This article explores how IoT is changing the laser-cutting world, its risks, and upcoming trends that will help businesses succeed. Let’s get started.
What is the Internet of Things (IoT)?
Internet of Things (IoT) is an umbrella term for a system of devices that can be connected to the Internet and exchange real-time data over a wireless network. Your everyday smart thermostats, Wi-Fi cameras, smart washing machines, and TVs are typical examples of IoT-enabled devices.
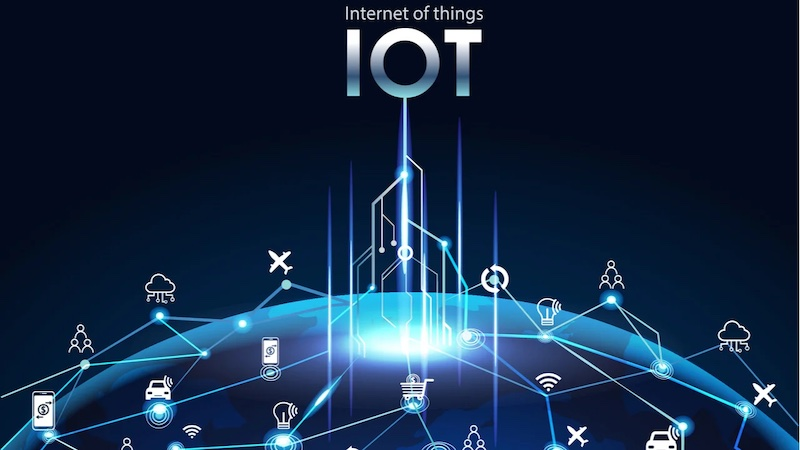
IoT is the backbone of the Fourth Industrial Revolution (Industry 4.0), and due to its unique applications in the manufacturing industry, it has become its own field called the Industrial Internet of Things (IIoT).
The manufacturing industry is experiencing rapid improvements in efficiency, speed, and accuracy and an enhanced capacity to handle complex tasks that previously took eons with traditional methods. Owing to this, the leading technology firm Accenture estimates that the IIoT market will soar to US$14.2 trillion in the coming years.
How Is The Internet Of Things (IoT) Changing Laser Cutting?
Laser cutting is already the most advanced manufacturing process in modern times, and with the combination of IoT and artificial intelligence (AI), it has taken a huge leap in terms of performance and profitability. The key components of IoT-enabled laser cutting systems that make all the magic happen are Sensors, Connectivity to a centralized system, and Data analytics.
IoT-based laser technology can process real-time data and transfer it over a cloud system, greatly optimizing the cutting process, enabling preventive maintenance measures, facilitating communication with multiple machines, and providing the possibility of remote access.
Do You Have Any Questions?
Let Us Solve Your Problem
Integration of IoT and Laser Cutting
Integration of IoT into modern fiber laser cutting machines has made them so efficient that the CO2 machines from 10 years ago feel like old horses. Let’s discuss the key benefits that IoT brings to laser cutting manufacturing in detail.
1. Real-time Data Acquisition
Through IoT, the machine’s operator can observe cutting parameters such as laser light intensity, laser power, lens health, cutting speed, temperatures, etc., in real-time. This data can also be uploaded to the cloud, allowing workers to access it remotely.
If the cut is not up to the mark, the IoT-enabled laser system gives timely warnings, helping the operator make the necessary adjustments to cutting parameters. Additionally, remote data access greatly improves the safety of the work environment, as workers don’t need to be in the same room as the machine.
IoT paired with machine learning also facilitates better material selection for laser cutting. In 2021, Mustafa Doga Dogan, a PhD candidate, and his team at MIT CSAIL developed SensiCut, a device that can differentiate between dozens of similar-looking materials in an instance.
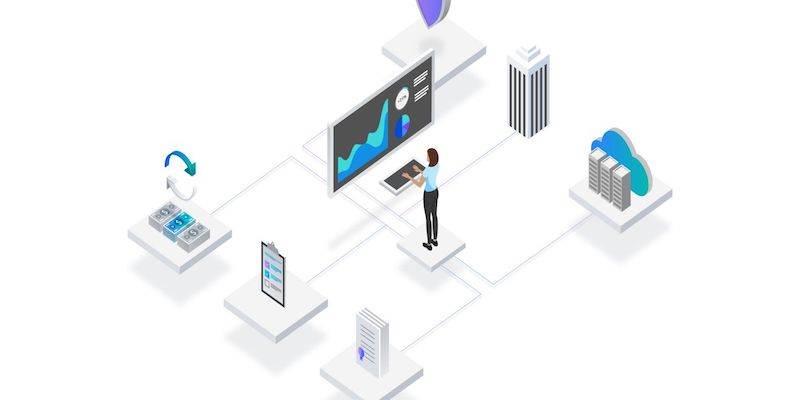
2. Predictive and Preventive Maintenance
Real-time data collection also aids in monitoring machine health. In many cases, machines malfunction well before scheduled maintenance, so timely monitoring via IoT systems warns the operator long before reaching the point of no return.
Also, IoT helps cut back downtime and allows scheduling maintenance on off-peak hours, greatly improving profitability. It’s not an understatement that IoT and AI have completely transformed conventional practices through smart predictive maintenance.
3. Optimizing Cuts
New smart laser cutting machines have cameras and microphones that monitor cutting-edge quality in real-time. In earlier days, if the operator observed any anomaly in the cut quality, they would have to stop the machine and fine-tune the issue. However, with IoT, the system listens and watches the laser cutting process, optimizing parameters automatically to improve the edge quality.
The IoT-integrated laser cutting system can now determine more than 250 cut conditions through machine learning. That’s like the crux of decades of human experience and intuition.
4. Quality Control
IoT also helps tremendously with quality control of the post-cutting process. The smart control gathers all the information about the edge quality along with the process parameters that lead to this end quality. With data analytics and AI, manufacturers can accurately determine the leading cause of poor cut quality.
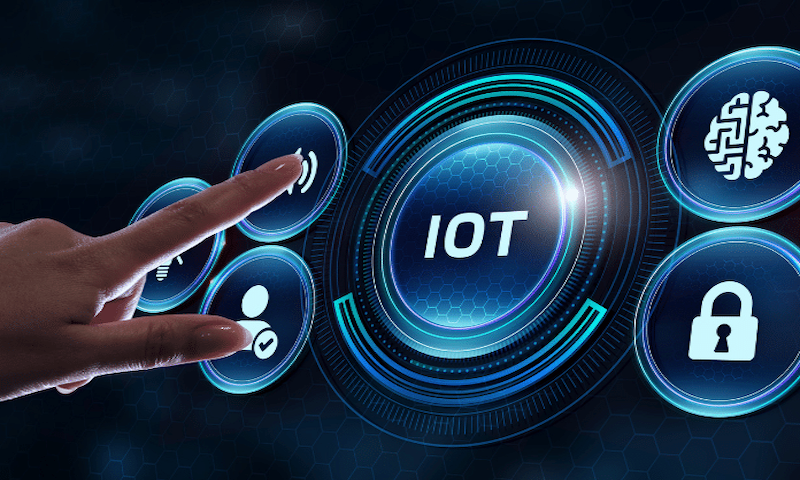
Moreover, the system optimizes itself to prevent future mishaps and becomes smarter with every process. Manufacturers incorporating IoT-supported laser cutting machines generate higher profits because of this.
The inclusion of smart tech in the laser cutting industry also opens doors for a more efficient Lean Manufacturing ecosystem that focuses on minimal waste and high productivity.
5. Improved Automation
Automation in CNC and Laser cutting machines is nothing new. It dramatically improves the efficiency of the cutting process but sacrifices the adaptability of the machine. However, with IIoT-supported systems, real-time data acquisition helps guide the automatic process and adjust it to the current scenario, just like any human engineer would do, making the process infinitesimally smarter.
Additionally, multiple IIoT-supported machines can connect with each other and communicate over a wireless network, reducing bottlenecks and improving the automation process in the manufacturing sector.
6. Improved Supply Chain
A smooth-running supply chain is the lifeline of any laser-cutting company. However, disruptions and inefficiencies are inevitable as the scale of work becomes bigger. Thanks to industrial IoT, almost all analog devices can communicate easily, improving the supply chain and inventory. For example, ordering new raw materials promptly or accessing real-time data on when a product will be ready to ship.
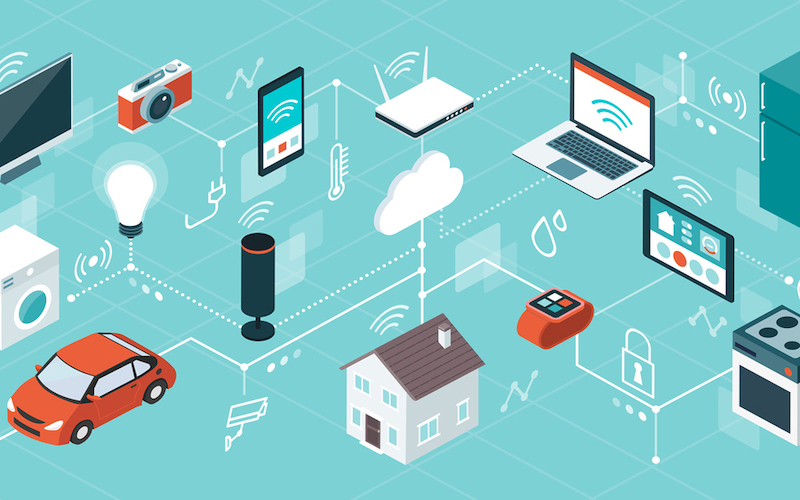
All the information can easily be transferred through Wi-Fi ( or Ethernet)and mobile networks and is readily available in your hands. Additionally, industry experts can generate greater insights with this holistic database.
7. Integration of AI
IIoT complements artificial intelligence (AI), paving the way for the industrial revolution. With the help of AI, the complex physical processes behind laser cutting can be thoroughly studied. IoT, on the other hand, collects real-time data for AI to train with.
Researchers at the University of Tokyo’s Institute for Solid State Physics have developed a deep learning algorithm called Meister Data Generator, which gathers high-quality data on manufacturing processes. This advancement is expected to significantly improve modern-day machines’ efficiency, accuracy, and precision.
Do You Have Any Questions?
Let Us Solve Your Problem
The Benefits of Adding IoT to Laser Cutting
IoT brings tremendous benefits to the industry and is becoming the go-to choice of manufacturers. The advantages outweigh the expensive equipment cost, resulting in greater overall profits. Here is how standard laser-cutting machines differ from IoT-supported ones.
Areas | Traditional | IoT Supported |
---|
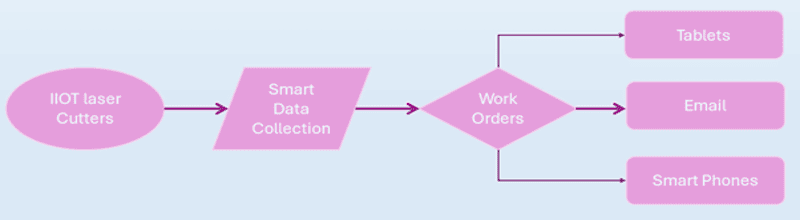
Challenges and Considerations of Industrial IoT
Industrial Internet of Things is truly a game-changer in modern robotic laser cutting. However, it also brings specific challenges to smart manufacturing. Let’s discuss the negatives of IoT and how researchers are working to remedy them.
1. Cybersecurity
The vast infrastructure of interconnected machines through a wireless network makes the system prone to cyber attacks from multiple avenues. There are security concerns regarding data privacy and operations.
As a result, active research is ongoing to revamp the IIoT system with the latest security measures. Moreover, blockchain technology is seen as the answer to fortifying the integrity of IIoT systems.
2. Connectivity
IoT requires internet connectivity all the time, but in real life, loss of connection is bound to happen either due to a power outage or maintenance break. This disrupts the flow of information and may cause problems.
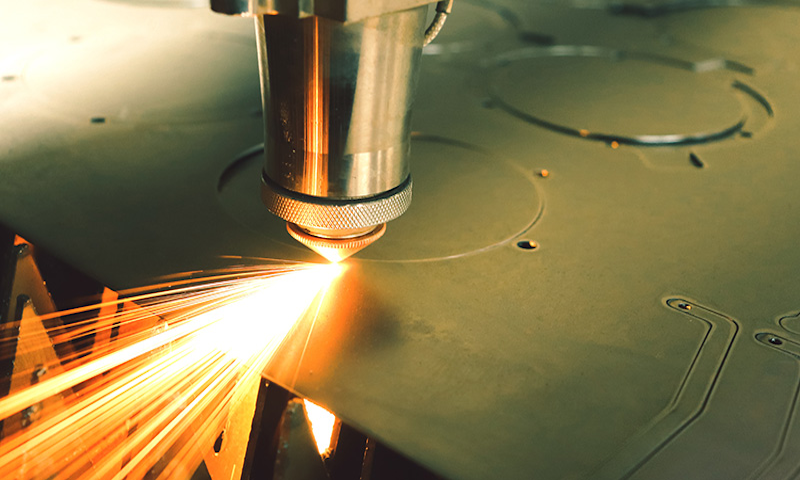
The frequent interruptions in connectivity can result in the transmission of erroneous data through various machines, compromising the safety of machines (and people) in the network. That’s why it is vital to set up a system with foolproof connectivity to prevent unfortunate incidents.
3. Data Surge
Industrial IoT data networks operate differently compared to consumer-based IoT devices in our homes. The scale of data collection is exponentially larger, expanding over a vast network of IIoT-supported machines, sometimes spanning across various manufacturing plants. This may lead to uncertainty in decision-making and data processing.
To address this, a thorough understanding of the company’s objectives is needed to filter relevant data from the rest. Companies seek robust data validation and analytics to counter this.
Do You Have Any Questions?
Let Us Solve Your Problem
How to Choose Laser Cutters In The Era Of Industry 4.0?
Consider the following things before making a decision to purchase IoT-supported laser-cutting machines:
1. Assess Integration Capabilities
Make sure the laser cutting machine offers seamless integration with your current work equipment and software. Compatibility with industry-standard protocols like OPC UA (Open Platform Communications Unified Architecture) will facilitate fluid data transfer.
2. Evaluate Connectivity Options
Not all IoT machines are the same. Choose the one that features remote monitoring, diagnostics, and maintenance so that you get real-time insights into machine performance and productivity.
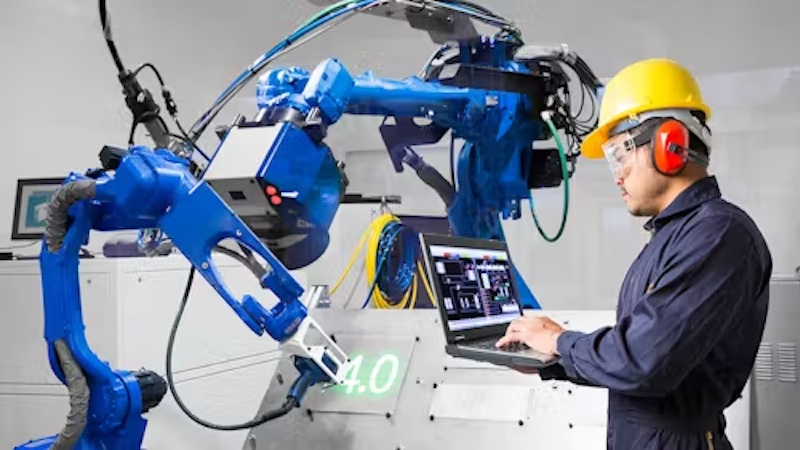
3. Seek Scalability and Flexibility
Choose the laser cutter that offers scalability and adaptability to expand with the latest industry 4.0 trends. IoT-supported laser cutters that can adopt future upgrades are the best choice.
4. Cybersecurity Measures
Ensure you get an IIoT-enabled laser cutter backed by robust cybersecurity measures, such as protection of sensitive data, restriction of unauthorized access and cyber-attacks. This is one of those things that demand zero compromise on your part.
The Future of IoT in Laser Cutting
Innovation in industrial IoT in laser cutting technology is just getting started. Recently, a Chinese company, Goodix, developed a new and improved Sensing & Connectivity Solution that combines cutting-edge laser drivers and image sensors capable of precisely measuring depths and capturing movements and gestures.
Laser cutters, with the help of IoT and AI, will become better at intelligent maintenance, progress tracking, and remote access, which will help businesses increase their effectiveness manifold. Industry 4.0 will also help manufacturers with sustainable mass production.
Do You Have Any Questions?
Let Us Solve Your Problem
Conclusion
We’ve delved deep into the revolutionary trends of IIoT and AI-supported laser cutting machines and how the future is brimming with technological advancement. However, such IoT-enabled smart machines are still relatively rare in the market, and proper consideration is needed before any business explores its benefits. We are sure the above guide will help steer you in the right direction.
Upgrade to Baison Laser for Superior Laser Cutting!
Baison Laser is a market-leading Chinese fiber laser cutting machine manufacturer catering to clients worldwide across various industries. Our machines are constructed using premium-quality components under the supervision of industry experts. With two decades of experience in laser processing and intensive R&D, we produce durable and highly efficient CO2 and fiber laser-cutting machines.
At Baison Laser, we offer customized solutions to our customers at competitive prices, ensuring timely delivery. Take advantage of our FREE sample proofing or request a FREE application evaluation for your project today. Contact our expert helpline, available 24/7, to propel your business to new heights.