Selecting the appropriate equipment between pulsed fiber and continuous wave lasers challenges novices due to their similarities. These tools are famous in the automotive and aerospace industries for their fast cleaning and precision heat control features.
Understanding these machines’ capabilities and limitations aids your selection for desired applications.
This article will discuss pulsed fiber and continuous wave lasers in-depth. You’ll also learn laser cleaning applications and factors to consider before choosing. Let’s get started.
What is Fiber Laser Cleaning
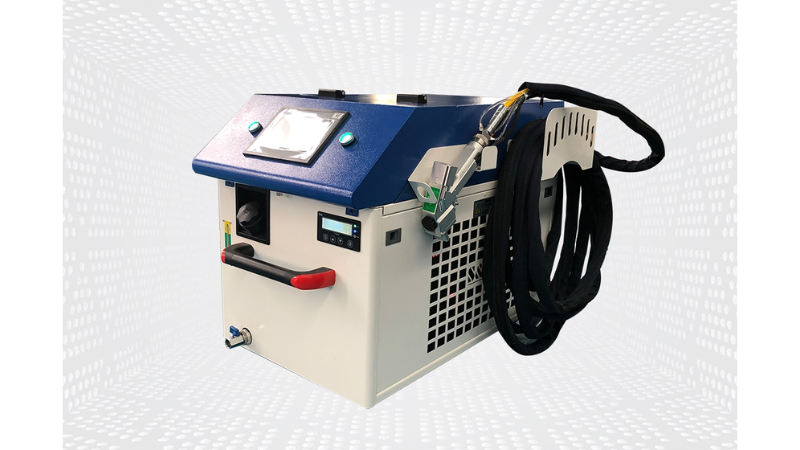
Fiber laser cleaning removes oil and oxide layers from the surfaces of small and large steel structures. This eco-friendly process uses high-energy density machines to vaporize paint stripping and rust on aluminum alloy, steel structures, pipes, etc.
High-power lasers remove contaminants and modify surface texture without chemical cleaning methods. The laser cleaning process requires a pulsed laser with at least 50 watts or more for effective results.
The good cleaning performance is controllable and easily applied to specific areas. You can automate the machine, and it guarantees repeatability demanded by most users to meet quality standards.
Pulsed Laser Cleaning
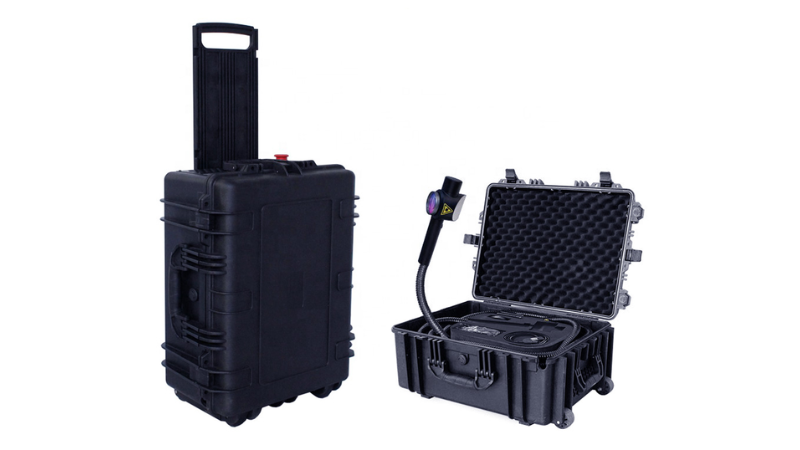
Pulsed laser cleaning is a non-contact method of removing contaminants such as rust and coating from material surfaces. This eco-friendly technique has no thermal effect.
Pulsed cleaning is non-destructive and has zero effects on material parts. Using a focused laser beam ensures efficient and faster removal speed than the fiber machine technology.
Unlike labor and time-consuming conventional methods, pulsed laser cleaning is energy efficient and consistently removes contaminants.
How Do Pulsed Lasers Work?
Pulsed devices emit intense laser light energy bursts at a specific frequency determined by the machine’s properties.
The machine releases concentrated energy through an external modulator. It functions as a switch allowing light transmission in optical pulses for a short period.
The high-energy pulse is typically in the picoseconds to nanoseconds range. They’re ideal for cleaning surfaces, drilling, welding, and cutting materials.
Advantages of Pulsed Laser Cleaning
Precise heat control, cleaning efficiency, and non-contact are a few benefits of different laser models. Other lasers and pulsed fiber advantages include versatility and environmental-friendly.
Precise Heat Control: A pulsed laser cleaning machine with a master oscillator power amplifier (MOPA) structure has precise heat control. It’s critical for users when cleaning as it prevents improper heating and improves efficiency.
Cleaning Efficiency: The pulsed laser cleaning technology offers efficiency with fast removal speed. The machine cleans faster but requires less time and energy and generates little heat.
Non-Contact: The non-contact method is another benefit of pulsed laser cleaning. It doesn’t touch or damage your cleaning surface, making it ideal for sensitive or delicate materials.
Environmentally Friendly: Unlike conventional cleaning techniques, pulse laser cleaning is eco-friendly. It doesn’t require harmful chemicals or cause pollution, which is ideal for the environment.
Typical Applications for Pulsed Fiber Laser Cleaning
Fiber laser cleaning is an effective method used for different applications across various industries. Some of the uses include the following:
Precision Laser Ablation: Pulsed cleaning application for precision laser ablation is ideal for surface machining. The typical usage of precision laser ablation includes routine welding of metal parts.
Removing Surface Contaminants: Pulsed fiber laser cleaning is perfect for vaporizing unwanted impurities from metal surfaces. They include rust, oil, paint, and coatings.
Preparing Bonding Surfaces: Pulsed fiber laser cleaning removes various contaminants, leaving a smooth surface perfect for bonding. Clean surfaces thoroughly before welding to create a strong bond.
Cleaning Tools and Molds: These materials often build up residue over time, leading to production downtime. Pulsed fiber laser cleaning eradicates unwanted contaminants, ensuring molds and tools are in top condition.
MOPA Pulsed Fiber Laser
The Master Oscillator Power Amplifier (MOPA) comprises an optical amplifier and a master laser. These features boost the machine output power to generate a higher pulse repetition rate.
MOPA fiber laser technology is handy in various industries as it can perform stainless steel marking and color engraving. It can also etch and carve plastic without burning or affecting the material.
Since MOPA pulsed fiber laser energy emits briefly, it concentrates the power into pulses for desired results.
Continuous Wave Laser Cleaning
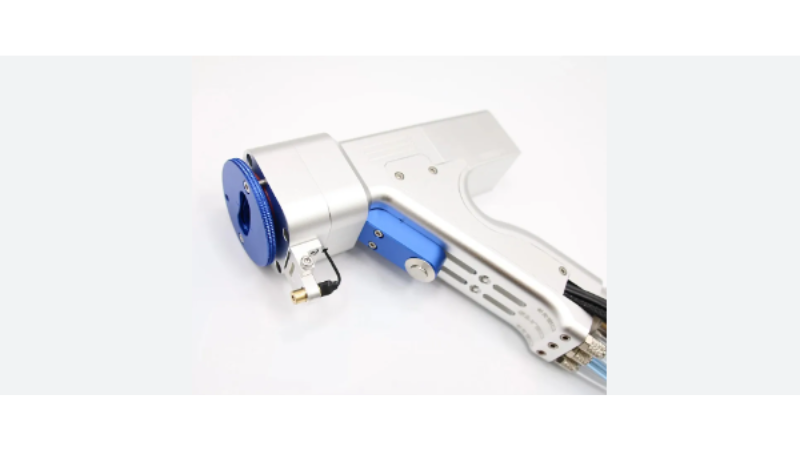
CW laser cleaning uses a constant light beam to remove contaminants. It emits a coherent stream of lower-energy light, which makes regular vaporization suitable for applications that require control and precision.
The coherent beam laser output ensures precise material removal and can eliminate surface layers without damaging the material.
How Do Continuous Wave Lasers Work
The CW fiber lasers work with atoms and photons and absorb or emit them in three ways.
Absorption: The CW fiber laser atom remains in the ground while an incoming photon excites and absorbs it.
Spontaneous Emission: The CW fiber laser excited atom emits a photon before returning to the ground state.
Stimulated Emission: The CW fiber laser excited atom collides with a photon before returning to the ground, producing another identical light quantum.
It would be best to excite half of the CW mode atom to get a laser working. After colliding, it generates a second photon by stimulated emission, which could start a chain reaction. It’s also called Light Amplification by Stimulated Emission of Radiation (LASER).
Benefits of Continuous Wave Laser Cleaning
The advantages of continuous wave laser cleaning include the following:
Fast Heat Dissipation: Continuous wave device cleaning ensures heat dissipates quickly. There’s a low risk of the laser light heat damaging materials.
Large Steel Structure Cleaning: Continuous wave laser is ideal for extensive steel structure cleaning due to its non-contact properties. You can also remove contaminants in specific locations with this technology.
Excellent Precision and Cleaning Control: Continuous wave lasers have greater cleaning control and precision than pulsed devices. It keeps the surface clean and smooth without surface damage.
Speed: Continuous wave laser cleaning is faster than pulsed fiber technology or conventional machines. It increases productivity and saves time.
Energy Efficiency: Continuous wave lasers are energy-efficient, requiring less power to deliver desired results.
Pulsed vs. Continuous Wave Lasers: How to Choose
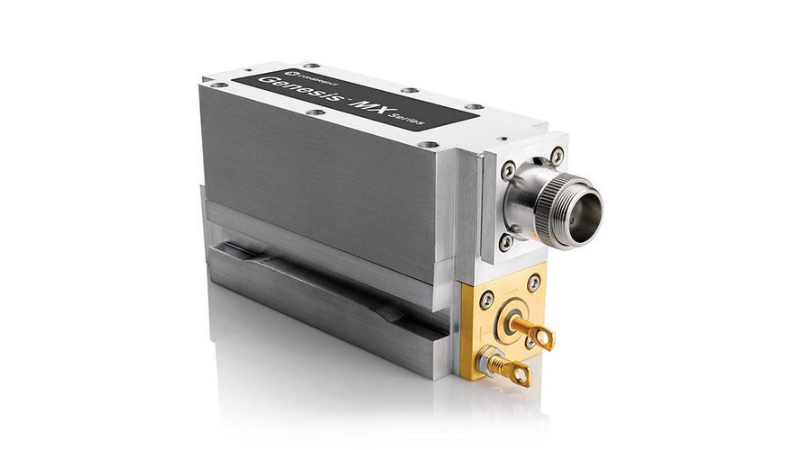
There are various reasons to choose between pulsed fiber and continuous wave lasers. Here’s an illustration of their differences:
- Heat Control
Pulsed fiber lasers generate adjustable heat in short bursts
CW lasers generate a more consistent and stable adjustable heat output
- Cleaning Efficiency
Pulsed machines are effective for texturing and surface cleaning due to high-intensity bursts of energy
CW devices are ideal for surface cleaning, cutting, and laser welding due to consistent energy output
- Heat Dissipation
Adequate transfer of heat at a specific frequency and pulse width until stopped
CW devices offer continuous transfer of heat on the object until stopped
- Power Output
Pulsed mode devices generate high peak power but keep the average energy relatively low.
CW lasers produce stable, consistent, and constant power.
- Energy Efficiency
Pulsed fiber lasers have high energy density because of their pulse energy concentration in a shorter period.
CW lasers have lower efficiency interaction due to their coherent power output
Selecting between pulsed fiber and CW lasers should depend on applications, precision requirements, and desired level of cleaning efficiency.
How to Choose Between Pulsed and CW Laser Cleaning
You want to evaluate different factors before choosing between these cleaning machines. Some of them include the following:
Cleaning Efficiency: Pulsed lasers are more effective when cleaning brittle, hard materials such as glass or ceramics. CW fiber laser cleaning machines are suitable for flexible, soft materials like plastic or rubber.
Precise Heat Control: Considering precision heat control is crucial. Pulsed devices offer greater control and higher precision. Continuous-wave lasers are more appropriate for the welding process and cleaning large-scale applications.
Material Type: Pulsed lasers are ideal for delicate items that heat can damage easily. CW lasers are more suitable for rigid materials requiring longer exposure and higher power.
Surface Area: Pulsed fiber lasers occupy minimal space and are ideal for hard-to-reach areas. Continuous wave lasers are perfect for large surface areas.
Equipment Cost and Maintenance: Pulsed lasers are more expensive than CW lasers but might require less maintenance. Continuous wave lasers are inexpensive but may need regular maintenance.
Importance of Selecting the Suitable Laser Type
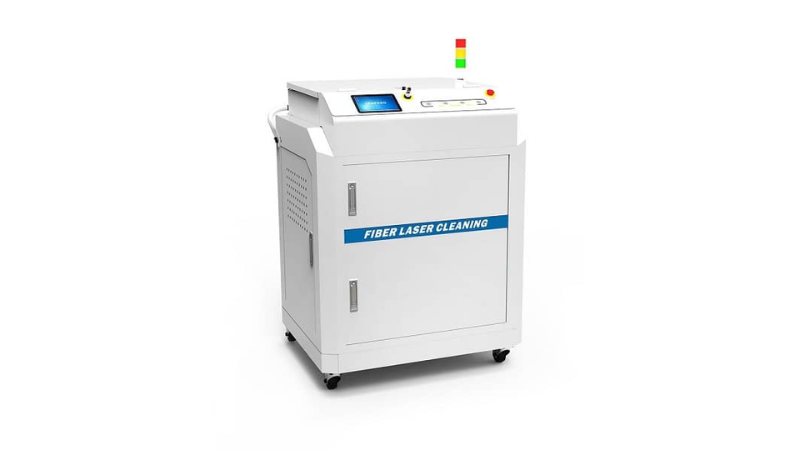
Choosing the proper fiber laser cleaning machine is crucial for achieving optimal effectiveness and efficiency. Consider the laser beam size, pulse duration, wavelength, and power before selecting it for a given application.
Removing contaminants depends on the laser’s interaction. Short-wavelength lasers can vaporize some impurities, while longer wavelengths work for other materials. The beam size and power output determine its cleaning efficiency.
A higher-power machine can quickly remove contaminants but may damage the material without proper use. Carefully choose the beam size to remove impurities with damage effectively.
Conclusion
You know the differences between emerging laser cleaning applications, so get the appropriate equipment for your projects. Your ideal tool should provide precise heat control and adjustment features.
It would help to have a laser with excellent precision, cleaning control, and adjustment features for desired results.
Buy High-quality Fiber Laser Cleaning Machine from Baison Laser
Buy fiber lasers and pulsed cleaning equipment with adjustment and precision control features from the best manufacturers. Baison Laser is a reputable and reliable mechanical and industrial cleaning technology producer.
Contact us today for a consultation, and you’ll get the best products that deliver excellent results.