Choosing the appropriate bending machine manufacturing firm is fundamental to enhancing your business efficiency and productivity. From all of the available possibilities, it can be challenging to select the best solution. Honestly, trying to determine whether the company is competent enough to craft the perfect machine can be a bit overwhelming at times.
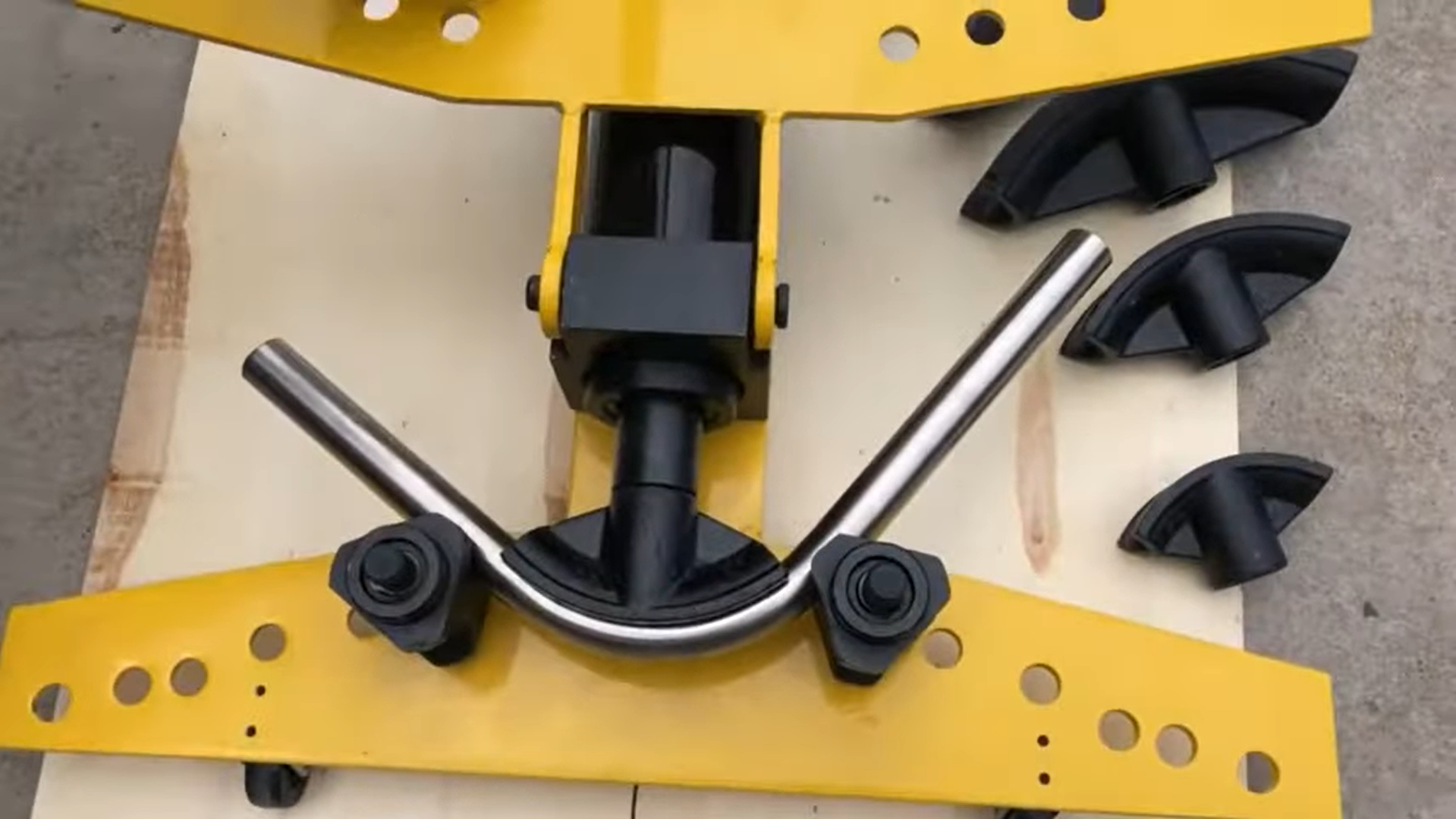
This guide is going to give you an insight into some of the best pipe benders available in the industry, reliable as well as effective. We will touch on a variety of models, both manual and state-of-the-art CNC machines, concentrating on accuracy, durability, and great support. In exposing all your options, you can do research and choose wisely in a way that will increase your production ability.
So, let’s dive in to discover the best bending machinery for your business!
What is a Bending Machine?
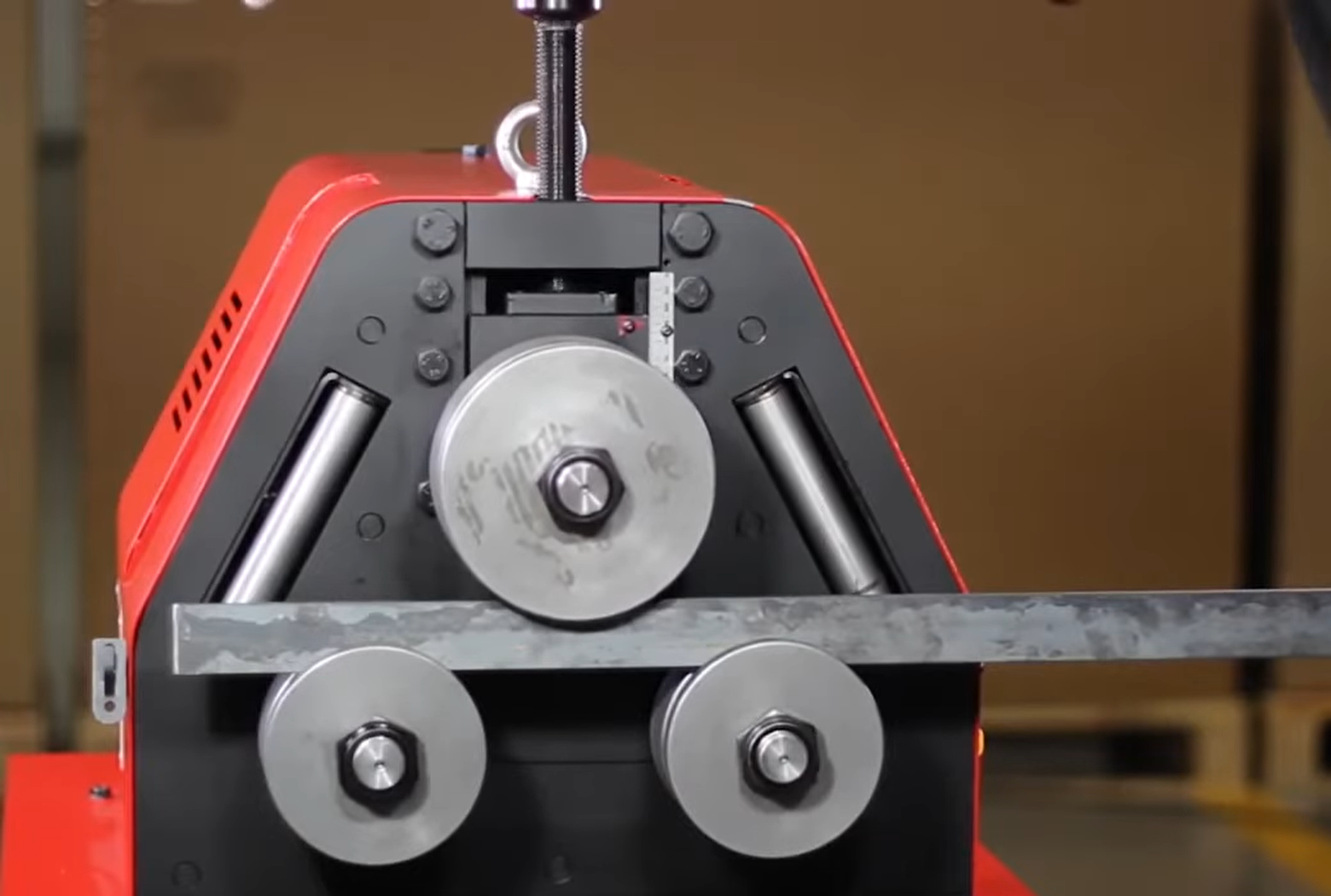
Definition and Uses
A bending machine is a versatile tool for bending and shaping materials like pipes, metal plates, and angle bars. This is especially important in sectors including civil engineering, car making, aerospace, and manufacturing.
Generally, a bending machine does its work by placing the applicable force onto a workpiece to push it to a given angle. To make sure that precision and consistency are undertaken; several tools and dies are utilized. Different types of bending machines are appropriate for varying levels of complexity of the task at hand, especially manual, semi-automated, and fully automated.
If you understand the features and DOM of bending machines, then you can easily figure out what to get for your company.
Types of Bending Machines
Bending machines come in several types, each suited for different tasks and materials. Here’s an overview of roll bending and tube bending machines:
Roll Bending Machine
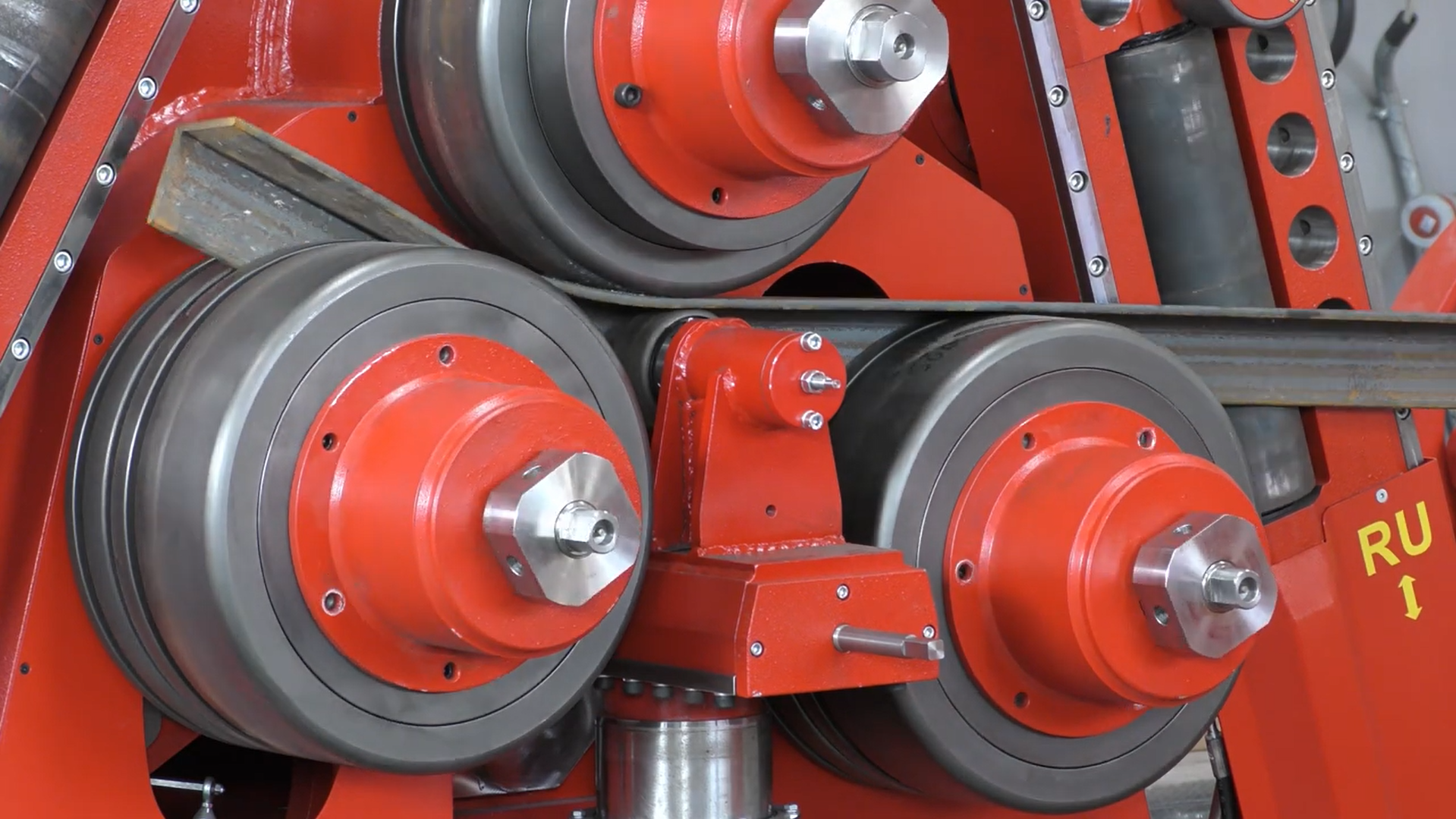
These are used for bending profiles, flat bars, and large pipes or tubes by passing the material inside a series of rolls. The rolls exert force against the material, inducing it to take up some curve or radius. Such burst and more popular roll bending machines make it ideal for forming thinner sheets of metal work.
These are mostly used for roundness production since the radius is quite a large one, thus very useful in buildings, shipbuilding and other manufacturing.
Types:
- Hydraulic Roll Bending Machines: These hydraulic machines are robust and suitable for heavy-duty tasks. They can bend thicker materials with precision.
- Electric Roll Bending Machines: These machines are efficient and precise. They run on electric motors and are mainly used for lighter materials.
Features:
- Adjustable Rollers: Rollers can be set to accommodate various material thicknesses and bend radii.
- Multiple Roll Configurations: Depending on the complexity of the bending task, these are available with two, three, or more rolling gears.
- Automation: Advanced models may include CNC controls for automated and accurate bending.
Applications: Ideal for creating large-radius bends and curves in metals such as steel and aluminum. These machines are widely used in the construction, shipbuilding, and manufacturing sectors.
Tube Bending Machine
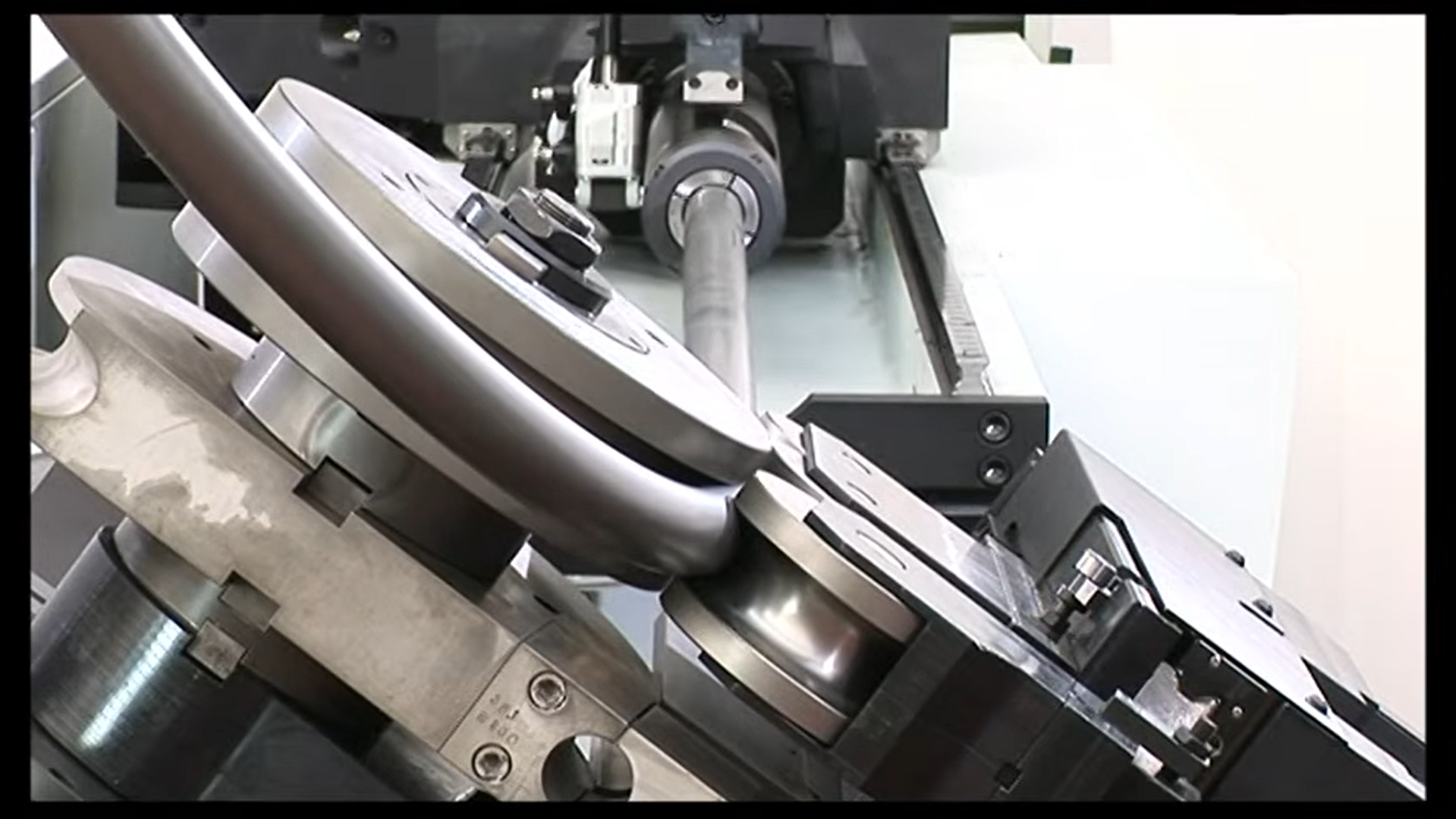
Also known as tube or pipe bending machines, they are manufactured to bend tubes or pipes specifically. To function, the machines clamp a tube and force a bending die to the tube to achieve a bend. These machines are helpful in the fabrication process to achieve accurate bends in tubes and small pipes. They find applications in several industries, such as plumbing, automotive, and aerospace. They’re also seen in other sectors, for example, in exhaust systems and hydraulic lines.
There are different types of tube benders, including hydraulic ones, electric ones, and even advanced tube benders that use mandrel bending for thin-walled tubes.
Types:
- Hydraulic Tube Bending Machines: Utilize hydraulic power for bending thicker and tougher tubes, these are known for their durability and high production capability.
- Electric Tube Bending Machines: They feature electric motors for precise and controlled bending, suitable for complex and delicate bends.
Features:
- Mandrel Bending: A mandrel prevents tube collapse during bending, and it is especially useful for thin-walled tubes.
- Rotary Draw Bending: Clamps the tube and rotates it around a fixed die to achieve precise bends.
- CNC Controls: Many modern machines are equipped with CNC controls for automated and highly accurate bending.
Applications: It is perfect for exact bends in small-diameter pipes and tubes, and it is used in exhaust systems, hydraulic lines, and structural parts.
Read: How to choose the right bending machine?
Key Considerations
When selecting a bending machine, consider these factors:
- Material Type and Thickness: Ensure the machine can handle the specific materials and thicknesses you require.
- Bend Radius and Angle: Choose a machine capable of achieving the desired bend radius and angle.
- Production Volume: Assess the machine’s capacity and speed to fit your production needs.
- Automation and Control: CNC controls can improve precision and efficiency for more complex tasks.
Top 10 Bending Machine Manufacturers
Global Leaders
If you’re looking for a reliable bending for your business, here are some top brands that offer high-quality products across various industries:
TRUMPF: Dedicated hydraulic and electric bending machines that TRUMPF manufactures include TruBend Series 5000, which is flexible and produced bending machines that range in price. Their panel bending equipment has models, including the TruBend Center 7020.
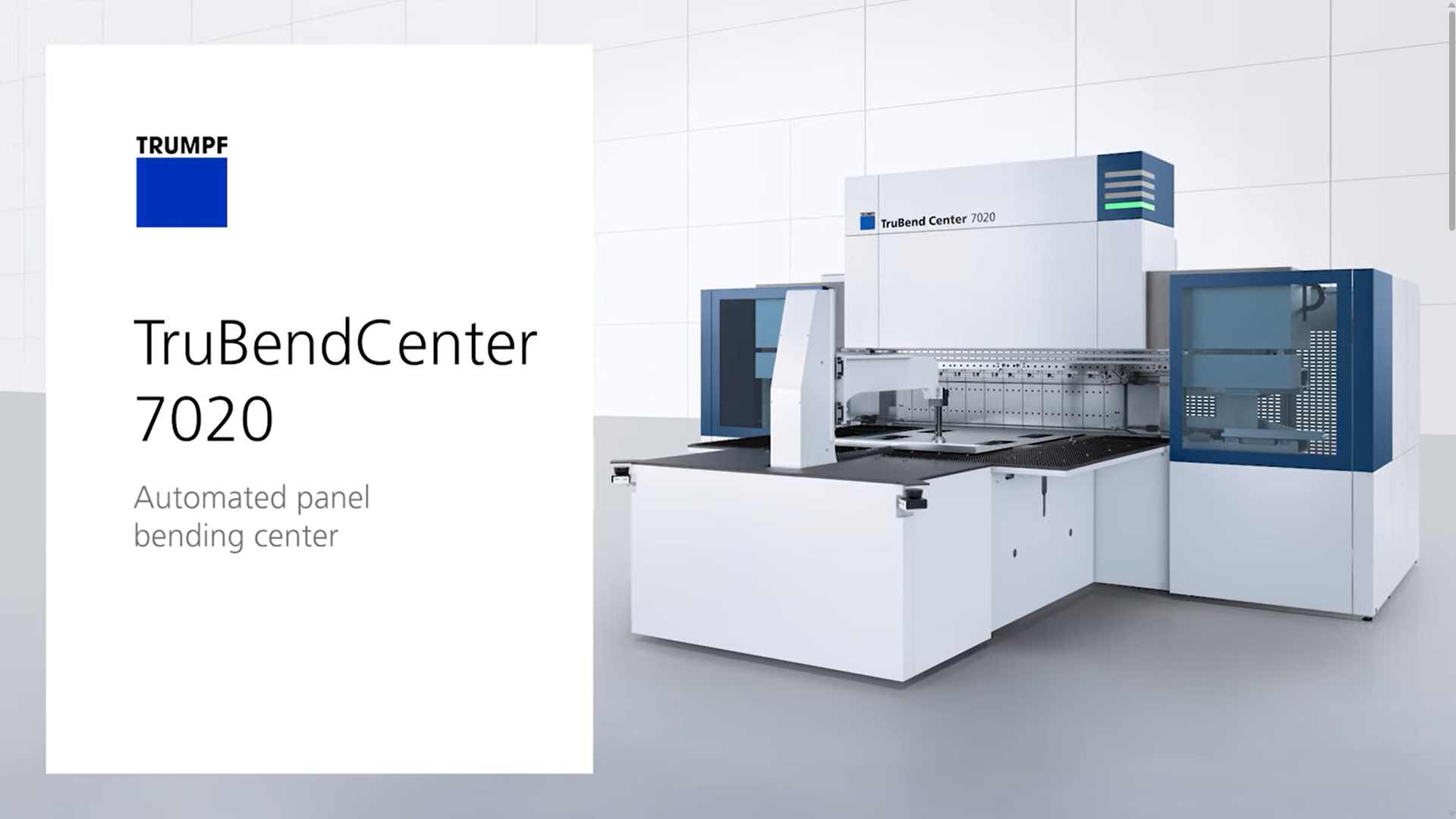
The TRUMPF machines have a variety of modern technologies such as automatic changing of tools and angle measuring devices, which facilitate the work of the operator and enhance the productivity of the below machines.
TRUMPF machines are well recognized to be used with durability, backed with great customer care and support service. The cost is quite different although most of the TRUMPF machines fall in the expensive category as they have complicated features and more reliability.
SweBend: Section bending machines, plate rolls, and applications based machines are some of the bending machines provided by SweBend. Customized options include modifying machine parts that are typically utilized in construction machinery. Sister Company SweBend manufactures heavy-duty machines according to the requirements of the customer. They are ideal for various market applications.
SweBend’s high-performance machines provide a good return on investment. They are competitively priced, offering strong value given their capabilities.
Comco: Comco corporation specializes in CNC tube bending machines, with models like the TMS and KB series for industries such as automotive and aerospace. Comco uses advanced technologies like direct servo motor drives and multi-servo controls. Their benders ensure fast and precise bends. With a focus on high performance, Comco machines are also durable and supported by a strong service network.
Comco machines tend to be in the mid to high price range, reflecting their advanced technology and capabilities.
AMOB: AMOB provides a broad selection of tube and pipe bending machines, including CNC and hydraulic models, as well as section benders. AMOB machines are equipped with adaptive tooling and CNC controls for complex bending tasks while minimizing material deformation. AMOB has a global reputation for dependable, innovative machines backed by a solid customer support system.
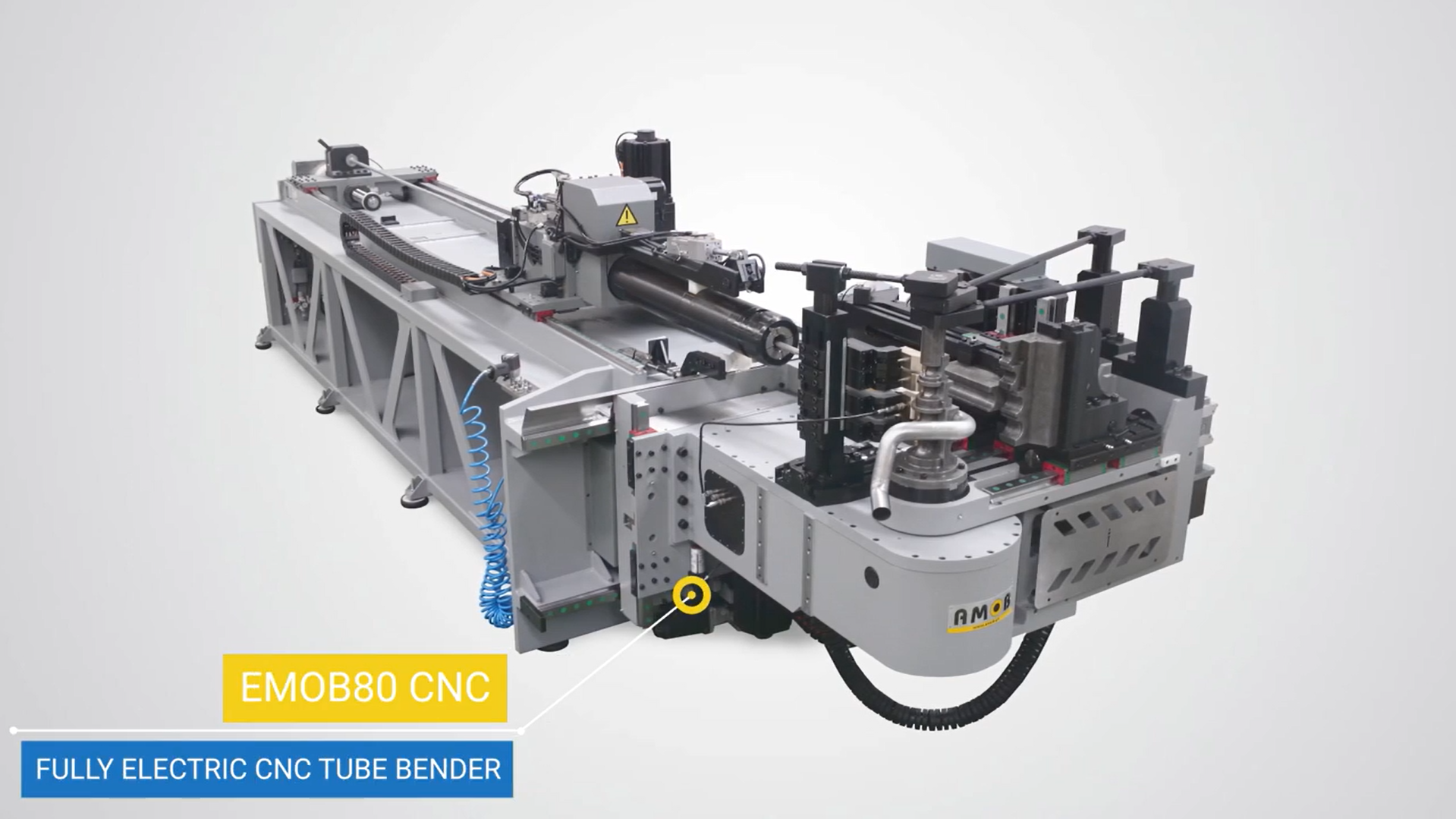
AMOB machines offer a good balance between price and features, making them an affordable option for many businesses.
BLM: BLM Group specializes in solutions for tube and sheet metal processing, offering machines for laser cutting, bending, and end-forming. BLM’s machines are equipped with automatic and smart software to enhance precision and efficiency in production. BLM is recognized for its quality and cutting-edge solutions, with strong industry experience and a skilled team.
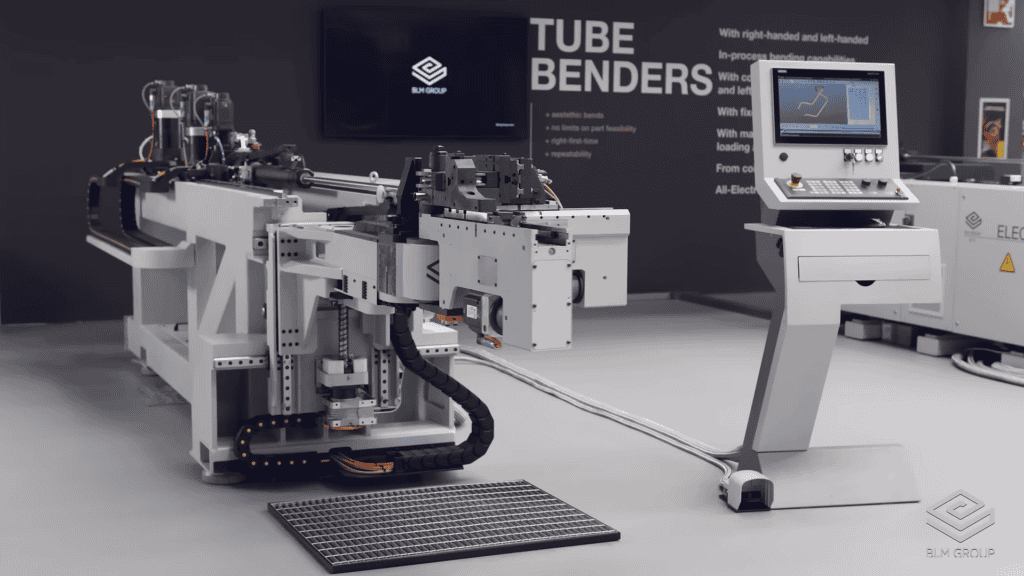
BLM machines are typically priced higher due to their advanced technology and high-performance design.
Baileigh Industrial: Baileigh Industrial manufactures a wide range of bending machines, including tube and pipe benders, plate rolls, and angle rolls. Their equipment is known for its durability and precision, making it suitable for both small workshops and large industrial operations. Baileigh emphasizes user-friendly designs and robust construction. They also provide extensive customer support, including training and service options. Their commitment to quality ensures that clients receive reliable machines tailored to their specific needs.
JMT USA: JMT USA offers a comprehensive line of bending machines, focusing on plate rolling, angle rolling, and press brakes. Their products are engineered for high performance. JMT emphasizes innovation with features like CNC controls for enhanced accuracy. They also provide customization options to meet unique customer specifications. With a strong reputation for quality and service, JMT supports clients in achieving efficient production processes.
HGG 3D Profiling: HGG 3D Profiling specializes in advanced 3D profiling machines that integrate bending technology with cutting capabilities. Their systems are designed for complex geometries often required in construction and fabrication industries. The company focuses on innovation and automation. They help clients streamline their production workflows while maintaining high standards of quality.
Peddinghaus Corporation: Peddinghaus Corporation is renowned for its heavy-duty steel processing equipment, including plate and section bending machines. Their products are designed for the structural steel industry. Peddinghaus emphasizes precision engineering and durability in their machines. They also provide extensive training and support services for optimal operation. With a strong focus on innovation, Peddinghaus continues to lead in the development of advanced metalworking technologies.
KAAST Machine Tools: KAAST Machine Tools manufactures a variety of bending machines, including hydraulic press brakes and plate rolling machines. Their equipment is known for its reliability and efficiency in metal forming applications. KAAST focuses on providing high-quality products at competitive prices. They produce tools for a wide range of customers. They also offer customization options to meet specific production needs.
Explore some other machines and top manufacturers before settling for the best one for your job.
Bending Machine Manufacturer: Overview
Manufacturers | Machine Types | Key Features | Applications |
---|
Benefits of Using a Bending Machine
Bending machines offer many benefits that can improve your manufacturing process, making it faster, more accurate, and cost-effective.
Increased Efficiency and Productivity
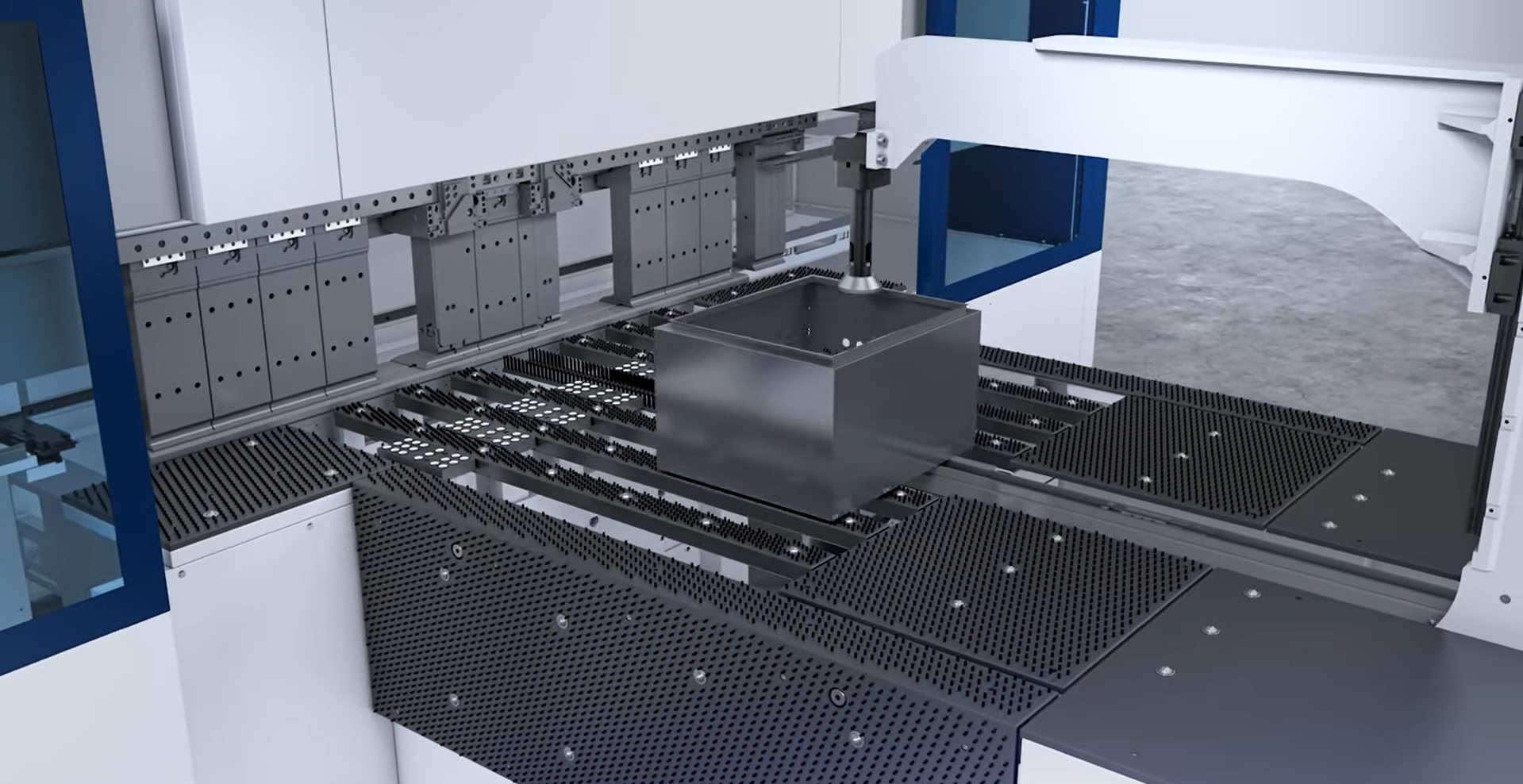
Bending equipment reduces the amount of bending processes performed manually by most workers. They increase the rate and volume of production, hence allowing for performing more in less time. This also means that there is minimal risk of deviations from the required outcome since there are errors that may occur in manual bending. Getting a modern CNC system means that setup time is significantly cut down, making it easier to carry out various assignments and increasing productivity.
Improved Accuracy
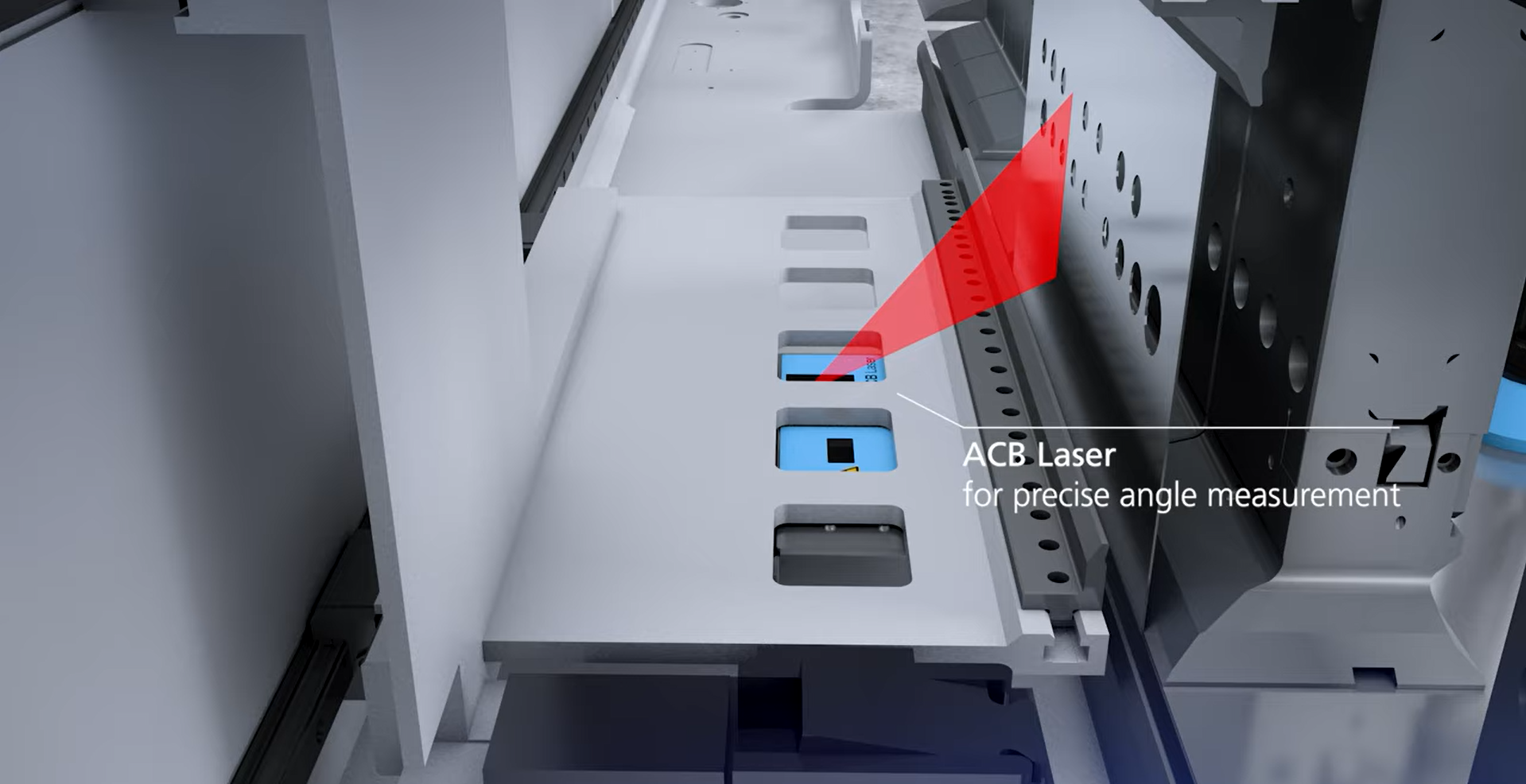
If used with a CNC system, a bending machine will yield bends that are neat and firm. Meeting tight tolerance specifications requires such precision in order to achieve defined specifications. The machines also allow for replication in such a manner that each part is identical, a major requirement for assembling parts that need to fit perfectly into one another.
Cost Reduction
Working with a bending machine can be cost-effective in several ways. Reducing the manual process means that there will be a low requirement for professional labor. Hence, the overhead on labor will decrease. Also, the accuracy of the machines implies less wastage of materials; therefore, costs on any rework and scrap decrease. Moreover, up-to-date equipment is lasting, and thus, machine repairs are irrelative.
Versatility in Applications
No doubt, bending machines are beneficial for lots of operations. These types of machines can be used to bend different lengths and types of pipes, which answers why it is mostly applied in plumbing, automotive, and construction industries. They’re also great for bending tubes for exhaust systems, hydraulic lines, and structural components. These machines can even handle angle bars and channels used in architectural projects.
Enhanced Safety
What is more, with bending machines, you have to manipulate materials less and, therefore, have fewer opportunities to get injured. It also makes the task more systematic, thus reducing the several hazards associated with manual bending of the wire.
Flexibility and Customization

Bending machines allow a particular bend for prototyping or a limited quantity of production. They are also versatile in that one can easily interchange between one material and another and between different tasks. Bending machines are very useful in any production line in your establishment.
How to Select a Bending Machine Manufacturer
Type of Workpiece to be Processed
First of all, it is necessary to define the material that has to be bent: it might be steel, aluminum, copper, or plastic, for example. Every material varies in its characteristics and may necessitate some specific aspects of the machine used. Also, the size and shape of the workpieces, which include pipes, tubes, sheets, and profiles, must be defined. Ensure that the manufacturer provides machines that are capable of processing the type of material that you want and the size of the material as well.
Processing Method
Subsequently, assess the type of processing method that will be ideal to be applied to your case. Electric bending machines are very accurate and are best suited for complex bends, as well as where high repeatability is required. Hydraulic machines are more powerful and are ideal where there is a need to cut through thick materials. Some manufacturers have designed machines that use both electric and hydraulic systems so that you have the benefit of both in one machine.
Power Source
Electric-powered machines are effective and reduce the effects of pollution; they have the best precision. A hydraulic system powers tabletop machines, and this makes them strong enough to work on thick materials. For this reason, hydraulic machines are ideal for industrial use and where high force is needed. Pneumatic is preferred where the work is light and the frequency of operations is high and prefers materials that are tender in nature.
Product Specifications
Make sure that the machine which you want to purchase should be capable of producing your product. The bending radius is crucial for the accuracy of the bent part with minimal distortion of the required geometry.
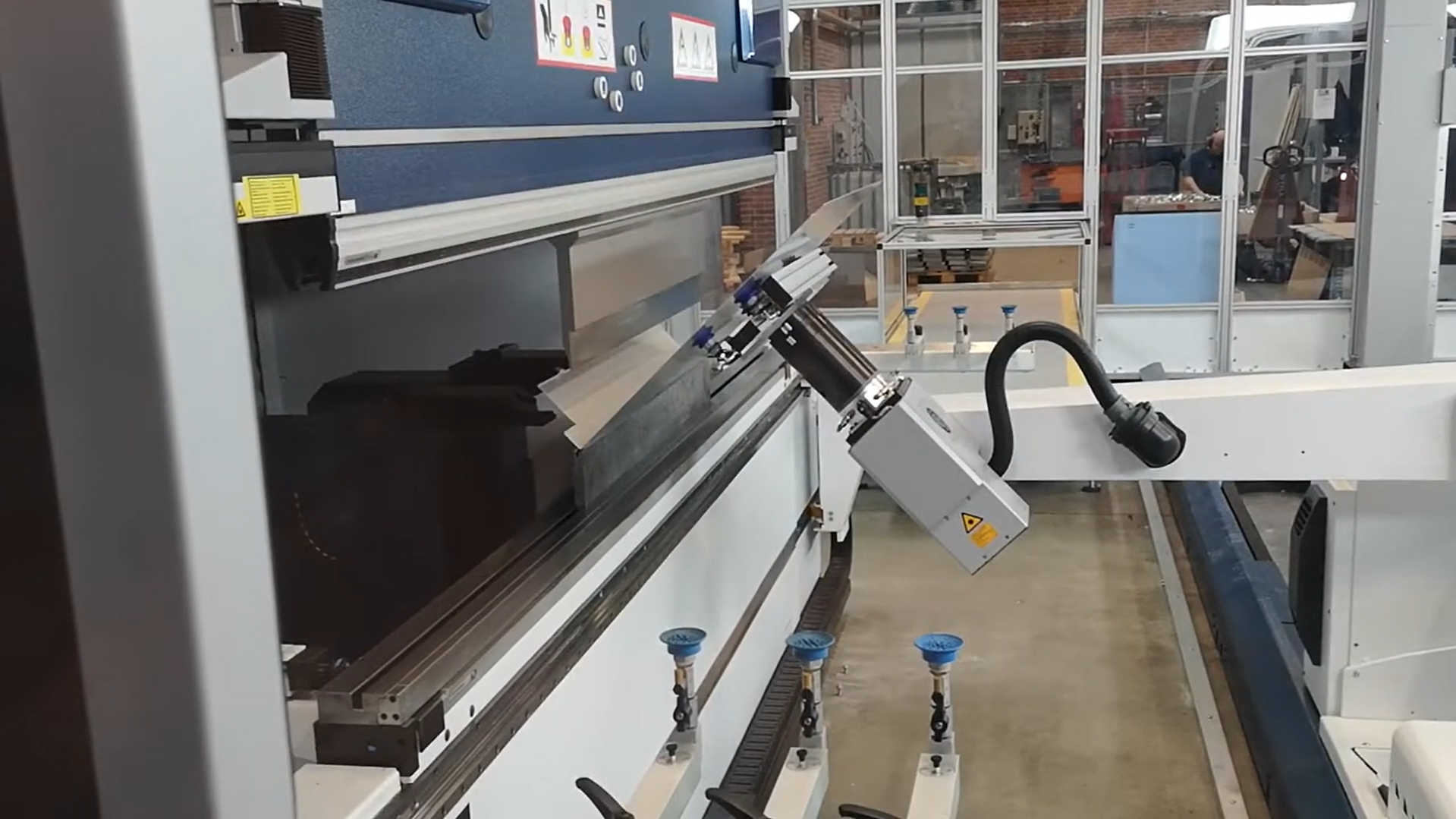
Also, ensure that the kind of pipe diameters you will be using in your projects are manageable by the machine. Wall thickness is another factor—check to see whether the difference in thickness of the materials you use results in a lack of precision of the machine.
Custom Solutions
For complex parts, consider manufacturers that offer custom solutions. These may include specialized tooling, machine modifications, or even software adjustments to suit specific bending requirements. Sometimes, you may need to prototype or produce smaller batches. In such cases, some manufacturers offer solutions fit for smaller-scale operations.
Additional Considerations
Given factors such as brand image, it is important to look at the manufacturer’s record in the market. Take your time to read some of the reviews and feedback that different customers left for you to establish the reliability and level of satisfaction you will receive from them. Reliability is also significant, so the selected manufacturer should be able to offer training and technical and maintenance services to reduce product downtime. Therefore, when buying the machine, one should compare the price with the benefits, which include durability and increased efficiency, hence making a worthy investment.
Industry-Specific Solutions
Aerospace Industry
In the aerospace industry, bending machines produce complicated products such as heat-exchanging equipment and aircraft structures. Many parts of these automobiles demand rather strong materials, such as titanium. To achieve the essential quality level of the industry, high-quality CNS machines, as well as engineered tools, are applied.
Automotive Industry
In the automotive industry, bending machines manufacture the engine components such as the exhaust systems and the chassis pieces. These parts need to be bent accurately so that the best safety can be offered to the vehicle as well as efficiency. Automotive manufacturers utilise tools that can be used to produce car components at a faster rate than tools that require time for set up, this is due to the huge order placed.
Custom Solutions
You can tailor bending machines for your specific needs, from handling special materials to achieving complex shapes. Thanks to the advancements in technology, these machines often integrate with other systems and support advanced controls like CNC for precise, efficient operations.
Customization and Flexibility
Meeting Specific Industry Needs
Special machines for bending are manufactured to fit the several requirements of the various sectors depending on the profiles, shapes that it has to manage, and the materials used. Using tools such as bending punches and die sets, bend angles and radii of bends are configurable while accommodating for geometries of bends. Since bending is highly automated, for instance, by using computer numerical controls, it is possible to achieve a high degree of precision on every bend, making it suitable for complex uses.
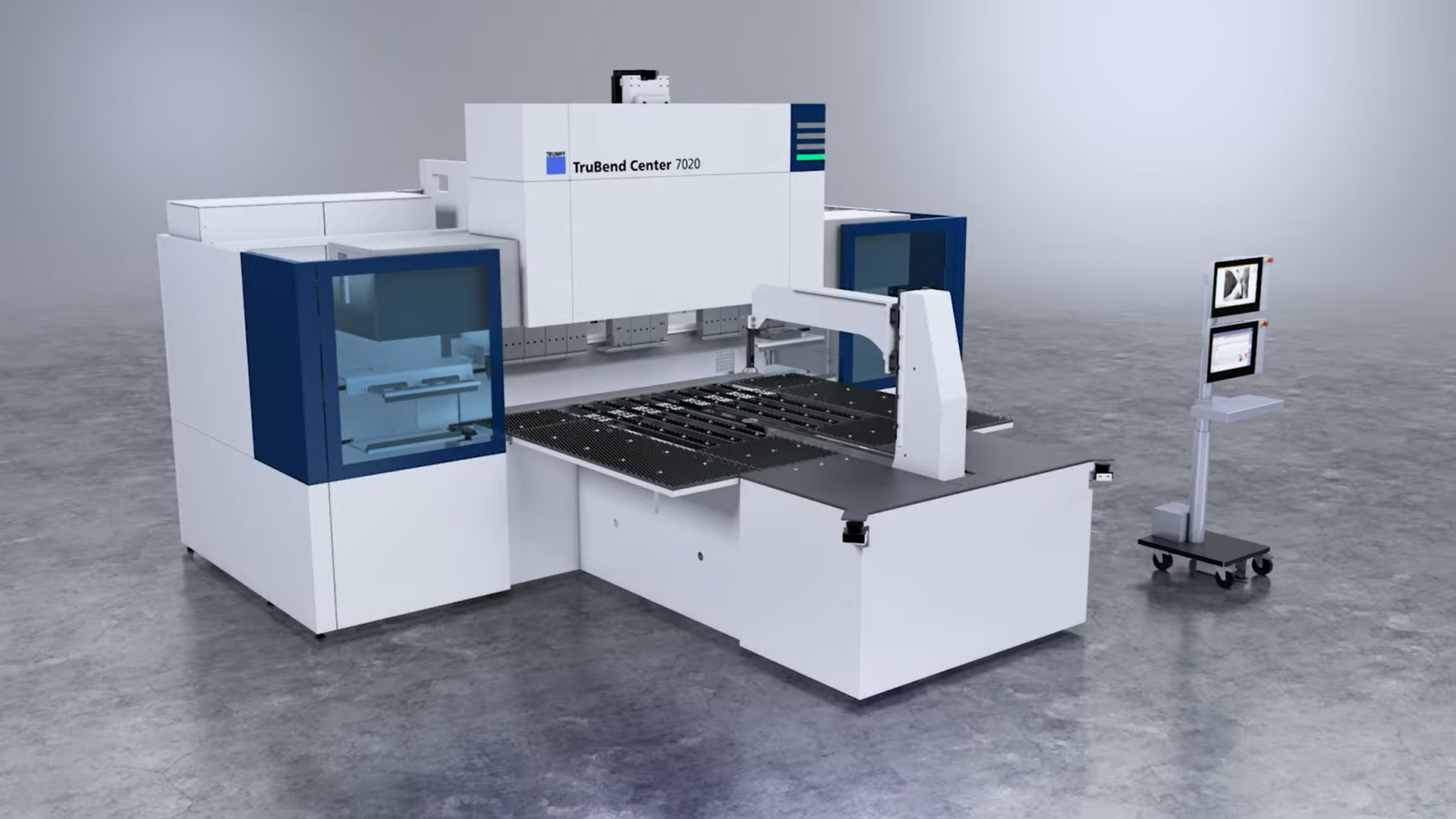
These machines are best suited to materials including steel, aluminum and composites with specific hard settings according to the material tensile strengths. Some incorporate heat treatment options in a material that has to undergo heat when bending, for instance. Furthermore, custom bending machines are flexible and ideal for low production quantities. Some also work hand in hand with other procedures, such as welding and cutting, to enhance your working flow.
In aerospace industries, automobile industries, and construction industries, the use of these custom machines gives a sharp bend and takes care of complicated pieces, thereby increasing your productivity.
Training and Support
Importance of Proper Training and Support
This is one of the reasons why it is very important for bending machine owners to ensure that their machine operators are well-trained and supported. You should also ensure that operators have adequate knowledge of aspects such as changing the settings of the machines, their maintenance, and safety measures that are to be taken.
Likely, sustained support is just as crucial as initial support, depending on how long the implementation will take across the various units within the organization. You should be able to have support in the form of assistance in case there’s a problem, and also technical help where necessary, and fairly frequent updates.
Requesting a Quote
Getting Started with a Manufacturer
The first thing that one has to do when dealing with a manufacturer is to ask for a quote. Be as clear as possible while putting down specifications and requirements in order to arrive at a good quote. Manufacturers should respond to such queries as soon as possible and should provide detailed info and price tags on products. It also assists the user in making a proper decision and establishing a good relationship that enhances a successful partnership.
Conclusion
Consider factors such as product specifications, customization options, and the availability of training and support. Top manufacturers should offer high-quality machines and excellent customer service to ensure your needs are met efficiently.
Consider partnering with BaisonLaser, an ideal solution for custom parts produced with advanced fiber laser technology. Our precision-engineered components are integral to the performance and reliability of bending machines. Contact BaisonLaser today and explore how our innovative solutions can enhance your manufacturing capabilities!