In this post, we’ll dive into the advantages of CO2 laser cutting and die-cutting, explore the key differences between these two methods, and provide real-world examples to illustrate their applications in various sectors.
By understanding the benefits and limitations of each technique, you’ll be better equipped to make the right choice for your business.
CO2 Laser Cutting
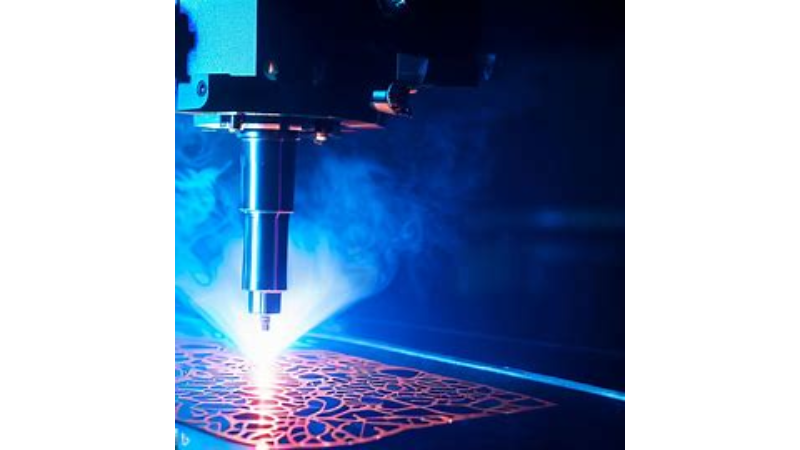
What Is CO2 Laser Cutting?
CO2 laser cutting is a non-contact, precision cutting method that utilizes a high-powered, focused laser beam to vaporize, melt, or burn materials like metal, plastic, wood, and textiles.
The CO2 laser cutter gets its name from the carbon dioxide gas mixture fiber lasers that are used to create the laser beam. This process is guided by a computer-controlled system that follows a predetermined design or cut pattern made of fiber lasers, ensuring highly accurate and intricate cuts.
Advantages Of CO2 Laser Cutting
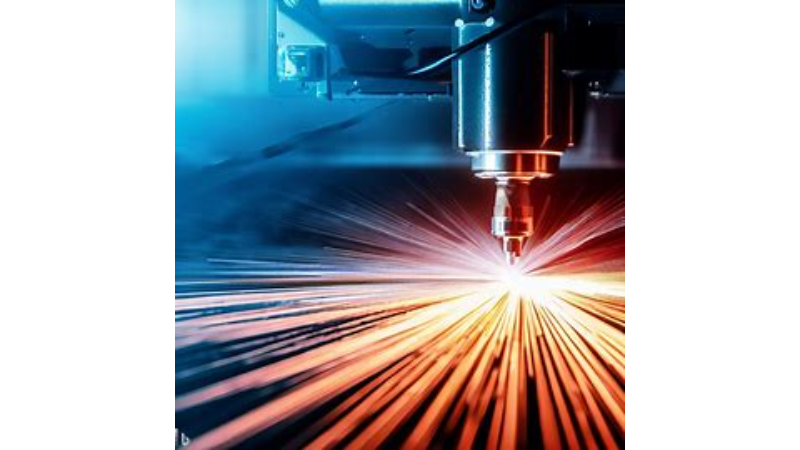
CO2 laser cutting machine offers several advantages over the other cutting machine techniques:
1. High-precision cutting:
CO2 laser cutting systems use a computer-controlled process that allows for extremely accurate and intricate cuts. The two laser cutter’s narrow and focused beams can produce fine details and tight tolerances, making them ideal for creating complex designs and shapes. This level of precision is especially beneficial for industries that require intricate components or parts, such as electronics, aerospace, or medical devices.
2. Greater design flexibility:
Since CO2 laser cutting relies on digital files and a computer-controlled system, it’s easy to make design changes or adjustments on the fly without creating new physical templates or dies.
The laser cutter’s high speed and flexibility allow for rapid prototyping, customization, and design iterations, streamlining the production process and reducing lead times.
3. Lower setup costs:
Traditional laser die cutting in-cutting involves the creation of physical dies, which can be time-consuming and costly to produce, particularly for intricate designs. CO2 laser die cutting, on the other hand, doesn’t require any physical tooling, as the cutting process is guided by digital files.
This eliminates the need for dies and reduces setup and operating costs, making it a more cost-effective option for small production runs or projects with frequent design changes.
4. Versatility in cutting various materials:
CO2 laser cutting systems can work with various materials, including metal, plastic, wood, textiles, acrylic, etc. This versatility makes it a valuable tool for businesses that work with multiple material types or want to expand their product offerings. Here is a blog article about how to choose the right CO2 laser cutter.
Additionally, the non-contact nature of the laser cutting process minimizes the risk of material deformation or damage, ensuring high-quality results for various applications.
Traditional Die-Cutting
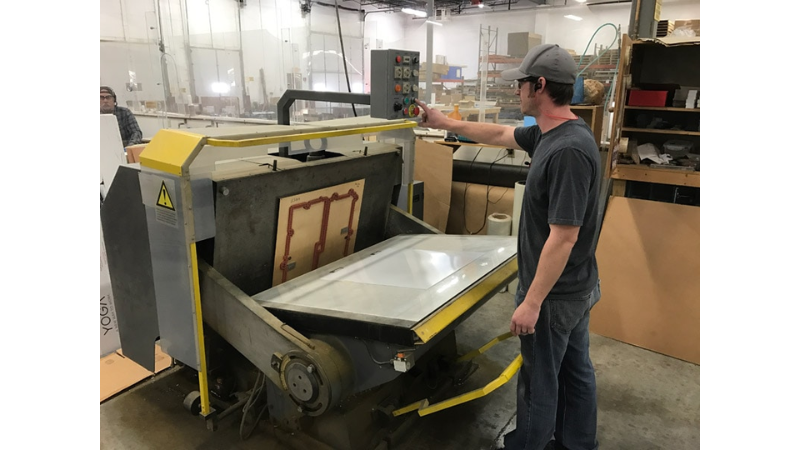
What is Traditional Die-Cutting?
Traditional die-cutting is a cutting process that uses custom-shaped, sharp-edged dies to cut, shape, or form materials such as paper, cardboard, plastic, sheet metal, and more. The dies, usually made from steel, are designed and manufactured according to specific patterns cut materials, or designs.
In the die-cutting process, the material is placed on a flat surface, and the die is pressed onto the sheet metal roll or sheet form metal cutting it using a machine that applies force or pressure to molten material.
This force causes the die to cut through the material, creating the desired shape or design. Die-cutting can be done manually using a hand-operated press or with an automated machine for higher production volumes.
Traditional die-cutting is widely used across various industries, including packaging, printing, automotive, and manufacturing, for producing items such as boxes, labels, gaskets, seals, and other components with specific shapes and patterns.
Advantages of Traditional Die-Cutting
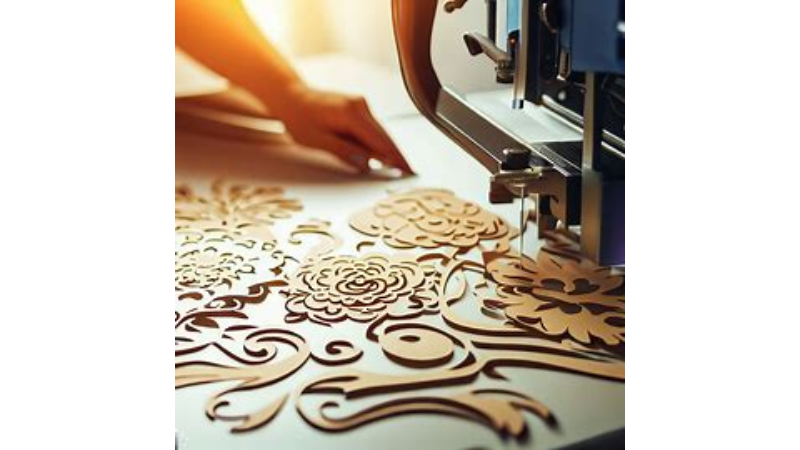
Traditional die-cutting offers several advantages over other cutting methods:
1. Reliability and Consistency:
Traditional rotary die-cutting machine re-cutting offers high reliability and consistency in producing uniform, accurate cuts. Once a used die-cutting machine is set up, it can be used repeatedly to create identical pieces without any deviations, making it an excellent choice for mass production and large-scale projects.
2. Cost-Effectiveness for Large Production Runs:
Although the initial upfront costs and setup cost upfront costs for creating dies can be high, traditional die-cutting becomes more cost-effective for large production runs. The cost per unit decreases as the volume of items being produced increases, making it a suitable option for businesses with high-volume production needs.
3. Speed and Efficiency:
Automated die-cutting machines can process materials quickly and efficiently, enabling very high-speed and volume production with minimal downtime. This high-speed cutting and efficiency are particularly beneficial for industries with tight deadlines and large-scale manufacturing operations.
4. Ability to Handle Thick and Rigid Materials:
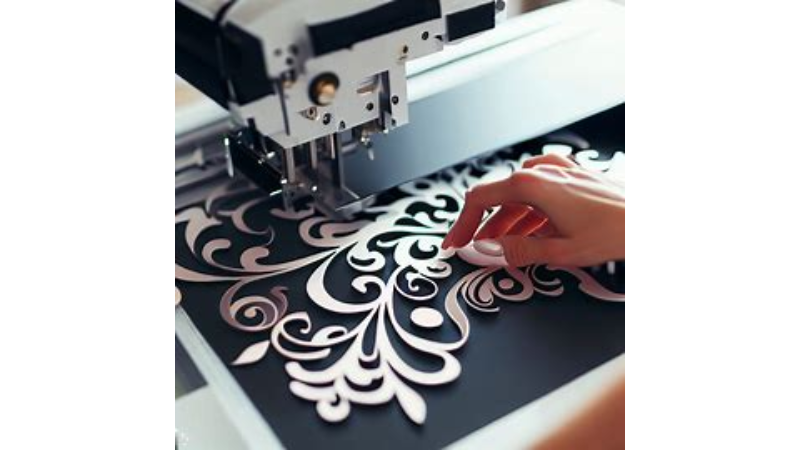
Traditional die-cutting can efficiently cut through thicker, more rigid materials that may be challenging for some laser-cutting systems. This capability makes it a versatile option for industries that require the cutting and shaping of heavy materials, like thick plastics, metals, and dense foams.
5. Simple, Low-Maintenance Process:
Die-cutting machines are generally straightforward to operate and maintain, making them a practical choice for businesses with limited technical expertise. The simplicity of the die-cutting process also reduces the likelihood of errors and allows for quick and easy adjustments during production.
CO2 Laser Cutting vs. Traditional Die-Cutting
Here’s a table comparing the differences between CO2 laser cutting and traditional laser die-cutting re-cutting:
Factors | CO2 Laser Cutting | Traditional Die-Cutting |
Speed of Cutting | Generally faster due to its non-contact nature | Can be slower, especially for intricate designs |
Pattern Flexibility | Offers greater pattern flexibility, allowing for the cutting of complex shapes with a high degree of accuracy | Traditional die-cutting is limited to the shapes that can be created with the dies, which can limit pattern flexibility |
Material Limitations | Can cut various materials, struggles with thicker metals | Traditional die-cutting is limited to cutting paper, cardboard, and plastic |
Cut Quality | CO2 laser cutting offers high cut quality, with a narrow cutting incision and small heat-affected zone | Traditional die-cutting may result in jagged edges and burrs |
Cost-Effectiveness | It can be slower, especially for intricate designs | Traditional die-cutting may require more labor and setup costs |
While both CO2 laser cutting and traditional die-cutting have advantages and limitations, the choice between them ultimately depends on the specific needs and requirements of the project.
How Can CO2 Laser Cutting Be More Profitable Than Traditional Die-Cutting?
CO2 laser power and cutting can be more profitable than traditional die-cutting laser power, for several reasons:
1. Lower setup costs:
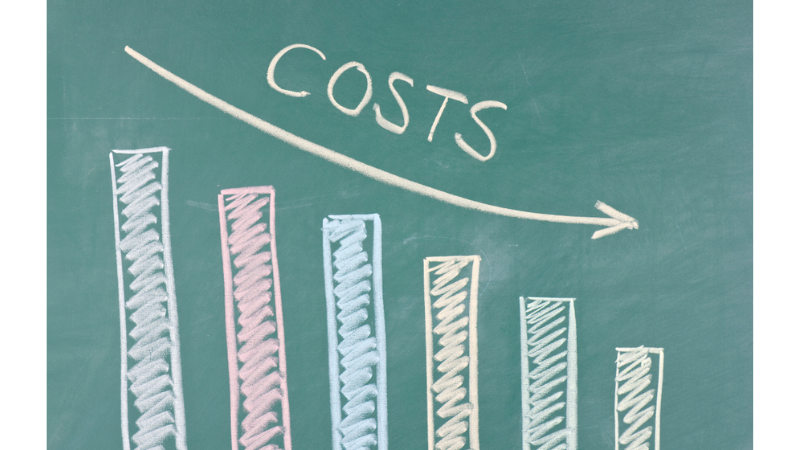
CO2 laser cutting eliminates the need for physical dies, which can be expensive to produce, especially for complex designs. Instead, the process relies on digital files, making it more cost-effective for small production runs or projects requiring frequent design changes.
2. Faster production times:
The non-contact nature of laser cutting allows for faster cutting speeds compared to traditional die-cutting, which requires applying force to the material. Faster production times on thicker materials can result in higher output, shorter lead times, lower cost, and ultimately, increased profits.
3. Greater design flexibility:
CO2 laser cutting offers the ability to quickly and easily modify designs using digital files, making it ideal for customization, prototyping, and design iterations. This flexibility can help businesses stay competitive and adapt to market trends, leading to increased profitability.
4. Reduced material waste:
The high precision of CO2 laser cutting ensures minimal material waste, as fiber laser cutting machines can make precise cuts without additional cutting metals trimming or finishing. This efficient use of materials can lower production costs and contribute to higher profit margins.
5. Expanded capabilities:
CO2 laser cutting machines can handle a wide range of materials, including metals, plastics, wood, textiles, and more. This versatility of laser machines allows businesses to expand their product offerings, cater to diverse markets, and increase their potential revenue streams.
By taking advantage of these benefits, businesses that choose CO2 laser cutting over traditional die-cutting can potentially see increased profitability through lower costs, faster production times, lower costs, and the ability to adapt to changing market demands.
Which One is Better?
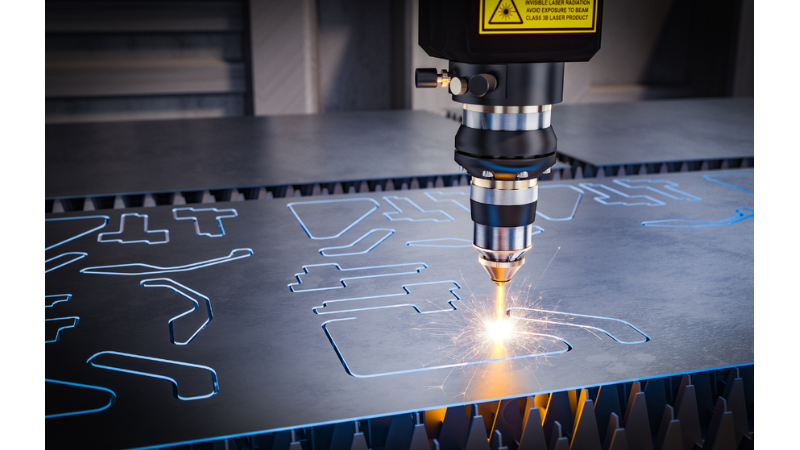
While CO2 laser cutting and die-cutting have advantages, CO2 laser rotary die-cutting machines are often considered more profitable and versatile for a wider range of applications. This cutting method offers greater precision, faster production speeds, and reduced material waste, contributing to cost efficiency and higher profit margins.
Additionally, the ability of CO2 laser and die-cutting machines to work with various materials and handle complex designs gives businesses a competitive edge in the market. However, the specific needs of your business should always be considered when choosing between the two cutting technologies.
Why Should Choose the Right Cutting Technology for Your Business?
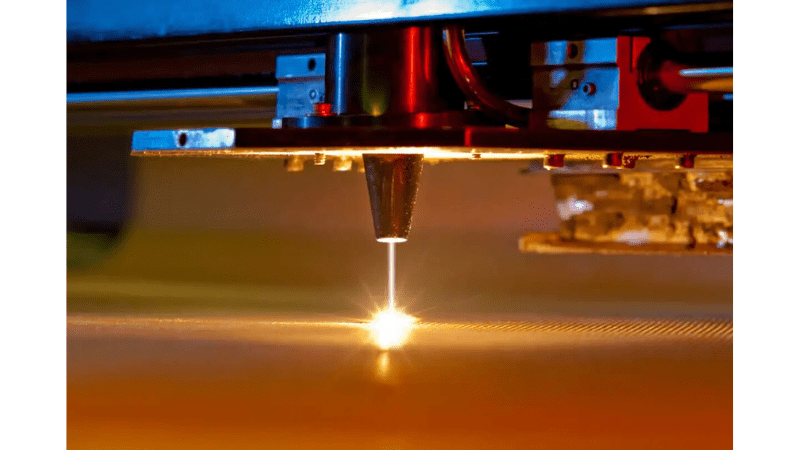
Selecting the most suitable cutting technology for your business is vital for several reasons. Understanding the factors contributing to this decision can help you optimize your production process, save costs, and improve overall product quality. Here are some reasons why making the right choice matters:
1. Cost Efficiency:
Choosing the most appropriate cutting technology can lead to significant cost savings for your business. You can optimize your operational expenses by reducing material waste, improving production speed, and minimizing the need for manual labor.
Additionally, a more efficient process can lead to higher profit margins, operating costs, and a faster return on investment.
2. Product Quality:
The cutting technology you choose directly impacts the quality of your final product. Precision cutting and other methods used, like CO2 laser and plasma cutting alone, can offer cleaner edges, fewer defects, and more accurate cuts than traditional die-cutting. This can lead to a higher-quality product, which in turn can help you establish a better reputation and attract more customers.
3. Production Speed and Scalability:
The right cutting technology can significantly impact your machine, production speed, and your ability to scale up your business. For example, CO2 laser die-cutting machines can often cut faster than traditional die-cutting machines, especially for intricate designs.
This faster production time means you can produce more units in the same amount of time, allowing you to grow your business more quickly and efficiently.
4. Material Versatility:
Some laser-cutting machines and technologies are better suited for certain materials than others. For instance, CO2 laser cutting is ideal for cutting a wide range of materials, such as wood, plastic, fabric, non-metals, and more.
By choosing a laser cutting machine or technology that is compatible with various materials, you can expand your product offerings and better cater to your customers’ needs.
5. Adaptability to Complex Designs:
The right cutting technology can easily handle complex and intricate designs, whereas more traditional die-cutting methods may be limited in this aspect. CO2 laser cutting, for example, is computer-controlled, which allows for more precise and detailed cuts.
This flexibility can help you produce innovative and unique products, giving your business a competitive edge in the market.
In conclusion, choosing the right cutting technology for your business is crucial for improving cost efficiency, product quality, production speed, material versatility, and adaptability to complex designs of multiple materials.
By carefully considering these factors, you can make a more informed decision and select the cutting method that best aligns with your business goals and requirements.
Conclusion
In conclusion, precision truly matters when selecting the best fiber laser cutting technology for your business. CO2 fiber laser cutting and die-cutting have unique benefits, but CO2 fiber laser cutters and cutting often prove more versatile, efficient, and profitable for a wide range of applications.
Remember that the ultimate decision should be based on your business’s needs, considering cost efficiency, product quality, production speed, material versatility, and adaptability to complex designs.
We hope this blog post has provided valuable insights to help you make an informed decision for your business. For more information on CO2 laser vs. fiber laser, and other manufacturing technologies, feel free to explore our other resources on our website.
By staying informed and choosing the right cutting technology, your business can thrive and continue to grow in this competitive market.
Request a Free Demo or Consultation to Experience the Benefits of Precision Cutting!
Is your business struggling to keep up with the ever-evolving manufacturing industry? Look no further! Discover the game-changing benefits of precision-cutting technology and elevate your production process to new heights at Baison Laser.
With our cutting-edge CO2 laser cutting and die-cutting solutions, you’ll experience a significant boost in cost efficiency through reduced material waste and lower labor costs. Achieve enhanced product quality with cleaner, more accurate cuts while increasing your production speed and scalability for rapid business growth.
Our precision cutting technology allows you to expand your product offerings with unmatched cut material and versatility and create intricate, innovative designs and cut materials that set you apart from the competition.
Don’t let outdated cutting methods hold your business back any longer. Request a FREE demo or consultation today, and unlock the full potential of your manufacturing process. Experience the difference precision cutting can make – your bottom line will thank you!