Understanding Laser Cutting and Its Application on Sheet Metal
Laser cutting technology, with its precise and efficient method, utilizes intricate cuts made by diode laser or state-of-the-art kilowatt-level lasers to slice through sheets of various materials. This advanced technology offers a multitude of advantages over traditional cutting techniques, making it a preferred choice for cutters. Laser cutting technology is capable of creating narrow kerf, allowing for more intricate cuts on materials ranging from mild steel to reflective metals.
What is Laser Cutting?
Laser cutting is a precise and efficient manufacturing process that utilizes high-powered laser beam to melt, burn, or vaporize materials, including sheet metal. As a tool to cut and shape materials, laser cutting has become widely popular in industries such as automotive, aerospace, and electronics for the fabrication of sheet metal. It offers several advantages over traditional cutting methods and is commonly used in engraving as well.
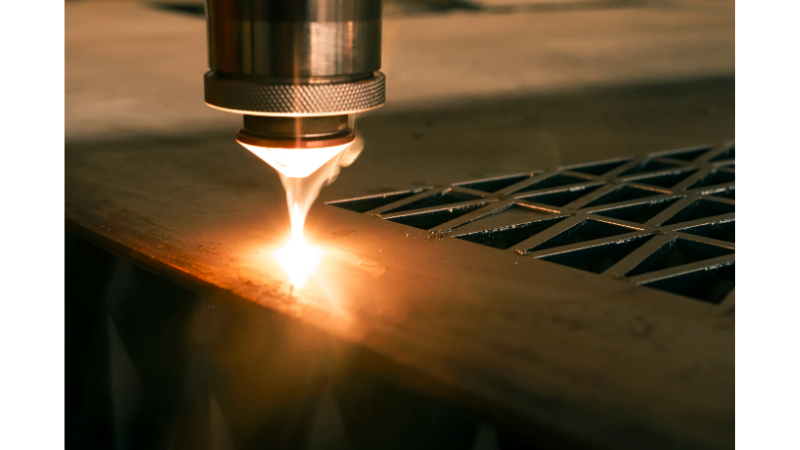
Laser cutting works by focusing a laser beam onto a specific point on the sheet metal parts, which melts or vaporizes the material. This process is guided by a computer-controlled machine that follows a predetermined cutting path. The result is a clean and accurate cut with minimal heat-affected zone.
Why is Laser Cutting Preferred for Sheet Metal?
Let’s explore the reasons and applications of laser cutting in sheet metal fabrication.
- Versatility: Laser cutting can be used on a wide range of sheet metal materials, including stainless steel, aluminum, brass, and copper. It can also handle different thicknesses, from thin foils to thicker plates. This versatility makes laser cutting suitable for a variety of applications in industries such as manufacturing, construction, and automotive. Why not see this article for details?
- Precision: Laser cutting processes offer high precision and accuracy. The laser beam can be controlled to cut intricate shapes and patterns with tight tolerances. This level of precision is particularly important in industries where precise cuts and tight tolerances are required.
- Efficiency: Laser cutting offers efficient production processes due to its speed and automation capabilities. The laser beam can cut through sheet metal at a high speed, reducing production time and increasing productivity. This is especially beneficial in industries where large volumes of sheet metal need to be processed.
- Minimal Material Waste: By using focused laser beams in the heat affected zone, laser cutting minimizes material waste during the fabrication process. This leads to cost savings and improved sustainability.
Types of Lasers Used in Sheet Metal Cutting
CO2 lasers and fiber lasers are the two main types of lasers used for cutting sheet metal. Each type has its own advantages and is suited for different applications.
CO2 Lasers
CO2 lasers are a common type of laser used in sheet metal cutting. They generate a high-powered laser beam flame using a mixture of carbon dioxide, nitrogen, and helium gases. CO2 laser cutting machine has a wavelength of around 10.6 micrometers, which is well-suited for cutting non-reflective materials like stainless steel and aluminum. These lasers are known for their excellent beam quality and high cutting speeds, making them suitable for various sheet metal applications.
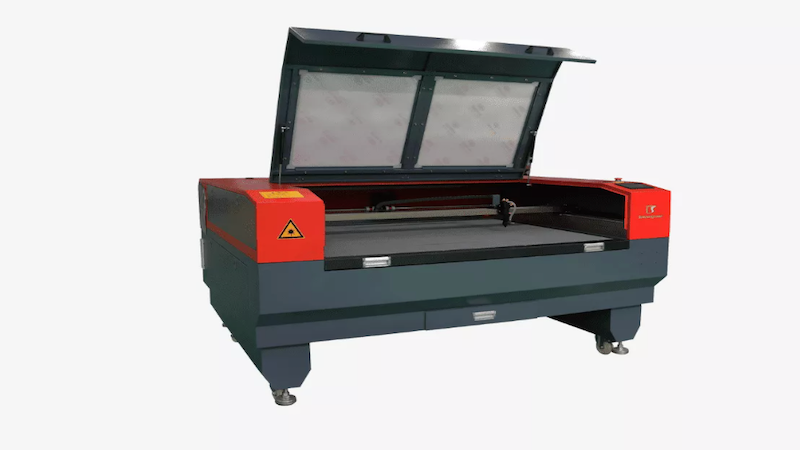
Fiber Lasers
Fiber Lasers: Fiber lasers have gained popularity in the manufacturing industry for sheet metal cutting. Fiber laser machine utilizes glass fibers to amplify the laser beam, resulting in higher laser power and intensity. A fiber laser cutter uses a solid-state laser source and has a wavelength of around 1.07 micrometers, which is highly absorbed by metals, including reflective materials like copper and brass. This makes fiber lasers ideal for cutting a wide range of sheet metal materials. They offer fast cutting speeds, high precision, and energy efficiency, making them a preferred choice for many industrial applications.
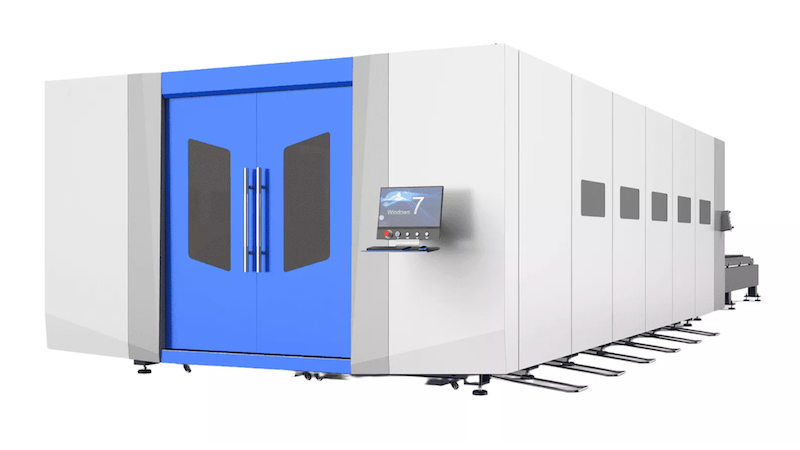
Choosing the Right Laser for Your Needs
When selecting a laser for sheet metal cutting, several factors come into play. These include the type and thickness of the material, desired cutting speed, level of precision required, and overall production needs. The CO2 laser is often preferred for thicker materials and applications that require high cutting speeds, while fiber lasers excel in cutting thin sheets to medium-thickness materials with precision.
When choosing sheet metal laser cutting, it is crucial to consider the specific requirements of the project. This will help determine the best laser type for working with metals and engraving. It is also important to factor in maintenance, initial investment costs, and operational costs associated with different lasers before making a final decision on which laser will be suitable for cutting the workpiece based on its material thickness.
The Process of Laser Cutting Sheet Metal
The process of laser cutting sheet metal involves three main steps: preparing the sheet metal, setting up the laser cutter, and executing the cutting process. Here’s a brief overview of each step.
Preparing the Sheet Metal
Before laser cutting can begin, the sheet metal needs to be properly prepared. This involves cleaning the surface to remove any dirt, dust, or contaminants that could interfere with the cutting process. Measure and mark the desired cut path on the sheet metal. Additionally, the sheet metal may need to be flattened or straightened to ensure it is flat and uniform, which helps achieve accurate and precise cuts.
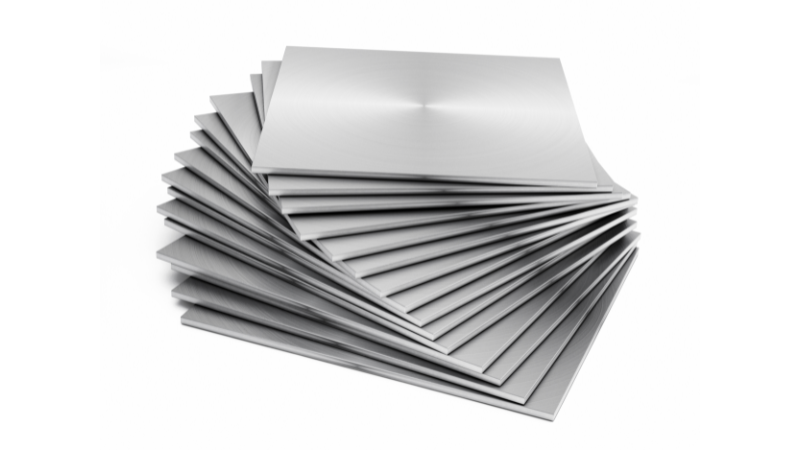
Setting up the Laser Cutting Machine
Material Selection: The appropriate laser cutting parameters, such as power, speed, and focus, need to be determined based on the type and thickness of the sheet metal being used. Different materials require different settings to achieve optimal cutting results.
CAD Design Import: If the desired design or pattern for laser cutters or laser engraving on metal workpieces is not already programmed into the machine, it needs to be imported from Computer-Aided Design (CAD) software. This allows the machine to follow the specific cutting path and produce the desired shape or design.
Machine Calibration: The laser cutting machine needs to be calibrated to ensure accurate cutting. This involves aligning the laser beam and verifying the focus to achieve precise cuts. Calibration may also include adjusting the laser cutting speed and laser power settings based on the specific requirements of the project.
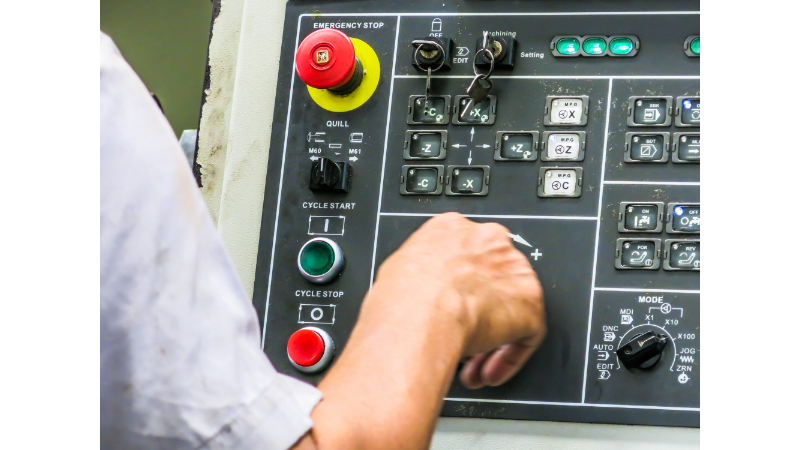
Executing the Cutting Process
Material Clamping: The sheet metal is securely clamped onto the cutting bed or table to prevent movement or vibration during the cutting process. This ensures that the laser light accurately follows the programmed cutting path.
Laser Cutting: The laser cutting machine is activated, and the laser beam is directed onto the sheet metal at the predetermined cutting path. The laser light heats and melts or vaporizes the material, creating a clean and precise cut. The machine’s computer numerical control system ensures that the laser follows the programmed cutting path with high accuracy.
Cooling and Removal: After the cutting process is complete, the sheet metal may need to be cooled to prevent warping or distortion, and the laser cutters need to be coole/d to prevent reduce the longevity of the machine and the quality of their cuts. Cooling can be done using air or water. Once cooled, the cut pieces can be removed from the machine and further processed or used for their intended purpose.
Laser cutting is widely used for various applications due to its precision and versatility. It offers advantages such as faster production times, minimal material wastage, and high-quality cuts. Whether you need intricate designs or simple shapes, laser cutting can provide efficient results for your sheet metal projects.
Safety Measures in Laser Cutting Sheet Metal
This section highlights important safety precautions that should be followed during laser cutting, especially when working with metals. It is important to consider the material thicknesses and radius when determining the appropriate settings for the laser. Following these precautions will help ensure a successful result.
Handling the Laser Cutter
- Training and Certification: Operators should receive comprehensive training on how to safely operate the laser cutter. This includes understanding the machine’s controls, safety features, and emergency shutdown procedures. Certification programs can help ensure that operators have the necessary knowledge and skills to operate the typical laser cutter safely.
- Personal Protective Equipment (PPE): Operators must wear appropriate PPE during cutting operations to protect themselves from potential hazards. This typically includes safety glasses or goggles to shield the eyes from laser radiation, as well as gloves and protective clothing to safeguard against sparks, hot metals, and potential chemical exposure in the cutting process.
- Machine Maintenance: Regular maintenance and inspections of the laser cutter are essential for safe operation. This includes checking for any loose or damaged parts, ensuring proper ventilation, and keeping the machine clean to prevent the buildup of debris or flammable materials.
Workplace Safety Practices
- Ventilation and Air Quality: Adequate ventilation is necessary to remove fumes, smoke, and gases generated during the laser cutting process. Proper ventilation systems should be in place to ensure good air quality and to minimize the risk of respiratory issues or exposure to hazardous substances.
- Fire Safety: Laser cutting can generate sparks and heat, increasing the risk of fire. It is important to have fire prevention measures in place, such as fire extinguishers, fire alarms, and a clear evacuation plan. Consider using inert gases to blow the molten metal for improved safety during laser cutting metals. Additionally, flammable materials should be stored and handled properly to minimize fire hazards.
- Emergency Preparedness: A well-defined emergency response plan should be in place, including procedures for handling accidents, injuries, or equipment malfunctions. All employees should be familiar with the plan and know how to respond in case of an emergency.
By adhering to these safety measures, operators can minimize risks associated with laser cutting metal.
Achieving the Best Cutting Results
Tips for Clean and Precise Cuts
To achieve high-quality cuts when laser cutting sheet metal, it is essential to employ effective cutting techniques. Here are some tips to ensure clean and precise results:
- Optimize cutting speed: Adjusting the cutting speed can significantly impact the quality of the cuts. Finding the right balance between speed and precision is crucial.
- Choose the appropriate cutting technique: Different materials may require specific cutting techniques such as fusion cutting, plasma cutting, or other methods. Understanding which technique works best for each material ensures optimal results with laser focus.
- Utilize cutters with extreme precision: Investing in high-precision cutters can make a substantial difference in achieving clean cuts. These tools offer narrow kerf widths and tight tolerances, ensuring accuracy.
- Maintain cleanliness: Keeping the sheet metal clean before and during the cutting operation helps prevent any debris or residue from interfering with the process, resulting in cleaner cuts.
Avoiding Common Mistakes
While striving for efficiency, it’s important to be aware of common mistakes that can compromise the quality of your laser-cut sheet metal. Here are some pitfalls to avoid:
- Neglecting proper calibration of your laser cutter can impact cutting speed, metal thickness, and the ability to accurately bend metals over time. Regular calibration ensures consistent performance and precise cuts.
- Ignoring material considerations: Different metals have varying properties that affect their response to laser cutting operations. Understanding these characteristics helps avoid issues like burning or warping.
- Overlooking maintenance routines: Regularly maintaining your equipment, including cleaning lenses and replacing worn parts, helps maintain optimal performance and extends the machine’s lifespan.
- Failing to account for material thickness: Adjusting settings based on metal thickness is crucial for achieving desired results without compromising quality or efficiency.
By following these tips for clean and precise cuts while avoiding common mistakes, you can enhance your sheet metal laser cutting operations, ensuring superior quality with every cut made.
Why Choose Baison Laser Machines for Sheet Metal Cutting
In conclusion, Baison Laser is a leading resource in manufacturing with CNC machining. With a deep understanding of laser cutting and its application on sheet metal, they offer a wide range of machines that cater to different needs.
Superior Quality and Precision
Baison Laser Machines are known for exceptional quality and precision in sheet metal laser cutting. These machines are designed using advanced technology, ensuring high-performance results. Baison Laser Machines offer excellent beam quality, resulting in clean and precise cuts, even for complex shapes and intricate designs. With high repeatability and accuracy, Baison Laser Machines deliver superior quality cutting edge, meeting the highest industry standards.
Excellent Customer Service
At Baison Laser, we take pride in delivering excellent customer service to our clients. We provide comprehensive support throughout the entire process, from selecting the right machine for the cutting speed and bend of different metals to after-sales service. Baison’s team of experts is readily available to assist customers with any queries or technical issues related to material thickness, ensuring a smooth and hassle-free experience. Our dedication to customer satisfaction sets us apart and establishes long-lasting relationships with our clients.
Wide Range of Options for Different Needs
Baison Laser Machines offer a wide range of options to cater to diverse sheet metal laser cutting needs. We provide a variety of machine models with different power capacities, bed sizes, and cutting speeds, allowing customers to choose the perfect machine for their specific requirements.
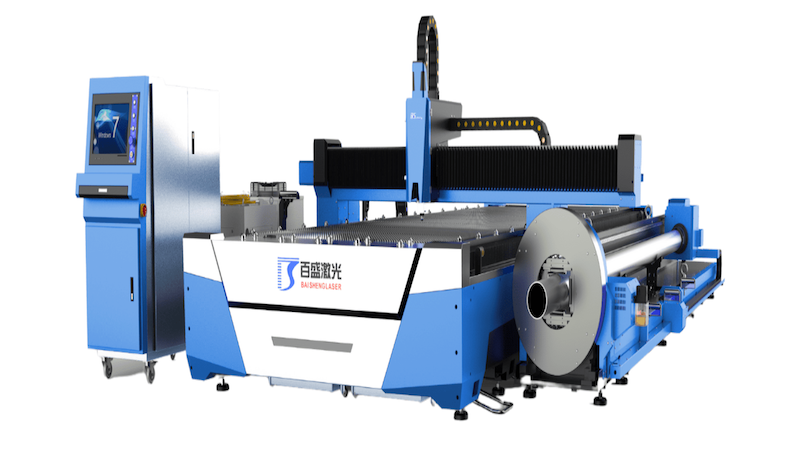
Baison can handle various sheet metal materials and thicknesses, making them versatile for a range of applications. Whether it’s a small fabrication shop or a large industrial operation, Baison Laser Machines provide customizable solutions to meet any sheet metal laser cutting demand.
So why wait? Take advantage of Baison Laser Machines’ expertise and state-of-the-art equipment to elevate your sheet metal laser cutting projects. Get free sample proofing and experience the best laser cutters today.
FAQs
What materials can be cut using laser cutting machines?
Laser cutting machines are versatile and can cut various materials such as stainless steel, aluminum, mild steel, copper, brass, and more.
How accurate are laser-cut parts?
Laser-cutting provides exceptional accuracy with tolerances as low as ±0.1mm depending on the material thickness and machine capabilities.
Is laser-cutting cost-effective compared to other cutting methods?
Laser-cutting is highly cost-effective due to its precision, minimal material wastage, and reduced setup time compared to other cutting methods like plasma cutting.
Conclusion
By now, you should have a good understanding of laser cutting sheet metal, from the basics to safety precautions and best practices. Is there a particular aspect of this process that you find most intriguing? Share your thoughts in the comments. If you’re ready to explore the precision and efficiency of Baison Laser machines, reach out to our experts for personalized assistance.