What is Laser Cutting?
Laser cutting is a manufacturing process that uses a laser to cut materials, usually by melting them. Laser cutting works by directing the output of a high-power laser beam at the material to be cut. The focused laser beam melts or vaporizes the material, causing it to break away from the surrounding area. The beam is guided along the desired path by using mirrors and lenses.
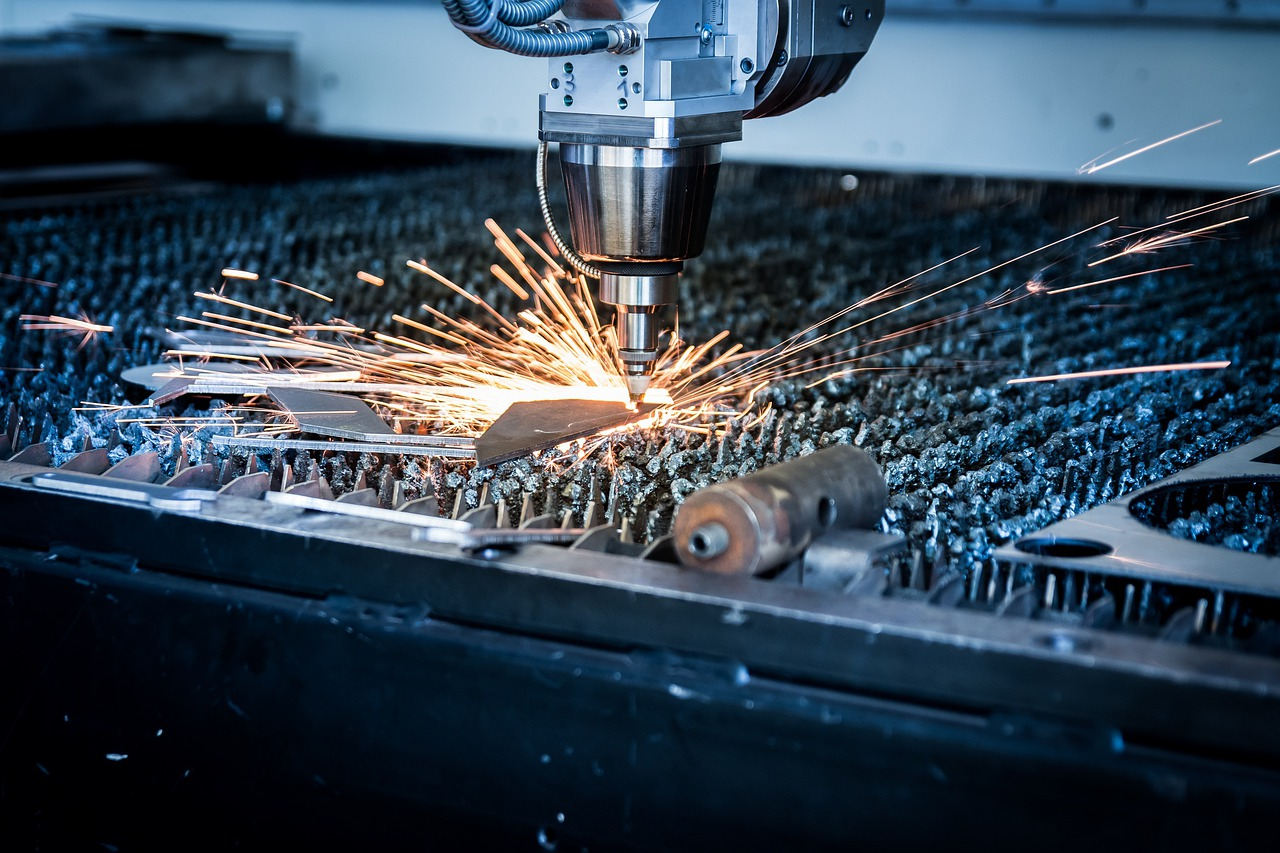
Applications of Laser Cutting
Laser cutting can melt and shape metals from mild to stainless steel and non-ferrous metals. This cutting technique is best suited for non-reflective materials. However, fiber lasers can be used with reflective metals such as silver and aluminum. Laser cutters are widely used in the automotive and aerospace industry. Thanks to programming and automation, this system allows for the bulk production of metal parts.
Lasers offer fast cutting while maintaining quality and accuracy. This cutting process is, therefore, suitable for the medical industry, where speed and tight dimensional tolerances are critical. It is used when manufacturing various medical equipment and even components for surgical implants.
Lasers have been a game-changer in the world of engraving and marking. Thanks to their pinpoint accuracy, detailed etching that would otherwise take hours can now be completed quickly. This technology is, therefore, a great choice when making metal signs, jewelry, or logos.
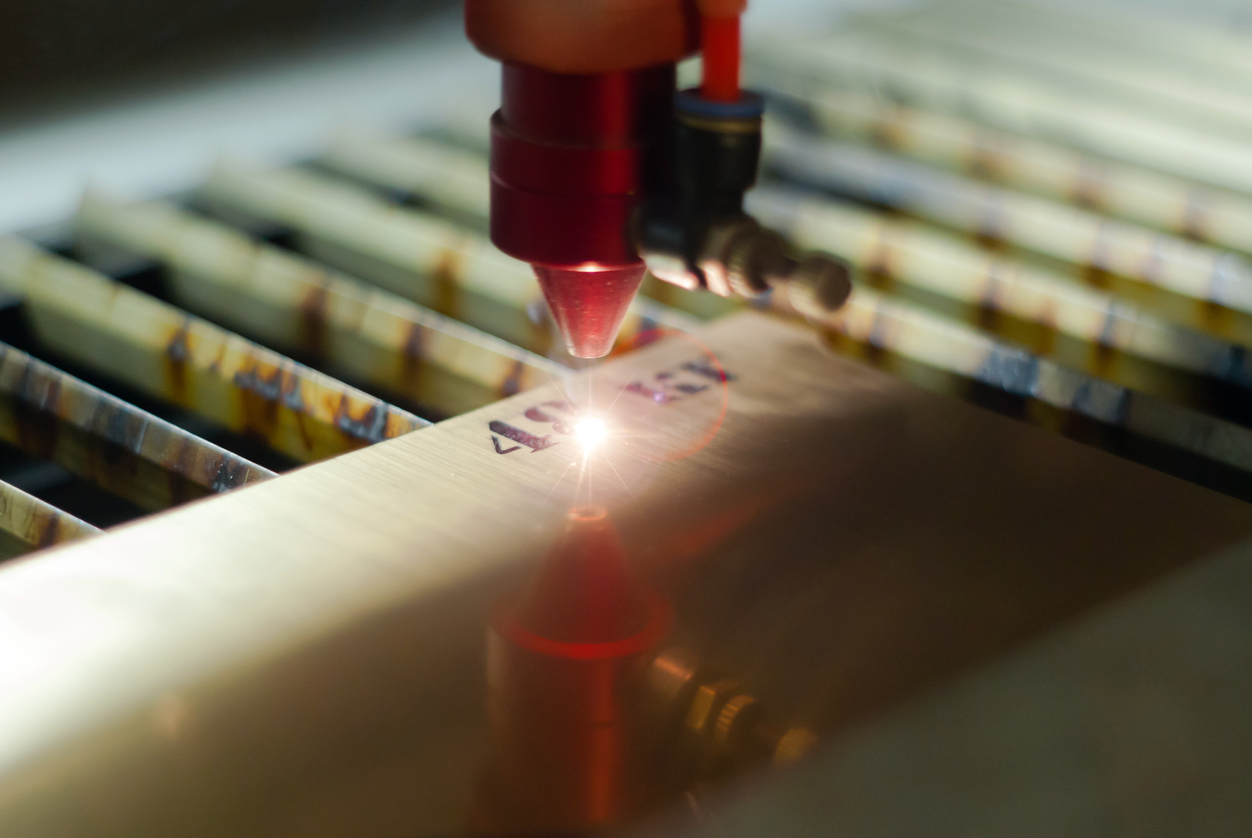
Silicon is a critical component in various electronics, solid-state semiconductors, and much more. Lasers are one of the primary methods of cutting this indispensable material.
What is EDM Cutting?
Also known as spark machining, Electrical Discharge Machining (EDM) is a metal fabrication technique that uses electrical discharges to cut materials.
A wire EDM machine features two electrodes; the tool electrode and the workpiece. The electrode is made from brass, copper, graphite, or other conductive materials. Inside the machine, the wire electrode has an electrical charge opposite the workpieces. Sparks are created as the electrode gets closer to the workpiece, and the heat will melt the material.
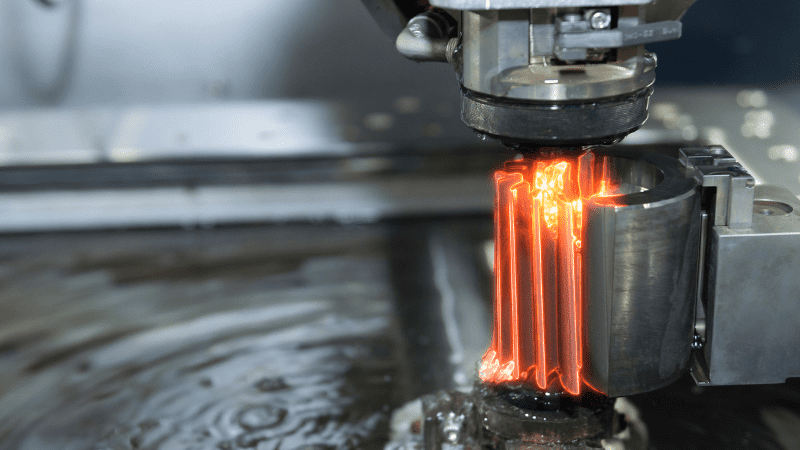
The dielectric fluid, or coolant, is another critical component of the wire EDM process. It acts as a flushing agent and removes the eroded debris from the spark gap area.
Applications of Wire Electrical Discharge Machining
Wire-cut EDM is cost-effective when it comes to small-volume production. This makes it an excellent choice for prototype production. This cutting technology is also utilized in the aerospace, automotive, and electronics industries when the number of parts required is low.
With EDM systems, you can create highly detailed products with intricate designs. Jewelers will therefore use this machining process to create elaborate pieces.
Wire EDM is suited to cutting thicker materials and thinner metal sheets. Whether cutting thick steel or relatively soft copper, this precision technique will deliver a pristine surface finish.
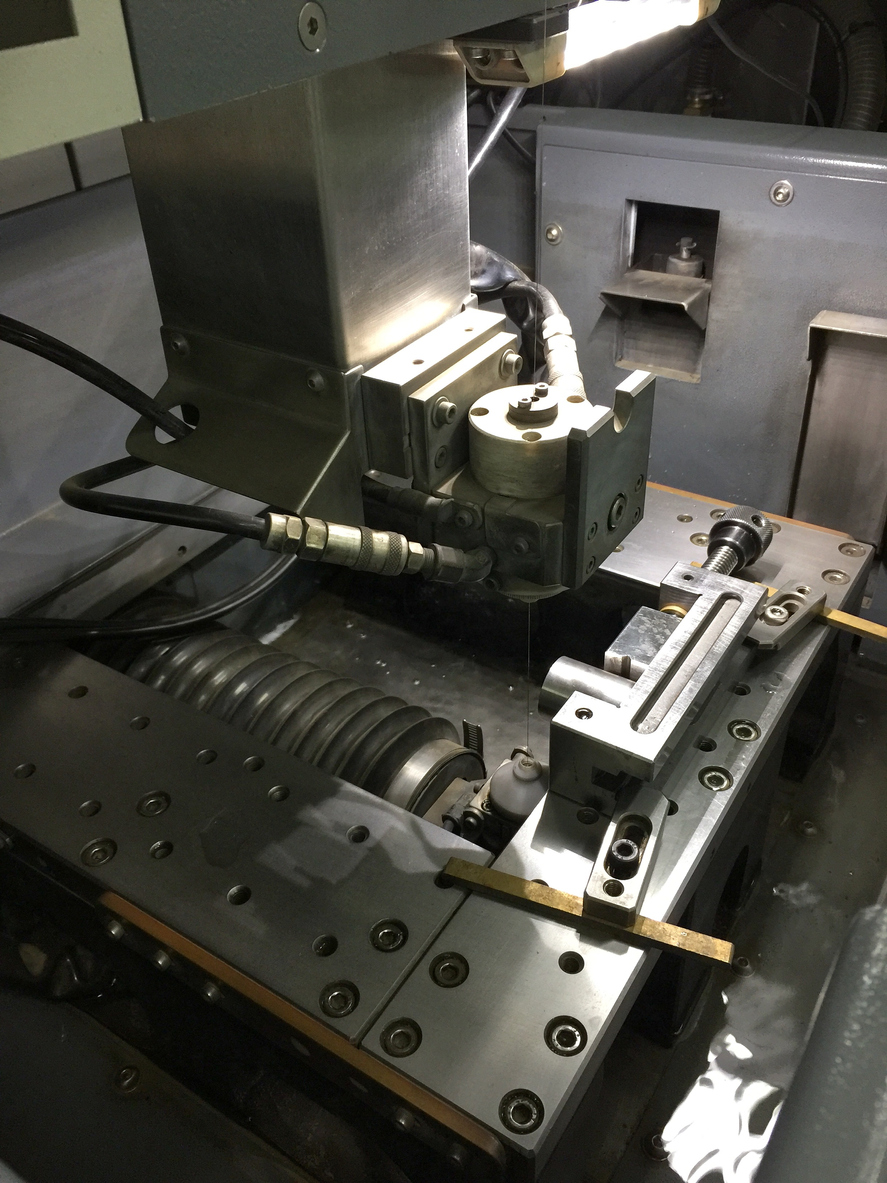
Comparison of Laser Cutting and Wire EDM Cutting
Taking these basic concepts as a background, let’s compare these two precision cutting techniques more comprehensively now.
Process of Operation
Laser cutters use an intensely focused beam of light. These high-power lasers provide heat, melting away the unwanted workpiece material.
Conversely, wire EDMs use a super-thin, electrically charged wire to remove material and achieve the desired shape. This is a no-contact process, but the charge on the wire is high enough that it creates sparks melting the material being cut.
Material
Laser technology is best suited for cutting thinner materials. It applies to many metals, including stainless steel, aluminum, gold, and silver. This process can also cut silicone, wood, plastic, and acrylic materials.
A wire EDM system relies on electricity to cut through materials. Therefore, this cutting technology is limited to metals and alloys since the workpiece needs to be conductive. Wire EDMs are the ideal solution for cutting thick metals.
Tolerances
A laser cutter can achieve tolerances of up to 0.001 inches or 0.05 millimeters when cutting thinner materials. The cutting accuracy is lower for thicker parts.
Compared to the other cutting methods, the EDM process is ultra-precise. It can achieve accuracy in the 0.0001-inch range. A wire EDM system is preferable for projects that require tight tolerances.
Cutting Speed
Laser cutters are pretty fast. This cutting process can provide volume without sacrificing quality, making it the better choice for mass manufacturing.
The Wire EDM system is much slower. Therefore, it is not suitable for bulk production.
FAQs
Is Laser Cutting Cheaper Than Wire EDM?
A laser cutter separates work materials much faster than a wire EDM cutter making it the better choice for mass production.
Further, laser cutters have no consumables, unlike wire EDM cutters, which require copper wire, molybdenum wire, and cutting coolant. These auxiliaries ultimately add to the production input cost.
What Are the Downsides of Using a Wire EDM?
A well-known disadvantage of the EDM system is its slow-cutting speed. Although this technology can achieve high precision, even when cutting thick metals, it typically takes several passes to get there.
This is a relatively expensive cutting process considering the speed and consumables involved.
A wire EDM is limited to only conductive materials.
What Is the Difference Between Waterjet Cutting and Laser Cutting?
As the name suggests, waterjet cutting utilizes pressurized water that contains abrasives to cut through materials. It can machine tolerances up to 0.003 inches, making it less precise than laser cutting.
Waterjet cutting is also slower than its laser counterpart. For more comparative information you can click on this article.
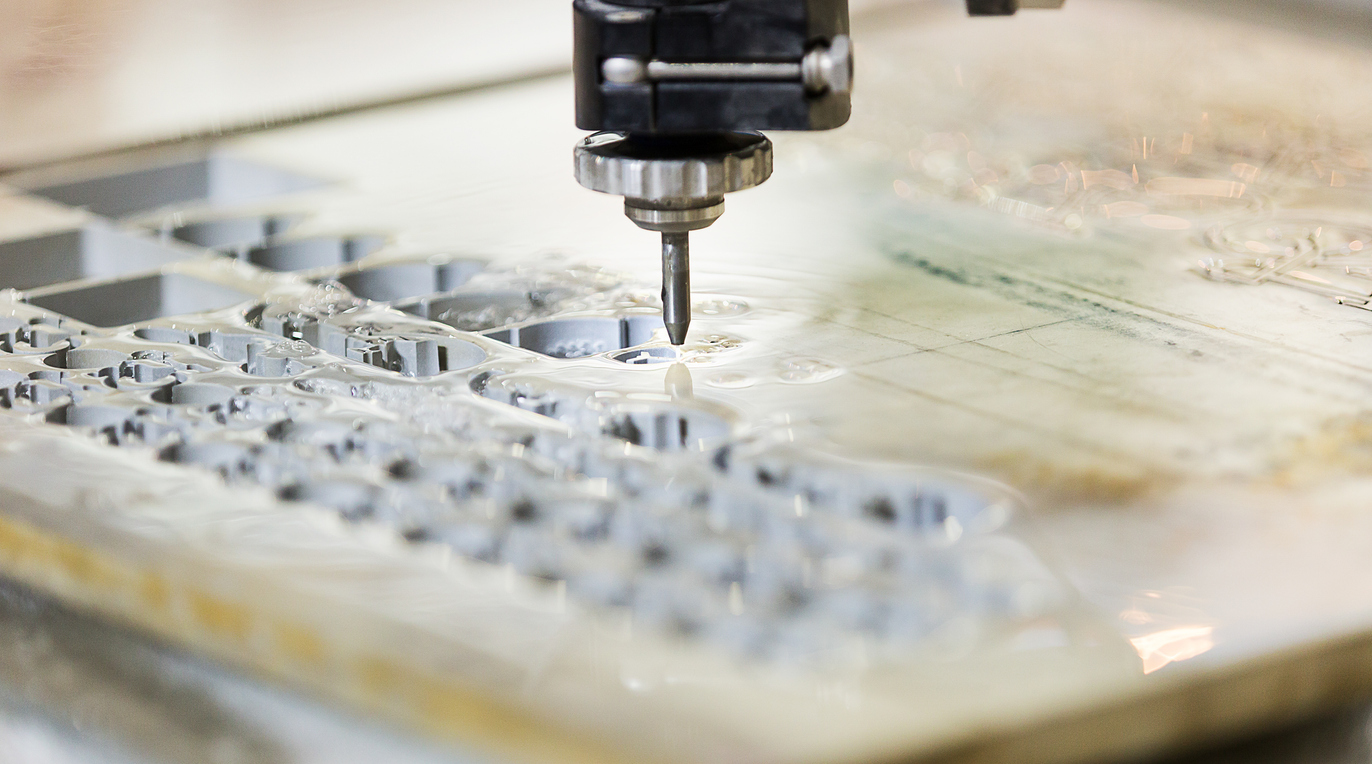
Other Cutting Methods
Other methods commonly used in splitting materials are waterjet and plasma cutting. Each of these processes comes with its benefits and applications.
Plasma cutting uses heat from a high-temperature plasma arc to melt an electrically conductive workpiece. This process can achieve tolerances in the 0.03-inch range.
Conversely, waterjets can cut metals and non-metals using a high-pressure water flow-carrying abrasive garnet.
Laser Cutting Services from Baison Laser
If you’re looking to take your business and production quality to the next level, a laser cutting system would be an excellent addition to your organization. Baison Laser is the perfect partner to help you maximize productivity.
We are a one-stop shop for all your laser cutting requirements. Our professional team is on hand to guide you through every step – from providing a thorough technical guide to installing and maintaining your laser system. Contact us today to find out more about our laser-cutting solutions.
