In this blog post, we’ll explore the art and science of pinpointing the ideal focus position for your laser cutting and welding machines, ensuring that your business consistently delivers high-quality, accurate products to customers worldwide. Join us as we delve into a detailed analysis of this skill.
What Is Laser Cutting?
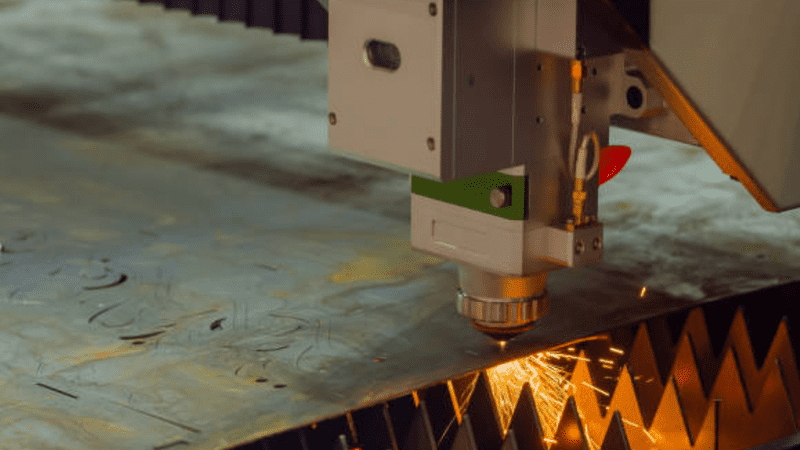
The laser cutting process is a highly powerful yet delicate process that uses a laser beam to vaporize, melt, or burn through the cutting material.
For this, it has to have a focal point in order for accurate cuts. Industries worldwide use this machine to aid manufacturers of parts and products, including aerospace, automotive, shipbuilding, construction, etc.
Laser-cutting machines hold immense importance in that they help produce exact designs with efficiency, cutting speed, and minimal waste. As a result, they increase the overall output, cutting quality, and a business’s ability to cater to higher demands.
Therefore, it has become an indispensable tool for businesses striving to meet the growing demand for complex, custom-designed products.
How Laser Cutting Works?
The laser cutting process using an automated machine involves a series of processes that occur one after the other. The order follows:
Laser
Starting with the laser is responsible for creating a high-energy beam that helps melt or cut through various materials.
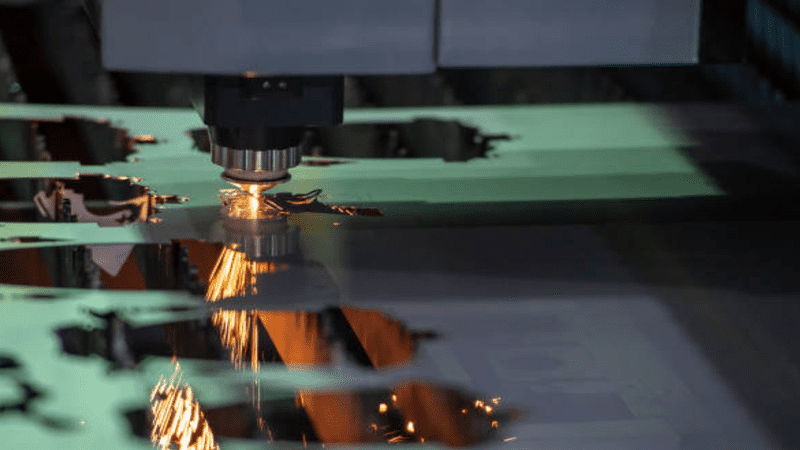
Cutting Head
This component of the laser machine helps guide the high-energy beam to a specific spot. As a result, the laser is able to make cuts as commanded by the software inputs.
Gas Assist
Once the laser beam finds the perfect focus, nitrogen or oxygen gas assists the cutting process by removing unwanted materials and heat. This helps achieve undistorted, precise, and high-quality cuts.
If you want to learn about how to choose the right auxiliary gas, click here.
Motion Control
This feature of the laser cutting machine allows for smooth movement from points A, B, C, and D in all directions while maintaining an ideal focus position.
What Is Focus Position?
A focus position is one of the most vital aspects of a laser-cutting machine. It refers to that precise point where all the laser beam power converges to its smallest diameter. Here the energy is the greatest, meaning all concentration is at a tiny point for maximum cutting power and accuracy on the cutting surface.
As a business, you must invest in a premium laser machine that comes with smooth and effective focus point capabilities. This will help achieve high-quality results in less time and use fewer resources. On top of it, you will be able to minimize waste as well as get a competitive advantage over other businesses like yours.
What Are the Factors That Determine the Ideal Focus Position?
Here are the most important considerations to keep in mind when choosing the ideal focus position:
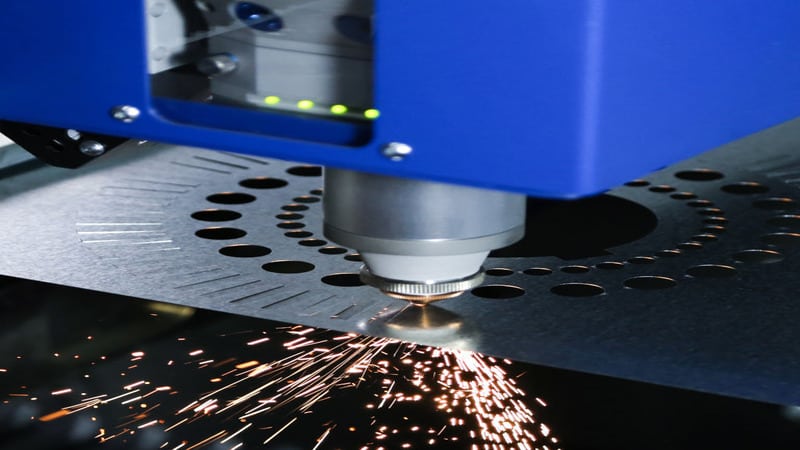
- Material Thickness: Focal position adjustments may be necessary for thicker materials to keep the cutting quality high.
- Material Type: A material’s reflectivity and melting point, for example, can affect the focus location, so you must know these credentials in advance.
- Beam Quality: The laser cutting machine must have a high-quality laser beam for finer cuts and a smaller focus area.
- Laser Power: Higher-powered lasers can cut thicker materials, but the focus location may need to be adjusted for optimal use of the high power on the cutting surface.
- Nozzle Diameter: The nozzle diameter influences the focal point, which also affects the gas flow and the distance between the nozzle and the workpiece surface.
- Working Distance: The right working distance maximizes cutting strength and reduces the risk of lens damage.
As a business, you must keep these factors in mind in order to maximize ROI and ensure a consistent stream of laser-cutting results.
Techniques for Finding the Ideal Focus Position
Using the proper ideal laser focus techniques is highly significant for any business working with laser cutting machines. Here are some of the well-researched and practically tested tips for you to achieve effective results:
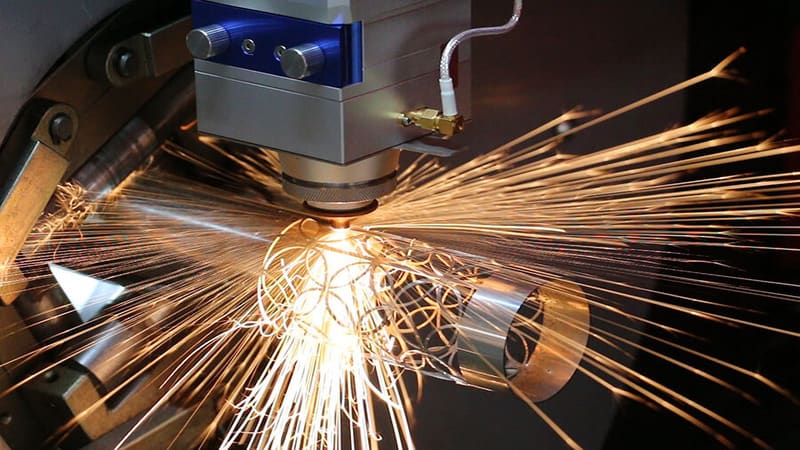
- Manual Focusing: use this feature of the laser cutting machine when working with materials of varying thicknesses. It gives you complete control over the focal cutting point on the workpiece surface, ensuring you can make specialized cuts for customized orders.
- Depth of Field Preview: This feature helps you assess the focal range before cutting through the material. As a result, you can ensure that it is in the right position for focal accuracy and waste reduction.
- Auto Focusing: Use this feature on a laser cutting machine for consistent, efficient, and quick focusing. This usually comes in handy for large-scale production orders, such as in the automotive industry.
- Focus Stacking: This technique combines multiple layers of the laser cutting process at different focus positions. It aids with enhanced cutting precision, improved edge quality, and suitability for complex designs and uneven materials.
What Should You Consider When Setting the Focus Position?
As a business professional, you must consider the following factors when setting the focus position:
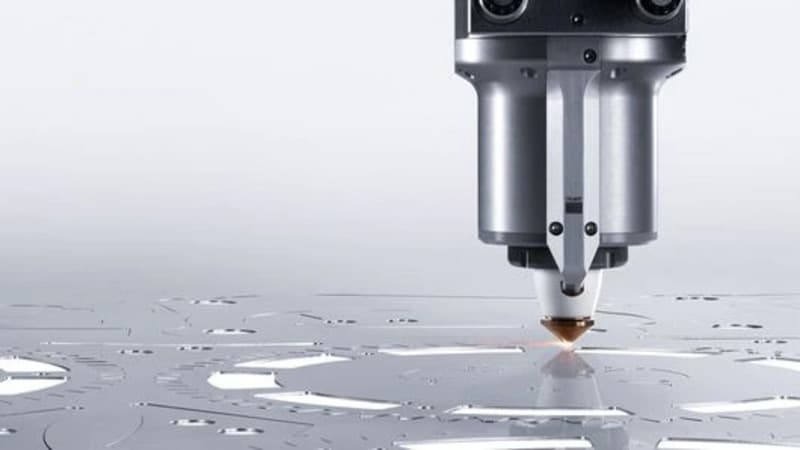
- Cutting Speed: this directly impacts the cutting focus as a slower cutting speed may require a different focus position for higher accuracy and cutting quality. Similarly, faster speeds may require a short focal length lens to achieve the same results in lesser time.
- Material Characteristics: religiously study the characteristics of the material you are cutting. Whether it is brass, copper, carbon steel, or aluminum sheets and tubes, you must know all the details to set the perfect focus position. This is because different materials require certain adjustments to the focus position to achieve optimal cutting results. If not done right, the cutting focus appears rough sometimes on the cutting surface.
- Cutting Quality: every manufacturer has set its own precedent for cutting quality. You must always aim for high, and to achieve that, you need to set the right focal position. It directly affects the cut quality, including accuracy and edge smoothness. Hence, you must ensure the focus position is set on the workpiece surface to produce the desired level of quality for the specific application or order.
- Production Volume: every time you work with an advanced laser cutting machine, you have to have focal position options: autofocusing or manual focusing. Based on the production volume, you can go for either. For instance, if the volume is extremely high, it is recommended to choose auto-focusing for consistency throughout the batch.
- Operator Experience: the more experience the operator has, the more expertise they have to produce superior results with manual focus. As a result, the operator experience greatly influences the focusing technique. Technicians who are just at the beginning of their careers must consider taking help from auto-focusing until they have solid experience in handling manual focus.
- Efficiency is another important area because cutting focus at the right settings ensures speedy, optimized, clean results on the cutting surface. On top of it, it also helps reduce waste. Hence, the most efficient technique for the success of laser cutting would be the best.
Common Mistakes in Finding the Ideal Focus Position
Often manufacturers make some common mistakes when finding the ideal focal position. These include:
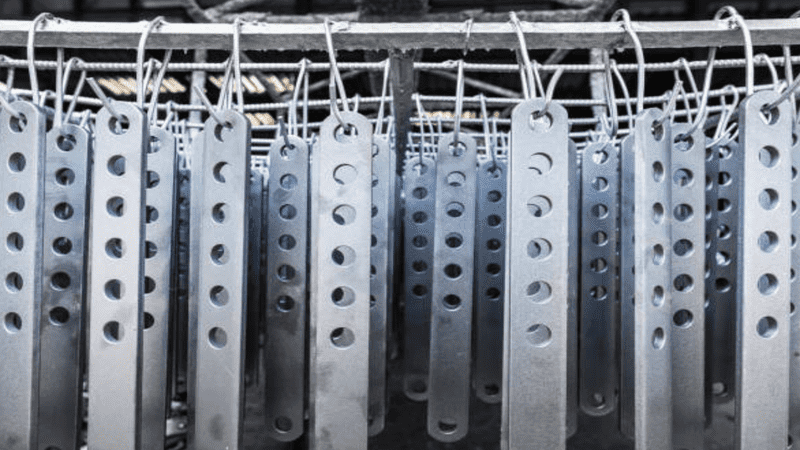
Not Taking into Account Laser Beam Quality and Power
Ignoring the impact of fiber laser beam quality and power on the focus position can lead to inconsistent cutting results. This can also result in potential damage to the material or equipment.
Incorrect Focus Position
Neglecting to set the correct focus position can lead to suboptimal cutting results, including uneven edges, reduced precision, and increased material waste.
Not Considering Cutting Speed and Quality
Overlooking the relationship between cutting speed, quality, and focus position may result in slower processing times or compromised edge quality.
Not Adjusting Focus for Different Materials
Failing to account for varying material characteristics, such as thickness and density, can compromise the efficiency and quality of the cutting process, such as, when cutting stainless steel plates, you need to have a certain laser beams focus compared to carbon steel plates.
Conclusion
The focal position is undoubtedly one of the most vital factors for efficient laser cutting. Businesses that don’t realize the importance of this factor fall prey to material waste, uneven cuts, and low-quality results.
As a result, if you want to stay on top of quality, make sure your focus positioning game is strong. Do this by investing in a premium machine and a supportive manufacturer who helps you achieve desired results.
At Baison, we have incorporated the latest technology for focus position assistance. Additionally, we provide customer support to utilize our highly advanced machines to their full potential. If you get one from us, your business is just a step away from exponential growth. Contact us today!