A press brake plays a key role in the metal fabrication industry. It bends sheet and plate materials with great care. Factories can’t do without these machines. They help make complex shapes and parts used in many fields, from cars to planes.
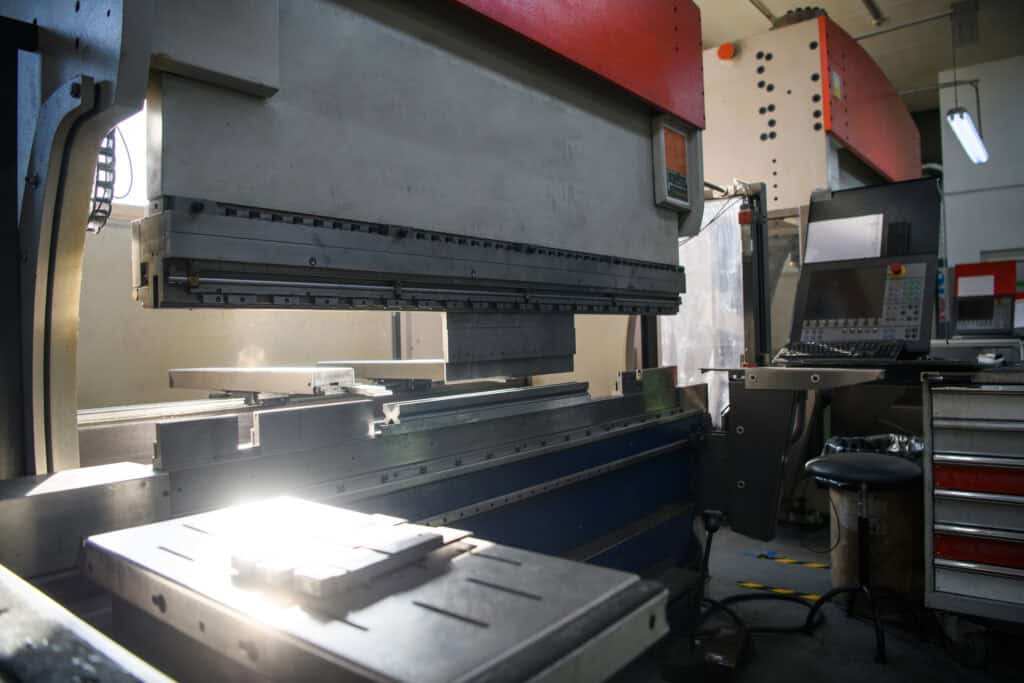
Press brakes use force through a punch and die to make exact bends, folds, and creases in metal sheets. This boosts output and quality in making things. Anyone who works with metal needs to grasp how press brakes work and what they offer. These tools add a lot to what modern factories can do and how flexible they can be.
What is a Press Brake?
Sheet metal and plate materials can be bent and folded into a variety of shapes and angles using a press brake. The metalworking sector uses this strong machine tool that applies a heavy load on metal sheets to bend them to the desired angles. The metal workpiece is clamped between a punch and a die to facilitate the process. When force presses the punch, the metal takes on the desired shape.
Read also: How to choose the right bending machine?
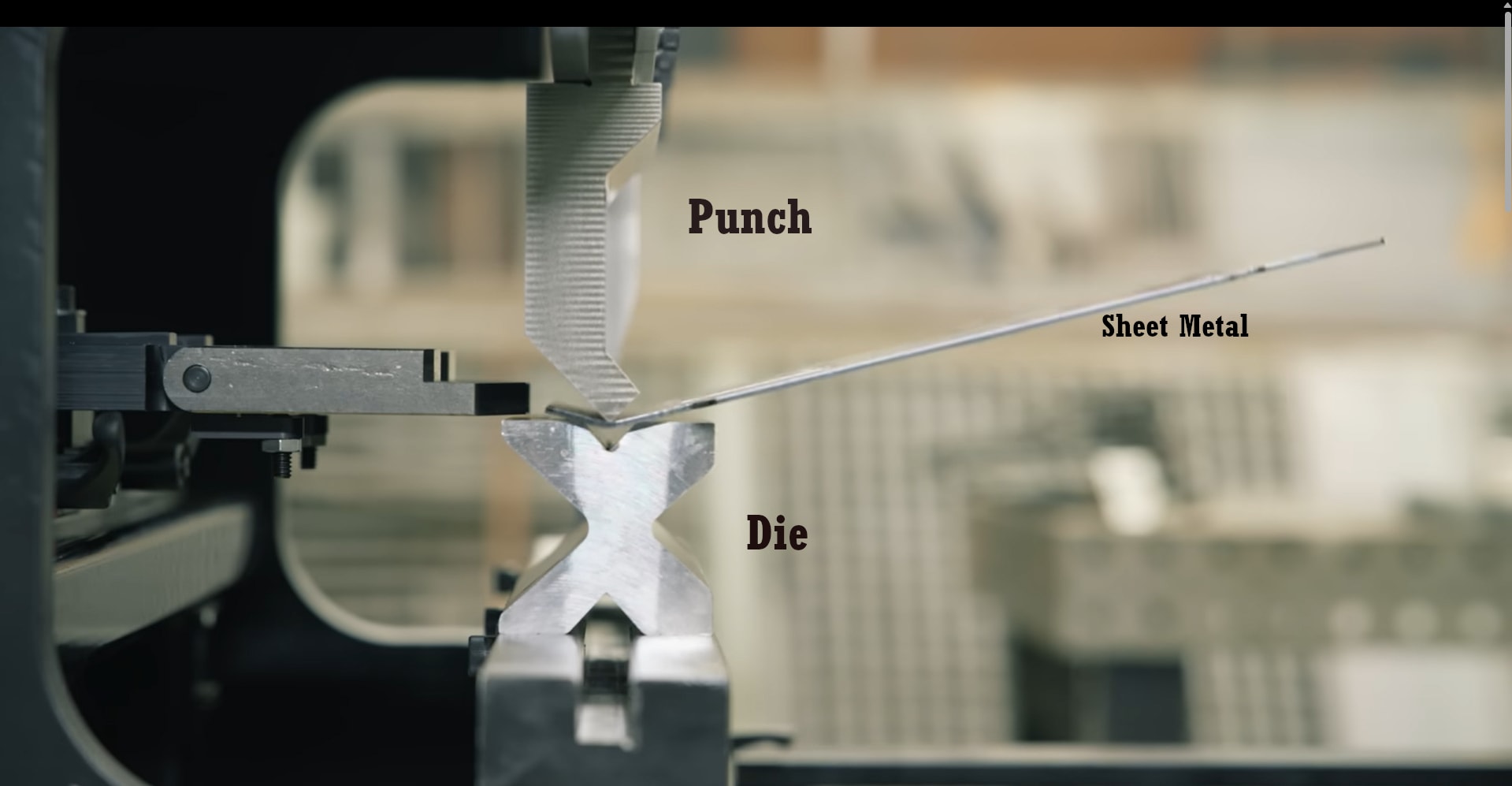
Press brakes use force to shape metal plates precisely. To force the punch into the die, which is fixedly positioned on a bed, the machine’s ram, or beam, oscillates up and down. Depending on the press brake type you choose, the force might be generated by electric, hydraulic, or mechanical means.
Press brakes are used in a variety of industries. Automakers use them to bend sheet metal for body components, including doors and hoods. The aerospace industry also uses them to create airplane parts where precision is crucial.
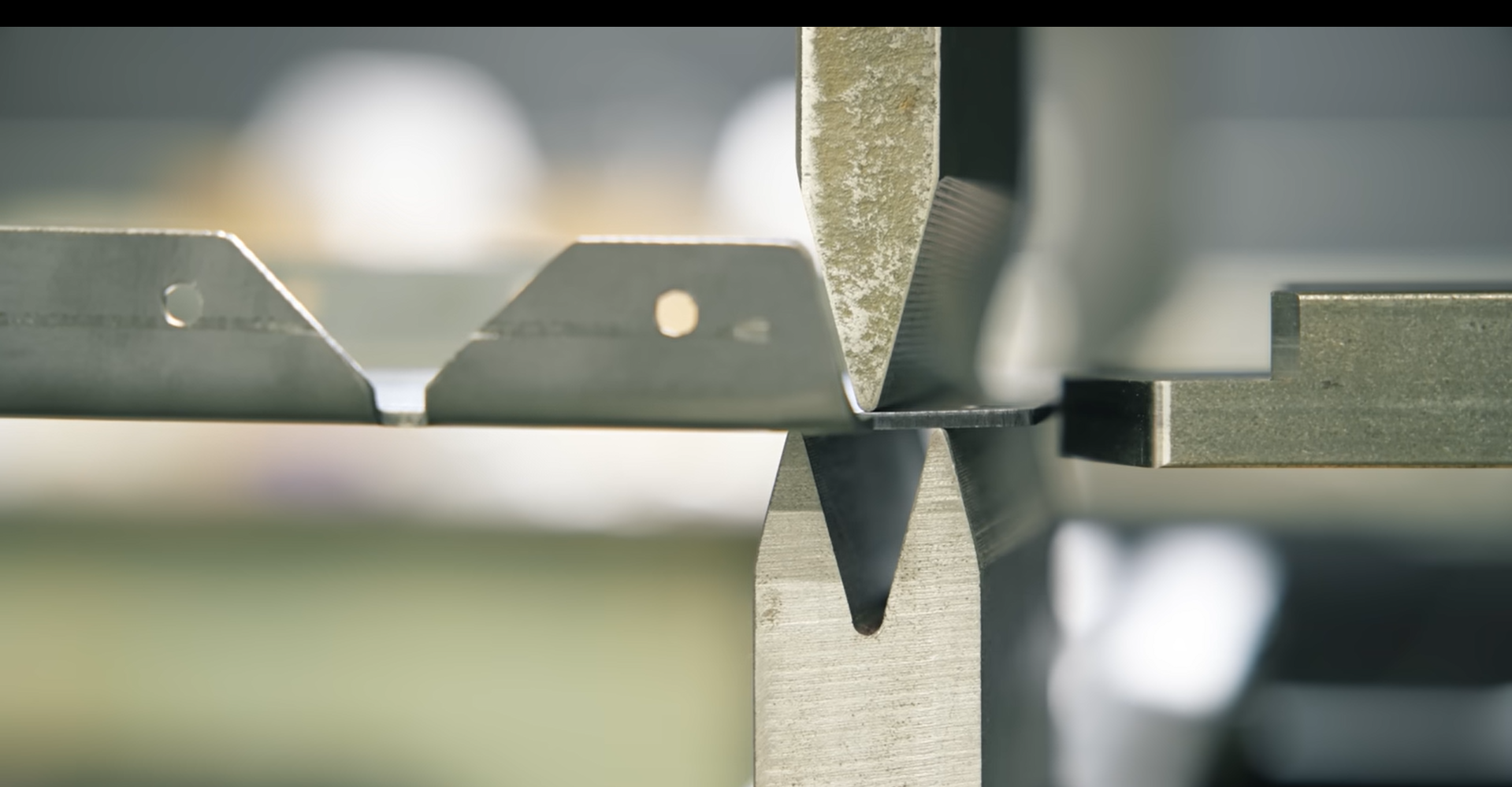
Press brakes are essential tools for shaping a metal plate used in building projects. They assist in building structural elements and roofs. These devices form metal for appliances such as refrigerators and washing machines. Press brakes are often used by people who do bespoke metal work. This involves creating decorative metal pieces or brackets.
How Does a Press Brake Machine Work?
Before you use a press brake machine, put safety first. Wear the right gear to protect yourself. This includes gloves, safety glasses, and steel-toed boots. Look over the machine to check for any damage or wear. Make sure all safety guards are in place and work well.
- Setting Up the Machine: Pick the right punch and die for the bend you want. Check that they’re clean and have no flaws. Put the punch on the ram and the die on the bed of the press brake. Double-check that they line up.
- Adjusting the Machine: Set the back gauge to place the workpiece in the right spot. This helps make sure all bends are the same. If you’re using a CNC press brake, type the bend settings into the control panel. For manual machines, change the ram stroke and angle settings to fit your needs.
- Positioning the Workpiece: Set the metal sheet or plate on the die, lining it up with the back gauge. Hold the workpiece in place using clamps or by gripping it to stop it from shifting while you bend it.
- Performing the Bend: Activate the press brake by pressing the foot pedal or control button. Monitor the process as the ram moves down, ensuring the punch presses the workpiece into the die smoothly. Once the bend is complete, release the pedal or button to raise the ram.
- Inspecting the Bending angle: After the bend is complete, check the angle using a protractor or angle gauge to ensure it meets the specifications. Inspect the bend for any cracks, wrinkles, or other defects. Rework the piece if necessary.
- Finishing Up: Carefully remove the bent workpiece from the machine and clean the area by clearing any debris or metal shavings.
Types of Press Brakes
In the metal industry, press brakes are indispensable for bending sheet metal. Selecting the appropriate kind for your task is made easier by being aware of its various varieties.
Press brakes are categorized into four main categories. Hydraulic, CNC, mechanical, and pneumatic press brakes.
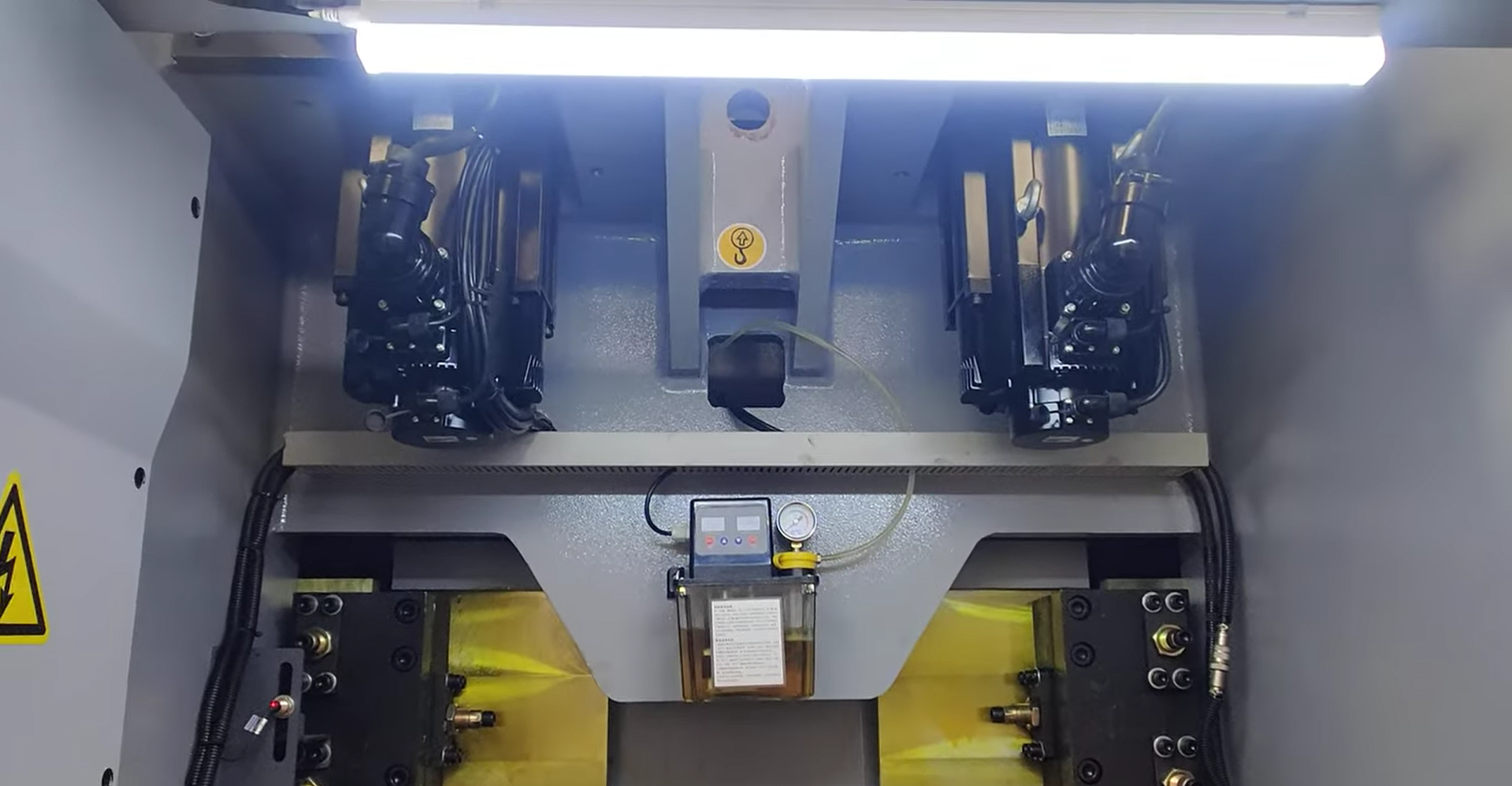
Electric servo motors drive the flywheel in a mechanical or CNC press brake. The material is bent by the flywheel, which stores and releases energy. These devices are incredibly productive and fast, which makes them ideal for high-volume jobs like manufacturing cars.
Hydraulic cylinders use pressurized fluid to apply force, which controls the ram movement in a hydraulic press brake. Hydraulic presses are accurate for handling thicker materials. Their skill makes them suitable for demanding jobs like shipbuilding and building construction.
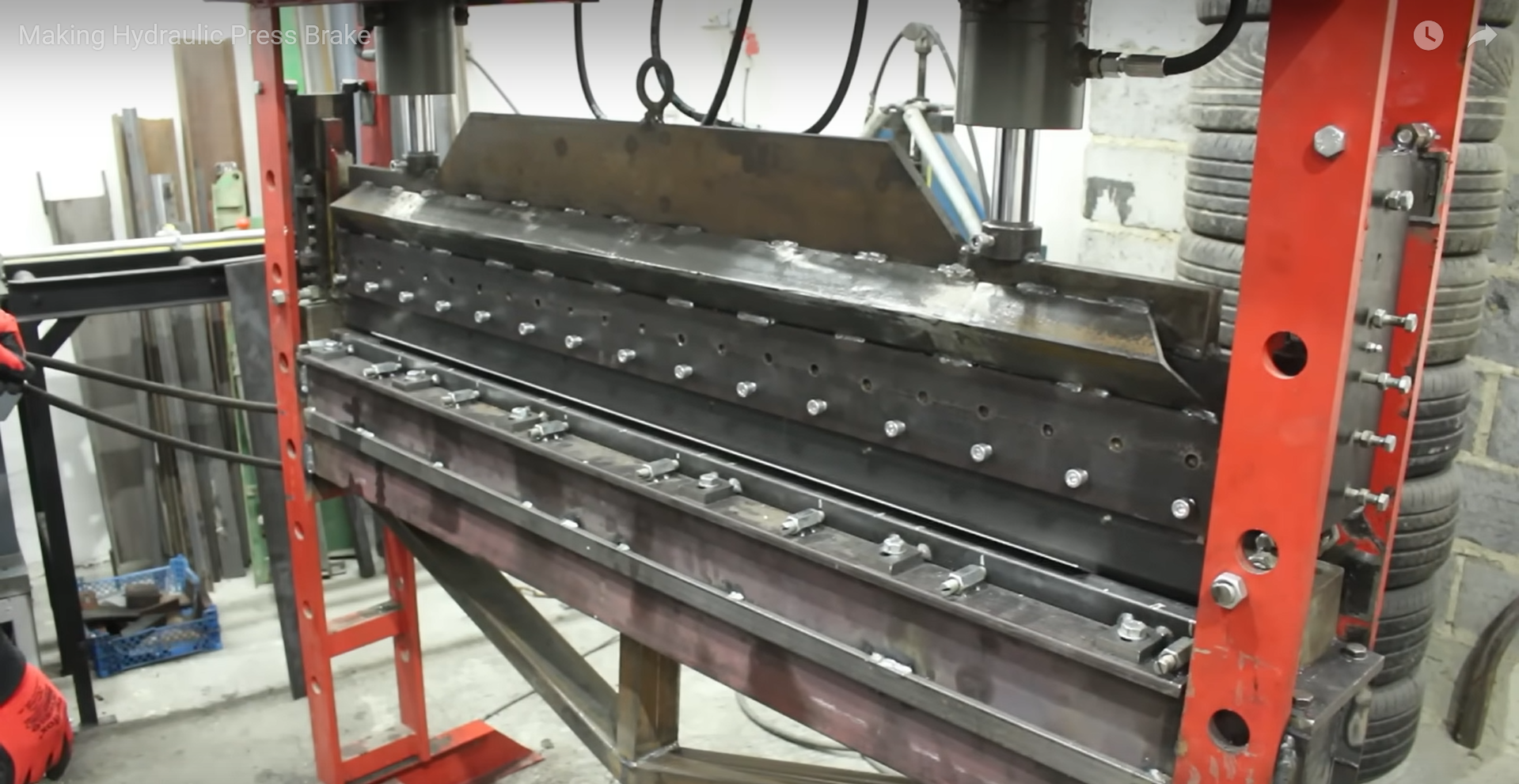
An electric press brake, also known as a Servo-electric press brake (CNC), uses electric servo motors to control the bending process. They save energy, bend with high accuracy, and need little upkeep. These machines work best for jobs that need exact bends, like aeroplanes and computer part-making.
Hybrid press brakes mix hydraulic press brakes and servo-electric tech to work better. They offer the precision of servo-electric systems with the power of a hydraulic system, making them versatile enough to handle a wide range of tasks, from light to heavy-duty bending.
Press Brake Types: General Comparison
Type | Drive Mechanism | Key Features | Advantages | Disadvantages | Typical Applications |
---|---|---|---|---|---|
Mechanical Press Brake | Rotational motor | Fast processing speed, simple mechanical structure, high productivity. | High speed and easy maintenance. | Difficult to adjust pressure and speed; low force for thick materials. | Bending small parts where precision is less critical. |
Hydraulic Press Brake | Hydraulic cylinders | Uses synchronized hydraulic cylinders for flexibility in speed control and retraction. | High versatility and accuracy; suitable for complex tasks. | More complex maintenance; potential for hydraulic leaks. | Heavy machinery, automotive, and general fabrication. |
CNC Press Brake | Computer Numerical Control (CNC) | Allows programming of complex shapes; high automation and accuracy with feedback systems. | Excellent for high-volume production; minimal rework needed. | Higher cost and complexity in operation; requires skilled operators. | Complex workpieces in high-volume manufacturing environments. |
Pneumatic Press Brake | Compressed air | Utilizes air pressure for operation, often lighter and more compact than hydraulic models. | Faster setup and operation; less maintenance required than hydraulic brakes. | Limited force compared to hydraulic; not suitable for heavy-duty applications. | Light to medium-duty applications, such as HVAC work. |
Benefits of Using a Press Brake
Some of the most prominent benefits of using a press brake are as follows:
On-Site Equipment: Having a press brake on-site makes metalworking much easier. You can set it up and tweak it, cutting down on wasted time and boosting output. With a press brake right there, you can handle changes in what you need to make or rush jobs without depending on outside help.
Worker Protection: New press brakes have lots of safety features to keep workers safe while they’re using them. These include light barriers that spot things in dangerous areas, safety mats that stop the machine if someone steps where they shouldn’t, and emergency buttons to shut everything down fast if something goes wrong. These safety measures help make the workplace safer and lower the chances of accidents happening.
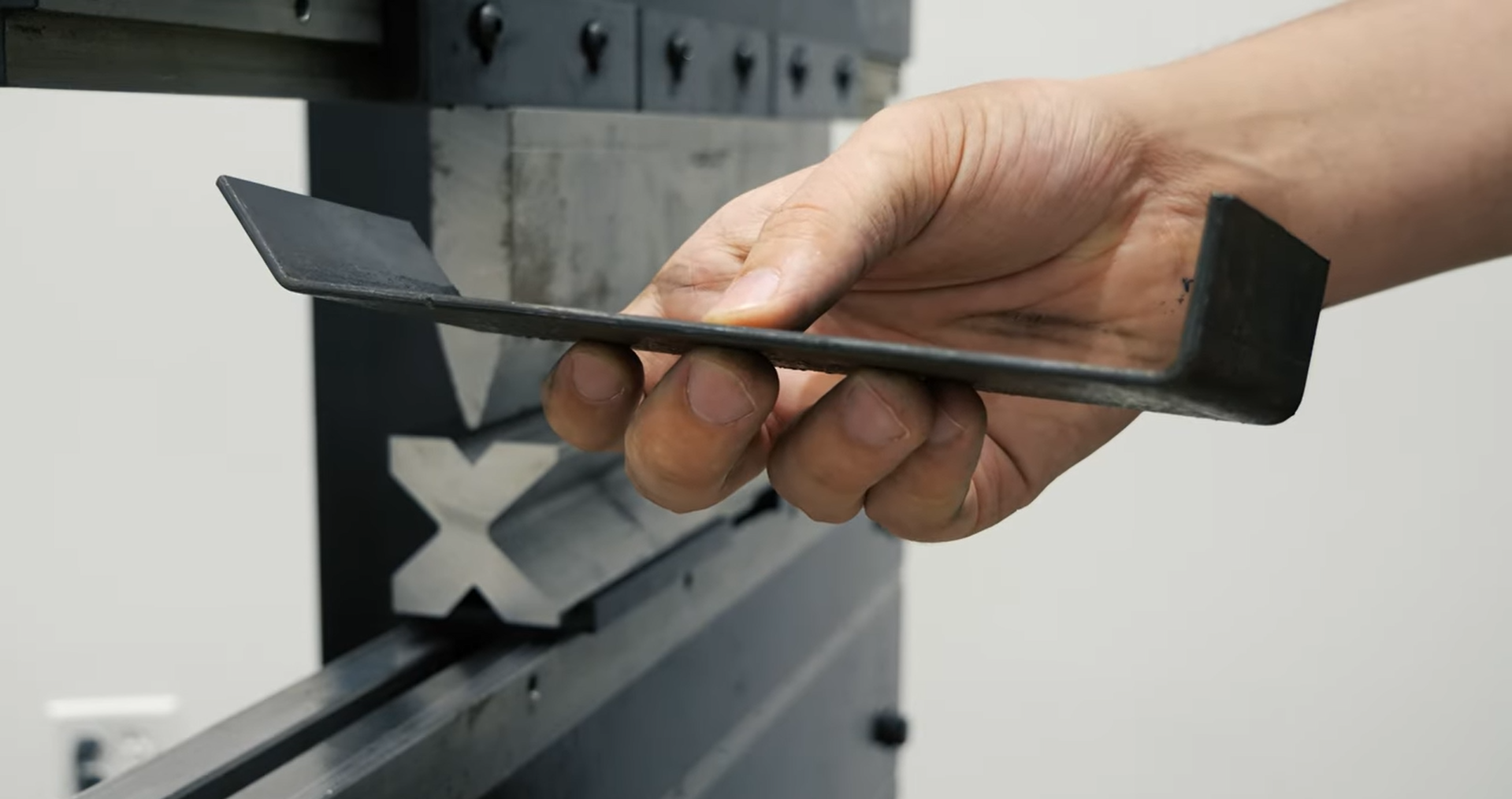
Quick Manufacturing: Press brakes speed up the process of bending metal sheets. They work fast and , which matters a lot when you need to meet tight deadlines. Being able to make high-quality bends helps boost overall production speed. This gives companies an edge over their competitors in the market.
Less Physical Work: CNC press brakes make bending much easier. They do most of the work on their own. This means workers don’t have to do as much heavy lifting. They watch the machine and put materials in, and take them out. These computer numerical control system brakes help workers feel more comfortable and don’t tire them out as much.
Saving Money: Press brakes help companies spend less in a few ways. These machines work so well that companies don’t need to hire as many people, which cuts down on wages. Also, press brakes bend metal so well that there’s less waste. They make fewer mistakes, so less metal gets thrown away. All of this helps companies save money and make more profit.
Applications of Press Brakes
Press brakes bend materials in different ways, each with its own uses and advantages. The main ways to bend are air bending, bottom bending, and coining. Each method works best for certain tasks based on the material and how precise it needs to be.
1. Air Bending
Air bending process happens when the workpiece touches the tip of the punch and the edges of the die. The punch pushes the workpiece into the V-shaped opening of the die but doesn’t reach the bottom. This lets you make different bend angles with the same tools by changing how far the punch moves.
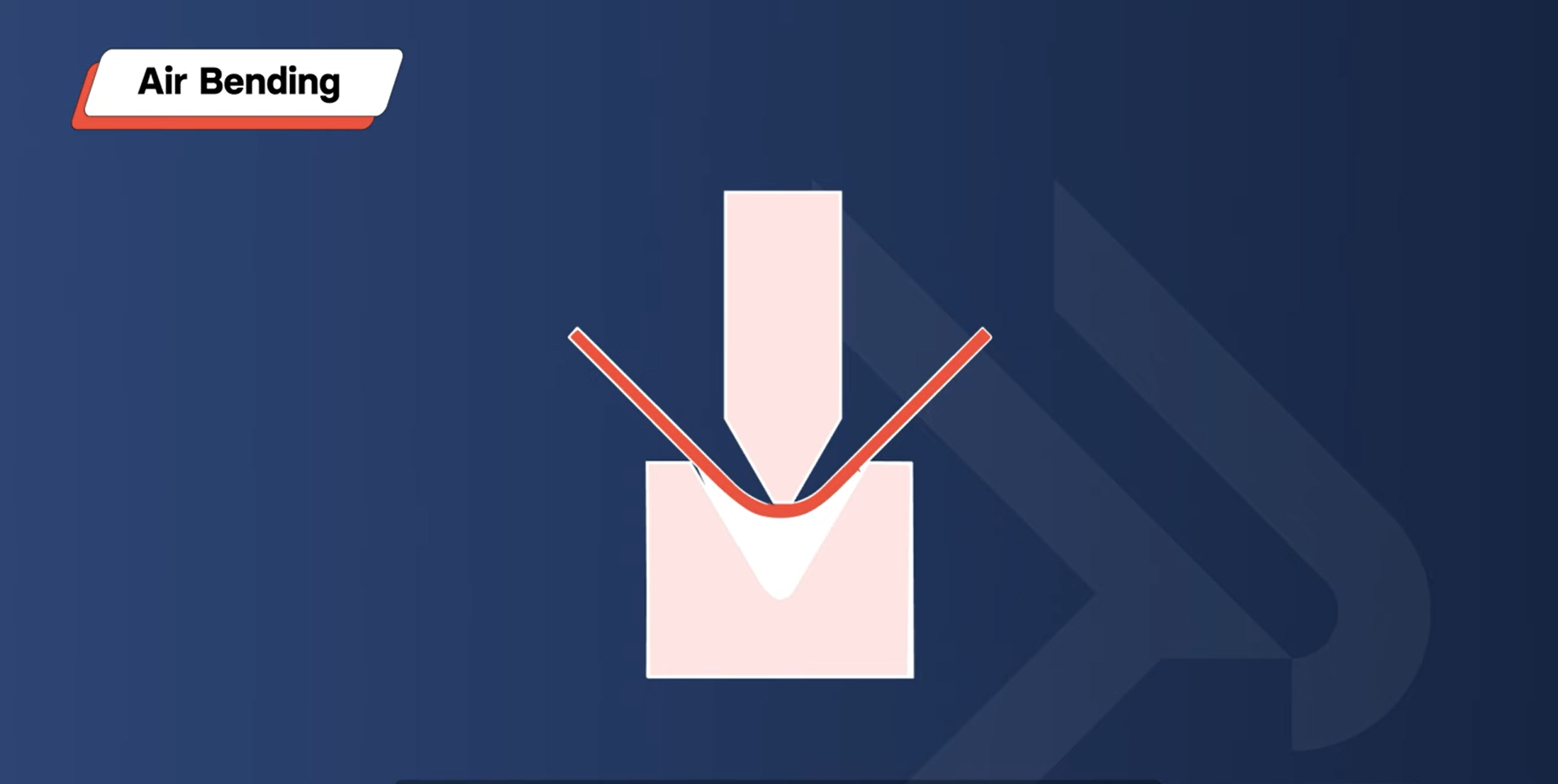
- Sheet Metal Work: Great to make various angles in sheet metal parts, like brackets, cases, and panels.
- Making Models: Helpful when trying out different angles without changing tools.
- Car Making: Used to shape light parts like brackets and clips.
Example: A company that makes custom metal brackets for electronic cases can use air bending to get different bend angles without changing how the tools are set up.
2. Bottom Bending
Bottom bending needs the die and workpiece angles to match. You press the workpiece hard against the die, and the punch’s radius shapes the bend in the material. This method gives you better accuracy and consistency in the bend angle.
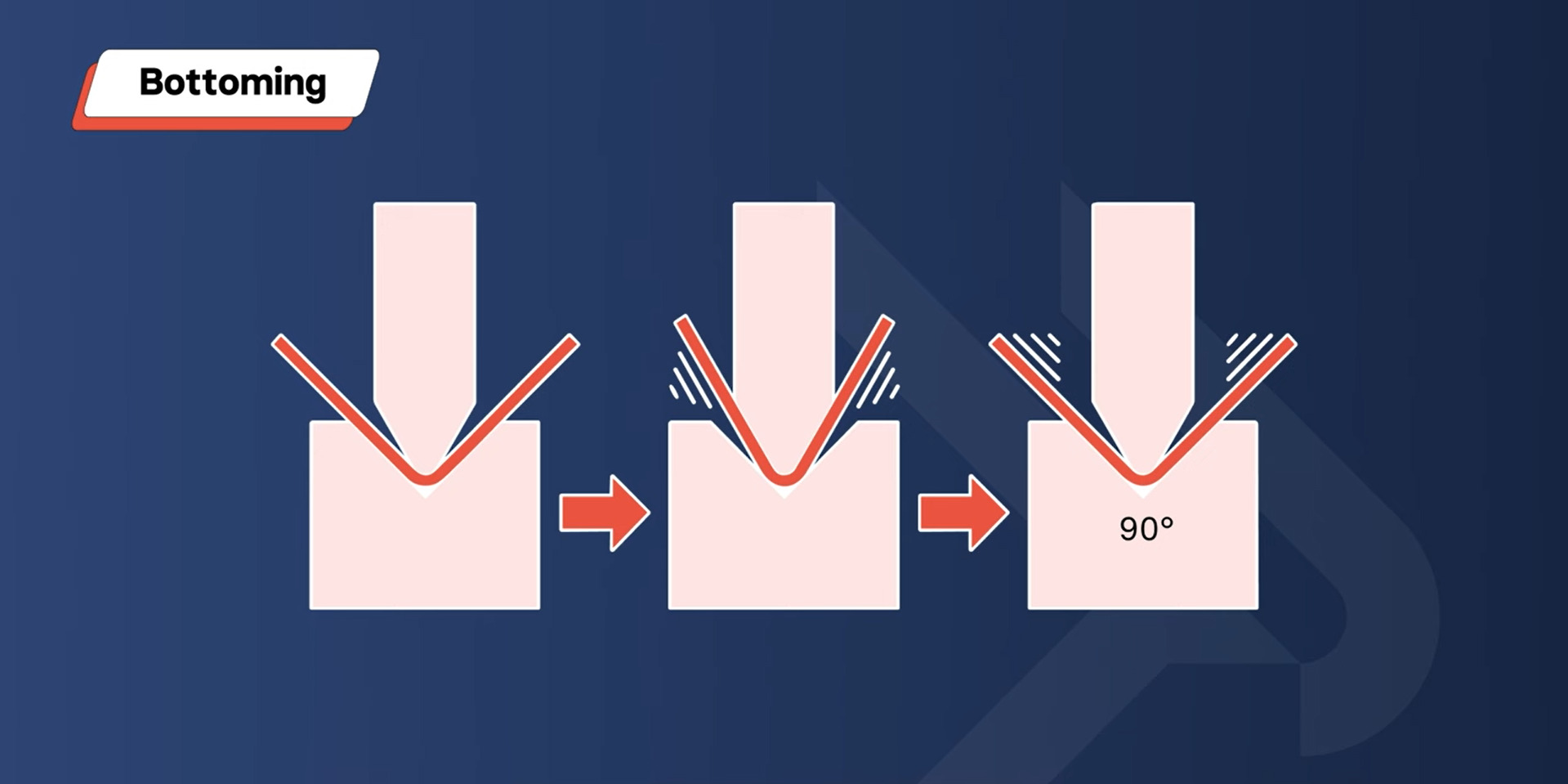
- Precision Parts: Good for making parts that need exact and steady bend angles, like parts in aerospace and medical tools.
- Heavy-Duty Bending: Used to bend thicker materials when you need higher accuracy.
- Batch Production: Great for making many parts that all need the same bend angle.
Example: An aerospace firm making exact parts for planes can use bottom bending to make sure all their parts have the same correct bend angles.
3. Coining
Coining has an impact on the workpiece by stamping it between a die and an upper punch with sufficient force to penetrate and flow into the material. This results in the highest accuracy and repeatability, as the material gets pressed into the die.
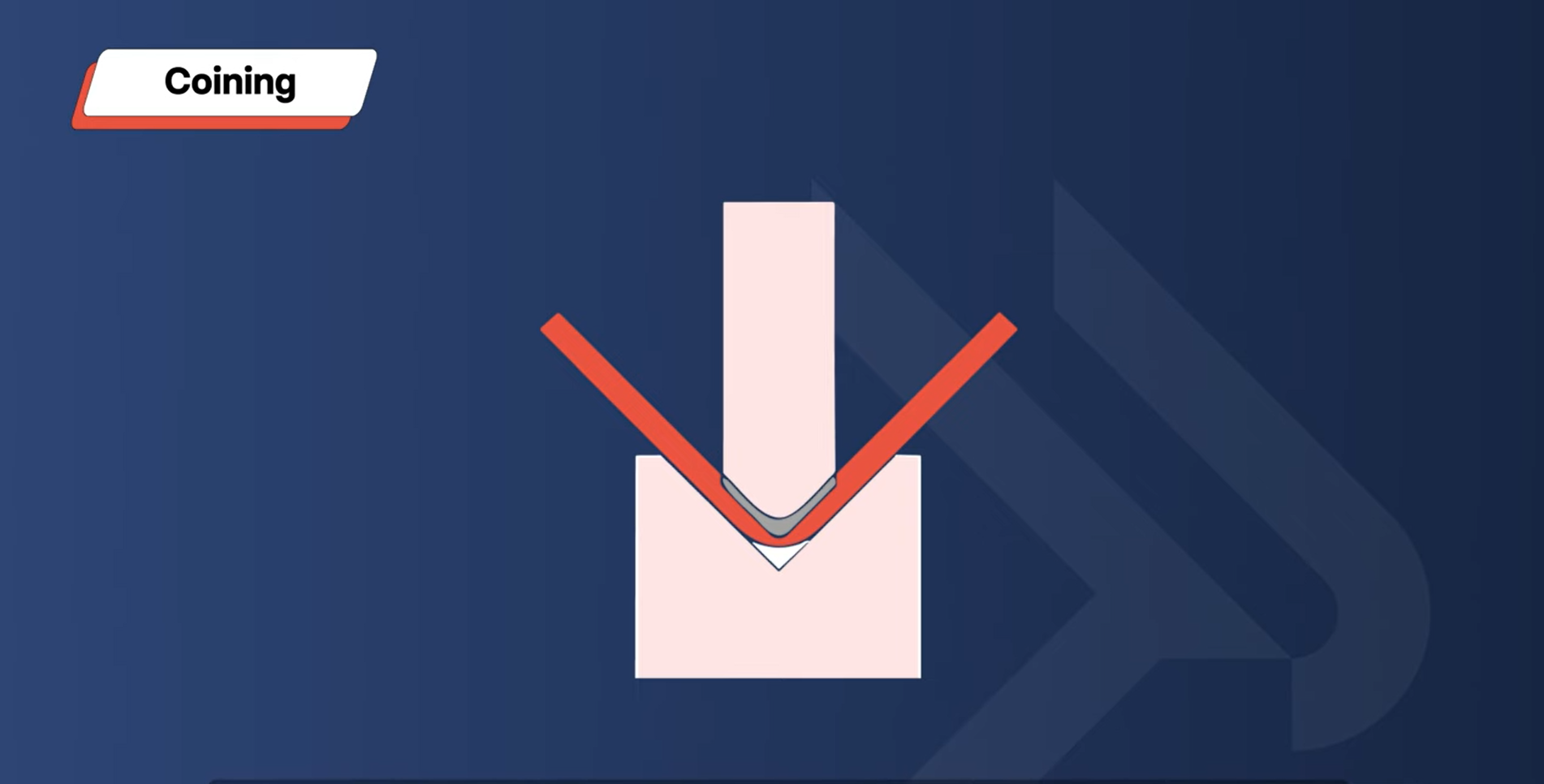
- High-Precision Parts: Used to make parts that need very tight tolerances and high precision, like electronic connectors and small mechanical components.
- Complex Shapes: Useful to create intricate shapes and detailed features in the workpiece.
- High-Volume Production: Ideal for high-volume production where consistent quality is critical.
Example: A manufacturer producing electronic connectors can use coining to achieve the precise shapes and tolerances required for reliable electrical connections.
Safety Measures for Press Brake Operation
- Keeping workers safe when using a press brake is key to stopping accidents and injuries. The main way to do this is to train operators often. Regular training helps operators stay up to date on the newest safety rules and how to use the machine right, so they can work with the press brake in a safe and good way.
- Safety gear is a must to guard operators from possible dangers. Workers should always put on safety glasses, gloves, and boots with steel toes to protect themselves from bits of metal sharp edges, and other risks that come with press brake work.
- Safety devices on the machine play a big part in stopping accidents. Use machine guards light curtains, and laser sensors to prevent accidental touch with moving parts. These safety features help make a wall between the worker and the dangerous parts of the machine.
- Routine machine check-ups and upkeep are crucial to ensure the press brake stays in tip-top shape. Perform regular inspections for signs of wear and fix any faulty components right away. This hands-on strategy helps avoid breakdowns and lowers the chances of accidents due to equipment issues.
- An emergency stop button is a key safety feature that needs to be easy to reach and work well. Put the emergency stop button where people can get to it fast if something goes wrong. This lets them shut down the machine if they need to.
- The right setup and alignment of the workpiece help prevent problems. Make sure you place and hold the metal sheet or plate before you start working. When you line things up right, you lower the chance of wrong bends and possible accidents.
- Clear talk with your coworkers matters a lot for safety. Use hand signs or other ways to let everyone know about how the machine is doing and any changes in what’s happening. This helps everyone work together and stops mix-ups that could cause accidents.
- Finally, keep the work area clean and clear of obstacles. A tidy workspace cuts down on the chance of trips and falls, making for a safer place to work. New press brakes come with cutting-edge safety gear, like side curtain safety tools and laser sensors, which boost safety. Always follow the maker’s rules and safety guidelines to keep a safe work setting.
Choosing the Right Press Brake for Your Application
First and foremost, what do you need? Figure out the materials you’ll work with, like steel, aluminium, or stainless steel. Work out the range of material thicknesses you’ll handle, as thicker materials need more force and a tougher press brake. Think about the bending angles you want to achieve. Some press brakes let you adjust angles more than others.
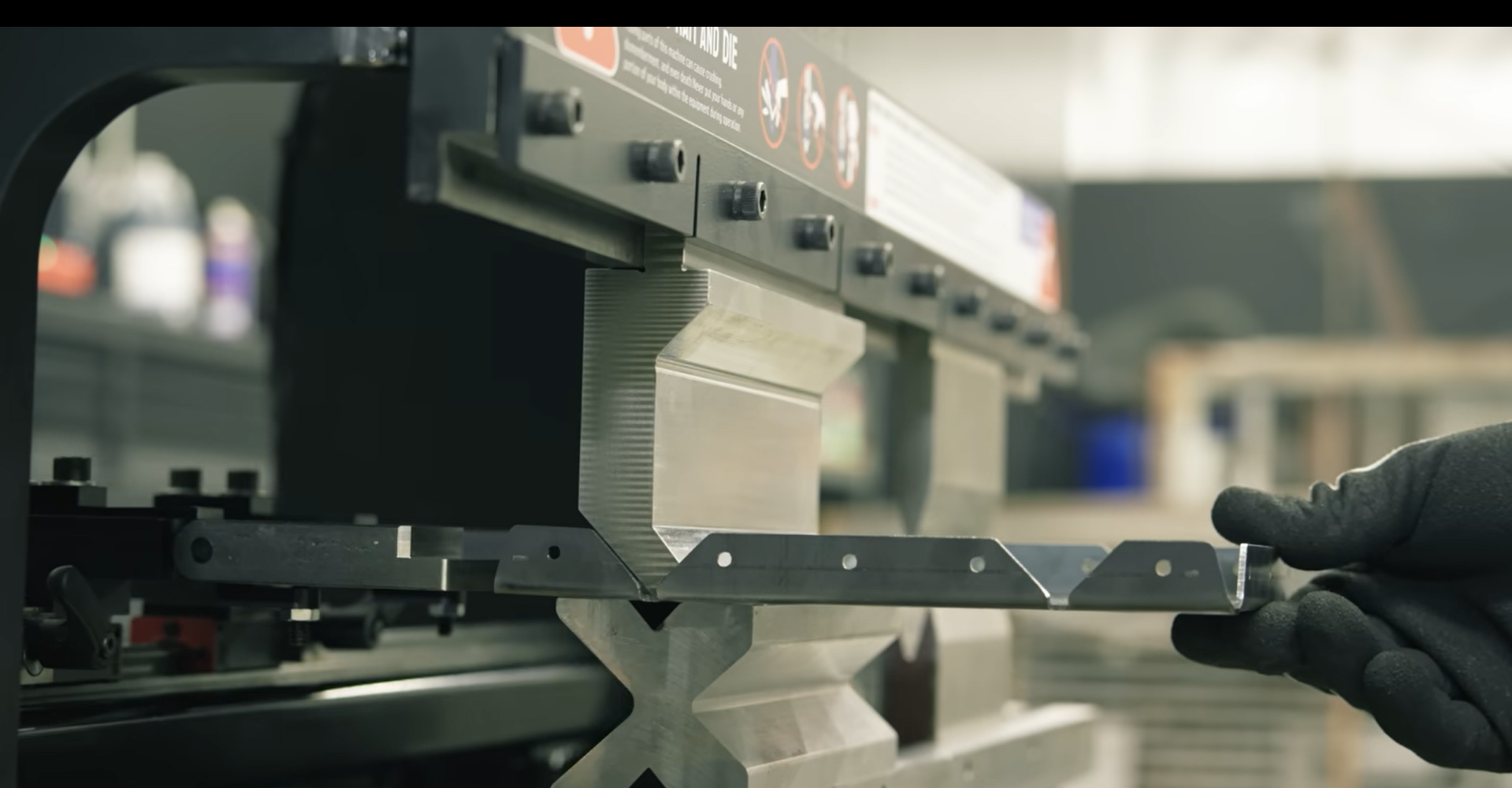
Let’s say you need to bend thin aluminium sheets for electronic boxes and thick steel plates for building projects. Make sure the press brake can do both jobs.
Find Tonnage Capacity and Bending Length
After that, figure out the tonnage capacity and bending length you need for your work. The tonnage capacity means the highest force the press brake can apply. It’s also known as the bending force. It should be enough to bend the thickest and toughest materials you use. The bending length is how long the press brake bed is.
The length decides the longest piece of material you can bend at once. If you make long metal panels for building, you’ll need a press brake with a longer bed and higher tonnage capacity.
Automation Features
Take a close look at the control systems and automation features of the press brake. Today’s press brakes come with cutting-edge control systems that boost precision and make them easier to use. Keep an eye out for features like CNC (Computer Numerical Control) to automate and improve bending accuracy.
Features that automate tasks, such as tool changers that work on their own, back gauges, and systems to measure angles, can boost productivity and cut down on manual work. If you run a facility that produces a lot, a CNC press brake with these automation features can speed up bending and make sure quality stays the same across the board.
Brand Reputation and Support
Check out the maker’s standing and help choices. Look into the maker’s track record for top-notch products and dependability by reading what other users say about them. Make sure the maker gives strong help and service options, like upkeep, training, and easy access to spare parts. Good help can cut down on time when machines aren’t working and keep your work going without a hitch.
Picking a press brake from a well-known maker with a solid help network can give you peace of mind and make sure it works well for a long time.
Additional Factors to Consider
Think about other things like if the tools work with it how easy it is to use, safety features, and how much energy it uses. Make sure the press brake works with the tools you need for your specific bending jobs, as having tools that can do many things can make it useful for more tasks.
Alternative to Press Brakes
1. Folding Machines: These machines excel at making exact folds and bends in sheet metal. They work well with bigger panels and can handle tricky bending jobs with great accuracy. Folding machines stand out for their ability to create steady bends without much help from the operator.
2. Panel Benders: Panel benders are automatic machines built for high-output production. They’re perfect for creating complex shapes and bends in sheet metal. Panel benders can work with many materials and thicknesses, which makes them flexible for different manufacturing jobs.
Conclusion
Press brake technology plays a key role in fabrication shops as machine tools that bend simple and complex parts for different industries. Modern press brakes work well and use cutting-edge tech, shaping metal with punches and dies. For a press brake operator, it’s crucial to know the basics of how these tools work and how to use them.
For high-quality, custom laser-cut parts for press brake machines, folding machines, and other large-scale machinery, consider partnering with BaisonLaser. Our expertise in producing precision components can skyrocket your manufacturing speed! Contact BaisonLaser today to learn more about our services!