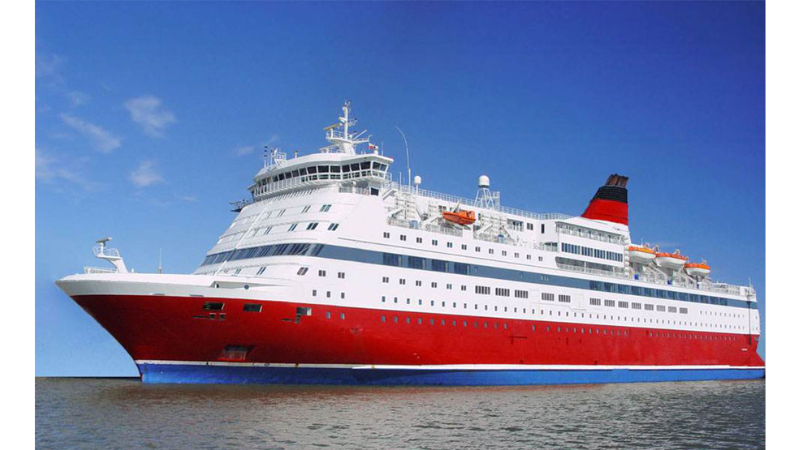
The shipbuilding industry has a lot to gain from utilizing laser cutting technology, as it offers numerous advantages. Here are some of the key benefits of flame cutting is:
1. Smooth surface and high curve cutting accuracy
Laser cutting is an efficient method that produces smooth and clean edges with minimal roughness or burrs, reducing the requirement for additional finishing or post-processing operations. The high precision and accuracy enable intricate designs and tight tolerances, resulting in high-quality components and structures.
2. Reduced labor and material waste
Laser-cutting machines are great at minimizing material waste, which leads to cost savings and promotes sustainable practices. Moreover, these machines’ automation capabilities have the potential to decrease labor costs and human error, leading to a reduction in assembly workload and an enhancement in overall efficiency.
3. Increased accuracy and efficiency
The ability of laser-cutting equipment to process materials quickly and accurately results in increased productivity and reduced delays. This efficiency allows shipbuilders to complete projects faster, keeping up with industry demands and staying competitive.
4. Versatility and customization
Laser cutting machines can process a wide range of materials, including marine-grade steel plates, and can be conveniently modified to suit different thicknesses and design specifications. This flexibility enables shipbuilders to create custom components and structures without investing in multiple cutting technologies.
5. Enhanced safety and reliability
As laser cutting is a non-contact technique, it minimizes the possibility of material distortion or damage, preserving the material’s mechanical properties and creating more efficient ships.
Processing & Application Characteristics of Laser Cutting Machines
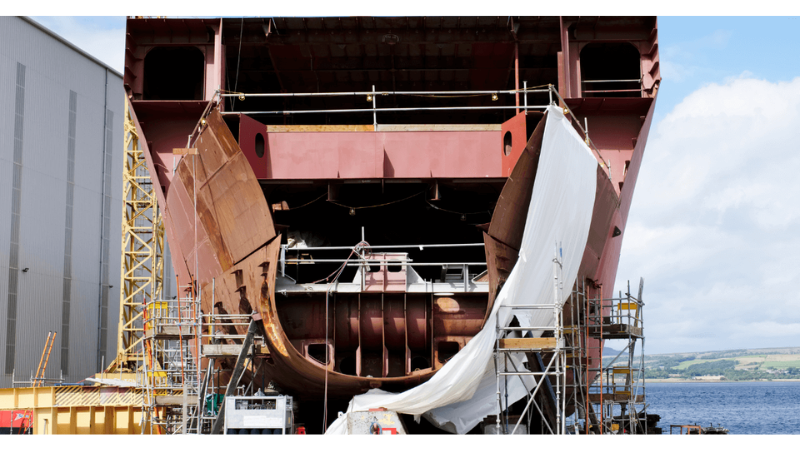
Laser cutting equipment possesses unique processing and application characteristics that give it an edge over other cutting technologies.
Some of these characteristics include:
- High precision and accuracy: Laser-cutting machines are suitable for tasks that demand exceptional detail and precision due to their ability to produce intricate designs and maintain tight tolerances.
- Excellent edge quality: The edges of materials cut with a laser are uniformly smooth and clean. This reduces the need for post-processing and finishing operations.
- The minimal heat-affected zone (HAZ): Since laser cutting is a non-contact process with concentrated energy, it generates minimal heat in the surrounding material. This reduces thermal distortion and material warping, preserving the material’s mechanical properties.
- Versatility: Metals, polymers, wood, glass, and even fabrics all be cut using a laser cutter. This versatility makes them suitable for various industries and applications.
- Reduced material waste: The narrow kerf width and precision of laser cutting minimize material waste and contribute to cost savings and sustainable practices.
Do You Have Any Questions?
Let Us Solve Your Problem
How to Use Laser Cutting Machines in the Shipbuilding Industry?
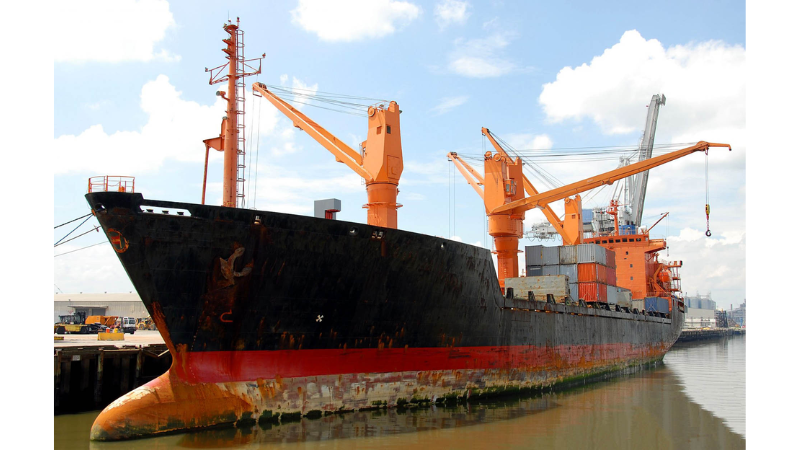
To ensure efficient and precise construction of ships, employing a laser cutting machine in the shipbuilding industry requires several key steps and considerations. Here is a comprehensive guide on how to use laser-cutting machines in this sector:
- Design and planning: Before you start the laser cutting process, create detailed digital designs and plans for the components and structures you want to build. Use computer-aided design (CAD) software to generate these designs, ensuring they meet the required specifications and tolerances.
- Material selection: Choose the appropriate materials for your shipbuilding project, such as marine-grade steel plates, aluminum alloys, or other suitable materials. Before using a laser cutter, check to see if the material you want to cut is suitable for laser cutting.
- Material preparation: Prepare the materials by cleaning and deburring them to remove any surface contaminants, dirt, or burrs that may affect the quality of the cut.
- Machine setup: Set up the laser cutting machine according to the manufacturer’s instructions, ensuring that it is properly calibrated and aligned. The cutting parameters for laser cutting, such as laser power, cutting speed, and assist gas pressure, are dependent on the material type and thickness.
- Import the design: Import the digital design files (usually in DXF or DWG format) into the laser cutting machine’s control software. Make any necessary adjustments to the cutting paths, nesting, or layout to optimize the cutting process and minimize material waste.
- Test run: Perform a test run to ensure that the laser cutting machine is functioning correctly and that the cutting parameters are suitable for the material being processed. Adjust the settings as needed to achieve the desired cut quality.
- Cutting process: Once the machine is set up and the test run is successful, start the laser cutting process. The machine will follow the imported design files to cut the material with high precision and accuracy.
- Inspection and quality control: Inspect the cut components and structures to ensure they meet the required specifications, tolerances, and quality standards. Address any issues or inconsistencies, such as rough edges, burrs, or warping, with appropriate post-processing methods, such as grinding or sanding.
- Assembly and welding: Use the laser-cut components to assemble the ship’s structures, such as the hull, decks, and internal systems. Weld the parts together according to the design specifications, ensuring proper alignment and fit. For cutting and welding applications in shipbuilding, please see this article.
- Final inspection and testing: Perform a final inspection and testing of the assembled ship to verify its structural integrity, functionality, and compliance with industry standards and regulations.
By adhering to these procedures and using laser-cutting technology, shipbuilders can improve productivity, assembly quality, and savings. This results in high-quality, innovative, and reliable ships that meet the demands of the global maritime market.
Why Laser Cutting Machines Ideal in the Shipbuilding Industry?
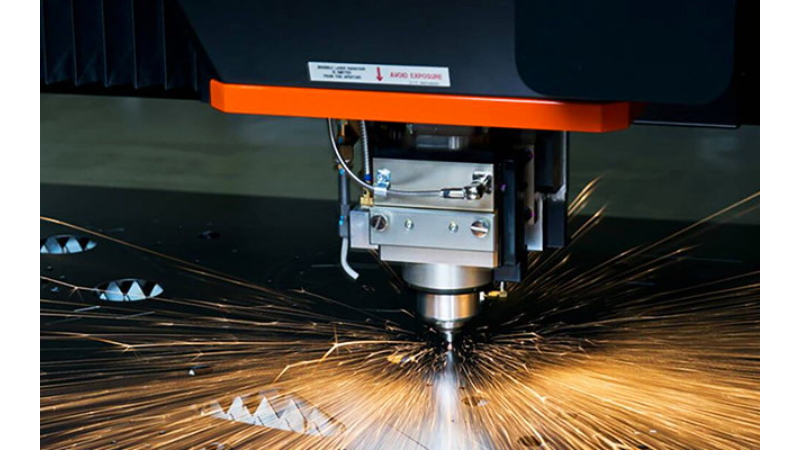
Laser-cutting machines are ideal for the shipbuilding industry due to their unique capabilities and advantages, which significantly contribute to the efficiency, precision, and overall quality of the laser-cutting machine technology in shipbuilding and construction.
Some of the key reasons why laser-cutting machines are ideal for this industry include:
- Improved efficiency: Laser cutting equipment can process materials at high speeds, reducing lead times and improving productivity. This efficiency allows shipbuilders to complete projects faster and stay competitive globally.
- Versatility: Laser cutting machines can process various materials, including marine-grade steel plates, alloys, and even non-metallic materials. This versatility makes them suitable for various shipbuilding applications, such as cutting structural components, pipes, and electronic enclosures.
- Non-contact process: As laser cutting is a non-contact process, it reduces the risk of material distortion or damage, ensuring a better-quality finish and more reliable components.
- Automation and integration: Laser cutting machines can be combined with various automated systems, such as robots, material handling tools, and CAD programs, to improve efficiency and precision. This streamlines the shipbuilding process, enabling more efficient workflows and better project management.
- Customization: Laser cutting machines are highly adaptable to new materials, varying thicknesses, and diverse design specifications, providing an exceptional level of versatility and flexibility.
Do You Have Any Questions?
Let Us Solve Your Problem
Conclusion
In conclusion, laser-cutting technology has proven to be a game-changer for the shipbuilding industry, offering unparalleled precision, efficiency, and versatility in the construction process. By adopting this cutting-edge technology, shipbuilders can create more innovative, reliable, and durable ships that meet the ever-evolving demands of the global maritime market.
The key takeaway is that laser-cutting machines significantly contribute to the overall quality and success of shipbuilding projects by minimizing material waste, reducing labor costs, and ensuring the structural integrity of components.
As the industry continues to evolve, the importance and application of laser cutting and in-cutting technology in shipbuilding cannot be overstated.
Unlock the Power of Laser Cutting in Shipbuilding: Transform Your Maritime Projects Today!
Are you ready to revolutionize your shipbuilding process and stay ahead of the competition? Embrace the future of shipbuilding materials with laser-cutting technology from Baison Laser, offering unparalleled precision, efficiency, and cost savings in the maritime industry.
Don’t miss the opportunity to have laser technology to transform your shipbuilding projects and enhance your company’s reputation for innovation and excellence. Contact us now to learn more about our cutting-edge laser-cutting machines and how they can revolutionize your maritime construction endeavors.