What Is Laser Cutter Thermal Output?
A laser cutter can generate incredibly high temperatures, ranging from several hundred degrees Celsius to over 1000 degrees Celsius. These intense heat levels are necessary for the laser cutting process, as they allow the machine to melt or vaporize materials.
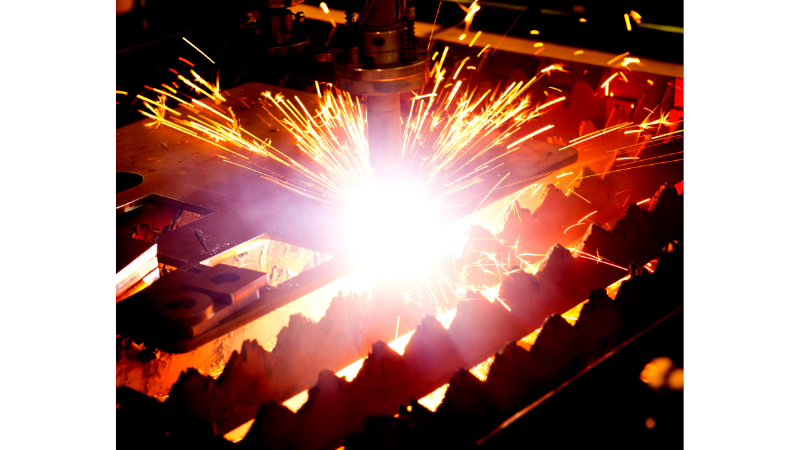
Understanding the thermal output of fiber lasers, crystal lasers, CO2 lasers, and diode lasers is crucial for maximizing their efficiency and ensuring optimal performance. The thermal output refers to the amount of heat produced during the cutting process, affecting everything from evaporation and fusion cutting to mechanical and die cutting sections.
The thermal output influences various factors like heat transfer, thermal distortion, and even molten material flow. By comprehending this aspect, users can optimize their laser cutting operations for better results. Whether we’re talking about emission or stimulated emission, scanning, or inert gas cutting processes, understanding the laser technology output’s thermal impact is essential for achieving desired outcomes.
Importance of Understanding the Laser Cutter Temperature Range
Understanding these temperature ranges is crucial when working with a laser cutter. For several reasons:
Safety: Laser cutting machines generate intense heat during the process of laser processing, and if not properly controlled, this heat from lasers can pose a safety risk. Excessive heat from the cutting machine can cause material ignition, fires, or even explosions. By understanding the thermal output of lasers, operators can implement appropriate safety measures to prevent accidents and ensure a safe working environment.
Cutting quality: The thermal output directly affects the quality of the cuts made by the laser cutting machine. Excessive heat can lead to material deformation, melting, or charring, resulting in imprecise or damaged cuts. By understanding and controlling the thermal output, operators can achieve the desired cutting results with clean, accurate, and high-quality cuts with the appropriate kerf width.
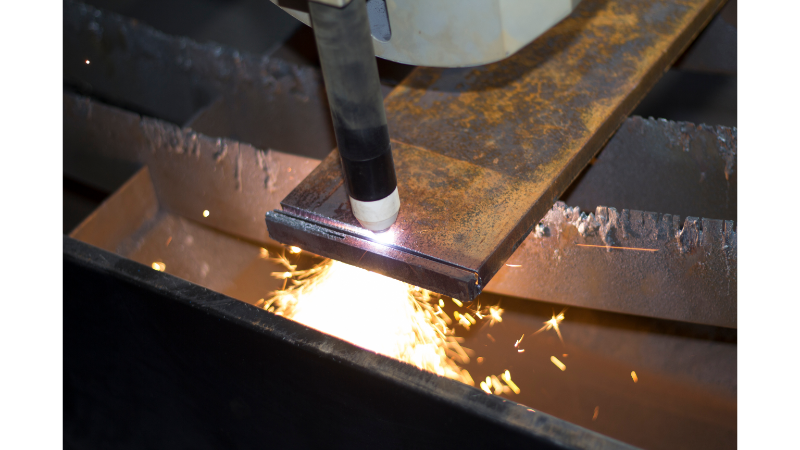
Material compatibility: Different materials have varying heat tolerances. Understanding the thermal output allows operators to select the appropriate laser power and cutting parameters for specific materials, especially highly reflective materials, organic materials, and the electrically conductive material. This ensures that the laser cutter operates within the safe thermal limits of the material, preventing damage or distortion.
Equipment longevity: Excessive heat can strain the components of lasers and plasma cutting machines, leading to premature wear and tear. By understanding and controlling thermal output, operators can prevent overheating and extend the lifespan of the cutting equipment. This reduces the need for frequent repairs or replacements, saving both time and money in the laser cutting process.
Energy efficiency: Excessive thermal output results in wasted energy. By understanding and controlling the thermal output, operators can optimize the laser cutter’s energy usage, reducing operating costs and promoting environmental sustainability.
When operating a laser cutting machine, it’s important to be aware of other cutting methods that use different heat sources such as waterjet cutting, plasma cutting, and mechanical cutting. Each method has its own temperature ranges and considerations for lasers, scanning, beams, and machines.
Types of Laser Cutters and Their Thermal Output
There are several types of laser cutters available in the market, each with different thermal outputs. The thermal output of a laser cutting machine refers to the amount of heat generated during the laser cutting process. The different types of laser cutters and their thermal outputs are as follows:
CO2 Laser Cutters
CO2 laser cutters are the most common type of laser cutters used in various industries. They use a carbon dioxide gas mixture as the laser medium and typically have a thermal output ranging from 10 to 150 watts due to their longer wavelength.
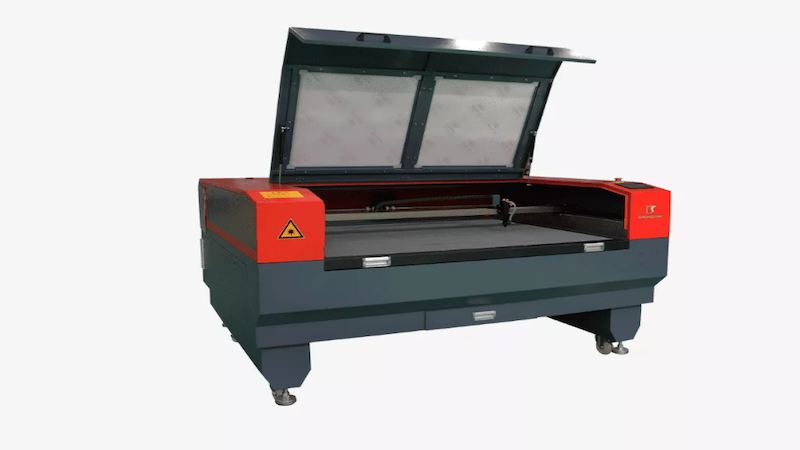
These laser cutters are versatile and can cut through a wide range of materials, including non metals like wood, acrylic, fabric, and certain metals. They excel in laser cutting processes like oxidation cutting where high temperature is necessary.
Fiber Laser Cutters
Fiber laser cutters use a solid-state laser source, typically a fiber laser, to generate the cutting beam. Due to fiber lasers, these laser cutters have a higher thermal output compared to CO2 laser cutters, ranging from 500 to 50,000 watts. Fiber laser cutters are known for their high precision and speed and are commonly used for cutting metals, such as steel and aluminum.
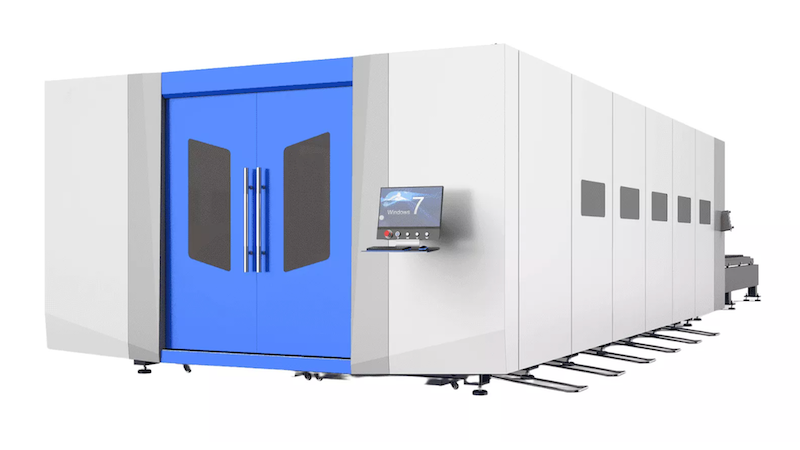
Diode Laser Cutters
Diode laser cutters use diode-pumped solid-state lasers as the laser source. These laser cutting machines have a lower thermal output compared to CO2 and fiber laser cutters, typically ranging from 10 to 100 watts. Diode laser cutters are often used for cutting thin materials, such as paper, cardboard, and thin plastics.
Nd: YAG Laser Cutters
Nd: YAG (Neodymium-doped Yttrium Aluminum Garnet) laser cutters use a crystal as the laser medium and have a thermal output ranging from 100 to 500 watts. These lasers are commonly used for precision cutting of materials, such as metals, including stainless steel and titanium, using a focused beam of gas.
It’s important to note that the thermal output of a laser cutting machine can vary depending on the specific model and manufacturer. It’s recommended to consult the specifications provided by the manufacturer to determine the exact thermal output of a particular laser cutter model.
Actual Thermal Output Measurement
Measuring the thermal output of a laser cutter is essential for optimizing its performance in the cutting process. It can be measured using various methods and instruments accurately measure output.
Power meter: A power meter is a device specifically designed to measure the power output of a laser. It typically consists of a sensor that detects the laser beam from the laser cutting head and provides an accurate reading of the power level. By measuring the power output, you can indirectly assess the thermal output of the laser cutter.
Infrared (IR) thermography: IR thermography involves using an infrared camera to capture thermal images of the laser cutting machine and the material being cut. This allows you to visualize and analyze the heat distribution and identify any hotspots or areas of excessive heat generation.
Thermocouples: Thermocouples are temperature sensors that can be attached to different parts of the laser cutter to directly measure the temperature. They can provide real-time data on the thermal output at specific locations, helping to monitor and control the heat generated during operation.
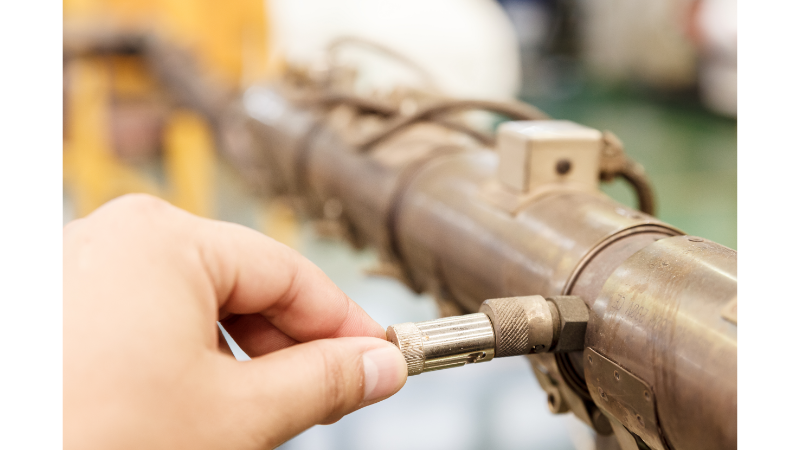
Thermal imaging cameras: Similar to IR thermography, these cameras can capture and analyze heat distribution in real time using laser energy. They provide a visual representation of the thermal output and help identify any potential issues related to heat buildup. These cameras work by detecting the laser beam emitted by a laser machine or laser system.
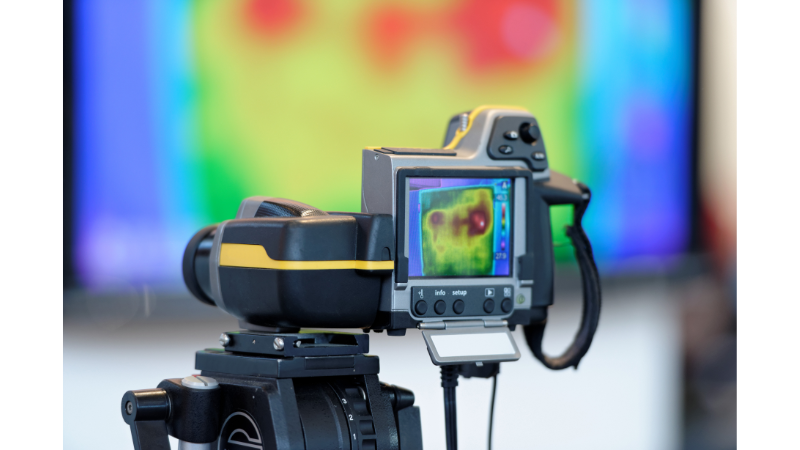
Factors like high power, light amplification, focal spot size, plasma formation, resolution requirements, crystal properties, and even inert gas usage can influence the thermal output of a laser cutter during the cutting process. Regular monitoring and measurement of the thermal output can help identify any deviations or abnormalities in heat transfer, allowing for timely adjustments and maintenance to ensure optimal performance and safety of the cutting beam and the quality of the final product.
Optimizing the Thermal Output of a Laser Cutter
The thermal output of a laser cutter is influenced by several key factors. Understanding these factors is crucial for achieving optimal cutting results and preventing potential issues. Here are some common methods to control the thermal output.
- Power settings: Laser cutters typically have adjustable power density settings that allow you to control the intensity of the laser beam during the cutting process. The upper and lower kerf widths increase as laser power increases. By reducing the power output, you can decrease the thermal output and prevent excessive heat buildup on the surface, thereby minimizing charring.
- Cutting speed: Adjusting the cutting speed of metal laser cutters can also impact the thermal output. Slower cutting speeds may generate more heat while increasing cutting speed can help dissipate laser energy more effectively. Finding the optimal cutting speed for each material can help control the thermal output of the laser machine.
- Material Properties: Different materials have varying responses to laser cutting, affecting their thermal output. Factors such as material composition, thickness, and even substrate type (like FR4) play a role in determining heat generation on the surface during the laser cutting process.
- Focus and beam diameter: The focus and beam diameter of the laser beam can greatly impact the cutting process. A smaller beam diameter and precise focus can concentrate the laser power on the heat affected zones, reducing the overall thermal output. The concentration of heat is crucial for an efficient cutting process.
- Cooling systems: Laser cutters often come equipped with cooling systems, such as water or air cooling, to dissipate heat generated during the cutting process. Ensuring these cooling systems are properly maintained and functioning optimally can help control the thermal output of the laser beam on the surface of the substrate and prevent damage to the cutting gas used in the cutting process.
- Oxygen and Nitrogen: When using different assist gases like oxygen or nitrogen during laser cutting, assist gas pressure can affect both material ignition temperature and overall thermal output.
By taking these factors into account when operating a laser cutting machine, you can optimize your cutting process while minimizing any adverse effects related to excessive heat generation. Remember to always refer to manufacturer guidelines and experiment with various settings to achieve desired results for different materials and applications.
FAQs
Can I use a regular thermometer to measure the temperature of a laser cutter?
No, using a regular thermometer is not recommended for measuring the temperature of a laser cutting machine during the cutting process. Laser cutters operate at extremely high temperatures, which cannot be accurately measured with conventional thermometers. This is because laser cutting machines rely on thermal efficiency and gas to achieve precise cuts on the surface.
How often should I measure the actual power output of my laser cutter?
It is advisable to regularly measure the thermal efficiency and power output of your gas-powered laser cutter, especially before important cutting projects. This helps ensure that the machine’s surface is operating at the desired power level and provides consistent results throughout the cutting process.
What are some common materials that can be cut using a laser cutter?
Laser cutters are powerful machines that can effectively cut through a wide range of materials, including wood, acrylic, leather, fabric, paper, and certain metals. When using a laser cutting machine, it is important to consider its specific capabilities for the cutting process and its compatibility with different materials.
Conclusion
In conclusion, understanding and controlling the thermal output of a laser cutter is crucial for achieving optimal cutting results, ensuring safety, and prolonging the lifespan of the equipment. By applying this knowledge effectively, you can harness the full potential of your laser cutting machine while ensuring safe operation and achieving high-quality results in various applications.
Baison Provides the best Laser cutter
Baison provides the best-performing laser products for all types of manufacturers. Our products are designed to maximize thermal efficiency and use gas as the primary material. We not only have the most cutting-edge laser cutting equipment on the market but also provide laser welding machines, laser marking machines and so on. Contact us now for the latest samples!