Whether you’re working on a small DIY project or a large-scale industrial operation, laser-cutting aluminum is a viable method. Its versatility makes it suitable for various applications, from aerospace engineering to architectural design. So get ready to open up new possibilities in metal fabrication with laser technology and CNC cutting machines.
Aluminum’s Reflective Nature: Challenges and Solutions
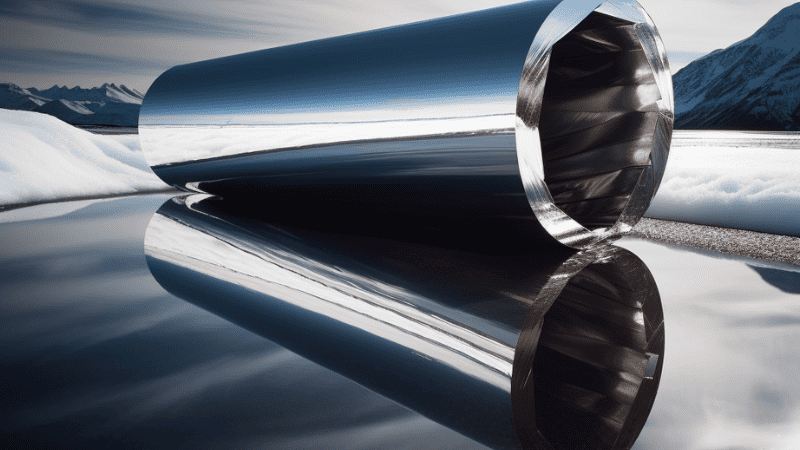
Aluminum’s High Reflectivity Poses Challenges for Laser Cutting
Engraving aluminum with a laser cutting machine can be challenging due to the metal’s high reflectivity. The reflective nature of aluminum makes it difficult for the plasma machine to cut through the material effectively.
Overcoming Energy Absorption Issues with Shorter Wavelength Lasers
Special techniques are employed to overcome the challenges of aluminum’s reflective nature in laser cutting processes. One effective solution is using lasers with shorter wavelengths for engraving on metal. Shorter wavelength lasers have higher energy levels, allowing them to penetrate through the reflective surface of aluminum more effectively. By utilizing this technique, aluminum processing becomes more efficient and precise.
Enhancing Laser Absorption with Anti-Reflection Coating
Another way to improve laser absorption on aluminum surfaces is to coat them with an anti-reflection layer. This coating helps reduce the energy reflected from the material, increasing absorption and making it easier for lasers to cut through.
The anti-reflection layer acts as a barrier between the laser beam and the reflective surface, absorbing more energy rather than being bounced off. This technique is particularly useful for aluminum cutting, as it enhances the efficiency of water jet cutting on a cutting table by maintaining a high cutting speed.
Coating Options:
- Spray-on anti-reflection coatings
- Vacuum deposition of thin films
- Dip coating methods
Alloying Elements and Their Impact on Laser-Cutting Aluminum
Aluminum alloys often contain various alloying elements that can affect their laser-cutting properties. These elements are added during metal processing to enhance specific characteristics or properties of the alloy. However, they can also impact how well the material absorbs laser energy.
Examples of Alloying Elements:
- Silicon: Increases thermal conductivity in aluminum materials, aiding in heat dissipation during laser cutting of aluminum plates. Additionally, anodized aluminum is also known for its enhanced thermal conductivity.
- Magnesium: Improves machinability but may increase reflectivity.
- Copper: Enhances electrical conductivity in aluminum materials but can lead to increased reflectivity in anodized aluminum plates when exposed to a reflected laser.
Dealing with Ferrous Dust Contamination
During laser cutting, ferrous dust particles from the surrounding environment can settle on the aluminum surface, affecting the cutting process of aluminum. This contamination can worsen the challenges caused by aluminum’s reflective nature and interfere with laser absorption. It is important to address this issue when using fiber engraving machines.
Solutions for Ferrous Dust Contamination:
- Regular cleaning: Keep the cutting table and laser equipment work area clean to minimize dust accumulation for laser engraving using laser technology.
- Install effective air filtration systems: To reduce airborne contaminants using laser technology, such as fiber laser machines. These systems are especially important when working with materials like nd and aluminum.
- Protective covers: Protective covers shield the aluminum surface during laser cutting. These covers are essential when working with aluminum engraving machines, as they help protect the delicate aluminum surface from any potential damage caused by the laser fiber.
Nitrogen-Assisted Laser Cutting for Improved Results
Nitrogen-assisted laser cutting is a technique that can be employed to enhance the cutting process when working with aluminum. Several benefits can be achieved by introducing nitrogen gas into the laser beam path. Nitrogen helps prevent material oxidation, reduces burrs and dross formation, and improves overall cut quality. This technique is particularly useful for engraving aluminum using fiber laser machines.
Tips and Techniques for Efficient Laser Cutting Aluminum
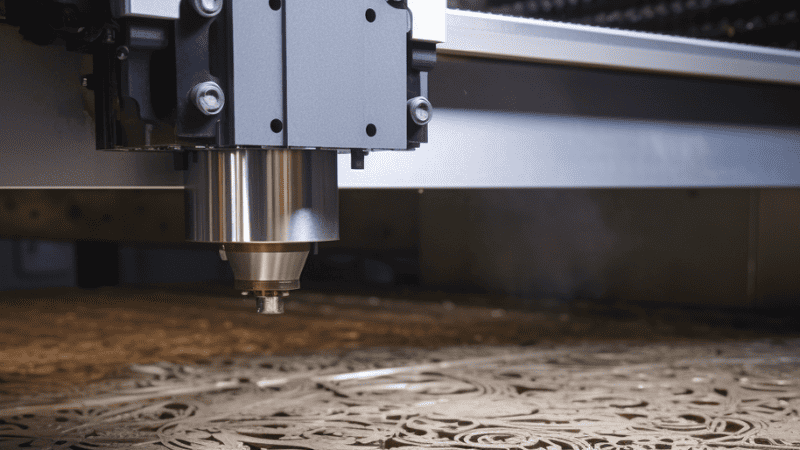
Optimizing laser parameters
Optimizing the laser parameters for machines is crucial to achieving efficient aluminum laser cutting. By adjusting the power, speed, and focus spot size, you can greatly improve the efficiency of the process. Here are some tips to consider for fiber laser cutting of aluminum machines.
- Power: Finding the right balance between power and speed is essential in optimizing your laser cutting process. Fiber laser machines usually range from 500W to 40,000W. As a general guideline, for 1mm thick aluminum, you might start experimenting with a power of around 1000W. If the aluminum sheet is 2mm thick, a power of approximately 1500W may be a good starting point. Remember, higher power levels can result in faster cutting speeds, but excessive power may lead to unwanted melting or warping of the material.
- Speed: Different cutting speeds can be used to determine the optimal setting for your specific aluminum thickness. For aluminum around 1mm thick, a typical cutting speed may be between 1 and 2 meters per minute (m/min). For 2mm thick aluminum, the speed may drop to around 0.5 to 1 m/min. But bear in mind, going too slow can cause excessive heat buildup, while too fast a speed may result in incomplete cuts.
- Focus spot size: The laser’s focal point size, typically between 0.1 and 0.2mm for fiber laser cutting machines, affects precision and efficiency. A smaller spot size, like 0.1mm, allows for finer cuts but may require slower speeds to maintain accuracy. A larger spot size, such as 0.2mm, offers faster cutting speeds but can compromise precision.
- Gas Pressure: Using assist gas, like Nitrogen or air, is also critical in laser cutting aluminum. The pressure can range from around 6 to 20 bar, depending on the thickness of the material and other cutting parameters. Higher pressures can help to eject the molten material more effectively, but overly high pressure can disturb the cutting process.
As always, conduct a series of test cuts under different conditions to find the most effective combination of parameters. Prioritize safety at all times when operating such machinery.
Using assist gases
Assist gases, such as nitrogen and oxygen, are essential in laser cutting aluminum. They help remove molten material during the process, ensuring efficient machine performance.
- Nitrogen: When nitrogen is used as an assist gas, it helps prevent oxidation during cutting, resulting in cleaner edges and reduced burrs. This is particularly useful when working with highly reflective aluminum alloys.
- Oxygen: Oxygen assists in exothermic reactions that enhance cutting speed. It reacts with aluminum to produce additional energy that aids in melting and vaporization.
Employing advanced nesting software
Maximizing material utilization and minimizing waste are key considerations when laser cutting aluminum. Advanced nesting software can help achieve these goals by optimizing how parts are arranged on a sheet before cutting. This software is essential for efficient and precise aluminum machining, as it ensures that the machine uses the aluminum fiber efficiently and minimizes any potential waste.
- Material utilization: Nesting software analyzes part shapes and sizes to determine the most efficient layout on a given aluminum sheet. By minimizing wasted space between parts, more materials can be utilized effectively.
- Reduced waste: With precise nesting algorithms, the software can minimize scrap material, resulting in cost savings and environmental benefits. By intelligently arranging parts, it reduces the need for excessive repositioning of the laser head.
Different Laser Types for Aluminum Cutting: Pros and Cons
Fiber Lasers: High Beam Quality and Efficiency
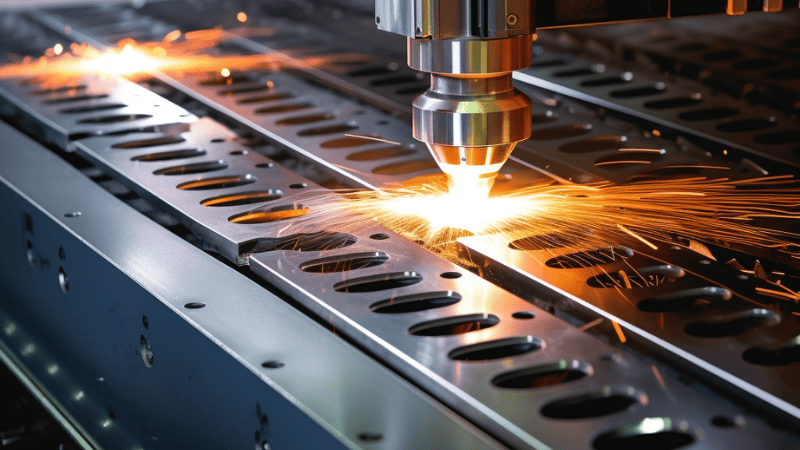
Fiber lasers are the go-to choice for cutting aluminum with a machine, thanks to their exceptional beam quality and efficiency. These lasers utilize a fiber optic cable to deliver the laser beam, resulting in precise and clean cuts on aluminum sheets. Here are the pros and cons of using fiber lasers for aluminum cutting with a machine.
Pros:
- High beam quality ensures accuracy and precision.
- Efficient energy consumption reduces operating costs.
- Suitable for thin to medium-thickness aluminum sheets.
- Fast-cutting speeds enhance productivity.
Cons:
- Limited suitability for thick aluminum sheets.
- Higher initial investment compared to other laser types.
- Fiber laser machines may require specialized maintenance.
CO2 Lasers: Versatile but Limited with Thick Aluminum Sheets
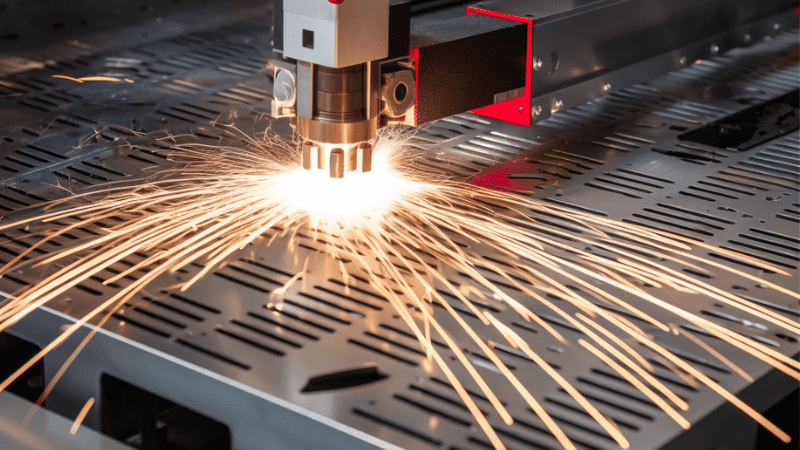
CO2 lasers offer versatility in various applications, including cutting aluminum and fiber. However, they may have limitations when it comes to aluminum cutting. Let’s explore the pros and cons of CO2 lasers for cutting aluminum and fiber.
Pros:
- The versatile laser machine type was suitable for cutting various materials, including aluminum and fiber. The cutting speed is optimized for efficient production.
- Can handle intricate designs with ease.
- A wide range of power options is available for different cutting requirements with the fiber laser machine and CO2 laser. These options cater to a variety of needs, including cutting aluminum efficiently.
Cons:
- Less efficient than fiber lasers regarding energy consumption.
- They may struggle with thick aluminum sheets due to lower absorption rates when using a fiber laser cutting machine.
- Slower cutting speeds compared to fiber lasers.
Solid-State Lasers: Excellent Precision but Not Ideal for Large-Scale Industrial Applications
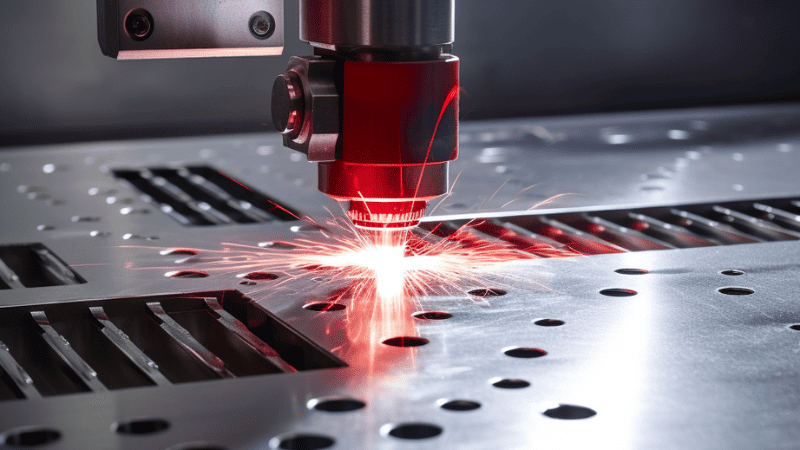
Solid-state lasers are known for their exceptional precision in cutting aluminum and fiber in various industrial applications. While they provide excellent results when working with aluminum, they might not be the best choice for large-scale operations. Consider the following pros and cons of solid-state laser machines.
Pros:
- Exceptional precision allows intricate cuts on aluminum surfaces.
- The laser cutting machine, specifically the fiber laser cutting machine, is well-suited for small-scale or detailed projects requiring high accuracy. With its advanced technology, the fiber laser machine offers precise cutting speed for efficient and precise results.
- Reliable performance over extended periods.
Cons:
- Limited suitability for large-scale industrial applications due to lower power options of the laser cutting machine. However, the aluminum industry can benefit from using a fiber laser machine for precise and efficient fiber laser cutting.
- Higher initial investment compared to other laser types.
- It may require more frequent maintenance and calibration.
Comparing Laser Cutting Aluminum with Stainless Steel and Other Materials
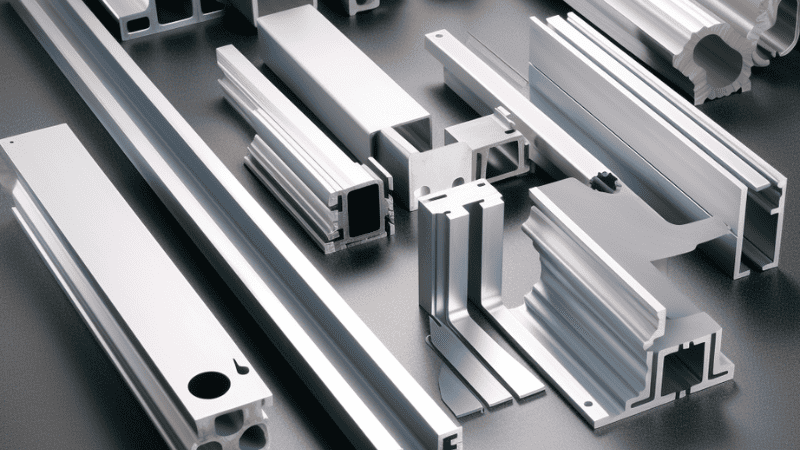
The reflective Nature of Aluminum Requires Higher Laser Power
One important factor to consider when using a laser machine is the reflective nature of aluminum. Unlike stainless steel, which absorbs more laser energy, aluminum reflects a significant amount of the laser beam. As a result, higher laser power is required to achieve clean and precise cuts on aluminum sheets or plates.
Superior Strength and Durability Compared to Wood or Acrylic
While there are various materials suitable for laser cutting, aluminum stands out. Compared with wood or acrylic materials, which may be prone to warping or breaking under stress, aluminum offers exceptional structural integrity. This makes it an ideal choice for machine applications requiring robustness and longevity.
Unique Material Properties Impact Laser Cutting Parameters
Laser cutting involves adjusting several parameters to ensure optimal results, including aluminum, based on the cut material. The unique properties of different materials, such as aluminum, affect these parameters in distinct ways. Here’s how some key factors impact the choice of laser cutting parameters for aluminum machines.
- Reflectivity: Higher laser power is necessary for effective cutting due to its reflective nature.
- Melting Point: Aluminum has a lower melting point than stainless steel or other ferrous metals. This characteristic affects the speed at which the laser moves across the material.
- Thermal Conductivity: Aluminum has high thermal conductivity, meaning heat dissipates quickly throughout the material during laser cutting. This can affect the quality of the cut edges.
- Material Thickness: The thickness of the aluminum sheet determines the appropriate focus position and nozzle size for optimal cutting results.
To achieve precise cuts when working with aluminum materials, it’s crucial to adjust the parameters of the laser cutting machine accordingly. Using a fiber laser cutting machine is particularly effective for cutting aluminum.
The Advantages of Laser Cutting Aluminum
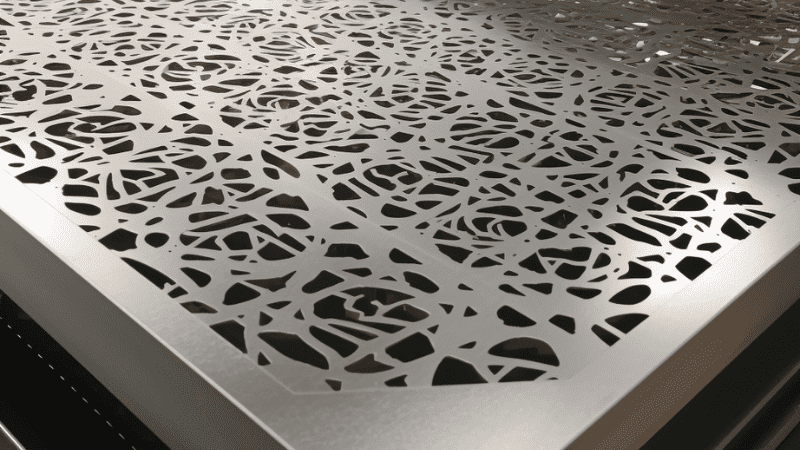
Precision
Laser-cutting technology offers unparalleled precision for cutting aluminum. The focused laser beam allows for intricate designs and cuts with utmost accuracy. Unlike traditional cutting methods that may cause distortion or warping due to excessive heat, laser cutting minimizes the heat-affected zones on the aluminum surface. This ensures that the material retains its structural integrity and prevents unwanted deformities. Laser cutting is a highly efficient machine for working with aluminum.
Speed
One of the key advantages of laser cutting aluminum is its high cutting speed. The laser machine beam swiftly moves across the aluminum sheet, making precise cuts rapidly. This significantly reduces production time compared to conventional methods such as sawing or shearing.
With laser cutting, manufacturers can complete projects in a fraction of the time it would take using traditional techniques. This increased efficiency allows businesses to meet tight deadlines and improve overall productivity.
Cost-effectiveness
While initial setup costs may involve implementing laser-cutting technology, the machine is cost-effective in the long run. Laser cutters require minimal maintenance compared to plasma or waterjet cutting methods. This translates into reduced downtime and lower repair expenses over time. Laser cutting eliminates the need for expensive tooling or specialized fixtures required by alternative processes, further contributing to cost savings.
Precision, speed, and cost-effectiveness make laser cutting with a machine an excellent choice for working with aluminum sheets.
Benefits at a Glance:
- High precision ensures accurate results without compromising quality.
- Fast processing speeds save valuable time during production.
- Reduced maintenance needs lead to long-term cost savings.
- Elimination of expensive tooling or specialized fixtures reduces expenses.
Overcoming Common Challenges in Laser-Cutting Aluminum
Thin Sheets
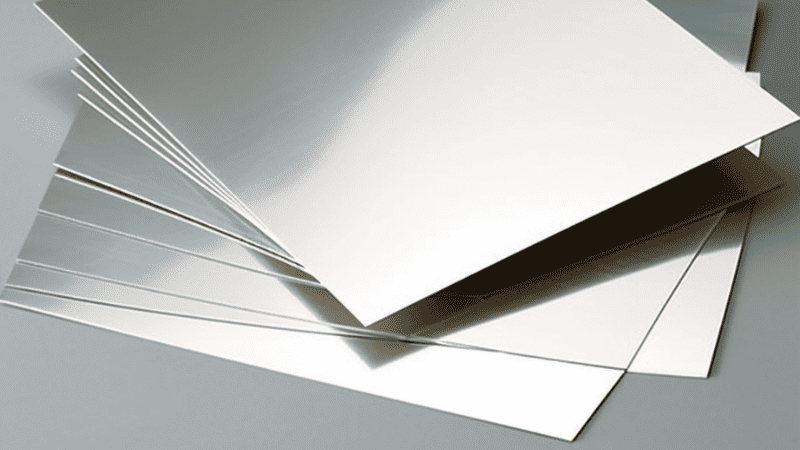
One of the common challenges in using a laser machine is dealing with thin sheets. Thin aluminum sheets are prone to distortion or warping during the cutting process if not handled properly by the machine. To overcome this challenge, it is crucial to have precise control over the laser parameters.
Here are some key considerations to prevent distortion and warping using a fiber laser cutting machine.
- Optimize laser power: Adjusting the laser power ensures it is sufficient for cutting through the thin aluminum sheet without causing excessive heat buildup. This helps maintain the structural integrity of the material.
- Control beam focus: Properly focusing the laser beam is essential for achieving clean cuts on thin aluminum sheets. An unfocused beam can result in wider kerf widths and increased chances of warping. You can minimize heat transfer and reduce distortion by ensuring a tight focus.
- Use assist gases: The choice of assist gas is vital in preventing distortion during laser cutting. Nitrogen or argon can be used as assist gases in creating an inert atmosphere around the cut, minimizing oxidation and reducing the thermal stress on the material.
- Implement cooling strategies: Heat dissipation can be challenging when working with thin aluminum sheets. Employing cooling strategies such as air or water jets directed at the cutting area helps dissipate excess heat quickly, preventing distortion and maintaining dimensional accuracy.
By carefully controlling these parameters with a laser cutting machine, you can achieve precise cuts on thin aluminum sheets using fiber laser cutting while minimizing any potential distortions or warping issues.
High Processing Cost
Laser cutting aluminum using a specialized machine involves significant costs due to various factors such as equipment requirements and ongoing maintenance needs. However, there are ways to optimize machine costs without compromising quality.
- Efficient nesting strategies: Implementing efficient nesting strategies helps optimize material usage, reducing waste and lowering processing costs. By arranging parts closely together, you can maximize the utilization of the aluminum sheet and minimize scrap.
- Process optimization: Fine-tuning the laser cutting process can lead to cost savings. By optimizing cutting speeds and power levels and assisting gas flow rates, you can achieve faster and more efficient cuts while minimizing unnecessary energy consumption.
- Regular maintenance: Proper maintenance of laser cutting equipment is essential for its longevity and performance. Regularly cleaning lenses, calibrating optics, and checking alignment ensures consistent quality and prevents costly breakdowns or repairs.
- Consider outsourcing: If your production volume is low or sporadic, it might be more cost-effective to outsource laser cutting services rather than investing in expensive equipment upfront. Outsourcing allows you to leverage specialized expertise without significant capital investment.
While laser-cutting aluminum with a machine may have higher initial costs than other methods, implementing cost-saving measures and optimizing processes can help mitigate these expenses over time.
FAQs
Q: Can laser-cutting aluminum be used for decorative purposes?
Laser-cutting aluminum is highly suitable for decorative purposes due to its precise ability to create intricate designs. The accuracy provided by lasers enables the production of complex patterns and shapes that enhance aesthetics.
Q: Is laser cutting aluminum a cost-effective method?
Yes, laser-cutting aluminum is a cost-effective method in the long run. Although initial investment costs may be higher than traditional methods, such as sawing or milling, laser cutting reduces material waste and requires less labor. This leads to overall savings in terms of time and resources.
Q: What are some common applications for laser-cut aluminum?
Laser-cut aluminum finds application in various industries, such as automotive manufacturing, aerospace engineering, electronics production, and architectural design. It creates components like brackets, panels, enclosures, signage, jewelry, etc.
Q: Are there any limitations to laser cutting thin sheets of aluminum?
Special care must be taken when using a fiber laser cutting machine to prevent warping or distortion. Delicate handling techniques should be employed along with appropriate power settings to ensure precise cuts without compromising the integrity of the material.
Q: Can laser-cutting aluminum replace other traditional fabrication methods entirely?
While laser cutting offers numerous advantages over traditional fabrication methods like sawing or milling, each technique has strengths and limitations that need consideration depending on project requirements.
Q: Does laser cutting aluminum produce harmful fumes or toxins?
Laser-cutting aluminum can produce fumes and particles, especially coated or painted materials.
Conclusion
While laser cutting aluminum poses challenges, it can be readily managed with the right equipment and expertise. Baison’s state-of-the-art fiber laser cutting machines offer a seamless blend of precision, efficiency, and versatility, making them ideal for all aluminum cutting needs.
Invest in a machine that’s designed to bolster your success. Don’t let the complexities of laser cutting hold your business back. Harness the power of Bison’s cutting-edge technology to enhance your production and efficiency.