Why is Assist Gas Necessary for Laser Cutting?
Assist gas, also known as “Auxiliary” and “Shielding,” is a high-pressured gas that flows from the laser head to the workpiece during the laser cutting process.
Assist gas blows the molten metal edges from the recently cut workpiece resulting in smoother edges. In addition, this gas pushes the cut piece and slag downwards, separating it from the rest of the workpiece, which prevents the material from welding again at the same spot. It also cools the edges resulting in fewer heat-affected zones.
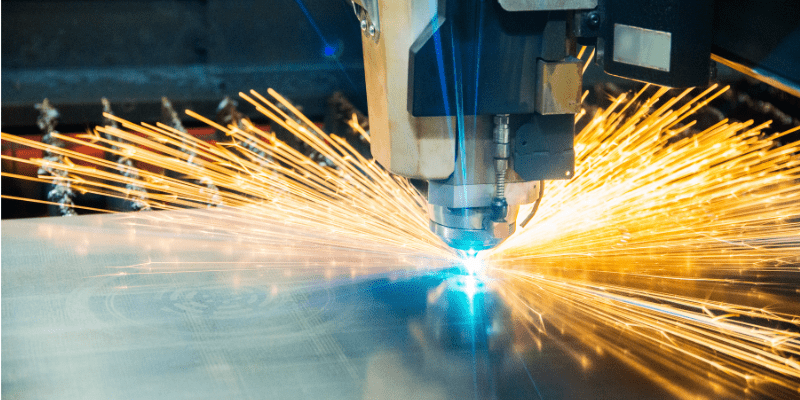
Moreover, it protects the laser lens, nozzle, and lens from cutting spatter. Shielding gas protects the laser from the outside environment, such as dust, debris, and air.
Auxiliary gas is a consumable item and adds to the cost of laser-cutting operations.
Benefits Of Using Different Types of Gases for Laser Cutting
If you plan on starting a laser cutting business or want to learn about the process, you will come across the following four options for assist gasses.
Nitrogen
Nitrogen is versatile and produces higher-quality cuts. It’s non-reactive and doesn’t support combustion during laser cutting; hence the process is purely mechanical.
When gas is reactive, it undergoes a chemical reaction upon hitting the material. This severely damages the edge or kerf quality.
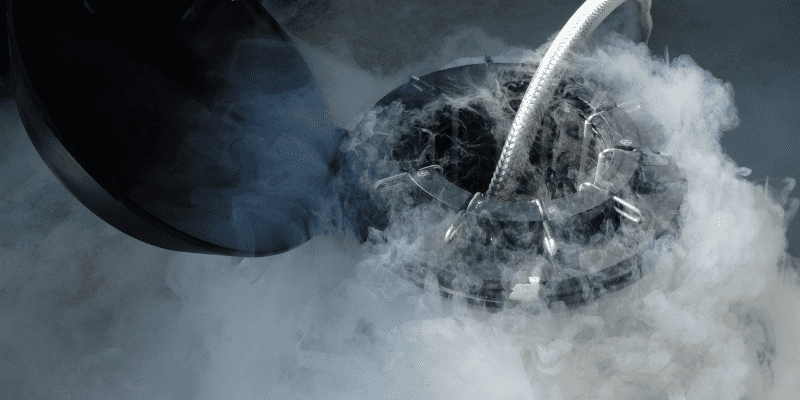
Unlike other gases, nitrogen is directly related to machine power. Therefore, greater power yields better speeds and work.
Nitrogen is present in liquid form in the cylinders. Usually, the bottom half of a cylinder is liquid, while the upper half has gas vapors.
In laser cutting, high pressure is needed. Typically, nitrogen is supplied at 22-30 Bars (319-435 psi) of pressure.
Nitrogen Gas Settings | ||
Material Thickness | Pressure (Bars) | Volume (m3/hr) |
Less than 8 mm | 15 | ~50 |
12 mm to 15 mm | 15-22 | ~120 |
Up to 22 mm | 22-30 | ~150 |
As nitrogen requires higher pressure for working, this can significantly increase the cutting speed. Sometimes the pressure drops due to continuous use as liquid nitrogen’s conversion to vapors in the tank can’t keep up.
So an external “Nitrogen Vaporizer” is used, which speeds the conversion. Remember, it doesn’t increase the pressure of nitrogen. Rather, it boosts the volume of nitrogen. This excess volume maintains high pressure and a steady flow rate.
You can use nitrogen gas for cutting stainless steel, brass, and aluminum. Not only does it prevents the reaction and burning of slag, but it also resists corrosion. Considering the gas is pure enough. Nitrogen’s purity criteria are high and close to 99.99%.
All the great things about nitrogen gas come at a price. It is the most expensive gas among all other options. As the thickness of the material increases, so is the cost of nitrogen gas usage. It usually lasts 10-15 times lower than other gases.
Nitrogen gas is unsuitable if your production mainly fabricates metal parts, as cutting costs combined with post-finishing will raise the overall cost. Only use it if high precision and edge quality is required.
Oxygen
Oxygen assist gas is also a good option for assisting gas in laser cutting for thicker materials, but one must be careful about its oxidation properties. Oxygen can react with the base metal. It’s an exothermic reaction that creates excess heat during the cut. It aids in cutting by burning the edges but to a certain extent before causing damage to the material.
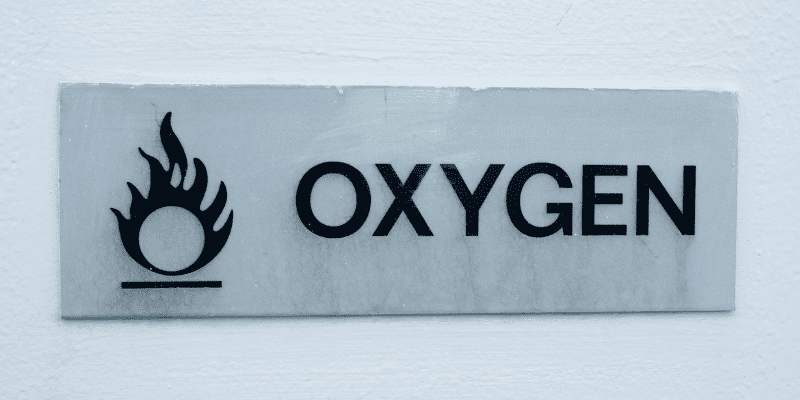
It’s suitable for reflective materials like carbon steel and mild steel. Due to oxidation, a layer is formed that increases the laser absorption rate, thus helping in the cutting process. It’s also suited for thinner workpieces.
On the downside, the same oxidizing film attached to the workpiece can hinder the post-processing. Welding the part afterward becomes a problem, creating welding defects in the workpiece.
Oxygen works slightly differently than nitrogen. It supports the combustion (similar to plasma cutting) of molten edges and blows of the slag. The cutting happens partially due to the said oxidation.
The purity requirement for oxygen is 99.97%, which is vital in cutting. The higher the purity is, the greater the combustion, which aids in cutting.
However, increasing the purity raises the cost of the oxygen cylinder significantly. Therefore, experts recommend only increasing the quality when very thin sheet metals (prone to damage) are involved.
This limits the cutting power as increasing it might cause excessing burning of the cutting edge. Because of this, poor cut quality is achieved.
Moreover, the pressure and flow rate of this gas is lower. This eventually saves a lot on the operational cost. Making it a much cheaper option than nitrogen gas.
Oxygen Gas Settings | ||
Material Thickness | Pressure (Bars) | Volume (m3/hr) |
Less than 8 mm | 3 and above | ~20 |
Up to 22 mm | 10 | ~22 |
Compressed Air
Compressed air is simple and convenient to use for fiber laser cutting. It’s also the cheapest and mostly used for thinner sheets, although exceptions are always there. Typically, galvanized steel, brass, and aluminum are cut using it.
Even though it’s the cheapest, you must consider some factors before purchasing the system. Unlike oxygen and nitrogen gas, you must invest in compressors and filters first. This initial investment can easily pay off if consistent production is needed for the long term.
The cuts made by compressed air are, at best, average. It’s due to the fact the air contains 75% nitrogen and 25% oxygen (volume %) which can oxidize the material resulting in poor cuts.
However, it can also help in the cutting process by introducing oxygen’s over-burning effect and the high cutting speed of nitrogen. So in a sense, it gets the best of both worlds. However, you’ll also notice a slight yellowish hue on the cuts due to oxygen.
If there is large post-processing, then compressed air is not recommended. Other than that, it’s cost-effective. Many small businesses prefer compressed air as it’s readily available.
Even though it’s the most cost-effective, there is still some major issue concerning this gas. The air contains moisture and oil droplets from compressors. This contaminates the air, damaging the protective lens or, worst cases, the laser head. To prevent it, extreme caution is required, and there should be no compromise on the filtration process.
Argon
Argon is the rarest of all gasses and is seldom used in fiber laser cutting. This gas has higher specific heat, which means it can absorb the heat from laser cutting. This can lead to localized quenching that rapid cooling at an incision area which can be detrimental to the material. Therefore, it’s only used as an alternative for metals that can react with nitrogen.
Cost Of Different Gases for Laser Cutting
Nitrogen
Nitrogen costs the most when it comes to an assist gas. The price varies from country to country, but here are some rough estimates. A typical nitrogen supply costs $2.5 (in the US), lasting for 20 to 60 minutes, depending on the job. You must negotiate with the vendor and see what offers you can get. Make sure you know how much cubic meter of gas flow you require for the job before deciding the rates.
Many large industries prefer nitrogen generators to refill gas cylinders. It’s a one-time investment but pays off in the long run.
Oxygen
In thinner material, nitrogen is best suited and most economical. Nitrogen is seven times faster in cutting pieces when thicknesses up to ⅛ in. But the cost of nitrogen would rise exponentially without any increase in speed.
For greater thicknesses, oxygen is feasible, and the job costs roughly $1 per hour. However, we have not included the cost of deburring and finishing.
Compressed Air
Air is the most cost-effective solution and contains oxygen and nitrogen by some percentage. Air is readily available, so the cost is electricity used to run the plumbing system.
Compressed air requires an initial investment in a piston compressor or screw compressor.
You will also need air dryers, dust, and oil filters with this setup. Compressed air with the least impurities like water and oil droplets will yield better quality cuts.
How To Choose the Right Assist Gas for Your Needs?
You must consider these factors before setting up your laser cutting system. Even a slight miscalculation regarding the assist gas can cause a big loss on your project.
Material Choice
The type of material you will work on is the most crucial aspect of selecting an assist gas. For stainless steel and aluminum, nitrogen works best. But oxygen is better for reflective and oxidizable materials like mild steel, carbon steel, and galvanized steel.
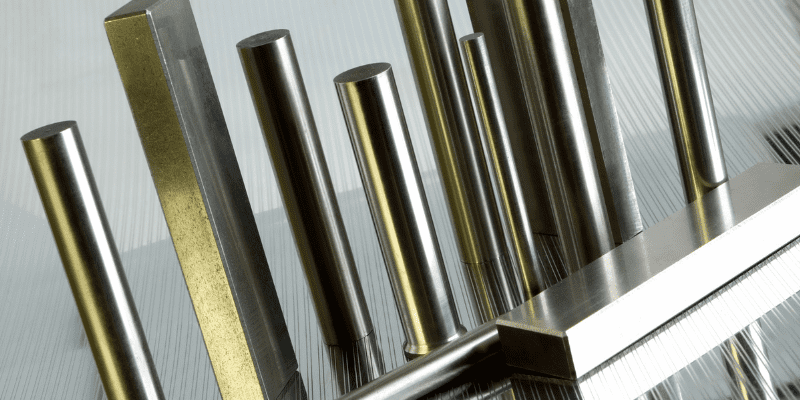
Compressed air is also suited for steel, aluminum, and brass, but the quality is reduced. Also, keep in mind the finishing cost when using air.
Thickness
To understand how thickness plays a vital role in the laser cutting process, you must understand the basic principle. Nitrogen is an inert gas and doesn’t aid in cutting but prevents the laser beams from debris and dust. It also cools down the cut area and reduces heat affected zone.
However, this can only be achieved for thinner materials that require less laser power. As the thickness increases, the quality of the cut using nitrogen decreases.
On the contrary, oxygen aids in cutting by burning the material. Hence, it increases the laser’s cutting capacity, resulting in thicker material processing.
Finish Quality
Nitrogen, by far, produces the highest quality cuts in thinner materials. If the job doesn’t require post-processing, then nitrogen cutting is profitable.
Oxygen also produces good-quality cuts but leaves a black layer of oxidization at the cut area. This may require some post-processing work.
You can use compressed air for jobs that are done for fabrication purposes only. The cuts are low quality but, at the same time, cheap.
Cost
The laser cutting cost depends on the material, thickness, assist gas, and machine power. Thickness is also relative. For example, a 1500 W laser cutting machine may struggle to cut an 8 mm job compared to a 3000 W machine using the same volume of assist gas.
So a proper cost analysis of auxiliary gas is required before starting a commercial project. However, besides “Assist gas,” there is no crucial operational cost of a laser cutting machine.
Quick Overview
Gases |
Nitrogen |
Oxygen |
Compressed Air |
Material |
Stainless Steel, Aluminum, Brass |
Galvanized Steel, Carbon steel, Mild Steel. |
Steel, Aluminum Brass |
Thickness (Preferred) |
3 mm (⅛ in) |
8 to 22 mm |
1 to 22 mm |
Gas Purity Requirement |
Moderate |
Crucial |
Moderate |
Pressure |
High |
Low |
Low |
Flow rate |
High |
Moderate |
Moderate |
Extra Equipment |
Nitrogen Vaporizer |
None |
Dryers, filters, compressors |
Finish Quality |
Best |
Moderate / High |
Moderate |
Cost Per Hour |
High |
Moderate |
Low |
Tips For Reducing Gas Costs in Your Laser Cutting Operation
Optimizing Gas Supply
Laser machines require consistent pressure and flow rates of assist gases to maintain the quality of the cuts. Moreover, faults in the gas supply may lead to unnecessary pressure drops affecting the quality of the production.
Pipe length and diameter determine the flow capacity of the assist gas. Optimally the gas supply line should have minimum amounts of bents. Make sure regular maintenance is done to avoid unnecessary costs.
Gas Purity
Oxygen purity plays a significant role in the machine’s cutting capacity. Experts say that even the drop in purity from 99.97% to 99.95% can affect the process adversely.
In the case of compressed air, if poorly filtered can destroy the laser lens. To reduce costs be mindful of the purity of the gas.
Nitrogen purity is essential, but it doesn’t affect the quality of the laser. The laser is still effective but is more prone to outside factors that can adversely affect the cost.
Not using the proper impurity will result in a poor cut which means a loss of money. Better quality equals reduced costs.
Gas Tanks and Regulators
Assist gases for laser cutting are supplied in different sizes of containers. Therefore, evaluating which type of supply suits best is necessary to reduce the cost.
For small businesses, gas cylinders with periodic refilling are best. Large production houses should opt for gas tanks or their gas generation equipment. This will save the cost of logistics.
Regulators, hoses, and valves must be regularly maintained to avoid leakages. Also, ensure the cylinders are top-quality, as they can pollute the gas.
Machine Settings
This is real-time monitoring of the laser cutting machine. You must select the right gas according to the job if you use multiple gas systems.
Secondly, pressure is selected according to the working thickness, material, and shape. Be sure to get the units right, as they can be confusing. The right settings will prevent the wastage of gas and hence reduce the overall cost.
There are many parameters to look out for in machine settings. One such is the “Nozzle Size” in the laser head.
Generally, a larger nozzle means greater flow rates of assist gas. This can increase the cutting speed. However, this can make the cutting cost expensive. So optimize it to reduce the cost while maintaining the operations.
Conclusion
After going through each assist gas’s benefits, capabilities, and characteristics, you can easily choose the right gas for your laser cutting process.
Nitrogen is the best assist gas for fine-quality laser cutting of stainless steel. On the contrary, oxygen gas best suits reflective and oxidizable materials like carbon steel.
Air can work on steel, aluminum, and brass, but edge quality is poor, which can be compensated by low operational costs.
Remember to do a detailed analysis before making any decision because it’s a recurring cost that can make or break your project.
Even if the job only costs you ten cents per cubic meter more than the market, the price will eventually soar and cause big losses.
Baison Laser Provides Best Fiber Laser Solutions
Buying an efficient, durable, and high-quality laser-cutting machine affects long-term profits. Our laser machines can provide you with premium quality that guarantees success.
Baison Laser makes machines using a high-tech facility run by expert engineers and technicians.
Our catalog includes heavy-duty laser cutting, welding, marking, and cleaning machines at competitive market rates.
If you are not sure about the specifications of the machine, you can always try out our free application evaluation. We are serving clients all over the world and have established a relationship of trust.
But that’s not all. Our experts are available for call 24/7 to give you customized guidance. So what are you waiting for? Contact us NOW!
