Understanding Holemaking in Sheet Metal
Holemaking plays a crucial role in various sheet metal applications. Whether it is for fasteners, ventilation, or electrical components, creating holes in sheet metal is essential.
Holemaking refers to the process of creating holes in the sheet metal. It is a fundamental step that allows for the integration of different components and functionalities within a sheet metal structure. Holes may serve as entry points for wires, connectors, or mechanical fasteners. They also aid in improving airflow and reducing weight by removing unnecessary material.
Punching Machines for Holemaking
Punching might be the most economical way to produce holes. These powerful machines, also known as punch presses, employ punching operations to efficiently and effectively produce precise hole patterns in various types of materials. Let’s delve into the benefits and limitations associated with using punching machines for holemaking.
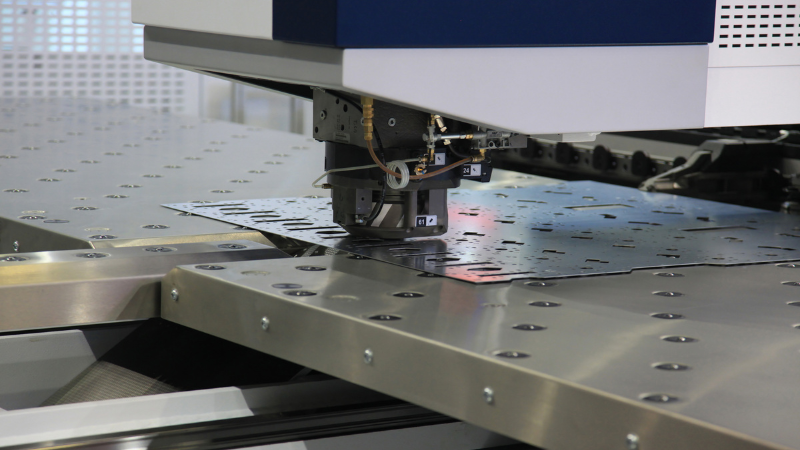
Benefits of Using Punching Machines
- Speed: Punching machines are renowned for their high-speed operation, allowing for rapid production of holes in sheet metal.
- Cost-effectiveness: By automating the holemaking process, punch presses enable efficient production and reduced labor costs.
- Versatility: These machines offer a wide range of tooling options, allowing for flexibility in creating different hole sizes and shapes. So you should consider the final hole size.
- Production efficiency: The punching pattern can handle large volumes of sheet metal, making them ideal for mass production scenarios.
- Consistency: With precise controls and reliable tooling, punching processes ensure consistent hole quality throughout the production run.
Limitations Associated with Punching Machine Holemaking
- Punching force limitations: The ability of the punch press may restrict the thickness and hardness of materials it can effectively punch through. To help keep sheets flat, the punching pattern can be altered to avoid concentrating all the punched holes in one area.
- Tool wear: Continuous use can lead to wear on punches and dies, necessitating regular maintenance and replacement to maintain optimal performance.
- Limited hole shapes: While capable of producing various hole patterns, punching machines have certain restrictions.
Laser Cutting for Holemaking
Laser cutting is a remarkable technique for creating holes in sheet metal. By utilizing laser cutters, this process offers several advantages, including precision and versatility. Let’s delve into how the laser cutting process works and explore the advantages and disadvantages of laser cutting.
How Laser Cutting Works
When a laser beam interacts with a workpiece, it generates an intense heat that melts or vaporizes the material along the hole perimeter. The laser’s focused energy allows for precise and accurate cuts, resulting in clean and smooth edges. Two common types of lasers used for holemaking are fiber laser cutting technology and CO2 lasers.
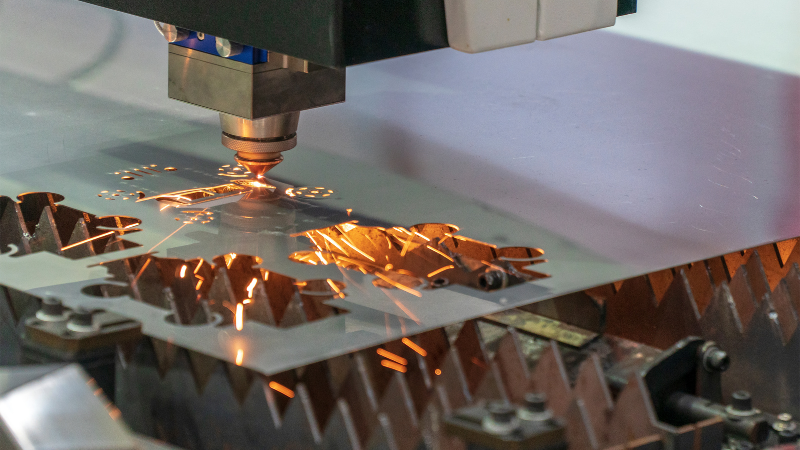
Advantages of Laser Cutting
Laser cutting has gained popularity due to its numerous benefits:
- Precision: The focused laser beam ensures high accuracy, allowing for intricate hole shapes.
- Versatility: Laser cutters can create hole patterns in various materials like stainless steel, aluminum, brass, and more.
- Speed: This method enables fast production rates compared to traditional holemaking techniques.
- Minimal Material Distortion: As the heat input is localized, there is minimal distortion to the surrounding material.
- No Tool Wear: Unlike punching machines that require frequent tool replacements, laser cutters have no physical contact with the workpiece.
Disadvantages of Laser Cutting
- Start-Up Costs: Setting up laser cutting equipment involves initial expenses, including the cost of the machine and necessary safety measures. This can be a barrier for small-scale or occasional use.
- Noise and Fumes: Laser cutting can generate noise and release fumes, especially when cutting certain materials. Adequate ventilation and noise mitigation measures may be necessary.
Comparative Analysis
Two popular options are laser cutting and punching machines. Let’s dive into a detailed comparison between these technologies and explore the factors that need to be considered: speed, accuracy, and material thickness compatibility.
Speed
- Laser cutting: Utilizes high-powered lasers to quickly cut through sheet metal.
- Punching machines: Employ mechanical force to punch holes at a rapid pace.
Accuracy
- Laser cutting: Provides exceptional precision, allowing for intricate designs and patterns.
- Punching machines: Offer good accuracy but may not be as precise as laser cutting technology.
Material Thickness Compatibility
- Laser cutting: Suitable for a wide range of materials and thicknesses no whether thin sheet metal or thicker materials.
- Punching machines: More suitable for thinner sheets of metal.
Long-Term Cost Considerations
Laser cutting and punching machines are two popular methods. However, it’s important to consider the long-term costs associated with both options. Here are some factors to keep in mind when evaluating their cost-effectiveness over time.
Initial Investment
Laser Cutting: The initial investment for a laser cutting machine is typically higher compared to a punching machine.
Punching Machine: Punching machines generally have a lower initial cost, making them more accessible for smaller businesses.
Maintenance
Laser Cutting: Laser cutting machines require regular maintenance and calibration to ensure optimal performance.
Punching Machine: Punching machines also need maintenance but usually have simpler mechanisms that may result in lower maintenance costs.
Consumables
Laser Cutting: Laser cutting involves the use of consumables such as laser gases and lenses, which can add up over time.
Punching Machine: Punching machines use tooling components like punches and dies that may need occasional replacement but tend to be less costly than laser consumables.
Considering these factors, the cost advantages of each method can vary depending on your specific requirements and business needs. While laser cutting may have a higher initial investment and ongoing consumable expenses, its precision and versatility might make it more suitable for certain applications. On the other hand, punching machines offer a cost-effective solution for the simpler hole pattern or high-volume production.
FAQs
Can I use punching machines for intricate hole shapes?
Yes, punching machines are best suited for simpler hole shapes like the round hole or square. For more intricate designs or irregular hole patterns, laser cutting offers greater versatility.
Does laser cutting produce cleaner edges compared to punching machines?
Yes, laser cutting produces cleaner edges with minimal burrs compared to punching machines. This makes it ideal for applications where aesthetics or smoothness of the cut edge is crucial.
Which method is more cost-effective in the long run?
The cost-effectiveness of each method depends on various factors such as production volume and complexity of designs. In general, if you have high-volume production needs with simple hole shapes, punching machines may be more cost-effective. However, for low-volume production or complex designs, laser cutting can offer long-term cost savings due to its efficiency and reduced material waste.
Conclusion
We explored both punching machines and laser cutting as viable options for creating holes in sheet metal, now that you have a better understanding of holemaking in sheet metal. Punching machines offer high-speed production and cost-effectiveness for simpler hole shapes, while laser cutting provides greater flexibility and precision for complex designs.
In conclusion, It ultimately depends on your specific needs and requirements. If speed and cost are paramount, punching machines may be the way to go. However, if you prioritize flexibility and precision, laser cutting is likely the better option.
Experience the Future of Holemaking with Baison Laser
Ready to make an informed decision for your holemaking needs? Explore the precision and excellence of laser cutting with Baison Laser. Discover how our cutting-edge laser cutters like the fiber laser cutting machine redefine sheet metal fabrication. Check out our production catalog and ask our experts if you have any questions.