Lean manufacturing is a production strategy to maximize efficiency and reduce waste in traditional manufacturing methods. Laser marking machines can be an essential part of any lean manufacturing process.
Laser machines can efficiently add identification codes and other signs that can be used in analyzing and streamlining all aspects of production. It minimizes waste, such as overproduction, waiting times, excess inventory, unnecessary motion, defects, and unused employee potential.
Laser marking means using a laser beam to etch or engrave a mark or code onto a product or material. It is a non-contact, high-precision, and non-invasive method of marking that is increasingly being used in manufacturing for product identification, traceability, and branding purposes.
This article will discuss how applying lean manufacturing principles can benefit businesses and how manufacturers can improve quality and profit using laser marking machines.
We will discuss lean manufacturing, its benefits, and how it can be implemented in business to gain profit and reduce costs. We will also see how laser marking machines’ automated systems eliminate jobs and help you embrace lean manufacturing principles.
What Is Lean Manufacturing?
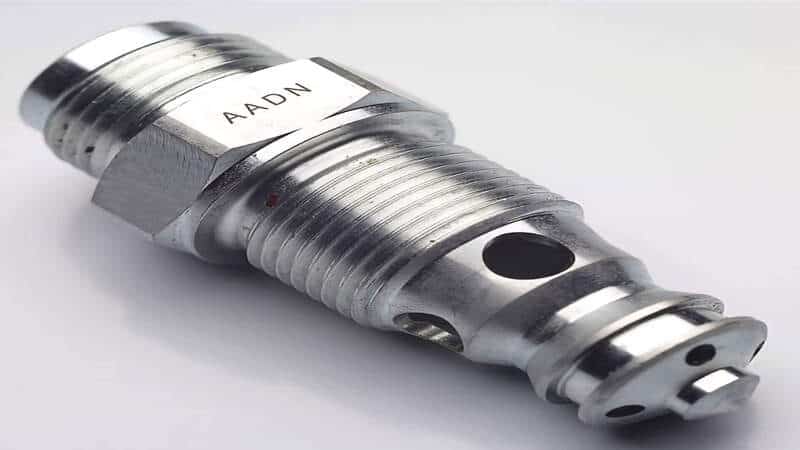
Lean Manufacturing is the production and management philosophy that advocates reducing waste to increase profit, customer satisfaction, and product quality. As its proponents define, lean manufacturing is a way to do more with less.
It became popular in the 1940s when Toyota adopted this manufacturing process. It has become popular in businesses to improve profit and reduce waste.
The idea of lean manufacturing is based on the core principle of how to get more profit by exercising continuous improvement, That is, to produce high-quality products with minimum cost. and to improve customer satisfaction.
For lean manufacturing businesses, map out their value stream and identify areas where they can reduce costs. They implement layout changes to ensure better product quality, traceability, and how the material is handled to reduce waste.
What are some benefits of Lean Manufacturing?
Let’s look at some of the benefits of lean manufacturing:
1. Reduced Costs
The principle of lean manufacturing is to reduce costs. It aims to reduce costs by better-managing inventories and reducing waste material and unnecessary processes.
2. Improved quality
While it aims to reduce cost but not at the price of quality, it emphasizes improved quality and keeps improving product quality and management.
3. Increased efficiency
By streamlining the management and reducing the cost, the system increases efficiency. Lean manufacturing increases overall efficiency and productivity.
4. Better Customer Satisfaction
Less cost, better product quality, and efficiency translate into better customer satisfaction. Better management efficiency, less time, and less waste aim to improve customer satisfaction.
5. Improved Employee Morale
All of the above benefits empower the management and ad causes better customer relations and overall flourishing businesses.
6. Better Tracking of the Production Process
The principles of lean manufacturing require eliminating inefficiencies through better management systems. It encourages a visual management system that makes it easier to track processes and materials. This real-time tracking provides information on production status.
How Does Laser Marking Impact Lean Manufacturing?
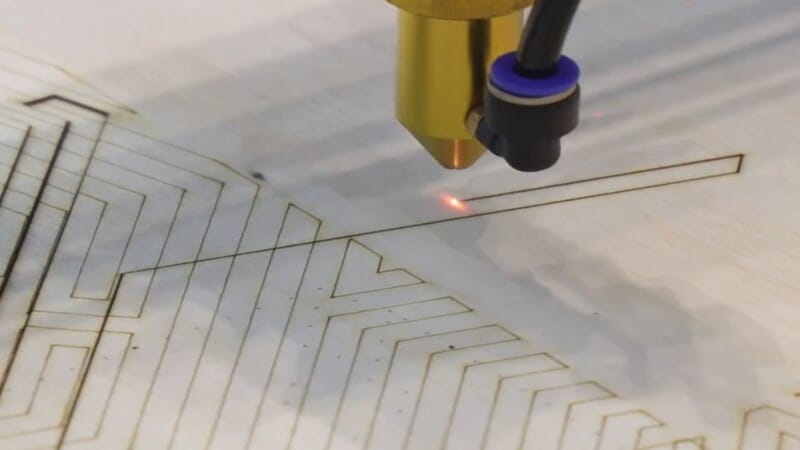
Lean manufacturing stresses a visual management system that laser marking systems provide. Laser marking implies adding a tracking system and codes to the products. Laser machines are the most accurate and efficient way of labeling products. These codes and serial numbers help streamline production quality. Here is how laser marking effect lean manufacturing:
Faster and More Precise Marking
Laser marking is a fast and accurate way to mark products, which can help reduce cycle times and increase productivity. This can help lean manufacturing by reducing the time and cost associated with the marking process.
Reduced Material Waste
Laser marking is a non-contact process, so there is no need for any consumables like ink or labels. This can help reduce material waste and lower costs, an important goal of lean manufacturing.
Improved Traceability
Laser marking can produce permanent and highly readable markings, improving product traceability throughout manufacturing. This can help reduce errors and improve quality control, which is important for lean manufacturing goals.
Customization and Flexibility
Laser marking can mark various materials and shapes, providing greater flexibility and customization options. This can help lean manufacturing by enabling manufacturers to respond more quickly to changing customer demands and market trends.
Laser marking can help lean manufacturing by improving efficiency, reducing waste, improving quality control, and providing greater flexibility and customization options.
What Is the Basic Principle of Lean Manufacturing?
Let’s look at some of the methods of lean manufacturing:
Streamline Production Process
A key principle of lean manufacturing is to streamline the production process. It is done by identifying and eliminating any steps or activities that do not add value to the final product.
Streamlining the production process helps manufacturers to reduce lead times and increase production output. It affects the overall product quality and improves it by identifying and eliminating activities that do not add value to the production process.
This unnecessary movement can be overproduction or waiting time before the next batch is complete. Streamlining means the product does not wait, but manufacturers are continuously identifying opportunities for improvement.
Lean manufacturing also stresses the need to improve the use of Kaizen continuously. Kaizen means continuous improvement. It means implementing changes to make the process more efficient and effective.
Some specific ways that lean manufacturing can help streamline the production process include:
- Implementing just-in-time (JIT) inventory management systems to reduce excess inventory and reduce the need for storage space.
- Implementing visual management systems to make it easier for workers to identify issues and make improvements in real time.
- Standardizing work processes to improve consistency and reduce errors.
Coding and Marking Systems
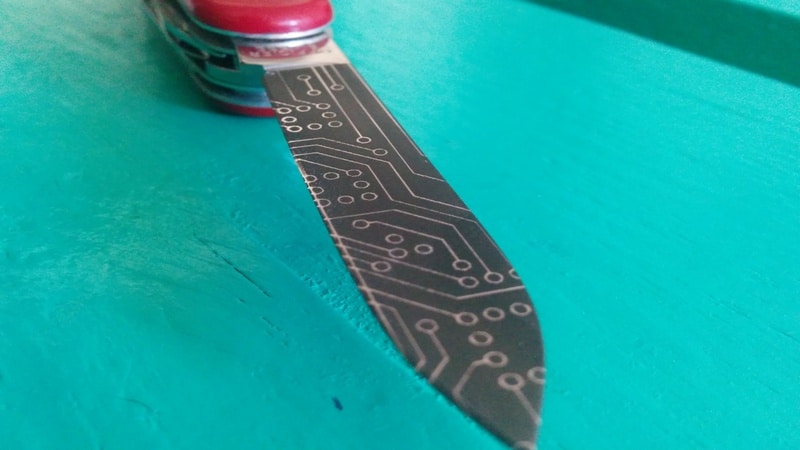
Coding and marking systems are important in lean manufacturing as they help ensure that products are accurately labeled and tracked throughout production. These solutions involve using specialized equipment like Laser marking machines to apply mark or engrave unique identification numbers and other markings to products.
Using these coding and marking solutions, lean manufacturing facilities can ensure that their products are accurately labeled and tracked throughout production, reducing errors and increasing efficiency.
Reducing Unnecessary Manufacturing Waste
Manufacturing waste is anything that does not add value for which customers are unwilling to pay. By reducing waste, manufacturers can improve product quality and reduce pricing.
Identifying Excess Manufacturing waste
Another practical way to implement lean manufacturing is by reducing manufacturing waste. It can be a waste of time or resources with an efficient marking system.
It means identifying the steps that are not needed, and you can easily eliminate them from the streamlined production process. It can not only reduce production time as no time is wasted on unnecessary steps and improve productivity.
Types of Manufacturing Waste
Here are some types of manufacturing waste:
- Unnecessary production
- Excess inventory
- Unnecessary movement
- Waiting
- Defects that require costly repairs
Automated Coding Solution
As mentioned, modern production lines demand streamlining production processes. This can only be achieved by coding and marking. By marking identifications manufacturer can identify the product.
Automatic Identification and Data Capture
Human intervention in tracking data and identifying objects takes a long time. It requires lots of human resources, time, and money. Plenty of coding automation software can be used to limit manual data entry, thus reducing costs.
Automatic identification and data capture (AIDC) solutions refer to technologies that automatically identify and track objects or data. It means adding barcodes or unique biometric identifications to the products so that manufacturers can track them in less time with less waste of time and resources.
It plays a major role in reducing waste and improving efficiency. It also helps streamline the production process and minimize inventory holding costs.
Optimizing Automated Production Line
Optimizing modern production lines requires a systematic approach that involves analyzing the current system, identifying areas for improvement, and implementing changes that can enhance productivity and efficiency. Here are some steps that can help optimize modern production lines:
- Map out the current production line: Before making any changes, it’s important to clearly understand the existing production line. This includes the flow of materials, the sequence of operations, and the machines and equipment involved.
- Identify bottlenecks and inefficiencies: Once the current production line is mapped out, identify bottlenecks and inefficiencies slowing down the process or causing waste. This may involve analyzing data on cycle times, machine downtime, and defect rates.
- Develop an improvement plan: Based on the analysis, develop an improvement plan that addresses the bottlenecks and inefficiencies. It may also include redesigning the layout of the production line and introducing new equipment that is more efficient and modern.
- Implementing Continuous Improvement Ideas: Once the plan is developed, implement the changes on the production line. This may involve training operators on new equipment or processes, reorganizing workstations, or modifying the production schedule.
- Monitor and measure results: After implementing the changes, monitor and measure the results to ensure that the improvements achieve the desired outcomes.
- Continuous improvement: Finally, optimizing modern production lines is an ongoing process. It requires continuous monitoring and implementation of improvements.
Embracing Value-Added Production Processes
Another key principle of lean manufacturing is embracing a value-added production process. It means focusing on the steps that add value to the final product while eliminating or minimizing non-value-added steps. It is aimed at maximizing efficiency and reducing wastage.
By embracing a value-added production process, manufacturers can reduce costs, improve quality, and increase throughput. By eliminating non-value-added steps, manufacturers can reduce lead times, improve delivery times, and improve customer satisfaction.
Improve Profitability with the Theory of Constraint
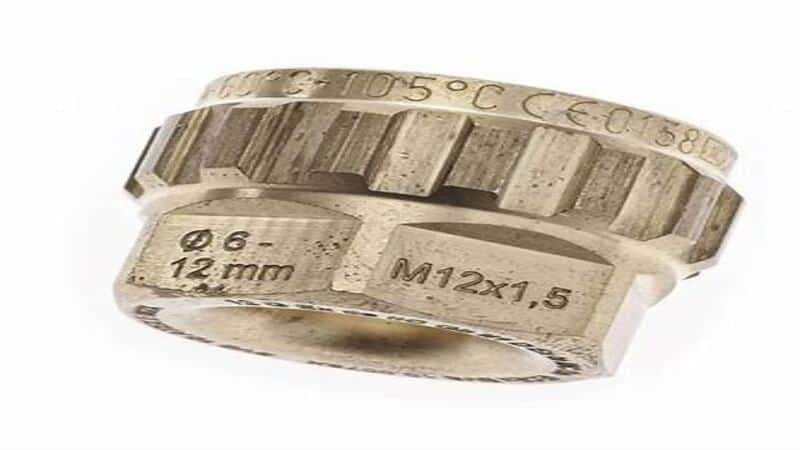
Another management theory that can be combined with lean manufacturing is the theory of constraint. Eliyahu M. Goldratt developed the theory of Constraints in the 1980s. The theory lays stress on finding constraints that are restricting performance and are hindering the system from producing at its maximum capacity.
The goal of the theory of constraint is to identify the constraint and then manage the system in a way that optimizes the performance of the constraint. It aims at improving the overall performance of the system.
In lean manufacturing, the TOC is used to identify the constraint in the production process, often called the bottleneck. Once the bottleneck is identified, lean manufacturing techniques such as Kaizen and Just-in-Time (JIT) can optimize the bottleneck’s performance and increase the production process’s overall efficiency.
Benefits of Theory of Constraints
Here are some benefits of the Theory of Constraints:
Increased Efficiency
By identifying and addressing constraints in a system, organizations can improve the overall efficiency of their operations.
Improved Decision-Making
It provides a framework for decision-making. Manufacturers can prioritize actions that are more conducive to the overall system.
Better Resource Utilization
By focusing on the constraints that limit performance, TOC helps organizations use their resources better, reducing waste and increasing profitability.
Improved Communication
TOC encourages communication and collaboration between different parts of an organization.
Continuous Improvement
TOC is a continuous improvement process that constantly encourages organizations to evaluate and improve their systems.
Competitive Advantage
Organizations that apply TOC can gain a competitive advantage by improving efficiency, decision-making, resource utilization, and communication.
How to Effectively Utilize Laser Marking Machine Data in Rework Processes
Laser marking machines are the most efficient way to generate data useful for industries reworking defective products. They can help in collecting the data and analyzing it. Analyzing this data can help you identify the key issues and implement some improved rework processes.
Data collection also helps in implementing quality control measures,
By effectively utilizing laser marking machine data in rework processes, you can improve the overall quality of your products and reduce the need for rework in the future.
Why Is Laser Marking Important in Lean Manufacturing?
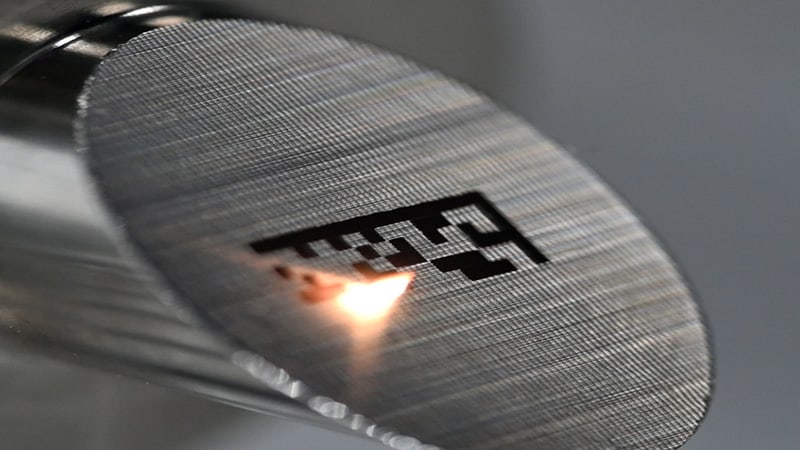
As mentioned, the lean manufacturing model advocates an efficient and modern management system that ensures better customer value, improves production lines, and reduces manufacturers’ waste. It’s a win-win solution for everyone.
Laser marking is essential for streamlining the production line and assigning automatic identification codes and visual management systems. A laser marking system is more efficient than a laser marking system. Laser marking machines can be automated and thus can be used for marking or labeling. It is a fast, efficient, and accurate system.
Laser marking is essential in lean manufacturing because it offers increased efficiency and accuracy. Manufacturers can use laser marking to reduce waste, improve quality control, and increase productivity.
Conclusion
Lean manufacturing is a management system to enhance productivity, performance, and profit. By applying its methods or principles, businesses can streamline their production process.
It involves identifying and eliminating any activities that do not add value to the product or service being produced. By implementing Lean Manufacturing principles, businesses can reduce costs, increase productivity, and improve quality.
A laser marking system is essential for implementing a lean manufacturing system. The machines are fast and accurate. They can mark unique identifications, serial numbers, information, and barcodes for production.
These laser machines are versatile and can mar signs, labels, or small numbers that are permanent. These unique identifications help the modern inventory system, automatic tracking, and data analysis. It reduces the waste of time and resources.
Embrace Lean Manufacturing Principles with Baison’s Laser Marking Machines
If you are looking for laser marking machines to implement lean manufacturing systems in your business, Baison‘s Laser marking machines help streamline the production process and increase efficiency. We offer high-tech laser machines for marking, labeling, or engraving.
Our laser machines can be fully automated. Laser marking machines are user-friendly and a modern solution to add barcode serial numbers or other identification codes to almost all types of material. Baison’s laser marking machines can handle ceramic, paper, plastic, metal, or wood.
So contact us to learn more about our laser marking machines. We offer a free application evaluation to help our customers choose the best laser machine for their business needs.