Accuracy matters a lot in today’s manufacturing, and laser cutting has changed the game. But how precise is this tech? To get this, you need to know about laser cutting tolerance—the small differences allowed in cut sizes. This shows how the process balances near-perfect accuracy with its natural limits.
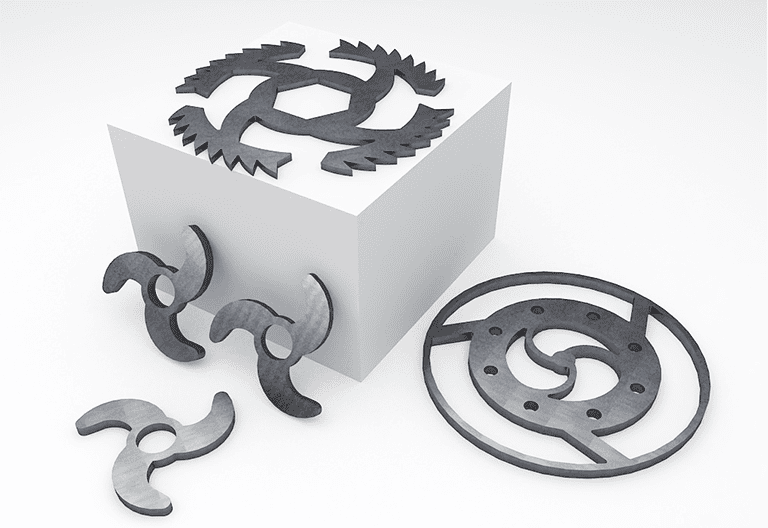
Getting super-precise cuts is key in fields like aerospace and medical gear. Laser cutting helps meet these needs where even a tiny change can matter. Let’s look at laser cutting tolerance and see how it pushes new ideas in exact engineering, shaping the future of the tools and devices you count on.
What is Laser Cutting, and How Does it Work?
Laser cutting is an exact and flexible way to cut or etch many materials, like metals, plastics, wood, and fabrics. The process begins by making a strong laser beam, which can come from a laser diode, CO₂ gas, or fiber optics. This beam then goes to the material using mirrors and lenses, focusing the power on a small spot, often just a few microns wide.
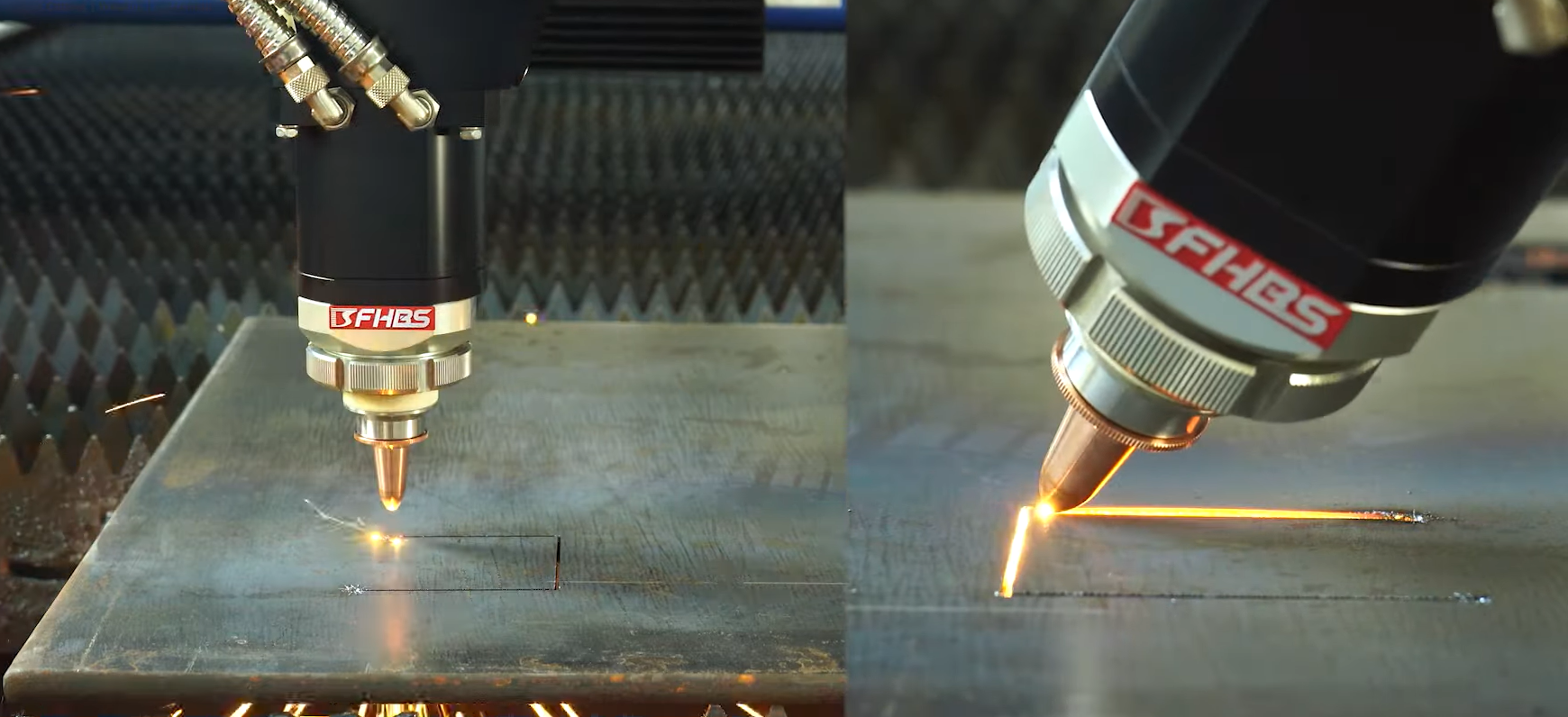
Laser cutting tech began to grow in the mid-1900s. In 1965, the Western Electric Engineering Research Center in Buffalo, New York, built the first useful laser cutting machine, which they used to make holes in diamond dies. British engineers made a breakthrough in 1967 when they introduced laser-assisted oxygen jet cutting for metals. CO₂ lasers found new applications in the early 1970s, as people began to use them to cut non-metal materials like textiles.
In today’s machines, computer software has control over the cutting process. It guides the laser head along the path you want to cut. The laser’s strong energy heats the material until it melts or turns to vapour. This allows you to cut through it with great accuracy. The cut edges are usually clean, so you don’t need to do much more work on them.
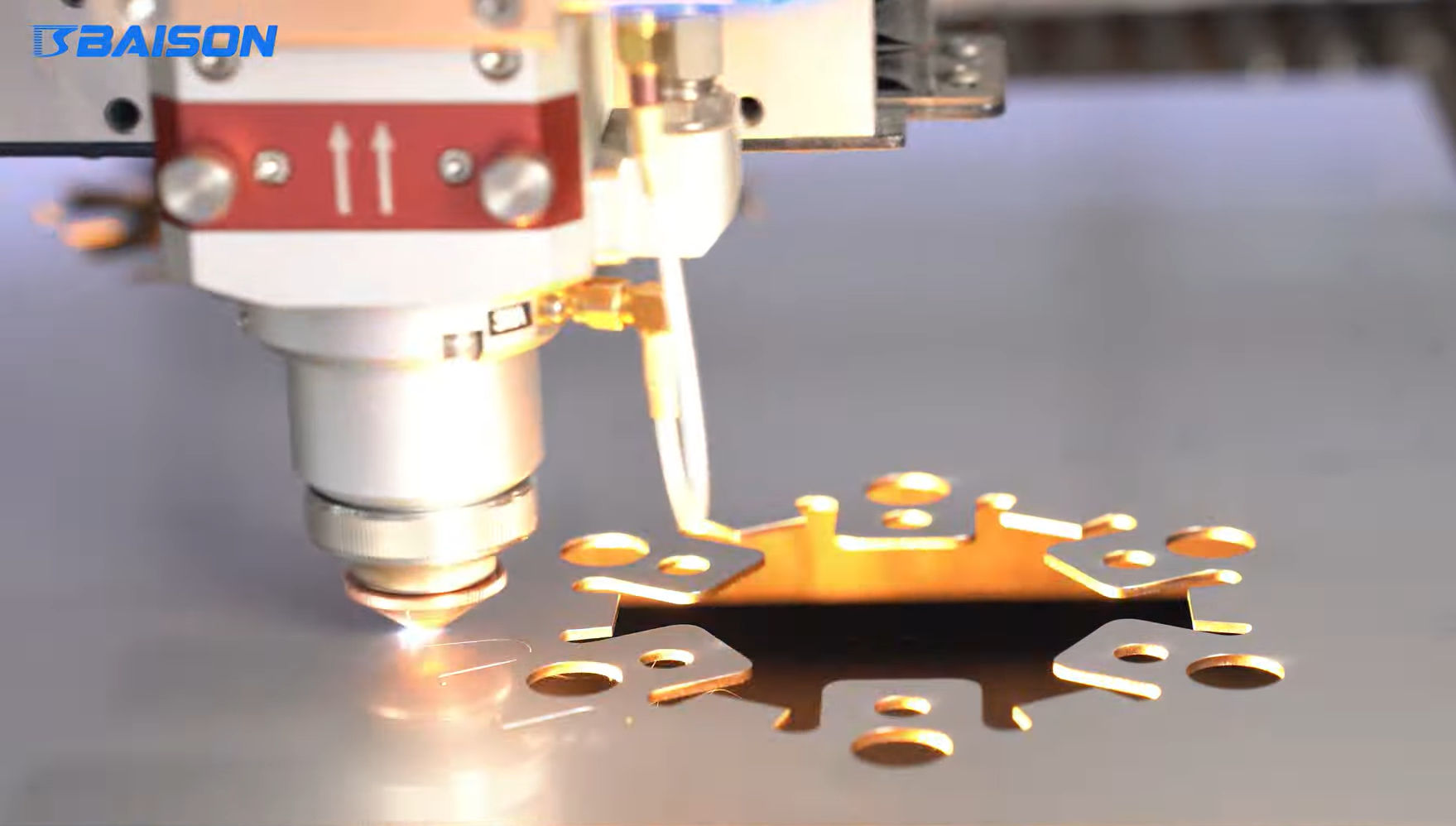
The accuracy and quality of laser cutting depend on many things. These include the kind of laser, how powerful it is, and what the material is like. CO₂ lasers work best to cut non-metal materials such as wood and acrylic. Fibre lasers, on the other hand, do a better job of cutting sheet metal because they have more power and work more.
Laser cutting has a big impact on cars, planes, electronics, and medical tool-making. It can cut complex shapes and designs super, so it’s a key part of today’s manufacturing. Whether you’re making car parts or tiny medical gadgets, laser cutting helps you get the fine details and exactness you need for top-notch products.
Factors Affecting Laser Cutting Tolerance
Dimensional accuracy plays a vital role in manufacturing, making sure parts fit exact specifications. Several factors influence how precise your cuts will be:
1. Laser Cutting Machine Quality: The machine’s precision matters most. Top-notch machines with auto-focus and high-resolution optics give better accuracy. To keep it running well, you need to clean and adjust it often. Use perfect chucks for superior cutting.
2. Material Type and Thickness: Lasers cut different materials in different ways. Metals like steel and aluminium allow clean cuts, but thicker stuff might heat up and bend. Non-metal things like plastics and wood vary in how well they cut based on what they’re made of.
3. Cutting Parameters: The settings you pick, like laser power cutting speed and gas pressure, have a big effect on how the cutting works. Cutting faster might make things less precise, while the right power leads to clean cuts without too much melting or burning.
4. Beam Quality and Focus: A laser beam that’s well-focused with a tiny spot size makes cuts more precise. When the beam isn’t lined up right, or its quality is poor, it can make the cuts less accurate.
5. Thermal Effects: The heat created can warp materials that conduct heat well. To cut down on these effects, manage the heat and use techniques that pulse the laser.
6. Operator Expertise: Your operator skill plays a major role. With experience, you can fine-tune settings, troubleshoot problems, and ensure high accuracy. Proper training is essential to achieve precise results consistently.
7. Environmental Conditions: Ambient temperature, humidity, and air quality can also affect accuracy. A controlled environment helps you maintain consistent cutting performance.
Design Considerations for Laser Cutting
When you’re designing parts for laser cutting, following specific guidelines ensures the quality and strength of your final product. Here are some key considerations to keep in mind:
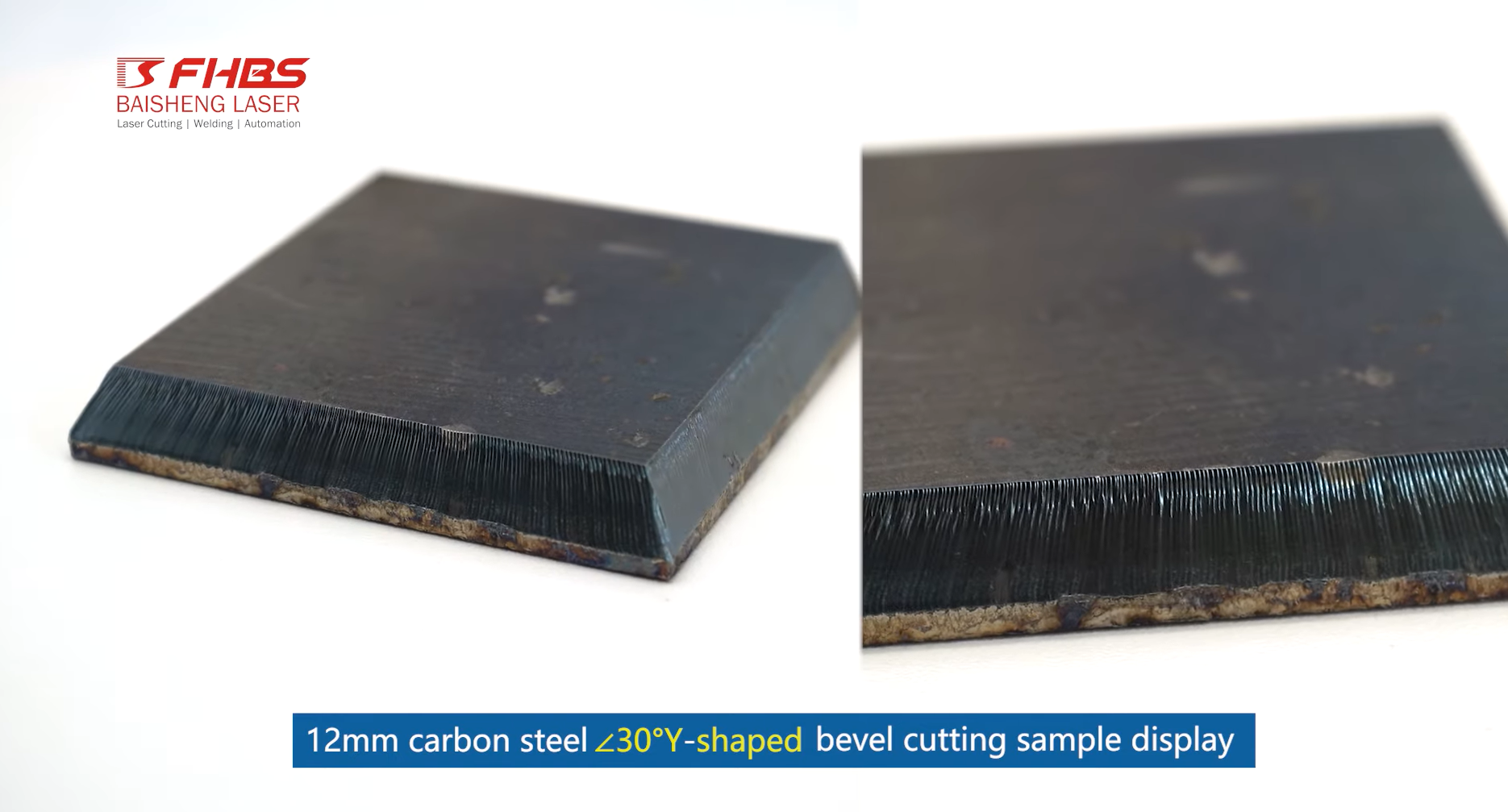
- Hole Placement: Put holes at least 1X their diameter from the part’s edge. This gap helps keep your material strong, stopping it from ripping or warping as it’s cut.
- Slot Placement: Position slots at least 1.5X their width from edges or other features. This extra room prevents weak spots that could cause bending, cracking, or breaking in thinner materials.
- Material Type and Thickness:
- Material Considerations: Different materials react in unique ways to laser cutting. Steel or aluminium needs more power and is cut at a slower pace than acrylic or wood. Make sure you tweak your settings to match the material you’re using.
- Thickness Considerations: Thicker materials can make designs trickier. When you work with thicker sheets, you’ll have to increase hole diameters and widen slots to account for the laser’s kerf (how wide the cut is). Keep this in mind so your parts fit together right.
- Kerf Width: The kerf, or the gap the laser creates when it cuts, changes based on the material and settings you use. It would be best if you thought about this when you design parts to make sure everything fits together. The kerf width falls between 0.1mm and 0.3mm, depending on your laser and material.
- Heat Affected Zone (HAZ): The heat from cut edges can impact the area around the cut, leading to discolouration or changes in the material’s properties. You can minimize this heat-affected zone by tweaking your laser settings or using cooling methods. This will help keep the material’s quality intact.
- Complexity of Design: Laser cutting allows for detailed designs, but complex patterns can increase cutting time and cost. Simplify where possible to maintain efficient production. Cutting out unnecessary details can save time and boost the overall cut quality.
- Tab and Slot Construction: If you’re putting parts together in your design, use tab and slot construction to make it stronger. When you’re creating tabs and slots, think about the kerf and how thick the material is. This helps ensure they fit together without gaps or being too tight.
- Engraving and Marking: When you’re adding engravings or markings, consider how deep and clear you want them to be. Different materials will give you different results, so it’s smart to try it out on a test piece first. This helps you find the right mix of power and speed to get clean, easy-to-read markings.
Laser Cutting Tolerances and Standards
Laser cutting tolerances are critical for ensuring precision and quality in manufacturing. Tolerances define the allowable difference between the actual cut and the intended maximum dimension of the part. To meet the required specifications, the part’s dimensions must fall within the upper and lower limits set by the design.
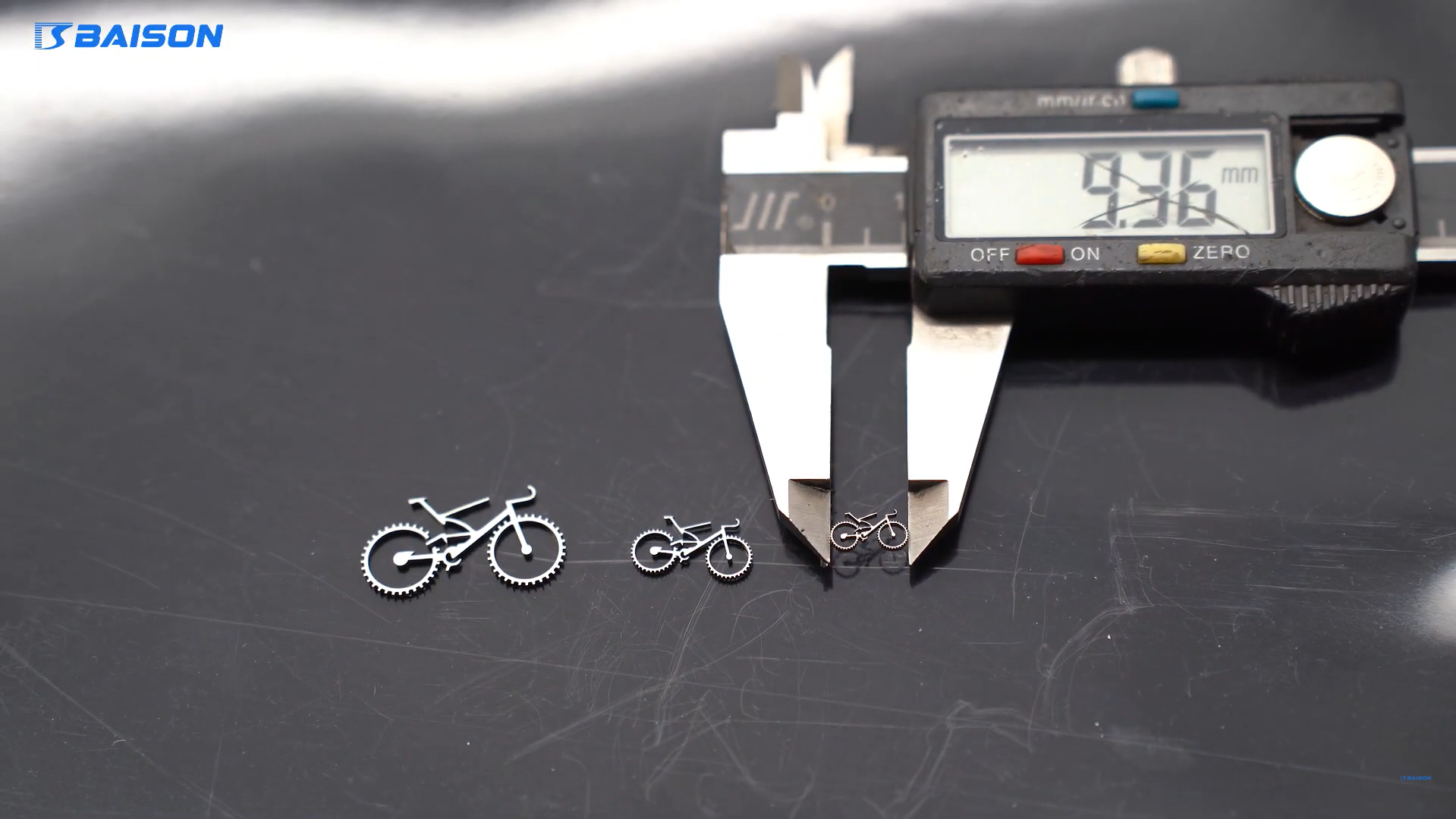
Understanding Laser Cutting Tolerance
Laser-cutting tolerance is the most variation allowed between a cut part’s measurements and the original design. It impacts how precise the part is and plays a crucial role in figuring out if it will fit with other parts. Tolerances set the acceptable limits of change in a part’s actual dimensions. They spell out how much the real measurement can be different from the intended size. This difference is shown as a range with an upper and lower limit.
- Dimensional Tolerances: These show how much a part’s size can change. Think about a hole that should be 10 mm wide. It might have a wiggle room of ±0.1 mm. This means the actual width can be anywhere from 9.9 mm to 10.1 mm.
- Geometric Tolerances: These keep tabs on the shape, direction, and spot of features on the part. Some examples are how flat, round, or parallel something is.
General Manufacturing Tolerances
Manufacturing tolerances often stick to rules like ISO 2768. This gives guidelines to set size limits in technical drawings. These rules make sure things stay the same and work well across different ways of making stuff.
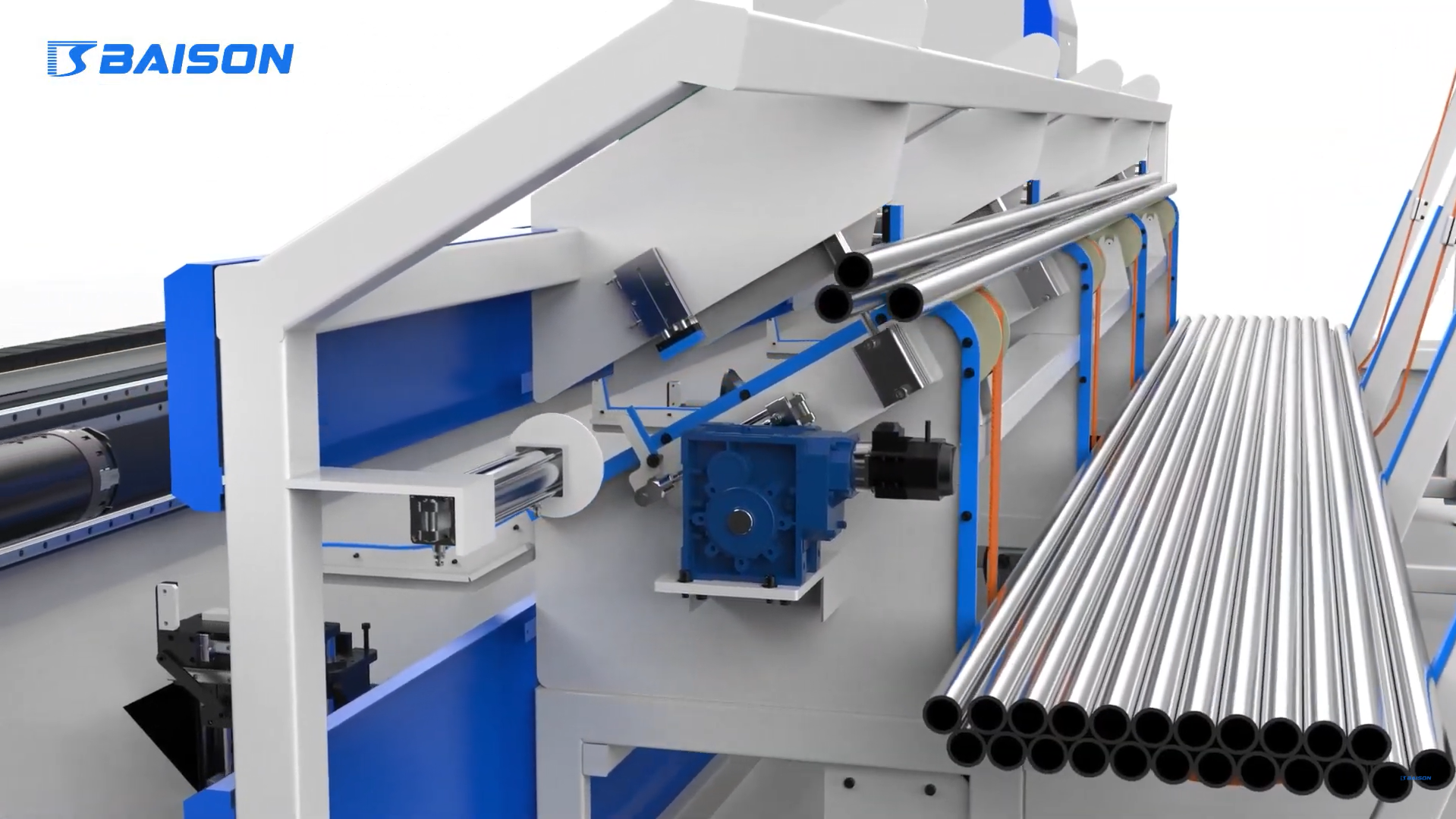
Factors Influencing Laser Cutting Tolerances
Many things can impact how precise laser cutting can be:
- Material Type: Metals, plastics, and composites each react when cut by lasers.
- Material Thickness: Cutting thicker stuff needs more control to stay precise. Different materials change the width of the cut.
- Laser Cutting Machine: How accurate the machine is sets the limit on how tight your cuts can be. Better machines can cut more precisely.
- Design Complexity: Fancy designs need more exact cuts to meet the required precision.
- Cutting Settings: Things like laser power, speed, and focus change how precise the cuts are. To get accurate cuts, you need to fine-tune these settings.
Typical Laser Cutting Tolerances
There’s no one-size-fits-all tolerance standard for all materials. However, here are some general rules of thumb based on how thick the material is:
- Up to 0.5 mm: ±0.05 mm
- 0.5 mm – 2.0 mm: ±0.1 mm
- 2.0 mm – 5.0 mm: ±0.15 mm
- 5.0 mm – 10.0 mm: ±0.2 mm
- 10.0 mm and above: ±0.3 mm
These tolerances are a guide and can change based on the material, machine, and project details. You might need to make changes depending on your specific needs.
Getting Precision with Laser Cutting Machines
Getting high precision with plasma cutting machines depends on several key factors, from the laser type to the operator’s skill. Let’s look closer at these points:
UV Laser Machines for Precise Cuts
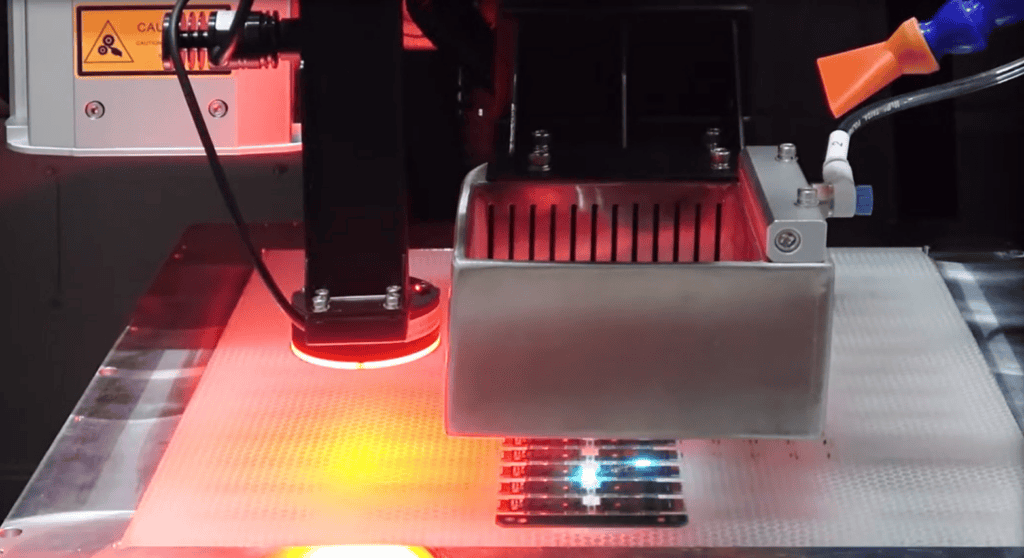
UV laser machines can make precise cuts for small parts. The UV lasers’ shorter wavelength creates a smaller spot size, which allows for finer cuts and tighter tolerances. UV lasers work great for electronics and medical device manufacturing, where tiny details and high precision matter a lot.
Inspection of Precision Parts
It would be best if you did visual and dimensional checks to make sure your precision parts are up to spec. Visual checks look at surface quality, edge finish, and any defects you can see. Dimensional checks confirm that the parts have the right tolerances. These checks are based on what the customer wants in detail to make sure each part is good enough.
Practical Tips to Achieve Precision
- Machine Calibration: To keep your laser cutting machine precise, tune it up often. Check if the laser lines up right, the lens is in good shape, and the whole system works well.
- Material Preparation: Clean your materials well to get rid of any dirt. When both your tools and materials are spotless, you’ll get cleaner, sharper cuts.
- Parameter Optimization: Change the laser’s power, speed, and focus to match your material and how thick it is. Look at trusted sources and good online guides to find the best settings for your job. This is tricky work – even a tiny mistake can cause problems.
- Focus Adjustment: Check that the laser has the right focus on the material’s surface. Tools like focus gauges can help you get the focus right for more precise cuts.
- Maintenance and Troubleshooting: Keep up with regular maintenance on your laser cutting machine. This includes cleaning the lens and nozzle. If you spot any problems, fix them to avoid downtime and keep your machine working well.
Common Misconceptions About Laser Cutting
People often misunderstand what laser cutting can and can’t do. Let’s clear up some of these mix-ups:
Misconception 1: It’s for Thin Materials
You might think laser cutting works on thin materials, but that’s not the case. It’s great for thin sheets, sure, but with the right tools, it can cut through thicker stuff, too.
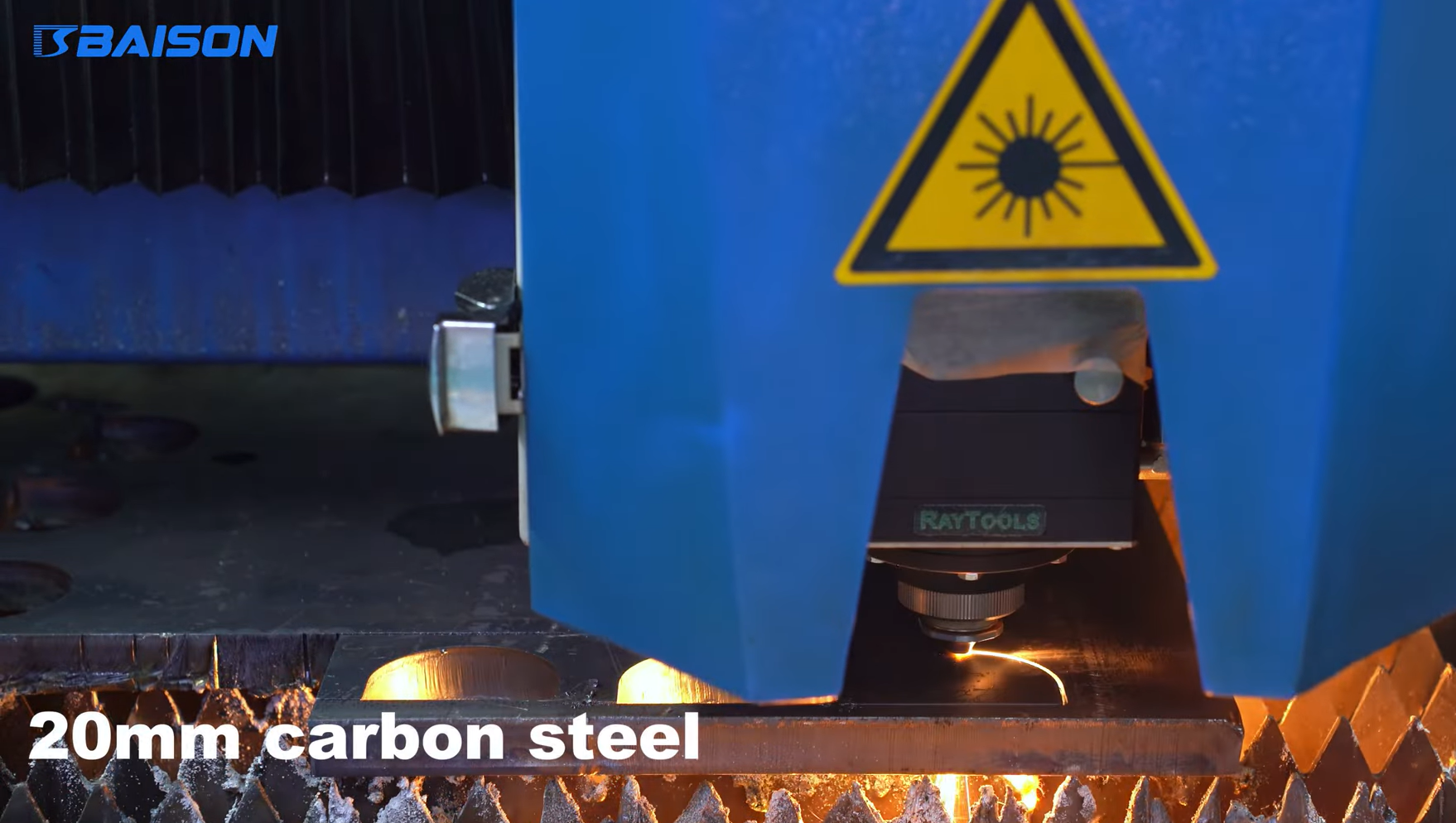
Thicker Materials: Today’s machines, like powerful CO2 or fiber laser, can cut materials several centimetres thick. For instance, industrial laser cutters can handle metals like steel and aluminium up to 25 mm thick or more.
Material Versatility: Beyond metals, you can cut thicker non-metal materials such as wood, acrylic, and composites. You need to adjust the laser power, speed, and focus to match the material.
Misconception 2: Slow Process
Some folks think laser cutting takes a long time. In fact, it can outpace traditional methods in many situations.
Speed and Productivity: Laser cutting doesn’t make contact, so no physical tools wear out or need changing. You can keep cutting without stopping.
Detailed Patterns: To cut complex patterns, laser cutting often beats mechanical methods. The laser’s accuracy lets you make detailed cuts in one go.
Automation: Many new laser systems use CNC (Computer Numerical Control) to optimize cutting paths and cut down on manual tweaks, making the process even faster.
Misconception 3: For certain Materials
Another common mistake is thinking laser cutting works on certain materials. In truth, it has wide applications and can cut many different substances.
Metals: Laser cutting works well on various metals, including steel, stainless steel, aluminium, brass, and copper. You need to tweak the settings for each metal type.
Non-metals: It’s also good for materials like plastics, wood, glass, ceramics, and fabrics. Different laser types (such as CO2 for non-metals and fibre for metals) are used depending on the material.
Composites: You can cut composite materials too. Laser cutting handles multiple layers of different materials in one go, which gives it a big edge in industries like aerospace and cars.
Misconception 4: It Costs Too Much
Laser cutting might look pricey at first because the machines are expensive, but the process is more budget-friendly than you might think.
The precision of laser cutting cuts down on wasted material, which can save you money over time. It also needs less manual work and fixes, which brings down overall costs. Plus, laser cutting’s quick and efficient nature helps boost production, making it a good choice for big projects.
The Importance of Maintenance for Laser Cutting Precision
Like many industrial operations, regular upkeep plays a crucial role in ensuring your laser-cutting machine performs at its best and cuts with precision. Essential maintenance tasks include cleaning the laser head to get rid of dust and debris, which helps to prevent the beam from scattering and keeps cutting efficient.
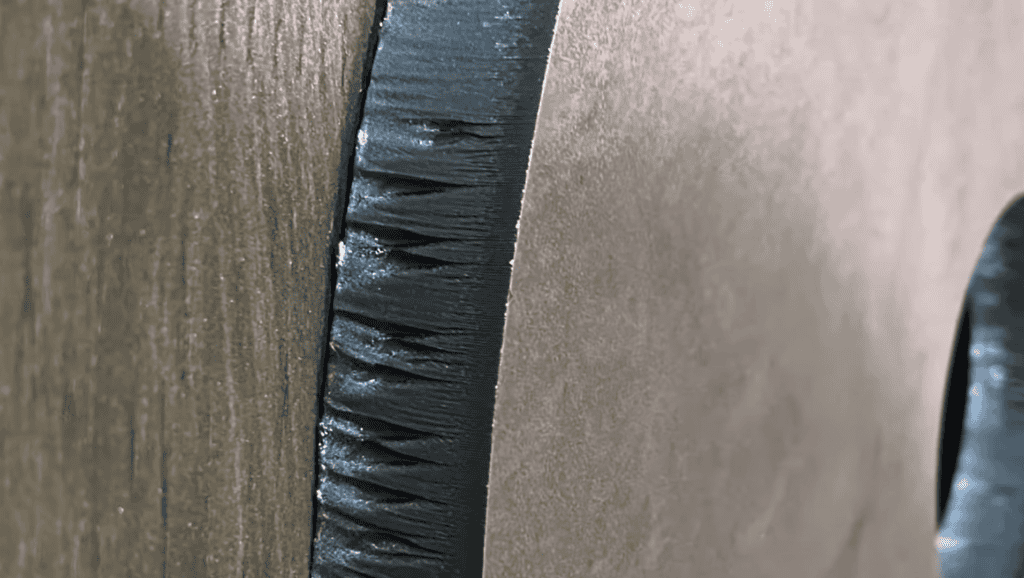
Checking and switching out worn parts, such as nozzles and lenses, on a regular basis lets you steer clear of uneven cuts and long periods of downtime. Also, making sure the laser beam is aligned allows for accurate cuts and helps you avoid poor-quality results.
Not taking care of your equipment has a big impact on how well it works. It can make cuts less accurate, cause machines to break down more often, and cost more money for fixes and new parts. To avoid these problems, set up a regular schedule to check, clean, and take care of your machines, as suggested by the maker.
Make sure your workers know how to take care of the machines and use good-quality parts when replacing old ones. Doing these things helps keep machines running well, keeps cuts precise, and gets more work done.
Conclusion
Getting precise cuts with lasers depends on how good your cutting machine is, what kind of material you’re cutting and how thick it is, and careful planning of your designs. That’s why knowing about laser cutting tolerances and standards is key for making things with high precision.
When you have the right tools, know-how, and upkeep, laser cutting can deliver tight tolerances and accurate outcomes. But it’s a tricky process. Without the proper gear and skills, things can go wrong fast.
That’s why at BaisonLaser, we provide top-notch laser cutting services to meet your accuracy needs. Our laser-cut parts are as precise as human hair, which works great for detailed tasks on smaller items. To get the most exact bulk jobs with low tolerances, get in touch with Baison Laser Cutting Services now!