By discussing the top 10 benefits, we aim to showcase how magnetic chucks increase productivity and enhance precision in various metalworking applications. Let’s get started!
What Are Magnetic Chucks in Cutting?
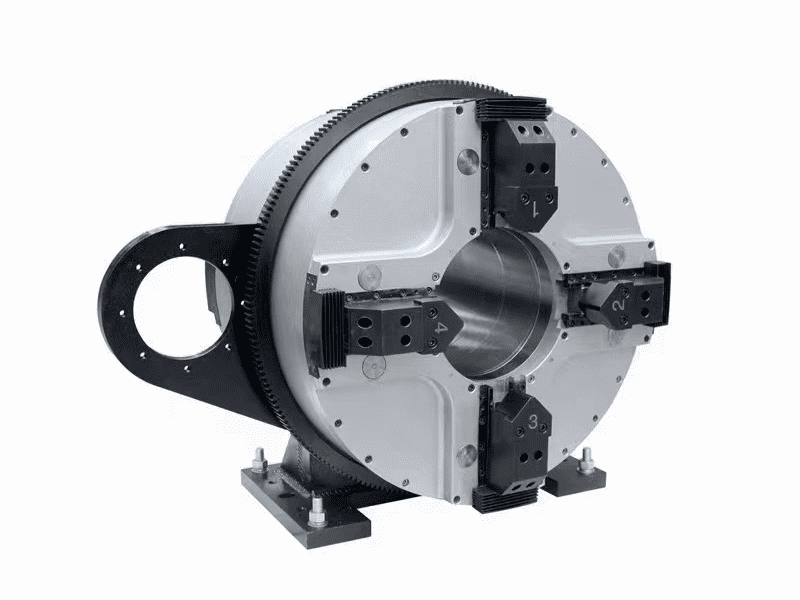
Magnetic chucks are specialized tools used in cutting operations to secure workpieces firmly in place using a magnetic force. They come in different forms, such as permanent magnetic chucks and electromagnetic chucks, each serving a unique purpose depending on the machining process involved. This versatile nature makes them suitable for a range of metalworking operations.
The importance of magnetic chucks in cutting cannot be overstated. They enhance productivity by providing a quicker, safer, and more accurate means of holding workpieces compared to traditional mechanical clamps. With the ability to securely hold varying dimensions and ferrous materials, magnetic chucks have become an indispensable tool in machining processes such as milling and surface grinding.
How Does Magnetic Chuck Cutting Work?
Without wasting any time let’s have a look at a simplified step-by-step process on how magnetic chucks are used in cutting:
- Placement: The workpiece is placed on the magnetic chuck’s surface. This surface area is often designed with a top plate to accommodate varying workpiece sizes.
- Activation: The magnetic chuck is activated, generating a magnetic field. In the case of electromagnetic chucks, an external power supply is needed. However, permanent magnetic chucks use permanent magnets, eliminating the need for continuous electric power.
- Magnetic Attraction: Once activated, the magnetic force holds the workpiece securely. This is due to the magnetic circuit formed, where magnetic flux flows from the chuck’s north to the south poles.
- Cutting Process: With the workpiece firmly held, the cutting or milling operation can begin. The magnetic chuck provides full support for the workpiece, mitigating machining-induced vibrations and ensuring a smooth, precise cutting process.
- Deactivation: Once the machining process is complete, the magnetic chuck can be deactivated, releasing the workpiece. In the case of an electromagnetic chuck, cutting off the electric current will do this. For a permanent magnetic chuck, a control unit is used to reverse the magnetic field, breaking the magnetic attraction.
10 Advantages of Using Magnetic Chucks in Cutting
The manufacturing sector often grapples with efficiency, safety, and precision issues during the machining process. One solution that has proven effective in addressing these pain points is the use of magnetic chucks. Here are ten consolidated advantages of using magnetic chucks in cutting that make them indispensable in machining operations.
Enhanced Safety and Precision
The magnetic force of a chuck provides a firm grip on the workpiece, minimizing the chance of slippage and potential accidents. This secure hold also reduces machining-induced vibrations, leading to smoother operations and increased precision in tasks such as surface grinding.
Speed and Productivity
Magnetic chucks significantly reduce setup and changeover times due to their easy placement and removal of workpieces. Holding multiple parts simultaneously and allowing faster feeds enable more efficient machining processes, thereby increasing productivity.
Versatility and Accessibility
With the ability to hold workpieces of varying dimensions, magnetic chucks offer immense versatility. Their design provides unobstructed access to the entire workpiece, facilitating complete and efficient machining, which is particularly beneficial in complex milling operations.
Uniformed Holding and Reduced Damage
By exerting uniform pressure across the workpiece, magnetic chucks ensure consistent machining results and minimize potential damage from mechanical clamping. This feature is vital when working with pressure-sensitive workpieces, as it avoids deformities and maintains the integrity of the parts.
Energy Efficiency and Heat Management
Permanent magnetic chucks do not require a continuous power supply, hence saving energy. Moreover, their operation generates minimal heat, thereby reducing thermal distortions in the workpiece, preserving the accuracy of the cut, and extending the life of the tool.
Power Failure Safety and Durability
In the event of a power failure, permanent magnetic chucks continue to hold the workpiece securely, providing an additional layer of safety. Besides, with fewer moving parts than mechanical clamps, they are more durable and require less maintenance.
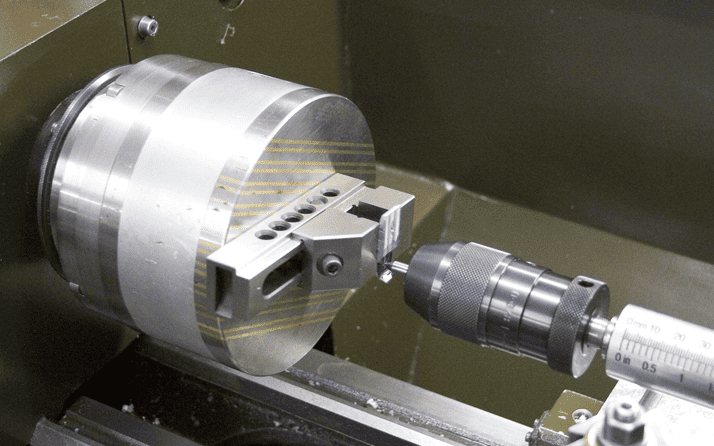
Improved Workholding for Ferrous Components
Magnetic chucks are particularly advantageous when working with ferrous materials. Their strong magnetic attraction ensures reliable work holding, enabling a more effective machining process for ferrous components.
Simplified Workflow in General Machine Shops
In a general machine shop setting, the use of magnetic chucks can streamline workflows. The fast setup, combined with their ability to securely hold multiple parts at once, simplifies the metalworking operation and saves valuable time.
Consistent Clamping Force
The magnetic chuck ensures a consistent clamping force across the entire surface of the workpiece. This results in a more uniform cut, particularly valuable in surface grinding applications.
Enhanced Longevity of Tools
The reduction in vibration and heat generation during operation improves the cut’s quality and extends the life of cutting tools. This leads to long-term cost savings and higher productivity in milling machines.
How to Choose Magnetic Chucks in Cutting?
Choosing the right magnetic chuck for your specific cutting needs can be daunting, especially given the wide array of options available in the market. The correct selection is crucial because it not only influences the quality and precision of your cuts but also affects the overall efficiency of your machining process. Here are some key points to consider when selecting a magnetic chuck:
- Size: The chuck should fit your machine and workpiece. Its size should offer a secure hold while fitting the machine table.
- Type: Magnetic chucks come in different types, namely permanent, electromagnetic, and electro-permanent, each serving different purposes. Select based on your specific needs.
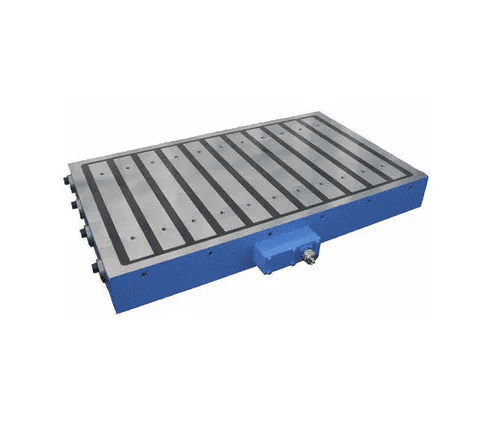
- Force: The magnetic force should securely hold the workpiece during heavy operations but also protect pressure-sensitive pieces.
- Material Compatibility: Magnetic chucks work best with ferrous materials. Ensure your workpiece material is compatible.
- Heat Resistance: Choose a heat-resistant chuck to withstand the heat generated during machining, preventing potential thermal distortions.
- Control Unit: A user-friendly control unit is crucial for electromagnetic and electro-permanent chucks. It should allow easy adjustments and provide reliable performance.
- Safety Features: Choose chucks that maintain workpiece security in case of power failures, ensuring safety and preventing damage.
- Durability and Maintenance: Opt for robust, low-maintenance chucks. These may initially cost more but will save money through reduced downtime and maintenance costs.
Successful Application of Magnetic Chuck in Different Industries
Magnetic chucks are transforming operations across various industries, with their efficiency, precision, and adaptability being substantially beneficial. From the intricacies of aerospace and medical applications to the robust demands of the automotive and oil and gas sectors, magnetic chucks are playing a pivotal role in improving productivity and accuracy.
- Aerospace: This industry requires high-precision parts, often made from hard-to-machine materials. The uniform clamping force of magnetic chucks allows for optimal surface grinding and milling of complex components, with reduced risk of deformation or damage, making them invaluable in producing intricate aerospace parts.
- Automotive: The automotive sector frequently handles large, bulky parts that need high-speed machining. Magnetic chucks provide consistent holding pressure across the entire body of the workpiece, allowing for faster feeds and speeds while reducing setup time. This contributes significantly to improved productivity in automotive manufacturing.
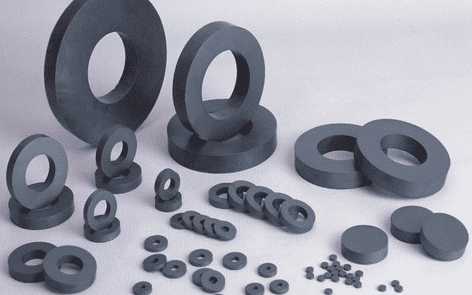
- Medical: The production of intricate, delicate medical devices often involves handling small or thin workpieces that could be damaged by mechanical clamping. Magnetic chucks, especially electro-permanent magnetic chucks, offer delicate yet secure work-holding solutions that minimize potential damage, resulting in a greater output of high-quality, precision medical devices.
- Oil and Gas: This industry often works with heavy-duty ferrous components, requiring strong clamping force. Permanent magnetic chucks, using the magnetic force from the north and south poles, offer powerful and reliable holds for such applications, ensuring safety and precision during heavy milling operations.
Limitations and Challenges of Magnetic Chucks
While magnetic chucks have significantly revolutionized various machining processes across industries, they also present certain limitations and challenges. Understanding these limitations helps users to make informed decisions when integrating these devices into their machining systems.
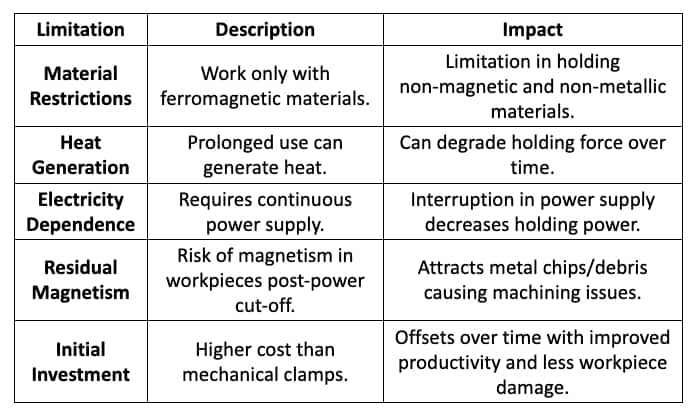
Conclusion
To wrap up, magnetic chucks are undeniably a valuable tool in the manufacturing industry, providing unmatched precision, efficiency, and safety in operations. Although they do have limitations, the benefits, such as improved productivity, uniform holding, and the ability to handle various shapes and sizes of workpieces, largely outweigh the challenges. This, in combination with their successful application across different sectors like aerospace, automotive, medical, and oil & gas, makes them a go-to choice in work holding. Feel free to explore our other resources for more insights into enhancing your machining and manufacturing processes.
Ready to Enhance Your Manufacturing Process with Our Top-Tier Magnetic Chucks?
Request an instant quote today! Baison Laser is dedicated to providing innovative and efficient solutions for the manufacturing industry. We pride ourselves on our industry-leading technology and exceptional customer service. Get started with a free application evaluation and discover the Baison Laser difference.
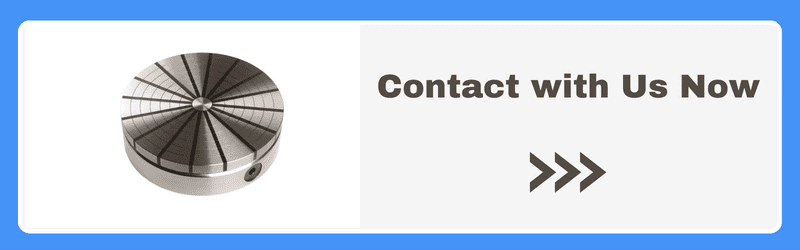