Picture a world where sheets of metal change into complex shapes as if clay shaped by a skilled potter. Thanks to the powerful press brakes, this now happens every day in metal fabrication. Whether you’re making a car’s smooth body, a plane’s tough frame, or the fine details in building designs, it’s key to know the types of press brakes and what each can do.
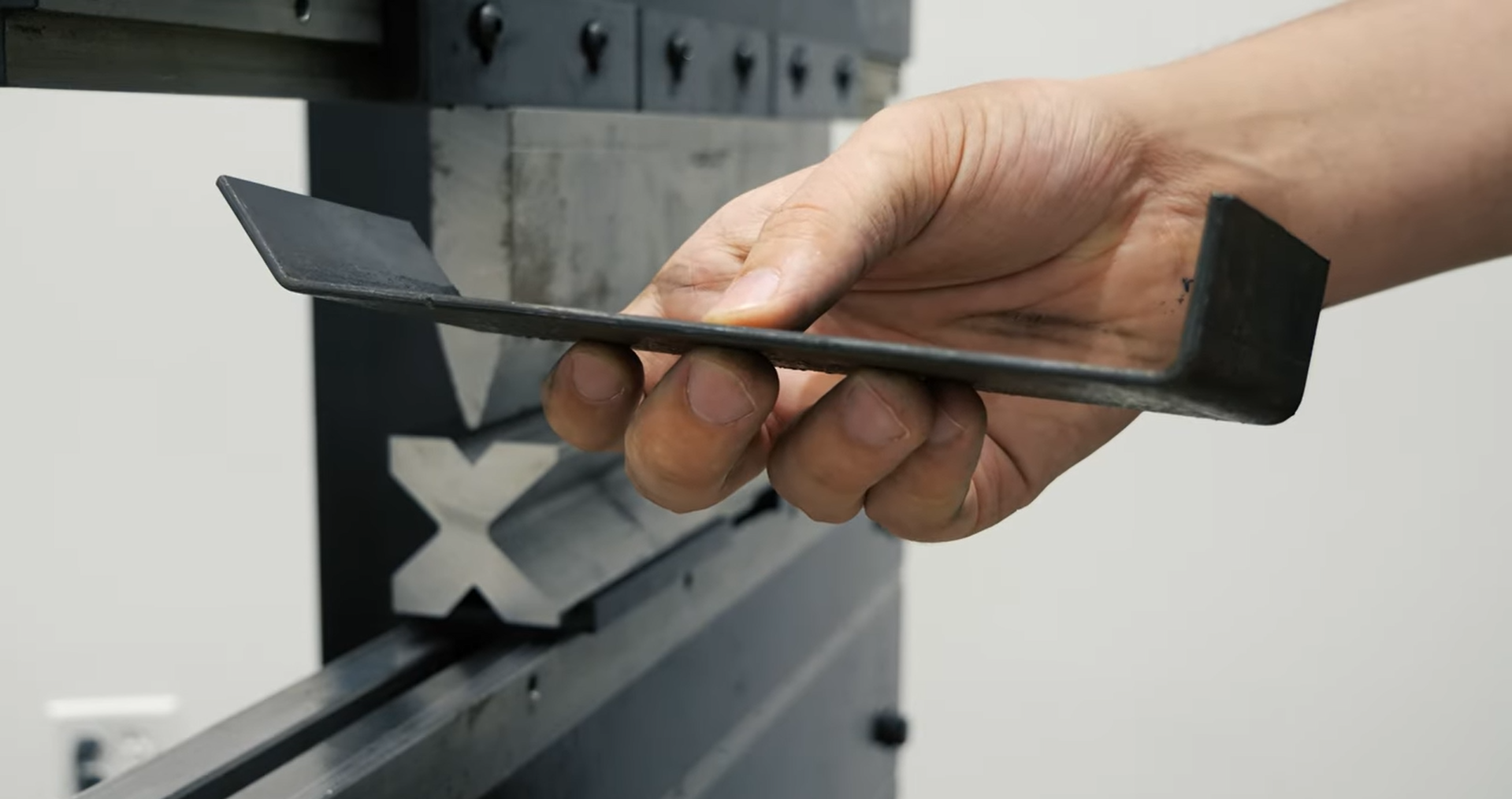
Read this full guide to learn the secrets of these strong machines and see how they mold the world we live in.
What is a Press Brake?
A press brake bends and folds sheet metal and plate materials into different shapes and angles. This powerful machine tool sees use in the metalworking industry. It works by clamping the metal work piece between a punch and a die. The metal takes on the wanted shape when force pushes the punch.
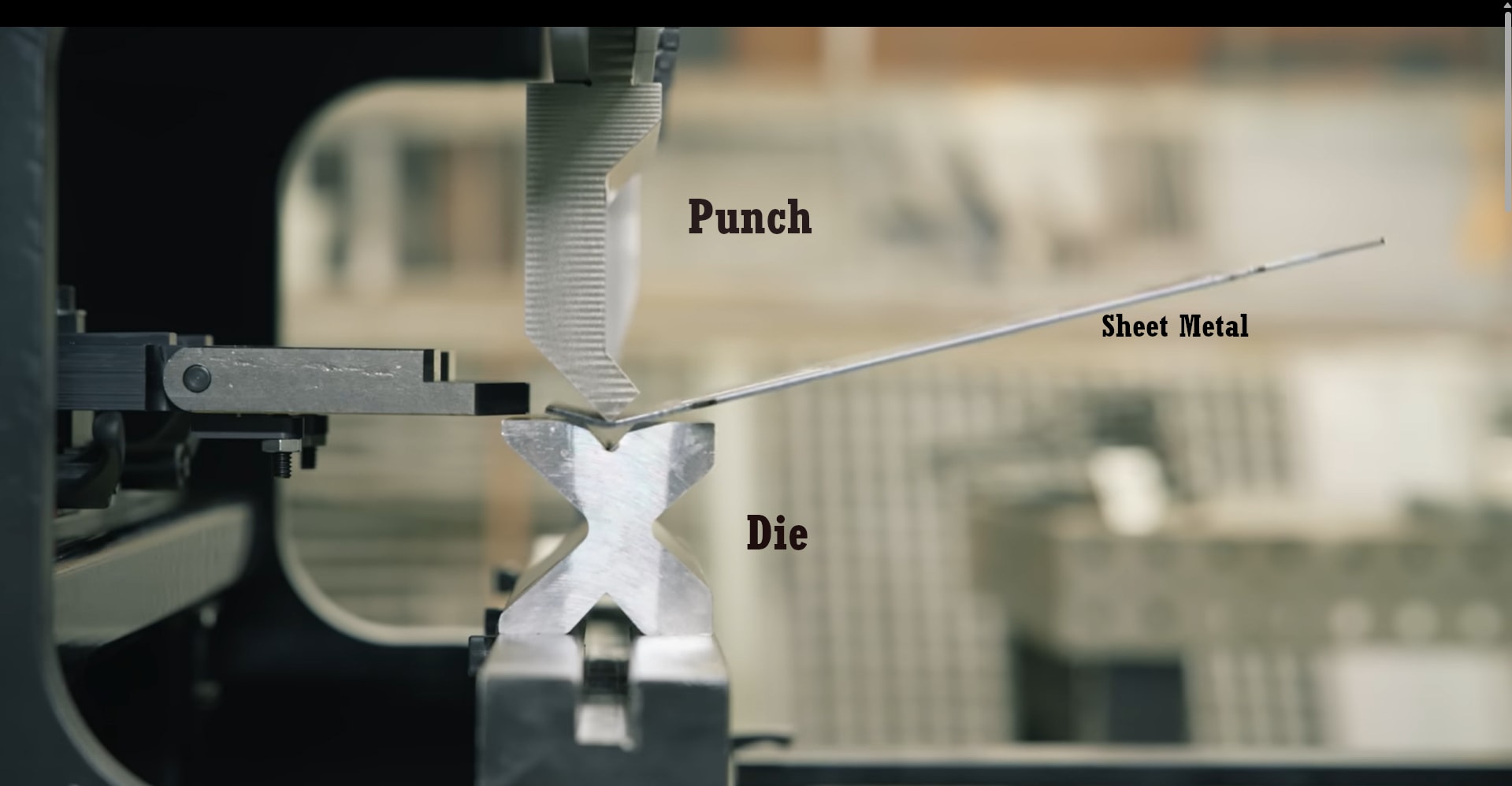
Press brakes shape metal with precision using force. The machine has a ram, or beam, that moves up and down to push the punch into the die, which sits on a fixed bed. The type of press brake you pick determines if the force comes from mechanical, hydraulic, or electric means.
Press brakes play a role in many fields. Car makers use them to bend sheet metal for body parts like doors and hoods. The aerospace sector relies on them to produce aircraft parts where exactness matters most.
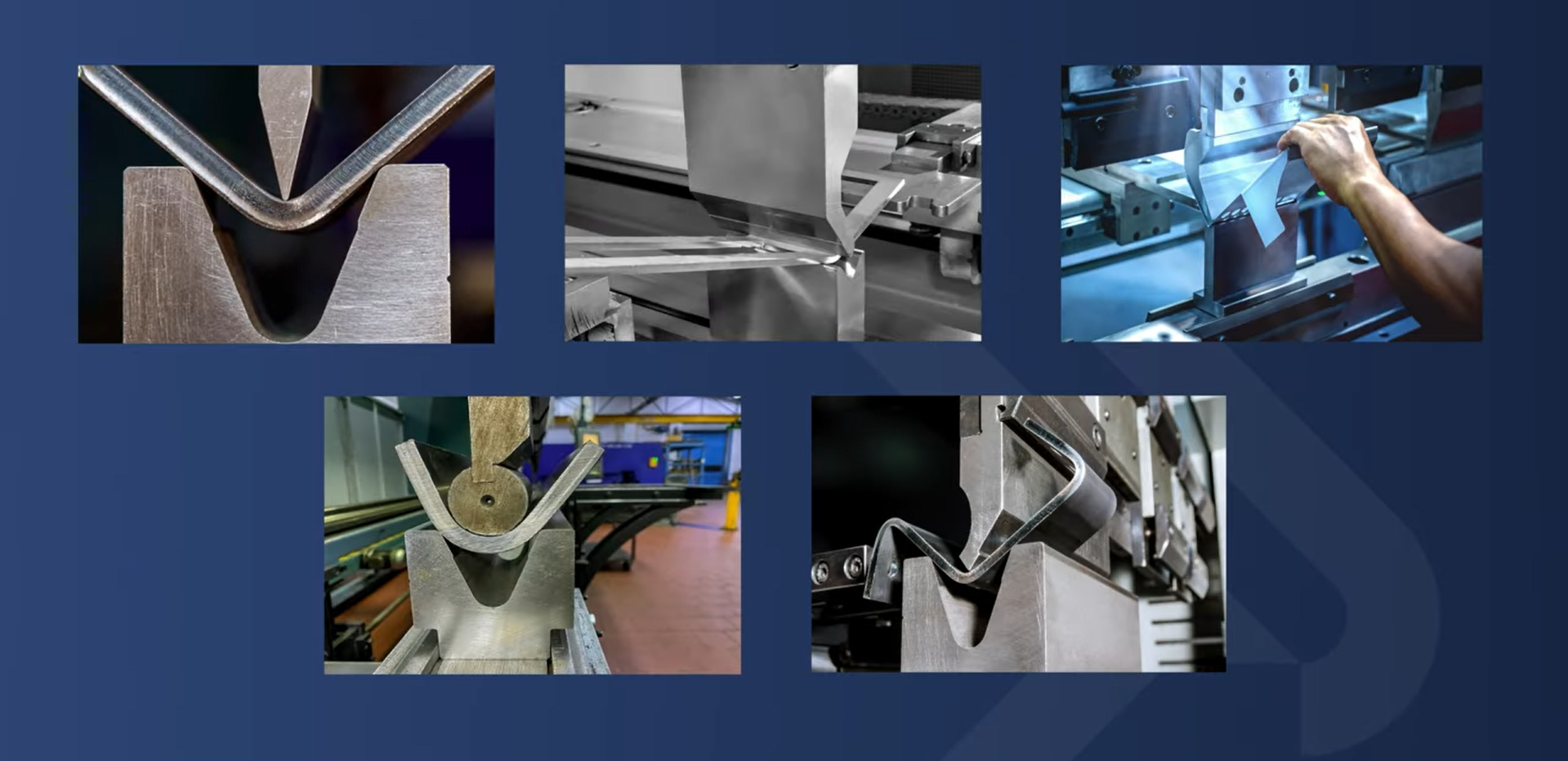
Press brakes play a key role in shaping metal sheets for construction projects. They help create roofs and structural parts. In the appliance industry, these machines shape metal for products like washing machines and fridges. People also use press brakes for custom metal work. This includes making brackets or crafting artistic metal pieces.
Read Also: Panel Bender vs Press Brake
Types of Press Brakes
Press brakes play a key role in the metal industry to bend sheet metal. Knowing the different kinds helps you pick the right one for what you need to do.
There are 4 primary types of press brakes. Mechanical, Hydraulic, CNC, and Pneumatic press brakes.
Mechanical press brakes work with a flywheel that an electric motor powers. The flywheel stores energy and releases it to bend the material. These machines excel at speed and productivity, which makes them perfect for high-volume work, like car manufacturing.
Hydraulic press brakes rely on hydraulic cylinders to exert force using pressurized fluid to move the ram. They can handle thicker materials accurately. This capability suits them for tough jobs such as building construction and shipmaking.
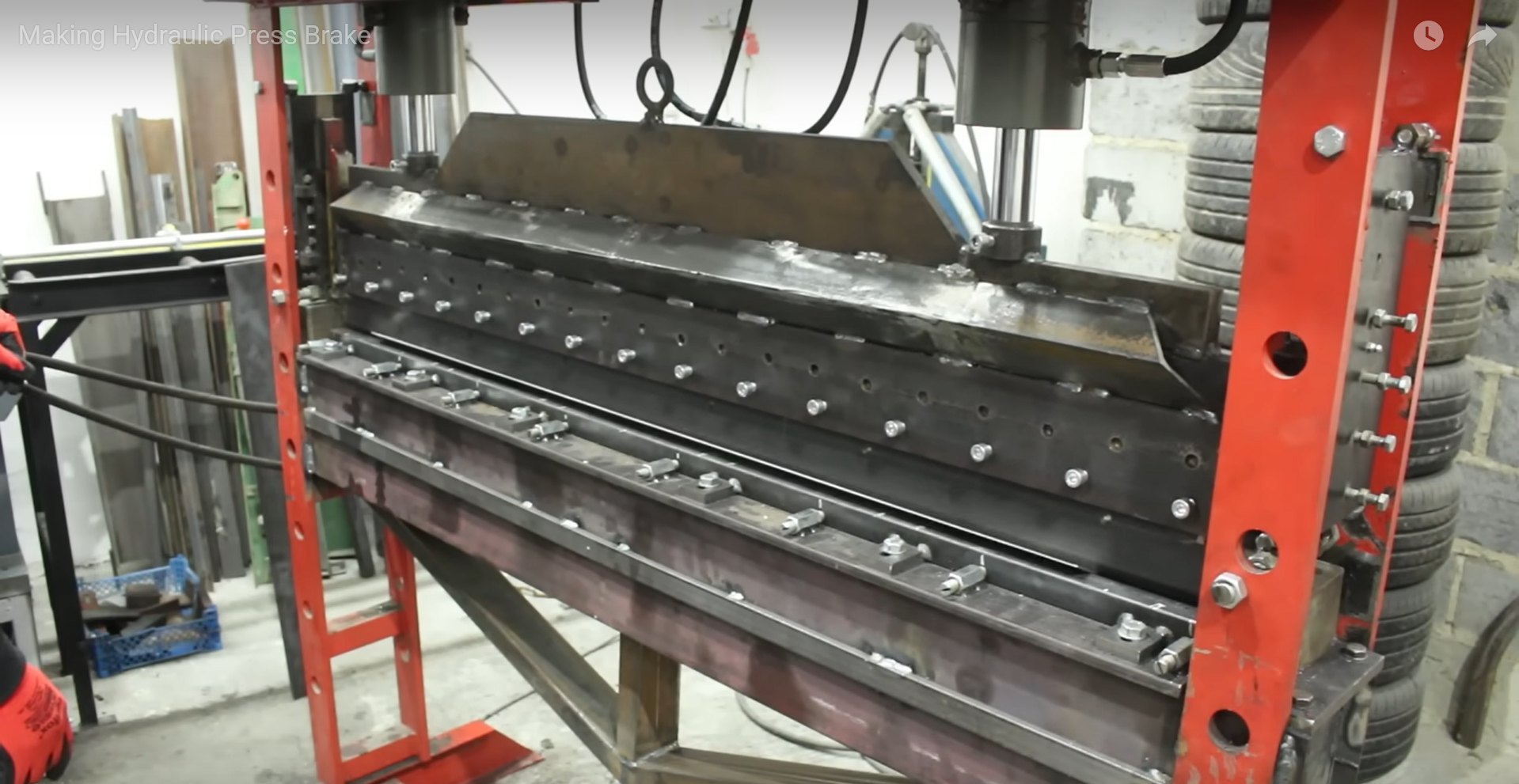
Servo-electric press brakes (CNC) use electric servo motors to control the bending process. They save energy, bend with high accuracy, and need little upkeep. These machines work best for jobs that need exact bends, like in airplane and computer part making.
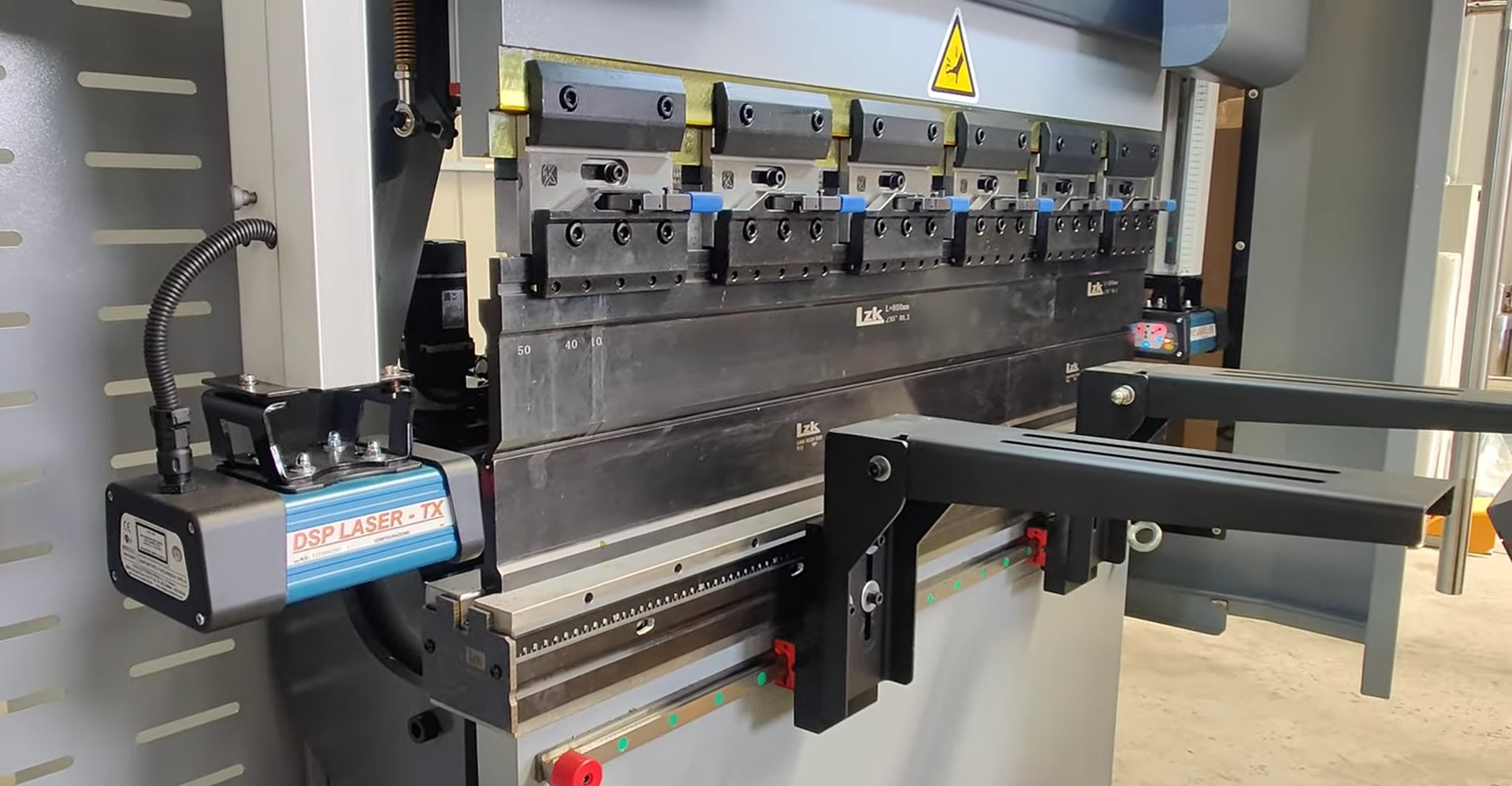
Hybrid press brakes mix hydraulic and servo-electric tech to work better. They offer the precision of servo-electric systems with the power of hydraulic systems, making them versatile enough to handle a wide range of tasks, from light to heavy-duty bending.
Mechanical Press Brakes
Manufacturing has relied on mechanical press brakes for ages. These machines stand out for their power and capacity to bend heavy materials. Let’s explore how they operate and what sets them apart.
Operation
A clutch system in mechanical press brakes engages and disengages a flywheel. An electric motor gives kinetic energy to the flywheel. The clutch when engaged, sends this energy to the ram via gears. These gears boost the force enabling the machine to bend thick materials.
Key Characteristics
The high force output of mechanical press brakes makes them perfect to bend tough materials. They run at quick speeds, which can boost productivity in a factory setting. These machines also offer good value, as they cost less to buy and keep up than hydraulic press brakes. While they may not be as exact as hydraulic models, they still work well for many jobs that don’t need pinpoint accuracy.
Application
You’ll see mechanical press brakes in industries that need heavy-duty bending. They help bend chassis parts in car manufacturing. In shipbuilding, they shape big metal sheets for ship hulls. The construction industry also uses them to make structural pieces like beams and columns.
Limitations
Mechanical press brakes are not as precise as hydraulic models. They may not be of much help if you need tight tolerances. Additionally, they can be more dangerous to operate due to their high speeds and force. You’ll need to make sure modern safety features are in place to reduce the risk when using these machines.
Hydraulic Press Brakes
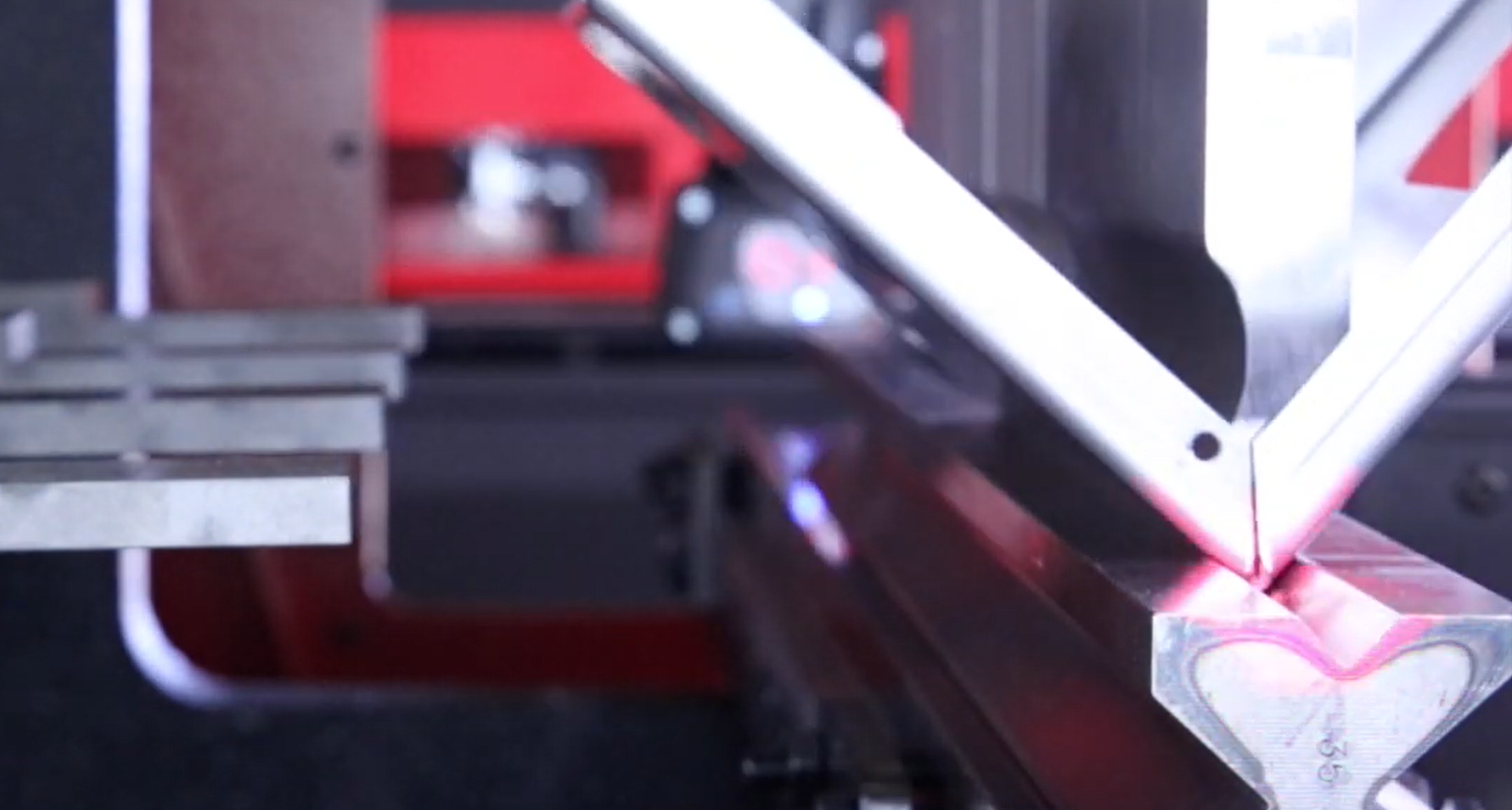
Hydraulic press brakes have gained popularity across industries thanks to their advanced hydraulic systems and ability to adapt. Here’s a straightforward explanation of how they work and their main features.
Operation
Hydraulic press brakes rely on two hydraulic cylinders that work together. These cylinders sit on the C-frames and power the machine. They control how the upper beam moves giving exact control over the speed and force used in bending. This leads to smooth and steady operation.
Key Characteristics
Hydraulic press brakes offer more flexibility than mechanical ones. They allow for exact speed control and easy pulling back making them useful for many jobs. These machines can handle big sheets, with the ability to fold sheets up to 8 meters in length. You can also set them up to act downwards or upwards, which adds to their adaptability.
Advantages
These press brake types stand out for their accuracy. They offer more precise and steady bending, which matters a lot for jobs that need tight tolerances. They’re also safer to use, as newer models come with cutting-edge safety features to lower the chance of mishaps. On top of that, these machines are simpler to handle, with programmable controls that make quick changes and repeatable tasks possible.
Applications
Hydraulic brakes are widely used in the automotive industries to manufacture body panels and components. In aerospace, they maintain precise control over brake forming to craft complex parts. They are also common in metal fabrication for creating custom metal parts and structures.
Limitations
These brakes are generally more expensive to buy and maintain compared to a mechanical press brake. They are also more complex. Their operations require skilled operators and regular maintenance.
CNC Press Brakes
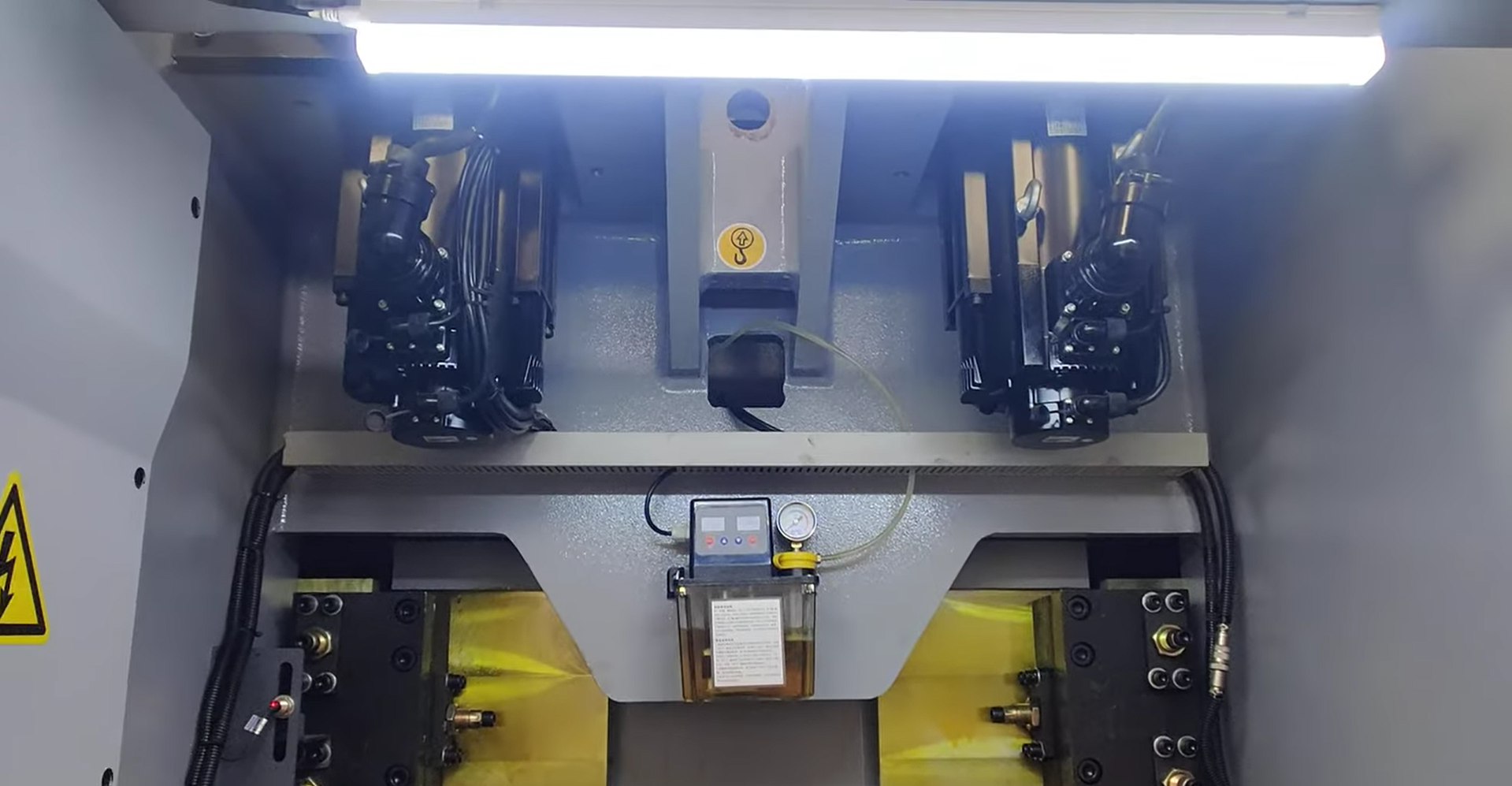
CNC press brakes have caused a revolution in press brake technology. They have an influence on manufacturing through their computer control systems and servo motors. Here’s a clear explanation of how they work and their main features.
Operation
Computers run a CNC press brake machine. The automation lets you bend materials consistently. You enter the parameters (such as bending angle or bending lengths), and the machine handles the press brake bending by itself. The machine uses servo motors to control the ram and backgauge.
Key Characteristics
CNC press brakes improve productivity. They reduce setup times and boost output. The automation helps to avoid human errors and results in consistent outcomes. You’ll find them easy to use, with a simple CNC interface that allows you to program and adjust settings . They can handle different materials and thicknesses.
Advantages
CNC press brakes deliver high-precision results. They shine when jobs need tight tolerances and complex bends. Automating the process increases output and speeds up production. Despite high initial costs, you’ll reduce labor expenses and benefit from improved efficiency in the long run.
Applications
You’ll see CNC press brakes used in industries where precision and efficiency are crucial. In aerospace, they make complex and accurate parts such as the aircraft fuselage panels, wing components, engine mounts, landing gear parts, interior components. In automotive manufacturing, they produce body panels and other parts with high precision. They are quite common in metal fabrication for creating custom parts.
Limitations
The main drawback of CNC press brakes is their high initial cost. However, the long-term savings in labor and increased productivity often balance this out. They also need skilled press brake operators and regular maintenance to keep running smoothly.
Pneumatic Press Brakes
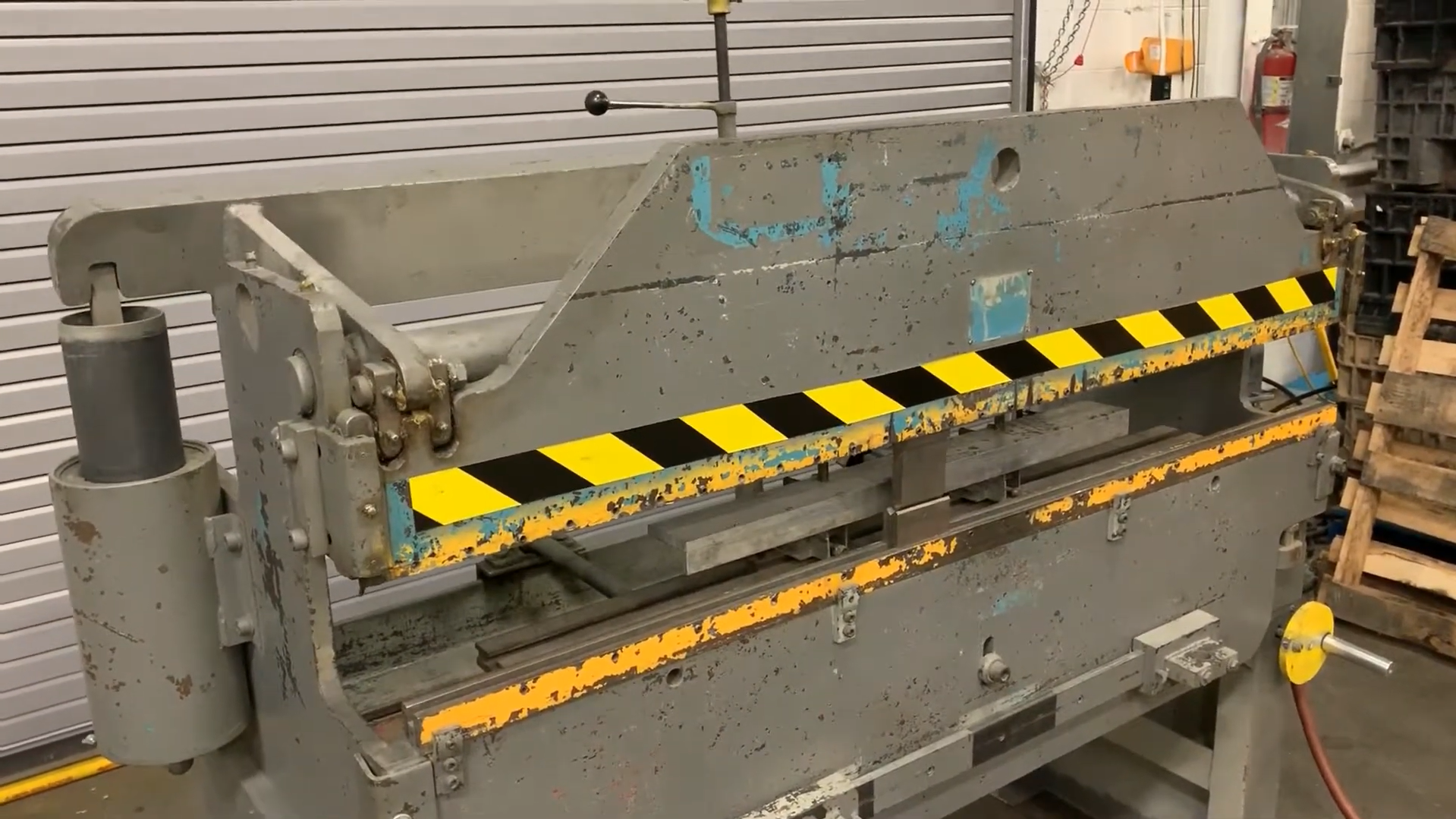
These air-powered press brakes can bend metal sheets like charms. They cost less and run easier than a hydraulic press brake, but might not be as exact. These machines save money and have fewer parts, which makes them simpler to run.
They work best for light jobs, like bending thin metal sheets and doing basic tasks. For some jobs pneumatic press brakes can work faster, which helps in making lots of items .
You can use these press brakes in many ways. They bend thin metal into shapes such as brackets and panels in sheet metal work. Car makers use them to make small light parts like brackets and clips. They also help make ductwork and parts for heating and cooling systems, create metal signs and display boards, and shape metal cases for electronic gear.
On the whole, press brakes powered by air strike a nice middle ground between how well they work and how easy they are to use. They’re a good value for bending jobs that aren’t too heavy.
Press Brake Types: Overview
Type | Drive Mechanism | Key Features | Advantages | Disadvantages | Typical Applications |
---|---|---|---|---|---|
Mechanical Press Brake | Rotational motor | Fast processing speed, simple mechanical structure, high productivity. | High speed and easy maintenance. | Difficult to adjust pressure and speed; low force for thick materials. | Bending small parts where precision is less critical. |
Hydraulic Press Brake | Hydraulic cylinders | Uses synchronized hydraulic cylinders for flexibility in speed control and retraction. | High versatility and accuracy; suitable for complex tasks. | More complex maintenance; potential for hydraulic leaks. | Heavy machinery, automotive, and general fabrication. |
CNC Press Brake | Computer Numerical Control (CNC) | Allows programming of complex shapes; high automation and accuracy with feedback systems. | Excellent for high-volume production; minimal rework needed. | Higher cost and complexity in operation; requires skilled operators. | Complex workpieces in high-volume manufacturing environments. |
Pneumatic Press Brake | Compressed air | Utilizes air pressure for operation, often lighter and more compact than hydraulic models. | Faster setup and operation; less maintenance required than hydraulic brakes. | Limited force compared to hydraulic; not suitable for heavy-duty applications. | Light to medium-duty applications, such as HVAC work. |
Key Components of a Press Brake
Ram
The ram moves in the press brake to push on the sheet metal. It can run on gears, oil pressure, or electric motors, depending on the press brake type. The ram holds the punch and pushes it down to bend the metal by pressing it into the die.
Bed
The bed stays still and holds the sheet metal during bending. It gives a firm base for both the metal and the die keeping the material lined up right while the ram pushes down.
Punch & Die
The ram holds the punch, which pushes into the metal sheet to shape it by driving it into the die. The die sits on the bed and decides the form and angle of the bend making sure the bending process is exact and uniform.
Press Brake Applications
Press brakes bend materials in different ways, each with its own uses and advantages. The main ways to bend are air bending bottom bending, and coining. Each method works best for certain tasks, based on the material and how precise it needs to be.
1. Air Bending
Air bending process happens when the workpiece touches the tip of the punch and the edges of the die. The punch pushes the workpiece into the V-shaped opening of the die but doesn’t reach the bottom. This lets you make different bend angles with the same tools by changing how far the punch moves.
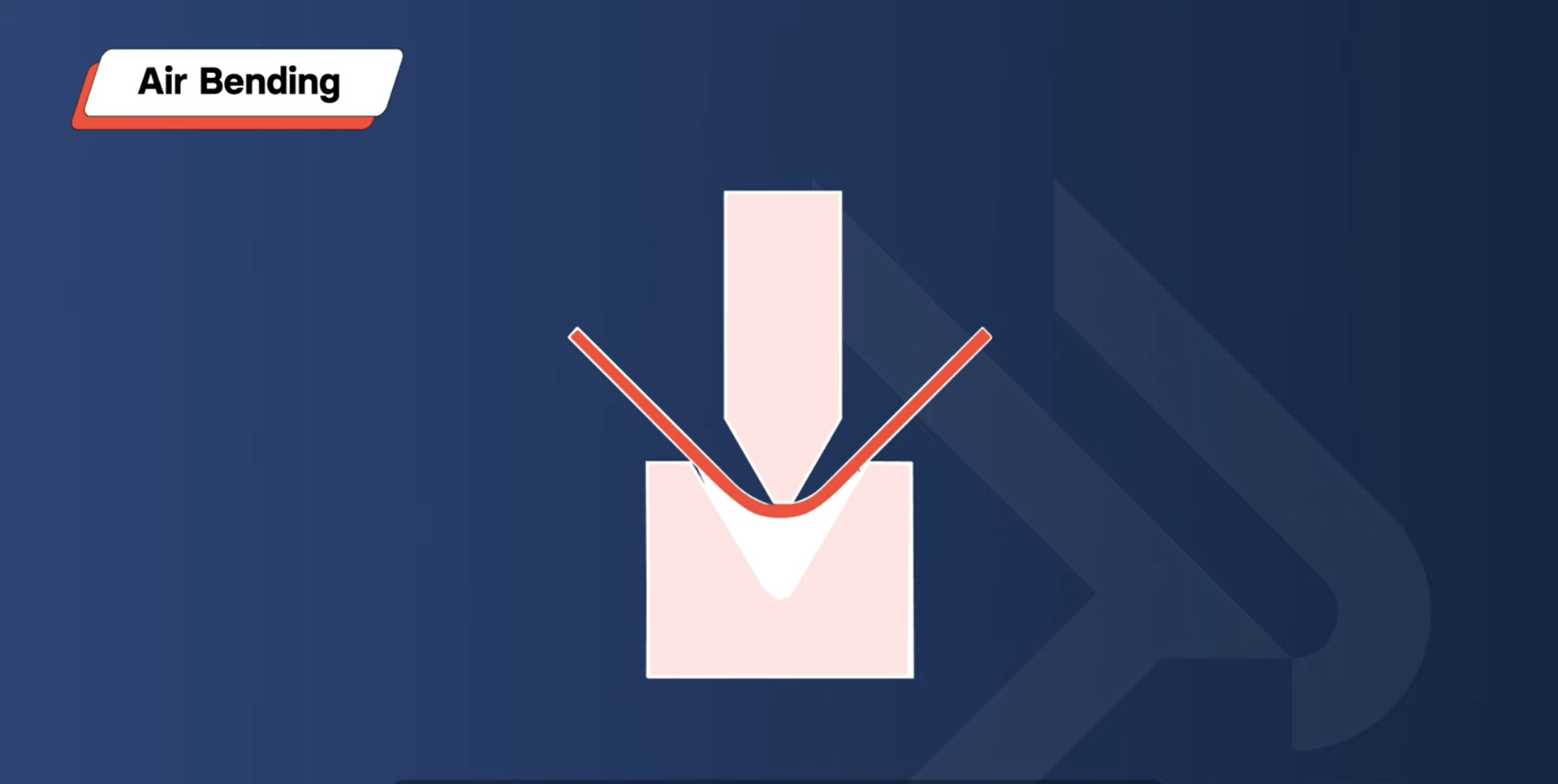
- Sheet Metal Work: Great to make various angles in sheet metal parts, like brackets, cases, and panels.
- Making Models: Helpful when trying out different angles without changing tools.
- Car Making: Used to shape light parts like brackets and clips.
Example: A company that makes custom metal brackets for electronic cases can use air bending to get different bend angles without changing how the tools are set up.
2. Bottom Bending
Bottom bending needs the die and workpiece angles to match. You press the workpiece hard against the die, and the punch’s radius shapes the bend in the material. This way gives you better accuracy and consistency in the bend angle.
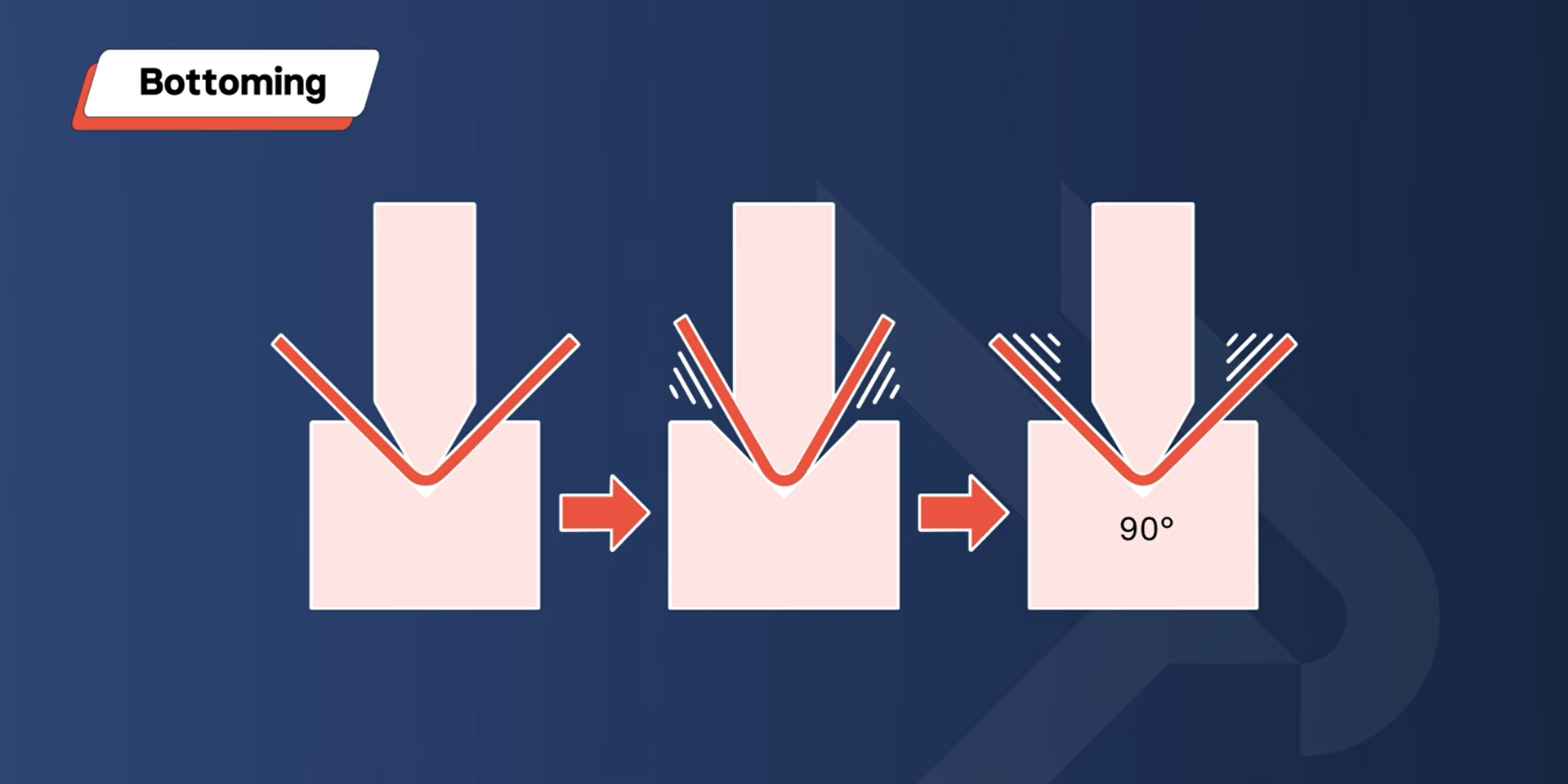
- Precision Parts: Good for making parts that need exact and steady bend angles, like parts in aerospace and medical tools.
- Heavy-Duty Bending: Used to bend thicker materials when you need higher accuracy.
- Batch Production: Great for making many parts that all need the same bend angle.
Example: An aerospace firm making exact parts for planes can use bottom bending to make sure all their parts have the same correct bend angles.
3. Coining
Coining has an impact on the workpiece by stamping it between a die and a punch with sufficient force to penetrate and flow into the material. This results in the highest accuracy and repeatability, as the material gets pressed into the die.
- High-Precision Parts: Used to make parts that need very tight tolerances and high precision, like electronic connectors and small mechanical components.
- Complex Shapes: Useful to create intricate shapes and detailed features in the workpiece.
- High-Volume Production: Ideal for high-volume production where consistent quality is critical.
Example: A manufacturer producing electronic connectors can use coining to achieve the precise shapes and tolerances required for reliable electrical connections.
Factors to Consider When Choosing a Press Brake
Material Type and Thickness
When picking a press brake, you need to think about what kind of material you’ll be bending and how thick it is. Each material bends. Take aluminum, for instance – it’s easier to bend than steel. On the other hand, stainless steel needs more power to bend. The thickness of your material is also key. The thicker it is, the more force you’ll need. Let’s say you’re working with stainless steel sheets that are 6mm thick. In this case, you’ll want a press brake that’s strong enough to handle the extra resistance from the material.
Bending Capacity
The bending ability of a press brake plays a key role in figuring out if it fits your needs. This covers the highest bending force and the bending length. The highest bending force is the top force the press brake can put out. It needs to match or go beyond the force you need for your toughest bending jobs. Also, the length of the press brake bed decides the bending length, which affects how long a piece of material you can bend at once. Let’s say you need to bend long metal panels for building. In that case, you’ll need a press brake with a longer bed and the power to handle more force.
Bending Accuracy and Precision
When picking a press brake, accuracy and precision play a key role. Accuracy means the press brake can hit the right bend angle every time. Precision shows how well the press brake can make the same bend over and over. If you work in fields like aerospace where parts must meet tough rules, you’ll need a press brake that’s both accurate and precise. This makes sure all parts meet the required standards.
Throughput
How much a press brake can produce matters when you choose one. This includes how many parts you need to make in a set time and how often you bend materials. In high-output settings, like car making, you need press brakes that can run non-stop and make parts fast. A machine that can handle frequent use and lots of work will be key to reach your production goals.
Benefits of Using a Press Brake
- Flexibility: Works with many materials and thicknesses fitting different jobs, like bending thin aluminum for electronics cases or thick steel for building parts.
- Exactness: Has advanced controls to ensure high exactness key for making aerospace parts with strict limits and steady quality.
- Speed: Does many bends at once cutting down on manual changes and speeding up production, great for boosting output in busy places like car factories.
- Money-Saving: Makes the bending job automatic to lower labour costs and cut down on wasted material, helping small shops save on both workers and supplies by making parts.
- Versatility: Manufacturers can equip these machines with different tools to create various bends and shapes. This lets them switch between setups to make simple bends or complex forms without needing several machines.
- Safety: These machines have features to keep workers safe and stop accidents in busy shops. They include light curtains, safety guards, and emergency stop buttons.
How to Choose the Right Press Brake for Your Needs
Assess Your Specific Needs
To pick a press brake, start by evaluating what you need. Figure out the materials you’ll work with, like steel, aluminum, or stainless steel, since each bends. Work out the range of material thicknesses you’ll handle, as thicker stuff needs more force and a tougher press brake. Think about the bending angles you want to achieve. Some press brakes let you adjust angles more than others.
Let’s say you need to bend thin aluminum sheets for electronic boxes and thick steel plates for building projects. Make sure the press brake can do both jobs.
Determine Tonnage Capacity and Bending Length
After that, figure out the tonnage capacity and bending length you need for your work. The tonnage capacity means the highest force the press brake can apply. It should be enough to bend the thickest and toughest materials you use. The bending length is how long the press brake bed is. This decides the longest piece of material you can bend at once. If you make long metal panels for building, you’ll need a press brake with a longer bed and higher tonnage capacity.
Evaluate Control Systems and Automation Features
Take a close look at the control systems and automation features of the press brake. Today’s press brakes come with cutting-edge control systems that boost precision and make them easier to use. Keep an eye out for features like CNC (Computer Numerical Control) to automate and improve bending accuracy.
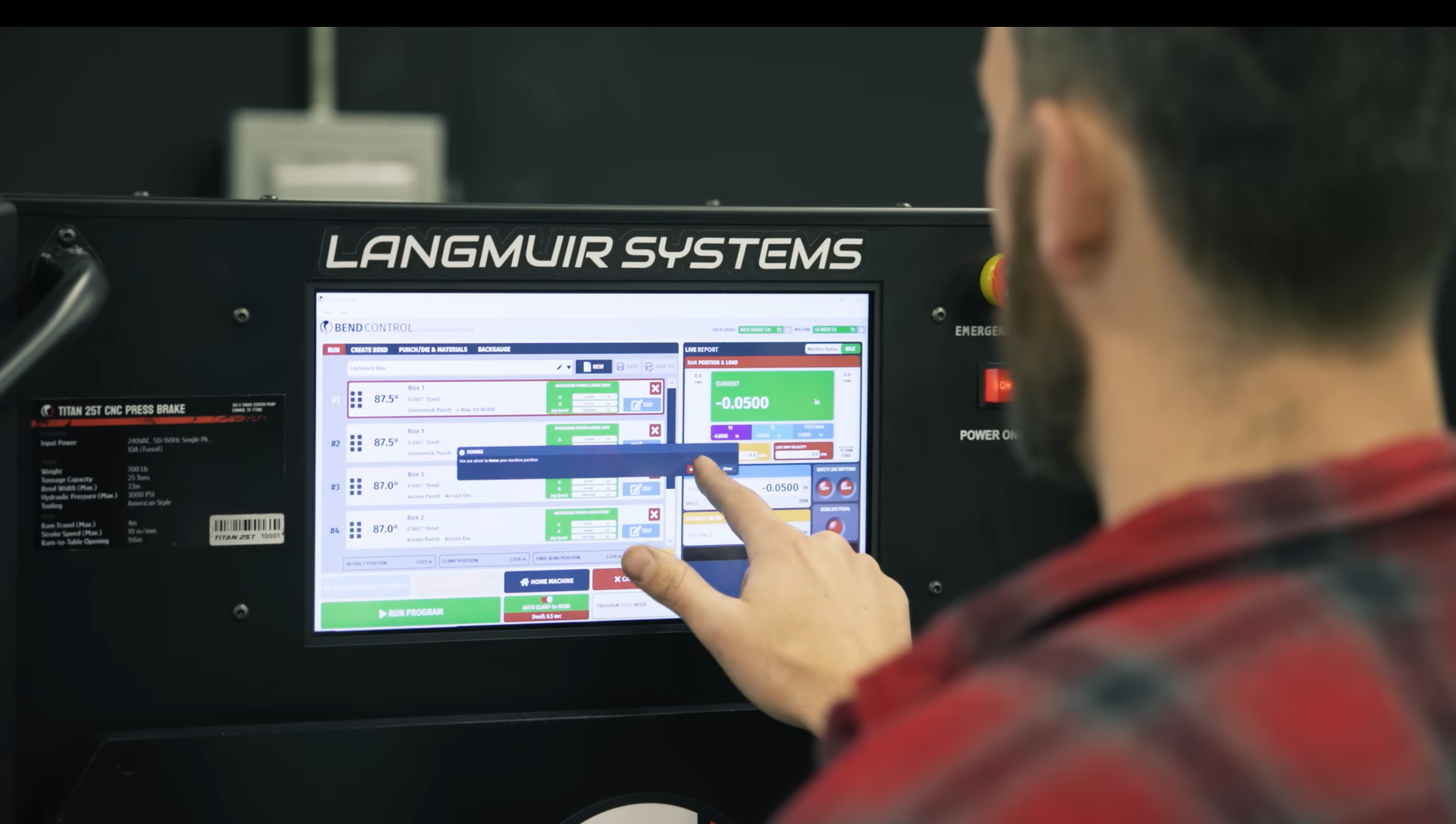
Features that automate tasks such as tool changers that work on their own, backgauges, and systems to measure angles, can boost productivity and cut down on manual work. If you run a facility that produces a lot, a CNC press brake with these automation features can speed up bending and make sure quality stays the same across the board.
Assess Manufacturer Reputation and Support
Check out the maker’s standing and help choices. Look into the maker’s track record for top-notch products and dependability by reading what other users say about them. Make sure the maker gives strong help and service options, like upkeep, training, and easy access to spare parts. Good help can cut down on time when machines aren’t working and keep your work going without a hitch.
Picking a press brake from a well-known maker with a solid help network can give you peace of mind and make sure it works well for a long time.
Additional Factors to Consider
Think about other things like if the tools work with it how easy it is to use, safety features, and how much energy it uses. Make sure the press brake works with the tools you need for your specific bending jobs, as having tools that can do many things can make it useful for more tasks.
Conclusion
Press brakes play a key role in metal forming. These machine tools bend metal with precision. High-end models can make exact bends on many materials of different sizes. Simple models handle easier bends on thinner materials helping to finish projects within budget. Press brakes come with features to boost output and allow for accurate bends.
If you need top-notch custom laser-cut parts for big machines like press brakes or pipe benders, BaisonLaser has you covered. They excel at making precise components to keep your manufacturing running and . Reach out to BaisonLaser now to talk about what you need and learn how their custom answers can step up your production skills.