Quick Overview
Before going into the details, check out this quick comparison between modern coil-fed processing and traditional laser cutting systems.
Characteristics | Coil-fed Laser Cutting Machine | Traditional Laser Cutting |
Small to medium-scale manufacturing | Not suitable | Suitable |
Large scale manufacturing | Suitable | Not suitable |
Production Speed | Higher | Lower |
Production Volume | Large | Small |
Material Feed | Automatic and continuous. | Manual/Semi-automatic |
Scrap Production | Less than 13% | Upto 25% |
Material Thickness | Suitable for less thickness | Suitable for thicker material |
Material Saving | Huge | None |
Storage of Raw Material | Easy | Hard |
Initial Machine Cost | Higher | Lower |
Operational Cost | Same | Same |
Overall Cost saving | Higher | Lower |
Manual Labor | No | Yes |
Why Are Coil-fed Laser Cutting Machines Better Than Traditional Cutting Systems?
Modern-day coil-fed laser cutting and blanking machines use a coil stock that continuously feeds material into the machine. Such coil stocks are attached to the laser cutting machines where the material is fed according to the requirement.
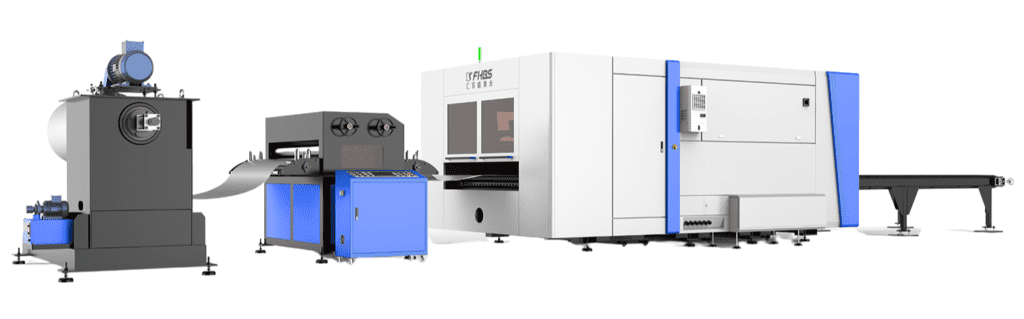
In traditional sheet-fed processes, a large rectangular metal piece of a particular length and width is fed from one end into the machine, from which various metal parts are made. This is usually done by the automatic gantry, robotic arms, or manual operator.
As you can see, there is a stark contrast in the material input of both machines. Let’s discuss the major benefits of coil-fed laser machines over sheet metal processing.
Automation
Coil-fed systems greatly reduce the loading and unloading time of the raw material. While this may not make much difference on a small scale, it can save a huge amount of time in mass production.
Since the process is automatic, there is no need to manually change the sheet metal sizes for different metal parts, thus reducing the number of cycles. In some cases, the entire production cycle goes without human intervention, reducing the element of human error. An operator is only required to supervise the whole process.
Optimized Nesting
Nesting refers to laying out the pattern and shapes on the material. With automatic coil feed, the sheet-fed laser nesting is optimized. Previously, it was quite difficult to nest complex and large parts due to raw material restrictions. It maximizes the nesting potential, which is impossible with traditional sheet metal laser cutting machines.
Material Optimization
Improvement in the nesting plan directly affects material wastage. It’s estimated that nearly 16% to 33% of the material can be saved with coil-fed laser cutting machines. This is huge, considering materials like stainless steel are quite expensive.
When cutting a long metal part, the length of the raw material can seriously affect the productivity of tasks in traditional machines, but that’s not an issue with coil-fed ones, as the length of the metal sheet can be increased or decreased as needed. Thus, it has very high material utilization.
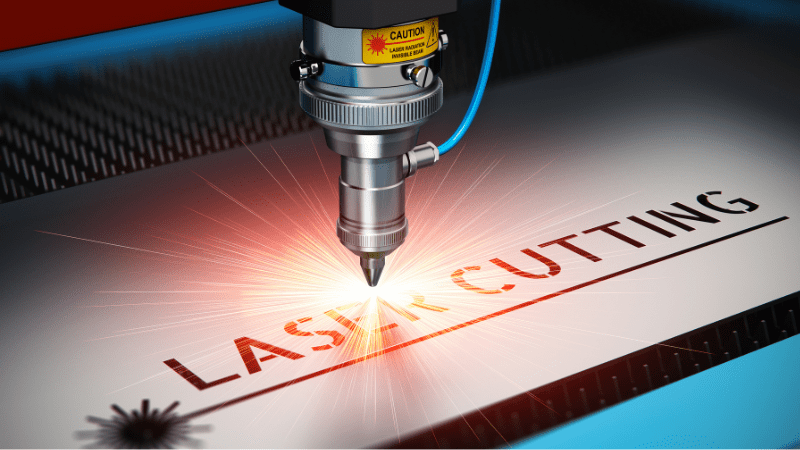
Less Scrap
Due to high material optimization in the material and nesting process, the scrap generated will be inevitably minimized. By an estimate, coil-fed laser cutting machines produce 3% to 10% less scrap than sheet metal production. This is great news for you if you own a sheet metal business.
The best practice is to slit the metal sheet coil to the exact width of the part. The scrap removal is also automatic, which further reduces the lead time.
Time and Cost Savings
Every manufacturer tries to reduce time and cost. The good news is that coil-fed machines target both these aspects.
You can save on the storage cost of various lengths and widths of metal sheet blanks. And then, there is an additional cost of feeding the metal blanks into the laser cutters. As you can imagine, carrying long panels (five meters or more) isn’t easy.
Instead, metal coils are compact with varied lengths and highly profitable with continuous feed.
With these machines, you can also reduce the cost and inefficiencies of manual labor.
Meeting New Challenges
Laser cutting has become better over the years. It has shifted from mere niche production to full-fledged mass production in modern industry. Coil-fed laser cutting is the next step in this evolution. It’s improving at processing sheet metal, complex materials, and intricate shapes within shorter lead times.
Cons of Coil Fed Laser Cutting Machine
It’s only fair to discuss some cons of coil-fed laser cutting to keep things unbiased. Firstly, the coil system is not suitable for small-scale production. Even on a medium scale, you wouldn’t find many benefits because the cost of replacing the coil is higher. Furthermore, it’s best to avoid parts of varied thickness and width are needed.
The best-case scenario for coil-fed cutting and coil-fed punching systems in high-volume production. Secondly, the initial cost of the coil system is higher, so you have to make a feasibility report before investing in this technology.
Lastly, many companies are accustomed to sheet metal fabrication, and their staff is trained in older technology. So, it may become difficult to switch to coil processing. However, the advantages of shifting to a coil-fed system outweigh the cons.
Easy Formulas for Efficient Coil Fed Processing
Coil-fed machinery is best for lean production and increased efficiency. Since this technology is relatively new, you may require certain calculations for efficient production planning. Whether you are a business owner or a production manager hired to supervise the coil-fed process, we’ve covered you.
Important Terms to Remember
Inner Diameter(ID)
ID is simply the inner bore size of the re-coiler. You’ll encounter the most common ones between 500 mm and 610 mm.
Outer Diameter(OD)
OD refers to the diameter of the coil taken from the center of the re-coiler. It’s also dependent on the dimensions of the un-coiler present at the coil-fed machine.
Material Type (D) and Weight
Material types provide extensive information about a material’s intrinsic properties. For our calculation, we will use the material’s density (D) in kg/m3. Weight refers to the overall mass of a metal coil.
Strip Length, Width, and Thickness
The sheet metal uncoiled for processing is called a strip length. It should not be confused with the overall length of the coil represented by “L” in the following calculations. Similarly, the width (W) and thickness (T) of the strip are important information for our calculations.
Calculate Coil Length
· When inner dia, outer dia, and thickness are known.
1, Start by calculating the volume of the overall metal coil. Plug the values in the following formula.
“V (mm^3)= (3.14/4)*(Outer Dia^2 mm- Inner Dia^2 mm)*(W mm)”
2, Once you have the value of volume, substitute it in the following equation. You’ll find the overall Length (L) in meters.
“L (m)=(V) / (W*T*1000)”
· When weight, material type, width, and thickness are known.
1, It’s much easier to find the length of the coil using material weight and type. Plug in the values in this equation. The final value will be in meters.
“Overall Length (L) = (Weight(kg))/(D(kg/m^3)*Width(m)*T(m))”
Calculate Running Time
It’s essential to know the total run time of the sheet metal coil. Here is how you can do it.
1, First, calculate the number of nested parts on the sheet metal.
No. of parts (N) = Overall Length (L) / Part Length
2, Find out the default cycle time needed for processing. This info is available to the machine operator. If parts have variable lengths and cycle times, use the average values. It’ll give a reasonable estimate.
(Coil Running Time in minutes) = (N)*(cycle time(seconds))/60
Calculate Sheet Metal Coil Weight
1, Start by calculating the volume of the coil.
“V (mm^3)= (3.14/4)*(Outer Dia^2 mm- Inner Dia^2 mm)*(W mm)”
2, Multiply the volume by the density of the material. Make sure to keep the units consistent.
“Weight (kg) = V (mm^3) * D (kg/mm^3)”
Final Thoughts
Coil-fed laser cutting isn’t limited to a specific niche industry anymore, as the technology continues to grow. We’ve covered all the benefits you’d expect from switching to coil processing.
We also discussed some limitations of coil-fed machinery and shared quick formulas to help you manage coil-fed production efficiently.
By going through all this knowledge, you’ll better understand coil processing, which will lead to success in the business.
Get High-Tech Coil Fed Fiber Laser Cutting Machines By Baison Laser
It’s no hidden fact that high-level manufacturing requires top-notch machinery. Here at Baison Laser, we understand the market needs, so we produce premium quality fiber laser machines for leading industries.
Our company focuses on R&D development, which makes us adept at customizing orders to your needs. We also offer installation services and guidance to our esteemed customers.
Baison laser ensures the product’s quality meets international standards and gives our clients the best deal on prices and warranties. So, what are you waiting for? Get your quote now.