What is Fiber Laser Cleaning?
Fiber laser cleaning removes oxides, dust, rust, coatings, and other contaminants from a target surface using pulsed fiber lasers. Laser beams provide a non-contact, non-abrasive, and eco-friendly alternative to traditional cleaning technology.
What is Chemical Cleaning?
Chemical cleaning eliminates contaminants such as salts, scales, bacteria, and grease using chemical solutions. The cleaning process may be entirely chemical, or it may also involve physical means such as steam. The ideal chemical reagents for your surface cleaning applications will depend on the type of impurity.
How does Laser Cleaning Work?
Laser cleaning technology is based on the interaction of a fiber laser with the top layer of the target surface. The objective is to vaporize and remove the thin layer of unwanted materials such as rust, oxides, powder coating, and paint using a laser pulse.
Laser processes are most effective when the target materials have a high absorption rate within the laser’s wavelength range and the base material is reflective within the same range.
The laser cleaning system distributes thousands of short, powerful pulsed fiber lasers onto the surface of a target material. The layer of surface contaminants will absorb this laser energy, and once they reach their ablation threshold, they are ejected from the substrate surface. Therm energy is released as the contaminants are removed from the substrate surface. Since the substrate material has a higher ablation threshold, it reflects the laser beam and stays untouched.

Typically, laser cleaning systems feature an integrated fume extraction system. It provides continuous suction at the laser target interface and traps the vaporized airborne contaminants. Therefore, unlike traditional cleaning technology, there is no need for cleanup.
This cleaning solution allows for a high degree of flexibility. Laser parameters such as energy density, beam size, wavelength, and laser pulse repetition frequency can be optimized to enhance surface cleaning. The correct laser solution can eliminate surface contaminants while preserving the underlying substrate.
How does Chemical Cleaning Work?
To optimize chemical cleaning technology, you’ll need to first analyze the nature of the contaminants. This will help determine the best chemicals and cleaning fluids for your industrial operations.
Typically, acidic or acid-based cleaning agents are suitable for treating inorganic deposits. If you want to remove organic deposits, alkaline solutions would be an ideal choice. Oxidants and ozone are also used to make removing organic deposits more efficient. To get rid of tar and polymer deposits, your best bet would be aromatic solvents that contain an emulsifying agent.
During the chemical cleaning cycle, you may need to monitor factors such as temperature, pH, flow rates, and the concentration of the cleaning agent. These variables will affect the efficiency of a chemical system.
This cleaning method may or may not be entirely chemical. In some instances, you’ll need to incorporate physical means such as steam or a high-speed jet to obtain the best results. For example, when cleaning towers or columns, steam is used to facilitate the movement of the chemical reagents from point to point.
In the case of small parts or particularly stubborn deposits, the equipment can be immersed in the cleaning solution.
The Benefits of a Laser Cleaning System
- Eco-friendly
Fiber laser technology provides a green cleaning alternative for industrial functions. Since there is no use of harmful consumables such as solvents and acids, this process is environmentally friendly and safer for personnel. Further, laser cleaning does not produce emissions or noise, making it a go-to solution for businesses looking to minimize environmental pollution.
- High-precision laser cleaning systems
Laser cleaning machines rely on computer algorithms, and therefore, they can achieve pinpoint accuracy. A pulsed fiber laser beam can remove sub-micron particles that would be challenging to eliminate using other methods.
- Preserves the substrate material
Laser cleaning is a non-contact process. A pulsed fiber laser can selectively vaporize and eliminate impurities without affecting the reflective substrate. This technique has no chemical, mechanical, or thermal strain on the solid surface.
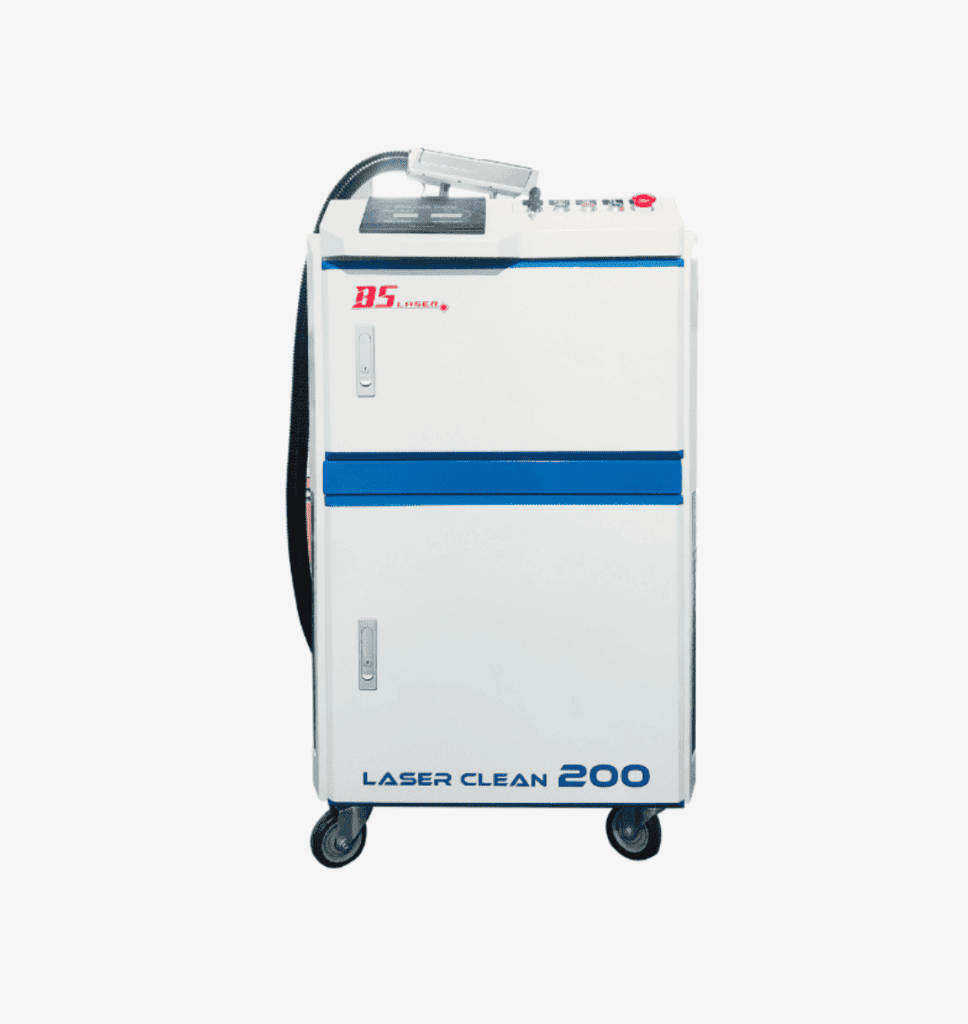
- Wide range of applications
Laser cleaning has a variety of industrial applications, including:
- Surface treatment before laser welding and brazing.
- Metal surface preparation and cleaning in virtually all industries.
- Protection and restoration of antique items and cultural relics.
- Clearance of oxides, coatings, electrolytes, and laser rust removal from surfaces.
- Cleaning of molds and tools.
Laser cleaning methods are ideal for eliminating an array of contaminants in your production line. The size of the job will determine the required laser power.
- Low operating costs
While the initial cost of purchasing a fiber laser cleaning machine can be high, this technology is cost-efficient in the long term. Once you’ve bought your laser machine, you can use the system for years. Moreover, you’ll enjoy a lower cost of operation thanks to minimal consumables and maintenance.
- Automation
Laser cleaning technology allows for easy automation. And with a system requiring minimal input from personnel, there is an added safety element. Further, automation will facilitate fast and efficient cleaning while helping you save on labor costs.
The Benefits of Chemical Cleaning
- Wide range of applications
Chemical cleaning can be used in various industries to eliminate contaminants, including salts, scales, bacteria, fats, oil, biopolymers, and grease. A specific chemical cleaning agent would provide the best results for every type of foulant.
- Lower initial cost
A chemical cleaning system does not require a high initial investment. This is because the process relies on chemicals and cleaning reagents rather than specialized machinery.
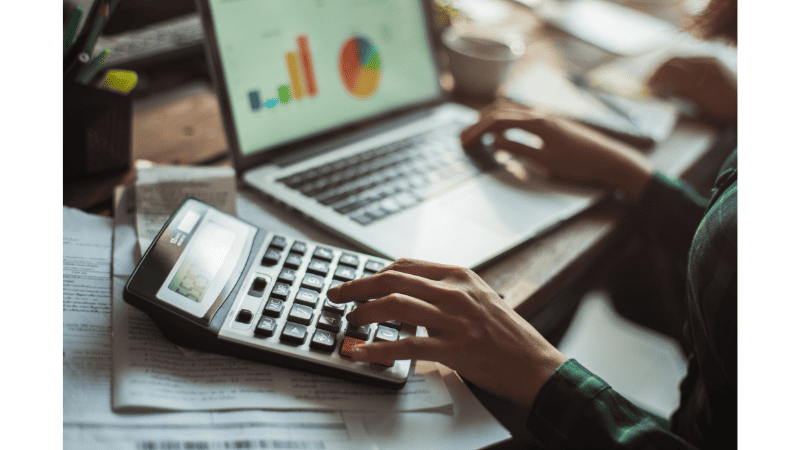
- Effective
When operated by a skilled contractor, the chemical cleaning system can be pretty efficient. The applied chemicals will react and break down the corresponding deposits, effectively eliminating them. This process can also be paired with other techniques for optimal cleaning.
Which is Better for You?
Each cleaning technology comes with its own unique set of pros and cons. Therefore, no one cleaning solution is ideal for all industrial uses.
So, how can you determine the best process for your cleaning needs? You’ll need to look at a couple of factors, including:
- Environmental/ health concerns
There is always a need to protect the environment. Businesses are responsible for ensuring that their activities keep the environment and their staff safe.
Lasers are a green cleaning method as the process does not use toxic chemicals or abrasive materials that can pollute the environment. This also means that employees are not at risk of exposure to hazardous products.
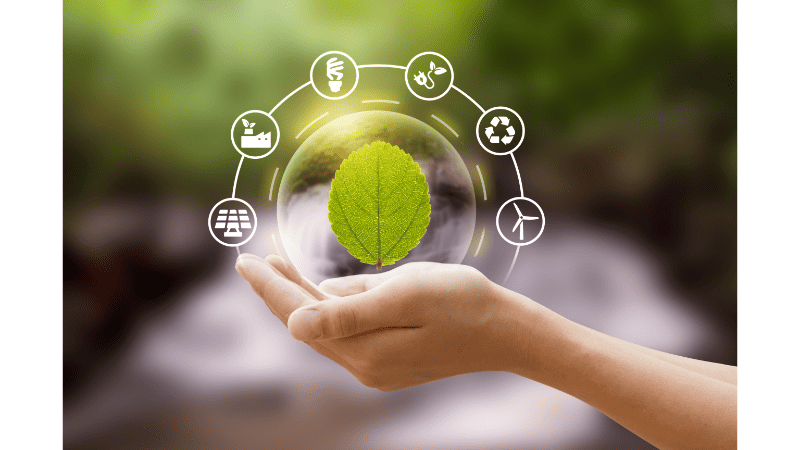
Conversely, chemical cleaning systems rely on cleaning agents such as solvents and acids, which can be harmful. Regulatory controls make it costly to safely dispose of the hazardous waste from these chemicals. Further, there is always a possibility of personnel exposure to toxic substances.
- Suitability
Your chosen cleaning method needs to fit your specific industrial operations. Needless to say, there are limitations to every cleaning method.
While laser technology has a wide range of industrial applications, it is not ideal for all cleaning needs. For example, there are general cleaning applications that do not require the strength of a laser beam. Also, this process may be challenging when working with complex geometries.
The same goes for chemical cleaning. If the contaminant is chemically inert, chemical processes will prove ineffective. Also, when there is a severe accumulation of deposits in equipment, it becomes nearly impossible to circulate chemicals and cleaning fluids through the channels.
- Cost
When analyzing the cost of cleaning technology, you need to consider the initial and ongoing expenses.
Laser cleaning systems require a higher initial investment due to the cost of laser cleaning machines. However, the maintenance and operation of a laser system are relatively inexpensive since the only consumable is electricity.
With chemical processes, the initial cost is meager. However, operating expenses can quickly add up thanks to consumables such as chemical cleaning agents and safety gear for personnel. You’ll also need to anticipate the costs of safely disposing of hazardous waste.
- Ease of handling
Another factor to consider when choosing an industrial cleaning method is the ease of operation.
Laser cleaning systems are known for their easy operation. With minimal training, personnel can safely conduct cleaning applications. And, if the system is automated, it essentially becomes a set-and-forget cleaning solution.
Chemical cleaning is not as easy to operate. Personnel needs to be highly skilled to prevent severe corrosion or equipment damage.
Comparison Chart
Item | Laser cleaning | Chemical cleaning |
Working principle | Uses laser, non-contact | Uses chemical cleaners, contact with the substrate |
Environmental Friendliness | Yes | No |
Damage to substrate | No | Yes |
Accuracy | Controllable, Ultra-precise | Uncontrollable, low precision |
Manual operation | Simple | Complex |
Consumables | Electricity | Chemical reagents |
Cost | Higher initial cost, low operating costs | Low initial cost, relatively high operating costs |
Cleaning efficiency | High | Low |
Frequently Asked Questions
Does Laser Cleaning Damage the Underlying Substrate?
No. The pulsed fiber lasers vaporize the impurities only. The underlying substrate usually has a higher ablation threshold and reflects the laser energy.
Where do the Contaminants Remove During the Laser Cleaning Process Go?
Laser cleaning machines are fitted with a suction system that continuously entraps the ejected impurities and vaporized fumes.
Conclusion
Industrial cleaning is an indispensable part of any manufacturing process. Choosing the proper technique will translate to optimal performance of industrial machinery, an extended equipment life span, and a better working environment for your staff.
Laser cleaning machines enable fast, efficient, precise, and eco-friendly cleaning for various contaminants in various industries. On the other hand, chemical cleaners generate toxic waste, are not easy to handle, and the recurring cost of consumables can quickly add up. Laser cleaning technology offers remedies to the shortcomings associated with traditional methods. Laser solutions are well worth considering if you’re looking for an effective industrial cleaning process.
Looking for Laser Cleaning Solution? Baison Can Help You.
So, which is better? Chemical cleaning or fiber laser cleaning? The answer: it depends on your needs. Chemical cleaning might be the way to go if you need a quick and dirty clean. But if you want a more thorough and longer-lasting clean, fiber laser cleaning is the better option. Contact Baison today for an instant quote – we can help you decide which method is best for your business.