What is Laser Cutting?
Cutting materials with the assistance of an intensively concentrated stream of laser beams is referred to as “laser cutting,” It is a technique that has received a great deal of attention in recent years. This technique utilizes vaporization and melting during the cutting phase to remove material.
The production of a light beam with a high density gets generated as a consequence of the stimulation of lasing material by electrical discharge. Then, with the assistance of optics and computer numerical control technologies, these lasers are focused and steered on the material. Laser cutting has been around for decades, and ever since it was introduced, there has been a constantly rising demand for these laser-cutting Nitrogen generators.
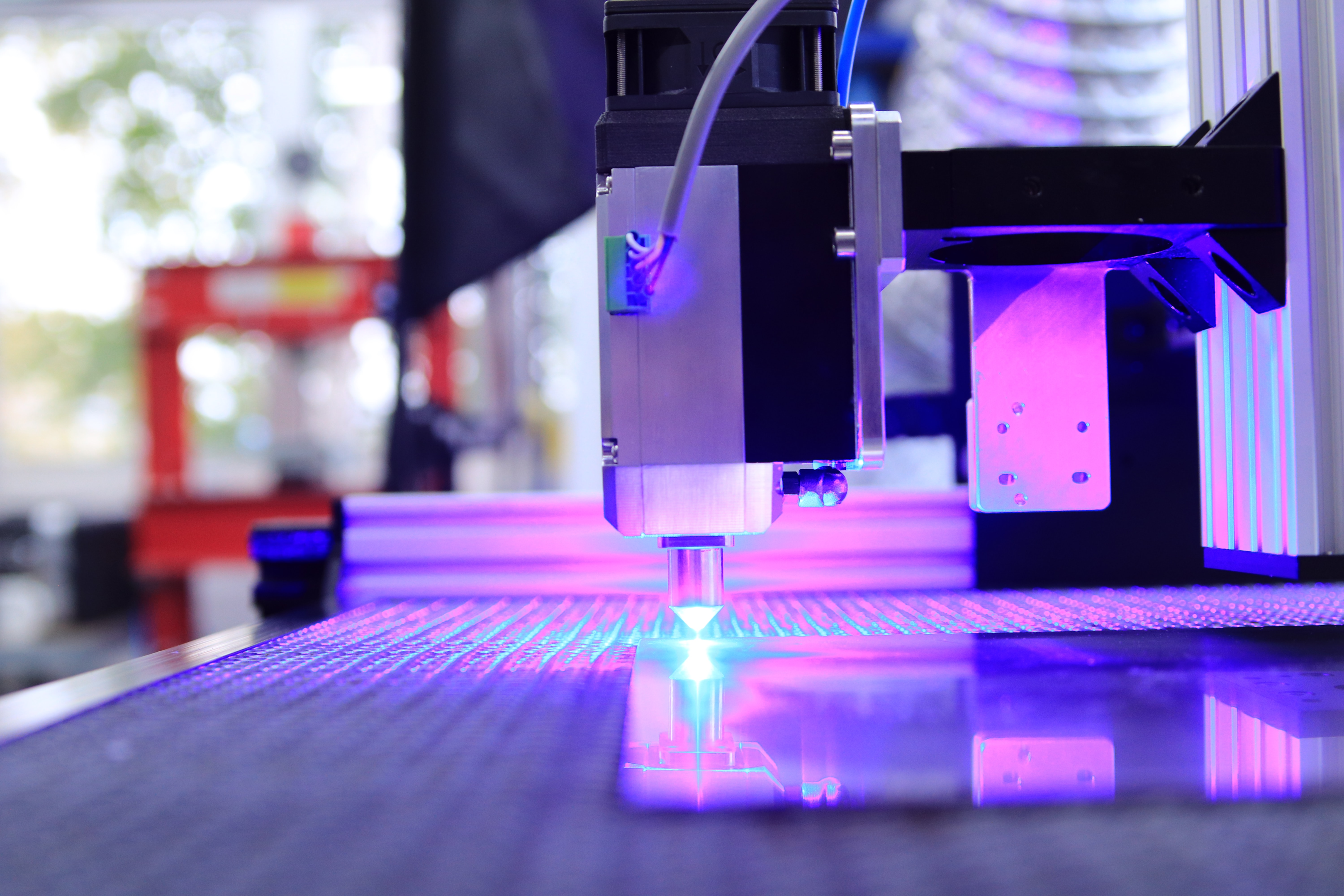
How Does Oxygen Laser Cutting Work?
Cutting with Oxygen involves heating the material to the point where it can be ignited and then allowing it to burn and vaporize. Additional heat energy gets generated due to the interaction between the metal and the Oxygen, which causes an exothermic reaction and provides a much easier cutting process.
Additionally, throughout this laser-cutting process, you can raise the pressure of the Oxygen to boost the removal process. It will help you get a better and more precise cut. It is very important to remember that the material’s thickness will determine the maximum allowable amount of pressure applied.
How Does Nitrogen Laser Cutting Work?
Nitrogen laser cutting works by utilizing the heat in the process, enabling the laser to cut through the metal by melting it as it passes. After that, Nitrogen gas gets used, so the accessible molten metal gets thrown off. Since the gas is inert, it prevents the contamination of Oxygen and ensures a finish that is very clean and of high quality.
Since Nitrogen facilitates highly efficient and effective cutting, it finds widespread application in commercial and industrial settings. In addition, cutting with Nitrogen is more advantageous than cutting with several other techniques, including cutting with Oxygen in certain aspects.
Why Is Nitrogen Used In Laser Cutting?
The inert quality of Nitrogen is the primary reason for its widespread application. Nitrogen is widely used in various modern industries as an assist gas because it minimizes the likelihood of unfavorable oxidation on the surface of a metal.
Nitrogen gas is recognized to displace Oxygen from the material’s surface efficiently. Additionally, it has become popular among businesses using laser cutting instruments because of its accuracy, precision, efficiency, and high-quality finishes.
Why is Oxygen Used in Laser Cutting?
Since the beginning of laser cutting, Oxygen has been an essential component. Oxygen gets used due to the ease with which they operate and the excellent quality edges they provide for thick materials. In addition, Oxygen cutting is more financially sustainable. The feature of having low power consumption is also a primary reason behind this. Most of their applications involve cutting mild steel and other metals whose oxides have a low melting point.
Benefits of Using Laser Cutting Over Other Methods of Cutting Metal Materials?
The flexibility that laser cutting offers have contributed to the system’s widespread use in various commercial and industrial settings, including small firms. There are a large number of additional cutting procedures that make use of a variety of sources and approaches. However, the use of laser cutting has long been prevalent. Therefore, today, we will look at some advantages of laser cutting over other methods.
Better Precision & Accuracy
Laser cutting technology is much superior to various other sorts of cutting technologies. In addition, using CNC technology in laser cutting allows the production of components to be highly precise, with no tolerance levels and absolutely no deviations. As a result, when it comes to cutting, laser cutting is far more detailed and accurate. In addition, there is no dross left behind after the cutting process.
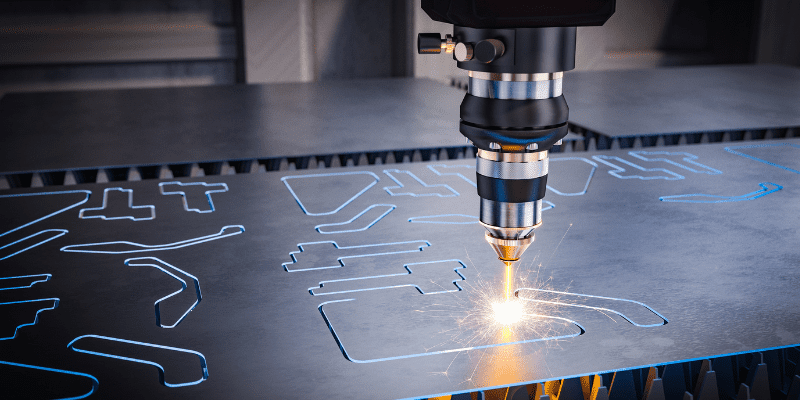
Better Efficiency
Compared to more traditional cutting methods, the speed with which laser-cutting equipment can cut through materials is significantly higher. They can operate on average between 20 and 60 inches per minute, which is a very effective speed range. In addition, a laser machine may operate without stopping indefinitely and will not have any issues that cause it to slow down. Therefore, the acquisition of laser-cutting equipment of superior quality is an excellent investment for your company.
Easy Handling
Many modern manufacturing organizations and sectors use the laser cutting process since it is simple. Compared to other cutting methods, laser technology does not need its users to have in-depth knowledge of the whole cutting equipment. The laser cutting equipment utilized is relatively simple and requires just a basic level of comprehension. However, it is necessary for anybody who operates the machine to be aware of all of the preventive measures and possible consequences.
Affordability
Laser cutting equipment might be a bit pricey, but when you include the cost of labor and the maintenance cost of the cutting machines, laser cutting is a far more cost-effective option. In addition, the laser cutting process uses various technologies that can automate the process, resulting in reduced costs associated with labor. Laser cutting is the method to use if you are searching for a cutting tool that will last for an extended period.
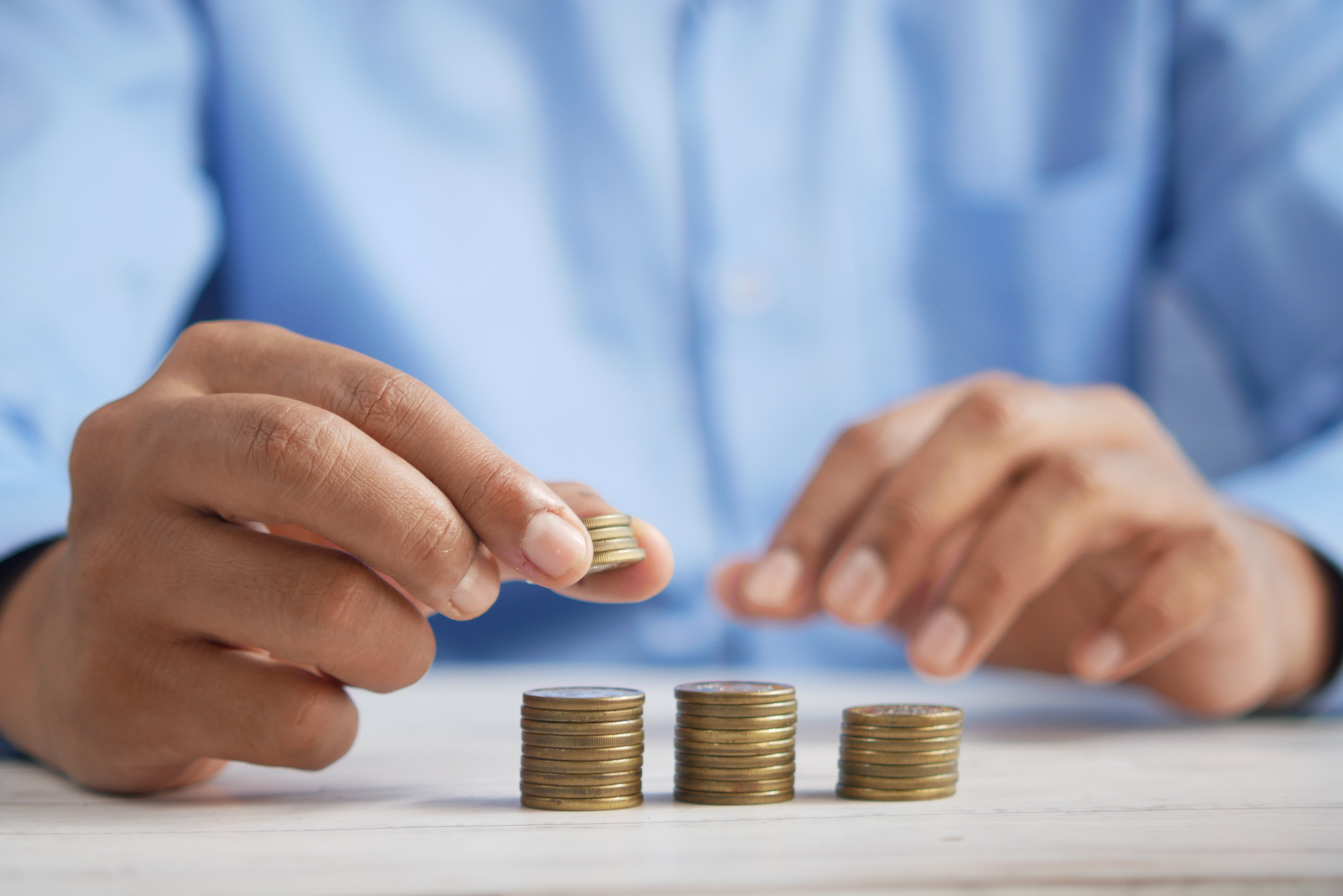
How Does Using Oxygen or Nitrogen Gas Affect the Finished Product Quality?
In recent years, projects that use the Oxygen and Nitrogen-cutting process have noticed a noticeable increase. Oxygen gets employed as a laser assist gas in cutting steel. In contrast, cutting with Nitrogen is mechanical because no chemical reaction is involved. However, the issue remains: how do these assist gases influence the material’s quality? There is a significant debate about the cutting quality and the utilization of Oxygen and Nitrogen as assist gases.
However, purity is among the most significant factors contributing to the highest possible quality. The average baseline purity of industrial-grade Oxygen is 99.5%, slightly lower. However, anything with a purity that is more than 99.5% will offer you high-edge quality and a premium cut for materials such as aluminum, brass, and many others.
The most up-to-date laser cutting approach involves using Nitrogen as an assist gas. Nitrogen is an inert gas making it very easy to handle. In addition, Nitrogen is a straightforward element since it does not react with molten material. Therefore, we recommended utilizing Nitrogen as the cutting medium when cutting thinner materials such as stainless steel. Also, keep a close eye on the purity levels, as even the tiniest amount of contamination may cause the cut edges to be completely yellow.
Which Gas Should You Choose for Your Specific Project – Oxygen or Nitrogen – And Why?
When working on a project requiring laser cutting, you must know which assist gas should be used for that endeavor. There are a variety of assist gases available; however, Oxygen and Nitrogen are the two that get used most often. Both have characteristics that set them apart and make them suitable for various materials and applications. To clarify the situation, we have outlined the applications of Nitrogen and Oxygen as assist gases.
Oxygen Assist Gas
Oxygen has been the go-to assist gas for laser cutting for many decades and continues to be the benchmark. They get used in the process of laser cutting carbon and mild steel. The Oxygen-cutting method involves vaporizing and melting the material that gets cut. Therefore, cutting with Oxygen is highly preferable for metal with a 2 and 3 millimeters thickness.
Since the reaction between Oxygen and metal generates more energy in the form of heat, using Oxygen for such materials is recommended since it will make cutting the material far simpler. Oxygen can be employed to cut through a wide range of materials, but to do it properly. You need to have an in-depth understanding of the substance you are dealing with.
Nitrogen Assist Gas
Cutting with Nitrogen is preferable when cutting materials such as stainless steel, aluminum, or alloy. Nitrogen is a gas that does not react with other substances; hence it is noted for its ability to offer clean cutting. However, laser power is required to melt the material for this procedure to succeed. In addition, increasing the Nitrogen pressure will cause the cutting speed to increase.
What Factors Should You Consider When Deciding Which Gas to Use for Laser-Cutting Metal Materials?
When it comes to laser cutting, a wide variety of assist gases are available. Therefore, selecting the appropriate cutting gas for your operation is paramount. The properties and capacities of gases vary, and one gas can’t behave the same for any given material. As a result, understanding how to choose the appropriate gases is essential.
Compatibility
Laser-cutting machines use various gases, each contributing a unique characteristic to the cutting process. Therefore, a particular assist gas may not be suitable for using a broad range of materials. Before settling on gas for laser cutting, you must ensure the assist gas is compatible with the material you’ll be working on. Using this strategy will save you substantial time and anxiety over incompatibility difficulties. However, if you still have trouble selecting the appropriate assist gas, we have included a table below that lists the gases and materials compatible.
Gas Expenses
The majority of individuals tend to overlook critical considerations like operational costs or gas expenses. Every gas comes with a price, and the owner of a laser device is responsible for paying for it. It is essential to remember that each kind of gas varies, which might cause your overall running expenses to either increase or decrease.
Furthermore, the power of the machine’s laser will impact the entire cost, both positively and negatively. For example, cutting with Nitrogen may be more costly per hour than cutting with Oxygen, depending on the machine used. On the other hand, you may find that cutting with Oxygen is more cost-effective when cutting extremely thick steel than other methods.
Processing Speed
The processing speed is the most significant concern when choosing laser equipment that uses assist gas. This is because the rate at which Nitrogen gets cut is directly proportional to the power. However, the speed at which Oxygen is cut gets restricted by the administration that the machine delivers. Therefore, using nitrogen gas to cut anything is recommended to complete the work quickly and effectively.
However, remember that Nitrogen will not always provide you with great speed in every situation. Nitrogen tends to slow down when thicker materials are getting used. In comparison, Oxygen may improve speed when utilized in thicker materials.
Edge Quality
When cutting any material, having good edge quality is crucial. For example, users observed that cutting with Nitrogen produces a better edge quality than cutting with Oxygen. The powder coat adheres very well to materials, which avoids further operation that would smooth off the edges. However, the oxide surface of materials cut with Oxygen may affect the powder coat, which results in slightly inferior edge quality.
Assist Gas | Material Compatible |
Nitrogen | Stainless Steel Copper Aluminum Brass Alloy |
Oxygen | Carbon Steel Stainless Steel Copper Alloy Electroplated Steel Plate |
Compressed Air | Carbon Steel Aluminum Copper Brass Non-Metal |
General Guidelines for Choosing Between Oxygen and Nitrogen Gas
Nitrogen or Oxygen gas is required to function correctly for CO2 or fiber laser-cutting devices. When deciding between Oxygen and Nitrogen gas, there are several guidelines that you need to follow. Therefore, we have compiled some pointers for you to consider before purchasing assist gas.
Step 1: Understand Your Requirements
You must fully comprehend all your requirements concerning the Nitrogen and Oxygen laser cutting before making any purchases. In addition, since each of them is suited for a particular use, you need to be sure you understand the purpose behind your purchase.
Step 2: Check the Compatibility
As mentioned previously, it is impossible to use a single assist gas capable of cutting through all varieties of metals and non-metals. In addition, since the characteristics of every gas are unique, you must be familiar with how various materials interact with the different gases. Therefore, we have included a table that lists the many materials compatible with each gas.
Step 3: Set a Budget
Before making any purchases, you must determine your total budget. You will be able to avoid going over budget and save money by doing things in this manner. In addition, if you are considering purchasing a Nitrogen or Oxygen laser, include the ongoing operating costs, maintenance costs, and other relevant costs. Doing so will give you a clear sense of how much the actual acquisition cost will be.
Step 4: Efficiency
A spectrum of efficiencies is available for lasers that use Oxygen and Nitrogen. Nitrogen has a strong tendency to be considerably quicker in comparison to Oxygen. Therefore, if you want to complete your task in a much shorter time, you might consider using Nitrogen laser cutting. Unless you employ thicker components, the speed of the Nitrogen will decrease; in this scenario, you may substitute Oxygen, which does not inhibit the speed but boosts it.
Step 5: Storage Availability
There are moments when we make purchases without considering whether or not the item will fit in the area it will occupy. Therefore, you should always ensure that you measure whether or not you have storage facilities or whether or not you can build some space. In addition, lasers available today come in a wide variety of sizes and shapes, allowing you to choose the most appropriate model for the area.
Conclusion
The Nitrogen or Oxygen laser will be a fantastic option for you to go with, depending on the particular cutting goals of the task that you are doing. The functioning of each approach may be somewhat different because mechanical and laser cutting provide results that are reasonably comparable to one another. Please contact us so we can give you more information if you are still unsure about these two assist gases.