Robotic welding machines have revolutionized the whole welding machinery industry in general. It is a welcomed technological advancement with potential and possibilities whose impact is easily felt in all industries. The robotic welding machine harmonizes precision, accuracy, safety, efficiency, and high productivity.
It takes welding processes to the next level with ease. Just like any other innovation, there are benefits and drawbacks. In this analysis, we explore the good and bad sides of robotic welding machines taking into account every detail.
What Is Robotic Welding?
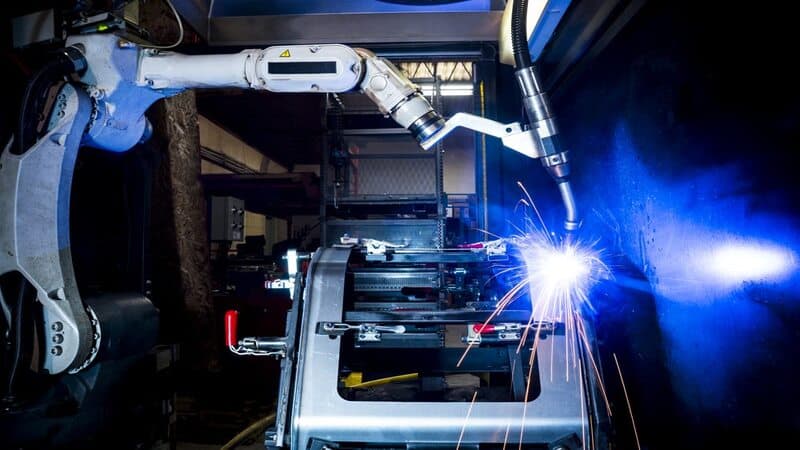
Robotic welding is associated with fully activating robots or automated machines to carry out welding processes. It synchronizes robots and welding procedures to achieve seamless welding results. They are often used in the aerospace, construction, and manufacturing industries. The robot tasked with welding is the primary factor in robotic welding.
A robot used in welding operations is programmed, configured, and set to carry out these operations according to the specified guidelines. A welding gun, torch, or lead is attached to the robot and is used to combine metals like the manual hand welding machine.
The sequence needed before a robot can carry out welding procedures includes inputting the required welding program into the Control system of the robots. The next step is to set the robot up, fix the desired welding operations and allow a trained robotic operator to monitor and control the outcome.
What Are the Types of Welding Robots?
A broad range of welding applications with corresponding welding robots suited for each specific purpose. Here are some of the top-ranking welding robots.
Articulated Robots
Articulated robots are the most popular and easily accessible kind of welding robot. The primary job description of the robot is to handle complicated welding, extensive and other various welding processes, and tasks. The selling point is its flexibility and human arm-like motion range suited for different welding processes.
Cartesian Robots
These robots are also referred to as Gantry robots. They take the form of a rectangle with a 3 axis framework. The 3-axis is the popular X, Y, and Z axes. The strong point of the robot is that it is best suited for spaces with clear linear points.
Dual-Arm Robots
These robots have two robotically controlled arms. These arms can either function differently or together. However, it gets the welding task done. The strength of these robots rests on their ability to handle multiple welding tasks at the same time. They can also perform complicated welding procedures, unlike the other welding robots.
Delta Robots
These robots are used to handle complex welding tasks with short time frames. They are popularly referred to as the spider or parallel robots. The strength of these robots is the solid base, speed, accurate and precise welding and techniques, and ability to handle small welding needs easily.
SCARA Robots
The full meaning of SCARA is Selective Compliance Assembly Robot Arm. It simply refers to the merging of two rotating X and Y frameworks. The Z axis is made to be strong and fixated. The strong point of the robot is in contained spaces and for arc, spot welding, or bent welding procedures.
Collaborative Robots (Cobots)
According to its name, these robots were created for collaborative purposes only. They are programmed and configured to work alongside humans on the same tasks. Their functionality is dependent on their human collaborator. Hence, they are designed with a few human-like features, such as vision and sensitive sensory systems. They are primarily used for medium-scale production needs.
What Are the Applicable Materials of Welding Robots?
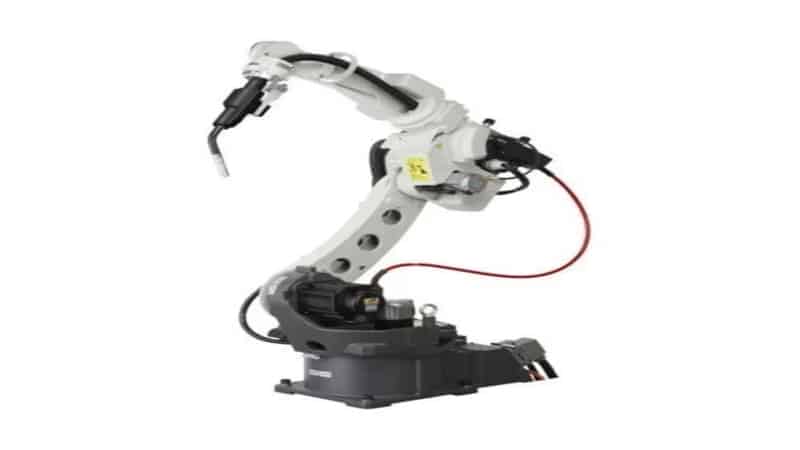
Stainless Steel
It is quite popular in the robotic welding industry. The steel is highly durable, reliable, and able to withstand corrosion. It is also aesthetic when used. Robots can use stainless steel for any welding process.
Carbon Steel
Carbon steel is another robotic welding machine-friendly material. Some of its strong points are that it is cost-effective and strong. It is also useful in ship construction.
Alloy Steel
This steel is known for its top mechanical framework. The strong points include its hardness and minimal wear and tear nature. It can be welded into accurate structures.
Silicon Steel
The silicon steel is primarily used for electrical purposes. Hence, the name electrical steel. It is often used to produce generators, vehicles, electric conductors, etc.
Spring Steel
Spring steel top the charts When it involves super strength and elasticity. They can be bent or twisted into varying positions with ease. Welding robots can carry out a wide range of operations on the spring steel.
Aluminum Alloy
It is a lightweight material. However, they have proven beneficial in welding purposes making certain applications. They can also be easily welded during procedures.
Galvanized Sheet
It is a zinc-layered sheet. It is easily corrosive. Welding robots can easily work on galvanized sheets for specific applications like metal compartments or panels.
Pros of Robotic Welding Systems
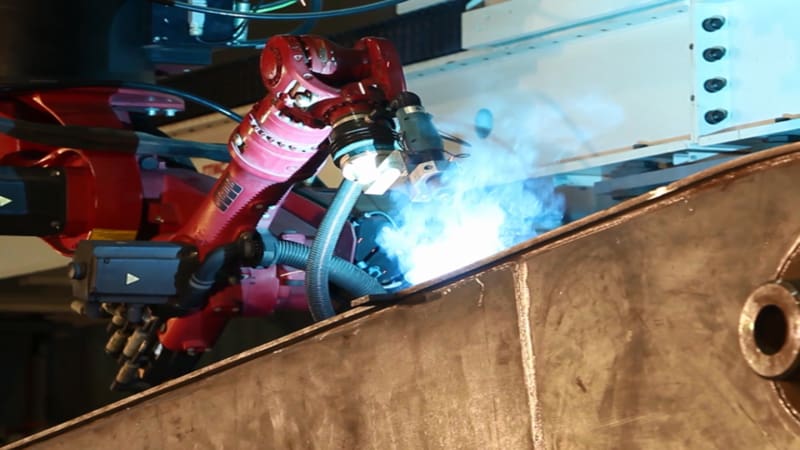
Enhanced Productivity
Robotic welding systems increase the productivity level of any welding operation. When compared with the manual welding process, there is an increase in the production outcome by 50%. It is because robots can get multiple tasks done within a limited timeframe. Unlike humans, they don’t suffer from frequent fatigue.
Enhanced Weld Quality
The weld quality of a robotic welder is far better than a human welder’s weld integrity. The welds are accurately and perfectly done, leaving no room for defects and fewer mistakes or errors. The perfection is because the required and desired calculation is programmed on the robot before execution.
Improved Safety
Robotic welding comes with minimal risks and safety hazards. Welding workspaces are associated with toxic fumes, heat, and other harmful wastes. Unlike human welders and human operators, who can be easily affected, welding robots are shielded by their safety barriers.
Cost-effective
Robotic welding quires huge initial investment and patience costs. However, they minimize production costs and the overall human labor costs.
Flexibility, Reliability, and Versatility:
Welding robots are known to be highly reliable. They can also be used for various welding operations and in different forms and positions during welding arcs. It also allows for easy transfer between applications during welding operations.
Cons of Robotic Welding Systems
Complex Programming and Configuration
Configuring a welding robot is an extreme sport. Caution must be exercised during programming to get the robot welding the right setup. The initial and subsequent programming is time-consuming and challenging, especially when specific welding operations are required.
Lack of Flexibility Robotic Welding Machines
Robotic welding systems can be difficult to alter during a welding procedure. In cases where a quick change is required, a robotic welder cannot make such necessary changes. To make any adjustments, the configuration programs must be altered.
Complicated Product Designs
Due to the nature of robotic welders, they cannot work on complicated product designs. They are restricted to simple and regular-shaped designs. Unlike manual welding, which can be used for complex and irregular designs, robots require special configurations to work on them.
Variations
Any variation to the programmed specifications equals a defective product. Even the slightest disparities can easily affect robot welders during a welding procedure. They are not readily adaptable, unlike manual welders.
High Maintenance, Repair, and Purchasing Cost
It is a major disadvantage. The initial cost of procuring, programming, and maintaining a robotic welding machine is extremely high. It is costly to repair or change any part of a welding robot. The cost of training operators to handle these machines is also on the high side.
Who Should Choose Robotic Welding Instead of Manual Welding?
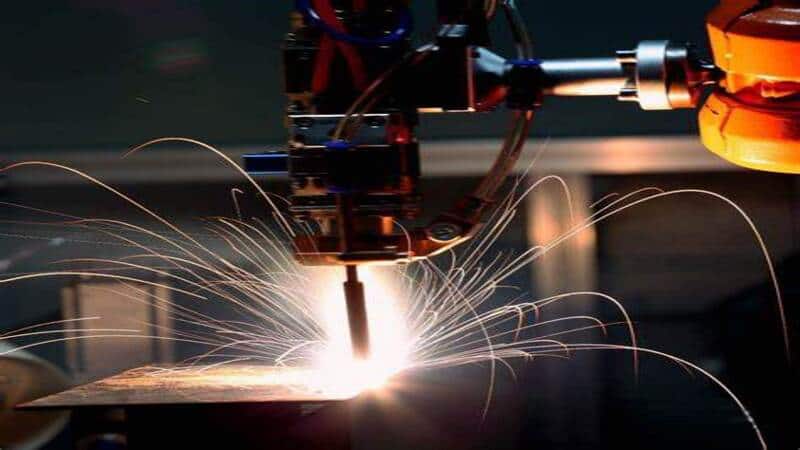
Large-Scale Manufacturing Companies
Companies that manufacture products on a large scale are expected to use robotic and welding techniques instead of manual welding. It will increase their production level and output and reduce labor and production costs. Also, they can rest assured that there will be minimal product defects or errors.
Companies With Duplicative Welding Tasks
Companies that carry out complex and duplicative welding tasks need the services of automated welding machines. Robots with automated processes can perform welding procedures repeatedly without fatigue or distraction. They can save money and also handle welding complexities with ease and speed.
Companies, Workshops With Dangerous Environments.
Robots are the best options in workspaces considered harmful, risky, and hazardous to humans. They are shielded with safety barriers making it easy for them to work in places with high temperatures or toxic atmospheres.
Conclusion
The pros and cons of robotic welding machines should be properly analyzed and evaluated. You should also weigh them according to your desired requirements or outcome. You can determine if the cons, such as costs, flexibility, and configuration issues, can be coped with.
Regardless of the cons, the numerous and attractive pros make the robotic welding system worth considering.
Discover the Perfect Solution for Your Business with Baison
Baison offers an outstanding solution for businesses seeking productive and detailed automated welding machinery and processes. Baison’s laser welding machines are designed to optimize the welding procedure. Their products are designed with user-friendly interfaces and innovative features.
Baison’s laser welding machines provide your business with versatile, flexible, quality welding solutions. You can request a quote to enjoy our wonderful products via sample proofing.