What Is a Punching Machine?
Punching machines, or punch presses, are powerful and versatile machines used in various industries. These machines utilize a mechanical process to create holes or shapes in metal sheets. Using punches and dies, they remove material from the sheet to achieve the desired outcome.
One of the key advantages of punching machines is their ability to handle high-volume production while maintaining consistent results. They excel at repetitive tasks and can perform multiple operations simultaneously, saving time and increasing the efficiency of secondary operations.
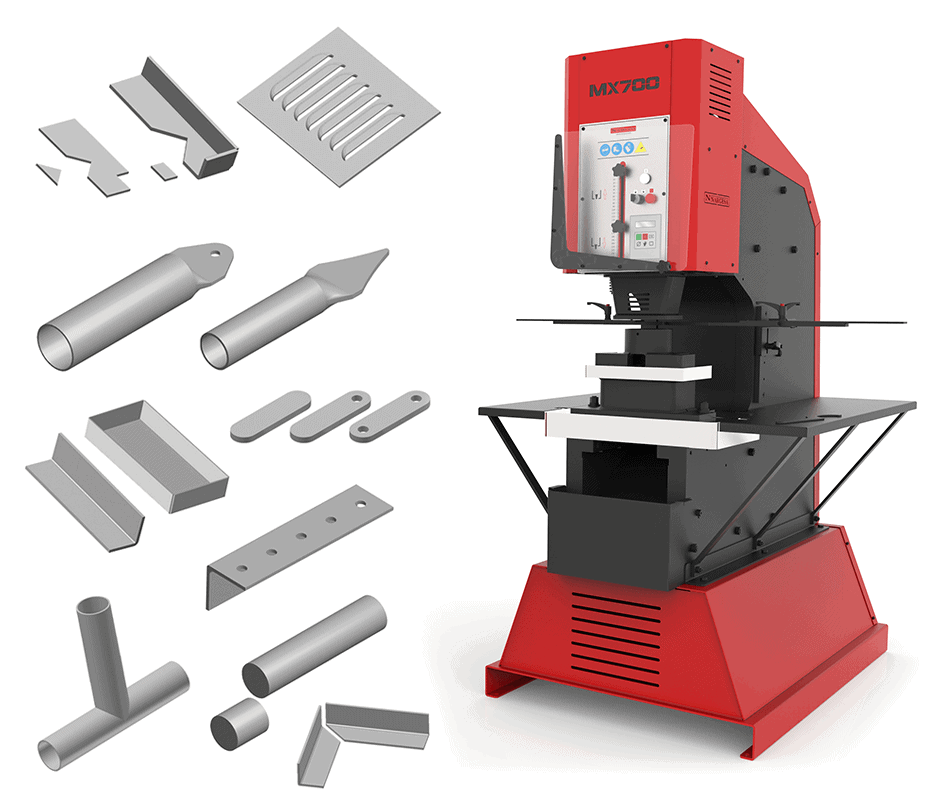
Punch presses are particularly suitable for working with thick materials and creating shapes that may be challenging for other methods. Their robust construction allows them to handle heavy-duty applications with ease.
Advantages of Punching Machines
Punching machines offer several advantages, making them a valuable tool in the manufacturing industry. Let’s take a closer look at some of these benefits:
- High production speed: Punch press systems are designed for batch processes. Punching machines excel in their ability to quickly produce large quantities of parts, significantly reducing manufacturing time. This makes them ideal for high-volume production runs where efficiency is crucial.
- Versatility in creating various hole sizes, shapes, and patterns: With punch press technology, manufacturers can create holes of different sizes, shapes, and patterns. Whether it’s round holes, slots, or custom designs, punching machines can handle various requirements.
- Cost-effective solution for large-scale production runs: Punching machines are a cost-effective choice. Their high-speed operation and ability to process multiple sheets simultaneously contribute to lowering overall production costs.
- Ability to perform additional operations like forming, embossing, and threading: Apart from punching holes or slots, these machines can also carry out additional operations such as forming metal into desired shapes, embossing logos or patterns onto surfaces, and even threading holes for easy assembly. A punch press could eliminate spot welding and the high cost of secondary operations.
Limitations of Punching Machines
Punching machines have their limitations. Let’s take a closer look at these limitations:
- Limited flexibility: Punching machines struggle with intricate designs or complex curves. They are better suited for simpler shapes and patterns, not complex shapes.
- Tool changes: Punching machines require frequent tool changes to accommodate different hole sizes or shapes, which can slow down the production process. Punch press operators must be highly skilled in machine setup.
- Unsuitable for thin materials: Thin materials pose a challenge for punching machines as they can easily distort or cause burring during cutting.
- Higher initial investment: Punching machines have a higher upfront cost than other cutting methods. This can be a barrier for businesses with limited budgets.
What is a Laser Cutting Machine?
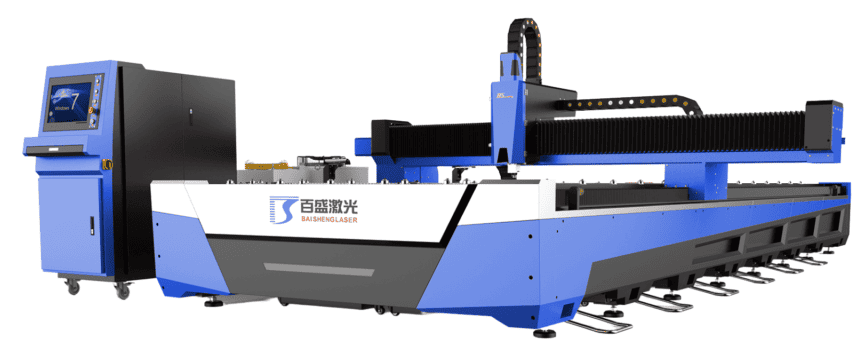
Laser cutting technology utilizes a focused laser beam to perform precise cuts on various materials, especially metal sheets. These machines have gained popularity due to their ability to melt, burn, or vaporize material accurately. The laser light process involves using CO2 or fiber lasers, which offer different power options, like the 3 kW fiber laser.
Key points about laser cutters include:
- Laser cutter enables intricate cuts with minimal heat-affected zones (HAZ), ensuring high precision and quality.
- This technology is suitable for working with thin and thick materials, making it versatile for various applications.
- By utilizing different types of lasers, such as CO2 lasers or fiber lasers, users can choose the most appropriate option based on their specific requirements.
Advantages of Laser Cutting Machine
Laser cutters offer several advantages over traditional methods. Let’s dive into some key points:
- Precise cuts with tight tolerances: A laser cutter uses CNC(Computer Numerical Control) technology to automate the process, ensure accuracy and reduce wastage. The laser beam follows a predetermined path, creating clean edges and intricate designs.
- Faster setup time: Unlike conventional tools, laser cutters don’t require physical tooling. This eliminates the need for time-consuming setup processes, allowing quicker production turnaround times.
- Versatility in handling various materials: Laser cutters can handle various materials, including steel, aluminum, and stainless steel. This versatility makes them suitable for diverse applications across industries.
- Minimal material wastage: Laser cutting produces narrow kerf widths, so less material is wasted. This efficiency translates to cost savings and reduced environmental impact.
Limitations of Laser Cutting Machines
- Higher operating costs due to energy efficient consumption and maintenance requirements.
- Limited thickness capacity compared to punching machines for certain materials.
- The potential risk of thermal distortion or discoloration on the cut edges.
- Not suitable for reflective materials without proper precautions.
Factors to Consider When Choosing Between Punching and Laser Machines
Several key factors must be considered when deciding between punching and laser cutters. These factors will help determine which machine best suits your needs and requirements.
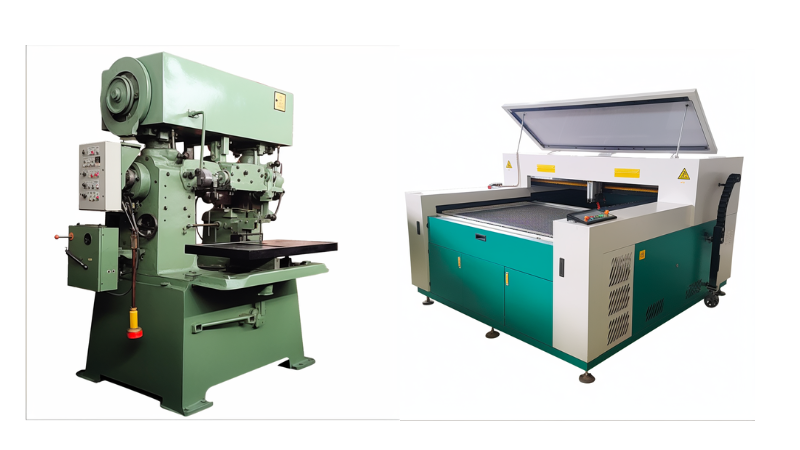
Production Volume and Required Operation Speed
Consider the production volume you anticipate and the desired speed at which you need the machine to operate. Punching machines are often faster for high-volume production, while laser cutters excel in precision and versatility.
Complexity and Intricacy of the Desired Designs
Evaluate the complexity and intricacy of the designs you intend to create. For complex and irregular shapes, choose an advanced laser cutter over a turret-punching one. Laser cutters offer greater flexibility for intricate designs with fine details, whereas punching machines may be more suitable for simpler shapes or patterns.
Material Thickness and Type to Be Processed
Consider the thickness and type of materials you plan to process. Punching machines are typically better suited for thicker materials such as sheet metal parts or sheets, while laser cutters can handle a wider range of materials, including metals, plastics, wood, and more.
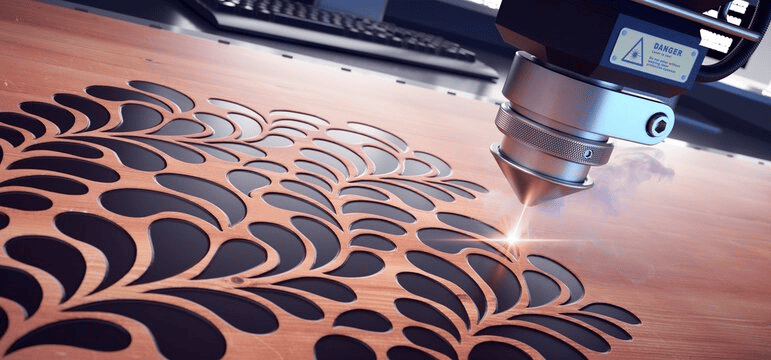
Initial Investment Budget and Long-term Operating Costs
Assess your budget for initial and long-term operating costs. Punching machines generally have lower upfront costs but may require more maintenance. Laser cutters often have higher initial costs but can provide cost savings regarding material waste reduction.
Considering these factors, you can decide whether a punching or laser cutter is the right choice for your application. Remember to weigh the pros and cons based on your unique production process metal and requirements, design complexity, material specifications, budget considerations, and long-term operational needs.
Revolutionizing Metal Fabrication with Punching and Laser Cutting
Combining the power of punching and laser-cutting machines has revolutionized metal fabrication, offering enhanced efficiency and productivity. This innovative approach to sheet metal fabrication and processing brings numerous advantages to the industry.
Enhanced Efficiency through Technology Integration
The integration of automation systems has streamlined production processes, allowing for faster turnaround times and increased output. Operators can focus on other critical aspects of the fabrication process by automating tasks such as loading and unloading workpieces. This automation saves time and reduces the risk of errors, ensuring consistent quality in every cut.
Design Optimization and Material Utilization
Improved software capabilities have further contributed to the advancement of punching and laser-cutting machines. With sophisticated design software, engineers can optimize designs for maximum material utilization, reducing waste, and minimizing costs. Nesting parts efficiently on a sheet increases productivity while conserving valuable resources.
Precision and Productivity with Advanced Machine Control Systems
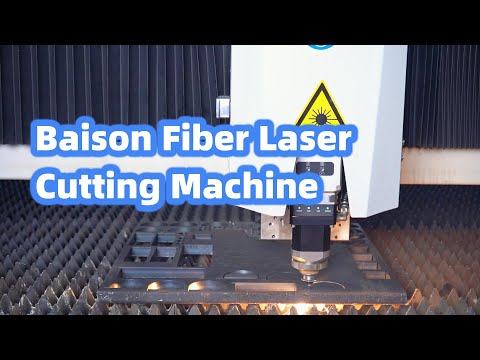
Advancements in machine control systems have led to higher precision levels during cutting operations. These systems offer real-time monitoring and adjustments, ensuring accurate cuts even on complex geometries. The improved control enables faster processing speeds without compromising quality or safety.
Conclusion
Choosing the right laser cutting vs. machine is crucial for maximizing productivity and achieving results. While punching machines offer high speed and cost-effectiveness for thicker materials, laser cutters provide versatility, precision, and intricate design capabilities. You can select the ideal machine that aligns with your needs by carefully considering your requirements, consulting with experts, and evaluating long-term costs. Remember, a well-informed decision will contribute to the success of your business or project.
Make a Powerful Move with Baison Laser Cutting Machines
When it comes to enhancing your metal fabrication capabilities, Baison is your trusted partner. As a leading company specializing in laser cutters, we offer cutting-edge solutions designed to revolutionize your production processes. Contact Baison today to explore our range of advanced laser cutters and unlock new possibilities for your business.