In the high-precision, fast-paced world of laser cutting, one component stands out as a critical factor in optimizing operations: the laser assist gas generator. Often overlooked, these devices play a pivotal role in driving operational efficiency, ensuring quality, and managing operational costs.
This article uncovers the strategic importance of laser generators, including a detailed explanation of their working principles and the factors influencing their performance.
What Is Laser Cutting?
Laser cutting is a non-contact manufacturing and production process in which a highly intense laser beam is used to cut or engrave various materials. The term “LASER” in laser cutting stands for Light Amplification by Stimulated Emission of Radiation. It involves the use of a laser generator to produce a concentrated beam of light, which is then directed onto the material using lenses.
This versatile process can cut a wide range of materials, including metals, plastics, wood, and glass. It is highly valued for its precision and speed and can handle intricate designs. This makes it a popular choice such as the manufacturing, automotive, aerospace, and electronics industries.
How Does Laser Cutting Work?
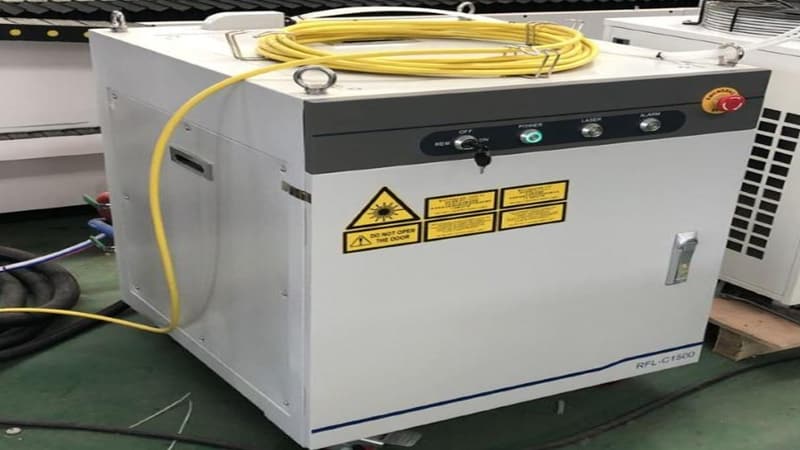
The laser-cutting process begins with the generation of a laser beam. This concentrated beam of light is directed onto the material surface using a series of mirrors and lenses. They focus on a precise point. The intense heat energy from the laser head causes the material to melt or vaporize, generating a cut or an engraving.
The laser head cutter is controlled by a computer numerical control (CNC) system, which guides the laser beam along the cutting path. So, this laser machine can cut intricate patterns with great precision.
A stream of gas, often referred to as ‘assist gas,’ is used to eject the molten material from the cut, resulting in a clean and precise cut edge. This gas, usually oxygen or nitrogen, is generated by on-site gas generators, shortly called laser generators.
What Is a Laser Generator?
In one terminology, the laser generator is called the laser source, which generates a highly concentrated, monochromatic, and coherent beam of light, focused at a point.
However, an assist gas generator is also referred to as a laser generator. Laser gas generation systems produce high-purity gases necessary for laser cutting processes. The assist gas from these generation units helps in achieving clean, precise cuts and prevents oxidation at the cut edges.
How Do Laser Gas Generators Work?
Laser generators generate an assist gas which is directed to the cutting surface to help evacuate the molten material from the cut line and prevent oxidation.
Typically, nitrogen-assist gas generators are more prevalent in industries. The gas molecules are particularly separated/generated via two principles: pressure swing adsorption (PSW) and membrane separation. The detail of which is discussed in the later section.
Types of Laser Generators
The classification of laser generators is based on the gas they produce for laser waste evacuation. There are compressed air, oxygen, and nitrogen generators. However, an on-site nitrogen generation system is more feasible for industrial applications.
Further, nitrogen generators have two types based on the principle in which nitrogen gas molecules are segregated:
Pressure Swing Adsorption (PSA) Generators
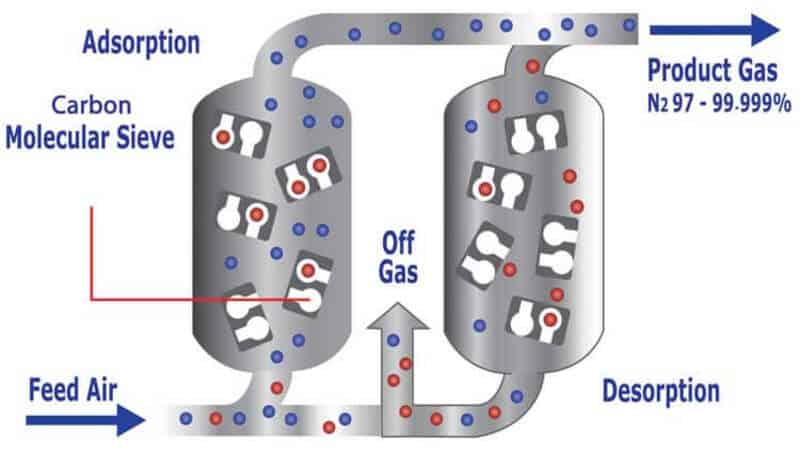
PSA Nitrogen Generators work like a big sieve or filter. They use a special material called a Carbon Molecular Sieve (CMS). This material is like a sponge with lots of tiny holes or pores.
When compressed is pushed into this sieve under high pressure, the smaller oxygen particles get trapped in the tiny pores, while the larger nitrogen particles can’t fit and bounce off, continuing their journey through the sieve.
This process happens in two tanks’ filled with CMS. While one tank is trapping oxygen and letting nitrogen pass through, the other tank is releasing the trapped oxygen (now at a lower pressure) back into the atmosphere. These two processes – trapping oxygen and releasing it – ‘swing’ back and forth between the two tanks, hence the name ‘Pressure Swing Adsorption’.
At the end of this swinging process, a stream of nitrogen gas, separated from the original mixture, is obtained. It is ready for use in laser-cutting applications.
Membrane Separation Generators
A nitrogen generator is like a long tube or a bunch of straws bundled together. These are ‘membranes’, which are essentially small hollow fibers. They’re special because they have tiny ‘pores’ in their walls.
These membranes have selective permeability. So, when compressed air is passed through hollow fibers, they allow oxygen, water vapor, and other impurities to permeate the membrane wall, while nitrogen molecules leave through the other end of the tube due to their lower permeability rate.
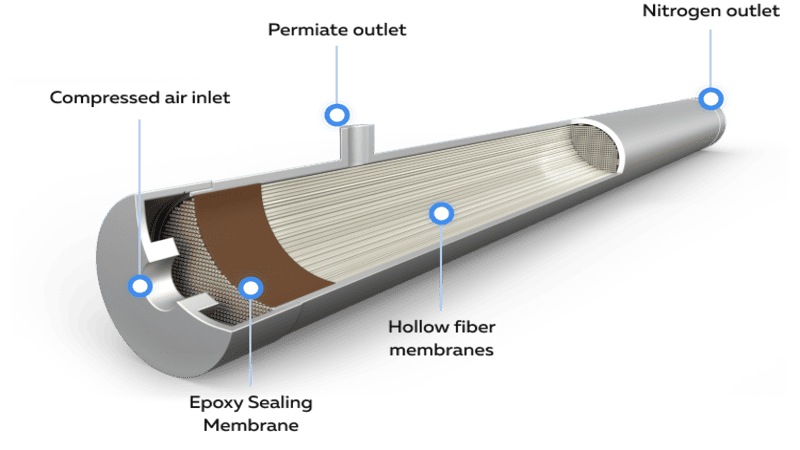
What Are the Factors Affecting Laser Generator Performance?
The properties of the assist gas generated by laser assist gas generators can significantly impact the quality and efficiency of laser cutting. Here are some critical factors:
Gas Purity:
The purity of the assist gas greatly affects the cutting process. High-purity gases result in cleaner cuts, less oxidation, and fewer impurities on the cut edges.
The gas purity must be chosen based on the thickness of the material. For instance, thick gauge stainless steel sheets require 99.99% pure nitrogen, while a purity of 99.90% would be enough for normal thin sheets. Modern in-generation gas systems have options to adjust the purity levels.
Gas Pressure:
The pressure at which the assist gas is delivered can influence the quality of the cut. Higher pressures can help to clear out molten material more effectively, resulting in cleaner cuts. However, excessive pressure might lead to unnecessary waste of gas.
The exact pressure varies based on the cutting operation and flow rate. However, typically a gas pressure between 350 to 400 is needed at the inlet of the laser.
Gas Flow Rate:
The assist gas’s flow rate affects the cutting process’s speed and quality. A higher flow rate can provide better cooling and more efficient removal of molten material but might increase operational costs due to greater gas consumption.
An assist gas generator typically needs to supply at least 1000 cubic feet per hour.
Type of Gas:
The type of assist gas significantly influences the cutting process. For example, oxygen can increase cutting speed in carbon steel due to its oxidizing effect, while nitrogen can provide oxide-free cuts in stainless steel and aluminum.
Gas Temperature:
The temperature of the nitrogen assist gas can also affect the cutting and welding process. If the gas is too hot, it may not effectively cool the cutting area, which can lead to poor cut quality.
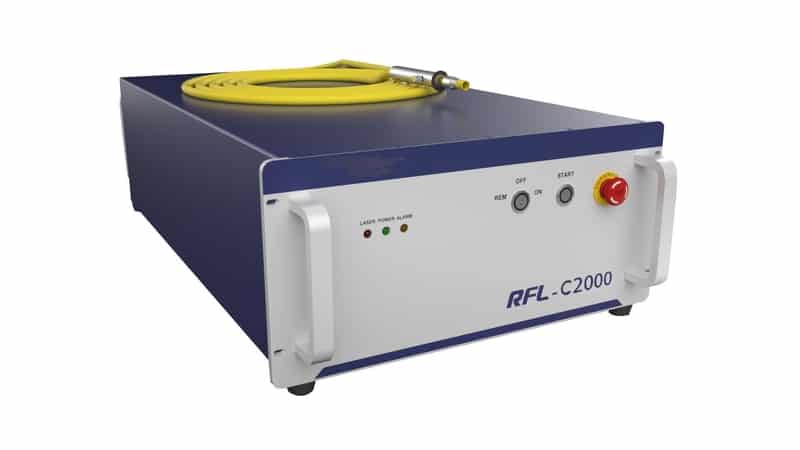
Benefits of High-Nitrogen Generators for Laser Cutting
Nitrogen generation systems bring several advantages to the table when used in laser cutting operations. Here are some key benefits:
Improved Cut Quality: Nitrogen is an inert gas that does not react with the cut material. This reduces oxidation at the cut edges, leading to cleaner, high-quality cuts, especially for materials like stainless steel and aluminum with undesirable oxidized edges.
Increased Efficiency: Industries get a steady supply of high-purity nitrogen with an on-site nitrogen generator. This eliminates the need for nitrogen gas cylinders. Therefore, there’s no downtime in production due to the gas supply running out—consequently, the overall efficiency of operations increases.
Cost Savings: While there’s an initial investment in purchasing and installing a nitrogen generator, the ongoing cost of producing nitrogen is significantly lower than the cost of continually purchasing and transporting bottled or liquid nitrogen. Over time, this results in substantial cost savings.
Dependability: Nitrogen generators are reliable and can produce high-purity nitrogen consistently, ensuring the consistent quality of the laser cutting process. Similarly, using an in-house nitrogen generation system is more convenient rather than buying gas from external suppliers.
Versatility: Nitrogen generators can be adjusted to produce nitrogen at different purity levels and pressures. This makes them versatile enough to accommodate a variety of cutter needs.
Some Popular Laser Generator Brands

The laser generators are produced by multiple local and international manufacturers. Here are a few popular names:
Generon
A pioneer in the world of on-site gas generation, Generon has carved a niche for itself with its efficient gas generators, pressure vessels, blowers, and gas conditioning units. Generon’s systems are known for their high-quality output and are a great fit for use with laser machines.
Atlas Copco
Atlas Copco is a globally recognized brand in designing gas generation systems. It offers a range of oxygen and nitrogen gas generators known for their efficiency and robustness. Their systems are versatile, catering to a wide range of purity and flow requirements, making them a favorite among many industries, including laser cutting.
Parker Hannifin
Parker Hannifin’s nitrogen generation systems are designed with a focus on reliability and ease of use. Their systems deliver high-quality nitrogen and have a reputation for longevity and consistent performance, making them a strong contender in the laser cutting sector.
Shenger Gas Equipment
With an emphasis on precision and durability, Shenger Gas Equipment offers a range of high-performance nitrogen generators. Their products are known for consistent results, which makes them a popular choice in the laser cutting industry.
CanGas Air Solutions
CanGas is renowned for its technologically advanced and energy-efficient nitrogen generators. Their air compressor systems are designed to deliver high-purity nitrogen gas. They are another great option for businesses looking for quality and effectiveness.
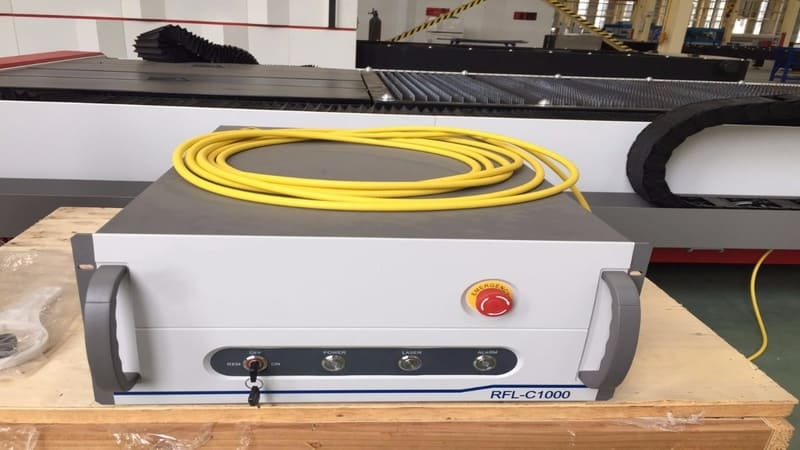
Conclusion
As we conclude this exploration of laser-assist gas generators, it’s clear that their role in laser-cutting operations is both crucial and transformative. These systems, particularly generators, are not just ancillary components of laser cutting machines but vital cogs in the wheel of laser cutting technology.
They enhance operational efficiency, improve cut quality, and offer significant cost savings, giving your business a competitive edge in this field.
From understanding how these generators work to exploring their various types and the factors that influence their performance, we have underscored the key benefits they bring to the table.
Discover the Perfect Solution for Your Business with Baison
As you contemplate the right laser-cutting solution for your business, Baison is here to help. We offer a range of services, from laser cutting and engraving machines to drilling and welding. All of our products are designed to meet your specific needs.
Don’t hesitate to request an instant quote for a tailored approach to your business needs. If you’d like to see firsthand the quality and precision we bring to the table, you can request free sample proofing.