In this article, we’ll break down the science of laser welding aluminum alloys, offering valuable insights into the challenges, techniques, and best practices. Prepare to unlock the full potential of laser welding technology in your business endeavors!
What Is Laser Welding?
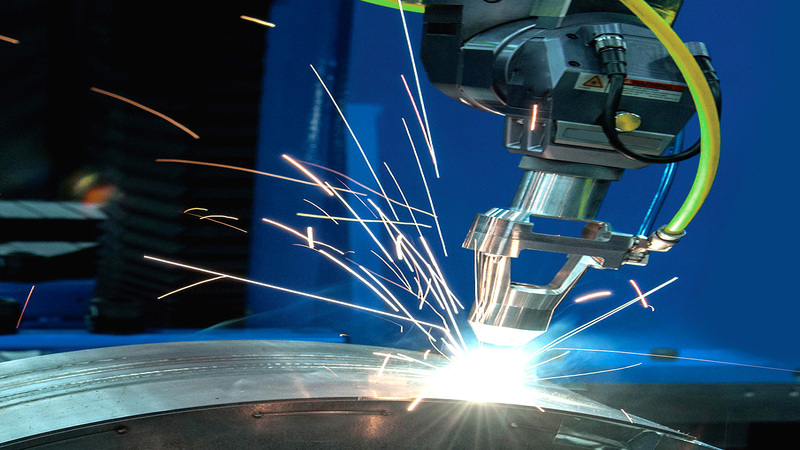
Laser welding, a state-of-the-art joining technique, has become an indispensable asset for businesses worldwide. It elevates their metal-working capabilities. Moreover, harnessing highly focused beams of light generates the required heat to melt and bond metals, resulting in durable, high-quality joints.
Additionally, the adaptability of laser welding extends across various sectors, such as automotive, aerospace, electronics, and medical devices, making it an integral part of modern manufacturing processes.
Laser welding presents many benefits for businesses operating in these industries over conventional methods. This technology minimizes heat exposure, reducing material deformation and ensuring superior end products.
Moreover, laser welding promotes production automation, effectively cutting labor costs and expediting processes. The ability to accommodate intricate designs and patterns also broadens the scope of product innovation.
By incorporating laser beam welding into their manufacturing repertoire, businesses can stay ahead of the competition and streamline their production processes.
What Is the Basic Process of Laser Welding?
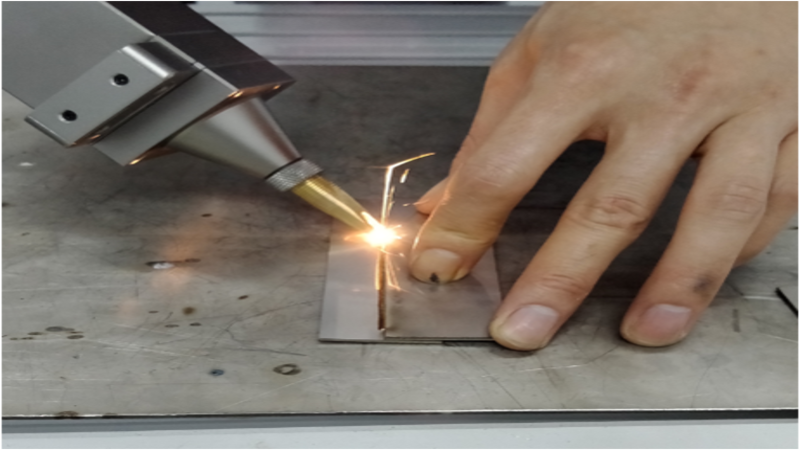
- Laser Generation: A laser source creates a highly focused beam of light, initiating the welding process. It is also sometimes referred to as electron beam welding.
- Beam Delivery: Optical components like mirrors and lenses guide the laser beam toward the workpiece.
- Focusing: The laser beam concentrates all the energy on a small area of the material.
- Melting And Fusion: The heat melts the material at the joint, forming a molten pool that fuses the metal components.
- Cooling And Solidification: As the laser beam moves along the joint, the molten pool cools and solidifies, creating a strong and durable weld.
- Gas Shielding: An inert gas, such as argon or helium, helps protect the weld area from oxidation and contamination.
- Process Monitoring: Sensors and cameras monitor the welding process in real time, ensuring consistent quality and detecting potential defects.
What Is Aluminum Alloys?
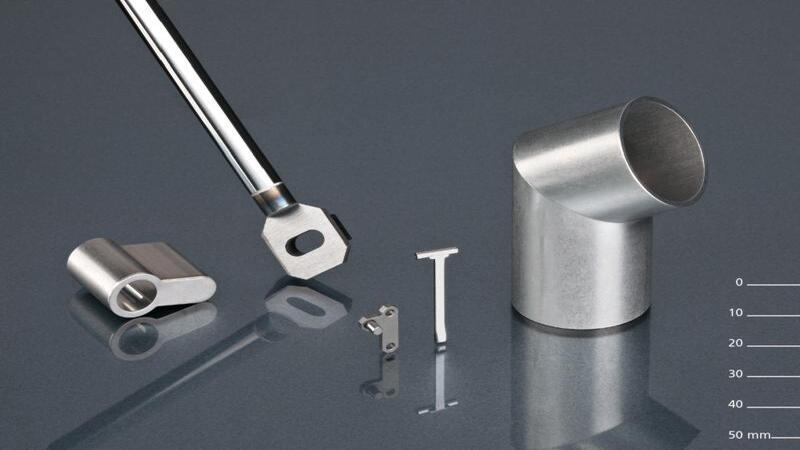
Aluminum alloys are specifically engineered materials created by combining aluminum (Al) with other metallic elements. The most common elements include copper, magnesium, silicon, and zinc. Businesses often use this process to enhance the base metal’s properties.
As a result, they can create versatile aluminum alloys with tailored characteristics that are invaluable for businesses across various industries.
Properties:
- Weight advantage: Aluminum alloys are recognized for their low density, providing significant weight savings in industries like automotive and aerospace, where reducing weight is a critical concern.
- Corrosion protection: The natural oxide layer on aluminum alloys offers superior corrosion resistance, ensuring lasting performance and minimal maintenance in diverse environments.
- Impressive strength-to-weight ratio: Aluminum alloys deliver exceptional strength while maintaining a lightweight profile, making them the material of choice for structural applications demanding both strength and minimal weight.
- Conductive properties: With outstanding thermal and electrical conductivity, aluminum alloys are ideal for heat exchangers, electrical components, and power transmission applications.
- Ease of fabrication: Aluminum alloys exhibit excellent machinability and formability, enabling manufacturers to create intricate shapes and designs easily.
- Eco-friendly option: Aluminum alloys contribute to sustainable business practices by being recyclable without losing their properties, promoting a circular economy, and minimizing waste.
Types of Aluminum Alloys
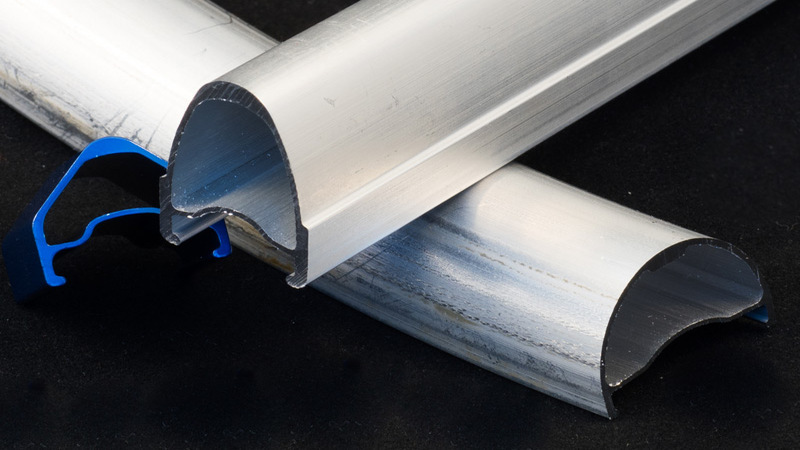
The laser welding industry works around different types of aluminum alloys for their distinct characteristics and applications. The most frequently used aluminum alloys for laser welding are from the 1000, 2000, 3000, 5000, and 6000 series:
1000 Series (Pure Aluminum)
These alloys have the highest aluminum content (over 99% purity) and exhibit excellent corrosion resistance, electrical conductivity, and formability. However, their low strength makes them less suitable for structural applications. Examples: 1100 and 1350 alloys.
2000 Series (Aluminum-Copper Alloys)
The 2000 series alloys, primarily alloyed with copper, provide high strength and good machinability. However, they are more susceptible to corrosion and may require protective coatings. Hence, these alloys come in super handy for aerospace applications. Examples: 2024 and 2219 alloys.
3000 Series (Aluminum-Manganese Alloys)
Containing manganese as the primary alloying element, 3000 series alloys offer moderate strength, good formability, and excellent corrosion resistance. The common use for this is found in sheet metal applications, such as roofing and siding—for example: 3003 alloys.
5000 Series (Aluminum-Magnesium Alloys)
These alloys combine aluminum with magnesium, increasing strength, excellent corrosion resistance, and good weldability. A good example of its use includes marine applications and other environments exposed to saltwater. Examples: 5052, 5083, and 5086 alloys.
6000 Series (Aluminum-Magnesium-Silicon Alloys)
With magnesium and silicon as the primary alloying elements, the 6000 series offers medium strength, good corrosion resistance, and excellent extrudability. These alloys are widely used in automotive and construction applications due to their versatile properties. Examples: 6061, 6063, and 6082 alloys.
What Is the Best Aluminum Alloy for Laser Cutting?
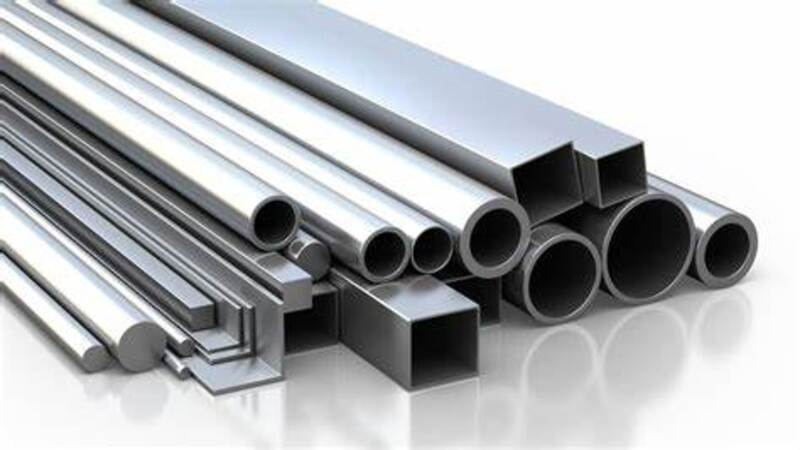
There isn’t a one-size-fits-all answer for the best aluminum alloy for laser cutting, as the ideal choice depends on the specific requirements and application.
However, the 6000 series, particularly the 6061 alloy, is commonly used due to its good combination of weldability, strength, and corrosion resistance. It’s essential to evaluate each project’s specific needs to determine the most suitable aluminum alloy for laser cutting.
Which Method Is Used For Welding Aluminum Alloys?
Several welding methods are used for joining aluminum alloys, each with advantages and applications. Here, we discuss four primary methods and the benefits they offer to businesses:
Gas Tungsten Arc Welding (GTAW) or Tungsten Inert Gas (TIG) Welding
This method uses a non-consumable tungsten electrode and an inert shielding gas to create high-quality, precise welds. GTAW is well-suited for thin aluminum sheets and intricate designs. It is commonly used in the aerospace, automotive, and custom fabrication industries.
Gas Metal Arc Welding (GMAW) or Metal Inert Gas (MIG) Welding
GMAW uses a consumable wire electrode and an inert shielding gas to create welds. This method offers faster welding speed and is more forgiving than GTAW, making it suitable for thicker materials and larger-scale projects. Automotive, construction, and shipbuilding industries often employ GMAW for welding aluminum alloys.
Friction Stir Welding (FSW)
FSW is a solid-state joining process that involves a rotating tool that generates frictional heat, causing the material to plasticize and mix. This method produces strong, defect-free welds and is particularly suitable for joining aluminum alloys. FSW is used in aerospace, automotive, rail, and marine industries, where high-strength welds are crucial.
Laser Beam Welding (LBW)
LBW uses a concentrated laser beam to melt and join materials. It offers high precision, fast welding speeds, minimal heat input, and low distortion, making it ideal for thin materials and complex geometries. LBW is used in various industries, including aerospace, electronics, medical, and automotive, where precision and quality are essential.
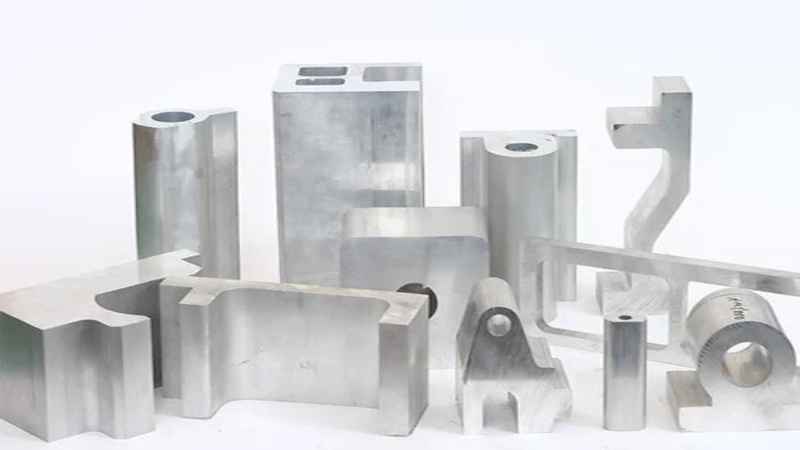
What Is the Problem with Welding Aluminum by Laser Welding?
Laser welding aluminum alloys presents certain challenges and issues businesses need to address to achieve high-quality, reliable welds. Some of these challenges include:
- Thermal Conductivity: Aluminum has a high thermal conductivity, which means heat dissipates rapidly from the welding area. This can make maintaining consistent temperatures and achieving proper fusion challenging, leading to defects and weaker welds.
- Oxide Layer: Aluminum naturally forms a tenacious oxide layer on its surface, with a higher melting point than aluminum. This oxide layer can cause issues during pulsed laser welding, as it may not break down completely and can lead to the formation of inclusions or porosity in the weld.
- Reflected Energy: Aluminum has a high reflectivity, which means a significant portion of the laser energy can be reflected away from the weld area, reducing the efficiency of the welding process. This can be overcome by using specialized laser sources and techniques to minimize energy loss.
- Hot Cracking: Aluminum alloys are susceptible to hot cracking due to their relatively low melting point and the presence of alloying elements. This can lead to the formation of cracks in the weld or heat-affected zone, compromising the joint’s strength and integrity.
- Porosity: Laser welding of aluminum alloys can result in porosity, which occurs when gas bubbles are trapped in the solidifying weld pool. Porosity can weaken the weld and reduce its overall performance. Proper shielding gas selection, joint preparation, and welding parameters can help minimize porosity issues.
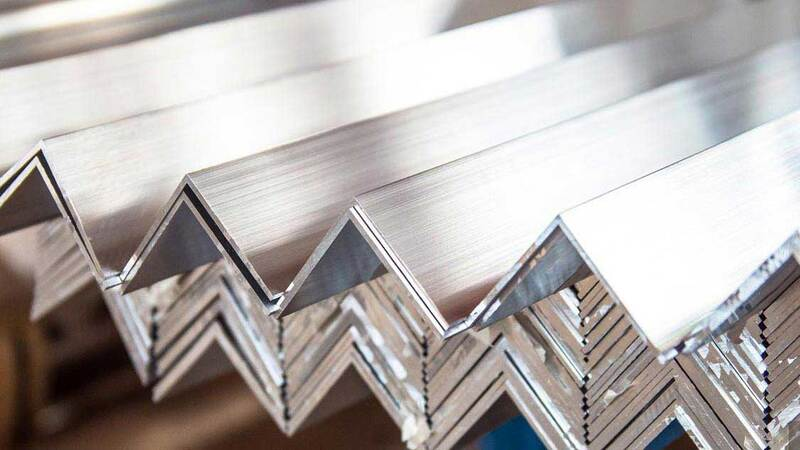
Benefits And Disadvantages Of Laser Welding For Aluminum Alloys
Benefits | Disadvantages |
High welding speed | Thermal conductivity issues |
Narrow, deep welds | Oxide layer interference |
Minimal heat-affected zone | Reflected energy loss |
Low distortion and minimal part warping | Hot cracking susceptibility |
High repeatability and precision | Porosity concerns |
Suitable for complex geometries | Requires specialized equipment and expertise |
Compatible with automation and Industry 4.0 | Potential material limitations |
This table outlines the primary benefits and disadvantages of laser welding for aluminum alloys. By considering these factors, businesses can make informed decisions about the suitability of laser welding for their specific applications and aluminum alloy requirements.
Common Mistakes Made During Laser Welding of Aluminum Alloys and How to Avoid Them
- Inadequate Joint Preparation: Failing to properly clean and prepare the joint before welding can result in a weak, defective weld. To avoid this, ensure the joint surfaces are free of contaminants, such as oils, grease, and dirt, and remove the oxide layer using mechanical or chemical methods.
- Incorrect Laser Parameters: Using inappropriate laser settings, such as laser beam power density, speed, and focus, can lead to various welding defects. To mitigate this, carefully select and adjust the laser parameters based on the aluminum alloy type, thickness, and desired weld characteristics.
- Poor Shielding Gas Selection: Using an unsuitable shielding gas can cause porosity and other weld defects. Choose the appropriate shielding gas, such as pure argon or a helium-argon mixture, based on the specific aluminum alloy and welding requirements to prevent this.
- Improper Fit-up: Poor alignment or gaps between the joint surfaces can result in weld defects or insufficient fusion. To avoid this, ensure the joint surfaces are tightly aligned and clamped together before welding to maintain proper fit-up throughout the process.
- Lack of Welding Expertise: Inexperienced operators may not be familiar with the unique challenges of laser welding aluminum alloys, leading to mistakes and subpar laser welds. To address this issue, invest in training and ongoing education for operators to ensure they understand the intricacies of laser welding aluminum alloys and can apply best practices.
- Inadequate Equipment Maintenance: Neglecting regular maintenance of the laser welding equipment can lead to performance issues and welding defects. To prevent this, establish a maintenance schedule and ensure the laser welding equipment, including the laser source, optics, and cooling system, is routinely inspected and serviced.
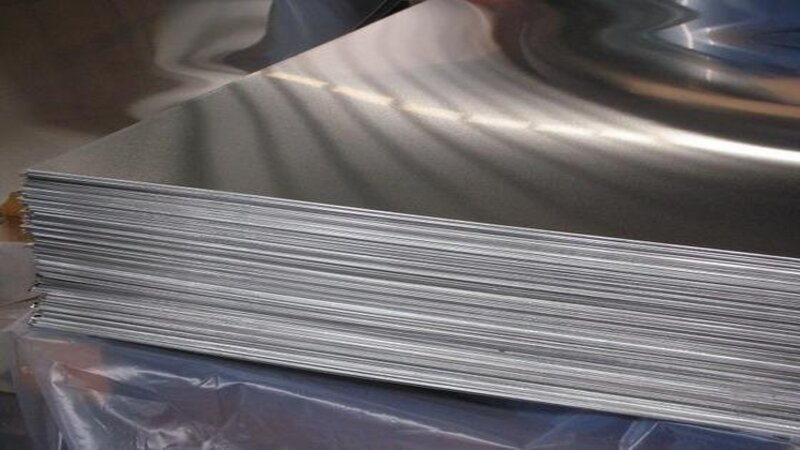
Conclusion
In conclusion, understanding the science behind laser welding aluminum alloys is crucial for businesses that rely on this process for their operations.
By familiarizing yourself with the various types of aluminum alloys, their mechanical properties, and the challenges and best practices associated with laser welding, you can ensure optimal results and avoid common mistakes.
For more information and resources on laser welding and other cutting-edge technologies, be sure to explore our blog section.
Experience Unmatched Welding Excellence with Baison
Baison is committed to providing top-notch laser welding solutions tailored to your business needs. Our state-of-the-art equipment and unparalleled expertise ensure that you receive the highest quality service and support, empowering you to achieve superior results and maintain a competitive edge in your industry.
Let Baison be your trusted partner in navigating the complexities of laser welding aluminum alloys and beyond. Contact us today!