Welding robots have revolutionized different industries with their speed and performance. Welding has been hectic as you are melting the material and joining it with another metal piece. It requires lots of physical effort, pressure, and skill. Welding robots are helpful as they are made to handle different types of weldings, and their arms can even hold the material.
In this article, we will discuss what a welding robot is. We will discuss robot welding processes, how they are helpful, some applications, and how they work. Before we go deeper, let’s understand what a welding robot is:
What Is a Welding Robot?
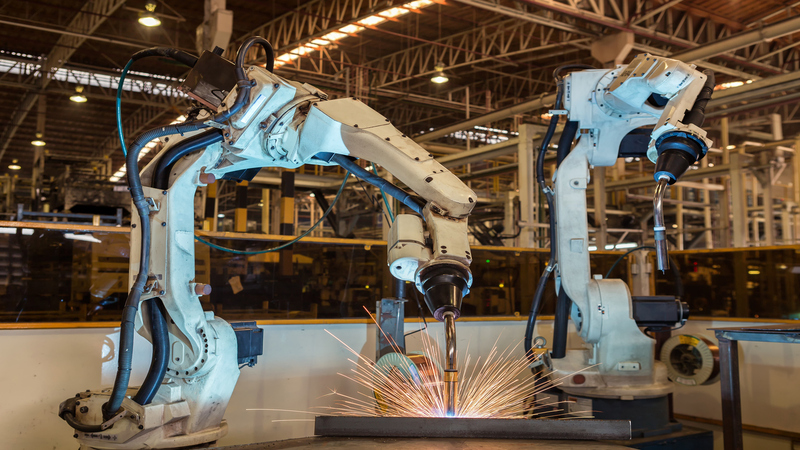
A welding robot is an industrial robot designed and programmed to perform welding. Welding is a process of joining two or more metal pieces together. The robot has arms with articulated joints that can move in different directions for welding. They are also equipped with a welding system to perform welding.
These robots are used in manufacturing industries like aerospace, automotive, or electronic industries for repetitive and precise welding. Welding robots have many benefits; they are programmed, reduce the need for manual intervention, have high speed, and can work day and night without fatigue.
Overall, This boosts the production process, which is why welding robots are used in high volume.
The History of Welding Robots
The history of robot welding is traced back to the mid-20th century when in 1960 first, welding robots were used. George Devol and Joseph Engelberger developed the first welding robot Unimation 001. The robot was implemented in the General Motor factory for spot welding.
But it was not until 1980 that robot welding started gaining popularity. Other automotive industries saw the profit and began implementing spot welding.
In this period, significant improvements were made to welding robots leading to developed and sophisticated welding robots. Soon they expanded to industries other than the automotive; sensors and a vision system were added to the robots, making them more precise and valuable.
Welding robots were useful on an industrial scale but were still too expensive. With time, technological advancement controls the price. As the prices come down, other industries are using welding robots.
Nowadays, welding robots are sophisticated tools with lots of utility on an industrial scale. Nowadays, collaborative robots and artificial intelligence are further expanding the capabilities and application of robot welding systems.
Click the button below to get a professional welding robot!
What Are the Types of Welding Robots?
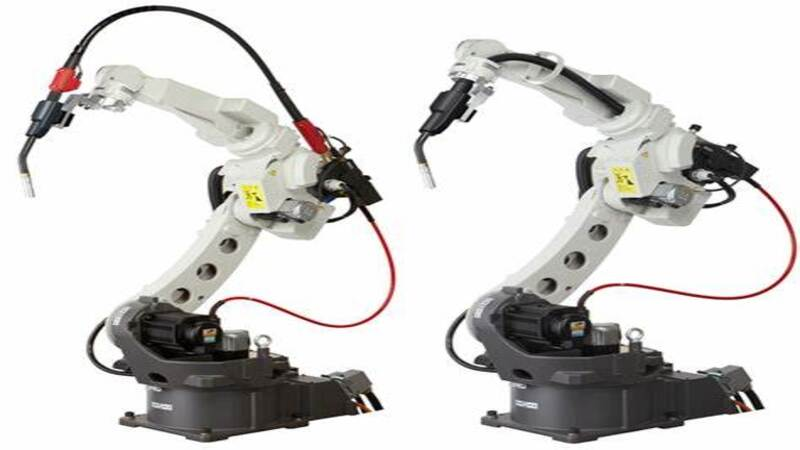
Welding robots have different types. Each type of welding technique has different kinds of robots. Let’s discuss some of the main types of welding robots: Each type is tailored for specific applications.
Cartesian Robots
These robots have a three-axis linear motion system. Their structure resembles a box, and they have a rectangular coordinate system. These robots are used for heavy and extra large workpieces requiring extended reach.
Articulated Robots
These are the most common welding robots with interconnected joints or arms. These arms give flexibility to robots for a range of motions. These robots can handle different welding techniques, including laser welding.
SCARA Robots
SCARA(Selective Compliance Assembly Robot Arm) has a rigid vertical and horizontal arm. They are fast and repetitive and are used in high-volume production where repetitive actions are required.
Collaborative Robots
These are designed to work with humans. They have advanced force sensors or collision detection so that they can stop when they sense human presence. These robots are required where human inspection or supervision is essential.
Delta Robots
They have three arms and are used in applications where high speed and accuracy are required, like spot welding or welding small components.
Mobile Robots
These robots have a mobile base, and they can move around. They are used in applications where workpieces are large and need to be reached from different angles. These robots can be specialized in MIG, TIG, or ARC welding.
How Do Laser Welding Robots Work?
A laser welding robot uses laser power to join the material. A welding robot comes fully programmed with instructions for a specific type of welding.
Before the welding process starts, the workpiece is prepared, which includes appropriately cleaning pieces and positioning them to a right angle with the help of fixtures or clamps.
A laser-generating source generates the laser beam. The beam is focused and directed on the workpiece through a beam delivery system that includes a series of lenses and mirrors.
Welding robots are programmed with a welding path that includes the trajectory and pattern of the laser beam. The robot positions the arms and moves them according to the programmed instructions. It focuses the laser head onto the workpiece. High energy laser beam melts the material and forms a weld pool.
The robot controls the movements of the laser beam and its speed. Sensors or a vision system can be integrated to supervise the welding quality, seam tracking, and other parameters during welding. The system provides real-time data to the robot to ensure welding quality.
What Materials Are Suitable for Laser Robotic Welding Technology?
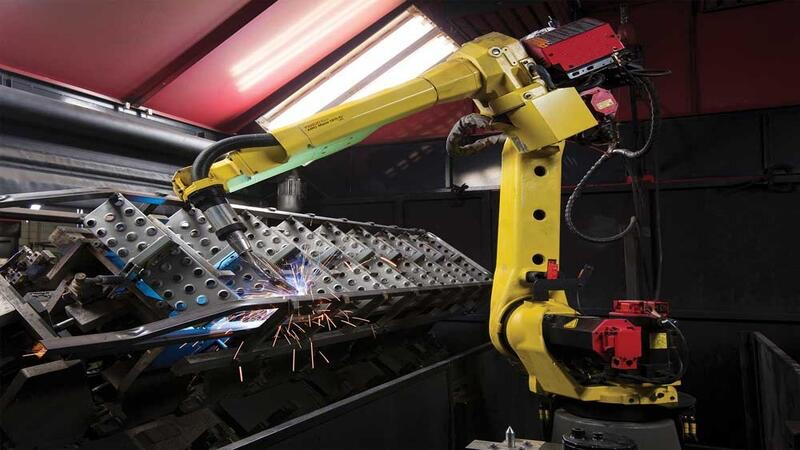
Laser robotic welders are versatile and can work on any material that manual welding can, including metals and non-metals. Here are a few materials that industrial robots work on:
Steel
It includes stainless steel, carbon steel, spring steel, alloy steel, silicon steel, and others. Steel is a hard material to weld. Not only are some types hard to weld, but some can be too thin and technical to weld, such as silicon steel or spring steel. These metals have different properties and may require different welding parameters. They can be hard, dense, thin, or too malleable.
Aluminum and alloys
Aluminum is a difficult-to-weld material. It may not be hard, but it is reflective and has high heat conductivity. That is why it requires precision and accuracy to save the material from burns, distortion, or cracks.
Copper and Alloys
Copper and its alloys are also reflective and challenging to weld.
Non-Metals
Metals and non-metals or composites are also extensively used in different industries. It includes polymers and composites.
Galvanized Sheets
Galvanized sheets can be challenging to weld due to the rich zinc coating. Zinc can vaporize and may produce fumes during welding. Welding robots can weld galvanized sheets safely and with precision.
Benefits of Using Welding Robots
Let’s take a look at some benefits of using welding robots on an industrial scale:
Increase Productivity
Robot welders can work non-stop without undermining the quality of products. They can boost the productivity of manufacturers. They work tirelessly without requiring any breaks or manual supervision. This can drastically increase productivity, so they suit the high-volume production business more.
Consistent Performance
Robots provide consistent performance. They are built on an advanced system and follow programmed instructions, resulting in precise welding results every time. They can maintain the welding speed and performance, improving welding accuracy.
The scope of rework or defects is almost zero with robot welding.
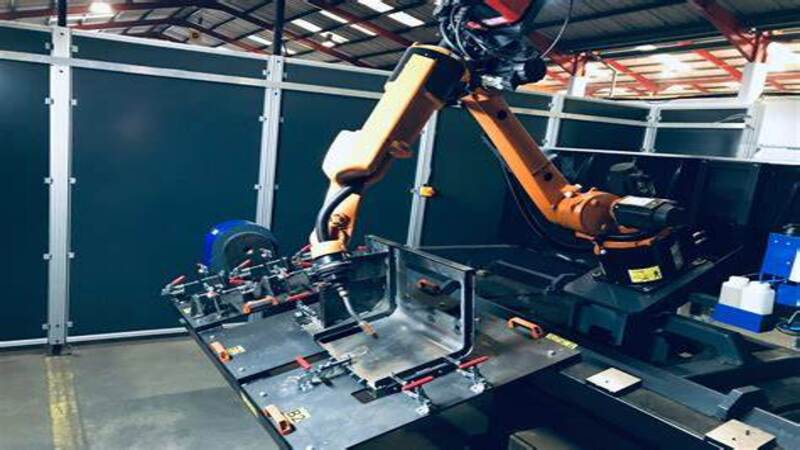
Improve Welding Quality
Welding is a technique that relies on more than just the machines. Workers’ skills, knowledge, and expertise play a great role in the accuracy and weld quality. Welding robots are programmed to work precisely.
The laser technology works precisely, and the weld quality is also strong. Robots have precise control over the parameters and laser beam movement, weld pool, and fusion. So we can expect a better and stronger weld seam.
Cost Saving
Cost is one of the defining factors when choosing a welding system like robot welding. If they do not return investment with profit, they don’t suit the business. One of the best parts of robot welding is that it saves a lot of costs.
First, automated welding saves labor costs as it does not need human welders like other welding techniques. , Secondly, it boosts production, which means you can fill more orders in less time.
Flexible and Versatile
Welding robots are flexible and versatile. They can be programmed to perform different welding positions. They can reach into difficult-to-weld positions and allow manufacturers to switch between different materials and products for welding.
Seamless Integration
Welding robots are designed for smart and efficient working. They can be integrated with your production line and help you manufacture products without hassle. They can be integrated with the loading and unloading system and material handling. Seamless integration saves labor costs and makes inspection easy.
It helps manufacturers to automate the entire production system and helps manufacturers to connect data, analyze it, and devise plans for better optimization, quality control, and predictive maintenance.
Applications of Welding Robots in Manufacturing
Although Welding robots can be used in any industry where welding is required, they are more suitable for high-production volume industries where precision, speed, and accuracy are required.
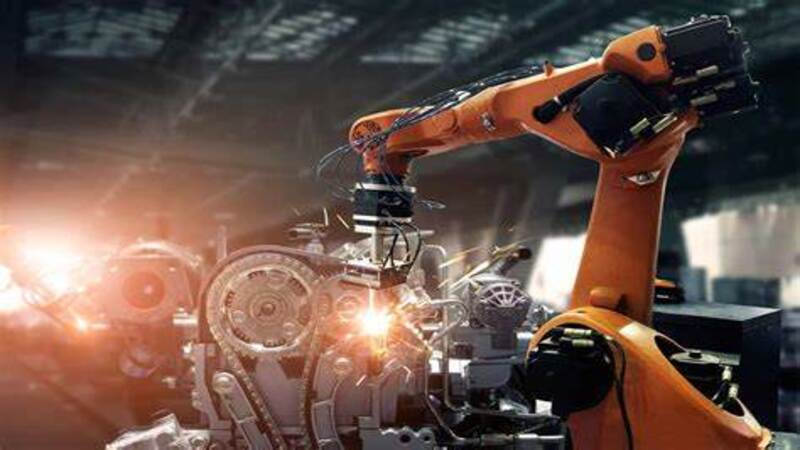
Automotive Industry
The first welding robot was used in the automotive industry, and their need is growing as the industry needs to weld large-size sheets for car bodies, frames, and several components. Laser welders are efficiently suitable for joint, spot, and other types of welding.
Aerospace Industry
Aerospace is another industry that requires welding large-size sheets and frames with precision and accuracy. They are used for manufacturing aircraft frames and bodies and components like wings, engine mounts, fuselage sections, and landing gears. Robots provide accurate and reliable welds that meet the safety requirements of the aerospace sector.
Heavy Machinery and Equipment
This sector needs building small and big components for heavy machinery. It includes building huge structures and also their smaller components. Laser welding machines are versatile enough to handle different materials, sizes, and shapes with consistent weld quality.
Furniture Industry
The furniture industry is wide. Modern furniture uses metal and other composite parts, making them more sustainable, strong, and innovative. The industry is wide enough to include doors, windows, furniture, cabinets, and almiras. Laser welders are fast and efficient enough to fit in the growing industry.
Shipbuilding Industry
The shipbuilding industry is booming with the growing need for international shipping. Robot welding can speed up building ship structures, frames, bodies, decks, and numerous other structural components.
These were only a few applications of robot welding that can be used in any industry that needs high production volume and deals with metal fabrication and metallurgy.
Advancements in Welding Robots
As technology advances, we expect more advancement in welding robots. They are becoming more efficient with more features added each day that takes a step ahead in excellence. Here are a few things we are expecting.
Collaborative Robots
We expect an increase in collaborative robots. They are becoming more efficient, so they can collaborate with human operators and work with them side by side, enhancing their capabilities.
Artificial Intelligence
Artificial intelligence will play an important part in making robot welders more efficient. These technologies will help robots to adapt to welding changes enabling them to change welding parameters to enhance weld quality. Artificial intelligence can also help in predictive maintenance, identifying potential issues, and optimizing robot performances.
Vision System and Sensors
New vision systems and sensors can enhance the robot’s capabilities and performance. Integrating high-resolution cameras, 3D scanning, and other sensors can help achieve further excellence in the welding industry.
Boost Your Production with Baison’s Laser Welding Robots
If you are looking for robotic welding systems, Baison offers all you need. We manufacture laser welding robots with laser power to weld thick and thin metals. These efficient robots seamlessly integrate within your production line and provide excellent welds.
The robotic welding machines are strong and require almost no postprocessing. Welding robots are fully automated and reduce human resource costs enabling industries to achieve high productivity and reduce overall manufacturing costs.
Don’t hesitate to contact us! We offer free application evaluation and sample proofing as well.