This article will guide you through selecting the ideal compact cutting system for your needs, focusing on productivity and cost-effectiveness. We’ll cover essential considerations, the pros and cons of various models, and maintenance tips for consistent performance.
What Is Compact Cutting System?
A compact cutting system is a specialized tool engineered to provide accurate, efficient cutting operations in a smaller, user-friendly package. It is designed to deliver precision cuts across various materials, from metal to wood, enhancing productivity and reducing wastage in production processes.
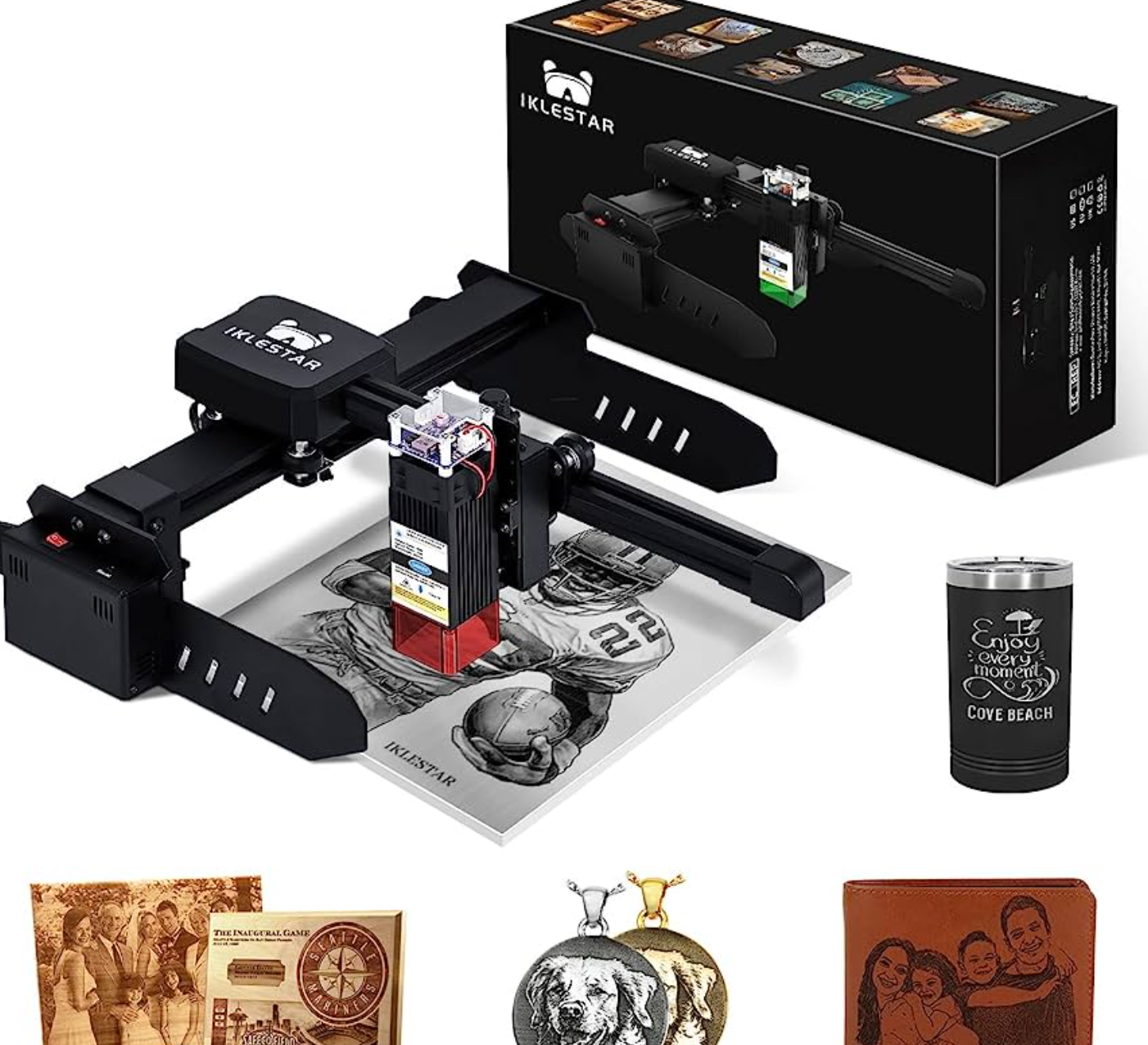
These machines integrate modern technology, such as computerized numeric control (CNC), ensuring consistent performance and easy adjustments. By reducing the footprint without compromising cutting capabilities, compact cutting systems are an excellent choice for operations where space is a premium or a diverse range of cut materials is required.
Types of Compact Cutting Systems
Like any other advanced machine, compact cutting systems come in various types. Each type of system boasts unique features and advantages. Hence knowing them helps to find the ideal match for your specific needs:
Electronic Cutting Machine
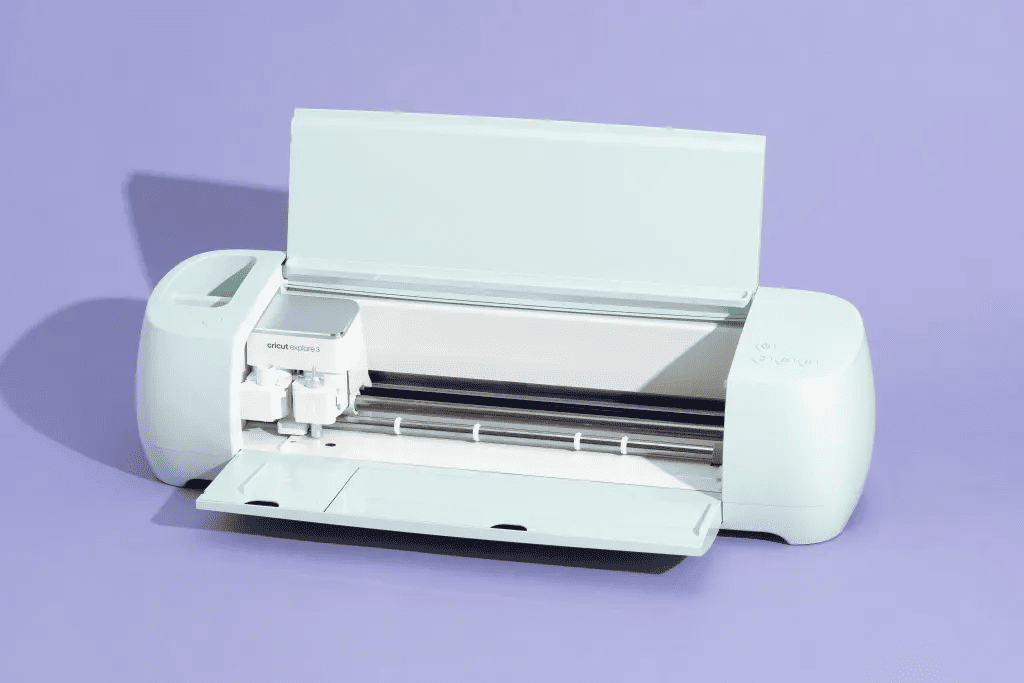
Often connected to a computer or a standalone device, electronic cutting machines utilize pre-programmed designs to cut various materials. They offer high precision and repeatability and can handle complex shapes easily. Moreover, they have a software-controlled cutting process, ensuring accurate cuts for intricate designs.
Clamp Edge Cutting System
The clamp-edge cutting system is popular for its ability to secure the material firmly during the cutting process. For imagination, the clamping end holds the material in place while the cutting tool, often a saw plate or blade, glides along the fixed center molded channel. This leads to straight-edge, clean cuts with less chance of slippage or errors.
NGX Compact Set
The NGX Compact Set is renowned for its flexibility and ease of use. This compact cutting system comes with a rip handle for easy adjustments and repeats cuts, delivering high precision in cutting various materials. Despite its smaller size, the NGX Compact Set does not compromise on accuracy and efficiency, making it an ideal choice for businesses needing frequent, repetitive cuts.
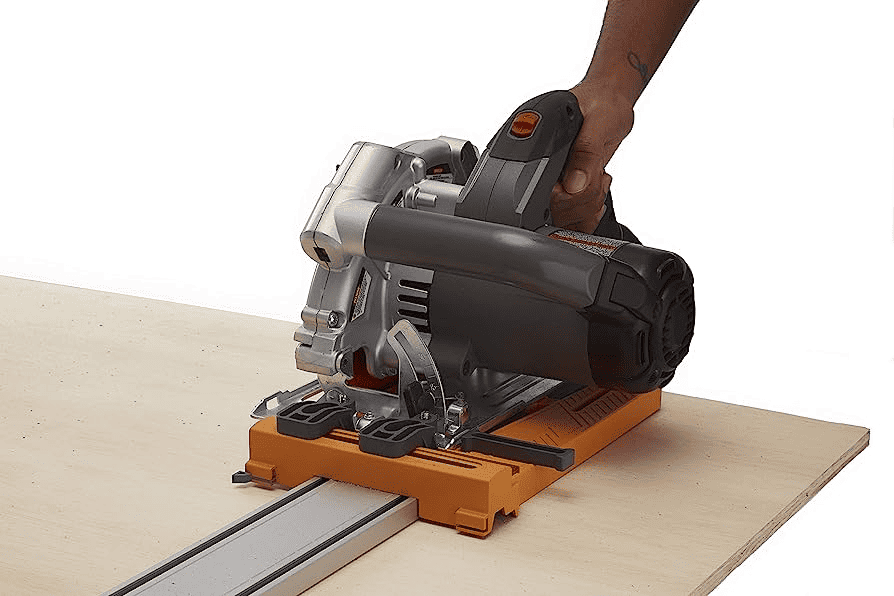
Plate Reduces Blade Offset System
The plate-reduced blade offset system focuses on minimizing blade offset, leading to more accurate cuts. The system has a mechanism where the blade’s position can be adjusted relative to the cutting line, ensuring that the cut material’s edge is straight and clean.
Factors to Consider When Choosing a Compact Cutting System
Deciding on a compact cutting system is not just about choosing the first system that catches your eye. Several considerations come into play to ensure your investment yields the expected returns. The wrong choice could lead to operational inefficiencies, escalated costs, and even safety concerns. Understanding the key factors influencing your decision is, therefore, critical. Here are a few to keep in mind:
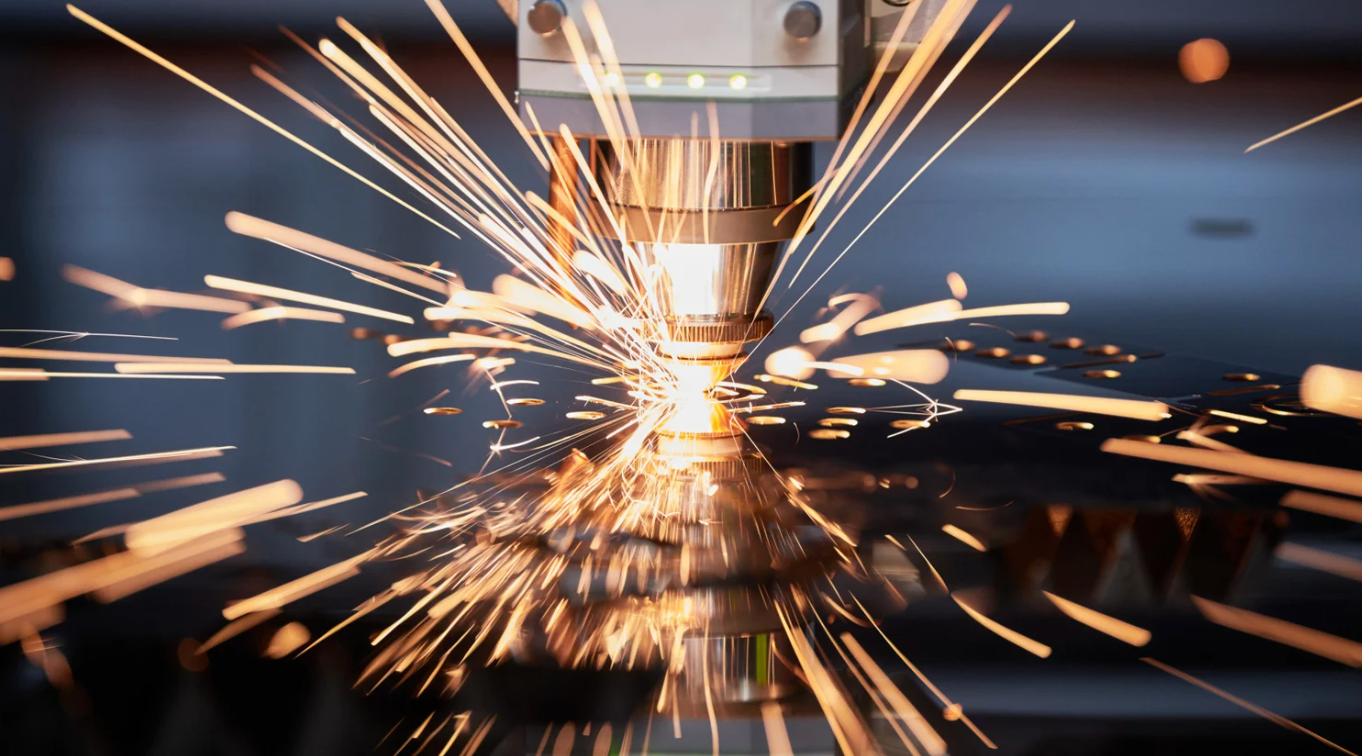
Type of Materials
The materials you intend to cut significantly influence your choice of a compact cutting system. For example, a clamp edge system might work exceptionally well with wood but not as effectively with metals. Talk to the manufacturer to ensure the cutting system is designed to handle your specific materials and achieve your desired finish. Make sure your clamp edge moves as it helps with adjustments
Cutting Speed and Accuracy
Speed and accuracy are integral to production efficiency. Where a system that delivers accurate cuts at high speeds boosts productivity and reduces waste. Hence, you should consider systems like the NGX Compact Set, which offers easy adjustments for accurate and repeat cuts.
Maintenance and Support
The longevity of your cutting system greatly depends on the maintenance it requires. Consider the associated maintenance costs, the service life of the machine, and the availability of after-sales service from the manufacturer.
User Interface and Customization
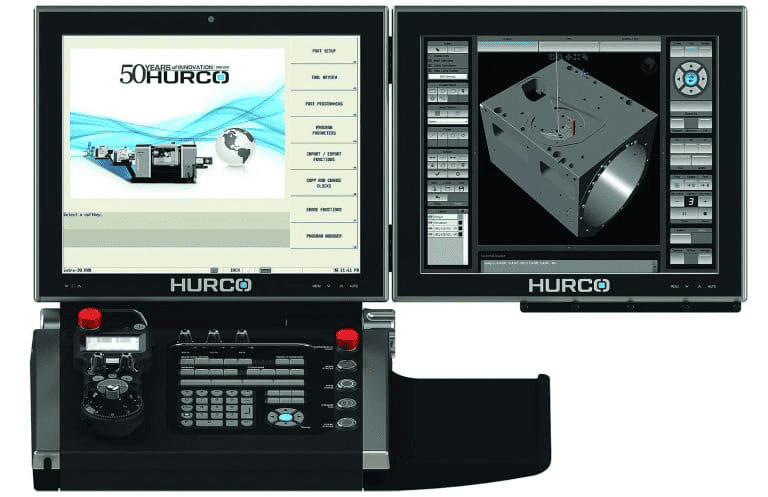
An intuitive user interface is essential for easy operation and minimizing errors. Opt for systems that allow for customization based on your cutting needs. Fortunately, electronic cutting machines often come with specialized software for this purpose.
Cost and ROI
Evaluate the cost of the machine against the return on investment. While the initial investment might be high, the operational efficiency and production volume can justify the cost. Remember, an economical machine isn’t always about the lowest price but about long-term profitability and productivity.
Safety
Safety should never be compromised. Look for systems that incorporate safety measures such as stable clamping ends, secure blade positioning, and safety protocols during operation.
As you navigate the maze of compact cutting systems available, consider these factors. Your choice should align with your operational needs, budget, safety standards, and the type of materials you frequently work with. Only then can you truly unlock the potential of a compact cutting system in your production process.
The Steps for Selecting a Right Compact Cutting System
Let’s get our knowledge of the factors and types mentioned above to play. Here is a systematic step-by-step approach that considers the key factors we discussed earlier. It will help you find a machine that not only meets your current needs but also has the flexibility to cater to your future demands:
Determine Your Needs
This should always be your first step. Understand what you’re looking for in terms of material compatibility, cut accuracy, speed, and capacity. For instance, if you work mostly with metal materials, a machine equipped with a strong blade and a fixed center molded channel for stable cutting should be among your top choices.
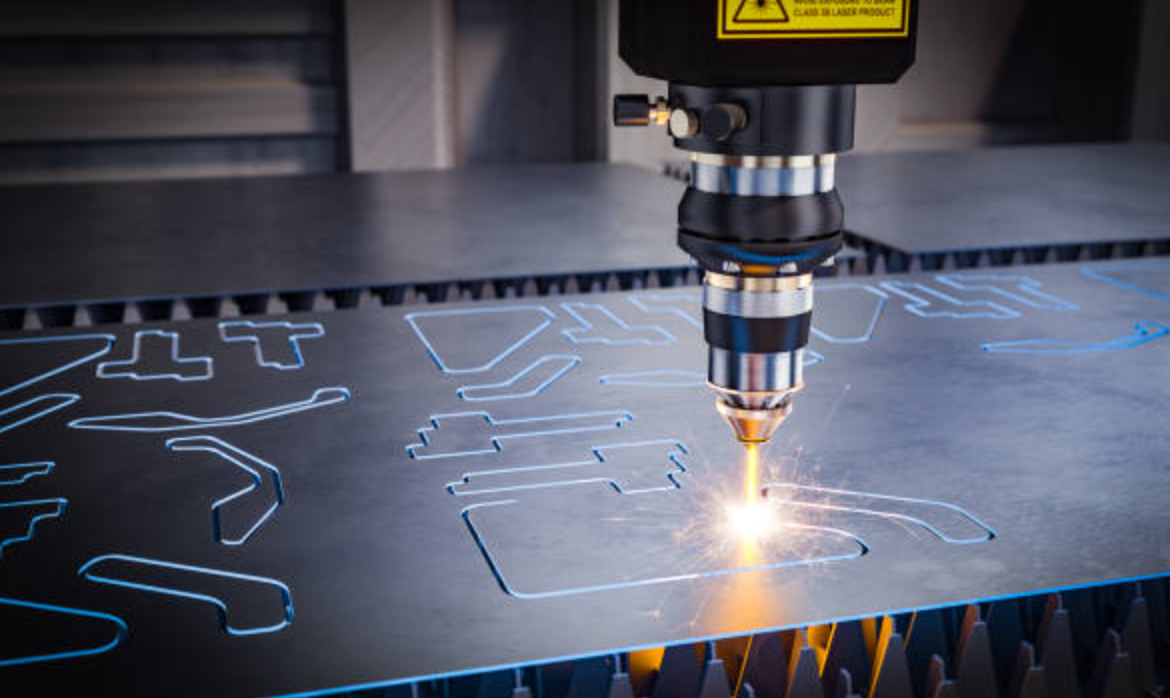
Do Your Research
Armed with a clear understanding of your needs, start researching various compact cutting systems. Utilize online resources, read product reviews, and study product descriptions. Pay attention to the systems’ features that ensure high cutting speed and accuracy, easy adjustments, and repeatable and accurate cuts.
Visit a Showroom or Demo a Machine
Seeing is believing. If possible, visit a showroom to see the machines in operation or request a demo. This hands-on experience will give you a better understanding of the system’s functionality, its ease of use, and whether it fits within your workspace. This step will help assess the machine’s user interface and customization options.
Get Recommendations
Talk to people who are already using compact cutting systems. They can provide first-hand insight into the machine’s performance, durability, and after-sale service. This information will be crucial in understanding the kind of maintenance and support you can expect from the manufacturer.
Consider the Future
While addressing current needs is essential, you should also consider your future requirements. If your business plans to expand or diversify the types of materials to cut, ensure your chosen system can accommodate these changes. This ties back to the factor of cost and ROI, as investing in a future-proof system can yield higher returns in the long run.
Take a Test Drive
If possible, test the system with your materials and designs. This will give you an idea of the machine’s actual performance. Observe the accuracy of cuts, the ease of adjusting the system, and whether the plate securely clamps the material, contributing to the safety of the operations.
Applications of the Compact Cutting System
Compact cutting systems, specifically laser cutting and welding machines, have diverse applications across multiple industries. Here’s how some sectors leverage these systems:
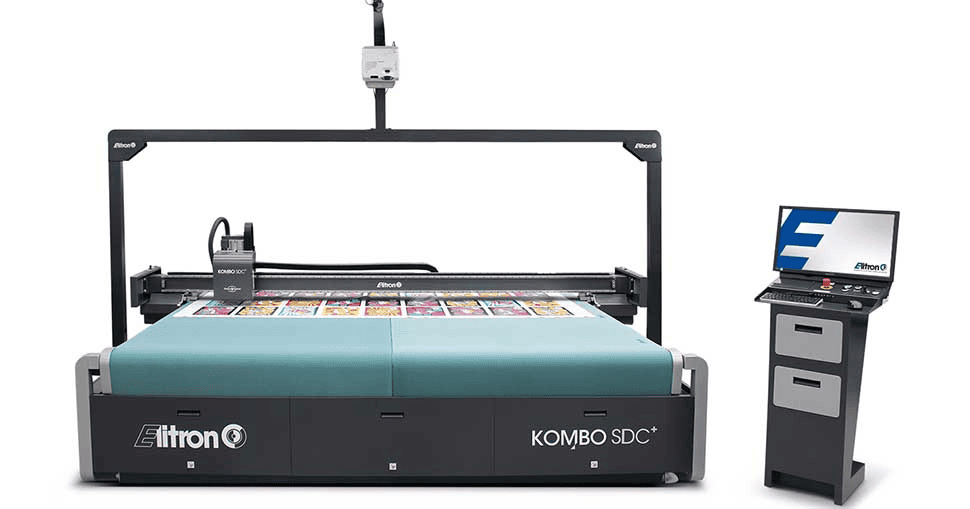
- Metalworking: Laser cutting systems excel in the metalworking industry, being capable of processing a variety of metals, including brass, stainless steel, and aluminum. They’re used for tasks such as sheet metal fabrication, pipe cutting, and parts production for machinery and vehicles, delivering precision and consistency that is hard to match.
- Automotive Manufacturing: Laser cutting and welding machines play a crucial role in the automotive industry. They are used to cut and weld components with high precision, contributing to the production of more efficient, reliable, and safer vehicles. Laser systems also speed up production, allowing manufacturers to meet high demand levels.
- Electronics Manufacturing: Laser systems are vital in electronics manufacturing, where precision and accuracy are paramount. They’re used to cut and weld components, often on a miniature scale, for devices like smartphones, computers, and other digital gadgets.
- Medical Device Manufacturing: In an industry where accuracy can impact human lives, laser cutting and welding machines are invaluable. They’re used to produce a variety of medical devices, including surgical instruments and implantable devices, with an unprecedented level of precision.
- Aerospace & Defense: The strength and accuracy provided by laser cutting and welding machines are crucial in the aerospace and defense industries. They’re used to produce parts that must withstand extreme conditions, contributing to the safety and effectiveness of aerospace and defense equipment.
Benefits of Choosing the Right Compact Cutting System
Choosing the right compact cutting system is not just about fulfilling your current needs; it’s about positioning your business for long-term success. The right system can streamline your processes, enhance your product quality, and boost your bottom line. Let’s take a closer look at these benefits:
Efficiency
Accurate and repeat cuts reduce the need for rework, increasing production efficiency. For example, efficient laser cutting systems in the automotive industry can expedite the production line, helping to meet market demand.
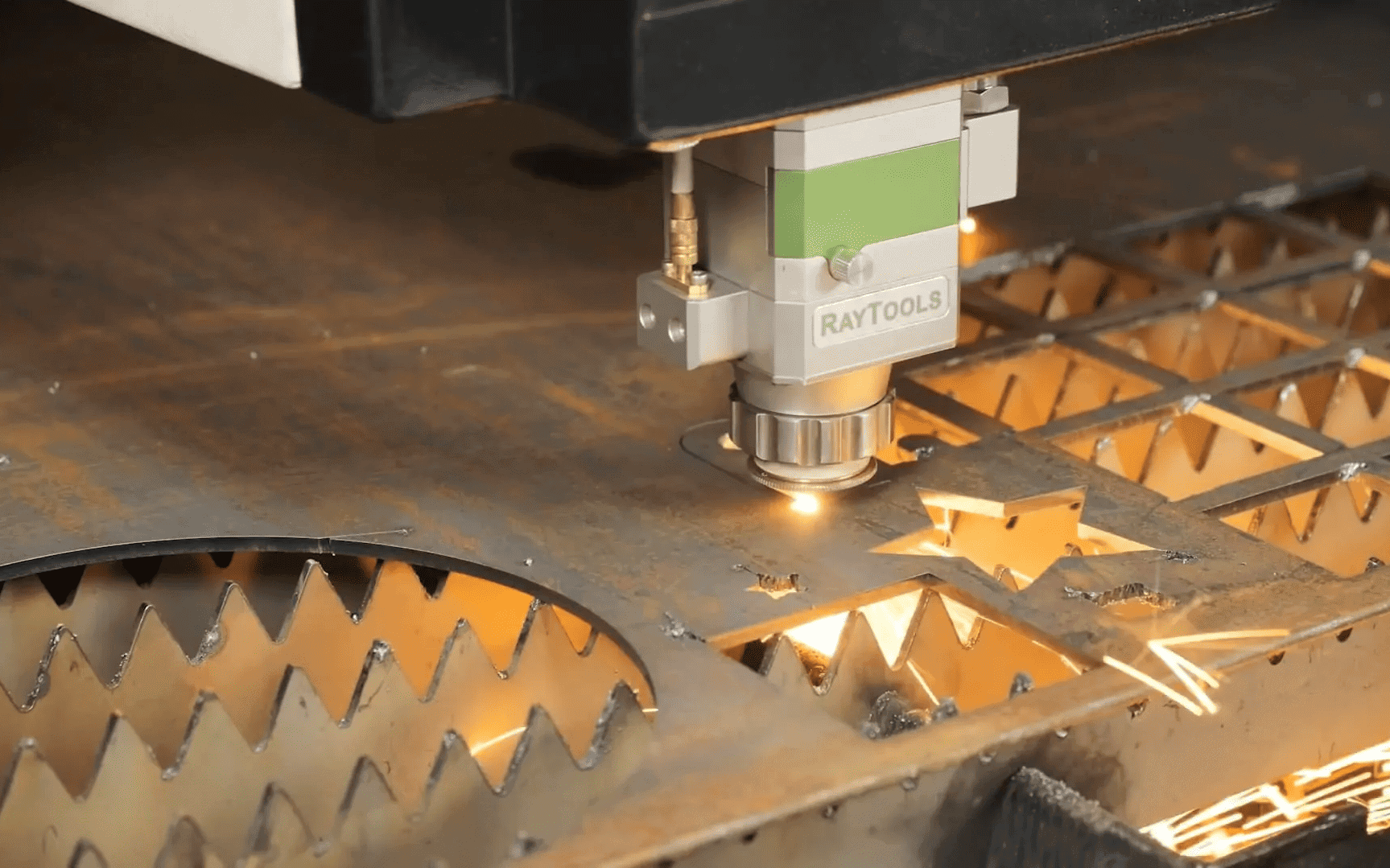
Quality
Consistent precision leads to higher quality products, enhancing your brand image. This is particularly true in the electronics industry, where high-quality cuts contribute to the overall functionality and aesthetics of devices.
Versatility
With the ability to cut a range of materials, you can diversify your product offerings. In metalworking, this versatility allows businesses to work with a variety of metals, enhancing their service scope.
Cost Savings
Lower maintenance costs and reduced waste can significantly cut down operational expenses. In the textile industry, minimizing fabric waste can lead to considerable savings over time.
Safety
High-quality systems come with enhanced safety features, protecting your staff and minimizing workplace accidents. This is particularly relevant in industries like metalworking, where operator safety is paramount.
Ease of Use
Intuitive user interfaces and easy adjustments make these systems simple to operate, even for beginners. This user-friendliness can save time and effort in training new employees, particularly in sectors like signage, where designs can be complex.
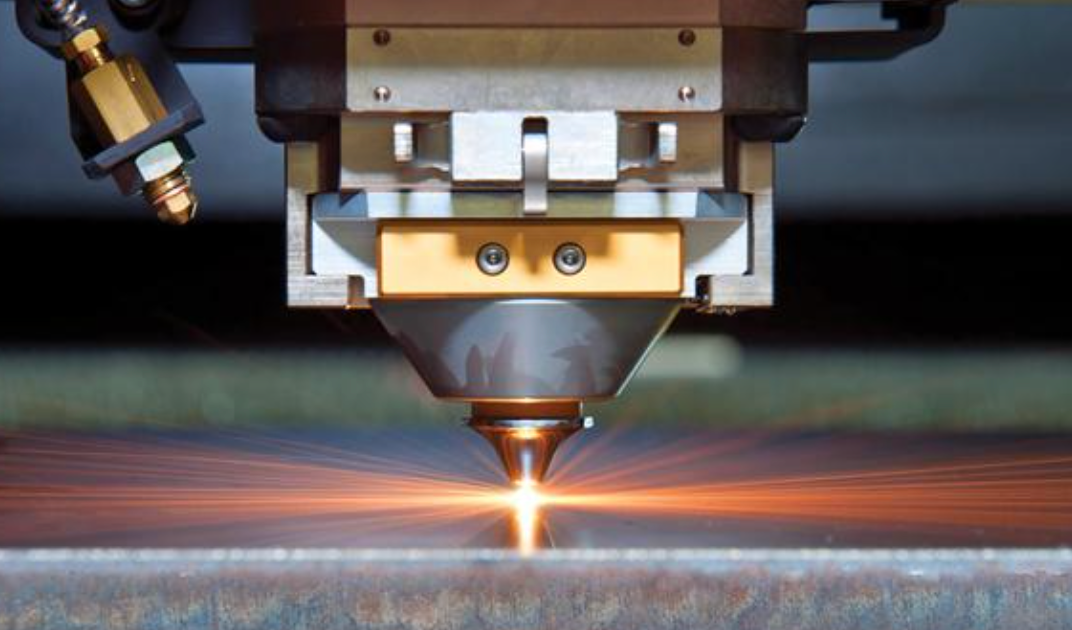
Future-Proof
The right system can adapt to your future needs with customizable features and upgradable software. This is particularly valuable in fast-paced industries like electronics manufacturing, where adapting to new technologies is crucial.
Q&A: Common Questions About Choosing Compact Cutting Systems
Q: What materials can a compact cutting system handle?
A: Compact cutting systems are versatile, handling a variety of materials, including metal, wood, plastic, textiles, and even food items. However, the exact range depends on the machine’s specific capabilities and settings.
Q: How important is cutting speed?
A: Cutting speed affects your production rate and efficiency. Faster speeds can increase output, but accuracy and quality shouldn’t be compromised. Balancing speed with precision is crucial.
Q: How can I ensure the longevity of my compact cutting system?
A: Regular maintenance, following manufacturer guidelines, and ensuring trained operators use the machine properly are key to extending your system’s lifespan.
Q: Is it worth investing in a high-end compact cutting system?
A: High-end systems often offer superior accuracy, speed, and versatility. They may also come with additional features and better support. Consider your needs, budget, and return on investment.
Q: Can I upgrade my compact cutting system in the future?
A: Many systems offer upgradability, especially in terms of software. Check with your manufacturer about future upgrade options to future-proof your investment.
Conclusion
In conclusion, choosing the right compact cutting system requires thoughtful consideration of your specific needs, thorough research, and making informed decisions. The benefits of this careful process are considerable: efficient and accurate cuts, versatility, cost-effectiveness, and a machine that evolves with your needs. Remember, the right equipment is an investment in your success.
Boost Your Production with Precision!
Baison Laser, as your trusted industry partner, is committed to providing you with optimal compact cutting solutions. Whether you need a free application evaluation or want to see our systems in action with free sample proofing, we’re ready to assist. Don’t wait—contact us today to elevate your production capabilities.
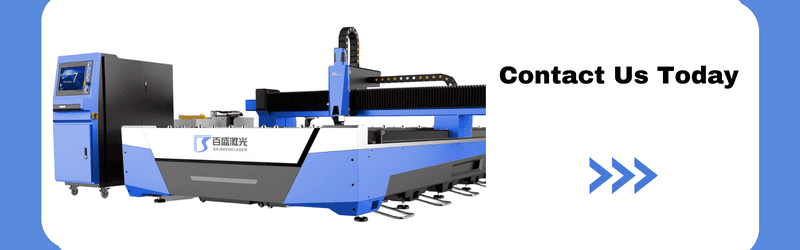