Shielding gas acts as a protective barrier between the weld pool and the surrounding environment, preventing oxidation and contamination during the fusion process. It creates an atmosphere that shields the molten metal from impurities, ensuring clean and strong welds.
But how exactly does shielding gas affect the quality of laser welds? What are its key roles in protecting the weld pool? And what factors should be considered when choosing the right shielding gas for different applications? In this ultimate guide, we will delve into all these questions and more, providing you with valuable insights to optimize your laser welding processes.
Laser Welding Gas
Laser welding gas refers to the gases used in conjunction with weldings like laser welding or gas metal arc welding to ensure clean and precise welds. The primary purpose of these gases is to shield the molten metal from oxygen and other reactive elements present in the surrounding environment.
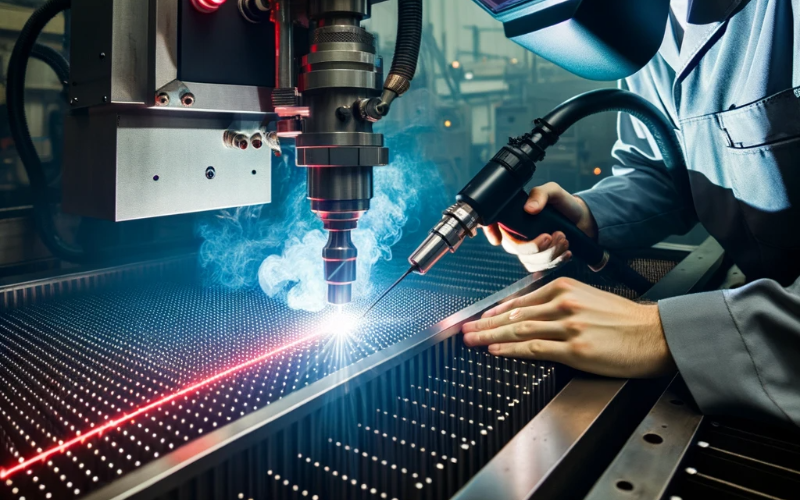
By displacing these contaminants, laser welding gases help maintain a stable arc and prevent porosity, spatter, or defects in the final weld. Several types of gases are commonly employed as shielding gases in laser welding processes:
- Auxiliary Gas (MDE): MDE gas (Methylaluminoxane/Diethylaluminum Chloride) is often used as an auxiliary gas for aluminum-based alloys. It helps improve weld penetration and reduces the risk of hot cracking.
- Shielding Gas: Argon is the most commonly used shielding gas in laser welding. Its inert nature and high thermal conductivity make it ideal for a wide range of applications, including austenitic stainless steels, carbon steels, and titanium.
- Jet Gas: Jet gas, such as nitrogen or helium, is sometimes used in combination with argon to enhance the stability of the laser beam and improve weld quality.
What is the Shielding Gas?
In laser welding, shielding gas is a critical component used to protect the weld area from atmospheric contamination. The high-intensity laser beam used in this type of welding generates a significant amount of heat, creating a molten pool of metal.
Without shielding gas, the hot metal would be highly reactive to the oxygen, nitrogen, and hydrogen in the air, leading to a variety of weld defects, such as porosity, oxidation, or a weakened weld joint.
The shielding gas, often an inert gas or semi-inert gas, forms a protective barrier around the weld area, displacing the surrounding air and effectively “shielding” the weld pool from the atmosphere until the molten metal has solidified. This prevents oxidation from occurring and ensures that the molten metal remains clean and free from impurities.
Effects of The Shielding Gas
The shielding gas plays a very important role in the welding process. Let’s take a look at its impact on the laser welding process.
Positive Effects
The choice of shielding gas in laser welding plays a crucial role in determining the quality and properties of the weld. Different types of shielding gases can have various positive effects on the welding process.
- Penetration depth and bead shape: The composition of the shielding gas can influence how deeply the laser beam penetrates into the material and how the molten metal forms during solidification. By selecting an appropriate shielding gas, welders can achieve optimal results with laser welding machines and laser welding equipment, ensuring the desired penetration depth and bead shape for sheet metal.
- Protect the weld pool from atmospheric contamination: When a laser beam interacts with the material, it generates high temperatures that can cause oxidation or other reactions with elements present in the air. Shielding gases act as a barrier, preventing these unwanted interactions and ensuring a clean environment for welding.
- Reducing spatter: The ionization energy of different gases also affects their effectiveness as shielding agents. Gases with low ionization energy are more likely to ionize and form plasma when exposed to high-energy laser beams. This plasma helps maintain a stable arc during welding, improving control over heat input and reducing spatter.
Negative Effects
While there are numerous advantages to using shielding gases in laser welding, it’s essential to consider potential negative effects as well.
- Improper use of the protective gas may cause deformation. Excessive reliance on shielding gases may lead to surface defects if not used correctly or if inadequate protection is provided during welding. Welders need to carefully balance factors such as gas flow rate, nozzle design, and distance between the nozzle tip and workpiece surface to ensure proper coverage without causing issues like porosity or lack of fusion.
- Choosing the wrong type of blow can have adverse effects. It’s worth noting that different materials may react differently to specific types of shielding gases. For example, certain gases may be more suitable for welding stainless steel, while others are better suited for welding aluminum alloys or carbon steel. Welders must consider the material being welded and select a shielding gas that complements its properties to achieve optimal results with laser welding equipment.
Types of Shielding Gas
In laser welding, different types of shielding gases are used to protect the weld pool and prevent oxidation. These gases can be classified into various categories based on their properties and composition. Let’s take a closer look at the different types of shielding gases commonly used in laser welding.
I. Argon
Argon is one of the most widely used shielding gases in laser welding. It offers excellent plasma suppression, preventing unwanted sparks and ensuring a stable welding arc. Argon provides effective protection against oxidation during the welding process. Its inert properties make it suitable for a wide range of materials, including stainless steel, aluminum, and titanium. For these reasons, Ar is commonly used as a conventional shielding gas.
II. Helium
Helium is another popular choice as a shielding gas in laser welding. It has superior heat transfer capabilities compared to argon, making it ideal for high-power laser applications. Helium also provides good plasma suppression and helps prevent oxidation during the welding process.
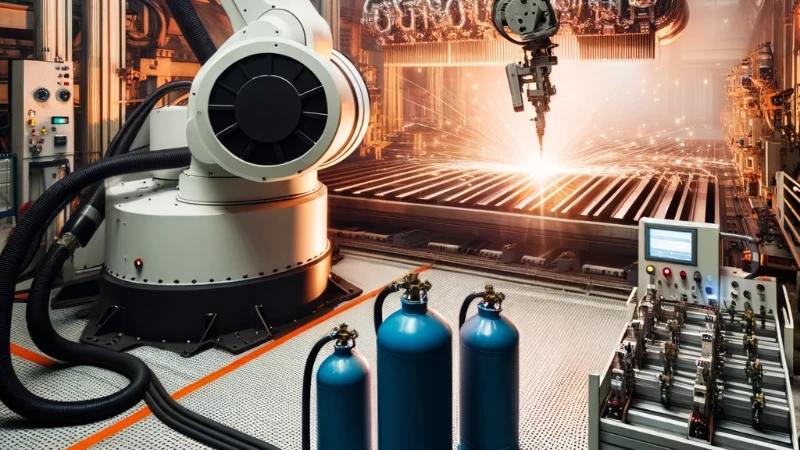
If you want to learn more about the role of Ar and He in welding, you can read this article on fiber lasers and aluminum alloys.
III. Nitrogen
Nitrogen is often used as an alternative to argon or helium in certain laser welding applications. While it may not offer the same level of plasma suppression as argon or helium, nitrogen is cost-effective and readily available. It can be used with both high-power and low-power lasers.
Here is an article about the effect of Ar and N2 shielding gases on the porosity of various metals in laser welding.
IV. Carbon Dioxide (CO2)
Carbon dioxide is commonly employed as a shielding gas in CO2 lasers but can also be used in other types of laser welding. Carbon dioxide improves weld speed, penetration, and mechanical properties.It offers good plasma suppression and helps prevent oxidation during the welding process. CO2 is often used for welding thicker materials due to its high heat transfer capabilities.
You may want to see specific examples. Here is an article about the effect of CO2 protective gas on laser welding of low-carbon steel.
V. Oxygen
While oxygen is generally not used as a primary shielding gas, it can be added in small amounts to enhance the laser welding process. Oxygen assists in achieving higher energy densities and faster cutting speeds. However, excessive oxygen levels can lead to increased oxidation and potential quality issues.
By understanding the characteristics of different shielding gases, you can make an informed decision about which one to use for your laser welding applications. Consider factors such as plasma suppression, prevention against oxidation, relative cost, advantages, and limitations when selecting the appropriate shielding gas.
Overview of the Common Shielding Gases in Laser Welding
In laser welding, choosing the right shielding gas is crucial for achieving optimal results. The following table can help you quickly understand some of the shielding gases commonly used in laser welding.
Shield Gas | Plasma suppression | Prevention against oxidation | Relative cost | Advantages | limitations |
Ar | Excellent(15.76eV) | Excellent (Inert) | Moderate | Prevents oxidation, excellent for titanium and reactive metals, provides stable arc and good weld pool visibility. | Lower thermal conductivity, can result in narrower weld profiles. |
He | Excellent(24.59eV) | Excellent (Inert) | High | Excellent heat transfer capabilities.Improved weld penetration | More expensive, requires higher flow rates, and is less accessible. |
N2 | Good(15.58eV) | Low (Can sometimes contribute to oxidation) | Low | Can be beneficial in certain stainless steel applications. | Not suitable for many metals, can cause porosity and brittleness in welds. |
CO2 | Poor (specific ionization energy not applicable for CO2 as a whole) | Low (Active gas) | Lowest | Improves penetration and stabilizes arc in certain processes. | Can lead to oxidation, more spatter, and rougher weld surfaces. |
O2 | Poor(12.07eV) | None (Contributes to oxidation) | Low | Can improve weld pool fluidity and surface appearance. | Increases oxidation, risk of porosity, and generally limited to carbon and low alloy steels. |
Methods for Delivering Shielding Gas in Laser Welding Processes
In the intricate process of laser welding, the method of delivering shielding gas is crucial to ensure the integrity and strength of the weld. There are primarily two methods employed in the application of shielding gas.
Side Blowing Method
This approach involves the lateral delivery of shielding gas into the welding zone. The gas is directed across the workpiece surface, creating a blanket that displaces atmospheric air, thereby preventing contamination of the weld pool.
The side blowing method is particularly advantageous in situations where the weld is performed in a straight line or large surface areas are involved, providing efficient coverage and protection. However, the effectiveness of shielding might be inconsistent due to the potential for gas dispersion, especially in environments with air movement or drafts.
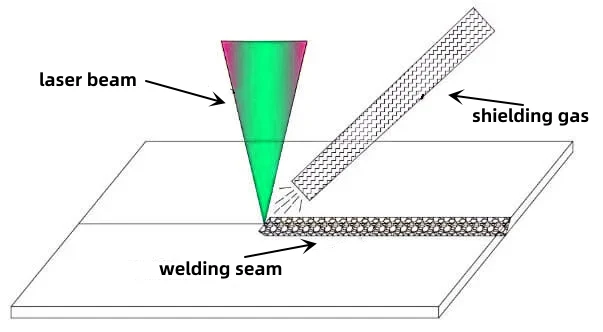
Coaxial Shielding Method
For applications requiring precision and consistency, the coaxial method is often preferred. Here, the shielding gas is supplied through the center of the laser welding head and is directed coaxially with the laser beam straight into the weld zone. This ensures a consistent gas flow and a stable atmosphere around the pinpointed welding area, essential for high-precision tasks.
Coaxial shielding is particularly effective in nullifying the effects of the surrounding air and is less susceptible to environmental interferences, making it suitable for intricate or smaller scale welds.
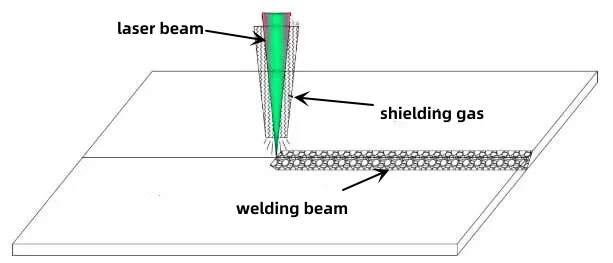
Both methods necessitate proper regulation of gas flow rates, ensuring the right amount of shielding gas is released to effectively protect the weld zone without excessive dispersion or waste.
The choice between side blowing and coaxial shielding will depend on specific project requirements, weld characteristics, and environmental conditions, all of which influence the overall quality of the welding process.
Selection of Specific Shield Gas Blowing Methods
Choosing the appropriate method for delivering shielding gas in laser welding processes is crucial to ensuring the overall quality and efficiency of the welds. This decision becomes particularly prominent when dealing with different types of welding seams, such as straight-line welding seams and planar closed graphical welds.
Straight Line Welding Seams
Straight-line welding seams are common in various applications and require a consistent gas flow to protect the weld area. The side blowing method is often utilized in these scenarios for several reasons:
- Efficiency: Side blowing protective gas covers the extensive length of straight welds effectively, displacing any contaminants in the process area.
- Accessibility: It is relatively easy to set up and doesn’t require highly sophisticated equipment or intricate adjustments during the welding process.

However, one must also be cautious of potential drawbacks, such as the susceptibility of the side blowing method to environmental interferences, like crosswinds, which can reduce its effectiveness.
Planar Closed Graphical Welds
When it comes to planar closed graphical welds, the complexity increases. These laser welding welds aren’t just linear, but may involve intricate shapes and turns. Here, the coaxial shielding gas method is frequently the preferred choice:
- Uniform Protection: Coaxial shielding delivers gas centrally over the weld pool, ensuring a consistent shield, critical for the complex shapes involved in planar closed graphical welds where even minor gas flow disruptions can lead to defects.
- Controlled Atmosphere: It offers a stable, controlled shielding environment, particularly important for materials sensitive to oxidation or other chemical changes during the welding process.
The choice between these methods depends heavily on the specific requirements of the welding project, the environmental conditions, and the materials involved. In some instances, combining both methods in a complementary manner may be beneficial.
Adjusting Shielding Gas Input and Heat Output
In laser welding, the adjustment of shielding gas input and heat output plays a crucial role in achieving optimal weld quality and efficiency. Let’s dive into the factors that influence the adjustment requirements for shield gas input during laser welding and explore techniques to optimize heat output through control over the shielded area.
1. Factors Influencing Adjustment for Shield Gas Input
The heat source used in the process. Laser beams with high power density require a higher flow rate of shielding gas to ensure proper protection of the molten metal from atmospheric contamination.
- Thermal conductivity: Different materials have varying thermal conductivities, which affect how efficiently they dissipate heat. For materials with low thermal conductivity, such as stainless steel or titanium, a higher flow rate of shielding gas may be necessary to compensate for their reduced ability to transfer heat away from the weld zone.
- Nozzle Type: The size of the nozzle affects the gas flow and coverage area, with larger nozzles allowing more extensive coverage but potentially less precision.
2. Optimize Heat Output Through Control Over Shielded Area
- Use of Air Curtains: Implementing an air curtain around the weld joint maintains an inert environment, keeping contaminants at bay while preserving the weld zone’s heat.
- Laser Power Adjustments: Modulating the laser’s output power helps manage heat input, crucial for heat-sensitive materials.
3. Balancing Heat and Shielding Adjustments
To achieve optimal weld characteristics while balancing heat input, it is crucial to make proper adjustments to the shielded area.
When aiming for deeper penetration, reducing the shielded area concentrates more energy into a smaller region, resulting in increased heat input. Conversely, increasing the shielded area spreads out the energy over a larger region, reducing heat input and promoting shallower penetration.
It’s important to note that finding the right balance may require some experimentation and fine-tuning based on specific welding requirements and material properties. Welding equipment often includes control systems that allow operators to adjust parameters such as gas flow rate and nozzle size easily.
Effects of Shielding Gas on Weld Morphology
The choice of shielding gas plays a crucial role in determining the appearance and structure of the weld. Different shield gases have varying effects on weld morphology. Understanding how shielding gas composition influences weld morphology is essential for achieving high-quality welds.
Influence on Weld Bead Width and Depth
The selection of shielding gas can significantly impact the width and depth of the weld bead.
Certain gases, tend to produce wider beads compared to others. This is because these gases have different thermal conductivities and ionization potentials, affecting heat transfer during welding.
- Argon or helium: These gases have higher thermal conductivities and create wider beads due to their ability to dissipate heat effectively.
- Nitrogen or carbon dioxide: These gases have lower thermal conductivities and result in narrower beads due to less efficient heat dissipation.
The depth of the weld bead is also influenced by the shielding gas composition. Gases with higher ionization potentials, such as argon or helium, tend to produce deeper penetration into the base metal. On the other hand, gases with lower ionization potentials like nitrogen or carbon dioxide may result in shallower penetration.
Overall Morphology Considerations
Shielding gas composition not only affects bead width and depth but also influences various aspects of overall weld morphology. Here are some key considerations:
- Bead Shape: Different shield gases can lead to variations in bead shape, ranging from concave (inwardly curved) to convex (outwardly curved). The choice of shielding gas depends on desired aesthetics and functional requirements.This is an article about the effect of shielding gas on the weld formation of double-wire DP-MIG high-speed welding.
- Spatter Formation: Shielding gases play a role in minimizing spatter formation during welding. Some gases are more effective at reducing spatter compared to others.
- Porosity: The presence of shielding gas helps prevent the formation of porosity, which are small voids or gas pockets within the weld. Proper selection of shielding gas can minimize porosity and improve weld quality.
- Oxidation: Shielding gases act as a barrier between the weld and atmospheric oxygen, preventing excessive oxidation that could weaken the weld joint.
- Weld Pool Stability: The composition of the shielding gas affects the stability of the molten weld pool, ensuring smooth and consistent bead formation.
Understanding these factors allows welders to make informed decisions about shielding gas selection based on specific welding requirements.
How to Choose Shielding Gas?
Choosing the most suitable shielding gas for laser welding involves understanding the material being welded and the desired outcome of the weld.
Identify the Material: Different materials react differently with various shielding gases. For instance, when welding carbon steel, a common material in industrial settings, argon is frequently used because of its inert properties that prevent any chemical reaction during the welding process.
Desired Weld Characteristics: If you’re aiming for a highly aesthetic weld on stainless steel with minimal oxidation, you might opt for a high-purity argon gas. Its inert nature ensures a clean weld, preventing contamination and discoloration.
You can click here to learn about welding shielding gases and their effect on the properties of stainless steel.
Compatibility with the Laser Welding Machine: Check your laser welding machine’s specifications. Suppose your machine is optimized for high-speed welding; helium might be recommended. Helium, with its higher thermal conductivity, supports faster welding speeds, particularly beneficial for thick materials.
By following these steps, you can make an informed decision that ensures the quality of your welds while maintaining cost efficiency and operational practicality.
FAQs
1 – Can I use any type of shielding gas for laser welding?
No, not all gases are suitable for laser welding. The choice of shielding gas depends on factors such as material type, desired weld characteristics, and process requirements. Commonly used gases include argon, helium, nitrogen, and mixtures thereof.
2 – Are there any safety precautions I should take when working with shielding gases?
Yes! When handling shielding gases for laser welding or any other application, it is essential to follow proper safety procedures. Ensure adequate ventilation in your workspace, use appropriate personal protective equipment (PPE), and store the gas cylinders in a secure and well-ventilated area.
3 – How can I optimize weld morphology using shielding gas?
Shielding gas plays a significant role in achieving optimal weld morphology. By selecting the right gas type, flow rate, and pressure, you can control factors such as porosity, spatter, and bead appearance. Experimentation and careful observation will help you find the ideal combination for your specific welding requirements.
Conclusion
In this guide, we’ve delved into the critical role of shielding gas in laser welding, highlighting the various types, their effects, and optimal delivery and adjustment techniques. Now, armed with this insight, it’s your turn to apply it. Test different gases, note their influences, and strive for the ideal shield gas and heat balance. Dive confidently into laser welding, and craft durable, high-quality welds.
Start Your Premium Welding Experience with Baison Laser!
Ready to elevate your laser welding projects with the perfect shielding gas solutions? Baison Laser is here to guide you through every step of your welding journey. With our industry-leading expertise and top-of-the-line technology, we ensure your welding needs are met with precision and quality. Contact us today to learn more about our products and services, and let’s create exceptional welding performance together!