Basics of Laser Technology
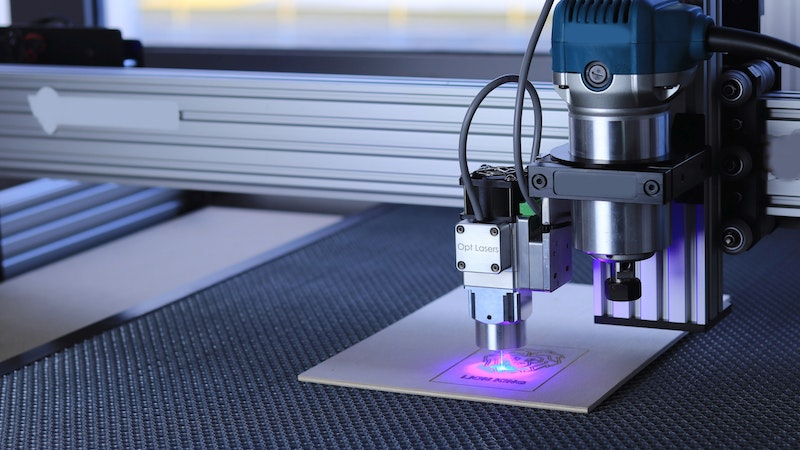
Laser-cutting technology has been around since the 1960s. Since then, laser cutting machines have been used in a wide range of industries because of their accuracy, speed, and versatility.
Here’s an overview of how lasers work in cutting applications:
1. Laser Beam Creation
Laser cutting machines contain a specific material or substance known as the lasing material within the laser source (also called the laser resonator). This material can be a gas (e.g., carbon dioxide gas mixture), a chemical (e.g., coumarin and fluorescein), a solid (e.g., neodymium crystals), or optical fibers.
To create a high-intensity laser beam, energy is pumped into the lasing material using lamps or an electric current inside a closed container. This process excites the material’s tiny particles, such as atoms or molecules, so they start giving off strong and highly focused beams of light. When this happens, it causes other nearby particles to do the same.
2. Focusing the Laser
The generated laser beam bounces back and forth inside a special mirrored cavity. This concentrates the beam’s energy in an exact spot. Once the beam is strong enough, the machine sends out a single, focused, and intense beam of light that’s capable of cutting through almost any kind of material.
3. Interaction With the Material’s Surface
There are several things that could happen when the machine focuses an intense stream of light on a material’s surface:
- The material absorbs the laser’s energy, causing rapid heating.
- If the laser power is enough, it melts or vaporizes the material to create a cut or hole. The machine usually uses an assist gas (e.g., oxygen and nitrogen) to push the waste material out of the cut zone.
Computer Numerical Control, as well as laser optics, automates and controls the movement of the laser head to ensure it follows the predefined desired cutting shape and path. The CNC system communicates with the machine using a Geometric Code, which consists of detailed instructions for the machine’s movements and actions.
Diving Into DC Glass Laser Tube
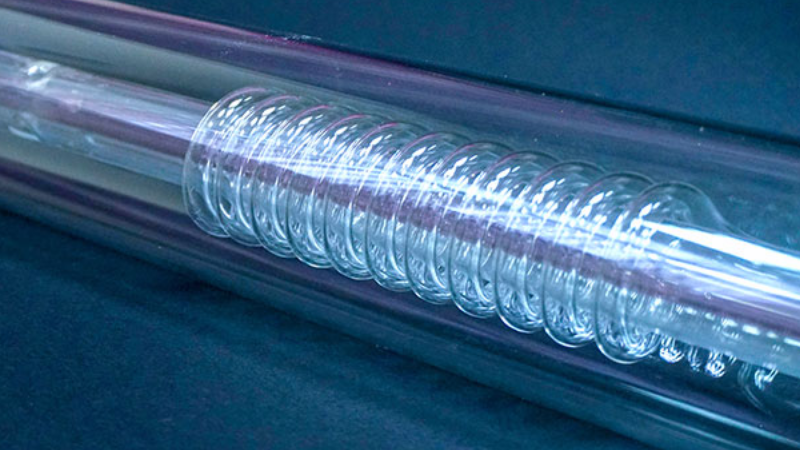
One of the main features that differentiates laser machines is their laser source. For DC glass lasers, they have water-cooled glass laser tubes. (Other machines you’ll come across use air-cooled metal tubes.) These fragile, handmade glass tubes should always have an efficient water cooling system to keep them from overheating and becoming defective.
Inside every glass tube of a DC glass laser is some type of laser gas mixture that consists of a variety of gasses:
- Nitrogen (the predominant gas in the laser mixture)
- Carbon dioxide (the active laser medium)
- Helium (which helps dissipate heat)
- Hydrogen
- Xenon
This gas mixture undergoes ionization by applying a high-voltage DC discharge to the electrodes in the glass tube. This causes the gasses to turn into plasma, whose presence in most glass tubes offers several benefits:
- It helps blow off melted material and debris from the cut zone, keeping the area clean.
- Since it’s a good electricity conductor, it helps ensure that there’s a continuous electrical path for the laser beam.
- The machine can cut cleaner and faster because it helps the material absorb more energy.
Unraveling RF Metal Laser Tubes
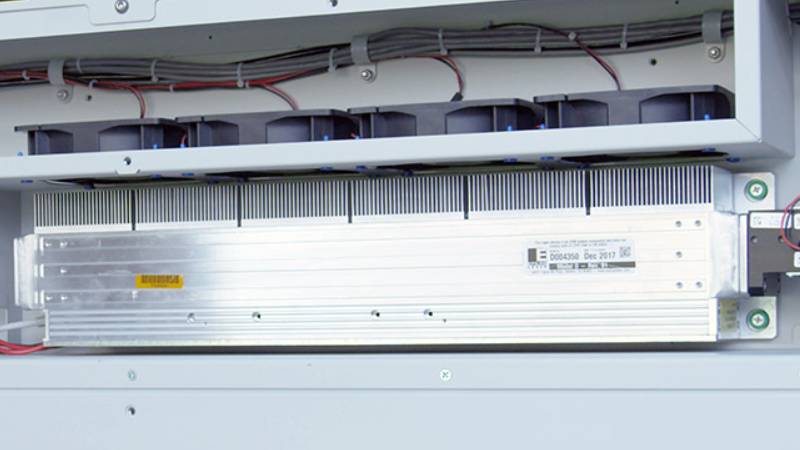
Cutting machines with an RF metal laser tube were originally used in the late 1980s for highly demanding military applications. Today, RF metal lasers are the go-to choice for many industrial applications, including cutting, engraving, and welding.
The RF in the RF metal CO2 laser stands for radio frequency, which is what it uses to produce an ionized gas plasma that ensures a clean and precise cut. Once this radio frequency hits the electrodes on each end of the RF tube, it generates an electric field that excites the gas mixture within the RF laser tube.
During this excited phase, some of the stimulated gas molecules return from a higher energy level to a lower energy level. When this happens, a burst of energy is released in the form of photons (or light energy). The released photons bounce off mirrors inside the laser cavity and eventually escape as intense laser light.
Comparison Between DC Laser and RF Metal Laser
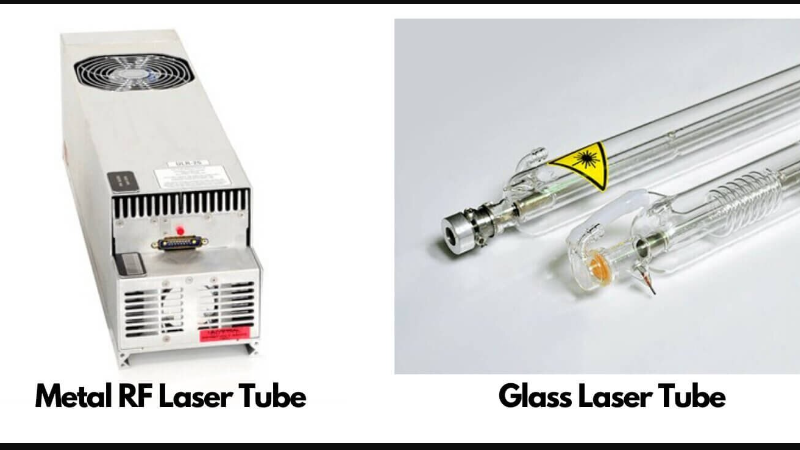
Both DC glass lasers and RF metal lasers have their pros and cons. To know which type is worth the investment, it’s important to review their key differences. Let’s go over some of them below:
Wavelength
The wavelength of a laser cutter determines how well the material being cut will absorb the light it generates. So, if the absorption characteristics of a material match those of a laser’s wavelength, it leads to faster and more precise cuts.
DC Glass Laser
A DC glass laser can release laser beams in a variety of wavelengths, usually in the near-infrared wavelength range. This means it’s more suitable for cutting and laser engraving projects that require high precision and finer detail.
RF Metal Laser
An RF metal laser operates in the far-infrared or mid-infrared wavelength, which makes it highly effective for cutting different materials.
Cut Precision
The precision of a laser cutting machine is usually directly related to its pulse rate. The common belief is that the higher the pulse rate, the higher the precision.
DC Glass Laser
In general, DC glass lasers are more suitable for applications that don’t require high precision, speed, or quality.
RF Metal Laser
RF lasers offer highly precise cutting performance. This is partly because they generate a smaller spot size.
Upfront Costs
DC Glass Laser
DC glass lasers tend to be a lot cheaper than RF lasers.
RF Metal Laser
RF lasers can be five to eight times more expensive than DC glass lasers.
Factors To Consider When Choosing the Right Laser Machine
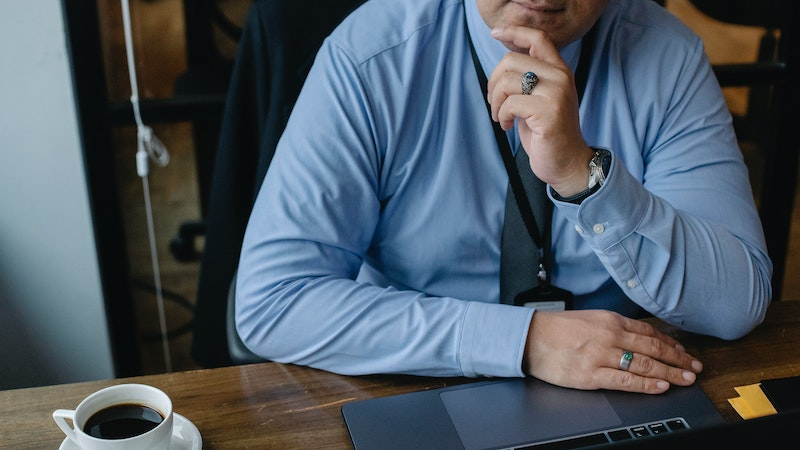
Buying a laser cutting machine is a major investment. So, it’s only right to do your research to ensure that your one-time payment won’t lead to expensive maintenance and repair costs down the line. Below are just a few things you need to consider before buying any laser machine.
Application and Material Compatibility
Each material will react differently to each laser cutting machine. For instance, if you mostly process many types of metals, RF metal lasers are more suitable options and are more commonly used compared to DC glass lasers.
Production Capacity
The production capacity of DC and RF lasers depends on several factors, including the power output, the specific model you’re going to buy, and the intended use. To make sure you get a laser cutter that fits your needs, always consult with the manufacturer or supplier.
Safety Features
This is often overlooked but should, in our opinion, be one of the first things you need to consider. Look for interlock systems, emergency stop buttons, protective enclosures, and safety interlocks for access doors, among others.
For more detailed tips on buying CO2 laser cutting machines, click here.
Conclusion
DC glass lasers and RF metal lasers have their advantages and disadvantages. Take your time evaluating each one, as well as your business’s long-term needs. Whatever laser cutter you end up choosing, make sure it has a longer life span and can accommodate your future production demands.
Experience the Precision of Fiber Laser Systems Today!
Are you thinking of adding the best laser cutting machine to your business? Get in touch with our team at Baison Laser today and schedule a consultation! Let’s discuss how our large selection of state-of-the-art laser cutting machines can help increase your productivity and precision.