We’ll cover five practical tips that can help optimize material utilization, improve efficiency, and minimize waste. By the end of this article, you’ll have actionable ideas to streamline your cutting process and make it more sustainable.
What is Sheet Cutting?
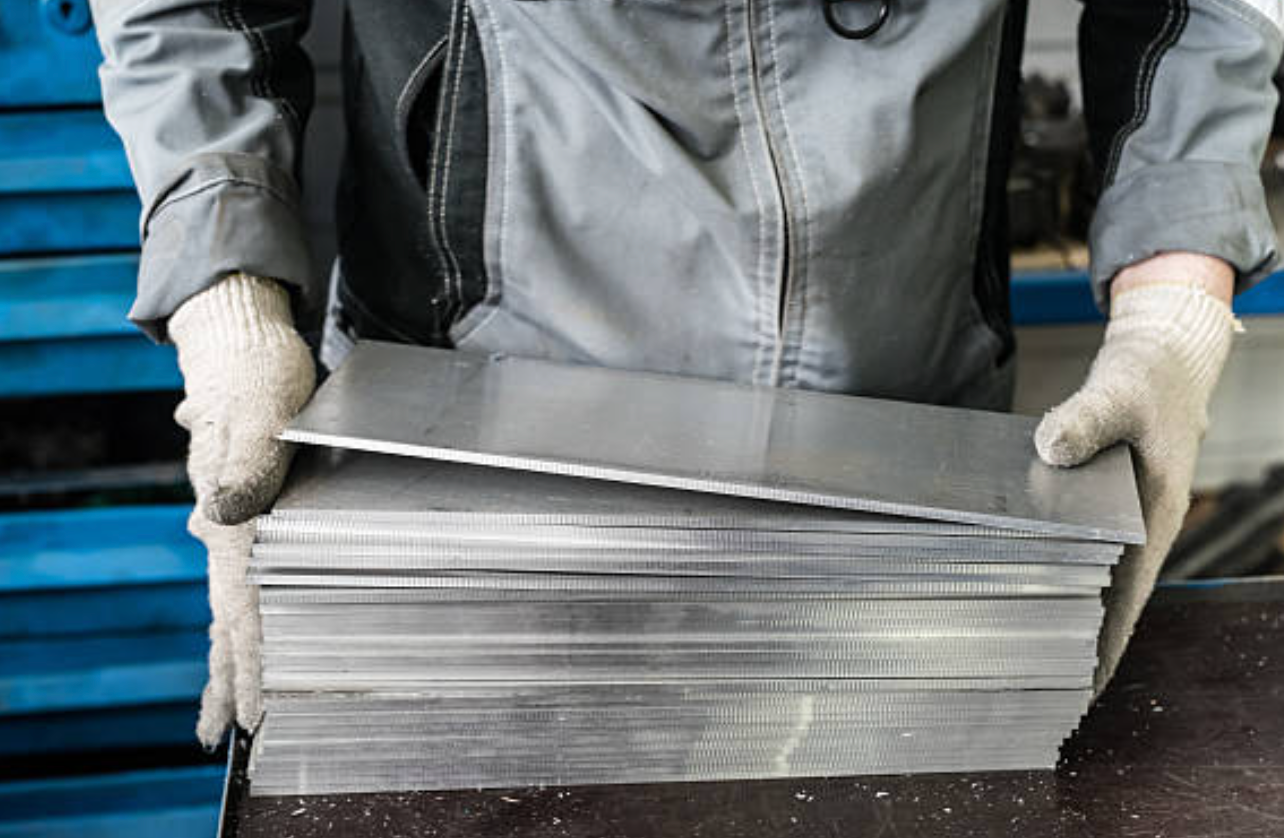
Sheet cutting is a crucial process in the manufacturing industry, especially when dealing with metals. It involves exceptionally precisely shaping large metal sheets into smaller, predefined segments. This operation not only determines the quality of the end products but also influences efficiency and profitability.
In metalwork, laser cutting stands out as a preferred method for sheet cutting. Its high precision and speed, combined with its ability to cut complex shapes without the need for tooling, make it an attractive option. Understanding the intricacies of laser cutting is essential to optimizing the process and minimizing sheet-cutting waste.
Why Is Sheet Cutting So Wasteful?
Waste in sheet cutting is an often overlooked yet significant challenge that manufacturing businesses face. It not only results in material wastage but also translates to economic losses. But how does all of this happen? Here are some of the key reasons:
High Quantity of Off-Cuts
One of the primary contributors to wastage in sheet cutting is the substantial amount of off-cuts produced. When metal sheets, for instance, are cut using conventional methods, the extracted shapes often leave behind irregularly sized and shaped remnants. Unless properly planned for reuse in future jobs, these off-cuts often end up being scrapped, leading to material and cost inefficiency.
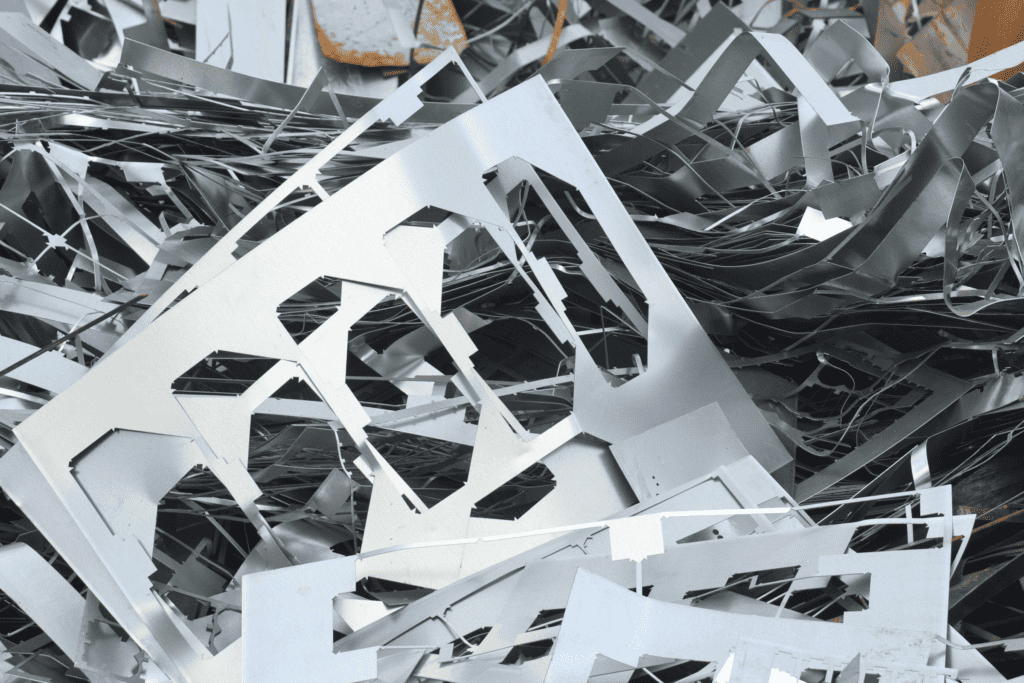
Inefficiency in Nesting
Inefficient nesting – the process of positioning different parts to be cut from a sheet – can also cause a high degree of waste. Without the correct software, expertise, and advanced machinery, pieces may be arranged haphazardly. This can cause unnecessary gaps between cuts, eventually wasting valuable material. As a result, using the wrong cut-off machine can escalate this issue. This results in a failure to optimize material use and maximize the number of pieces that can be obtained from a single sheet.
Lack of Precision
Precision is key in sheet cutting. However, if the cutting equipment is not properly calibrated or maintained, it may lead to inaccurate cuts. This creates a need for reworks, adding to the waste pile. Using a harder or premium cut-off wheel can improve precision, reducing waste and minimizing cut-off wheel wear.
Overproduction
Overproduction is another contributor to waste. Businesses sometimes produce more parts than necessary, intending to store them for future needs. This practice, however, could result in material wastage, particularly if the stored parts become obsolete or damaged over time.
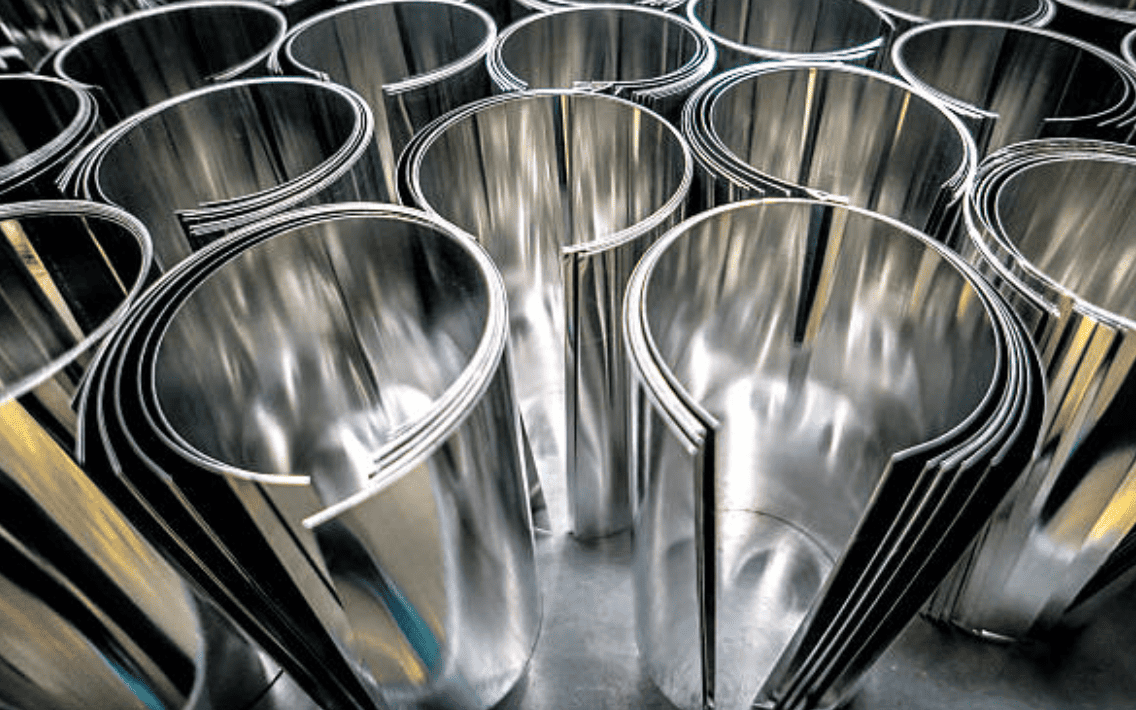
Resistance to Recycled Materials
Lastly, the resistance to the use of recycled materials can result in more waste. Many businesses prefer to use new sheets for their cutting needs, ignoring the potential of recycled or scrap materials. Integrating recycled content into projects throughout the production cycle and recycling bins where possible can help reduce the demand for new materials and lessen the overall waste.
5 Tips to Reduce Waste in Sheet Cutting
Now coming to the real deal. As discussed above sheet cutting equates to concerning amounts of waste which have both functional and economic costs. Reducing this waste can save costs and promote sustainability, both of which are crucial in today’s economic and environmental landscape. Here are five practical tips to help reduce waste in sheet cutting:
Tip 1: Utilize Efficient Nesting Software
Invest in high-quality nesting software that optimizes the placement of parts on a sheet of paper. This helps reduce gaps between cuts and maximizes material usage. Moreover, this software can dramatically cut down on paper waste and increase cost-effectiveness.
Tip 2: Regular Equipment Maintenance
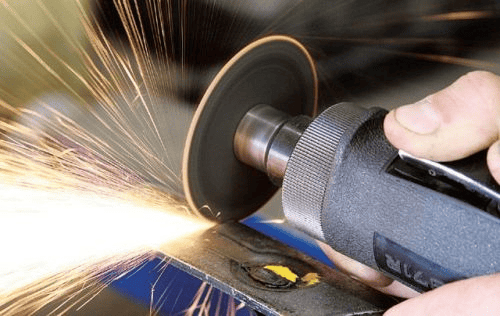
Ensure your cutting equipment is regularly calibrated and maintained to guarantee precise cuts. Precision reduces the need for reworks and mitigates waste. Additionally, opting for premium or harder cut-off wheels can further enhance precision.
Tip 3: Implement Lean Production Techniques
Consider incorporating lean production techniques, such as Just-in-Time production, to avoid overproduction and excess inventory. Producing only what is necessary when it’s necessary can save money and considerably decrease waste.
Tip 4: Encourage the Use of Recycled Materials
Promote the purchase and use of recycled or scrap materials where possible. Not only does this lessen the demand for new materials, but it also encourages a circular economy, reducing the overall waste footprint of your operations.
Tip 5: Opt for Advanced Cutting Technologies
Upgrade to advanced cutting technologies, such as laser cutting, which offer higher precision and less waste than traditional printing methods. While the initial investment may be higher, the waste reduction can lead to substantial savings in the long run.
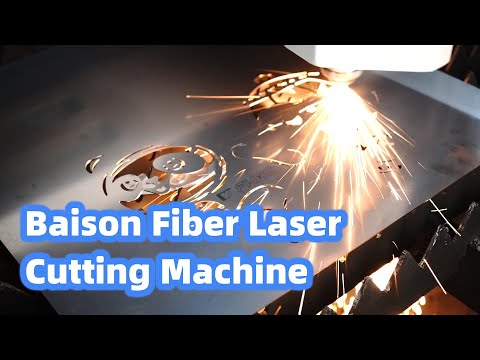
Benefits of Reducing Waste in Sheet Cutting
As a business, you might not realize the far-reaching benefits of reducing waste in sheet cutting. This dilemma mainly occurs because these benefits only become fruitful in the long run. As a result, you must look at it as an investment of resources that produces returns over time. Let’s try to understand this by discussing some of the major benefits of waste reduction in this process:
Cost Savings
When you reduce waste, you’re using your materials better, directly impacting your overall expenses. Less waste translates to less money spent on raw materials and savings from avoiding disposal costs. It’s not just about using less plastic or cloth bags and less packaging and saving on materials; it’s also about improving your overall process efficiency, which can bring about substantial cost benefits. Also, it makes it easier for your customers to purchase products.
Environmental Impact
Reducing waste also means reducing your environmental footprint. With growing awareness about environmental sustainability, businesses that demonstrate green practices can have a competitive advantage. Reduced waste means less material ends up in landfills, leading to lower emissions and less environmental impact.
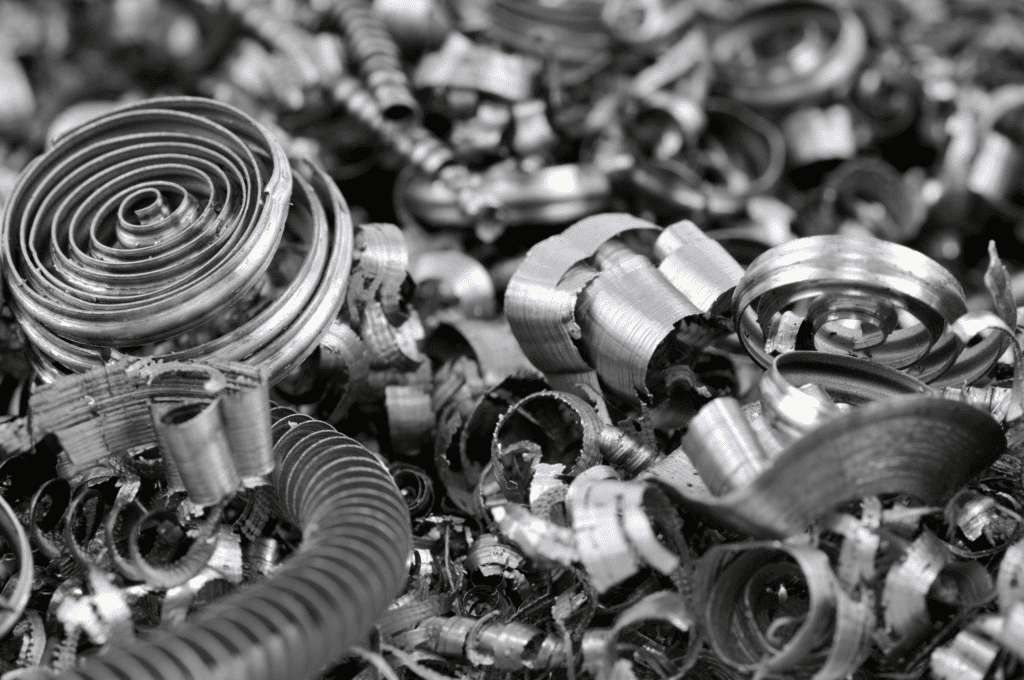
Process Efficiency
Waste reduction often goes hand in hand with process optimization. Adopting strategies to reduce waste can streamline your operations, enhance your process efficiency, and improve product quality. This can also contribute to better customer satisfaction and potentially increase sales.
Regulatory Compliance
In some industries, waste reduction in the second sheet is not just an operational preference but a regulatory requirement. By implementing waste reduction practices in sheet cutting, you’re contributing to creating a more sustainable world and ensuring that your business remains compliant with local, national, or even international environmental standards for reusable items.
Positive Brand Image
Today’s consumers are more environmentally conscious than ever, and businesses that demonstrate their commitment to sustainability can cultivate a positive brand image. By reducing waste in your sheet-cutting and packaging process, you’re saving resources and building a reputation as a responsible and forward-thinking business. It is also helpful to use reusable containers, print documents, paper napkins, paper towels, and cloth napkins around the office to reduce paper waste.
Case Studies
Let’s look at two real-world examples where businesses effectively implemented waste reduction strategies in their sheet-cutting processes, reaping significant benefits.
Case Study 1: Ashley Furniture Industries
Company: Ashley Furniture Industries
Industry: Furniture manufacturing
Problem: Ashley Furniture Industries was facing a significant problem with sheet-cutting waste. The company was using a traditional method of cutting sheets of wood, which resulted in a lot of paper use and scrap material. This was not only a waste of resources but also cost the company money.
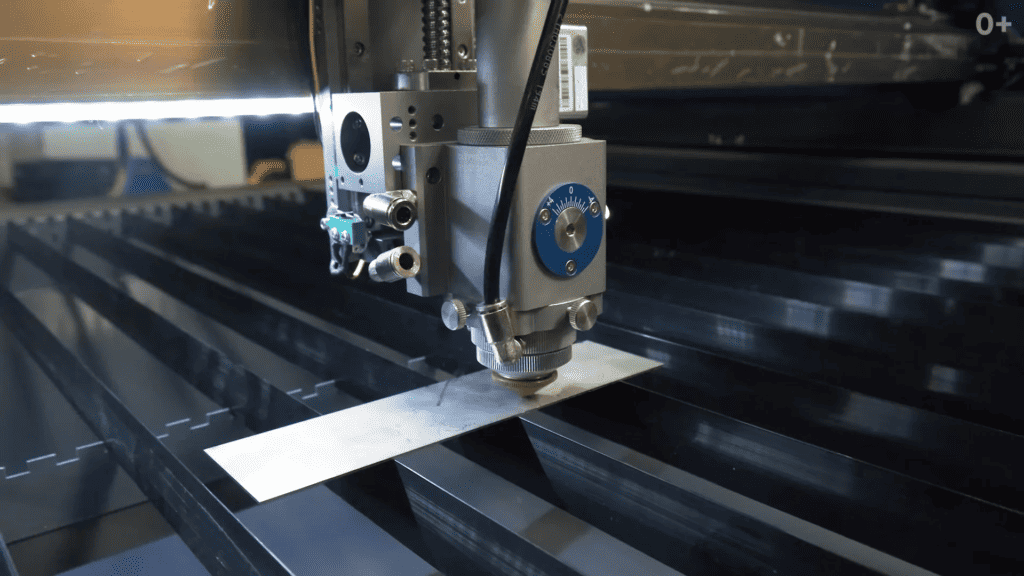
Solution: Ashley Furniture Industries invested in a new CNC cutting machine. This machine uses a computer to control the cutting process, which results in much less waste. The company also implemented a new system for managing its scrap material. This system allows the company to sell or donate its scrap material, reducing waste and costs.
Results: As a result of these changes, Ashley Furniture Industries was able to reduce its sheet-cutting waste by 75%. This has saved the company a significant amount of money and has also helped the company to become more environmentally friendly.
Case Study 2: Signarama
Company: Signarama
Industry: Signage Manufacturing
Problem: Signarama was also facing a problem with sheet-cutting waste. The company was using a traditional method of cutting sheets of acrylic, which resulted in a lot of scrap material. This was not only a waste of resources but also cost the company money.
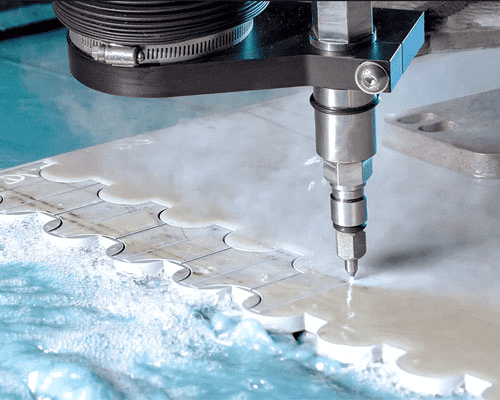
Solution: Signarama invested in a new waterjet cutting machine. This machine uses a high-pressure stream of water to cut sheets of material, which results in very little waste. The company also implemented a new system for managing its scrap paper material. This system allows the company to sell or donate its scrap material, which further reduces waste and costs.
Results: As a result of these changes, Signarama was able to reduce its sheet-cutting waste by 90%. This has saved the company a significant amount of money and has also helped the company to become more environmentally friendly.
These case studies show the potential for significant improvements when waste reduction strategies are effectively implemented in sheet-cutting processes. The benefits extend far beyond financial savings, contributing to a more sustainable operation and a more positive brand image.
Common Pitfalls to Avoid in Reducing Waste in Sheet Cutting
The drive to reduce waste in sheet cutting is a commendable one, and it can significantly benefit your business. However, it’s essential to ensure that the quality of your output is not compromised in the process. Here are some common pitfalls you should avoid:
- Sacrificing Quality for Speed: While faster sheet cutting might seem like it would increase efficiency, it can sometimes lead to inaccurate cuts and more waste. Always ensure that your machine settings and cutting speed align with the quality standards you aim to achieve.
- Over-Optimizing Processes: Over-optimization refers to making so many tweaks to a process that it becomes counterproductive. While optimizing cutting patterns is a good practice, doing so to the point of making the process overly complex can lead to errors and, paradoxically, more waste.
- Insufficient Staff Training: Invest time and resources in adequately training your staff to use cutting machines and implement waste reduction strategies. Remember, the success of any process largely depends on the people executing it.
- Ignoring Equipment Maintenance: Regular equipment maintenance is critical to ensuring consistent cutting precision and reducing waste. Overlooking this aspect can lead to machine malfunctions and unexpected downtime.
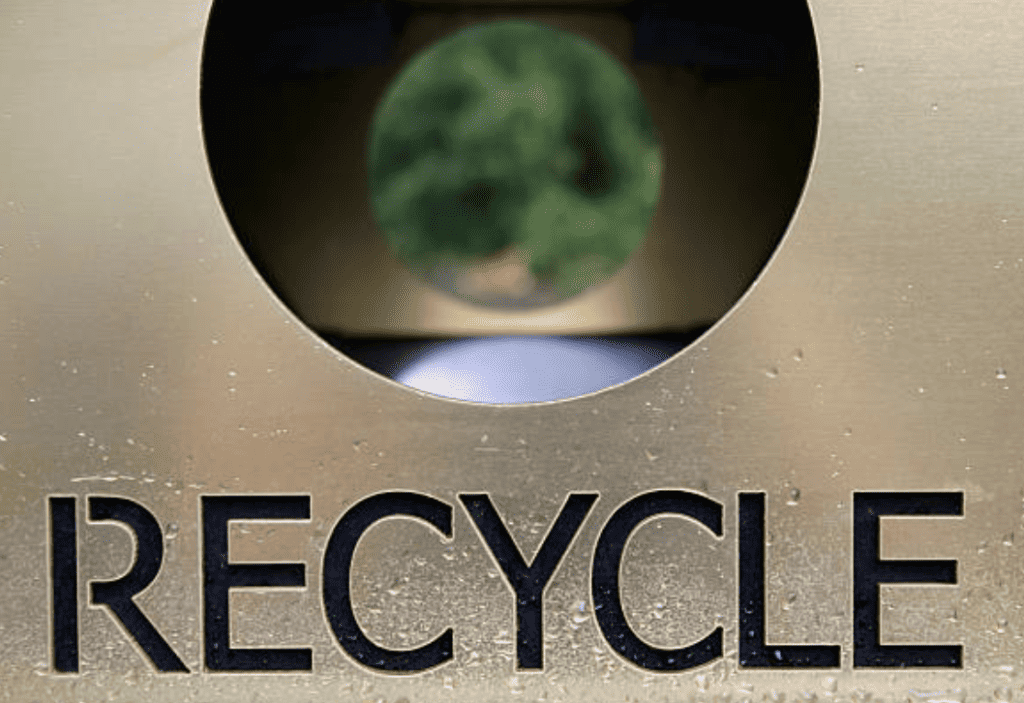
Q&A: Common Questions about Reducing Waste in Sheet Cutting
Q: How can I reduce offcuts from my sheet-cutting process?
A: Optimize your cutting patterns using advanced nesting software, which can arrange parts of documents in the most efficient way to minimize offcuts.
Q: Does the type of cutting machine I use affect waste generation?
A: Absolutely. Modern cutting machines with high precision and advanced software can significantly reduce waste compared to traditional methods.
Q: Can recycling be a solution to sheet-cutting waste?
A: Yes, recycling scrap materials is a great way to manage waste. It not only helps the environment but can be reused and also recoup some of your costs.
Q: How can staff training help reduce waste?
A: Well-trained staff can operate machines efficiently, adhere to optimized cutting patterns, and recycle and handle materials responsibly, all of which contribute to waste reduction.
Conclusion
In conclusion, waste reduction in sheet cutting is a multi-faceted endeavor involving strategic planning, optimal use of technology, regular equipment maintenance, and a well-trained team. By implementing the tips shared in this blog post, you can significantly reduce waste, save costs, and contribute positively to the environment. For more insights on how to improve your manufacturing processes, explore other resources on our website. Let’s journey together towards a more efficient and sustainable manufacturing world.
Transform Your Manufacturing Process Today
Take the first step towards a more efficient and waste-reduced production line with Baison Laser. Our cutting-edge sheet-cutting technology, coupled with our industry expertise, empowers businesses to optimize their operations and minimize waste. Let us help you make a lasting impact on your bottom line and the environment. Request a quote or get free sample proofing today.