In this post, we’ll define laser cutting technology, explore its accessories, provide tips and tricks for maximizing output, examine a few examples of sheet metal fabrication, and share best practices for laser cutting machines. Join us as we unlock the full potential of laser cutting for maximum output in sheet fabrication.
Laser Cutting Technology
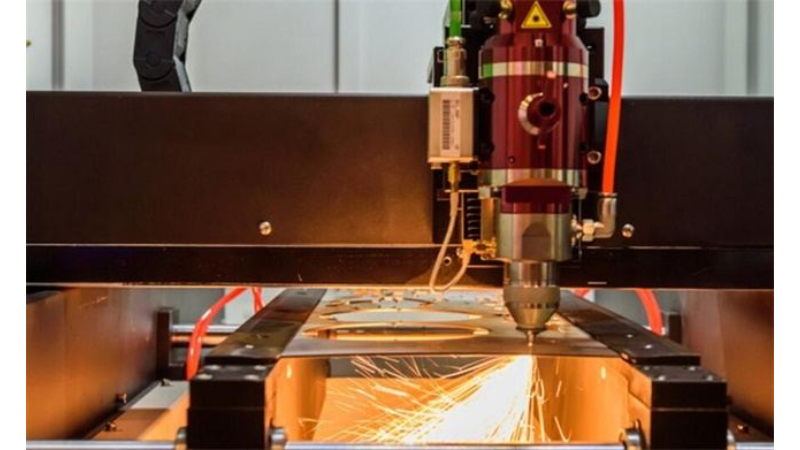
Laser cutting technology is a non-contact, thermal-based fabrication process that utilizes a focused, high-power laser beam to cut or engrave materials with exceptional precision and accuracy. The term “laser” is an acronym for “Light Amplification by Stimulated Emission of Radiation,” which explains the basic principle behind the technology.
What’s the Laser Cutting Process?
The process begins with a digital design, which is then converted into a format that the laser cutting machine can interpret. The material is placed on the full sheet metal laser cutting in bed, and the machine’s settings are adjusted for optimal results.
As the full sheet metal laser cutting head moves along the predetermined path, the intense heat from the beam melts, burns, or vaporizes the material, creating clean and accurate cuts. Depending on the material and application, assist gas may be used to enhance the cutting quality, speed, and efficiency.
How to Select the Right Laser Power for Different Metal Thicknesses?
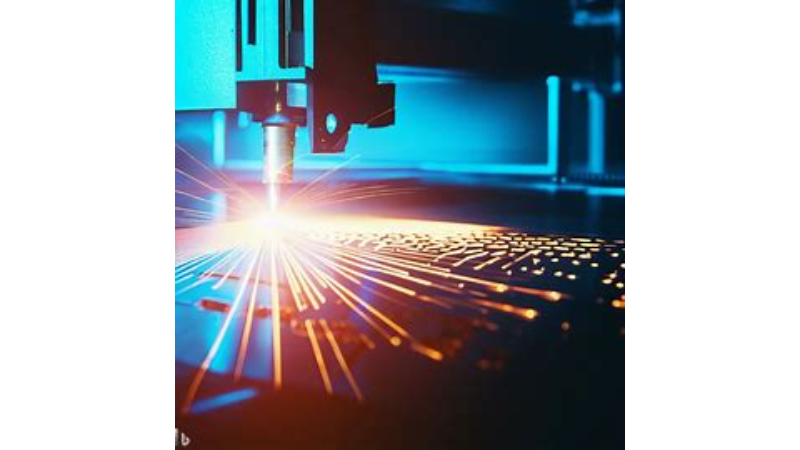
Selecting the right laser power for different metal thicknesses is crucial to achieving optimal cutting results, as it affects cutting speed, precision, and quality. Here are design tips and some general guidelines to help you choose the appropriate laser power for different metal thicknesses:
1. Thin metals (up to 3mm):
For cutting thin metals such as aluminum, high carbon steel,, stainless steel, or mild steel, a laser power of 500 to 1000 watts is generally sufficient. Lower-power lasers offer better precision and can achieve faster cutting speeds for thin materials without causing excessive melting or burning.
2. Medium thickness metals (3mm to 12mm):
A laser power between 1000 and 3000 watts is usually recommended for cutting medium-thickness metals. This higher power allows for faster cutting speeds and efficient processing of thicker raw materials without compromising the metal thickness’s quality.
3. Thick metals (12mm and above):
A laser power of 3000 watts or higher is often necessary to cut thick metals. These high-power lasers can penetrate and vaporize thicker materials more effectively, resulting in clean, precise cuts. However, cutting very thick materials may require slower cutting speeds to maintain quality and prevent excessive heat buildup.
It’s important to note that these guidelines are general and may vary depending on the specific type of metal, laser cutting system, and desired cutting quality.
To achieve the best results, it’s essential to consult the laser cutting machine manufacturer’s recommendations and perform tests on the material to fine-tune the laser power, cutting depth, speed, and other parameters for your specific application.
How Does Laser Light Create a High-Intensity Beam Path?
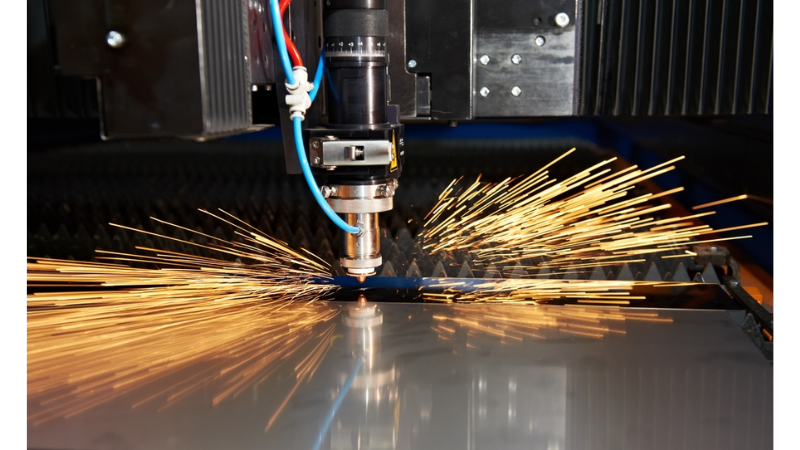
The process of amplifying laser light to create a high-intensity light beam involves a few essential components and steps, which can be briefly described as follows:
1. Gain medium:
The gain medium is a material that can absorb energy from an external source and store it in its atoms or molecules. This energy is then released as coherent light when the atoms or molecules return to their lower energy states. Gain media can be solid (like crystals), liquid (dye solutions), or gas (such as CO2 or helium-neon mixtures).
2. Energy pump:
An external energy source, called a pump, provides energy to the gain medium. This pump can be an electrical discharge, a flashlamp, a chemical reaction, or another laser source, depending on the type of laser being used. The pump excites the atoms or molecules within the gain medium, raising them to a higher energy state.
3. Population inversion:
When the number of atoms or molecules in the higher energy state exceeds those in the lower energy state, a condition called population inversion is achieved. This is a crucial requirement for laser action, as it allows for the amplification of light.
4. Optical cavity:
The gain medium is placed within an optical cavity, which consists of a set of mirrors, one of which is partially reflective. These mirrors are aligned parallel to each other, creating a resonant chamber for the light to bounce back and forth.
5. Stimulated emission:
As the light travels through the gain medium, it interacts with the excited atoms or molecules, causing them to release their stored energy in the form of additional coherent light through a process called stimulated emission. This newly emitted light is in phase with the original light, which amplifies the light intensity.
6. Continuous amplification:
The light continuously bounces back and forth between the mirrors within the optical cavity, passing through the gain medium multiple times. Each pass results in further amplification of the light due to stimulated emission.
7. High-intensity laser beam:
The partially reflective mirror in the optical cavity allows a small portion of the amplified light to escape. This escaping light forms a highly concentrated, high-intensity laser beam that can be directed and focused onto a specific target for various applications, such as cutting, laser engraving, or welding.
The process of amplifying laser light to create a high-intensity beam is a delicate balance of controlling the gain medium, energy pump, optical cavity, and population inversion to achieve the desired output power and beam quality.
Accessories in the Laser Cutting Process
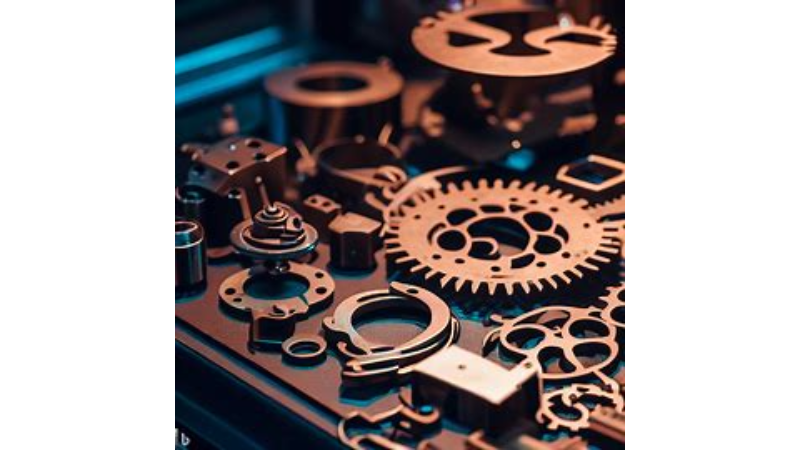
Several key accessories are essential in the laser cutting process, ensuring optimal performance, precision, and safety. Some of the main accessories for fiber laser, include:
1. Cutting head:
The cutting head is a vital component of the laser cutting machine, as it houses the focusing lens and the cutting nozzle. It directs the laser beam onto the material and maintains the correct focus.
The cutting head is usually mounted on a motion system, such as a gantry or a robotic arm, allowing it to move along the cutting path per the design requirements. High-quality cutting heads often include features like automatic focus adjustment and crash protection.
2. Protective lens:
The protective lens of fiber laser cutters, also known as the cover glass or coverslip, is a crucial accessory in the cutting head. It is a barrier between the focusing and cutting areas, shielding the lens from debris, dust, and molten material generated during the cutting process.
The protective lens is typically made of high-quality, durable material, such as fused silica or quartz, which can withstand high temperatures and provide excellent optical transparency. Regular cleaning and inspection of the protective lens are essential to maintain cutting performance and prolong the life of the focusing lens.
3. Cutting nozzle:
The cutting nozzle is an essential component of the cutting head that directs the laser beam and the assist gas onto the cut material. The nozzle’s shape and size can significantly impact the cutting process, as it influences the gas flow, the stability of the laser beam, and the kerf width.
Cutting nozzles come in various designs and sizes, each suited for specific materials, thicknesses, and cutting applications. Choosing the right cutting nozzle and maintaining it properly is crucial for achieving optimal laser cut quality, speed, and efficiency.
4. Assist gas system:
The assist gas system supplies the cutting nozzle with pressurized gas, such as oxygen, nitrogen, or compressed air. This gas helps remove molten material from the cutting area, prevents oxidation, and cools the material. The assist gas system typically includes gas cylinders, regulators, hoses, and flow control devices.
5. Chiller:
High-power laser cutting machines generate significant heat, which must be efficiently dissipated to maintain the system’s performance and longevity. A chiller is a cooling system that circulates a coolant through the laser components, such as the laser source and optics, to remove excess heat and maintain a stable operating temperature.
6. Fume extraction system:
Laser cutting can produce harmful fumes, smoke, and particulates, especially when cutting plastics or metals coated with paint or other chemicals. A fume extraction system, consisting of a fan, filters, and ductwork, helps capture and remove these pollutants from the cutting area, ensuring a safe and clean working environment.
These accessories play a critical role in the laser cutting process. They must be chosen, installed, and maintained with care to ensure the best possible laser cutting project results and prolong the life of the laser cutting machine.
Maximizing Output: Tips and Tricks for Sheet Fabrication
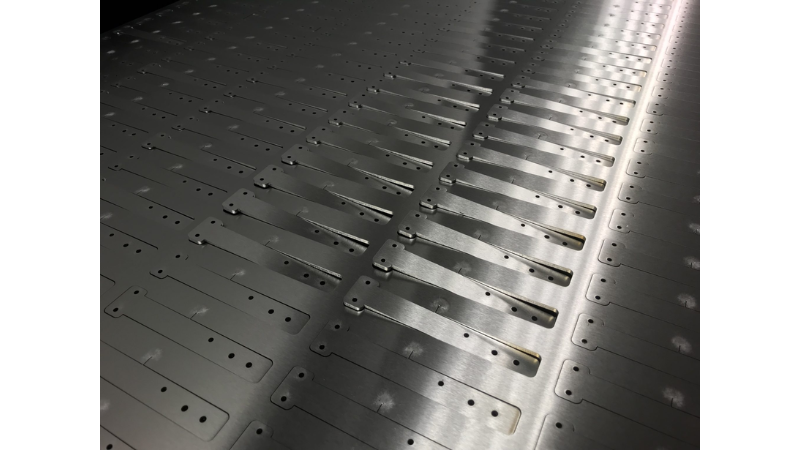
Optimizing various aspects of the process is essential to maximize output in laser cutting. Here are some tips and tricks for achieving this:
Tip 1: Improve good cutting quality
Achieving good cutting quality requires finding the right balance between laser power and cutting speed settings. High laser power may cause excessive material melting and heat-affected zones, while low power may result in incomplete cuts.
Similarly, a high cutting speed can compromise precision, while a low speed may cause heat buildup. To ensure clean, precise cuts, perform tests to determine the optimal settings for the same material thickness and thickness you’re working with.
Tip 2: Maximize production speed
Choose the right cutting parameters and a high-quality motion system to maximize production speed while maintaining high dimensional tolerances. Opt for advanced laser cutting machines with features like automatic focus adjustment and accelerations control.
Additionally, nesting software can help optimize cutting patterns and paths, reducing idle time and improving overall efficiency.
Tip 3: Minimize surface roughness
Surface roughness can be minimized by using proper laser power settings and assist gas, such as compressed air or nitrogen. High laser power can cause excessive melting, leading to rough edges, while low power may over-melt metals resulting in chipping.
Similarly, choosing the right assist gas and pressure helps remove molten material, prevents oxidation, and cools the material, ensuring smoother cuts.
Tip 4: Achieve desired shapes and sharp corners
To create intricate shapes with parallel lines and sharp corners, program the beam path accurately and adjust the cutting parameters, such as power, speed, and gas pressure, accordingly. You may need to reduce cutting speed and increase laser power momentarily for straight lines and sharp corners to ensure a precise cut.
Tip 5: Minimize material waste
To minimize material waste and reduce manufacturing costs, utilize nesting software to optimize the arrangement of parts on the material for sheet metal manufacturing used, maximizing material usage and minimizing waste.
Additionally, maintaining the cutting equipment, such as the cutting head, lenses, and nozzles, ensures consistent cutting quality and reduces the likelihood of scrap parts, further reducing waste and manufacturing costs for sheet metals.
How Can Laser Cutting Machines Create Highly Precise Parts?
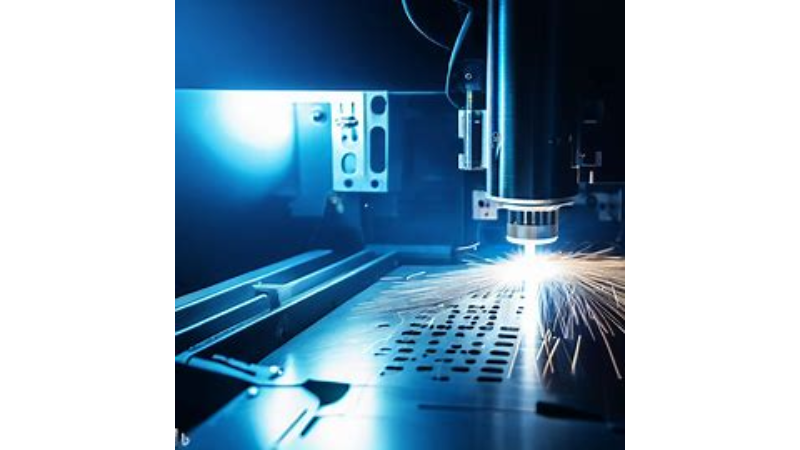
Laser cutting machines can create precise parts by utilizing the machine tools following features and capabilities:
1. High beam quality:
Laser cutting machines produce a focused, high-intensity laser beam with excellent quality. This enables the various laser cutters to make clean, precise cuts with minimal kerf width and heat-affected zones, resulting in high-quality parts with tight tolerances.
2. Non-contact cutting process:
As a non-contact cutting method, laser cutting eliminates the need for physical tooling, reducing the risk of material deformation or damage. This ensures the parts maintain their dimensional accuracy and surface finish.
3. Accurate motion control:
Laser cutting machines often use advanced motion control systems, such as CNC controllers, linear motors, or servo drives, to guide the cutting head along the desired cutting path with high precision and repeatability.
4. Programmable cutting parameters:
Laser cutting machines allow operators to program and adjust cutting parameters, such as laser power, cutting speed, and assist gas pressure, to optimize the cutting process for different materials and thicknesses. This ensures optimal cutting quality and precision for each specific application.
5. Advanced software:
Laser cutting machines use specialized software to convert digital designs into machine-readable formats, ensuring accurate reproduction of the intended design. The software can also optimize cutting paths and nest multiple parts to minimize material waste and improve production efficiency.
6. Versatility:
Laser cutting machines can handle various materials, including metals, plastics, and composites, with varying thicknesses and properties. This versatility enables the creation of precise parts for different applications and industries.
7. Automation capabilities:
Many laser cutting machines are compatible with automated material handling systems, such as loading and unloading devices, conveyors, and pallet changers. These systems improve the laser cutting process’s productivity, precision, and consistency.
By combining these features and capabilities, laser cutting machines can create highly precise parts with intricate shapes, fine details, and tight tolerances, making them an ideal solution for various industries and applications.
Applications of Finished Metal Parts in the Manufacturing Process:
The applications of finished metal parts refer to the different industries and manufacturing processes that utilize these parts created using laser cutting machines. Some of these applications include:
1. Automotive industry:
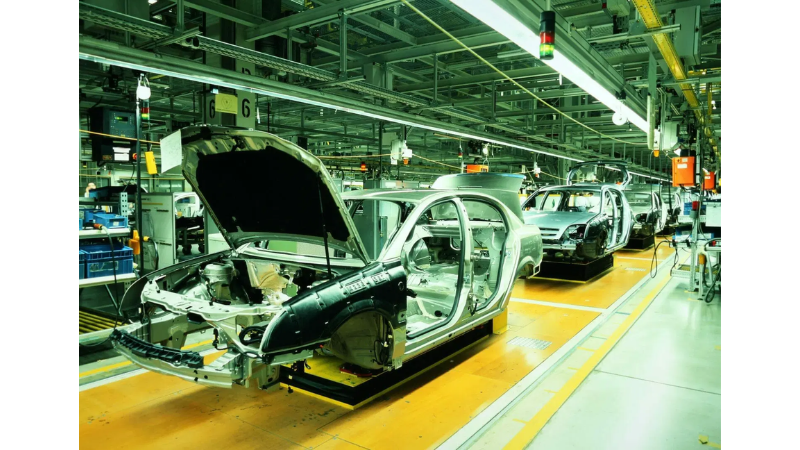
Finished metal parts are extensively used in the automotive industry for manufacturing various components, such as engine parts, suspension systems, exhaust systems, brackets, and body panels. These parts are critical for vehicle performance, safety, and aesthetics.
2. Aviation and Aerospace industry:
In the aviation and aerospace industry, finished metal parts are used to produce components for aircraft, satellites, and rockets. These components include structural elements, engine parts, avionics enclosures, and landing gear. The high precision and reliability required in aerospace applications make the use of finished metal parts essential.
3. Electronics industry:
Metal parts are used in the electronics industry for manufacturing heat sinks, shielding covers, enclosures, and chassis for various electronic devices. These components provide thermal management, protection, and mechanical support to electronic components, ensuring their proper functioning and longevity.
4. Medical industry:
The medical device industry relies on laser cutting finished metal parts for manufacturing surgical instruments, implants, diagnostic equipment, and other medical devices. These components require high precision and biocompatibility to ensure the safety and effectiveness of medical treatments.
5. Construction industry:
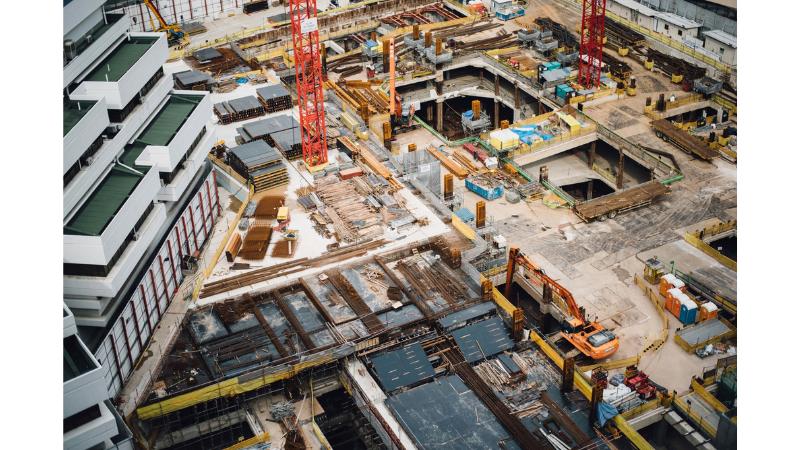
Finished metal parts are used in the construction industry for manufacturing structural elements, such as beams, columns, and fasteners, as well as architectural elements like railings, facades, and decorative panels. These components provide strength, stability, and aesthetics to buildings and infrastructure.
6. Energy industry:
Metal parts play a crucial role in the energy sector, where they are used to manufacture components for power generation and distribution systems, such as turbines, transformers, and electrical enclosures. They are also employed in renewable energy systems, like solar panels and wind turbines.
7. Consumer goods:
Finished metal parts are used to produce a wide range of consumer goods, including appliances, furniture, tools, and sports equipment. These components provide functionality, durability, surface quality, and aesthetics to our daily products.
8. Industrial machinery:
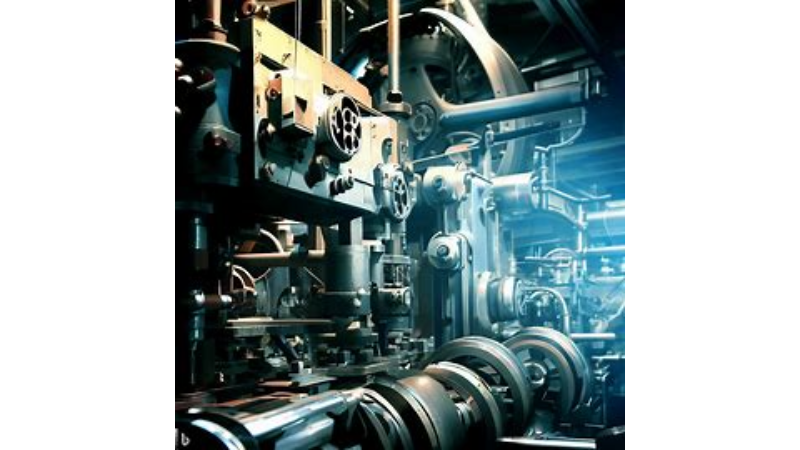
Metal parts are essential for manufacturing various industrial machines and equipment used in manufacturing, processing, and other material handling processes. Examples of metal materials include gears, shafts, bearings, and structural elements.
These industrial applications demonstrate the importance of finished metal parts in manufacturing across different industries. Their versatility, strength, and durability make them indispensable components in countless products and systems.
Benefits of Laser Cutting over Other Cutting Methods:
Laser cutting has several benefits over other cutting methods, including:
1. Laser cutting vs. plasma cutting:
Compared to plasma cutting, laser cutting offers higher precision and cleaner cuts. It also allows for cutting a wider range of materials, including metals, plastics, and wood. Additionally, laser cutting produces minimal waste and reduces the need for post-cutting processing.
2. Laser cutting vs. band saws:
Laser cutting is much faster and more accurate than band saws. It also allows for cutting a wider range of materials, including harder and thicker materials. With laser cutting, there is no need to change blades or deal with burrs, resulting in less downtime and increased efficiency.
3. Laser cutting vs. press brakes:
Laser cutting offers several advantages over press brakes, including higher precision, faster cutting speed, and the ability to cut complex shapes and patterns.
It also eliminates the need for expensive tooling and reduces the risk of material damage or deformation due to excessive bending. Additionally, laser cutting can produce high-quality parts with minimal waste, reducing overall manufacturing costs.
Best Practices for Laser Cutting Machines
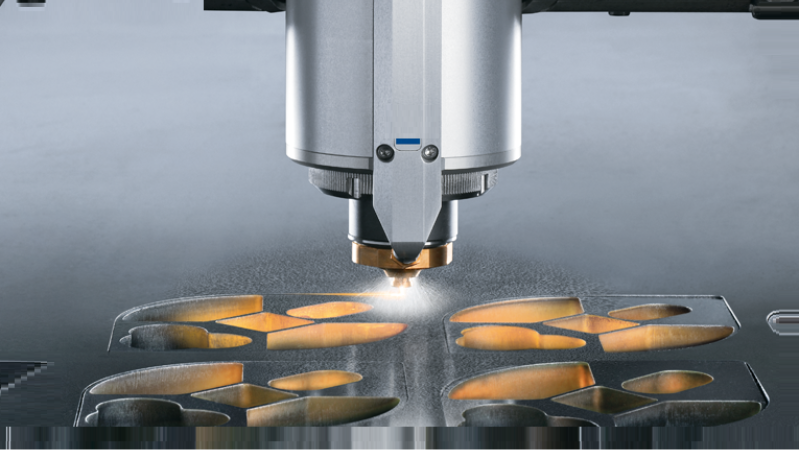
1. Regular maintenance and cleaning:
Laser cutting machines require regular maintenance to operate at their full potential. This includes cleaning the optics, replacing worn components, and lubricating the machine. Regular maintenance helps to ensure that the laser cutting machine is operating at its optimal performance level and can help to reduce downtime and repair costs.
2. Operator Training and Safety:
Laser cutting machines are powerful tools that require proper training and safety measures to be taken. Operators must be trained on the proper use of the machine, including safety procedures, troubleshooting, and maintenance. Proper training can help reduce the risk of accidents and ensure the laser machine is being used to its full potential.
3. Quality Control and Inspection:
Laser cutting machines can produce highly precise parts in large quantities, but quality control and inspection are essential to ensure that the parts meet the required specifications. This includes dimensional accuracy, surface finish, and edge sharpness.
Quality control and inspection can help to identify and correct any issues before the parts are sent to the next stage of the manufacturing process.
4. Data Management and Production Tracking:
Data management and production tracking are critical for managing the production process efficiently. This includes material tracking, inventory management, and production scheduling.
Data management and production tracking can help to ensure that the laser cutting machine is being used to its full potential and can help to reduce waste and production costs.
Conclusion
In conclusion, laser cutting technology transforms sheet fabrication by unlocking maximum output. Its precision, speed, and versatility make it a go-to solution for many industries.
By implementing the best practices for laser cutting machines, such as regular maintenance and cleaning, operator training and safety, quality control and inspection, and data management and production tracking, you can optimize the performance of your laser cutting machines and improve your overall production efficiency.
With laser cutting technology, you can achieve highly precise cuts, minimize waste, and maximize your output while reducing your manufacturing costs. It’s clear that laser cutting is the future of metal sheet and fabrication, and by embracing this technology, you can stay ahead of the curve in today’s fast-paced market.
Revolutionize Your Sheet Fabrication Today: Request an Instant Quote from Baison Laser!
Transform the way you approach your entire sheet metal laser fabrication with Baison Laser. Unlock maximum output and precision with our state-of-the-art laser cutting technology. Request an instant quote today and revolutionize your production process.
Say goodbye to inefficiencies and hello to optimal results. Let’s make your vision a reality with Baison Laser!