We will discuss everything in detail to equip you with the correct information for selecting the ideal nozzle for your fiber laser cutting machine. Let’s get right into it!
What Is a Nozzle in Laser Cutting?
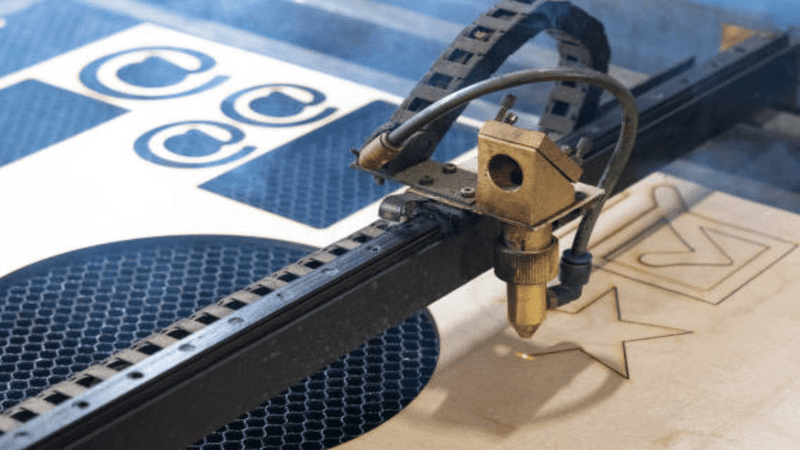
Nozzles play a crucial role in laser cutting, directing the gas flow onto the desired cutting surface. This helps keep all unwanted vaporized or molten material away, ensuring a refined and clean cut. The most common types of nozzles are made from either copper or ceramic, but we can also find other materials for the component.
These nozzles are designed to withstand the high gas pressure and temperature involved in the cutting process. On top of it, manufacturers offer them in a range of different sizes and types to optimize the cutting process.
Hence, any business using a fiber laser cutting machine must work with a suitable nozzle for the workpiece. But for that, we must first understand all the functions a nozzle plays in the cutting process.
What Are the Functions of the Nozzle in Laser Cutting?
Even though a laser nozzle plays various roles in the process, we will only focus on the four main areas. These include:
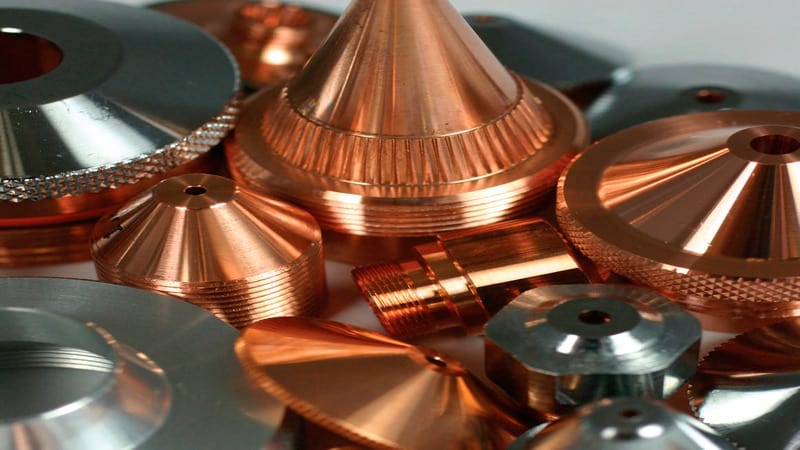
- Laser Beam Alignment: the nozzle is where the fiber laser beam comes out. Hence, it helps align the laser beam in the right direction onto the workpiece material. This ensures it flows in the correct path, producing clean and precise cuts.
- Flow Control: just like fiber laser beam alignment, the nozzle handles the flow control of the gas. It ensures the gas flows in the right amount and direction to remove any vaporized or molten material from getting in the way. You can also control the flow rate to adjust it for maximum optimization when working with different thicknesses and types of materials.
- Cooling: laser cutting process can generate intense heat. For this, the nozzle provides a cooling mechanism that helps prolong the cutting head life and prevents any overheating damage.
- Debris Removal: The flow rate and the type of gas passing through the nozzle help remove vaporized and molten materials from getting in the way of the fiber laser beam. This significantly helps prevent clogging of the cutting head. Most advanced nozzles come equipped with adjustment settings for optimal debris removal.
What Are the Different Types of Nozzles?
The industry sees seven different types of nozzles, which have different specifications. These include:
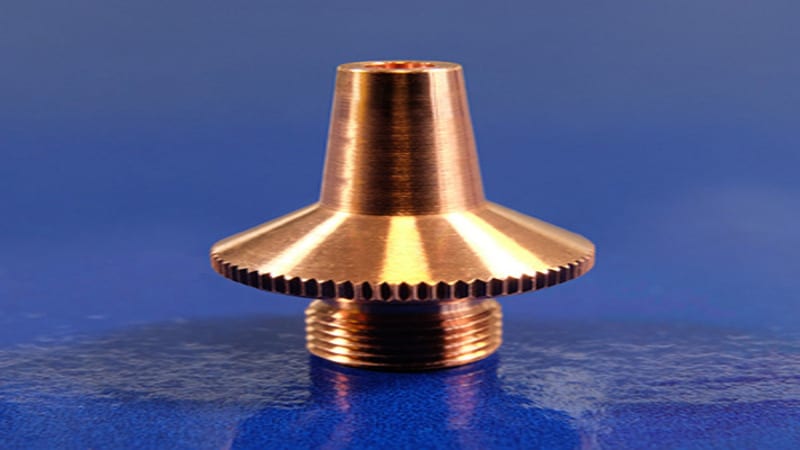
- Straight Nozzle: manufacturers often use a straight nozzle for general-purpose laser cutting. This includes working with materials such as stainless steel, mild steel, or aluminum sheets for signs, electrical parts, and automotive components. If you want to learn about laser cutting stainless steel sheets and tubes, click here.
- Convergent Nozzle: this type of nozzle is used explicitly for intricate cutting of extremely thin materials. For instance, they help achieve higher cutting speed, laser power, and narrow kerf width when working around metal sheets or stainless steel for electrical appliances and medical devices.
- Divergent Nozzle: this type of nozzle offers the opposite of a convergent nozzle. As a result, manufacturers use it to achieve higher laser cutting speed alongside a wider kerf width for thick materials. Examples of divergent nozzles include thick metal and steel plate cutting for shipbuilding, aerospace components, and construction parts.
- Venturi Nozzle: manufacturers who have to cut through materials that produce extensive debris use venturi nozzles. For instance, if you are cutting through wood, composites, or plastics, the venturi helps remove any debris from the cut. This results in fine-cutting quality, minimizing the risk of damage and clogging to the cutting head.
- Flat Fan Nozzle: The auto parts manufacturer readily uses a flat fan nozzle to cut straight, long lines or flat surfaces. Examples include cutting foam sheets, gaskets, and belts.
- Hollow Cone Nozzle: these nozzles are specifically designed for cutting curved or circular shapes. Good examples include cutting through tubes and pipes using tube cutting machines.
- Full Cone Nozzle: if you work around materials such as ceramics, semiconductors, or glass, then you need a full cone nozzle. It helps achieve a high-quality edge finish by evenly distributing gas around the cut. This also helps reduce the risk of thermal damage to the material.
Advantages and Disadvantages of Different Types of Nozzles
In this table, we will discuss the advantages and disadvantages of different types of nozzles to help you choose the right one for your cutting needs.
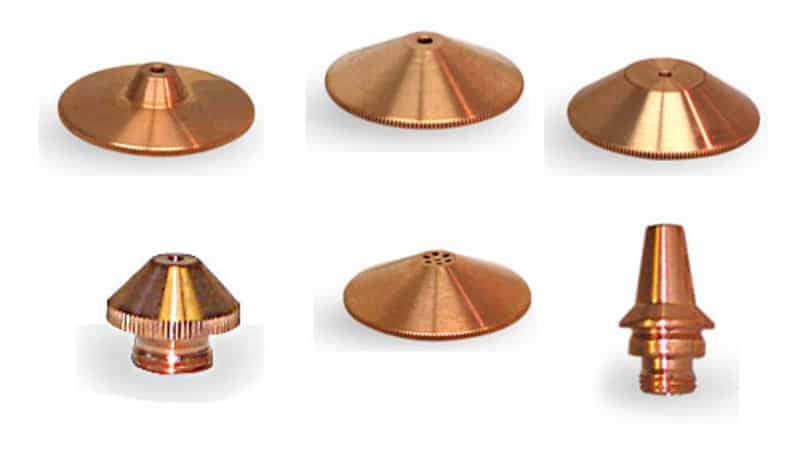
Nozzle Type | Advantages | Disadvantages |
Straight Nozzle | Stable gas flow, versatile, and easy to use | Limited precision and control over the cut. |
Convergent Nozzle | High precision and control over the cut, narrow kerf width, and high cutting speed. | Limited versatility and reduced cutting depth. |
Divergent Nozzle | High cutting speed and deeper cutting depth, suitable for thick materials. | Reduced precision and control over the cut. |
Venturi Nozzle | Effective debris removal, improved cutting quality and reduced risk of clogs. | Limited cutting speed and reduced precision. |
Flat Fan Nozzle | Ideal for cutting long, straight lines or flat surfaces. | Limited versatility and reduced precision for cutting complex shapes. |
Hollow Cone Nozzle | Suitable for cutting circular or curved shapes, with good precision and control over the cut. | Limited versatility for cutting flat surfaces or irregular shapes. |
Full Cone Nozzle | Suitable for cutting high-quality edge finishes on delicate or brittle materials. | Limited versatility for cutting thick or hard materials. |
What Are the Common Issues of Nozzle?
As someone who readily works around nozzles, you must be aware of the common issues that you can face:
- Clogging: clogging happens when excess debris builds up around the nozzle orifice. This dramatically diminishes production capacity and cutting quality. On top of it, clogging also increases cleaning downtime and reduces laser power.
- Corrosion: just like clogging, nozzles also get corroded based on the materials they are made from. This significantly affects nozzle life and cuts quality, and adds to frequent replacement costs.
- Operating Conditions: you must read through the optimal operating conditions for a nozzle as the manufacturer recommends. The operating conditions include temperature, flow rate, and gas pressure. You must ensure everything is within range to avoid any failures, downtimes, and damages.
- Wear and Tear: just like any other laser cutting machine component, nozzles also suffer regular wear and tear. Prolonged use can wear them out completely, so you must always keep an eye out for worn-out nozzles. These can affect the cutting quality and impact the overall productivity of the laser cutting machine.
- Improper Sizing: make sure you are using the right size of nozzle both for your laser system, laser head, and the cutting material. Failing to do so can lead to higher operating costs, decreased nozzle lifespan, and obviously poor-laser cutting quality.
- Improper Maintenance: Regularly maintain the nozzle; otherwise, you can face frequent downtimes and replacement costs. Hence, it is recommended to de-clog the nozzle regularly and ensure it’s clean before cutting. Bottom of Form
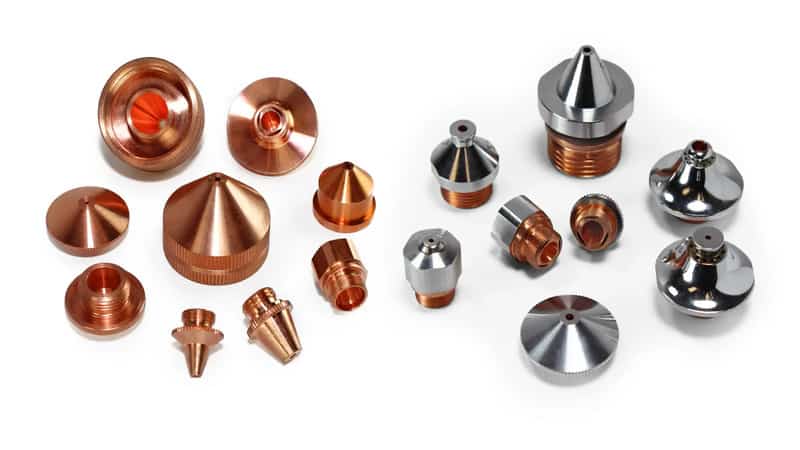
What Should Be Considered When Choosing a Laser-Cutting Nozzle?
Purchasing a nozzle is a crucial decision for a business that frequently uses a laser-cutting machine. But what should you consider when looking out for one? Here are the key factors to keep in mind:
Kerf Width
Kerf width, or the width of the cut in simpler terms, is determined by the nozzle shape and size. You must get the right kerf width for your cutting material to ensure precision cutting.
Nozzle Shape
Not all shapes of nozzles can cut through every material. Hence, it would help if you got the right shape and thickness of the material in question.
Cutting Speed
Different types of nozzles offer varying cutting speed and laser power. If you want fully optimized cutting speed, ensure you are working with the correct nozzle type.
Nozzle Material
This is important because not all nozzle materials are suitable for cutting through different kinds of cutting material. Therefore, you must look at the compatible materials list before deciding.
Cost
You must invest in a nozzle for all the right reasons. This includes knowing the cutting speed, precision, laser power and benefits your business requires. Getting a nozzle that doesn’t offer suitable features isn’t a good investment.
Auxiliary Gas Flow Rate
Consider the auxiliary gas flow rate specifications for the nozzle as they directly impact cutting speed and cutting quality.
Conclusion
Working around a laser-cutting machine isn’t everyone’s cup of tea. There are certain factors that one must consider for optimal machine operations. The nozzle is just one of these vital aspects that you must get right for precision cutting and high productivity.
Consider everything, including the cutting material and its thickness, and then match them with the nozzle specifications. Once done, you will know the right nozzle for your business needs to maximize laser cutting performance.
At Baison, we understand the struggle to maximize laser cutting performance. It is only possible to achieve with perfect knowledge. Therefore, our experts offer customized laser cutting solutions providing a free consultation to ensure you get the right machine and parts for your business needs. Contact us today!