In industries where precision and efficiency matter a lot, choosing the right press brake to bend metal is crucial. If you work in car manufacturing, aerospace, or custom metal fabrication, you always need machines that are reliable and perform well. But with so many choices out there, how do you figure out which press brake maker can give you the best option for what you need?
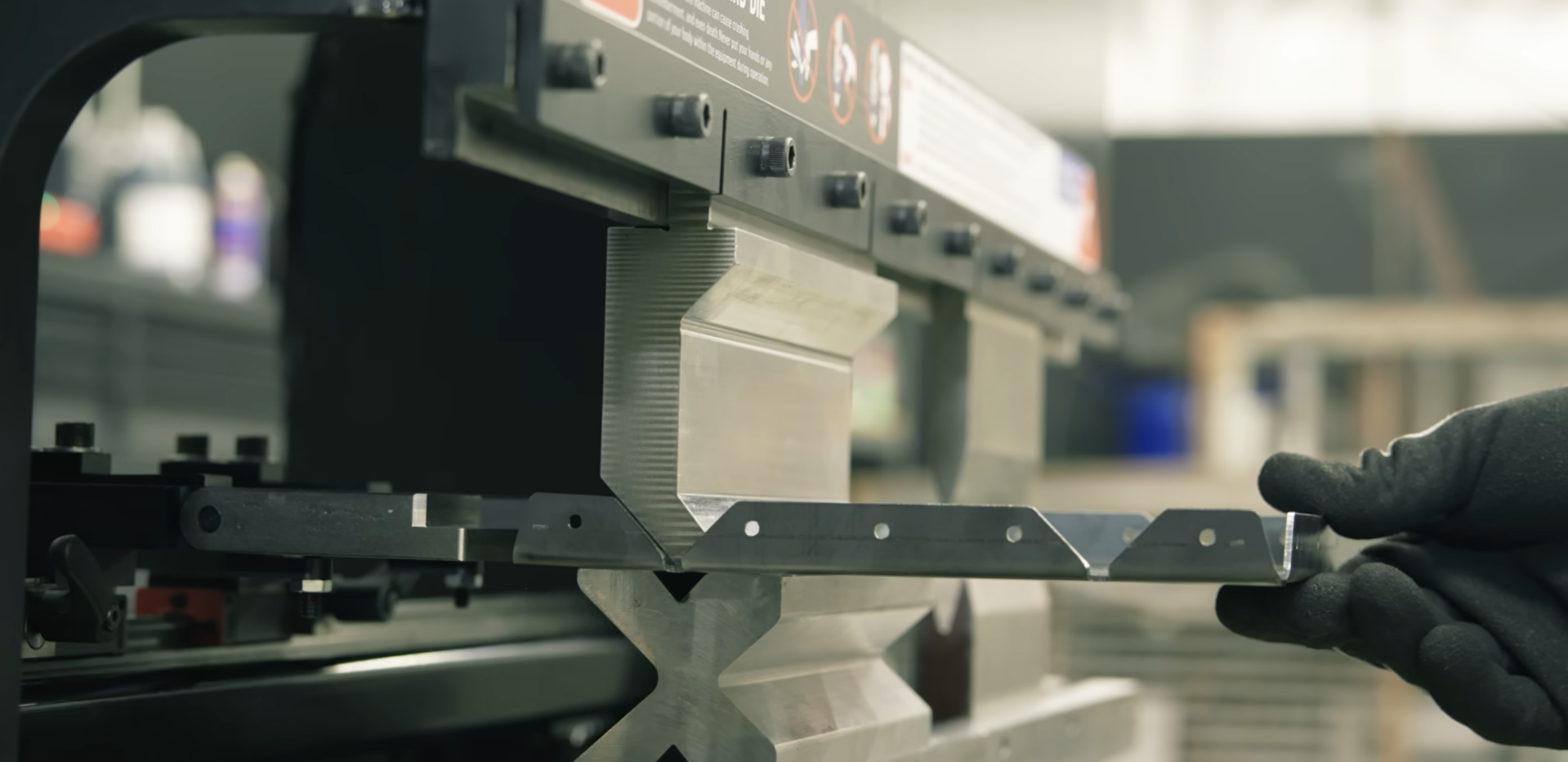
This article looks at the top press brake manufacturers in the market, giving you insights into how their tech, quality, and new ideas can meet the growing needs of today’s metalworking. If you want a machine that’s accurate long-lasting, and good value for money, keep reading to learn about the industry leaders.
What is a Press Brake?
A press brake is a key machine tool that bends metal sheets and plates by applying heavy pressure. It has a crucial part in industries like automotive, aerospace, and heavy equipment production where bending metal is needed to shape parts with accuracy and strength. Unlike a panel border that uses rollers and fingers to create bends, the main job of a press brake is to turn flat metal sheets into custom shapes with heavy hydraulic pressure. It’s a must-have tool for metal workers dealing with different metals such as steel, aluminium, and brass.
The press brake works with two main parts: the upper die (or punch) and the lower die (or V-die). The upper die moves and has a pointed or angled tip that pushes down on the metal sheet. The lower die stays still and has a V-shaped groove where the metal plate sits. When pressure is applied, the punch forces the metal into the V-die bending it where the two dies meet. These dies can be customized to create different angles and shapes, depending on what’s needed and the type of bend required.
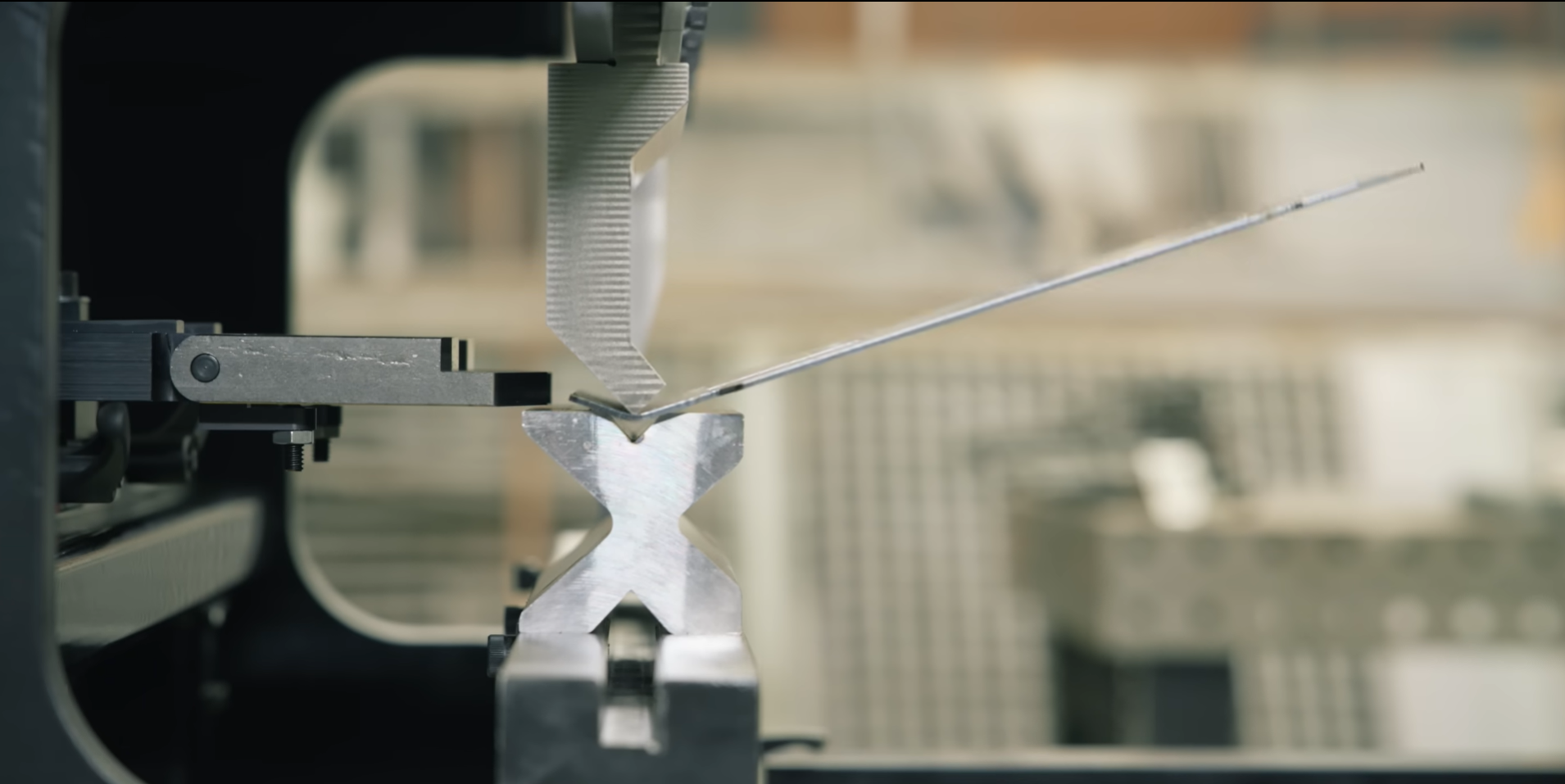
Today’s press brakes come with cutting-edge tech like CNC (Computer Numerical Control) systems, which boost their capabilities. CNC controls allow the press brake to make super-precise consistent bends. This makes them perfect for high production efficiency or custom work where you need to be spot-on.
CNC systems have control over things like punching machines that control how deep the punch goes, the angle of the bend, and even where the metal sheet sits. This ensures every bend hits the exact specs. What’s more, press brakes now often have automated back gauges and laser measuring systems. These upgrades make them even more accurate and productive by cutting down on the need to adjust things by hand.
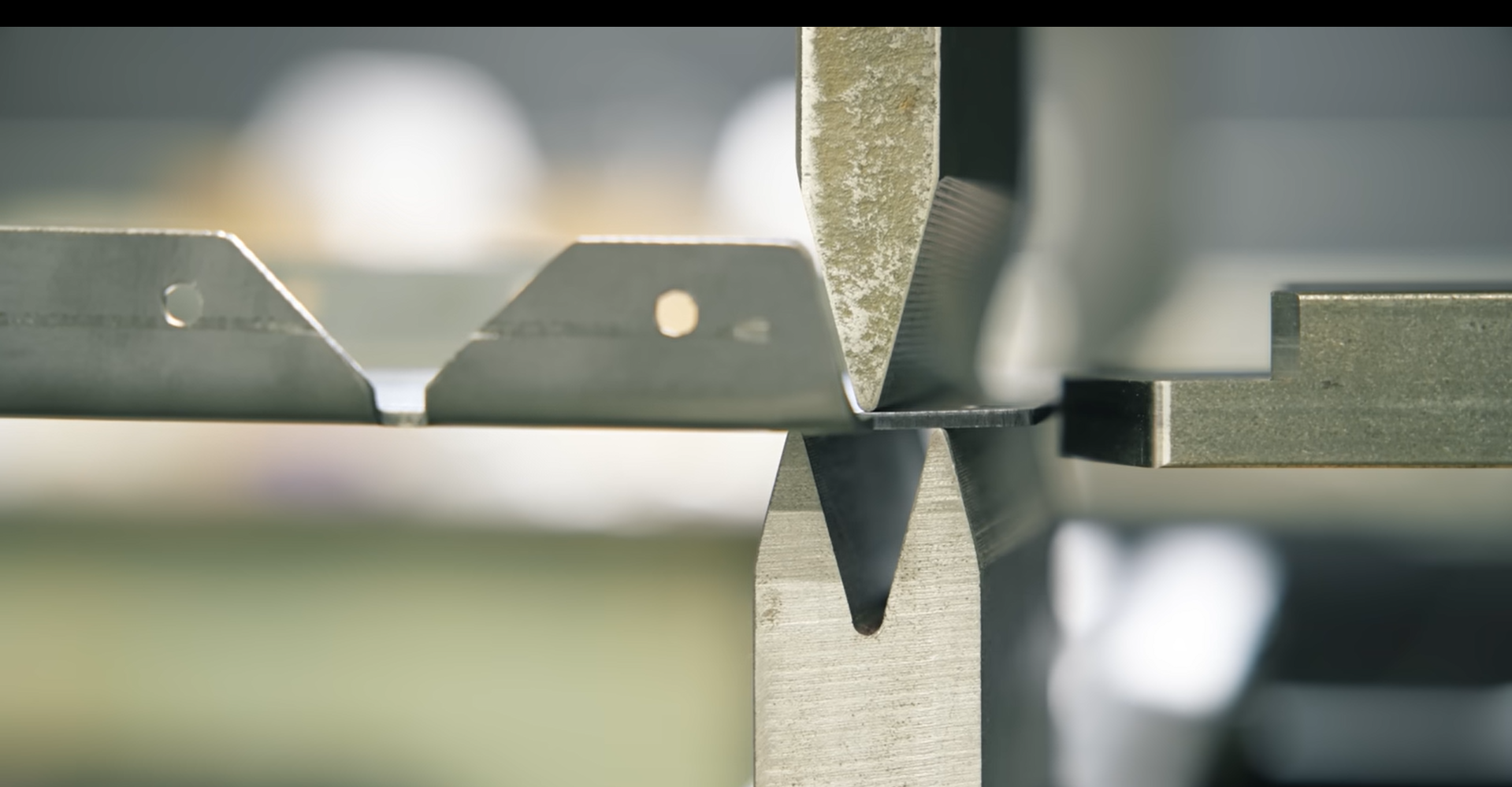
Press brakes stand out because they can handle many types of materials and thicknesses. They can bend everything from thin aluminium sheets to thick steel plates with high precision. By applying pressure and using shaped dies, metalworkers can make all sorts of complex parts. These range from basic brackets to complicated pieces used in high-tech machines.
Press Brake Industry Overview
The global press brake machine market has experienced substantial growth, reaching about $569.1 million by the end of 2021. Experts predict this upward trend to continue at a 6.1% CAGR from 2022 to 2032 fueled by rising demand in sectors like automotive, aerospace, and construction.
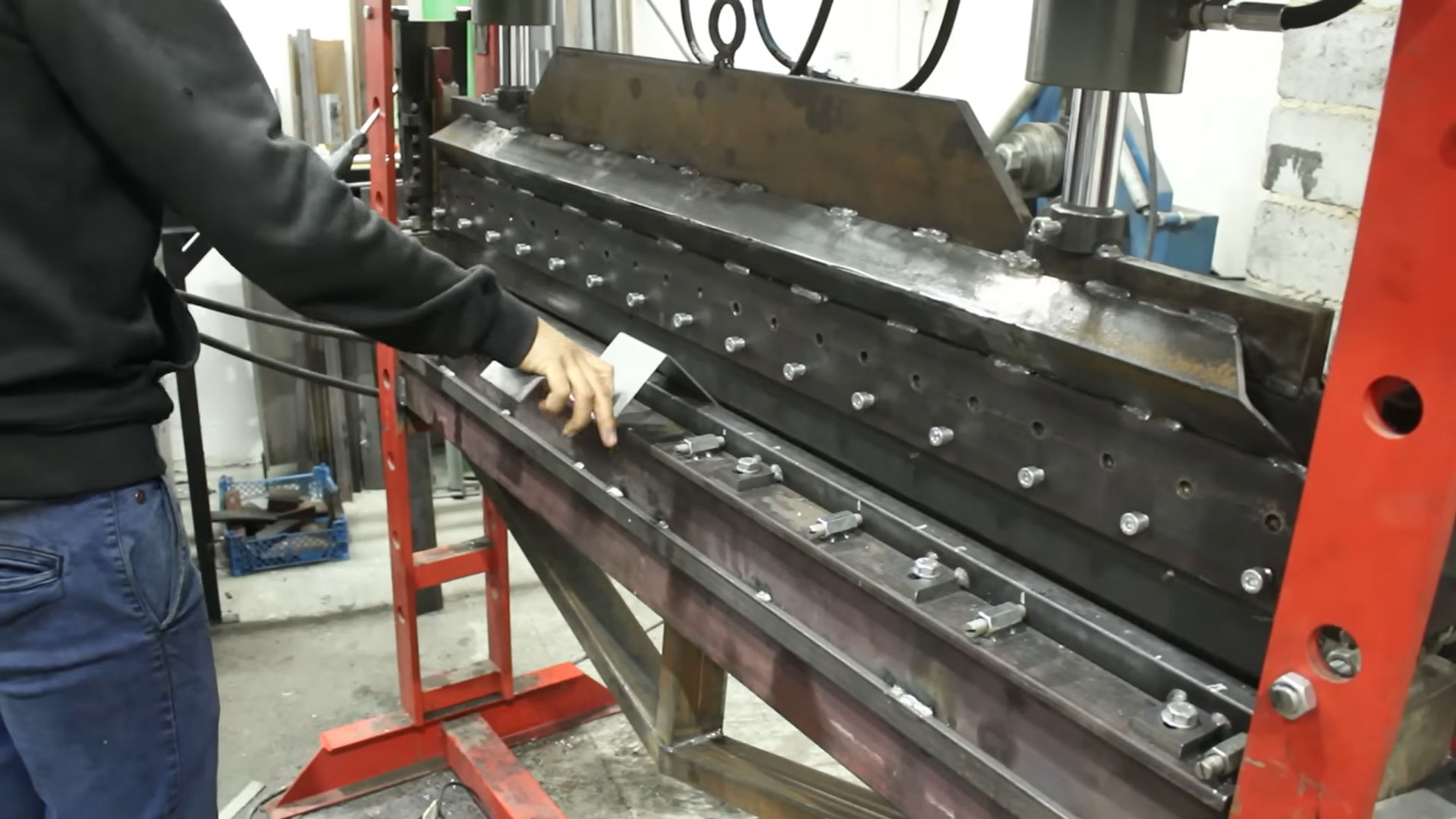
New tech developments, like the addition of hydraulics, pneumatics, and CNC systems, are boosting the accuracy and productivity of press brake machines. Automation is also causing a revolution in the industry by enhancing output and cutting down on labour expenses. With advancements in metal processing, sheet metal processing machinery, plasma cutting machines or laser cutting machines, grinding machines, and punch presses, the bending technology and the bending process evolved dramatically.
The market scene includes several major players with a strong worldwide reach, which creates a lively and competitive environment. As metal shaping becomes more crucial to modern manufacturing, we expect to see more companies using cutting-edge press brake machines, which will spark new ideas in the field.
More automation and the need for machines that can do many things are shaping what’s next for press brake technology in different industries.
Top 10 Press Brake Manufacturers
When you’re picking a press brake maker, your choice can have a big impact on how well your business runs and how successful it is. Let’s check out some of the big names in the field and what they offer.
Amada
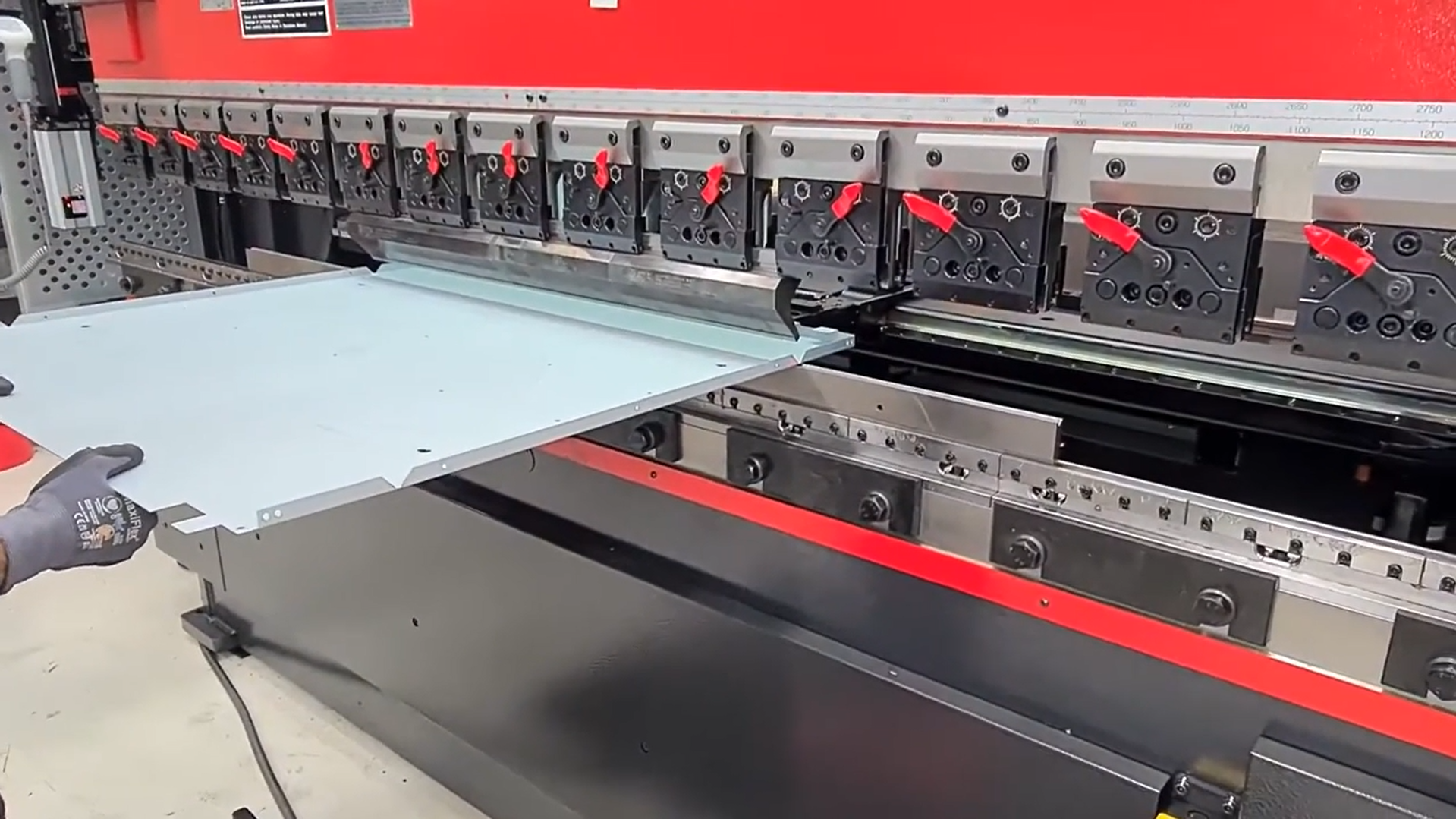
Amada, a top Japanese company, is known for being precise and using cutting-edge tech. If you want CNC-controlled press brakes that can change tools on their own and bend things, Amada has got you covered. They’ve built a name for making machines that last and work well because they put a lot of effort into coming up with new ideas. This means their machines do a great job and keep working for a long time.
Trumpf Inc
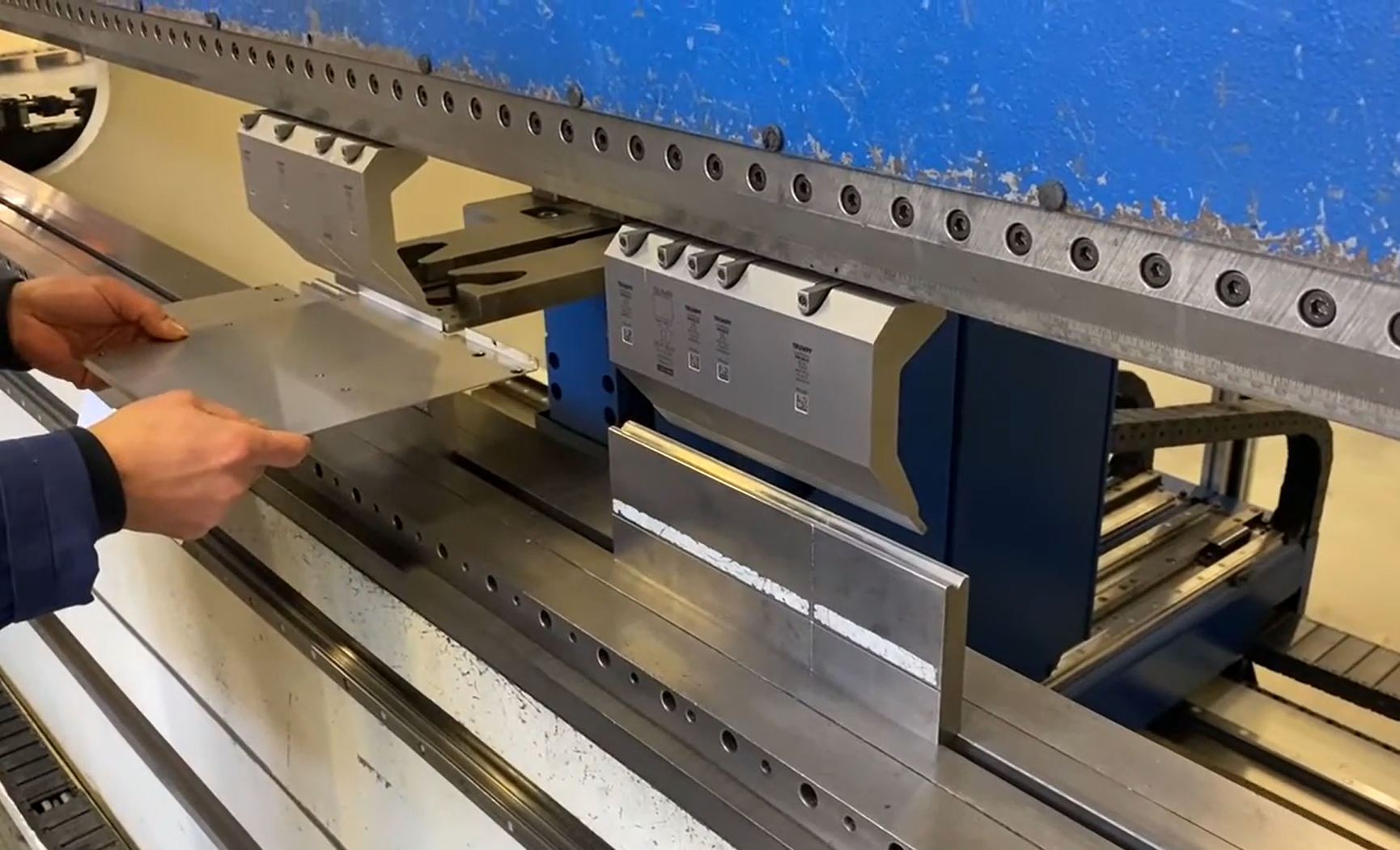
Another key player is Trumpf group, a German company that makes strong, precise press brakes. Their machines have features like bending that adapts angles that measure on their own and systems that prioritize energy efficiency. These aim to boost your operations. You can trust their machines to work well, and they offer good customer help and keep coming up with new ideas.
Accurpress
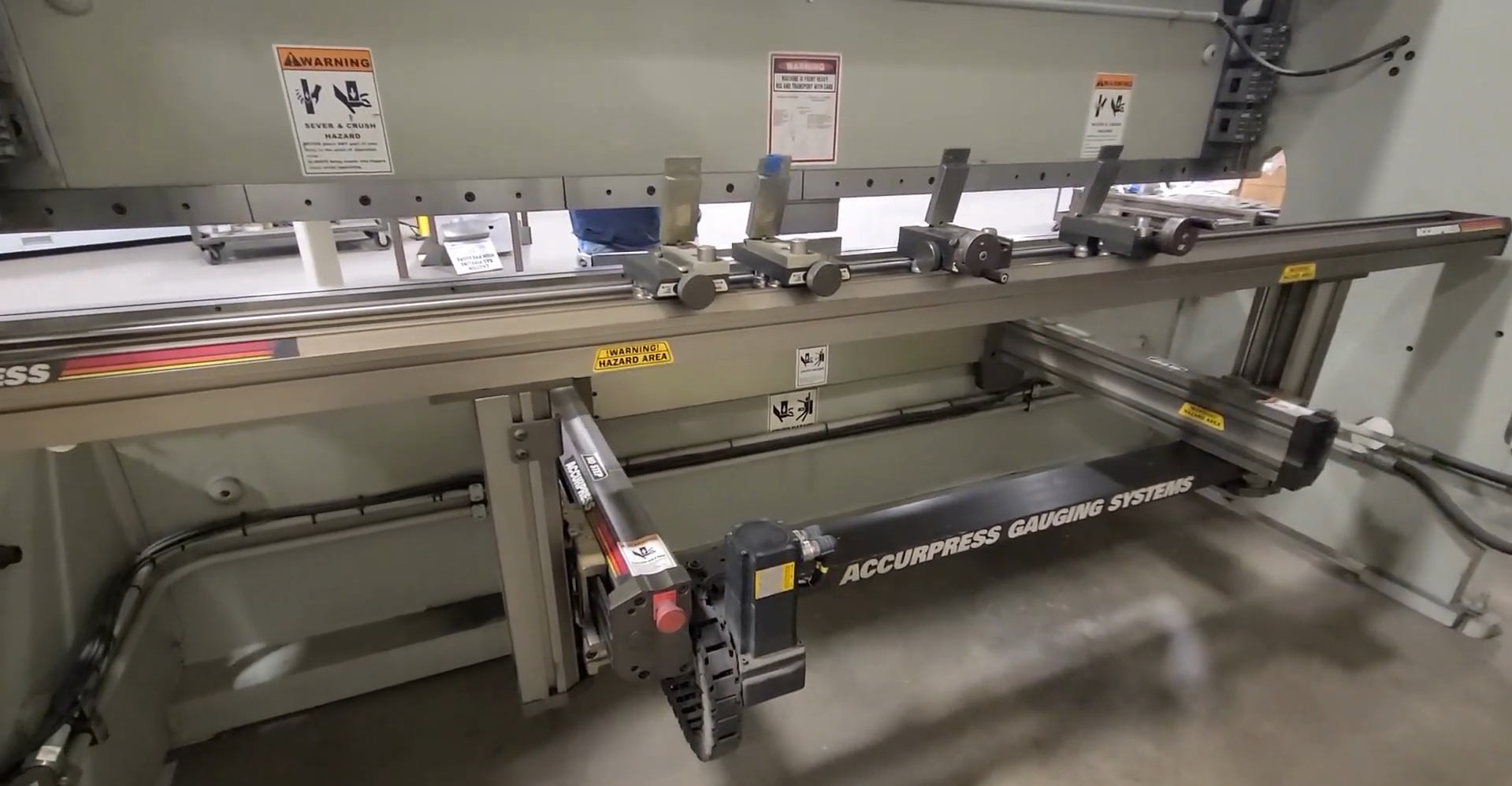
For more than 45 years, Accurpress, from Canada, has been making press brakes that can do many things and last a long time. People know their hydraulic and CNC models for being easy to use and getting a lot done. This makes them a great pick if you want machines that work well for years. Accurpress cares most about making customers happy, and they focus on giving strong support for what they sell.
Bystronic
Swiss manufacturer Bystronic makes high-performance press brakes. These machines are great for companies that need top-notch automation and easy-to-use controls. Bystronic’s dependable equipment suits both small and big businesses. They focus on making high-quality, cutting-edge products that fit each customer’s needs.
Durma
Durma, a Turkish company, offers many types of press brakes. They make hydraulic, CNC, and servo-electric models. People know Durma for making versatile, high-quality machines that last a long time. The company always tries to get better, making it a good pick for businesses that want trustworthy, high-performing tools.
Comco
Comco is known for its compact tube and pipe benders, offering versatile solutions for bending applications. Their machines are designed for ease of use in tight spaces while providing various bending angles and radii. Comco emphasizes quality construction and reliability in their products, making them suitable for HVAC, plumbing, and automotive industries.
AMOB
AMOB manufactures a diverse range of press brakes, including plate rolls and section benders. Their equipment is recognized for robust construction and flexibility in various bending tasks. AMOB focuses on providing high-quality machines tailored to meet specific customer requirements while ensuring efficient production processes.
BLM Group
BLM Group specializes in tube bending machines that incorporate advanced CNC technology for precision bending applications. Their systems are designed to handle complex shapes efficiently while maintaining high accuracy levels. BLM emphasizes innovation in their machinery, providing solutions that cater to the automotive and aerospace sectors specifically.
Baileigh Industrial
Baileigh Industrial specializes in a wide variety of press brakes, including hydraulic and CNC models. Their machines are designed for durability and precision, making them suitable for both small workshops and large manufacturing facilities. Baileigh emphasizes user-friendly controls and robust construction. They also provide extensive customer support and training, ensuring clients can maximize their machine’s potential.
JMT USA
JMT USA is known for its advanced press brakes that combine hydraulic and CNC technologies. Their machines offer high precision and efficiency, making them ideal for various metalworking applications. JMT focuses on customization options to meet specific customer needs. They also emphasize safety features and ease of operation, ensuring reliable performance in demanding environments.
These leading press brake makers are at the forefront of the industry, offering groundbreaking and reliable options. Which one fits your needs the best?
Press Brake Manufacturers: Overview
Manufacturer | Type of Press Brakes | Key Features | Strengths | Weaknesses |
---|---|---|---|---|
Amada | CNC, hydraulic | Known for CNC-controlled press brakes with automatic tool changing. Focuses on precision and durability. | High-quality construction and innovative design. | Higher initial cost compared to simpler models. |
Trumpf Inc | Hydraulic, CNC | Features self-measuring angle adjustments and energy-efficient systems. | Reliable performance and strong customer support. | Advanced features may require skilled operators. |
Accurpress | Hydraulic, CNC | Offers user-friendly hydraulic and CNC models with a focus on longevity. | Strong customer support and ease of use. | Limited advanced automation compared to competitors. |
Bystronic | Hydraulic, CNC | High-performance machines with advanced automation and intuitive controls. | Suitable for both small and large businesses. | May have a steeper learning curve for new users. |
Durma | Hydraulic, CNC, servo-electric | Versatile models with a focus on high-quality construction and continuous improvement. | Reliable performance across various applications. | Limited customization options in some models. |
Comco | Tube benders | Compact designs for tight spaces with versatile bending angles and radii. | Quality construction and reliability in HVAC applications. | Not focused on heavy-duty press brake applications. |
AMOB | Hydraulic, servo-electric | Robust construction with flexibility for various bending tasks. | Tailored solutions for specific customer needs. | May lack advanced automation features found in others. |
BLM Group | CNC tube bending | Advanced CNC technology for precision bending of complex shapes. | Innovation in machinery suitable for aerospace and automotive sectors. | Typically higher cost due to advanced technology. |
Baileigh Industrial | Hydraulic, CNC | Durable machines designed for both small workshops and large manufacturing facilities. | User-friendly controls and extensive customer support. | May not offer as many advanced features as competitors. |
JMT USA | Hydraulic, CNC | Combines hydraulic and CNC technologies for high precision and efficiency in metalworking applications. | Customization options available for specific needs. | Safety features may add complexity to operation. |
Hydraulic Press Brakes
Hydraulic press brakes have an essential function in the metalworking field when you work with heavy-duty jobs and thick sheet metal. These machines can handle high-force tasks, which makes them vital in many industries.
How They Work
Hydraulic press brakes use hydraulic fluid to generate the force needed to bend metal. The liquid gets pressurized inside hydraulic cylinders, which move the ram to put force on the metal sheet. This system gives you exact control over the applied force, which works well for bending tough, thick materials that other systems might find hard to manage.
Applications
When your job requires you to bend thick sheets or heavy-duty materials, hydraulic press brakes will serve you well. You can use them in many industries, like car manufacturing, aerospace, construction, and metal fabrication. They work great for jobs that need a lot of force and accuracy.
Examples
The AHK M 2160 from Knuth Machine Tools stands out as a good example. People know it for how well it works and how much you can rely on it. It handles big, thick metal sheets without trouble. You might also want to look at the AHK M 1230. It offers accuracy and gets the job done fast, making it useful for many different tasks.
Advantages
Hydraulic press brakes pack a punch, making them ideal for tough jobs. You can count on their hydraulic systems to keep performing well over time. Many new models now come with CNC controls, so you can bend metal how you want, time after time. When you need strength and accuracy, hydraulic press brakes are tough to top.
Press Brake Applications
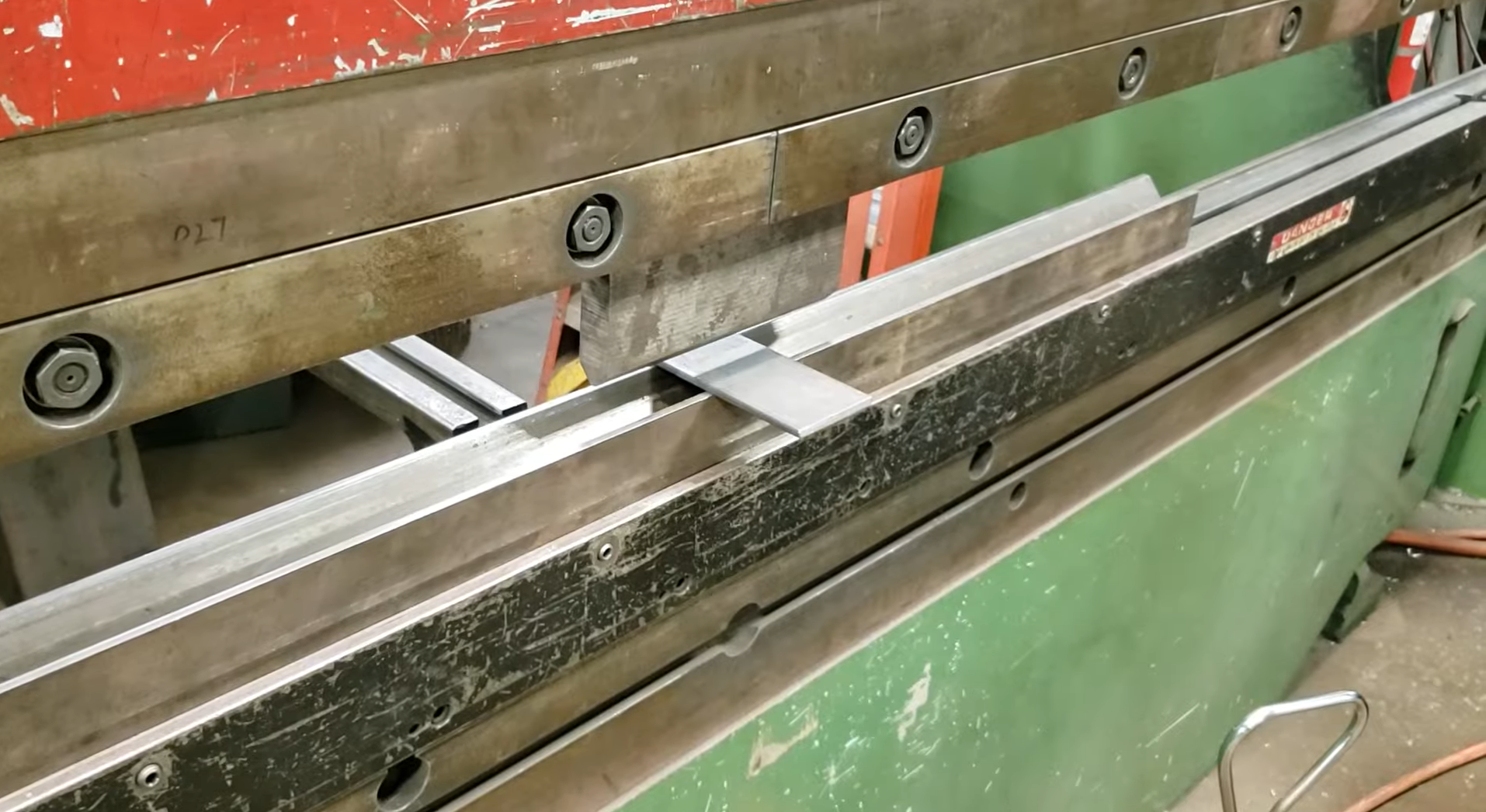
90-Degree Bending (L-Shaped Bending)
This is the most basic and common bending method. It bends metal sheets at a 90-degree angle to create an “L” shape. You’ll find this in making parts like brackets, frames, and enclosures. The simple yet strong 90-degree bend works great for building parts in construction, car making, and machine manufacturing.
U-Shape Bending
U-shaped bending involves bending a metal sheet twice in one go to create a U-shaped channel. This technique plays a key role in making trays, enclosures, and channels you often see in cabinets, metal housing units, and shelves. Car makers also use it to produce parts like suspension brackets or undercarriage pieces. Getting the symmetry and depth of the bend right is crucial to ensure a consistent end product. This is true for structural parts, where exact measurements can affect how things fit together and how much weight they can hold.
V-Shape Bending
A V-shape bend happens when metal gets pushed into a V-die. This creates grooves, channels, or eye-catching patterns. People often use this method in roofing building details, and HVAC ductwork. V-shaped bends let you make sharper angles. They’re common in parts that need precise, crisp angles or grooves. The V’s angle can make the bend point stronger. This makes it great for designs that need to be both sturdy and good-looking.
Z-Shape Bending
The Z-shaped bend needs two distinct bends in opposite directions, creating a Z-like profile. This technique has wide use for brackets, connectors, supports, and architectural fixtures where parts must connect at different planes or offer structural support with offset sections. Z-bending shows up often in sheet metal ductwork electronic chassis designs, and construction materials.
Hemming
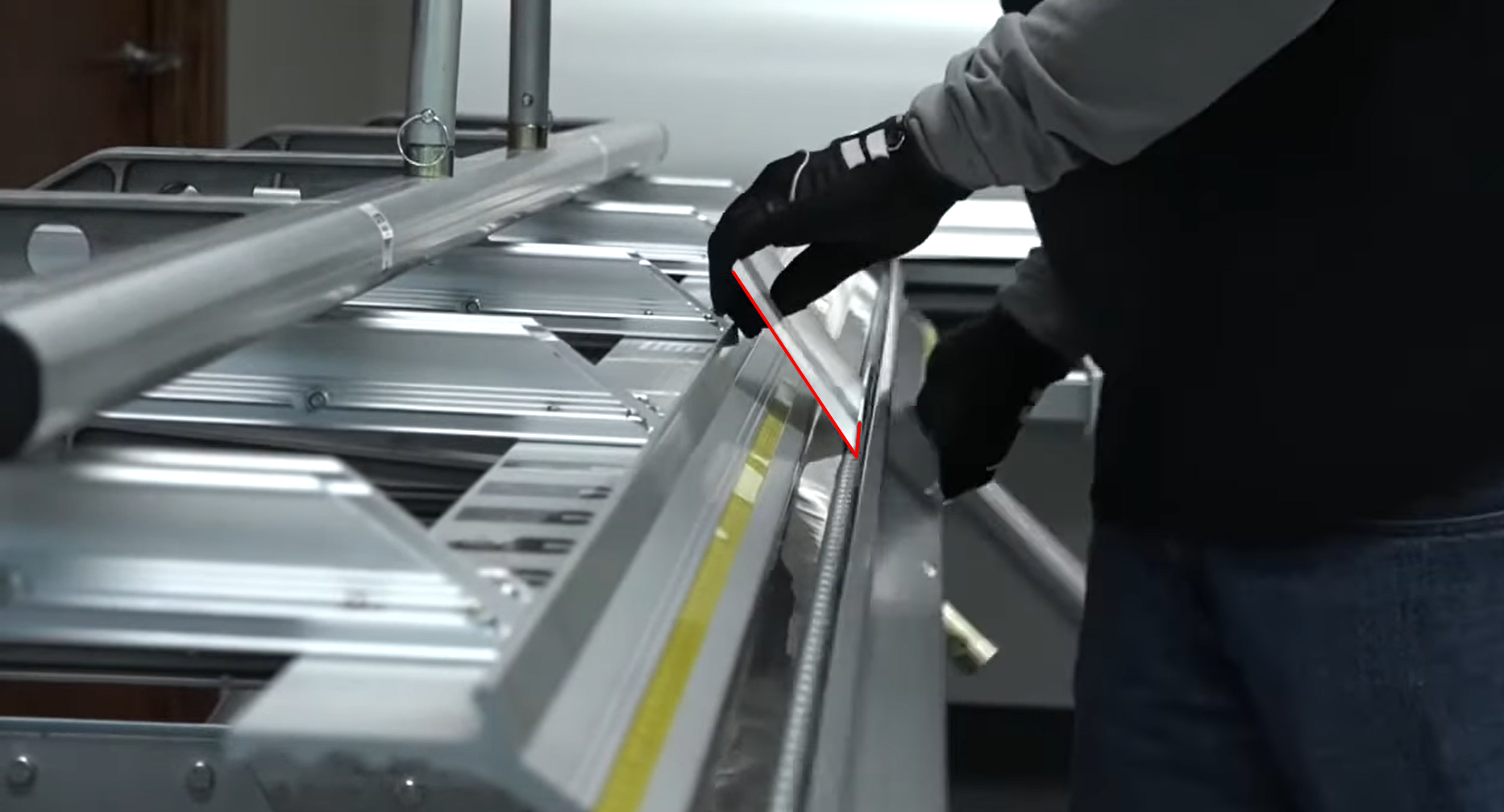
When you hem metal, you fold the edge over on itself. This creates a smooth round edge. Many industries use this method. Car makers and appliance builders often hem metal to make edges safer and stronger. It stops cuts and removes sharp edges. Hemming also makes thin sheets sturdier. You’ll see it in doors, hoods, and panels. It helps prevent warping and makes things look better. If you want even tougher edges, you can use double hemming.
Forming Complex Curves
Press brakes do more than just make simple bends—they can shape complex curves and multi-angle forms. This ability has a big impact on custom metal fabrication, artistic metalwork, and fields like aerospace or automotive, where you need detailed curved parts. To make custom pieces such as curved panels, chassis parts, or even building elements, you can adjust the bending force, dies, and tools to create smooth curves and complex shapes.
Customization Capabilities
Companies that make hydraulic press brakes know that each industry has its own special needs. That’s why they give you lots of ways to customize your machine:
- Range of Models: You can pick from many different types. If you work on small projects, you’ll find compact press brakes for precise control. If you need something for big industrial work, they have large, tough press brakes for high-volume production.
- Drive Types: You get to choose between hydraulic, electric, or servo-electric drives based on what you need. Hydraulic drives work well for heavy jobs. Electric drives save energy. Servo-electric drives give you accuracy and don’t need much upkeep.
- Automation Solutions: Adding CNC controls or robotic arms to your setup can boost your operation’s output. These features make things more precise, smooth out work processes, and cut down on manual work. They’re great for tasks that are repetitive or need high accuracy.
- Tooling Options: To work with different materials and bending jobs, changeable tooling makes sure your press brake can meet the exact needs of your project. This works whether you’re dealing with thick steel plates or thin aluminium sheets.
- Safety Features: You can put safety first for operators by adding things like light curtains, safety guards, and emergency stop systems to your machine. This makes the workplace safer without hurting how well the machine works.
After-Sales Services
When you buy a press brake, it’s crucial to think about the full range of technical support the makers provide. This support covers regular upkeep, quick fixes, and easy-to-get replacement parts to keep your machine running with little downtime.
Also, expert help and training for operators are key, allowing you and your team to use the equipment. Good support after the sale not only improves how well your press brake works and how reliable it is but also makes you happier with your purchase and more likely to stick with the brand, making your investment even more valuable.
Technological Advancements
The press brake industry is alive with new tech, and if you’re into this field, you’ll find these new ideas pretty cool. Companies are now using advanced tech like servo-electric drives, which give you great control and don’t cost much to keep up. These drives use less energy and let you bend things just right, which is perfect for jobs that need to be super exact.
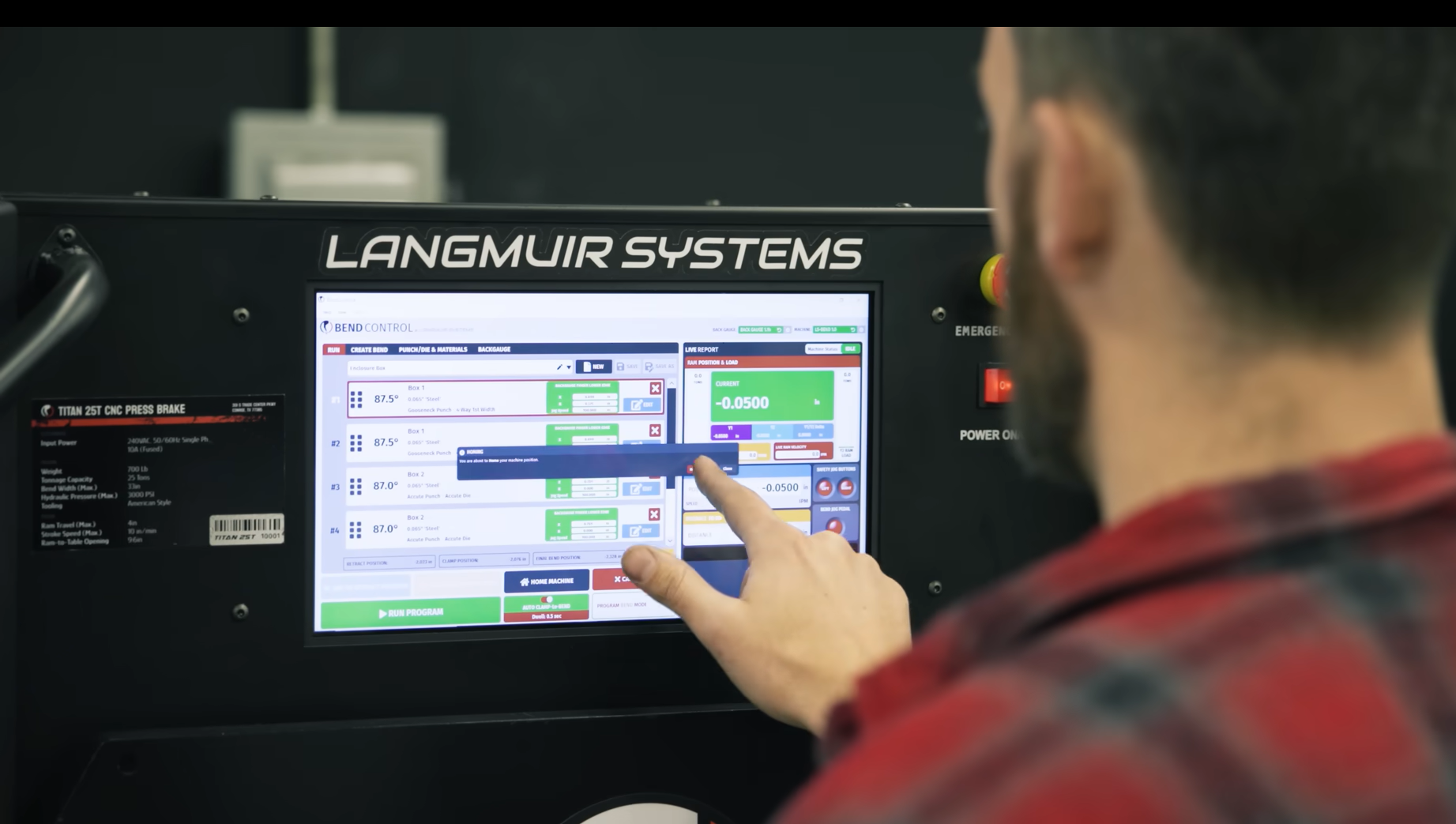
Systems that work on their own are also changing the game, making bends more accurate and saving you time and money. With tools like robot arms and computer controls, these systems can do precision bending jobs with little help from people, which means you can make more stuff, and it all turns out the same.
Companies that make hydraulic press brakes are putting a lot of money into coming up with new ideas. They want to see how far they can push what these machines can do. This means creating smarter equipment with better sensors and AI that can change how it works based on the metal and bending needs right away. These new ideas don’t just make press brakes work better and faster. They also allow people to take on custom jobs and tricky metal projects that weren’t possible before.
Future Trends in Press Brake Manufacturing
Technological Advancements
New tech shapes the press brake industry. Servo-electric drives bring better control and need less upkeep, making press brakes more exact and productive.
Research and Development
To keep up, makers put a lot into research. They aim to boost machine performance, add new features, and meet changing market needs.
Automation and Robotics
More companies now use automation and robots. These tools improve bend accuracy, cut down on human mistakes, and save time and money. Many modern press brakes now come with automation systems, like CNC controls and robot arms.
Industry 4.0 Technologies
Industry 4.0 technologies, like IoT (Internet of Things) and AI (Artificial Intelligence), are causing a revolution in press brake operations. These technologies help monitor in real time, predict maintenance needs, and improve data analysis. This leads to smarter and more productive manufacturing processes.
Sustainability and Environmental Awareness
Press brake manufacturers now pay more attention to sustainability. They work hard to cut down on energy use and waste. This includes creating press breaks that use less energy and adopting practices that are good for the environment. For example, they use lubricants that break down and recycle leftover materials.
Conclusion
The press brake industry stands as a key part of the metalworking field, with manufacturers fulfilling a crucial role in meeting industrial needs. Leading press brake makers like Amada, Trumpf, Accurpress, Bystronic, and Durma have built strong market positions through their focus on new ideas and top-notch products.
The industry looks set to keep growing, pushed by tech progress and changing industrial demands. To stay successful, manufacturers need to remain competitive and adjust to the shifting scene. If you’re in the market for top-quality laser-cut parts for machines such as press brakes or bending machines, think about teaming up with BaisonLaser.
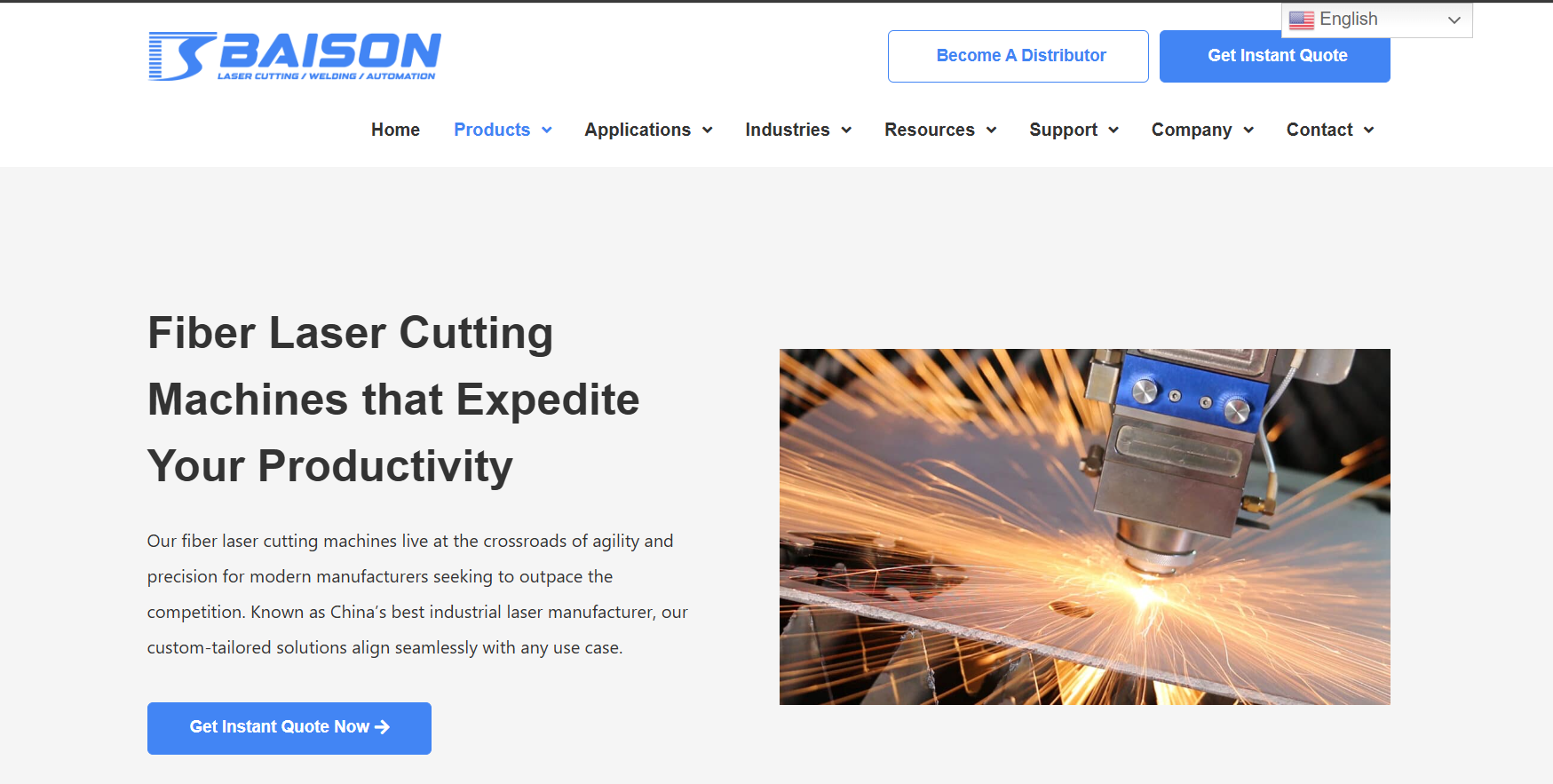
Our production plants with powerful laser machines can boost the performance and reliability of your machinery. Get in touch with BaisonLaser now to find out how their solutions can support your industrial needs and help you stay ahead in the tough market.