Laser cut kerf refers to the width of material removed during the laser cutting process. Understanding the laser incision can improve your laser cutting experience on the laser machine and is crucial for achieving accurate and detailed fabrication. In this guide, you can understand how laser kerf works and how to account for it when necessary.
Importance of Knowing Laser Cut Kerf
In laser cutting methods, kerf, or the width of the laser beam as it cuts through the material, replaces the saw blade of a saw with a laser beam. Understanding the laser cut kerf plays a significant role in achieving precise cuts. This knowledge is crucial in industries where precision is paramount, such as aerospace or medical device manufacturing.
1. Tight Tolerances
Knowing laser cut kerf is necessary for designing parts with proper dimensions. Understanding laser cut kerf ensures tight tolerances and avoids errors in production. It allows for efficient material utilization, reducing waste and cost.
Knowledge of laser cutting kerf, the width of the cut made by the laser beam from the laser head, enables the optimization of designs for specific materials using the laser cutting technique. This technique involves using a laser machine that directs a laser beam onto the surface of a material to create precise cuts.
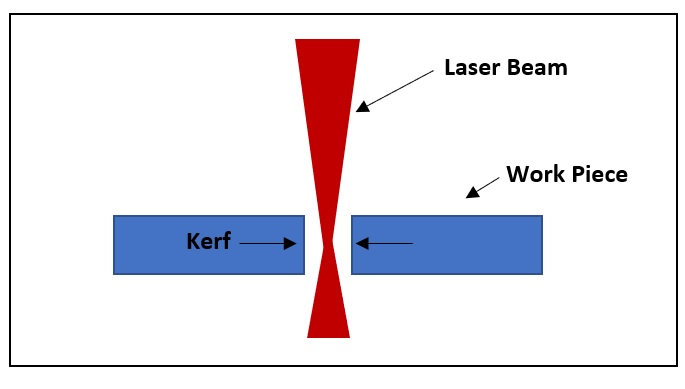
Tight tolerances are essential to ensure the functionality and performance of the final product. By considering the machine’s laser cut kerf and surface, manufacturers can avoid costly errors caused by parts that do not fit properly or meet the required specifications. The processing of the machine ensures that the laser tube and focus position are accurate for precise cutting.
2. Efficient Material Utilization
Efficient material utilization is another advantage of knowing the laser cut kerf. By accounting for the width of the laser beam during cutting, designers can optimize their layouts to minimize waste.
This optimization is crucial in ensuring that the machine accurately processes the materials and achieves the desired focus position on the surface. This not only reduces material costs but also contributes to sustainability efforts by minimizing environmental impact.
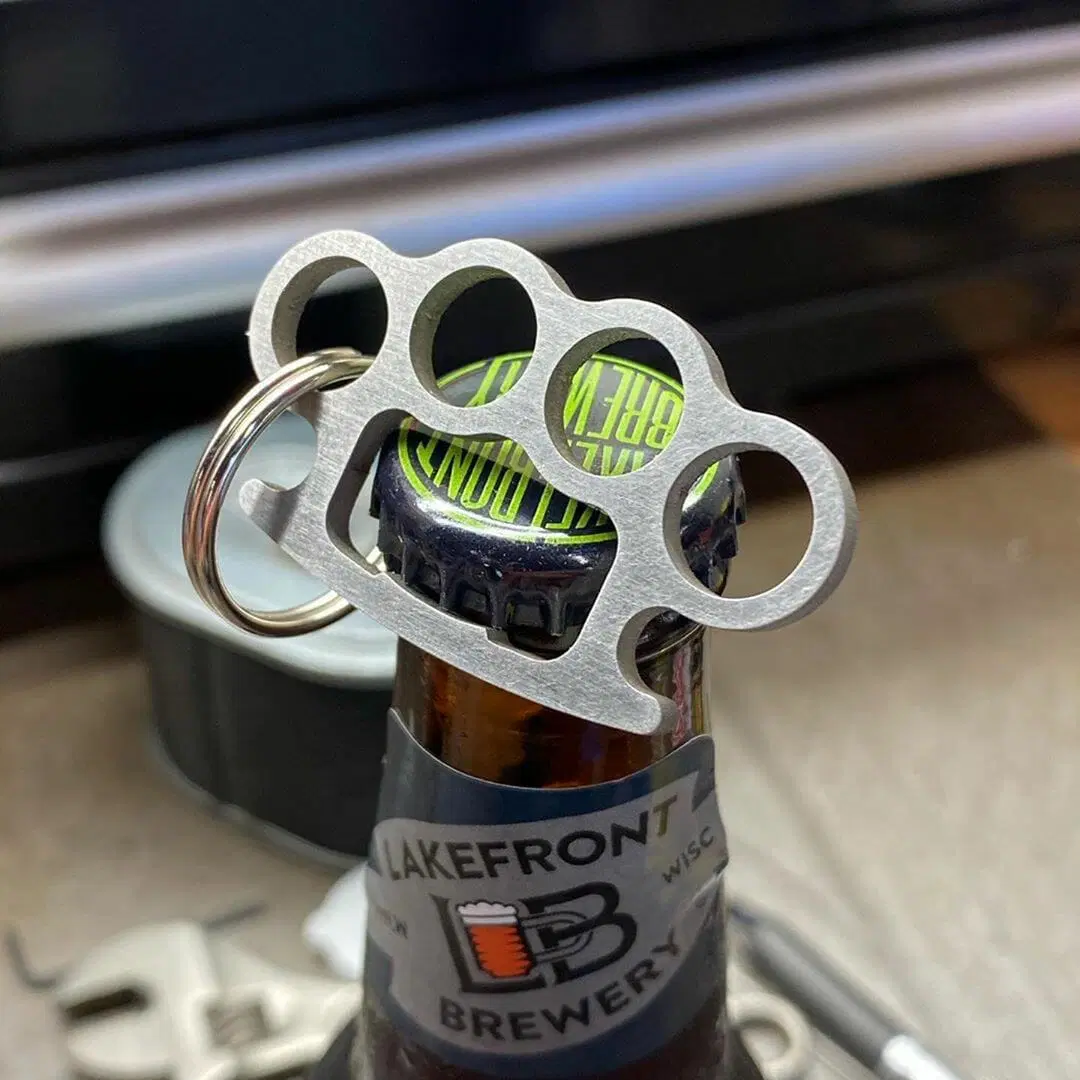
3. Tailor Designs
Furthermore, understanding how different materials interact with lasers allows designers to tailor their designs accordingly. Each material has its own unique characteristics, including variations in laser kerf width. Being aware of these differences enables designers to optimize their designs for specific materials, ensuring optimal results.
Do You Have Any Questions?
Let Us Solve Your Problem
Kerf Width and Material Types
Different materials have varying kerf widths due to their composition. (You may want to know more about the details of laser cutting kerf of different materials) Dense materials may require higher power lasers, resulting in wider kerfs. Adjustments are necessary when working with different material types to achieve desired results.
- Metals: Metal types, conductivity, and reflectivity impact kerf width. High thermal conductivity metals like copper might have narrower kerfs, while stainless steel could lead to wider kerfs due to its properties.
- Plastics: Plastic type, thickness, and melting points matter. Low melting point plastics or those prone to charring can result in wider kerfs, while high melting point thermoplastics might have narrower ones.
- Woods: Wood density, resin content, and grain patterns affect kerf width. Denser woods tend to have narrower kerfs, while those with complex grain patterns or resin content can lead to wider kerfs.
- Ceramics and Composites: Brittle ceramics usually mean narrower kerfs due to resistance to melting. Composites might have wider kerfs due to varied layer responses to laser energy.
- Coatings: Materials with coatings can alter how they absorb laser energy, impacting kerf width.
Understanding the relationship between material types and kerf widths is crucial for achieving accurate cuts in laser cuts. By considering the unique characteristics of each material, such as density and melting point, operators can make appropriate adjustments to ensure precise outcomes.
Comparing Laser Cutting Kerf with Other Methods
Let’s simplify the comparison of laser cutting kerf with other cutting methods:
- Laser Cutting: Uses focused laser beams from the laser head to create cuts. Offers precise, clean cuts with minimal material waste.
- Traditional Cutting: Employs tools like saws or blades. Generally produces wider kerfs and can lead to more material waste.
- Waterjet Cutting: Utilizes high-pressure water jets. Can result in wider kerfs and might require more post-cutting cleanup.
- Plasma Cutting: Involves ionized gas to cut. This can lead to wider kerfs and may require more material cleanup.
Laser cutting stands out for its precision and efficiency, resulting in narrower kerfs and less waste compared to other methods.
Factors Affecting Kerf Width
The width of the kerf produced during laser cutting is influenced by several factors. Let’s take a look at each of them:
- The power level of the laser: The intensity of the laser beam has a direct effect on the width of the kerf. Higher power levels tend to result in larger kerf, while lower power levels produce narrower ones. To learn more about the parameters of the kerf, click here.
- Focusing optics: The focal length and diameter of the focusing optics used in laser systems have an impact on the size and shape of the beam. This, in turn, affects the width of the kerf produced during cutting. Optics with different specifications can be employed to adjust and control the desired kerf value.
- Material thickness: The thickness of the material being cut also plays a role in determining the final width of the kerf. Thicker materials generally require more energy and wider beams to achieve clean cuts, resulting in wider kerfs.
- Laser speed: The speed at which the laser moves across the material affects how much energy is delivered per unit length. Faster speeds may result in narrower kerfs, while slower speeds can lead to wider ones.
By considering these factors – power level, material thickness, focusing optics, and laser speed – you can better understand and control the width of your laser cut kerf.
Do You Have Any Questions?
Let Us Solve Your Problem
Compensating for Kerf Width
Now that you understand the importance of knowing laser cut kerf and how it varies with different materials, let’s talk about compensating for kerf width. When laser cutting, it’s crucial to account for the material that will be removed due to the kerf. This ensures that your final product matches the intended dimensions.
I. Kerf Offset in Design
- Adjusting Dimensions: Increase or decrease the dimensions of your design by the kerf width to achieve the desired finished size. This compensates for the material that will be removed during cutting.
- Internal and External Features: For parts with internal holes or external contours, adjust their dimensions based on the kerf width to ensure proper fits and alignments.
- Test Cuts: Perform test cuts on similar materials to determine the actual kerf width for your specific setup. This helps you fine-tune the kerf offset for accurate cuts.
II. Compensated Parts
- Software Solutions: Some laser cutting software allows for automatic kerf compensation. These programs calculate and adjust the design dimensions to account for the kerf width, simplifying the process.
- Material Consideration: Different materials can have varying kerf widths. Adjust your design based on the specific material you’re using to achieve accurate results. You can get a good pair of calipers for measuring the actual kerf amount.
- Prototyping: Create prototypes and test pieces to validate the kerf compensation before proceeding with full production. This ensures that your parts fit together as intended.
By incorporating these methods, you can effectively compensate for the kerf width, ensuring that your laser-cut parts match your design specifications accurately and consistently.
FAQs
1. What materials are suitable for laser cutting?
Laser cutting is compatible with a wide range of materials such as wood, acrylic, leather, fabric, paper, and even certain metals like stainless steel and aluminum. However, keep in mind that each material has its own unique properties and may require specific settings or precautions during the laser cutting process.
2. Can I adjust the kerf width myself?
While adjusting kerf width may seem straightforward by modifying design files or settings on a personal laser cutter if available, it’s recommended to consult professionals or experienced service providers who can guide you through this process accurately. They possess knowledge about different materials and their corresponding kerf widths to ensure precise cuts.
3. How does kerf width affect my project?
Kerf width directly impacts dimensional accuracy in your projects. Ignoring or miscalculating it may result in parts not fitting together correctly or a final product that doesn’t meet your specifications. Understanding and accounting for kerf width is crucial to achieving the desired outcome.
4. Are there any techniques to minimize kerf width?
While it’s not possible to completely eliminate kerf width, certain techniques can help minimize its impact. Using a smaller focal length lens, reducing the laser power, or employing multiple passes with lower power settings can result in narrower kerf widths. However, these techniques may vary depending on the material being cut and should be tested beforehand.
Do You Have Any Questions?
Let Us Solve Your Problem
Conclusion
In the world of precision manufacturing, understanding the intricacies of laser cut kerf is paramount. The width of the cut may seem like a minor detail, but it significantly impacts the accuracy and fit of your laser-cut parts.
Laser cutting’s ability to deliver intricate, clean cuts is undeniable, and by mastering the art of kerf management, you unlock its full potential. Remember, no matter what method you take, the goal remains the same: to seamlessly translate your designs into precisely fabricated parts.
Unlock Precision with Baison Laser: Shape Innovation Today!
Now that you understand the importance of accurate laser cutting kerf, are you ready to increase the level of precision manufacturing with a quality laser cutting machine? Look no further than Baison Laser, your trusted partner in laser technology.
Our cutting-edge solutions and expertise ensure that you navigate the world of laser cutting with confidence and excellence. Contact us to explore how we can take your projects to the next level. Let’s shape innovation together!