Selecting the proper type of gas for the project you will complete ensures this is done more efficiently. This is why, in this post, we will review the different types of auxiliary gases suitable for this purpose and the general advantages and disadvantages of laser cutting.
What is Laser Cutting?
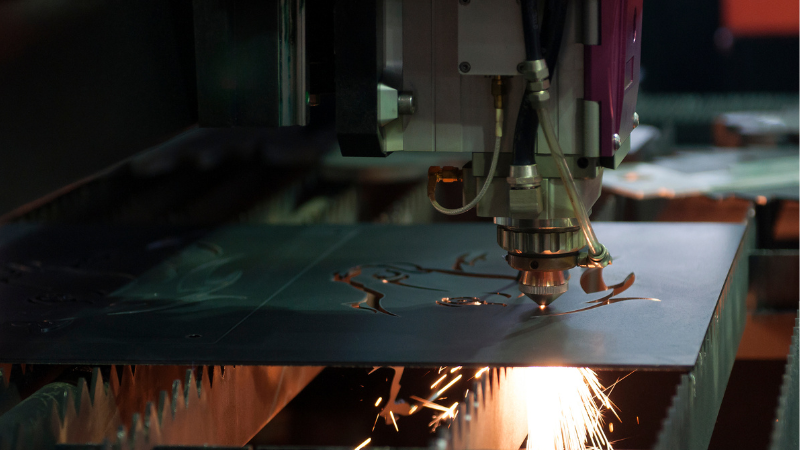
What is laser cutting? A laser cutter is a prototyping and manufacturing tool used primarily by engineers, designers, and artists to cut and etch into flat material that uses ‘a thin, focused laser beam to pierce and cut through materials to cut out patterns and geometries specified by designers,’ according to Instructables.
It is used primarily in manufacturing but several different fields are starting to utilize it. This is especially true when you consider all the different materials that laser cutting can be used for:
- Metals
- Paper
- Wood
- Cork
- Acrylic
- Foam
- And much more
In general, there is very little that a laser cutter is not able to cut. This would include polycarbonate, carbon, PVC, PVB, and leather which includes chromium. These materials could melt, causing damage to the laser-cutting machine itself. Others can release harmful chemicals when the laser is applied.
What are the basic principles of laser cutting?
A laser cutter uses optics and computer numerical control (CNC) to direct a high-powered laser to cut a specific pattern into a chosen material. In regards to our purposes, these cutting materials are primarily metal materials.
The laser beam is created with electrical discharges within a closed container. Sometimes these use lamps instead of electrical discharge. Then, the materials inside the container are actually amplified. This is done through a partial mirror, which reflects the energy back to build it up, creating a laser light.
The laser cutter then focuses this light to the specific location where it is needed using even more mirrors/ fiber optics. From there, the light or beam can be used to burn or melt different metal materials. It does this with the assistance of a gas (known as an auxiliary gas), which we will discuss further in a moment.
The laser can use more or less power and the gas used to assist can have a higher or lower flow rate. These different combinations, as well as different types of gases, will each work for different materials, including each of those discussed above.
Different Types of Laser-Cutting Machines
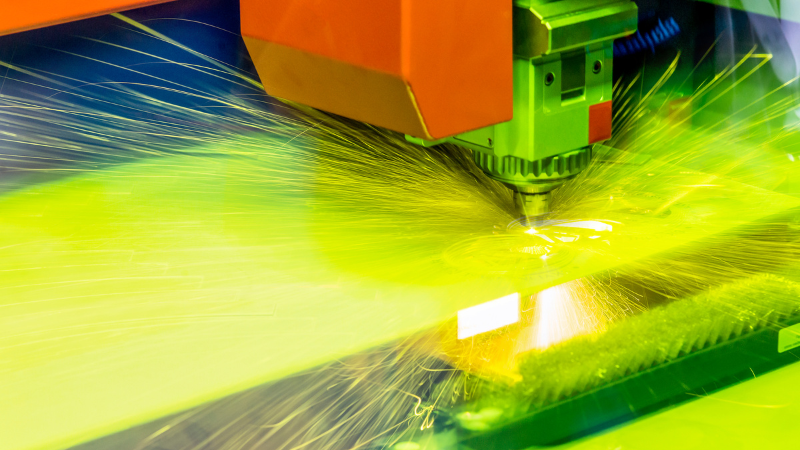
There are several different types of laser cutters to consider when you are looking for metal cutting capabilities. These include:
- Neodymium
- Neodymium yttrium-aluminum-garnet
- C02 laser cutting machines
Each of these machines is designed to cut different types of products using some gas. Whether you want to cut rolled steel, aluminum alloy, carbon steel, stainless steel, high tension plate, or any other type of metal materials, a laser power machine is available to assist with this process.
Neodymium & Neodymium yttrium-aluminum-garnet
Neodymium laser machines and neodymium yttrium-aluminum-garnet (Nd:YAG) machines are actually nearly identical overall. The difference is that Neodymium is used for situations where high energy is needed to execute low-repetition boring. On the other hand, Nd:YAG is used for high-power boring or for engraving processes.
CO2
CO2 laser power machines are good for cutting, boring, and engraving. These machines use a type of gas mix or radio frequency through which an electrical current passes. This process creates a small spot that can be used for more precise work.
Fiber laser cutting machine
Fiber lasers are one option that should be mentioned here as well. These types of lasers do not use an auxiliary gas or other inert gas. Instead, fiber lasers use what’s called a ‘solid gain medium.’ These are a benefit to those who want the smallest spot possible because they create a beam that’s even smaller than that from C02.
Water power laser machines
Also, it’s important to mention is the laser microjet, which actually uses ‘wet’ cutting rather than ‘dry.’ It uses the combination of a laser beam pulse with a low-pressure water jet that actually guides the beam (rather than a gas jet). This is a benefit in situations where you want high dicing speed, omnidirectional cutting, or parallel kerf. Plus, it cools the material as it cuts.
What is Auxiliary Gas?
What is auxiliary gas? According to Law Insider, it is “a substance burned in an incinerator to supply additional heat to attain temperature sufficiently high to dry and ignite waste material and to maintain ignition of the waste materials but which is never in contact with the waste material.”
Another definition, also from Law Insider is “natural gas, propane, butane, distillate fuel oil or other fuel free of toxic compounds and containing not more than 0.5% incombustible particulate.”
When we are talking about laser cutting, these auxiliary gases are primarily oxygen, nitrogen, air, and argon, which are each used in different ways to cut through different types of materials.
Benefits of Auxiliary Gas in Laser Cutting
- Get slag out of the way of the coaxial slot.
- Reduce the heat-affected zone of the object.
- Prevent contamination and overheating of the protective lens.
- Protect the base material (depending on your auxiliary gas).
- Improve cutting performance.
- Improve cutting speed.
- Improve cutting quality.
- Other benefits relative to specific gas and material combinations.
The Importance of Choosing a Suitable Auxiliary Gas for Laser Cutting
Why does the auxiliary gas matter? Why can’t you use whatever you have available at the moment? Why not just use the same gas all the time?
At a minimum, using the wrong gas could make your cutting process slower or less efficient overall. But it’s likely going to cause more trouble than that. If you’re not paying attention to your cutting surface when you choose between the different auxiliary gases available, you’ll see a few primary problems:
- Lens damage, which could damage your laser and/or your workpiece
- Cutting power fluctuations, which could damage your workpiece or slow you down
- Cut inconsistencies, which could make your workpiece look unfinished/unpolished
Choosing the correct assist gas will allow you to improve your cutting performance. It will ensure that you get the quality you’re looking for, especially when using the end product for any manufacturing process or purpose.
Common Auxiliary Gases Used in Laser Cutting
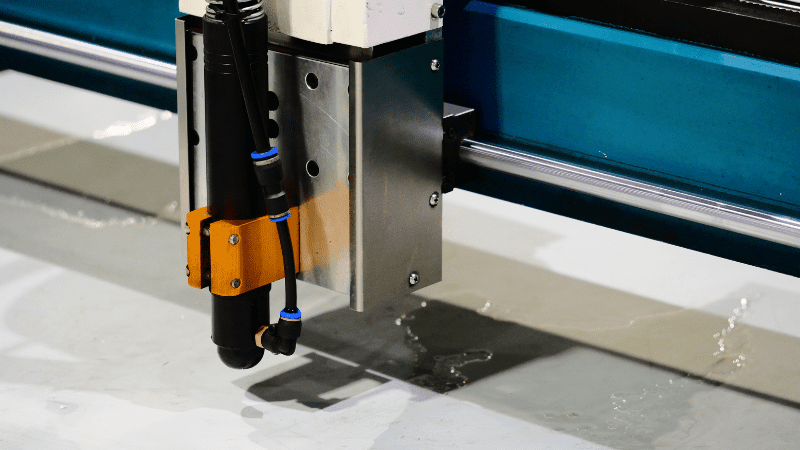
There are four different types of auxiliary gas for laser cutting. These are:
- Oxygen
- Nitrogen
- Air
- Argon
Oxygen
Oxygen is useful for several different types of material, including carbon steel, rolled steel, stainless steel electroplated steel plate, copper alloy, copper, and more.
It requires a pressure of approximately 0.3-1 Mpa, but the flow rate will vary based on the specific thickness of the material that you are cutting. Further, oxygen requires purity of 99.95% or higher, allowing for improved combustion and retaining purity of the cut melt.
Oxygen can be used to increase overall cutting efficiency, producing an oxide film that improves beam spectrum absorption, and creating a dark yellow or black cut end.
On the other hand, it is considered a combustion-supporting gas, and it’s possible for it to burn and to create slag.
Nitrogen
Nitrogen can be used to prevent oxidation film when you’re looking for a more sleek-looking finish. It can be excellent for stainless steel, electroplated steel plate, aluminum, aluminum alloy, and brass.
In general, this type of auxiliary gas is useful for direct welding and painting and is also very resistant to corrosion. It requires extremely pure nitrogen, as high as 99.999%, and approximately 1.5 Mpa or higher.
When we look at flow the variance can be wide but depends on the specific thickness of the cutting material.
This gas can be quite expensive, and it requires extremely high purity levels, which can difficult to achieve.
Air
Air is a good option for materials like aluminum, stainless copper, electroplated steel plate, non-metals, and brass. However, it is not intended for products that are of higher quality, which typically include stainless steel and aluminum alloy.
This auxiliary gas is about like nitrogen, coming in at a higher quality than oxygen. However, it also balances out the oxide film of the two, creating only a small amount of the film on a cut piece.
On the other hand, this gas can have the same problems as oxygen, though to a slightly lesser degree.
Argon
This is the fourth, and final option when it comes to auxiliary gas, but it is not as commonly used. It’s considered an inert gas and it doesn’t oxidize as well with other materials. It’s chemically inactive, and it’s going to be more expensive than your other options.
This material can also become contaminated with dust, water, oil, and other debris types, making it even more harmful for the finished product as it can affect the laser and the cut created.
If you are going to use argon, it would generally only be used with titanium alloy materials.
It is not effective for most materials, and also the cost is extremely high, which is something to keep in mind before choosing this gas.
Oxygen vs. Nitrogen: A Comparison
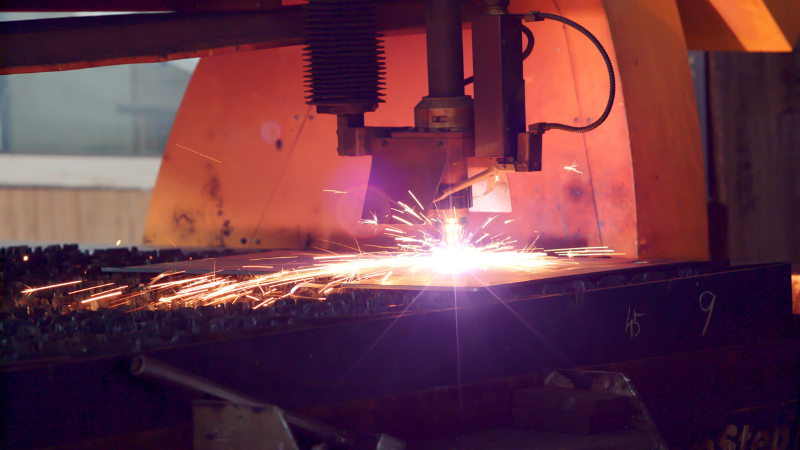
Two of the most popular cutting gas options are oxygen and nitrogen.
These two gases offer a wide range of different applications and can be used with a number of different materials in the laser-cutting process. Whether you’re cutting surface is carbon steel or stainless steel, these two gases are generally capable of getting the job done. But they have different benefits and drawbacks.
Benefits and drawbacks of using oxygen as an auxiliary gas
Oxygen has a number of benefits as an auxiliary gas, which starts with the number of different applications that oxygen has.
You can use oxygen to cut various materials ranging from stainless steel, rolled steel, and tool plate to carbon steel, copper alloy, and electroplated steel plate. The range of cutting materials is vast, so you can purchase larger quantities of a single gas for most of your workpieces.
Oxygen is also good for increasing beam spectrum absorption for reflective material. If you’re working with reflective material, with reacts to the oxygen reaction heat that comes from this source.
Now, on the downside, you’ll find that oxygen requires a high level of purity and can cause a return to slag.
Benefits and drawbacks of using nitrogen as an auxiliary gas
Nitrogen as an auxiliary gas is another excellent consideration. The drawback of oxygen, where it can cause a return to slag and is easy to burn is actually the opposite here. You’ll find that nitrogen does not do either of these things, which is a benefit to the auxiliary gas.
Another benefit of nitrogen is that it will provide corrosion resistance after you have made your cut. It also provides several different characteristics associated with direct welding, creating a strong and high-quality workpiece.
Versatility is another excellent factor here and this auxiliary gas will work with materials like stainless steel, electroplated steel plate, aluminum, aluminum alloy, and brass.
However, nitrogen is very expensive and requires extreme purity for success. It can also be quite a process to get through the laser cutting.
Comparison of oxygen and nitrogen for different materials and cutting requirements
When considering these two auxiliary gas options, you need to think about your specific material and the cutting requirements you have (which were also discussed above). Take a look at the chart below to get a better idea of the right auxiliary gas for your project.
Factors to Consider When Choosing an Auxiliary Gas
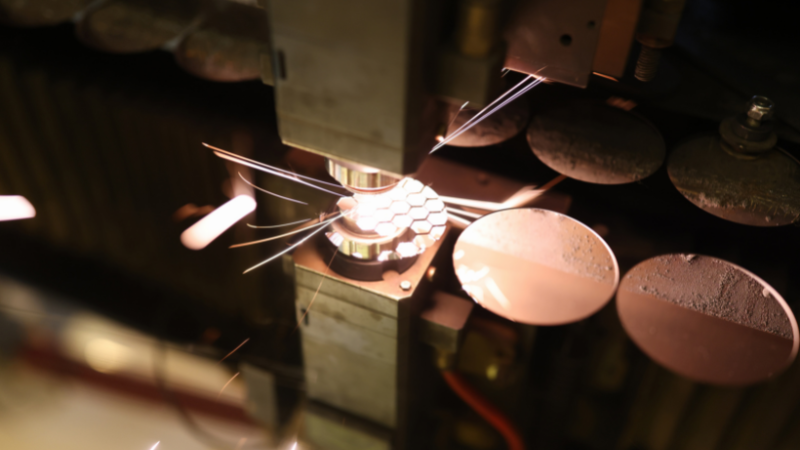
When it comes to choosing the best auxiliary gas for a laser cutting project, you must think about several different factors. These can be grouped into three different categories. Namely:
- Material factors
- Cutting requirements
- Environmental concerns
Material Being Cut
The material that you are cutting is perhaps the most important aspect in choosing the right auxiliary gas. You need to consider the specific type of material to know which gas will provide the right features.
For example, stainless steel generally cuts better with oxygen or nitrogen.
Aluminum could be cut with nitrogen or air.
Carbon steel may be cut with oxygen.
For each type of metal that you want to cut, there will be a preferred type of auxiliary gas to use. Some may also offer multiple options (such as stainless steel).
The thickness of the material is another point to consider. In general, you will be able to cut metal pieces of different thicknesses with the same type of auxiliary gas. You will need to increase the flow rate to accommodate thicker materials, however.
Cutting Requirements
There are also general requirements related to the specific outcome you’re looking for. If you want your stainless steel laser cut to be smooth and perfect, you should consider this when choosing your auxiliary gas.
If you are laser cutting carbon steel and want it to be fast you’ll need to consider this in choosing the correct auxiliary gas to use. Nitrogen is a good option if you’re looking for faster speeds without losing out too much on quality.
On the other hand, air is not as good with cutting efficiency (though it can be used for various materials). If you’re looking for quality with your laser cutter this is not the way to go about it.
Environmental Concerns
Protecting your cutting environment (and perhaps the environment as a whole) is also important. As such, you will need to consider this when choosing the auxiliary gas you want to use iwth your laser cutter.
Balancing cutting efficiency, cutting speed, and other factors with environmental concerns is important. Cutting gas such as oxygen or air is generally the most environmentally friendly option. On the other hand, argon and nitrogen can be harmful to your cutting environment.
As long as you’re using proper ventilation, however, and especially if you’re using smaller quantities of these cutting gas options, you can still get the benefits you need without too much environmental impact.
Conclusion
Choosing the right auxiliary gas for your cutting process is essential. It ensures your laser cutter is well maintained and protected, provides cutting efficiency, cutting speed, and improvement for your cutting surface, and helps create a high-quality finished product.
By taking a look at this article, you should have a better idea of the type of gas you want to use, and the best way to evaluate different cutting gas going forward.
Always Have the Tools You Need With the Right Laser Cutter
If you’re in need of a laser-cutting machine but aren’t sure which one will work best for you, sign up for a free application evaluation at Baison Laser today to find out more.