Introduction
Laser cleaning and sandblasting are two widely used cleaning processes in industrial applications. Laser cleaning uses a high-energy laser beam to vaporize surface contaminants. Sandblasting, on the other hand, uses high-velocity particles to strip away a thin layer from the object’s surface.
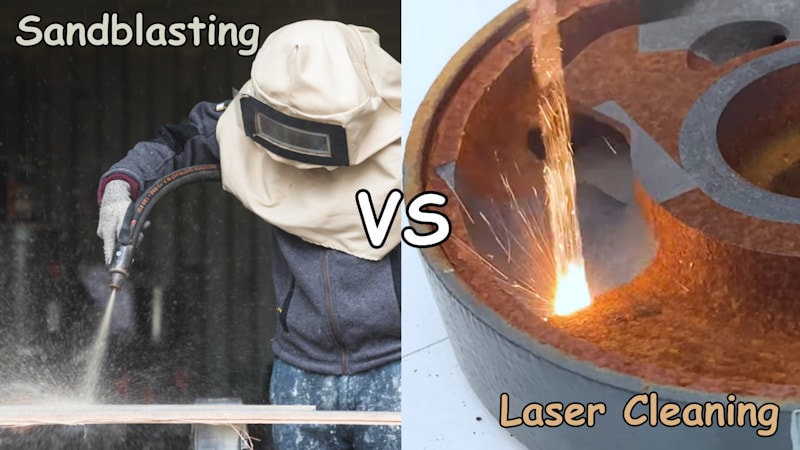
Which is perfect for your industry? What are the advantages and drawbacks? Find out in our Laser cleaning vs Sandblasting comparison guide!
What Is Laser Cleaning?
Laser cleaning is a non-contact surface preparation method that uses focused laser beams to remove contaminants, coatings, or unwanted materials from a substrate. The process works by directing high-energy laser pulses onto a surface. These pulses are absorbed by the unwanted layer, causing it to vaporize or break apart, while the underlying material remains unharmed.
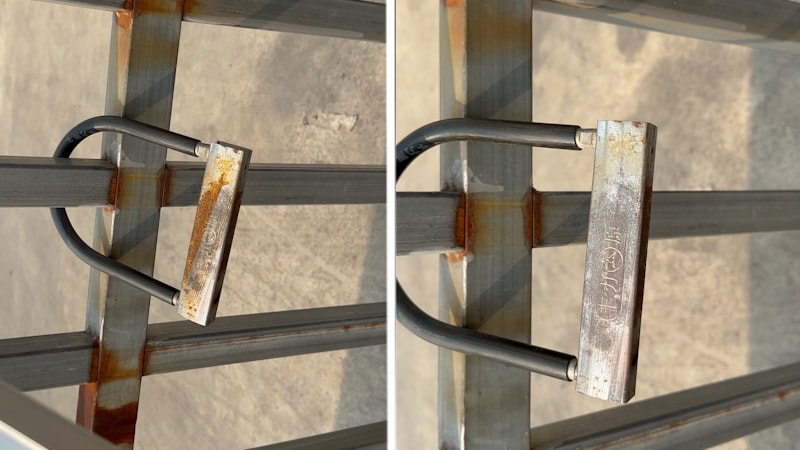
The technology relies on precise control of laser parameters such as pulse duration, energy, and wavelength to selectively target contaminants without damaging the base material. Unlike traditional methods, laser cleaning is highly controlled and repeatable for industrial use.
Fiber laser cleaning is widely adopted in the aerospace, automotive, and electronics industries. In aerospace, it is used to remove coatings, clean moulds, and prepare surfaces for bonding or welding, all without altering sensitive substrates.
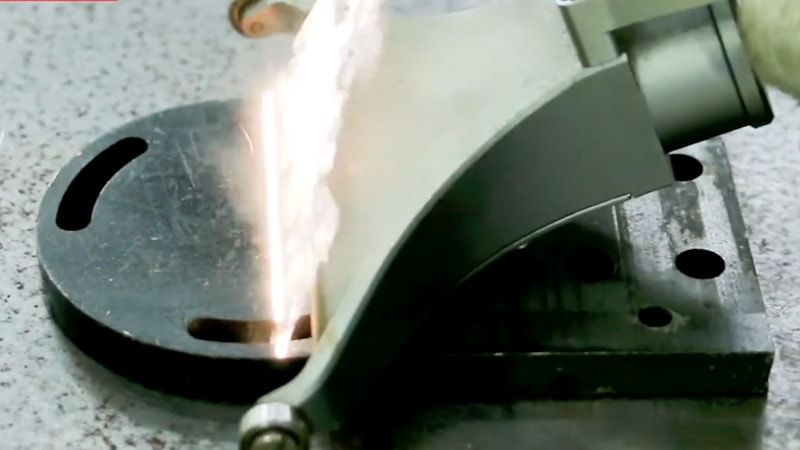
The automotive sector uses laser cleaning for rust removal, weld preparation, and injection mould cleaning. The method removes oxides, films, and residues from delicate components in electronics manufacturing, often in automated or robotic setups. Its versatility extends to sectors like shipbuilding, construction, and precision engineering.
Learn how to choose the best laser cleaning machine for your industrial applications.
What Is Sandblasting?
Sandblasting, or abrasive blasting, is a surface treatment process where you propel abrasive materials-such as sand, steel grit, or glass beads-at high speed using compressed air or a centrifugal wheel. This action removes rust, paint, scale, or other contaminants from surfaces and can also texture or smooth them.
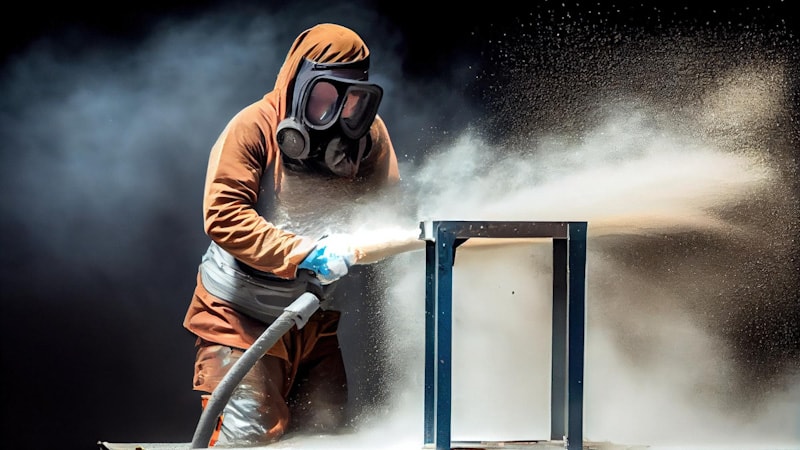
The process involves a blast pot, an air compressor, and a nozzle. You select the abrasive based on the substrate and the desired finish. Sandblasting is adaptable for metals, concrete, glass, and plastics.
You will find sandblasting widely used in construction, manufacturing, automotive, and marine industries. It prepares concrete, cleans facades, restores monuments, and strips paint or rust from vehicles. The oil and gas sector uses sandblasting to maintain pipelines and rigs, while heavy machinery maintenance relies on it for cleaning and refurbishing equipment.
The main benefits of sandblasting are its cost-effectiveness and efficiency for large-scale cleaning. The process is fast and reduces manual labor. You can often reuse the abrasive media, which lowers costs further. Sandblasting also improves surface quality, making applying new coatings easier and extending the life of treated components.
Be aware of the hazards of sandblasting, though.
Laser Cleaning vs Sandblasting: A Detailed Comparison
1. Efficiency and Speed: Which Method Saves Time and Costs?
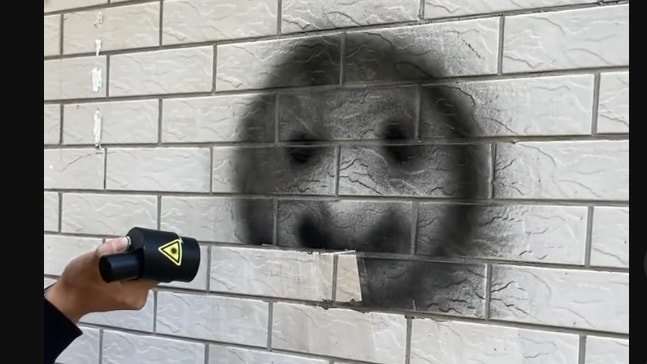
Laser cleaning offers high efficiency because you do not need to use consumables or spend time on abrasive replenishment. The process is fast, with minimal setup and cleanup. You benefit from rapid turnaround and lower labor requirements; ideal for operations where speed and continuous production are critical. It also makes you decent money if you provide a service based on it!
Sandblasting is more time-consuming due to the need for regular abrasive replenishment and equipment setup. You must also manage post-cleaning dust and debris, which further increases downtime. For large or frequent jobs, the cumulative time spent on preparation and maintenance can lead to higher operational costs and longer project timelines.
Precision: Which Method Provides Better Surface Quality?
Laser cleaning equipment delivers exceptional precision because it is a non-contact process. You can target contaminants without touching or damaging the underlying surface, making it suitable for delicate and intricate components. The focused laser beam allows for selective cleaning, preserving fine details and original surface integrity.
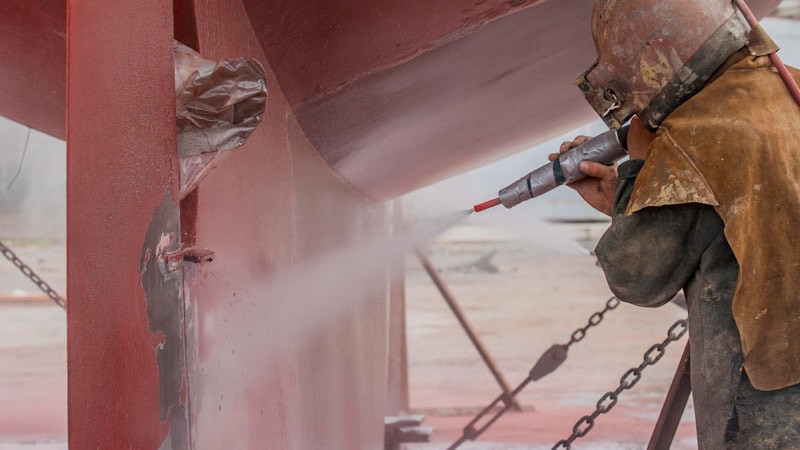
Sandblasting uses abrasive contact, which can increase surface roughness or cause material wear. You may achieve effective cleaning, but the process can damage sensitive substrates or erode fine features. This makes sandblasting less suitable for applications requiring high surface quality or preserving intricate details.
2. Environmental Impact: Which Method Is More Sustainable?
Laser ablation is highly eco-friendly, as you do not use chemicals or create abrasive waste. The process produces minimal dust and the only byproduct is a small amount of vaporized material, which you can filter. This reduces environmental impact and regulatory concerns.
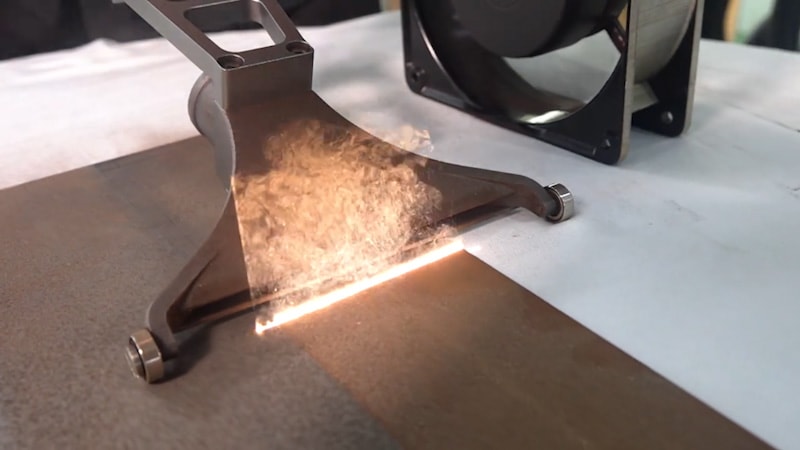
Sandblasting generates significant amounts of dust and spent abrasive, which can harm both the environment and operator health. You must handle and dispose of used media, and airborne particles can contribute to pollution. The process often requires additional controls to mitigate environmental risks.
3. Maintenance and Operational Costs
Laser cleaning systems require low maintenance because there are few moving parts and no consumables. You only need to perform routine checks and occasional cleaning of optical components. Over time, you save on operating costs, equipment wear, and labor. Laser is a cost-effective solution for long-term use.
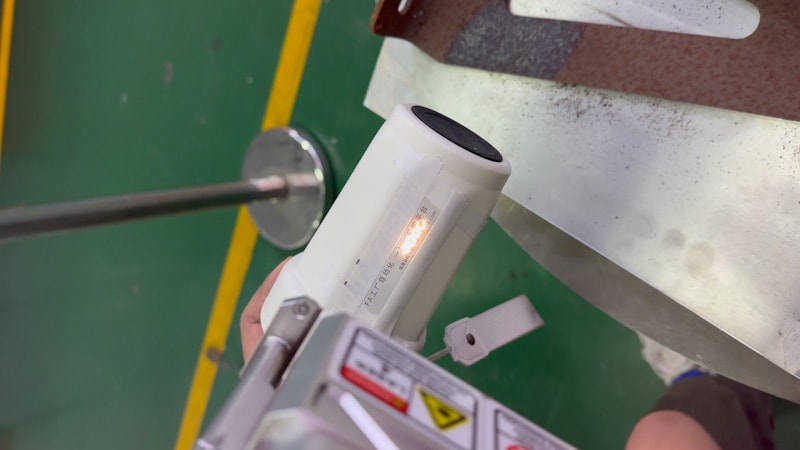
Sandblasting involves ongoing costs for abrasive media, frequent replacement of worn parts, and regular maintenance to address machine wear. You must inspect and service components such as nozzles and hoses, which increases downtime and total cost of ownership. The need for consumables and higher maintenance makes sandblasting less economical in the long run.
Pros and Cons of Laser Cleaning and Sandblasting
Here’s a quick overview of the pros and cons of both technologies. Let’s examine each one’s distinct advantages and disadvantages.
Laser Cleaning Technology
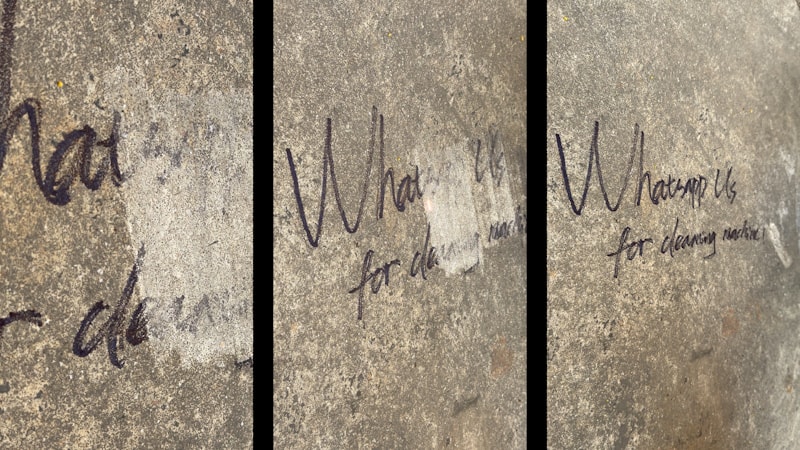
Pros | Cons |
---|---|
No damage to substrate; non-contact process | High initial equipment cost |
High cleaning speed and efficiency | Not suitable for narrow spaces or crevices |
Excellent cleaning quality and precision | Ineffective on highly reflective materials |
Environmentally friendly; no chemicals or waste | Slow for large surface areas |
Minimal operator risk; easy safety controls | Requires technical expertise and training |
Reduces consumables and waste management costs | Higher energy consumption for some applications |
Suitable for automation and integration | Limited effectiveness on thick coatings/rust |
Learn more about the advantages and disadvantages of laser cleaning!
Sandblasting
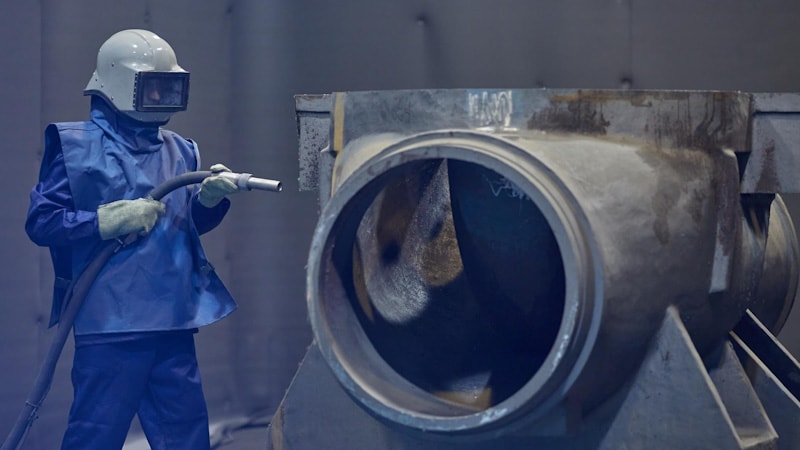
Pros | Cons |
---|---|
Effective for rust, grime, and paint removal | Can damage smooth or delicate surfaces |
Fast and efficient for large areas | Generates significant dust and air pollution |
Versatile- works on metal, concrete, wood, stone | Causes material erosion and surface roughness |
Simple setup and machinery | Health risks from dust and abrasive exposure |
Cost-effective for large-scale cleaning | Requires frequent abrasive replenishment |
Suitable for complex shapes and corners | Not suitable for heat-sensitive materials |
Automatable for continuous processing | High safety precautions and protective gear are needed |
Produces a uniform surface finish | Waste management and disposal are required |
Which Surface Cleaning Technology Is Right for Your Business?
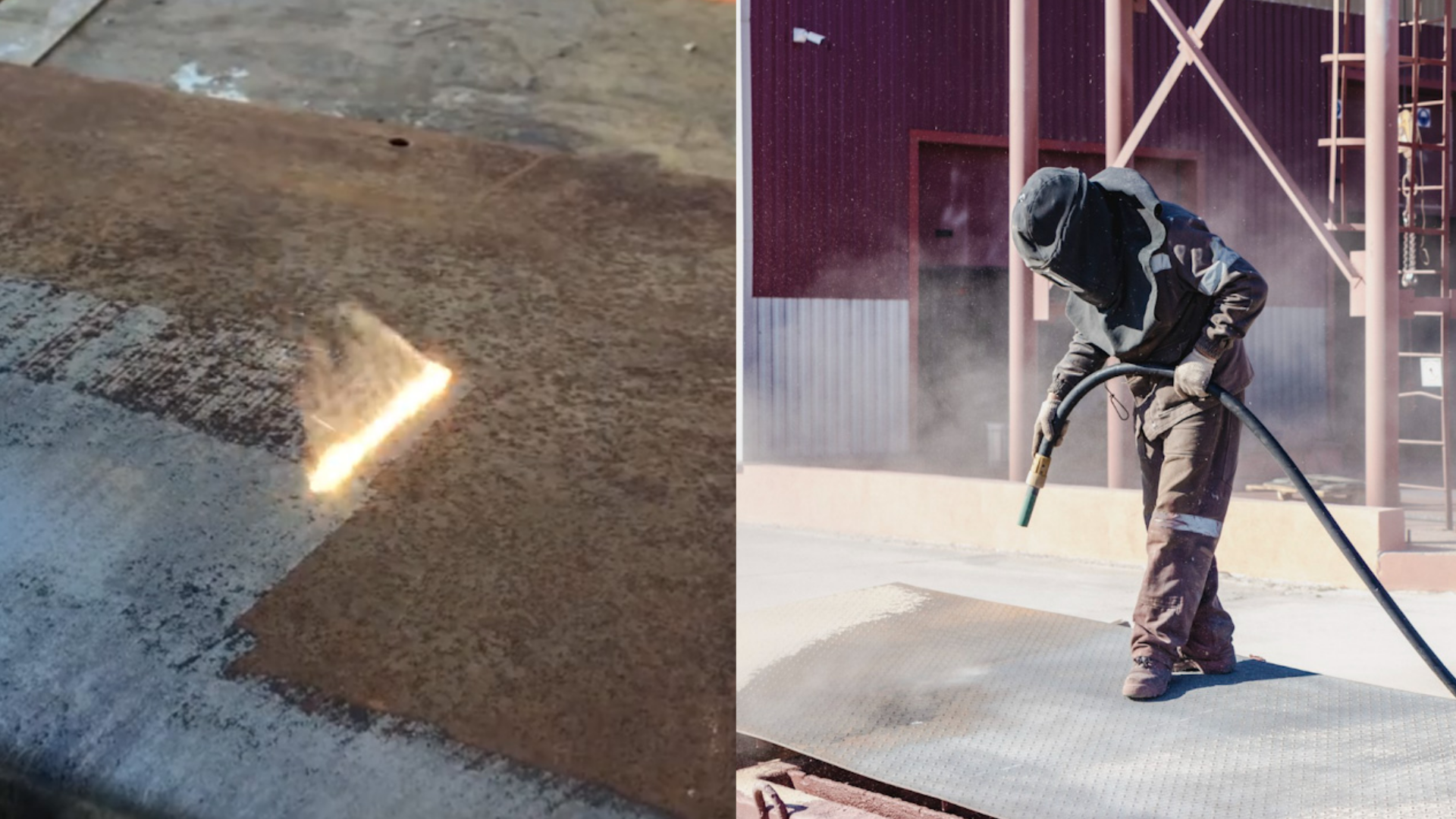
Factors to Consider:
Precision Needs: Choose laser cleaning if you require high precision or need to protect delicate surfaces. Sandblasting suits large, robust surfaces where fine detail is less critical.
Material Sensitivity: Laser cleaning is ideal for sensitive substrates like electronics or fine machinery. Sandblasting may damage soft or intricate materials.
Speed and Efficiency: Laser cleaning reduces downtime with fast, automated operation and minimal consumables. Sandblasting is effective for large areas but requires more setup and cleanup time.
Environmental Impact: Laser cleaning produces little to no waste or dust. Sandblasting generates significant dust and requires abrasive disposal.
Safety: Laser cleaning is generally safer for operators, while sandblasting poses risks from dust and abrasive exposure. Stay safe with proper safety precautions.
Cost: Laser cleaning has a higher upfront cost but lower long-term operational expenses. Sandblasting is cheaper to start but incurs ongoing costs for abrasives and maintenance.
Regulatory Compliance: Consider environmental and safety regulations relevant to your industry.
How to Integrate Laser Cleaning or Sandblasting into Your Business
Laser Cleaning
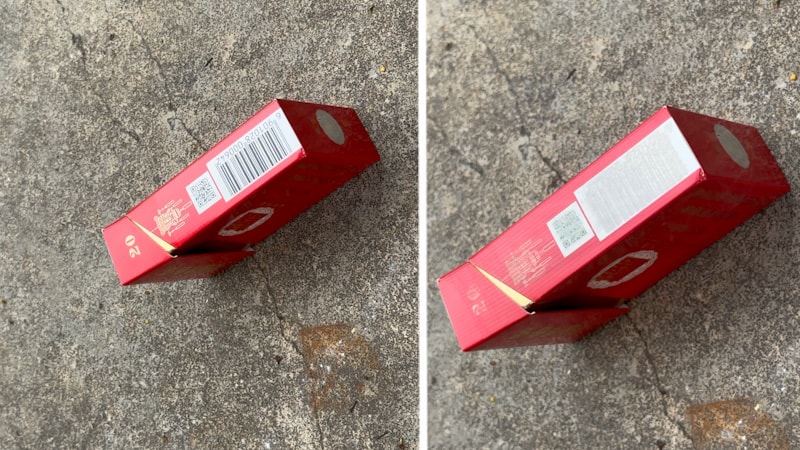
- Integrate laser cleaning with robotic arms or gantry systems for automated, high-throughput cleaning.
- Retrofit laser heads into existing production lines or robotic cells to clean parts before or after other processes.
- Use machine vision and sensors for precise targeting and real-time quality checks.
- Enclose laser systems in safety work cells to protect operators and enable 24/7 operation.
- Automate waste extraction and fume control for a clean, low-maintenance environment.
- Scale up by adding multiple laser units for larger or more complex tasks.
Sandblasting
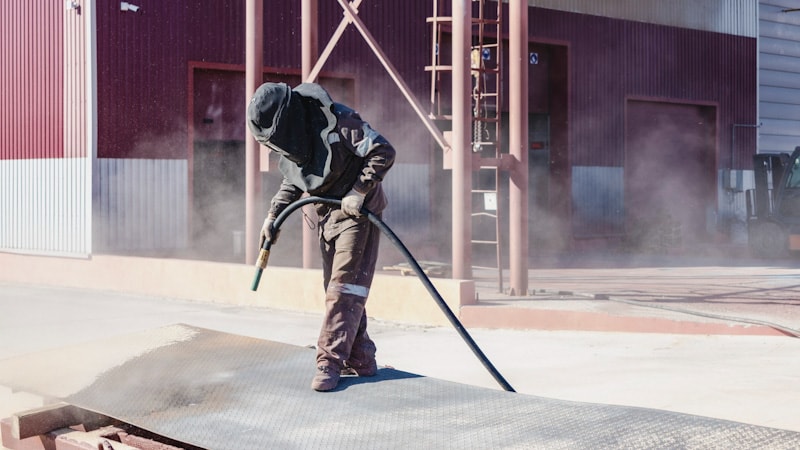
- Choose automated sandblasting cabinets or rooms for batch or continuous flow integration.
- Plan for adequate containment and ventilation to manage dust and abrasive waste.
- Use media recovery and recycling systems to minimize waste and lower costs.
- Regularly check and maintain nozzles, hoses, and media valves to ensure consistent performance.
- Integrate with conveyor systems or robotic arms for efficient loading and unloading.
- Schedule maintenance to prevent downtime and keep production flowing smoothly.
Real-World Case Studies: Laser Cleaning vs Sandblasting
Rolls-Royce adopted laser cleaning for electron beam welding of aero engine components in 2008. Before this, manual chemical cleaning caused productivity losses and chemical waste. After switching, Rolls-Royce improved productivity, reduced scrap, and eliminated hazardous chemicals, saving millions of pounds annually.
A renowned automotive company in India integrated a large sandblasting cabinet for cleaning engine components across 12 plants. Previously, manual cleaning was inefficient for complex parts. The new system increased cleaning rates, improved quality, and provided a pollution-free, automated environment for high-volume production.
Conclusion: Is Laser Cleaning Better Than Sandblasting for Your Industry?
Laser cleaning excels in precision, surface protection, and sustainability. It’s ideal for industries requiring delicate, residue-free results and minimal environmental impact. However, sandblasting remains viable for cost-effective, large-scale cleaning of robust materials where fine detail is less critical.
Before selecting a technology, you should assess your specific requirements, including material sensitivity, throughput, budget, and environmental priorities.
Laser Cleaning Machine Price: Superfast Sample Proofing and Quote by Baison Laser!
Not sure how much a laser cleaning machine costs? Or which brand reputation to trust? Baison Laser is your ultimate laser source!
We have the best laser technology for highly efficient cleaning with advanced features for commercial applications. Get a quote today! We also offer sample proofing so you know our fiber lasers are ready for heavy-duty applications!