Your ability to care for and manage your laser machine directly impacts your business and operations. It will even ripple out to client relations and your ability to retain current clients and attract potential customers in the future.
Why Is It Important to Maintain Your Laser Cutting Machine?
It is important to maintain your laser-cutting machines to lower the possibility of machine breakdown. When this happens, you could be looking at costly repairs. There is also a big chance that you might need to replace a few parts of your laser cutting machine. This means you could incur costs in parts replacement.
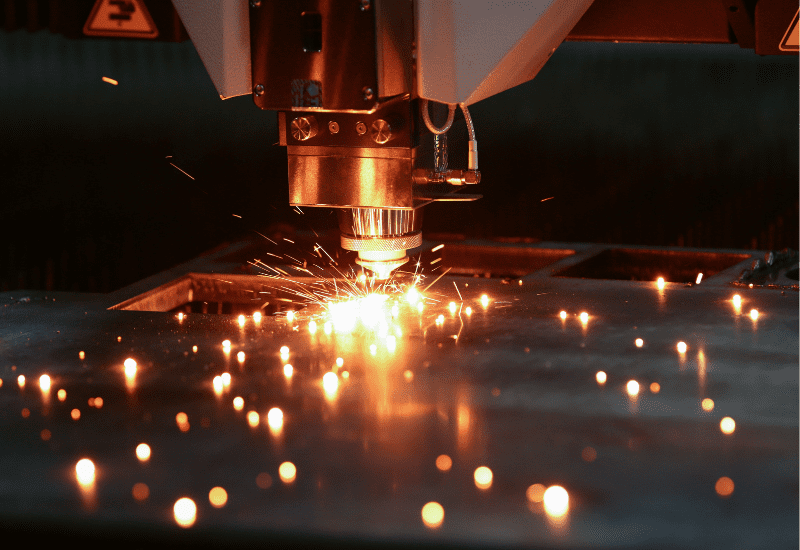
Not to mention that your production could slow down when you are fixing your machine. Operations will be bogged down with one machine unable to work. The challenging part is if you are starting and you only have one machine, and it breaks down. Not only will your only source of income cease to work, but you will also have to spend on repairs and parts replacement.
Remember that regular laser-cutting machine operation produces a combination of smoke, a fair amount of material debris, and even fumes. All in all, these particulates could build up over time when not cleaned. They can accumulate in and around different areas in your machine. As a result, overheating and, eventually, system failure can happen.
The good thing is that this and many more situations are preventable. You can mitigate the negative impact of system breakdown in your laser-cutting machine if you pay attention to regular maintenance of your units. Do not think about maintenance as an additional cost. Machine maintenance for your laser cutter aims to help you increase your bottom line in the years to come. It also prevents you from spending a fortune on preventable parts and machine replacement.

Real World Guide to Laser Cutting Machine Maintenance Checklist
Now that you know the importance of maintaining your laser-cutting machines, here is a comprehensive guide to help you look after your machines. Remember that these investments can be in service for an extended time, provided you take care of them.
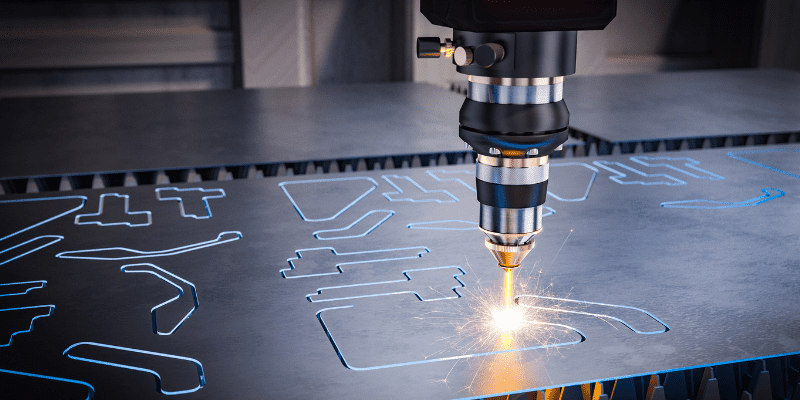
I. General Maintenance
Laser-cutting machine maintenance is lengthy, so we will break it down into segments starting with general maintenance. These are the things you need to perform regularly.
1. Fan Unit
You might think you do not need to clean the fan unit since it can easily expel debris. But remember that materials like wood, MDF, and acrylic give off a lot of residue and fumes when cut. Even if you have a fume filter, it helps to check the dust accumulation in your fan unit.
It can lower the chance of your fan unit being a fire hazard. This can also promote a good ventilation effect in your workplace.
The process is pretty straightforward to perform. In most, if not all, maintenance work, you must make sure you disconnect the power supply. This protects you from being electrocuted.
Once you have done that for the fan unit, disconnect the hose and then clean the fan duct in the ports. A paintbrush that is soft usually does the job. Once you’re done, connect the hoses again, and you’re done.
2. Compressors for the Air-assist
The most common issue with this area is elements getting into the filtration and obstructing airflow. When this happens, you might notice smoke or a small flame starting and breaking out the materials while laser cutting.
Simply check the hose from the cutting head to the compressor. The goal is to clean and remove any obstruction to ensure adequate air gets to the nozzle.
3. Lubrication
Remember that you are using a machine that uses moving mechanical parts made of steel. There are bearings and gaskets that can lower the friction between moving elements.
But lubricating friction areas like where the cutting bed moves around can ensure a smooth operation. This will help prevent hairline cracks and fractures in the machine from forming and contribute to giving you quality and consistent cuts every time.
4. Optics Maintenance for Laser Beam
Your optical lenses and their parts are arguably some of the most important parts of your laser cutter machine that you must regularly monitor and maintain. As you are dealing with lasers to cut several materials, your optics play a crucial role in your machine’s operation.
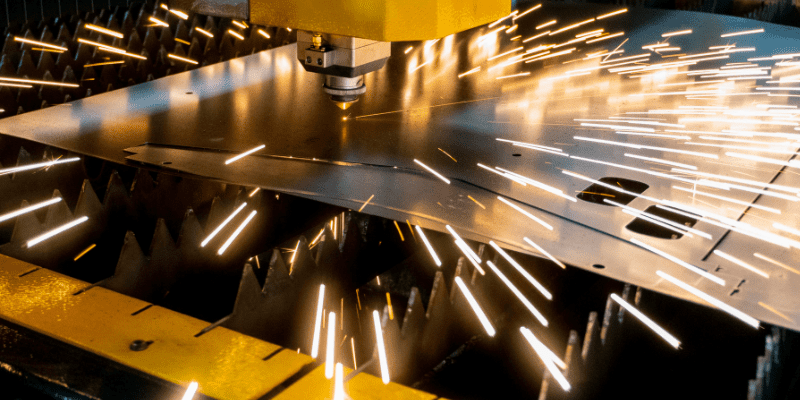
When your optical lens is not maintained, it can result in blurry lines in your cutting or not even reaching your desired cutting depth. There are even instances in which optical lenses catch fire because of contaminants. This causes permanent damage and usually leads to replacement.
Regularly checking and visually inspecting the optics, even the lens surface, is important. This helps ensure that you remove any contaminants on the optic’s surface and clean them as soon as you see them. You can use a few things to clean, but an acetone or IPA solution paired with cotton buds usually works.
5. Tube Chiller
You must remember that laser-cutting machines produce extreme heat, especially in and around the tube. This is where the laser travels around and out of the nozzle to cut materials. As a result, it needs constant care to ensure it does not overheat. remember that the tube chiller is like the water tank keeping the laser head cool.
This is one of the important maintenance work you need to put in your schedule. A good practice is to check the chiller’s filter to ensure that any contaminants are not blocking it. This could drastically reduce the ability of the chiller and the cooling water to control your machine’s temperature.
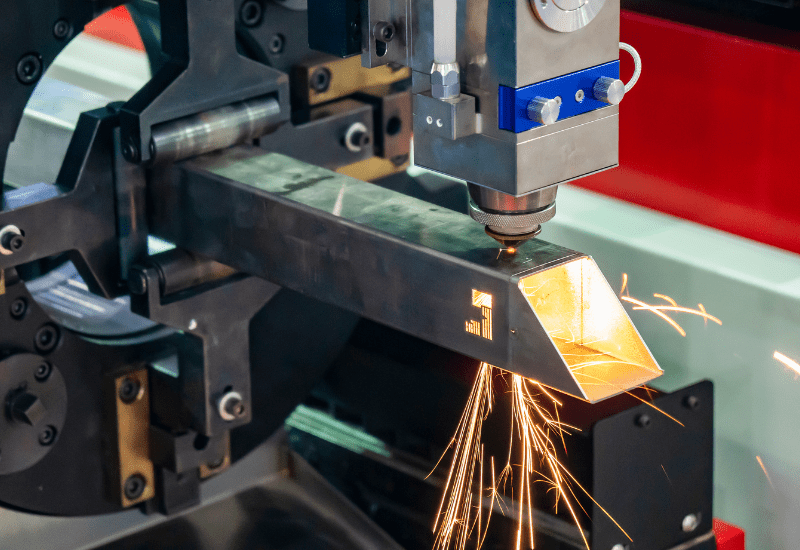
When cleaning the chiller, or any part of the machine, never use bleach. This can cause oxidation on the metal parts it touches. Water quality is essential. When this happens, it can trigger the formation of rust in your laser machine.
Now that you have an idea what some of the general maintenance routines you can make when it comes to your machines, did you know you can label these tasks based on frequency? There are certain tasks in your laser cutting machine maintenance checklist you need to do periodically.
Some daily and some on a weekly and monthly basis. Here is a helpful guide on how you can spread out your laser-cutting machine’s maintenance over time.
II. Daily Maintenance for Laser Cutting Machines
Let’s look at the daily maintenance tasks you can do to help your laser-cutting machine function well. This will help you prevent irregular maintenance on your machine.
- Check the laser working gas pressure of the machine before you turn it on for the day’s production. Overlooking the gas pressure could land you in a lot of trouble later on.
- To start the day, it is vital to check the machine bed and if the x-axis and y-axis (even the z-axis) are at zero points. Do a visual inspection of the whole machine and buttons to see if there is damage before starting it.
- Make sure that the mounting screws of the X and Y axis on the bed are loose.
- It is also important to verify the sensitivity of each axis’ limit switches.
- The circulating water in the chiller to maintain the tube’s temperature must be sufficient every day. The pressure also needs to be maintained. It is usually at 3.5 – 5 Bar, but this can vary depending on your machine.
- Ensure that there are no leaks in the circulating waterways. This is true, especially for the external optical path.
- The oil in the vacuum pump must be maintained at the required level of the machine. You can top-up the oil when it falls below the minimum level.
- Check the water, oil, and gas paths of the laser, pipe joints, and pneumatic components in the pump for leaks. If there is, identify the source and have then checked and repaired immediately by a professional
- Once you are done for the day, conduct a visual check on the focus lens to verify there is no evident damage.
- It is also important to regularly clean and around the entire machine after your daily work. This includes cleaning waste produced from cutting and other visible debris. Keep the work site neat also with a daily inspection. Check if you need specific machine tools to help you clean.
- It also helps to check the drain valve and open it to help the air tank underneath the compressor release water. Just make sure you close the drain valve after draining the water.
- Ensure you follow the shutdown procedure protocol when turning in for the day. After which, locate the main power supply and shut down the machine. If you see an indicator light still on, recheck the machine. This will help keep the machine working properly.

III. Weekly Maintenance
Now we look at the weekly maintenance tasks you can do every week.
- Check the air outlet to remove dust and clean debris and other contaminants from blocking the machine’s ventilation.
- You need to do the same with the filters that connect and deliver gas to the machine. It is a good idea to check and remove water and other types of debris build-up that can block that filter.
- Daily use can cause some screws to come loose little by little. Because of this, it will help your laser-cutting machine if you check the screws, especially the bumper bracket and those around the travel switch bracket if they are coming loose. If they are, tighten them down.
- Locate the ventilation fan’s filter screen of your machine’s electric control cabinet. As the filter is meant to keep dust from entering the panels and managing the temperature, you need to clean them to ensure adequate airflow in your machine.
- Regular operation of your laser-cutting machine can cause your guide rail to accumulate many types of debris. Every week, you can check and clean the debris that could get stuck in the cavity of your guide rails. This will ensure smooth movement, prolong your rail’s life, and ensure your laser light is on point.
- Once a week, it helps to check if your machine is still level on the ground. Remember that constant operation could cause it to make minor movements now and then. The movement of either the laser head or the bed is usually the cause for these slight machine movements. Over time, this can all add up and misalign your whole machine and could affect your laser beam.
- Regarding movement, proper maintenance means lubricating lead screws and guides of your x-axis and y-axis points (even the z-axis). This lowers the friction along your screws and axis guides. It will also extend the operational life of your machine.
- Check the focusing lenses as well and clean them regularly. This can help improve your laser’s beam quality. If your focusing lens is clean, you also help prevent costly repairs in the future.
- Make a visual check of the mirrors in the laser tube to ensure they are clean and free from contaminants. If they are beyond repair for any machine tool, replace them immediately before using the machine again.
- Look at the filter of your laser’s gas drying unit. Remember that the normal color of this filter is blue. If it is any other color, replace it immediately.
IV. Six-month Maintenance
There are also specific areas to check for proper maintenance of your machine every half a year. Here are some of them:
- Locate the cooling water pipe for your laser head and check for any signs of wear and tear or corrosion. If there is, replacement of the pipe must be done at once.
- There should be no leaks in your power supply’s fuel tank. This can cause serious damage not only to the machine but to your workspace as well. Make sure to have it fixed immediately if you see any leaks.
- Your laser cutting equipment has high-voltage cables running through it to power it during operation. Every six months, check if there is any visible damage or corrosion in these cables. Exposed wirings could lead to severe damage to your machine and is a potential fire hazard.
- Check your vacuum and root pump oil and replace them every 6 months.
- Clean the white plastic plug at the end of the roots pump. This is usually located at the gas splitter on one end of the pump.
V. Winter Maintenance
More than a time-specific maintenance guide, there are times that extreme changes in weather affect the machine as well. Just like when winter hits, you need to take extra care of your machine. Here are a few things to check to ensure your production runs smoothly during winter and your machine works.
- Make sure that your work area where your machine is has a temperature above 0°C. Ideally, it needs to be around 5°C.
- If needed under extreme drops in temperature, explore using anti-freeze in your coolant circuits. Just make sure to avoid automotive coolants because they are strictly forbidden and might not be compatible and cause more damage to your machine. Using distilled water might be a better option.
- Regularly check the chiller for the tube and make sure they are not icing up and within acceptable water temperature.
- Clean up contaminants or cut waste in and around the machine because they are much more challenging to clean in your equipment when they freeze up.
- During winter, a dark and humid place for your machine can also cause your equipment to seize up. Too much of this can shorten the service life of your machine.
Possible Effects of Poorly Maintained Machines
You could ask yourself why you need a comprehensive maintenance checklist for your laser machine. It could seem tiring and might take up most of your time. In reality, it will take time, but if you do not maintain your machines, you could lose a lot more.
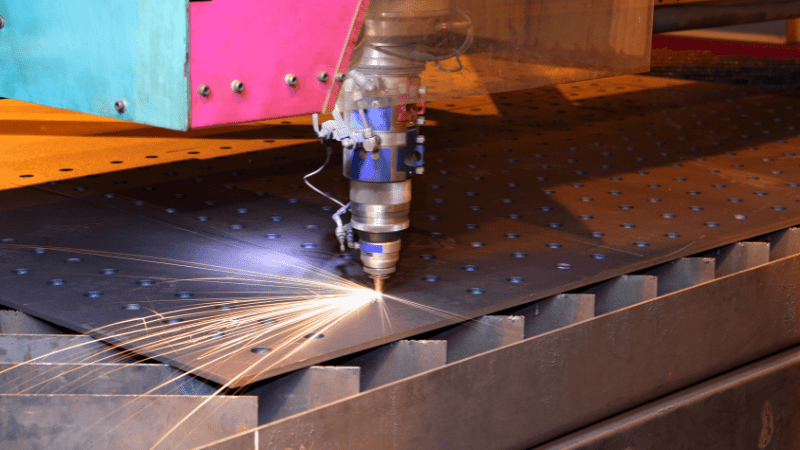
Look at what could happen if you forego machine maintenance and just run your machine to the ground.
Unnecessary equipment expenses – poorly maintained machines tend to cost you a lot of money over time. It can put too much pressure on your operating expenses. You can avoid this if you only get ahead of avoidable breakdowns. Machine maintenance is not about fixing several parts of your machine. It is maintaining them to make sure that you can avoid costly repairs in the future.
Working environment accidents – there are areas in your machine that, if not maintained, could cause serious damage to life and property. You want to ensure that your people are safe and can operate the machine without worrying if it will catch fire or blow up. More than that, you are also putting your production floor at risk when you run poorly maintained machines.
Dip in production quality – when you choose to look the other way and pass up equipment maintenance, there will be times when your output quality will suffer. It can be uneven cutting, damaging the material’s surface, or even a slowdown in the cutting timeline.
Loss of income – if you do not maintain your laser machine, there is a big chance that your equipment will experience breakdowns often. When one machine stops and requires repair, you will not be able to use it until it is ready.
During that time, you lose income because production is put on hold. Not only that, too many of these breakdowns and potential clients could choose to work with some other company. This means you lose potential income as well.

The Takeaway
The main point of this article is to ensure that you make time and put in the work to maintain your laser-cutting machines at regular intervals. Preventive maintenance will help you prolong the service life of your machines.
On top of this, it can give you peace of mind knowing they are in good condition. In doing so, you also save on unnecessary repairs now and then. You can focus on replacement parts due to age and normal wear and tear.
Your production will also not be interrupted, ensuring that you can deliver on time to clients. This strengthens your business relationship with them and shows your professionalism in your industry. This could help you retain current clients and attract potential customers.
Laser Cutting Machine Maintenance with Industry Experts!
It is true that laser machine maintenance might be a handful, but if you get to work with professionals like our experts in Baison Laser, this process becomes a breeze.
Not only will you be starting on the right foot, but our team of industry experts will guide you every step of the way. Contact Baison now for more professional advice and attractive machines!