What is laser cutting?
Laser cutting is a process that uses a laser beam to cut wood, plastic, paper, metals, and acrylics. The laser beam does not come into contact with the material it cuts. It makes extremely detailed cuts. Laser engraving permanently engraves barcodes, logos, and dates on your rings or professional equipment.
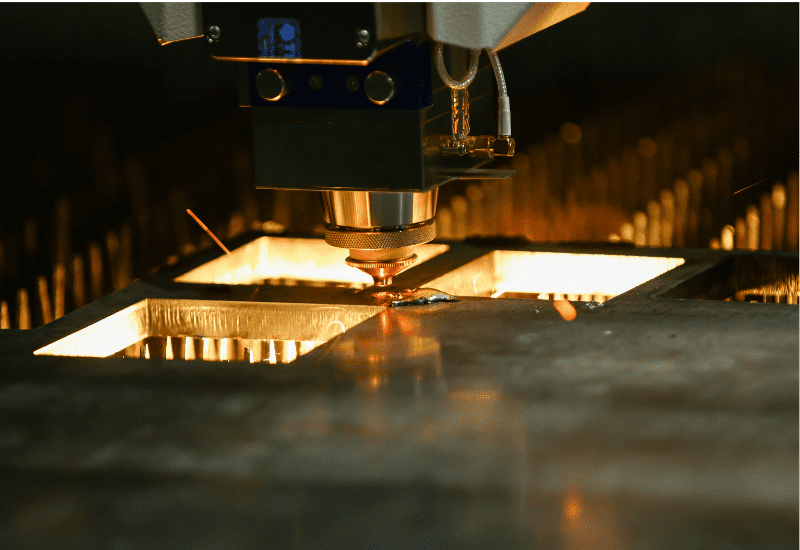
Three different lasers are used in laser cutting, such as:
- Carbon dioxide lasers: The laser beam is produced in a sealed glass tube, and the tube is filled with carbon dioxide gas. The gas particles react with the high voltage when passed through the tube. This reaction produces hot light, and the heat is used to vaporize the material. It is used for boring, engraving, and cutting through titanium, steel, wax, stainless steel, and paper. It is preferably used when cutting material thicker than 10mm because it has fantastic edge quality. One of the downsides of using carbon dioxide lasers is that they have an efficiency of only 20 percent.
- Neodymium laser: It works exactly like carbon dioxide laser but uses a crystal with small amounts of neodymium instead of gas as a laser source. It is used when high power is needed for boring and engraving in ceramic and scribing metals only.
- Fiber lasers: Unlike carbon dioxide lasers, fiber lasers do not use gas. Diodes are used to create light. Then the light is injected into a fiber cable and amplified. It is used when cutting materials thinner than 10mm because it is more efficient and precise than the above lasers. Plus, its laser head produces a 1064 nanometers wavelength, making it ideal for cutting reflective materials such as brass and copper. It also has an efficiency of 75 percent.
Benefits of Using Laser Cutter
Using a laser cutter has certain main advantages, including:
Precise
Laser cutting cutters are accurate to +/-0.1 mm, making them highly precise. They are far more accurate and precise than any other traditional cutting method.
Plus, a laser cutter seals edges by vaporizing or melting the edges of the cutting material, so you won’t need to take out your grinder to smooth anything down. They are used for rapid prototyping because they make highly detailed precision cuts.
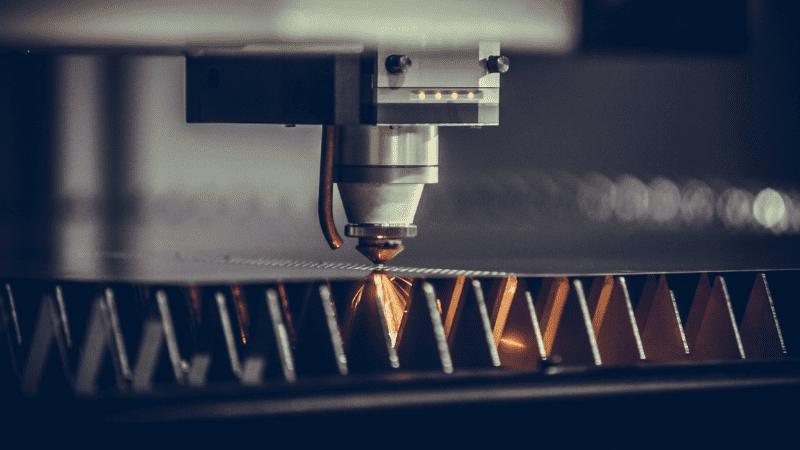
Efficient
If you want to cut many materials quickly, laser cutters should be your jam because they are precise, accurate, and highly efficient.
Laser cutters can cut 10mm of metal very quickly. According to Wikipedia, it can cut a 13mm thick stainless steel in 5-15 seconds; this reduces the usage time and, thus, excessive use of power.
Versatility
Laser cutters are versatile machines that can cut through almost anything — natural wood, steel, iron, and even paper. They can also be used to make precision cuts, which are not the strong suit of CNC cutters.
Just don’t use your laser cutter to cut a foot-thick steel block. You may need to buy yourself a new machine.
Flexible
Once you set up your laser cutting machine, you can cut almost anything. There is no need to change cutting tools for different designs. You will only need to upgrade if you need to cut something bigger.
Disadvantages of the Laser Cutter
If you’re using a laser cutter for a project, you should keep the following disadvantages in mind:
It Requires Expertise to Operate
A layperson cannot operate a laser cutter; it requires a specialist operator. This increases labor and, thus, the operational cost.
It Has a Cutting Limit
Laser cutters cannot cut through very thick metals. It can cut metals with a maximum thickness of 30mm. However, most laser cutters only cut metals with a width of 9 to 12mm.
It is Expensive
The cutting machine equipment is costly.
Initial cost
The cost can go up to $150k. Plus, the laser cutting machine has higher runtime power, thus greater power consumption and waste of energy. Furthermore, maintaining the machine is expensive.
It Emits Dangerous Fumes
Laser cutting produces gases and fumes that can be dangerous for people in the working space. So, a proper ventilation system needs to be installed to create a safe working environment.
It Causes Burn Marks
The laser engravers cause unwanted burn marks on the edges. The laser beam doesn’t touch the material, but when the fumes and material wastage come into contact with it, it causes burn marks.
Preventive measures can be taken to avoid unwanted burn marks and burnt edges, including using air to blow away fumes, removing material waste, and using damp wood.
What is CNC cutting?
Computer Numerical Control (CNC) machining is a process in which software commands the movement of machinery and cutting tools. The machine interprets the instructions and creates a tool path; the tool is programmed to move along the path to cut the custom shape. Unlike laser cutters, a CNC cutting machine is in contact with the workpiece and uses friction to cut through it.
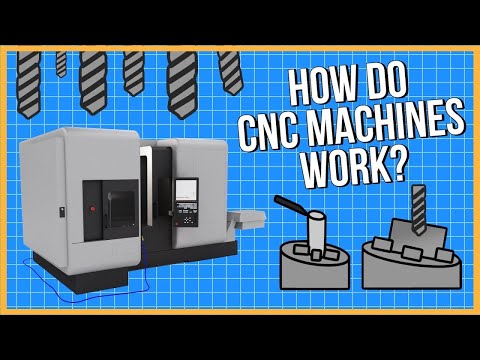
There are several types of CNC machines.
- Lathes: Basic lathe has two-axis. It moves the tightly clamped piece around the axis and is pressed against a craving tool. The programmed tool moves along the tool path. This action carves the workpiece into the desired shape. Lathes are commonly used to make objects that need to be symmetrical such as cones or squares.
- CNC Router: CNC routers support a hand-held router as a spindle. The spindle cuts wide dimensions in metals, plastic, and wood. A CNC router can work in three dimensions on a three-axis coordinate. The spindle speed can be adjusted according to the need. Usually, a CNC router is used to cut softer non-ferrous materials like wood and acrylic.
- Plasma Cutters: Plasma cutters do not mechanically cut the material but use hot plasma to cut shapes in sheets of stainless steel, aluminum, and brass. It ionizes gases like nitrogen to make plasma.
- Milling: CNC milling machine works oppositely to lathes. Instead of moving the cutting tool, it moves the cutting material. A milling machine uses a cutting tool attached to a rotating spindle. The workpiece is placed on a table. The table moves in different planes and axis so the cutting tool can create the desired shape. Milling machines come in several different sizes and can work on multiple axes. CNC milling machine is mostly used to cut metals.
Benefits of Using CNC Cutter
The main advantages of using CNC cutters for your projects include the following:
Precision
The process relies on computer instruction; therefore, the risk of human errors is eliminated. This creates a precise product.
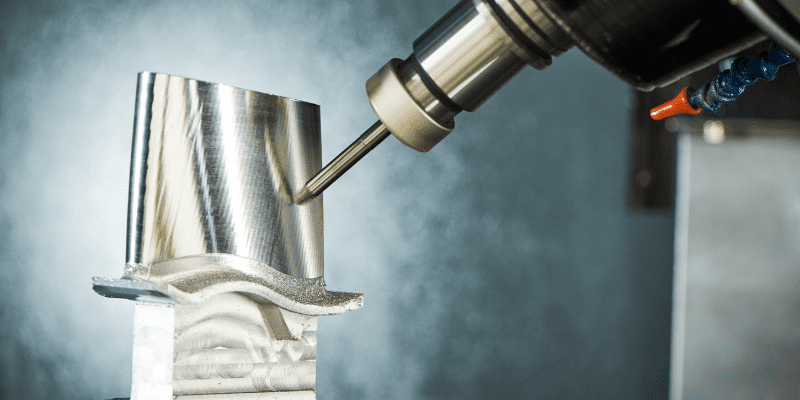
Endurance
One of the main advantages of using CNC cutters is that they can work 24/7, 365 days a year. They don’t need to be switched off between tasks for any maintenance.
Low-cost
Although CNC cutters have a higher initial cost, they need low maintenance. Moreover, they are less dependent on human labor, so very few paid workers are needed to overlook the process.
Improved Safety
Maintenance is usually only required when the tool is switched off. So people don’t need to go near the cutting tools, making the cutting process safe.
Disadvantages of using CNC Cutter
If you’re using a CNC cutter as a professional, you should keep the following disadvantages in mind:
It Requires Trained Operators
Basic training is needed to operate CNC machines; one person is enough to supervise and operate several machines. Fewer employment opportunities because labor cutting is no more required
Loss of Skill
In the past, engineering students used to study and take years of training to learn these physical precision cutting methods. With the introduction of CNC mechanics, new students are no longer taught these skills.
High-Cost
High installation, operational, and maintenance cost is one of the main drawbacks of CNC-cutting machines. They are more expensive than manual machines and require a greater initial investment.
Plus, a skilled professional worker must be hired to look into the matter in case of any breakdown. Different cutting tools are required for different applications and designs.
What is the difference between a CNC and a laser cutter?
CNC and laser cutters are used for subtractive manufacturing but differ significantly. Let’s look at some differences between some CNC laser cutting tools:
Material Capability Differences
CNC cutting tools and Laser cutters work on different materials. CNC can work on more material than a laser cutter. A laser cutter cannot process fragile materials such as polyvinyl chloride (PVC), polyvinyl butyral (PVB), and leather. Most CNC lasers cannot work on materials thicker than 12-13mm. Only a few can work on materials up to 30mm thick.
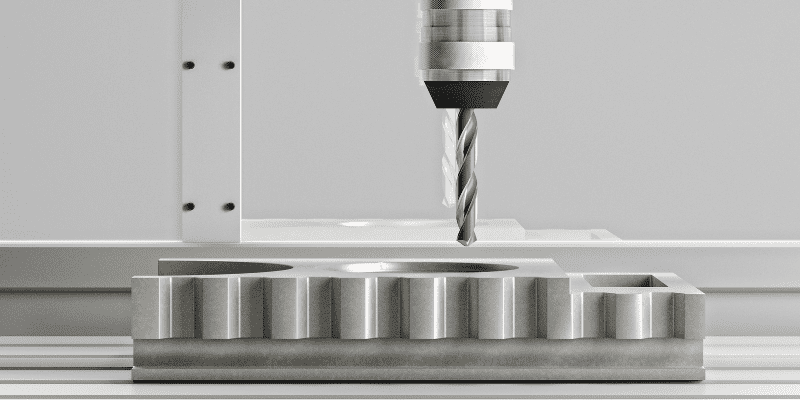
Cutting thick polycarbonate using a laser cutter makes the material melt rather than vaporize, and it is very inefficient as infrared radiation is absorbed by polycarbonate. Infrared is used by laser to cut material. Furthermore, cutting softer materials like PVC with a laser beam produces harmful gases that can corrode the laser cutter.
Unlike laser cutters, CNC cutters can be used to cut both thick PVC and polycarbonate.
Cutting Speed
Laser cutting is a faster process as compared to CNC machine cutting. Using a laser cutter to cut throw steel can cut 114 inches per minute (IPM), while CNC cutters cut only 70 inches per minute (IPM).
Plus, laser cutters often take only one try to cut through many materials, whereas CNC cutters require far more tries for the same process.
Accuracy
It is no shock that laser cutters are far better than CNC cutters to transfer accuracy. Accuracy is directly proportional to precision; greater precision means greater accuracy.
A CNC cutter only has 1mm of precision compared to the 0.1mm precision of laser cutters. This precision makes it possible for laser cutters to achieve great accuracy in the details of the cuts.
Cutting Depth and Width
A CNC cutting machine can create three-dimensional carvings by moving along all three axes. In contrast, laser cutters may give you clean vertical lines, but they cannot perform deep cuts because they have tight focus spots, and unlike CNC cutters, they don’t use Z-axis movements.
Price Comparisons
There isn’t much difference if we compare the initial cost of laser and CNC cutters. The price range of laser cutters falls anywhere from $150-$300K depending on their size, whereas CNC range from $130-$200K depending on their size.
Maintenance
In terms of maintenance, laser cutters beat CNC cutters. Laser cutters require little to no maintenance, unlike CNC cutters which need replacing cutting tools occasionally.
Waste
Laser cutters produce way less waste than CNC machine cutters. This ensures maximum utilization of cutting material.
Which one is right for you?
Both laser and CNC cutters have unique qualities that set them apart from each other. You need to figure out what you want to use your required machine for.
A laser cutter is better if the job requires cutting thin and highly accurate workpieces. If you are looking for something that can work on a greater number of pieces quickly, then a laser cutter should be your choice. It will have a shorter run time, decreasing overall power consumption. Moreover, the resulting piece will have more precise edges.
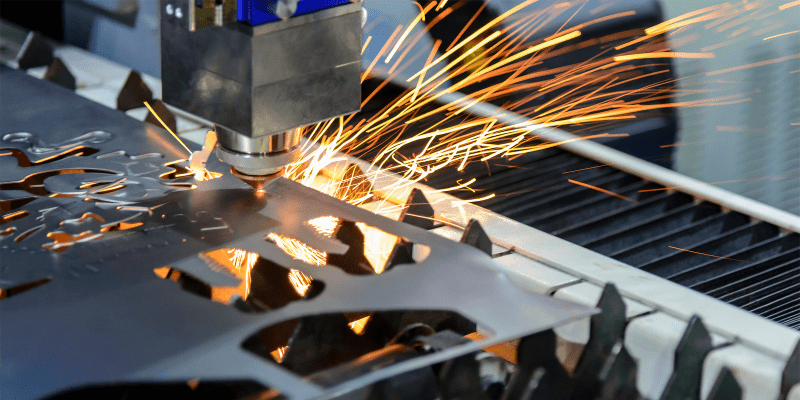
However, it is wiser to choose CNC cutters if the job requires three-dimensional cutting. Moreover, CNC machines can work for very long periods. So, if the final products are bigger, CNC cutters are a better option because you wouldn’t have to take breaks in between, thus decreasing the work hours.
Who Uses Laser Cutter And CNC Cutters
Both laser cutters and CNC are used in several different industries, such as:
- Medical
- Aerospace
- Electronics
- Automotive
Uses of Laser and CNC Cutters
Medical
Both laser and CNC have many uses in the medical industry. They are used to manufacture precise and free-from-human error ultrasound equipment, MRI scanners, catheters, diagnostic equipment, and biomedical implants.
Moreover, they are now used in manufacturing artificial joints like hip joints. In dentistry, they make customized and highly accurate dental implants for patients.
Aerospace
The aerospace industry is one of the biggest CNC and laser-cutting users.
Laser cutters cut aluminum alloy to make many mechanical flight components of different shapes and sizes.
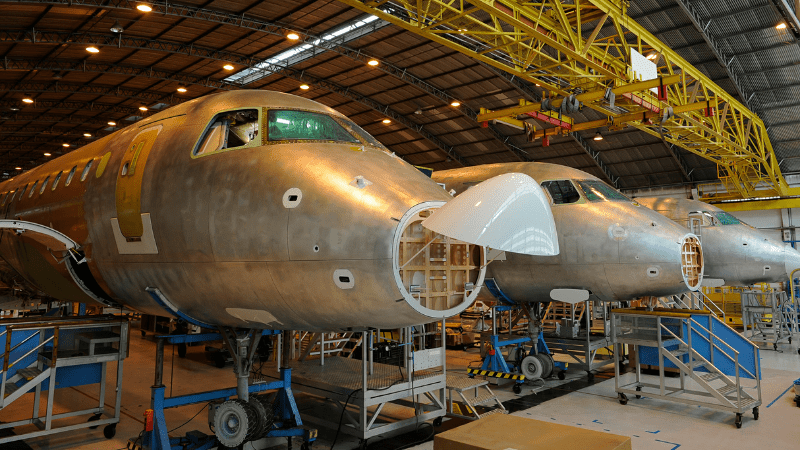
Just like laser cutters, CNC machines greatly use in the aerospace industry. Aircraft’s interior components are made up of polymer-based material. CNC machines create plastic parts for aircraft, including doors, ventilation ducts, and more.
Electronics
CNC milling machines and turning machines are used in the electronics industry to manufacture plastic and metal parts. They are used to cut through aluminum pieces to make keyboard holes for laptops and desktops.
On the other hand, laser cutters mark electronics like microchips, circuit boards, and keypads. Laser cutters engrave barcodes and serial numbers on electronics so they can be easily identified and recognized.
Automotive
Laser-cutting technology has made its way into the automotive industry too. Laser cutters make automobile parts like car door frames, roof covers, trunks, and bodies.

CNC machines are heavily relied on for making gearboxes, dashboards, and roof panels. Moreover, CNC machining to manufacture headlights and interior lights.
The Bottom Line
Laser cutters and CNC machine cutters come with their advantages and disadvantages. They have different working mechanisms; one uses a contactless way, and the other remains in contact with the workpiece throughout the process. Each one of them has its use. They are beneficial in different processes in different ways.
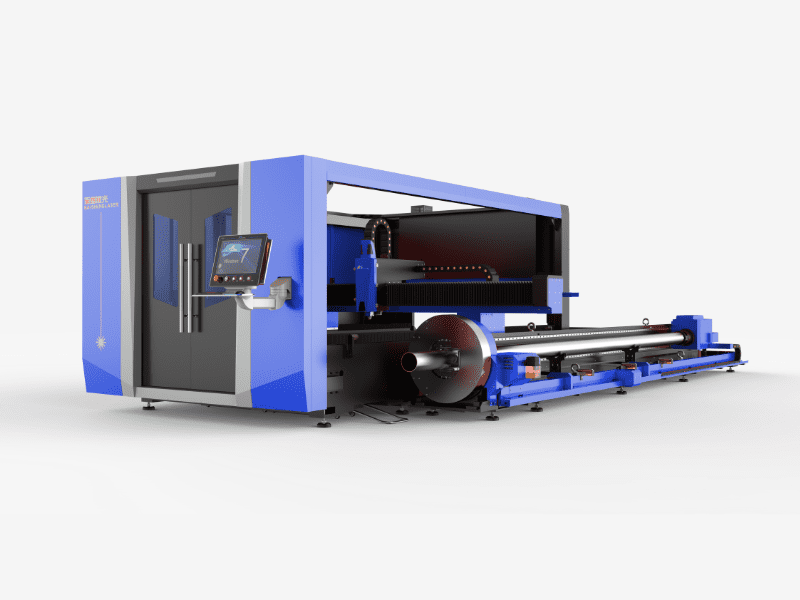
However, they are also very similar in many ways. Both are modern cutting methods. They have similar applications and features. They both make our work easy by creating precise pieces which are accurate and free from human error.
Over time laser cutting technology is becoming increasingly famous in many industries. With developments, it promises only to offer us more benefits.
We hope all the questions you had in mind before reading this blog have been answered. However, if you are still unsure what is right, contact Baison for a proper solution. We will help you pick out the machine that is worth your investment.