In recent times, welding has become the essential process that reinforces many industries and critical areas of our lives. Interestingly, there has been rapid growth in the manufacturing industry with the search for increased output with minimal costs and labor.
Hence, manufacturers face the dilemma of choosing one of the two welding processes. In this blog post, we will explore the nitty gritty of the two welding worlds: robotic and manual welding.
We will dissect the advantages and disadvantages of robotic and manual welding processes. In the end, you will be equipped with enough information to pick the best option.
What Is Robotic Welding?
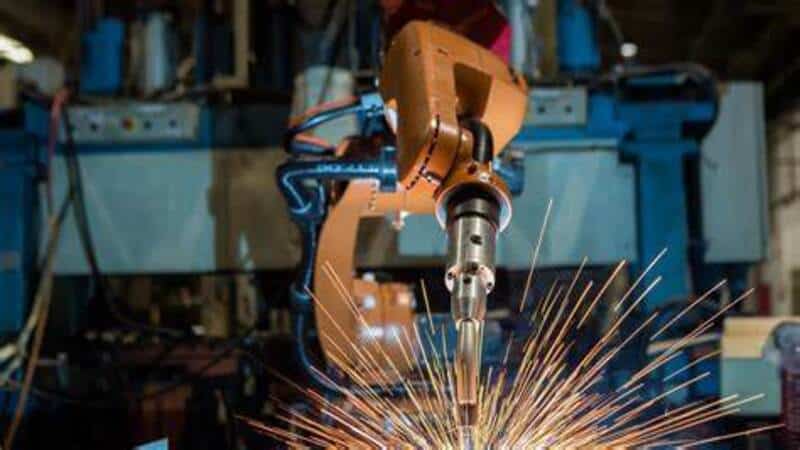
Robotic welding refers to the use of advanced types of automated robotic welding systems. The primary welding process is handled by machines controlled, directed, and supervised by human welders.
The robotic welding system deals with programming robot welders who carry out electronic weld process controllers and the required welding undertakings. These robots are given a set of guidelines necessary to carry out any welding operation.
These guidelines are specifically designed by some programming languages such as the robot, high-level, simulation, and offline programming languages.
Advantages of Robotic Welding
There are numerous advantages associated with using the robotic welding process. Here are some of the advantages:
Enhanced Precision
Robot welders are typically programmed to carry out all welding operations accurately. Hence, the production process is done without errors, with fewer defects, and within the same quality standards.
Enhanced Safety precautions
Welding is often associated with toxic wastes and extremely high temperatures. Human welders generally face all these issues. However, an automated welding or robotic process helps prevent workplace accidents, chemical exposures, bodily injuries, and other welding-related issues.
Enhanced Efficiency
It is another advantage associated with the use of welding robots. Their productivity rate and delivery are higher, quicker, and at lower labor costs. It allows for more work to be done within a limited time with fewer human workers and less waste. Hence, quicker completion rates.
Improved Flexibility
Robots can perform various welding operations with ease. They can easily handle various welding processes, changes in production requirements, and other welding tasks. The flexibility of welding robots helps reduce material waste and save costs by handling many tasks quickly and easily.
Disadvantages of Robotic Welding
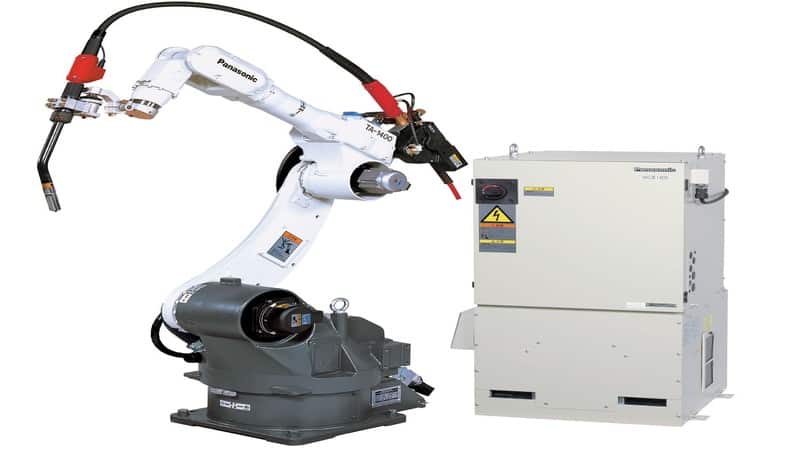
Highly Expensive
Getting robotic welders is known to be very expensive. The initial cost of getting the robots, programming them, and training the human operators is enormous. The initial investment and subsequent repair, labor, and maintenance costs have discouraged small business owners.
If you successfully purchase a robotic welder, you must also be prepared to replace damaged parts and reconfigure and program all the expensive software.
Limited Operation
Robots are limited in the welding operations they are wired to carry out. They need to be reconfigured or reprogrammed for specific high-skilled operations, which is expensive and time-wasting. The reconfiguration can also affect the operations previously embarked on by the robots.
Little or No Sense of Human Judgements
Robots, as welders, have little or no sense of human judgments regarding welding operations. Due to their programmed framework, they cannot detect or make corrections without interference.
Also, they cannot be used for specific operations requiring human production inputs. Hence, minimizing the range of product designs allocated to the robot-controlled welding robots.
Firm Reliance on Connectivity and Power
Robot welders depend heavily on connectivity and power, as they cannot function without them. From programming, updates, configuration, and even production, reliable power and internet connections are needed. Hence, it is a disadvantage because a robot or semi-automatic welding process’s operation can be halted due to power failure or poor internet services.
What Is Manual Welding?
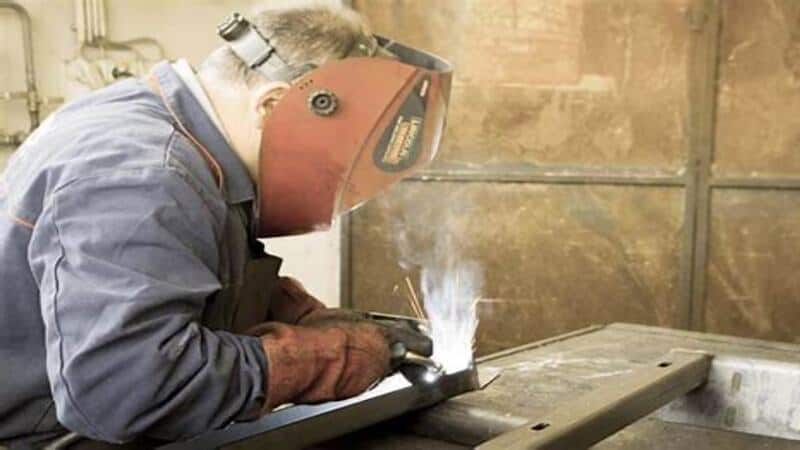
Manual welding is carried out with an electrode holder or hand-holding torch. The welding torch joins two or more metals to create a molten pool that solidifies to create a stronghold between the metals. Manual welding is primarily used for metal fabrication, molding, and repairs.
A human welder handles the manual welding risk and operation and can use various techniques depending on the product design and requirements. Manual welding is standard in the aerospace, construction, and manufacturing industries.
There are two types of welding machines; there are handheld and laser welding machines. The Handheld welding machine is manually portable for small-scale welding operations. They can be used in various locations and different positions by human operators.
The attractive details of the handheld welding machine are portability, versatility, and durability. In addition, handheld welding machines use minimal power; they can be easily maintained and used with minimal training.
On the other hand, the Laser welding machine uses laser beams. The laser beams create a kind of fierce heat used to melt the metal. It is left to cool down, causing a solid force capable of holding the metals together. Laser welding machines make precise and accurate welding; they can also be used on different kinds of metals while being automated.
You can also use them for a time-consuming welding job or special operations. Interestingly, laser welding machines provide little or no contact during welding, limiting the risk of contamination and damage.
Advantages of Manual Welding
Flexibility and Precision
it is highly adaptable, enhances precision control, lower production costs, and is flexible. It also allows skilled human welders to implement all their welding techniques. It can also be used for varying metals with different techniques and adjusted to suit any welding process.
Suitable for Specific Welding Requirements
Manual welding is highly beneficial when it involves complex products. It can be used to weld integrity in tight or uncomfortable spaces. Also, it is suitable for products with irregular shapes, which the automated process of welding cannot handle.
Easy Adjustment and Feedback Process
A human welder can easily detect errors and make amendments during welding. It is also easy to use manual welding to monitor the operation’s progress and make necessary corrections before the fabrication project or product is completed.
Cost-effective
Manual welding is very cost-effective. It does not require too much investment capital for automated machines. The primary requirement is highly skilled and trained welders. Getting skilled professionals and training them further does not cost much as getting a robotic welding system.
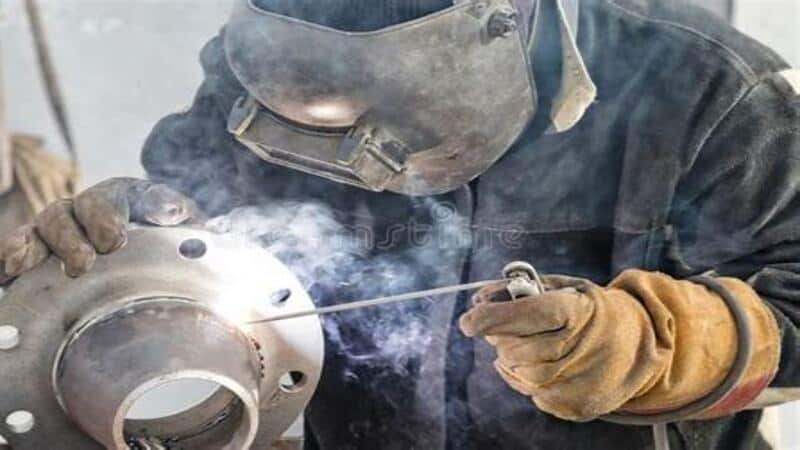
Disadvantages of Manual Welding
Human Error
Human errors can be avoided during Manual welding regardless of the skillfulness of the welder. These errors can affect product quality by creating defects. Human errors include incomplete and spot welding, weak fusion, undercutting, and little sputter. Fatigue, health issues, hand tremor, visibility issues, and lack of concentration can cause it.
High Skill Requirements
It also demands highly skilled professionals. The demand and dependence affect production. It can be challenging to get a skilled welder, and it takes years to train a new welder. Hence, it isn’t easy to expand.
Prone to Injuries
It also involves serious safety risks for qualified welders. Human welders face a lot of hazards during welding procedures. These hazards range from exposure to heat, fire, and toxic fluids to building hands and getting injured. It is known that a manual welding workspace is physically demanding and dangerous for human workers.
Unreliable Quality Products
There will always be cases of unreliable product quality after a manual process. It is regardless of the skill set of the human welder. A welding technique can go wrong, or the welder may experience fatigue or tremor, which can slow production and affects service and product delivery.
What Are the Differences Between Robotic Welding and Manual Welding?
Robotic welding | Manual welding | |
Automation | Fully on an automated welding system excited by robots | Handled by human welders who take charge of the welding system directly |
Consistency, accuracy, and precision | a high level of consistency, accuracy, and precision | minimal consistency, accuracy, and precision due to unavoidable human failings |
Speed and Productivity | High speed and productivity level | Low speed and productivity level due to human factors |
Cost | High initial investment and maintenance costs but low labor costs | Low equipment cost but high labor cost |
Safety | Highly safe for operators | Poses more risks and hazards to the operators |
Skills and training | Require more training for programming than welding techniques | Require more training and expertise in welding techniques than programming |
How to Choose a Suitable Welding Method?
There are numerous factors to determine the suitable welding methods for you. The common type or configuration you want to weld will determine the suitable welding method. The material type, thickness, and weld quality are other essential determinants. Before picking the best method, consider the required welding position and quality requirements.
Conclusion
It is imperative to consider the distinct advantages and disadvantages of both welding processes and weigh your options. Your desired production volume, requirements, cost considerations, weld quality, and material type should determine your choice.
Hence, with these factors in mind, you can confidently make the right-suited choice necessary to meet your project goals.
Discover the Perfect Solution for Your Business with Baison
Upgrade your welding capacity and enjoy new possibilities with Baison welding machines. Whether you’re an experienced professional or a small business owner, our cutting-edge technology will revolutionize your productivity and product quality.
Don’t hesitate to contact us today and receive an instant quote.