What Is Laser Cutting?
Laser cutting, a cornerstone in the modern manufacturing process, harnesses the power of a highly concentrated laser beam to slice through a variety of materials. From metals to plastics and even more delicate substances, the versatility of materials laser cutting can handle is vast. This noncontact process involves focusing the laser beam onto the material, causing it to melt, burn, or vaporize and resulting in clean and accurate cuts, making it an indispensable tool for precision manufacturing.
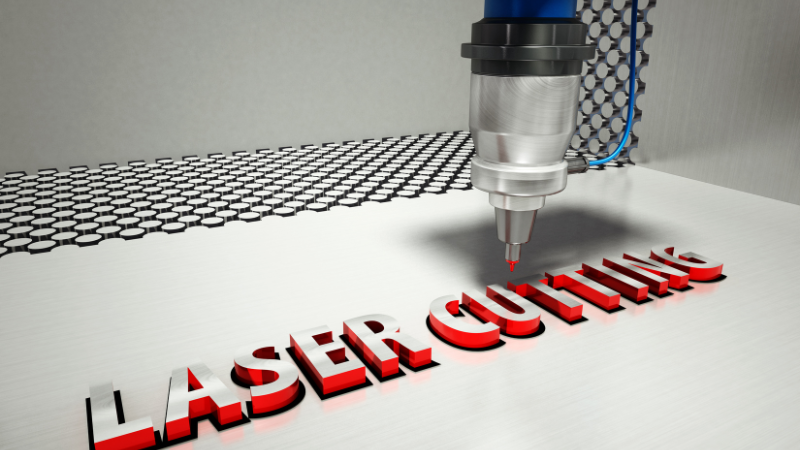
With advancements in fiber lasers and galvanometer lasers, this technology continues to evolve and offers even greater possibilities for achieving precise cuts in diverse materials. By harnessing the power of lasers, manufacturing companies in the manufacturing industry can enhance their manufacturing process and deliver high-quality products that meet the demands of today’s market. This is achieved through advanced design techniques that optimize production capabilities.
Laser Cutting Machine Application in Precision Manufacturing
Laser cutting machines have become an integral part of precision manufacturing across various industries, including automotive, aerospace, and electronics. Laser cutters are widely used to design and cut metal, such as titanium. These laser cutters and fiber lasers offer a multitude of benefits for the efficiency and accuracy of the manufacturing process. The galvanometer laser, in particular, is a valuable tool for precise design work.
- Aerospace: In the aerospace industry, where perfection is non-negotiable, fiber lasers used in the cutting process are invaluable for manufacturing companies. Laser cutting machines, especially those equipped with fiber lasers, play a crucial role in cutting materials like titanium. They produce components with tight tolerances, ensuring the reliability and safety of aircraft and spacecraft.
- Medical Devices: In the medical world, precision is crucial for manufacturing companies that specialize in implantable devices. From designing to cutting, every step is carefully executed to meet the highest standards of quality and safety. Laser cutter is essential for manufacturing companies working with titanium. The precision of these machines guarantees that medical instruments and devices meet the highest standards in the industry.
- Electronics: As electronic components become increasingly miniaturized, the demand for intricate circuitry grows. Laser cutting machines can accurately etch and cut delicate patterns, making them ideal for producing modern electronic components.
- Automotive: The automotive sector constantly pushes for innovations in design and efficiency. Laser cutting machines allow manufacturers to achieve complex designs, streamlining the laser cutting process of production and enhancing the overall quality of vehicle components. Why not look at the use of fiber laser cutting in the automotive industry?
- Jewelry and Art: Beyond industrial applications, laser cutting machines play a pivotal role in crafting intricate jewelry designs and art pieces. They offer artists and designers a level of precision that other cutting processes can’t match.
- Textiles and Fashion: Modern fashion and textile industries are continually evolving, and laser cutting machines help in crafting intricate patterns, designs, and innovative textiles, adding a new dimension to fashion design.
By understanding the diverse applications of laser cutting machines, it becomes clear how integral they’ve become to modern precision manufacturing. Their ability to combine speed with unmatched accuracy propels many manufacturing industries into new realms of efficiency and design possibilities.
Top 10 Benefits of Laser Cutting in Precision Manufacturing
In conclusion, laser cutting offers numerous advantages for precision manufacturing. With its ability to provide high accuracy and intricate designs, laser cutting has revolutionized the industry. Here are 10 of the most significant advantages of laser cutting technology.
1. High Precision
Laser cutting stands out for its remarkable accuracy. With the ability to produce cuts down to micrometer precision, it ensures components and parts are manufactured to the strictest specifications. This is especially vital in industries where even slight deviations can lead to product malfunctions or safety concerns.
2. Versatility Across Materials
One of the standout features of laser cutting is its adaptability to a wide array of materials. Whether it’s metals like steel and aluminum, plastics, ceramics, or even rubber, the process can be finely tuned to achieve optimal results based on the specific material in use. Flexibility Laser cutting opens up endless possibilities for manufacturers.
3. Smooth Cut Edges
The precision of the laser ensures that the edges of cuts are smooth and clean, reducing the need for post-processing or finishing. This not only saves time and resources but also ensures that components are ready for their next stage of production or assembly without additional interventions.
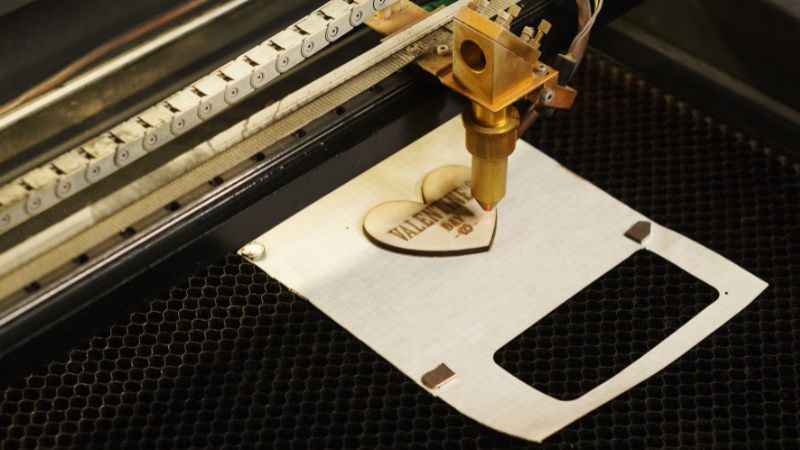
4. Consistency in Production
Once a laser cutting machine is calibrated and set, it delivers consistent results, you can use to cut a variety of shapes within the same material thickness. This repeatability is crucial in mass production scenarios where uniformity across parts is a strict requirement. Every piece produced mirrors the quality and specifications of the previous one, ensuring a standard of excellence.
5. Reduced Material Waste
Given its pinpoint accuracy, laser cutting ensures that material usage is optimized, leading to minimal waste. For industries that use expensive materials or aim for sustainable manufacturing practices, this can result in significant cost-effectiveness and reduced environmental impact.
6. Quick Setup and Transition
Transitioning between different jobs or adjusting settings on a laser cutting machine is generally faster than with traditional mechanical cutting systems. This agility translates to reduced downtime and faster turnaround times, meeting the demands of just-in-time manufacturing processes.
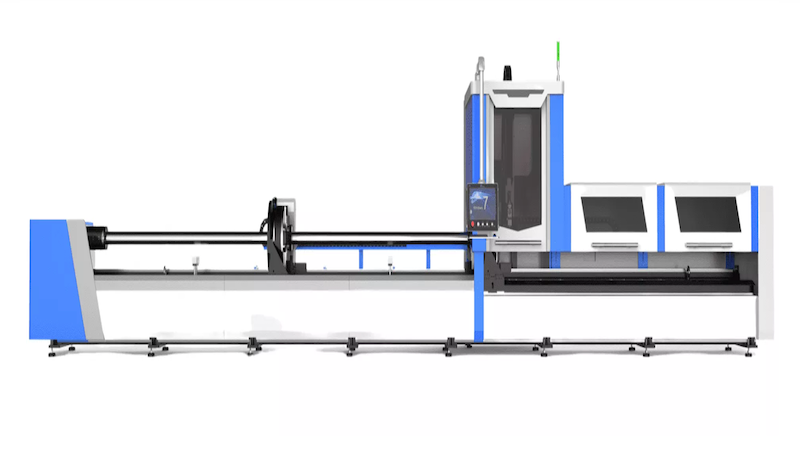
7. Safety Advantages
As a contactless cutting method, laser cutting minimizes the risks associated with physical tool-to-material interactions. This not only reduces the potential for material damage but also ensures a safer work environment, as there are fewer moving parts and physical interactions that could result in accidents.
8. Digital Integration
Modern laser cutting machines seamlessly integrate with digital design tools like CAD (Computer-Aided Design) systems. This means designs can be directly imported and cut, facilitating a smooth transition from the design phase to production, and enhancing overall efficiency.
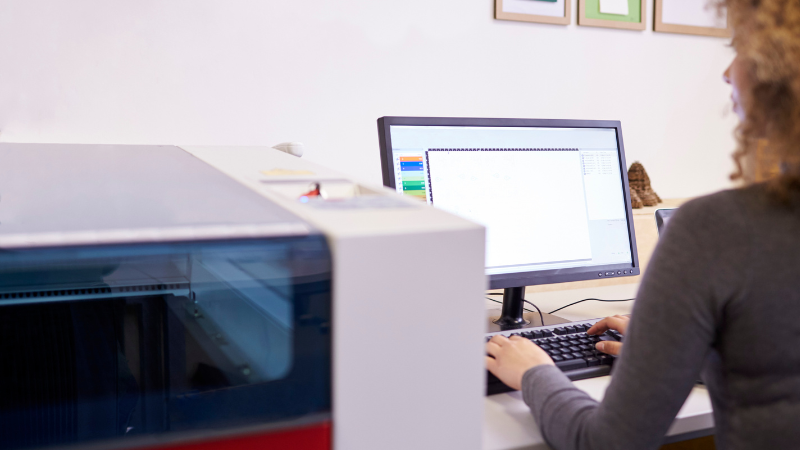
9. No Tool Wear
Traditional cutting methods like flame cutting and waterjet cutting, involve physical tools that wear down over time and require maintenance or replacement. Laser cutting, using a concentrated beam of light, doesn’t suffer from this issue. This ensures consistent performance across long periods and reduces maintenance downtime.
10. Ability to Handle Complex Geometries
Laser cutting shines when it comes to intricate and complex designs. Whether it’s elaborate patterns for aesthetic purposes or intricate components for technical applications, the laser’s precision ensures that even the most complicated designs are executed flawlessly.
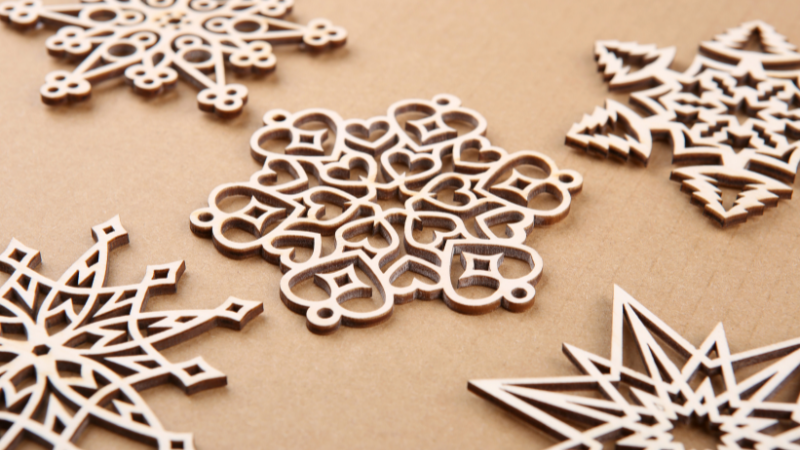
These benefits collectively underscore why laser cutting has become a cornerstone in the world of precision manufacturing, pushing boundaries and setting new standards of excellence. If you’re looking to optimize your manufacturing processes and achieve superior results, consider incorporating laser cutting into your operations.
FAQs
What types of materials can be cut using laser cutting?
Laser cutting is compatible with a wide range of materials such as metals (steel, aluminum, brass), plastics (acrylic, polycarbonate), wood, fabric, paper, and more.
How precise is laser cutting?
Laser cutting offers exceptional precision with tolerances as low as 0.1mm or even less depending on the material thickness and type of laser machine used.
Is laser cutting suitable for small-scale production?
Yes! Laser cutting is highly versatile and can be employed for both small-scale production runs as well as large-scale industrial manufacturing. Click here to learn about how to choose a laser machine for a small business.
Are there any limitations to laser cutting?
While laser cutting is incredibly versatile, it may not be ideal for certain materials that are highly reflective or contain chlorine-based compounds due to safety concerns.
Conclusion
This guide underscores its significance, illuminating a path forward for manufacturers aiming for excellence. Laser cutting has undeniably carved its niche in the realm of precision manufacturing, setting new standards in efficiency, accuracy, and innovation. Its myriad benefits cater to the multifaceted demands of modern industry. As technology continues to evolve, the role of laser cutting is poised to grow even more central.
Experience Precision with Baison
Intrigued by the transformative power of laser cutting? Take a look at Baison Laser! We have nearly 20 years of laser manufacturing experience, and a number of products have obtained CE certification in Europe. Take your manufacturing to the next level with Baison’s state-of-the-art laser cutting services and products. Explore unmatched precision and efficiency firsthand. Discover Baison’s Laser Solutions Today!