Nowadays, finding a cleaner, more effective, and eco-friendly cleaning approach seems challenging. With the current global warming problem, we should highly consider the safety of our cleaning method.
What cleaning process is reliable, high-precision, safe for the environment, effective, chemical-free, and suitable for all applications?
Consider the post below about the difference between thermal and fiber laser cleaning to see which is an ideal choice.
What is Thermal Cleaning?
Thermal cleaning is a process that uses heat to remove contaminants from surfaces. The heat causes the contaminants to expand and break away from the surface, where they can be collected and removed.
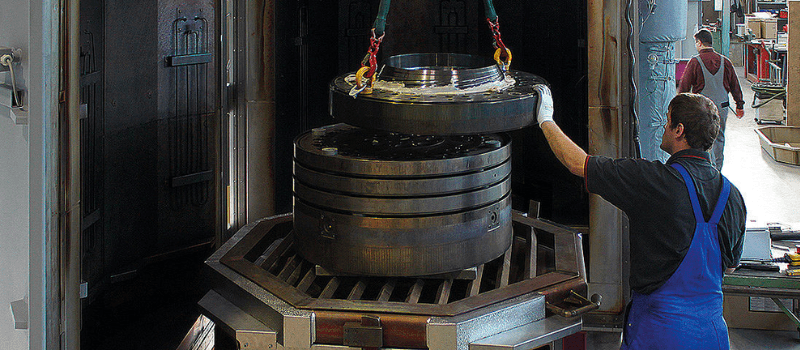
Thermal cleaning can be used on a variety of surfaces, including metals, glass, and ceramic. It is often used in manufacturing and industrial applications to clean equipment and remove unwanted build-up. Thermal cleaning is an effective way to clean surfaces without damaging them or causing harm to the environment.
The Difference between Thermal Cleaning and Fiber Laser Cleaning
We perform thermal cleaning when we remove contaminants, like rubber, plastics, resin, glue, paint, silicone, adhesive, grease, plant-based products, oil, and polymers.
It commonly takes approximately half an hour to one hour to eliminate all materials from the tooling when performing thermal cleaning.
Quick and effective cleaning phases significantly minimize downtime during line change-outs and maintenance.
Generally, different industries perform this cleaning process with excessive heat, depending on the application.
Thermal cleaning is considered the most typical cleaning approach performed by most industries. As a result, they develop diverse techniques for broader applications.
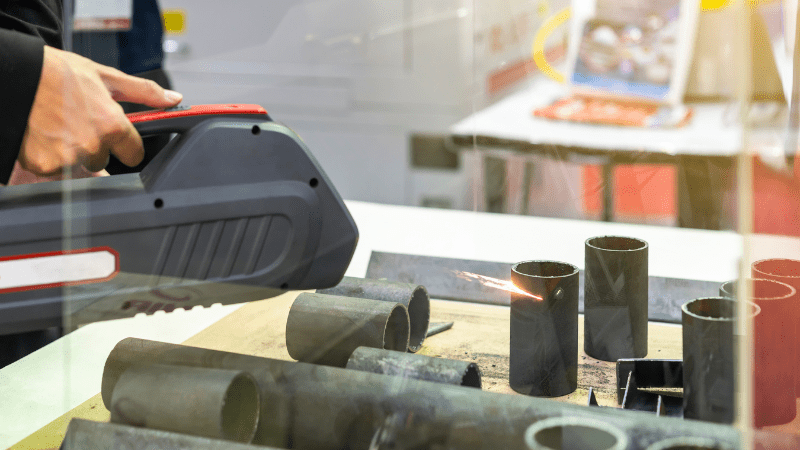
On the other hand, fiber lasers work quickly, cleaning an extensive array of materials, such as metals.
This process is different from thermal cleaning in using lower temperatures to prevent distortion and cracking of materials.
In addition, if you prefer a more energy-efficient and cost-effective approach, laser cleaning is a better option. You won’t have problems with the parts as they’re always available.
An eco-friendly laser cleaning machine works like a charm in removing impurities, residues, and contaminants with the laser irradiation process.
The fiber laser cleaning method is reliable in safely and effectively cleaning surfaces with little or no effort.
Areas of Application
Thermal Cleaning
- Thermal cleaning of filter disks and candle filters
Thorough and repetitious cleaning of disc filters, candles, and complete filter bundles plays a vital role in film and fiber production.
Thermal cleaning helps eliminate inorganic residues with a select after-treatment approach (ultrasound and high water pressure).
- Industrial laboratories
Industrial labs use thermal cleaning to efficiently clean glassware and ceramics.
- Plastic Industries
Corporations perform thermal cleaning to tidy production components such as static mixers, spinnerets, and extruder screws of plastic residue polymers.
- General industrial applications
Using the thermal cleaning method, you can effectively remove coatings, varnishes, and paint from industrial components.
- Coating removal and paint stripping
Thermal cleaning helps ensure fast and thorough removal of undesired coatings. This approach can provide you with a mainly designed technique control and a thermal off-gas cleaning, which means the process is adjusted per requirements.
- Rewinding businesses
Rewinding businesses use thermal cleaning to clean motor parts of greases, oils, and resins.
- Injection molding
Static mixers, screw tips, hot-runner systems, and injection nozzles call for incredibly dependable polymer removal.
Regular thermal cleaning of these valuable production tools is critical for the injection molder since it guarantees longevity.
- Remanufacturers
These corporations use thermal or chemical cleaning to eliminate greases and oils from used components, including starter housings or engine blocks.
Fiber Laser Cleaning
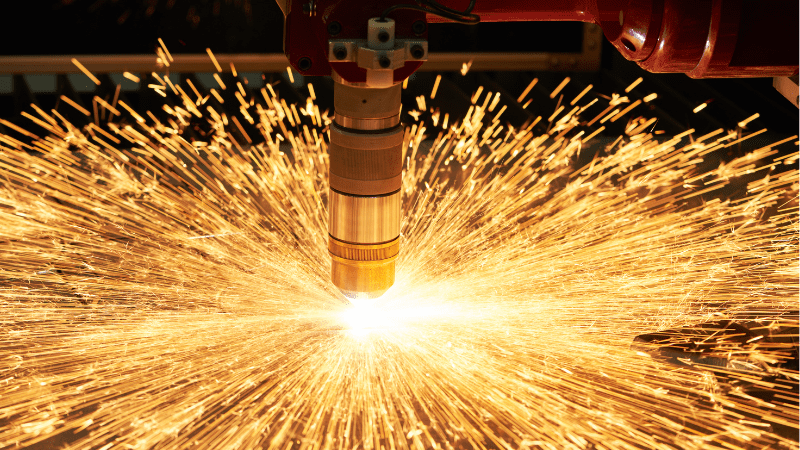
- Surface preparation and profiling
Since laser cleaning methods utilize a non-abrasive and non-contact process, laser cleaners work better in laser rust or scale removal and surface profiling.
Laser cleaning is famous for being an economical and environment-friendly approach to laser rust removal and preparing the surface of fabricated steel components and rolled steel products for protective coating.
- Laser rust removal in steel fabrication and surface profiling
You can effectively remove scale and rust from metallic components. Pulsed fiber lasers eliminate unwanted items or material surface deposits to avert rust formation.
The descaling method is necessary to ensure sleek surfaces for pre-finishing and finishing.
- Adhesive bonding preparation for metal components
The laser cleaning process is perfect for adhesive bonding preparation because the pulsed fiber laser eliminates oxides and other impurities like oxides and grease that minimize the vitality of adhesive bonds.
- Anode assembly cleaning
You can use laser machines in specific conditions, including cleaning cathode bars and removing debris from carbon butts, dirt, and impurities from stub rods and thimbles.
Laser cleaning machines make anode assemblies suitable for reuse since they help completely clean them by removing all surface impurities.
- De-oiling and degreasing
Laser cleaners do wonders in removing thermal stains from finished weld joints and debris like oxide materials and residual flux.
A laser cleaning machine is ideal for stainless or carbon steel components since the laser beam omits grain boundaries, enhancing corrosion resistance.
- Pre-treatment for brazing and welding
It’s essential to prepare the surfaces of steel and aluminum materials before brazing and welding to ensure thorough surface cleaning results.
Laser cleaners remove lubricants, ferrous and non-ferrous alloys, and other impurities from aluminum and metal surfaces.
- Selective paint removal
Aerospace and automobile corporations sometimes require removing the top layer of paint while maintaining the primer. You execute this process before applying the new paint finish.
Laser cleaning technology helps save materials and more time while enhancing the quality of finished surfaces.
- Partial de-coating
Laser cleaning machines are ideal when crucial weld seams on painted components require de-coating for inspection.
Fiber lasers make it easier to remove the coating without using chemicals, abrasives, or power tools.
The Upsides and Downsides of Thermal Cleaning and Fiber Laser Cleaning
Thermal Cleaning
Upsides
- Simple cleaning process
One of the many advantages of thermal cleaning is that the heat quickly reaches every spot in the harmful component.
Due to this, the conversion into dust happens everywhere in the components you need to clean.
This cleaning technology allows you to thoroughly clean the inner portion of the tubes, the surrounding areas, and the in-between pipes and shells.
Thermal or chemical cleaning helps eliminate the contaminants so that you can separate both components.
- Ideal for heat exchangers
The thermal effect guarantees an excellent cleaning solution. Heat can easily reach every area, making thermal cleaning ideal for heat exchangers.
This cleaning technology makes it more likely to disintegrate the contaminant in difficult-to-reach areas, allowing effortless removal of dust and impurities.
Downside
Thermal or chemical cleaning with molten salt takes roughly fifteen to thirty minutes. Nonetheless, this method has the hazard of toxic splatter due to chemical reactivity and possible risks of hazardous hydrogen cyanide gas or explosions.
Similarly, molten salt baths can be hazardous to our environment, and the components can be deformed or modified in design tolerances.
Unfortunately, molten salt baths are barely used nowadays because of the risks involved.
Fiber Laser Cleaning
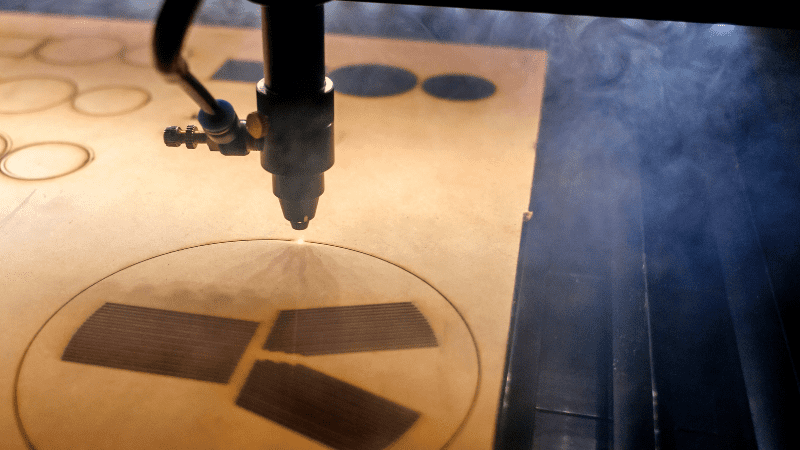
Upsides
- Controllable and non-damaging cleaning technique
Does laser cleaning work? Yes, fiber laser cleaning offers excellent control over its counterparts.
The laser beam can be targeted as preferred, while gentle and repetitious power settings distribute merely the amount of energy needed.
Pulsed fiber lasers generate maximum cleaning results with minimal heat production.
Laser cleaning offers more advantages than traditional methods since it ensures a completely automatic operation.
Likewise, laser cleaning machines adhere to the processing concept of environmental safety and protection.
- Complete removal of chemical solvents
One of the significant advantages of laser cleaning technologies is that they make managing and the disposal of toxic chemical solvents no sweat, saving time.
With lasers, you don’t need to deal with the decline in costs of utilizable solvents, costly requirements for post-process treatment, and the removal of these chemicals. As such, laser cleaning systems are an economical and eco-friendly solution.
- Reduction in waste materials
Since laser cleaning is a non-contact approach that eliminates only unwanted materials, it can ensure a lower cost.
Fiber lasers don’t involve secondary components and abrasive materials; therefore, they generate lower quantities and fewer waste materials than other methods.
Downside
- Unsuitability for all types of projects or applications
There’s no doubt about how effective laser technology is in removing impurities and dirt from metals and non-metals; however, you cannot use lasers for all applications.
Unlike other methods, laser cleaning technology works ideally only for small and targeted areas, which means it takes longer to clean large surface areas.
Due to this, you can’t expect satisfying surface cleaning results with fiber lasers. In particular, laser cleaning systems are not ideal for heavy equipment maintenance, the underside of a vehicle, and car restoration.
A pulsed fiber laser makes it challenging to clean crevices in the manufacturing process, like the inner sections of pipes.
If it’s hard for you to see the specific areas, the laser pulse can’t clean that spot efficiently.
Final Thoughts
Did you find this post about thermal cleaning vs. fiber laser cleaning informative? As discussed, many industries perform thermal cleaning to thoroughly remove organic impurities like plastics and polymers, using extreme heat.
While you can use high-pressure water to clean heat exchangers, thermal cleaning provides a better and highly effective technique.
Meanwhile, a laser cleaning system does the job faster and can effectively eliminate a more extensive range of components in a more gentle approach. Laser power is a more cost-effective solution than other conventional methods.
More than that, a pulsed fiber laser doesn’t use extreme temperatures and inhibits the potentiality of distortion and cracking of tools and equipment.
If you still don’t know how to choose the right machine, press the button below to contact us. Baison is a world-famous laser equipment manufacturer and solution provider. We can help you find the best cleaning technology for your business—and get you up and running as quickly as possible.