What is Laser Welding?
Laser welding is an advanced technique to join two or more pieces of thermoplastics and metals with the help of a highly focused laser beam in the visible/infrared region. The laser system used in this technique is a highly concentrated source of heat/energy with the capability to produce deep laser weld seams to solder the metal parts together. This laser-welding system was invented in 1988 by Jones and his team for an industrial application.
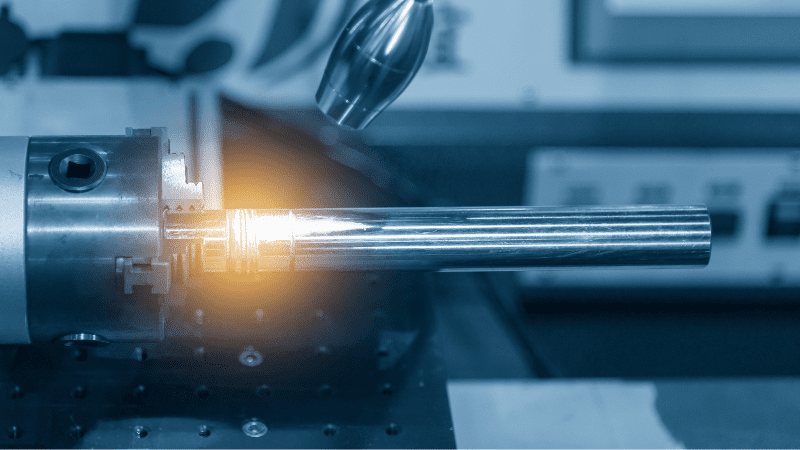
The heat laser beam is very focused, so it doesn’t damage other nearby metal parts. Due to this thin focus feature, this technique results in immaculate and aesthetic welding finishes. Moreover, laser power welding can weld pieces with even a few millimeters.
The technique is renowned for precision welding applications for these high accuracy features.
The laser welding process happens quickly since it doesn’t involve any additional consumable materials to bond between metals. However, this extra material is often required in traditional welding techniques, such as MIG (metal inert gas) and TIG (tungsten inert gas) welding.
The laser welding technique applies to metals such as aluminum, steel, and titanium and exquisite metals like silver and gold. With its ability to cope with various metals and precision capabilities, this technique develops delicate and highly accurate components. Moreover, laser welding techniques are very favorable to use in applications that are difficult for humans to access, meaning small access areas.
All these features will be much easier to understand after knowing what happens inside the laser welding machine. How do the results become accurate and focused? How does a small beam result in such a strong bond? To develop such understanding, one must dive deeper into the technical details of the backend process behind this advanced, i.e., laser welding technique.
Laser Welding Technique
The laser welding technique operates in two different modes. One is keyhole welding mode, while the other is conduction limited welding mode. The welding mode depends on the workpiece material and the power density with which the beam will hit the workpiece. Read the details below to understand the features of these two modes and how they differ.
- Keyhole Welding Mode
Manufacturers prefer keyhole welding as it is a high power density mode, and most metals weld perfectly with a high energy density laser beam. This high power density of the laser beam is acquired through a keyhole mechanism.
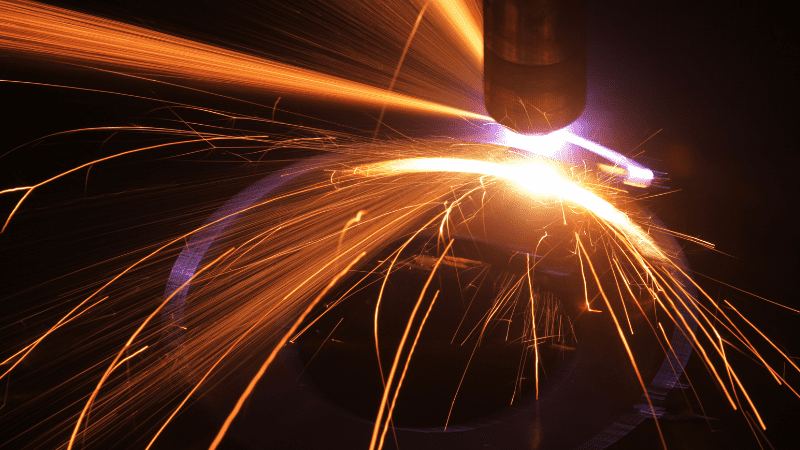
Initially, the welding machine is focused precisely on the workpiece where the joint is required. As the process starts, the laser machine produces a high-density heated laser beam. Know that the density is high enough not just to melt the metal workpiece part but even vaporize the workpiece material. As the laser enters the workpiece and vaporizes the part, a small cavity is created called a keyhole cavity. This cavity becomes ionized due to the high-energy focused beam and results in plasma formation, further assisting the process by preventing cavity walls from collapsing. This keyhole is traversed with the other metal or part to be joined. A high-intensity energy beam and plasma creation eventually join two parts and form a weld.
- Conduction Limited Welding Mode
This laser beam mode is generally not used much since it can’t penetrate the material. The laser beam in this mode has lesser power density, thus no plasma creation. Due to this, the beam is not energized enough to go deeper into the surface and offer a deep weld. Hence, this laser mode is used only to make intricate surface welds and is preferred for applications requiring high-precision surface joints.
What is MIG Welding?
MIG stands for Metal Inert Gas. This technique is often referred to as a traditional welding technique. In MIG welding, an electric current and an additional consumable material help bind the workpieces to be welded together. This traditional welding technique was first invented in the 1940s to weld nonferrous metals.

MIG is a subtype or a sub-process of GMA (Gas Metal Arc) Welding in which the intended workpieces are joined together with the help of a weld-current and a filler material (additional metal used). The gas used in this type of welding is either an inert gas, helium, argon, nitrogen, or a combination of these.
This welding technique is best for non-ferrous metals such as copper, titanium, magnesium, and their alloys. But, as advancements have been made, it works fine for some other metals, such as aluminum.
This traditional welding process demands proper precautions and safety procedures from the welder to ensure a safe welding process. The metals to be welded do not create much mess on the surface; hence the formed workpiece is often neat and clean, but not more than the laser welding finish. (Find a detailed comparison between Laser and MIG further in the article).
This welding technique sometimes results in deeper penetration or incomplete penetration due to exceeding current flows.
You may now know about the welding process but might be wondering where that inert gas is used in the welding process. How does a current stream join two metals? To understand the details, let’s dive deeper into the technical process that happens in the name of MIG welding.
MIG Welding Technique
MIG welding will utilize a lot of electricity and current for its successful application on the workpiece. A short circuit phenomenon occurs between a negative cathode and a positive anode. The additional consumption material, the electrode wire, acts as a positive anode. While the parent metal or workpiece, which is to be welded, acts as a negative cathode. An electric arc is established between these two weld materials, referred to as a short circuit. This established electric art helps in melting the electrode wire (the additional filler material). Then, this melted material gets deposited between the workpieces to be welded together. This melted filler acts as a binder after it cools and solidifies, resulting in the fusion of two workpieces as a weld.
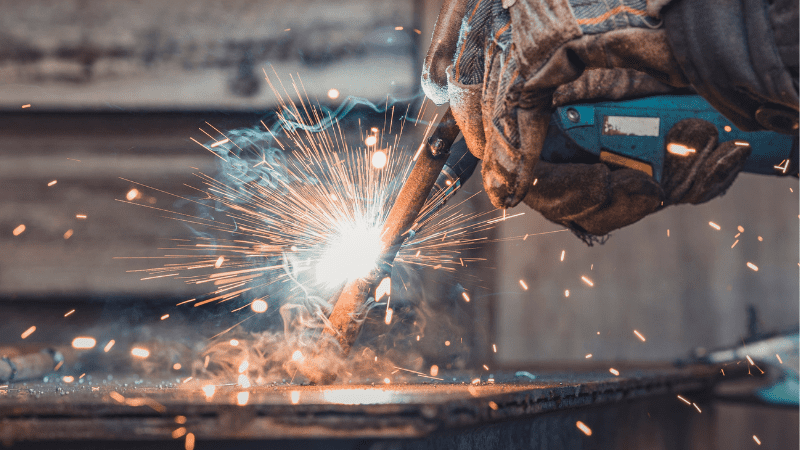
The inert gas here actually works as a shielding gas to protect the weld pool. It helps stop the melted filler material from reacting with the nitrogen or oxygen in the environment or metal areas. Suppose a shielding inert gas is not used. In that case, it will result in hole creation due to the reaction between material and oxygen, causing an excessive spatter, due to which the finishing of the workpiece can get affected.
Laser Welding vs. MIG Welding: Actual Visible Differences
Now that you’re already aware of how laser welding and MIG welding work, let’s know the primary differences between these two to see which one works best for which application. Below we have created a comparison table for you to understand better:
Laser Welding | MIG Welding |
Metals can be welded directly without any prior preparations | Traditional and old technique |
Suitable for thin materials with <1mm thickness | Works fine for metals with thickness >1mm |
Gives a Smooth and neat finish | Gives an okayish look |
Fast welding speed | Relatively slower welding speed |
Doesn’t require additional surface cleaning | Requires surface cleaning to acquire an equally neat look |
Easy to operate | Complex process and requires more attention |
No additional consumable material needed | Needs additional consumption of filler metal |
Makes use of highly concentrated heated laser | Makes use of electric current to weld |
Expensive procedure | Comparatively affordable |
Equally efficient for a variety of metals | Recommended for non-ferrous, works fine for other metals |
Metals can directly be welded without any prior preparations | Metals require pre-hand cleaning to make them free of possible contaminants |
Can be used for workpieces in overheld or vertical position | It doesn’t work well if the workpiece is in a vertical position due to the liquidity of the melting filler |
High depth to width weld ratio | Low depth to width weld ratio |
Less heat and energy emission | High heat and energy emission |
Safe to use due to the extremely focused laser beam | Can be dangerous and cause burns due to vulnerability to heat |
Little to no damage to the workpiece | Possible workpiece distortion in heat affected zone due to heat transfer |
Suitable to weld luxury items | Only to make general welds |
Best to use in inaccessible places | Best for open surfaces |
In the above table, we have laser welding compared to MIG welding. This comparison allows you to better understand which mode to use in your welding tasks. One prominent drawback of laser welding is that it is expensive, but note that the investment is worth it. However, if the workpiece material is compatible with MIG welding, it can also give good results. Thus, laser welding will not be a good option if the price is concerned more over the finish. However, to weld intricate materials such as luxury ornaments, using MIG weld will only result in a weak and poor finish. Make the best decision based on your discretion.
Pros and Cons of Laser Welding
No doubt, the laser is an advanced welding technology, but it has drawbacks that often are not given proper attention. Let’s have a look at a visible list of pros and cons for this technique:
Pros of Laser Welding
Here’s a list of advantages of laser welding:
- It gives an aesthetically neat look
- Best to use in applications where hygiene is concerned, such as medical equipment
- Results in a productive and robust weld
- Helpful to use in places where humans cannot intervene (inaccessible human areas)
Cons of Laser Welding
Here is a list of disadvantages of laser welding:
- Expensive as the laser welding system is costly
- Lesser gap tolerance
Pros and Cons of MIG Welding
Although MIG welding is a pretty old method compared to laser welding, it comes with its list of benefits. Let’s take a look at the pros and cons of this technique:
Pros of MIG Welding
Here is a list of advantages of MIG welding:
- Provides solid and long-lasting welds
- Lesser splatter if the process is done right
- Budget-friendly
Cons of MIG Welding
Here is a list of disadvantages of MIG welding:
- Susceptible to contamination and thermal deformation
- The material requires sheer maintenance
- Dangerous due to heat transfer thus requires protection
Laser vs. MIG Welding: Which One is Better?
Now comes the final part, and it’s difficult if you’re new to the welding realm and don’t know which one to choose.
When choosing a welding technique, we recommend you dive a little deeper into the details and ask yourself a few questions:
- What material are you going to weld?
- In which application will the workpiece be used?
- Are you concerned about the aesthetic looks of the material?
- How much budget do you have?
Once you get an answer to these questions, compare them with the above-provided differential table between laser and MIG welding. For example, if the metal and application will be some kind of jewelry, use laser welding. If aesthetic looks aren’t a concern and you want a budget-friendly process, go for MIG welding. Similarly, dive deeper into the details, research your material, learn about the welding procedures, and choose depending on your conditions.
Conclusion
Laser welding and MIG welding are two popular welding methods. Both have their advantages and disadvantages. If you’re unsure which one to choose for your project, contact us for an instant quote. Baison is one of the leading fiber laser machine manufacturers in China. We can help you decide which welding method is best for your needs.