The elevator industry is rapidly expanding, and with it, the demand for innovative technology to improve the efficiency of the manufacturing process.
Hence, the role of laser cutting machines in elevator manufacturing cannot be overemphasized as industry enthusiasts and manufacturers are beginning to turn to this modern technology for unparalleled precision, speed, and versatility.
Suppose you want to expand your production process and increase your productivity. In that case, this blog post will take an in-depth look into the significance and application of laser-cutting machines in the elevator industry.
What Is Laser Cutting?
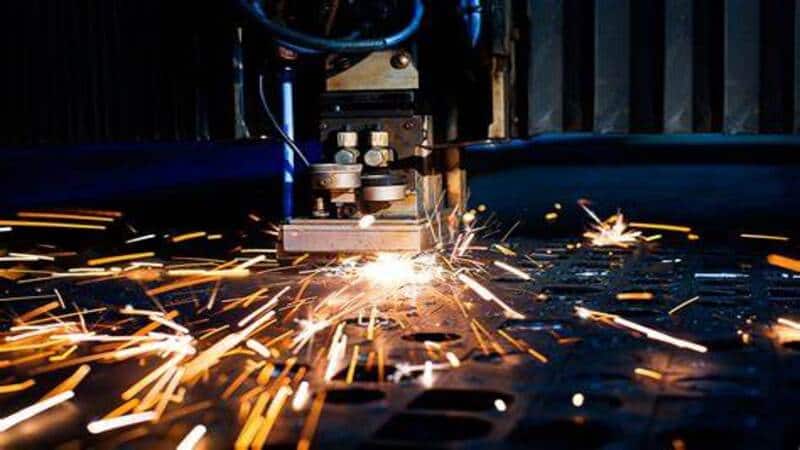
Laser cutting is a non-contact cutting technology that uses a high-powered, intensely-focused laser beam to cut through various materials with precision. The heat generated from the laser beam allows for thorough vaporization or removal of materials to achieve the desired shape or size.
The laser cutting process involves the preparation of the material to be cut, generating the laser beam using carbon dioxide (CO2) or fiber, and directing the laser using mirrors and lenses to a focal point on the material from where the cutting process commences.
The laser beam heats and melts the material following the preconfigured cutting parameters while assisting gases such as nitrogen and oxygen help in blowing away the vaporized material.
What Is Laser Cutting Machine?
A laser cutting machine is a type of Computer Numerical Controlled (CNC) device used to cut or etch into various materials. It employs a high-intensity laser beam to melt or vaporize the material to achieve precise cuts. The CNC allows the machine to receive digital design instructions and interprets the design into computer language the cutter can understand and follow.
Laser cutters have manufacturing applications in many industries, including automotive, oil and gas, aerospace, shipbuilding, construction, etc. But they have various capabilities based on several factors, including thickness, speed, flexibility, design, material thickness, and type of material.
These cutters also offer numerous benefits, such as clean cuts for high-quality finished products, the ability to make complex and irregular cuts, and the ability to cut off a range of materials.
Different Types of Laser Cutting Machines
Fiber Laser Cutting Machines
Fiber laser cutting machines use solid optical fibers to produce the laser beams, giving them their name. They use laser diodes that send light signals to flexible optical fiber cables, amplifying the light’s strength as it travels through. Due to its properties, the light gets easily absorbed and converted into heat to melt the material.
One of the significant benefits of fiber laser-cutting machines is that they reduce the light beam to a slimmer bore, enabling you to achieve much more precise and detailed cuts. You can also achieve outstanding edge quality and allow for clean cuts in thin materials.
Click the button below to learn how to choose a fiber laser cutting machine for elevator manufacturing.
CO2 Laser Cutting Machines
CO2 laser cutting machines are the most common laser cutters because they are the most affordable. They are highly versatile, sustainable, and widely used for various industrial applications.
CO2 laser cutting machines use carbon dioxide, often mixed with helium and nitrogen, filled in a long, vacuum-sealed, to produce intense light beams. The gas molecules become excited when an electric current is applied to the gas mixture.
Apart from being cost-effective, they can cut a wide range of materials with high levels of detail and intricacy. They also have high cutting speeds, reducing production cycle times and your overall productivity.
Nd: YAG Laser Cutting Machines
An Nd: YAG laser cutting machine uses neodymium-doped yttrium aluminum garnet crystal in a solid state as the laser medium. These crystals are known for having high energy levels and produce laser beams at a wavelength of about 1.064 micrometers. The neodymium atoms are excited using diode lasers or flash lamps to pump them.
Nf: YAG cutters are prized for efficiently cutting reflective materials such as copper and brass, which other laser types might not. They are also highly durable, as they can withstand rough operating conditions and heavy-duty operations. These cutters can also be used for welding applications.
Advantages of Using Laser Cutting Machines in Elevator Manufacturing
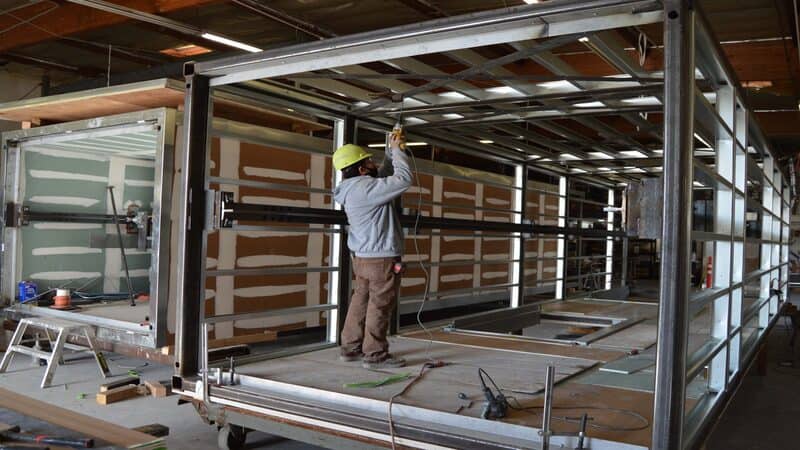
The elevator manufacturing industry is currently on the rise with the rapid construction of many high-rise buildings in property infrastructure. This has increased the demand for high-speed elevator technology with an efficient production cycle, which is why many elevator manufacturers in the industry are turning to laser-cutting machines as the way forward.
Here are some benefits you can enjoy when using laser-cutting technology in the elevator manufacturing industry.
High Processing Efficiency and Design Flexibility
As humans develop, so do their methods and products. Hence, elevator steel plates are no longer the boring, rectangular shapes we are used to. Manufacturers are now beginning to inculcate various designs and shapes into their production process, doing away with traditional cutting methods and requiring more automated methods to achieve such complex outlines and contours.
A laser cutting machine allows for easy customization of designs, allowing you to achieve complex designs with minimal material waste, cost, and labor. You can also make design changes rapidly, optimizing your production process and successfully achieving customer requirements.
Shorter Processing Cycle
Time is a crucial factor in the elevator industry, as specific processes, such as mold processing, can lead to a lengthy production cycle. Due to the speed and efficiency of the laser cutting machine, you can optimize your manufacturing time and reduce production costs while upholding the integrity and quality of your elevator designs.
Material Versatility and Compatibility
A wide range of materials are used in the elevator manufacturing process, and the laser cutting machine is versatile in cutting many of these thin or thick materials.
From metal materials such as stainless steel, carbon steel, silicon steel, titanium, and brass, to reflective materials such as aluminum and copper, to plastic and even laminates, their versatility allows you to select different materials without compromising your quality.
How Do Laser-Cutting Machines Help Achieve Precision in Elevator Manufacturing?
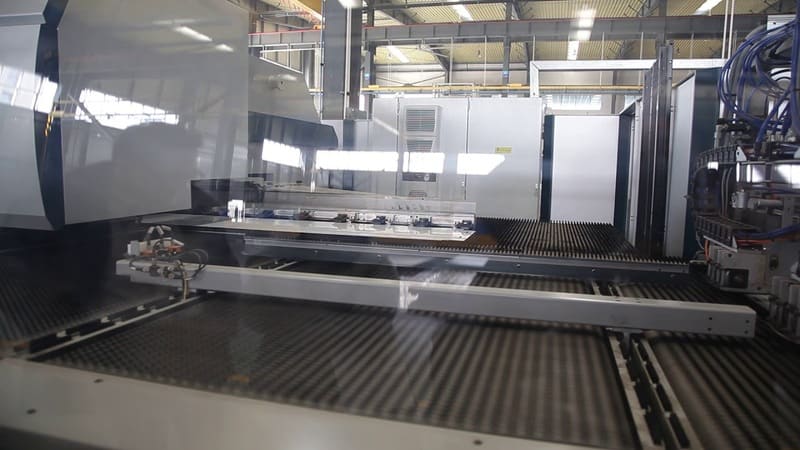
The elevator industry requires optimal efficiency to achieve clean, extremely precise cuts in manufacturing, especially for stainless steel decorative plates. For this reason, many manufacturers are beginning to turn to laser-cutting technology to achieve accuracy and avoid compromising on quality.
These cutters use advanced motion control mechanisms and high-resolution positioning systems, focusing the laser beam to allow you to make intricate shapes and detailed cuts and etch out components with tight tolerances, ensuring precision and accuracy.
The cutter also uses CNC systems which elevator manufacturers can use to program their desired designs, cutting paths, and dimensions for the machine to replicate. This system eliminates human error with consistent and repetitive cutting.
Unlike ordinary processing methods that require some finishing work and adjustments, laser cutters eliminate the need by maintaining the quality and required specifications of the elevator. Furthermore, their adaptability to various elevator materials, irrespective of their properties, thickness, or cutting requirements, ensures precision in elevator production.
The Importance of Precision in Elevator Manufacturing
We’ve already established that precision is crucial to the manufacturing industry to maintain accuracy and quality. Precision is essential for the following reasons:
Aesthetics
Elevators make up a part of a building’s appeal, and one with proper, accurate cuts enhances the aesthetics of the elevator. Precision ensures symmetrical and intricate cuts during production, resulting in a polished finish for a prominent, professional look.
Safety
Elevators are a means of transportation within a building, and you wouldn’t want one that will create hazards because their components are not correctly aligned.
Precision in manufacturing ensures that the elevator parts are accurately assembled and fit perfectly to prevent failures or malfunctions that threaten human safety. Precision allows proper alignments, which increases its integrity and quality.
Durability and Quality Assurance
Properly constructed components reduce the risk of wear and malfunction. Precision in elevator manufacturing ensures they can endure tough usage over a long period, decreasing maintenance or operational costs and downtime. Components that are precisely aligned increase operational efficiency, eliminating vibrations or friction.
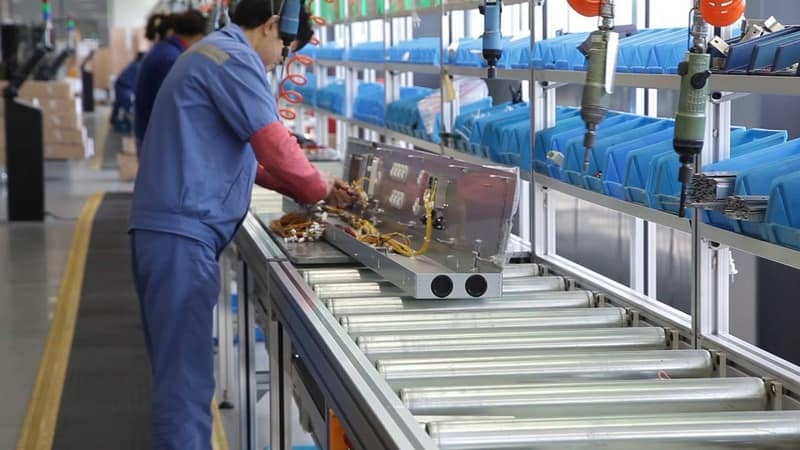
What Should You Consider While Choosing a Suitable Laser Cutter for Elevator Manufacturing?
There are many factors to consider when choosing a laser-cutting machine that best suits your elevator production needs. Aside from precision, whose importance we’ve established earlier, one of the most crucial considerations is the power and capacity regarding the type and thickness of materials it can cut.
Furthermore, your cutter must be fast enough to meet your production targets without compromising cut quality. And if you’re working with a budget, you must also consider the laser’s initial cost, installation, maintenance, and training costs, including return on investment.
Conclusion
It’s out with the old and in with the new when you include laser-cutting machines in your elevator production process. These should be your go-to solution if you’re looking for a more efficient way to attain precision and accuracy without compromising on quality and safety. From CO2 to fiber and ND::YAG, there are several options to choose from based on your needs.
Head to our website for more information on laser-cutting machines for your elevator manufacturing.
Discover the Perfect Solution for Your Business with Baison
At Baison Laser, we design and build state-of-the-art fiber laser systems that cover the entirety of your production needs, ensuring precision, efficiency, durability, and high-quality output. Our dedicated team of specialists is available 24/7 to help you find the right laser system for your business. Don’t hesitate to click the button below to contact us!