Bending stainless steel sheets is a must in the metal fabrication and metal manufacturing industry. This process helps create parts with specific shapes and functions. To get the results you want, you need to know the basics of sheet metal bending. The job involves using different machines and tools to shape metal as required.
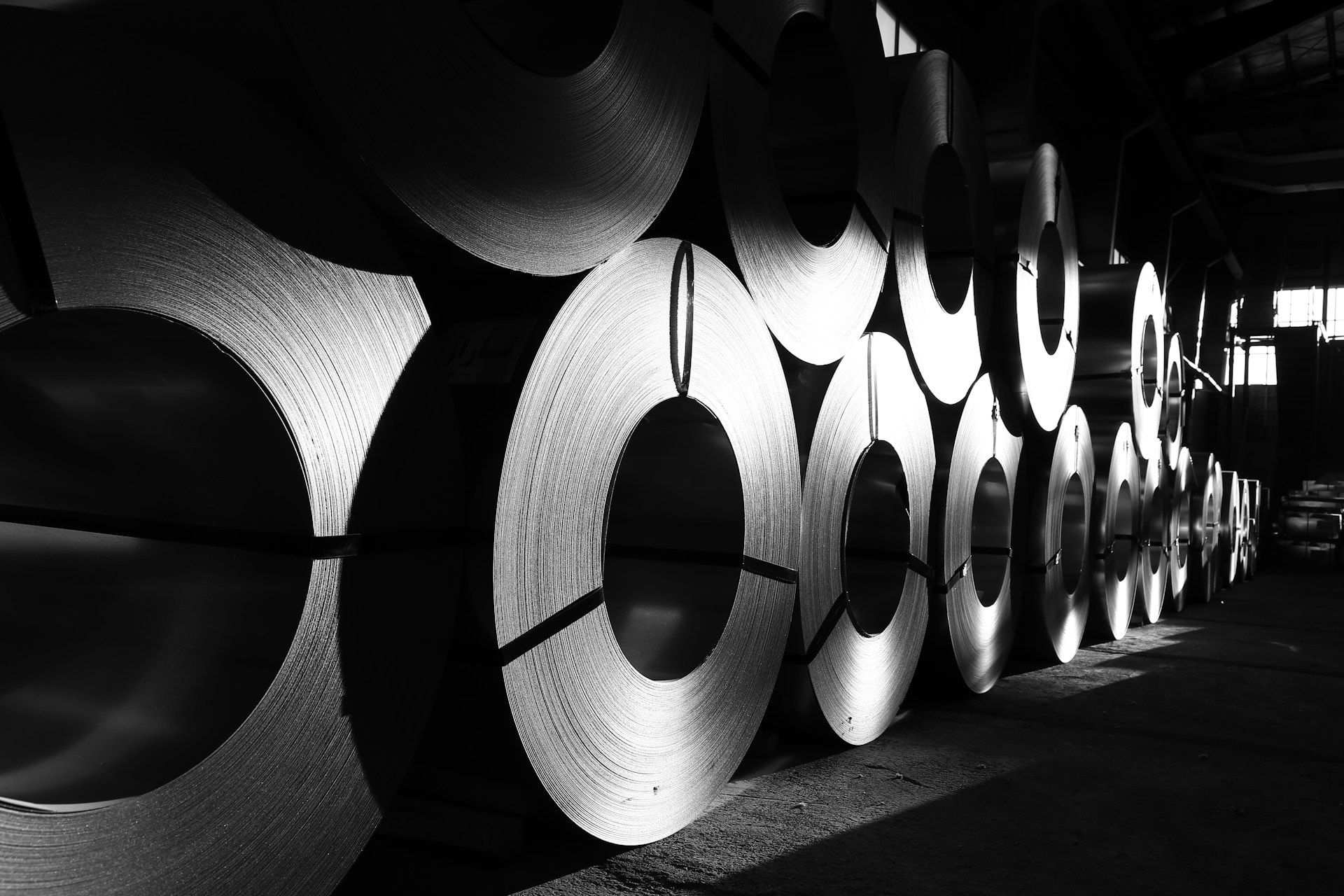
Many industries rely on this method, including car makers, aerospace firms, and construction companies. To make your bending work successful, you should plan your project, pick the right tools and gear, and learn about various bending methods.
This guide will show you the popular sheet metal bending techniques step by step. We’ll cover different bending methods, fabrication processes, mechanical properties, and other necessary details. This way, you can make high-quality bends that are both accurate and efficient.
Understanding Sheet Metal Bending
Bending sheet metal is a process that shapes metal sheets into specific forms with machines and tools. The aim is to alter the metal’s shape without removing any material. Manufacturers often use press brakes, folding machines, and other bending equipment for this task. To bend the sheet metal, huge force is applied to press it into the desired shape.
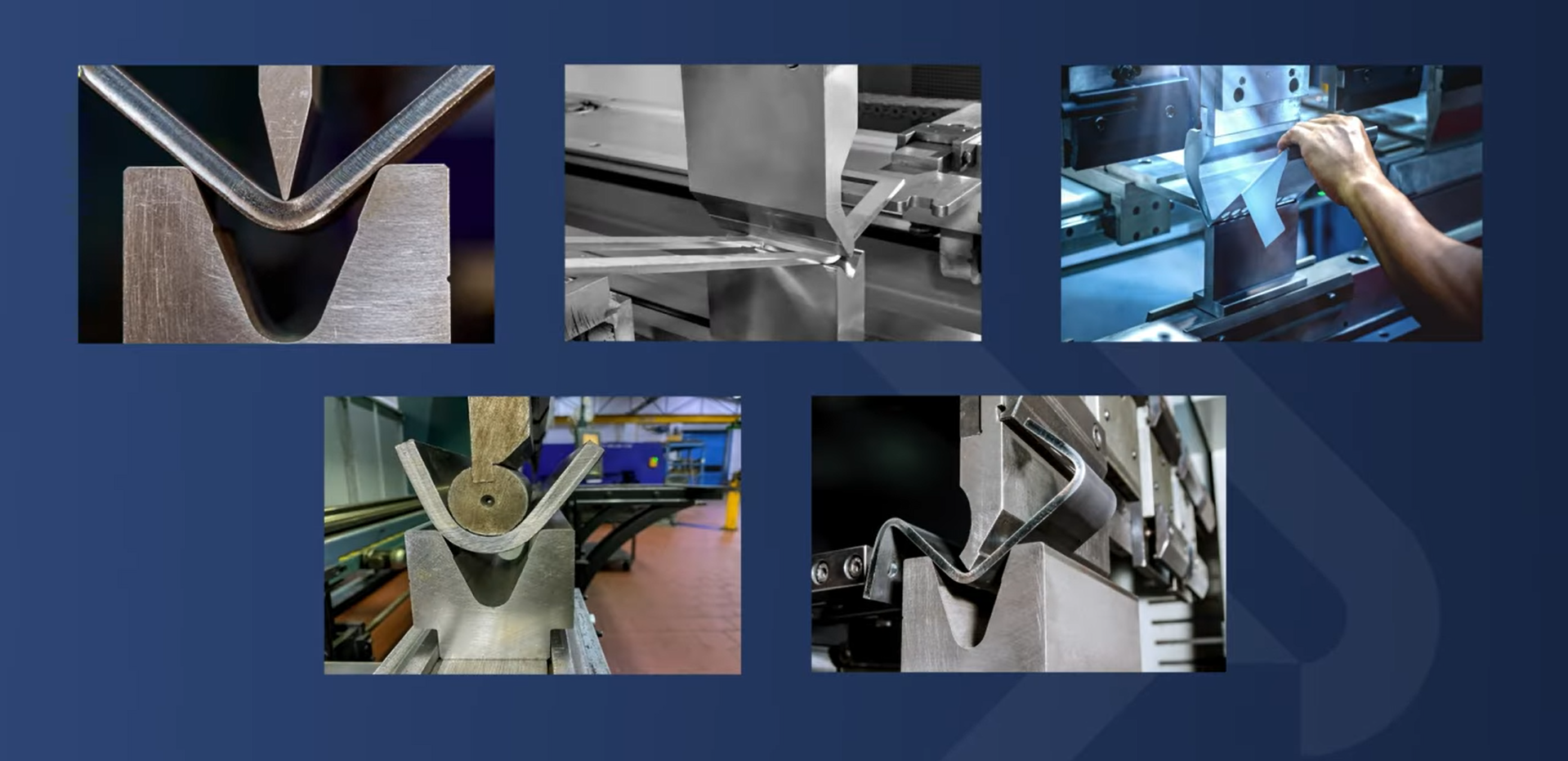
Tools and Equipment
Punches and dies are the main tools used to bend sheet metal. The punch exerts force to press the metal into the die, creating the needed bend. Choosing the right punch and die depends on how thick the material is and what angle of bend you want. Each tool is made to produce specific bending effects, so it’s essential to pick the right mix for the job.
Learn about 6 types of bending machines.
Types of Bends
Depending on the sheet thickness and type (carbon steel, mild steel, low carbon steel), you can determine the perfect bending method. The ease of bending steel plates also depends on whether you need a sharp bend radius, multiple bends, tight bends, final angle, dimensional accuracy, etc.
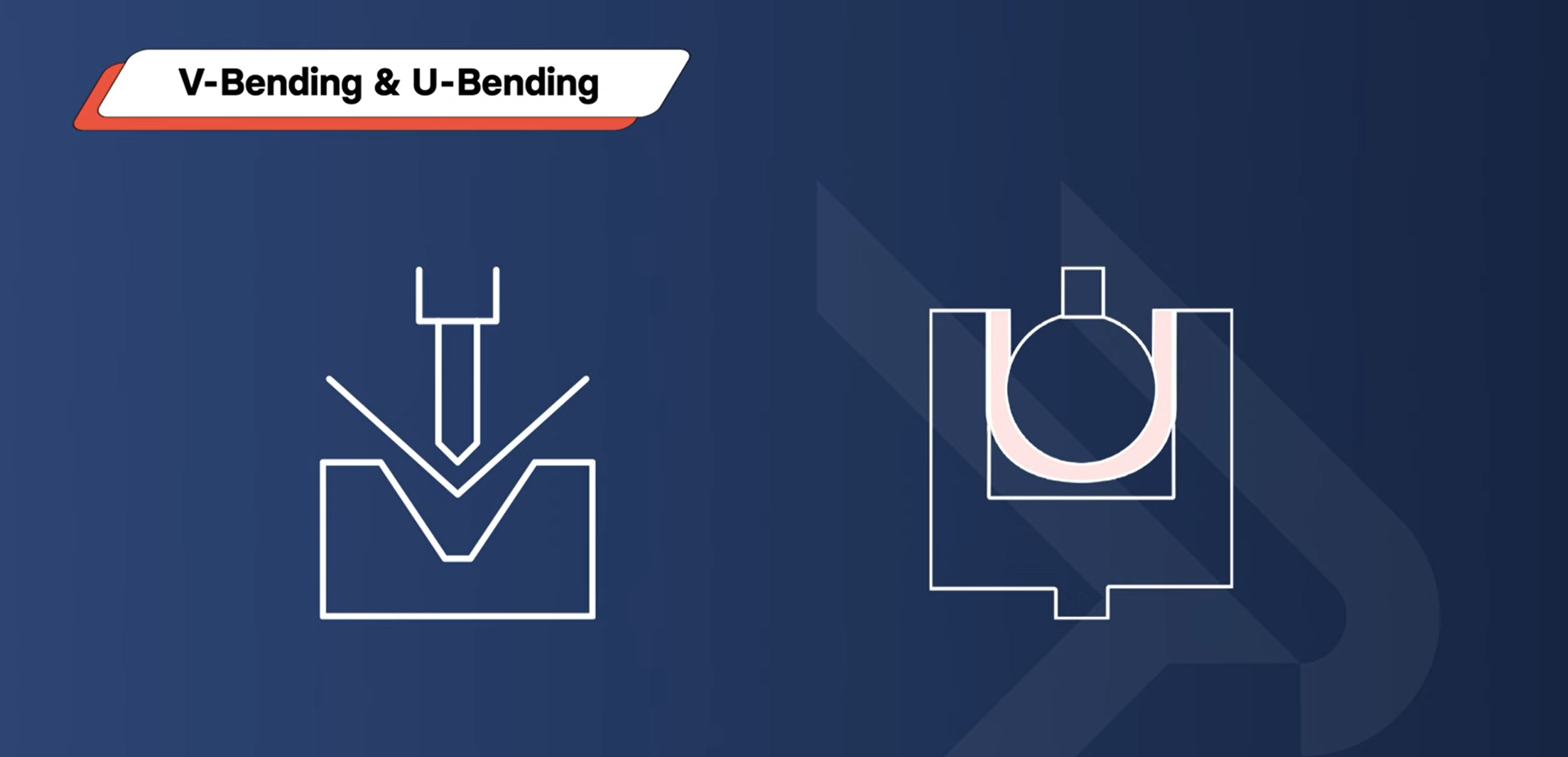
Metal fabrication uses several kinds of bends. V Bending method is the most common type. It involves pressing metal into a V-shaped die to create a specific angle. Edge Bending means bending the sheet’s edge around a radius. U-Bending forms a U-shape by pressing the metal into a U-shaped die. The design needs determine which type of bend to use.
There are also many popular bending methods such as bottoming, coining, rotary bending, and air bending method.
Material Considerations
Different materials have unique bending qualities. These qualities have an impact on the bending process and end result. Things like how thick the material is how it stretches, and how strong it is play a big role. These traits shape how the metal will bend and how much force you need to use. To get precise and steady results, you need to understand these material features.
Bend Allowance and Bend Deduction
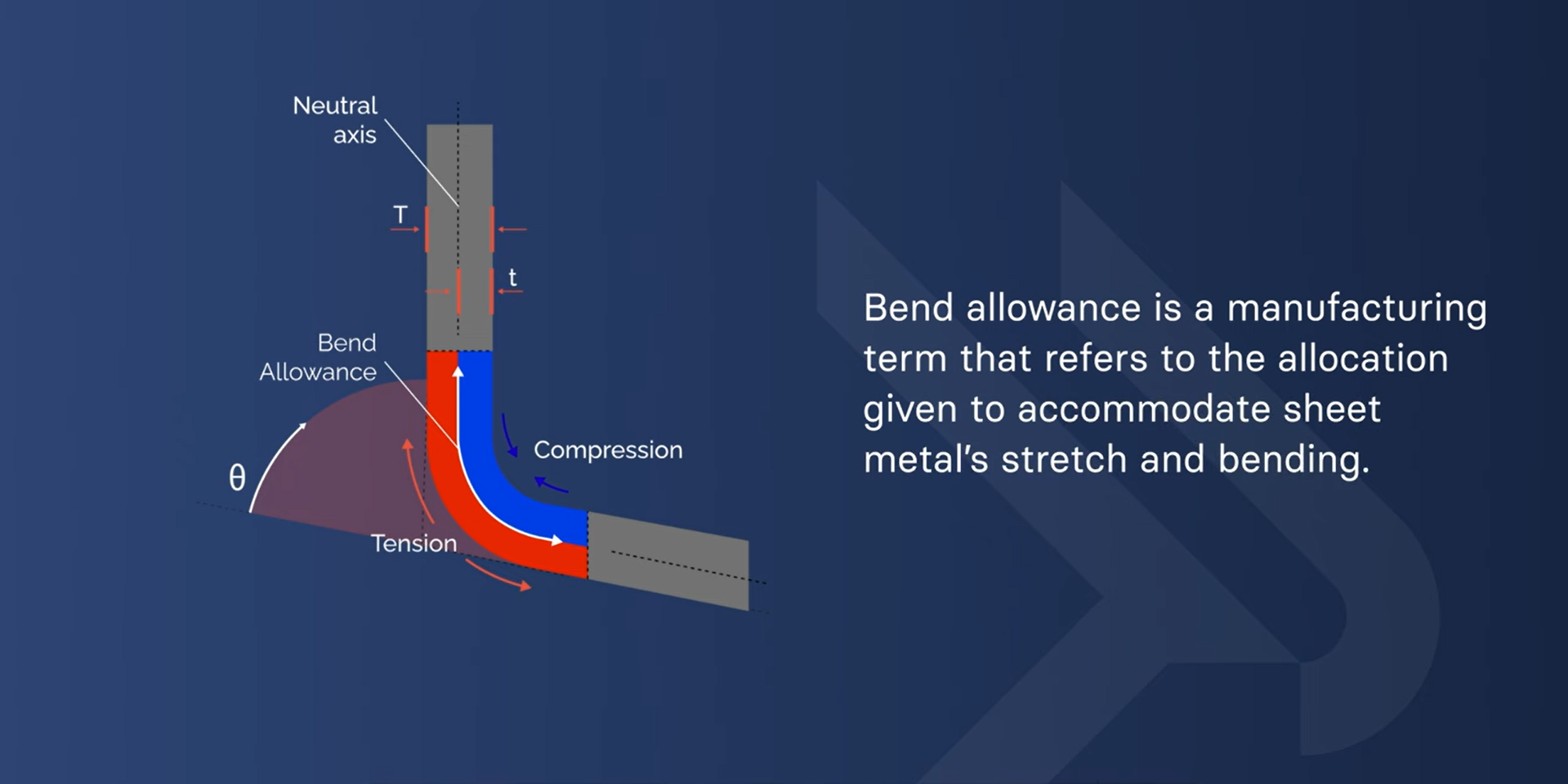
When bending sheet metal, you need to figure out the bend allowance and bend deduction. Bend allowance means how long the neutral axis of the bend is, which takes into account how much the material stretches. Bend deduction is the difference between how long the sheet is when it’s flat and how long it ends up after you bend it. These calculations help make sure the bent part ends up the right size.
Springback
Springback happens when metal tries to bounce back a bit to how it was before bending, thanks to its stretchiness. You need to think about this when you’re bending metal if you want to get the angles and sizes just right. Making sure you account for spring back is key to making bent parts that are spot-on and dependable.
Preparing for the Bending Process
Begin with making thorough sketches of the components you need to bend. Add measurements, bend angles, and allow variations. Work out the order of bends to stop clashes and get things right. Figure out the bend allowance and subtraction to account for the material stretching and squeezing.
Be Familiar with Your Materials
Get to know your materials’ features, like how much they can stretch when they start to give, and how far they can stretch. Find out how thick the material is, as thicker stuff needs more power and different tools. Think about which way the grain runs because bending along it might cause cracks. It’s better to bend across the grain.
Pick the Right Tools and Gear
Pick a press brake that has the right tonnage and bed length for your material and how long your bends need to be. Select the right punch and die set. When you’re air bending, make the die opening about 8 times as wide as your material is thick. Use back gauges to make sure your bends are in the same spot every time.
Extra Tips
Try out your bending on some scrap material to fine-tune what you’re doing. Always stick to safety rules to keep yourself and your tools safe.
Choosing the Right Tool to Bend Stainless Steel Sheet
Press Brake
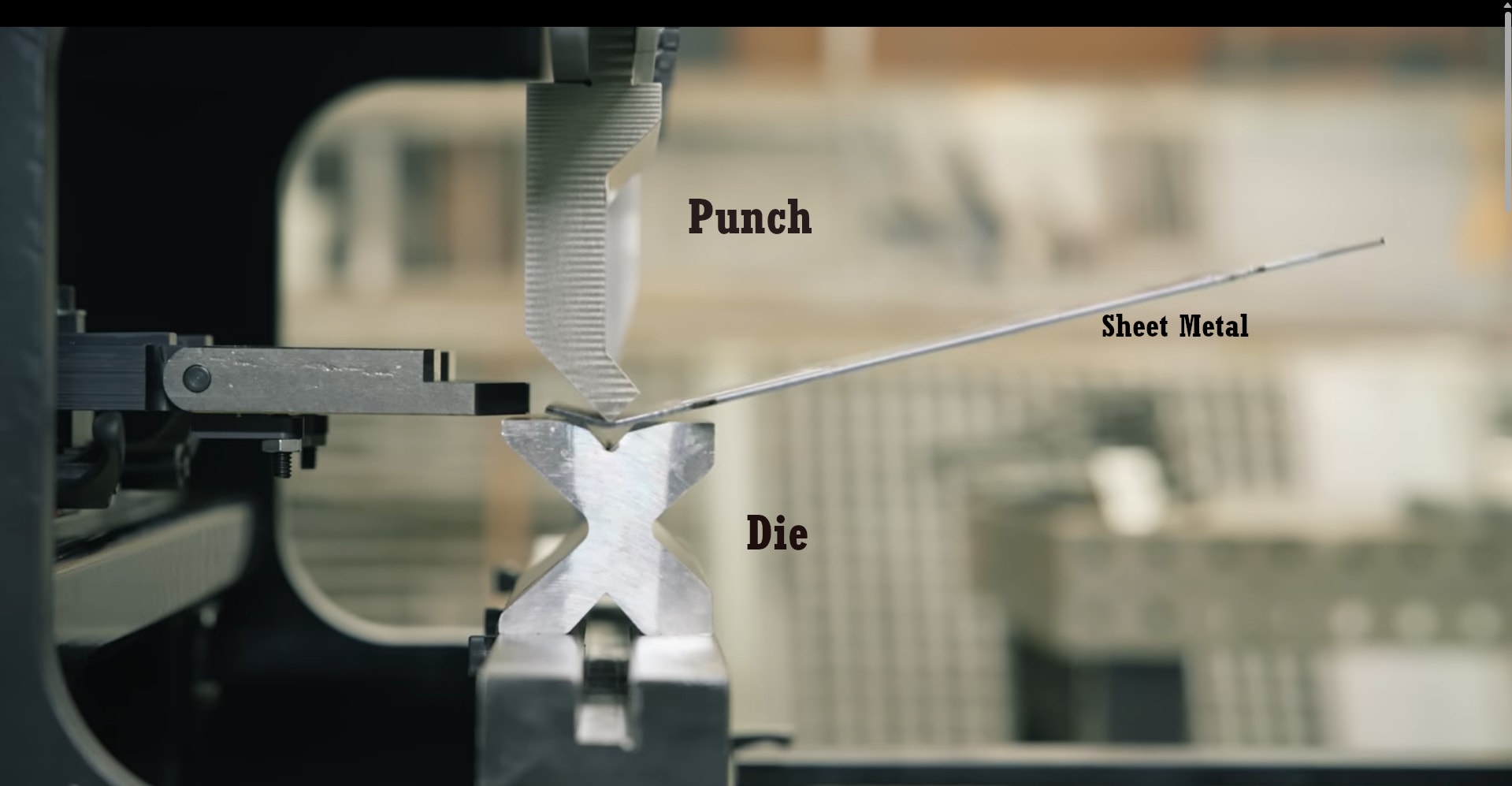
You’ve got a few choices when picking a press brake: hydraulic, pneumatic, mechanical, and electric. Hydraulic press brakes offer flexibility and strength. They handle many materials and thicknesses well. Pick a press brake with enough tonnage for your material’s thickness and length. Thicker and harder materials need more tonnage. Also, check that the press brake’s bed length matches the length of the material you want to bend.
Punching Machine
Punching machines make holes or shapes in sheet metal before bending. Pick punches and dies that fit the hole size and shape you need. Check that they work with the type and thickness of material you’re using.
Ironworkers
Ironworkers do multiple jobs, like punching, shearing, and bending metal. They help with many tasks in sheet metal fabrication. Please choose the right tools for each job and make sure they suit the material’s properties.
Tooling Section
Different metals like aluminium, steel, and stainless steel need their own special tools. Pick your tools based on the metal you’re working with. When you’re dealing with thicker stuff, you’ll need tougher tools and more force. The angle you want to bend also plays a part in choosing the right punch and die. Different ways of bending, such as air bending, bottom bending, and coining, all need their own setups.
Power System and Hydraulic Pressure
Hydraulic press brakes apply force through hydraulic pressure. Make sure you keep the hydraulic system in good shape and that it can deliver the pressure you need. Electric press brakes offer precision and save energy but might not match hydraulic systems in tonnage.
Additional Considerations
Back gauges help you make precise, repeatable bends. Check that your equipment has safety features like light curtains and emergency stops. To keep your machines and tools working well for a long time, you need to maintain them.
Bend Stainless Steel Sheet: Tools Comparison
Tool Type | Description | Key Features | Advantages | Disadvantages | Typical Applications |
---|
Bending Techniques for Stainless Steel Sheet
V-Bending
V-bending has used for many angles. It suits small and big production runs. This method needs exact tooling and setup to make accurate bends. V-bending works best to create simple bends and angles in stainless steel sheets.
U-Bending
U-bending helps to create U-shaped profiles. You can do this with normal press brake tooling. This method might need multiple steps or special tooling for deeper U-bends. People often use U-bending to make channels and frames.
Roll Bending
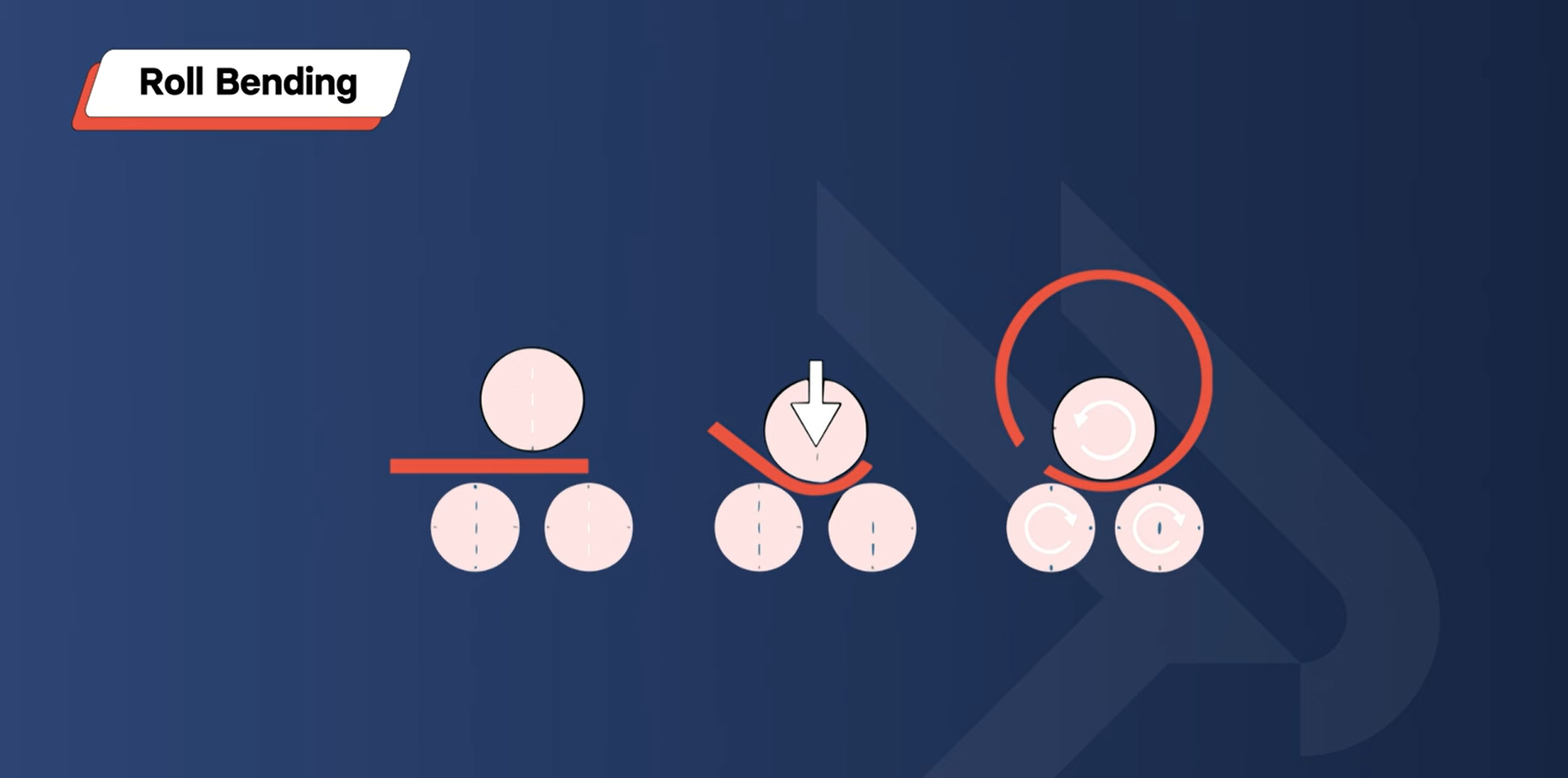
Roll bending excels at creating big-radius bends and cylinder shapes. Several cylindrical axes rotate and shape the sheet metal, mostly into cylinders. It fits long sheets and thicker materials. You’ll need roll bending machines, which can cost more and take up more room. This method often sees use to produce pipes, tubes, and large curved panels.
Air Bending
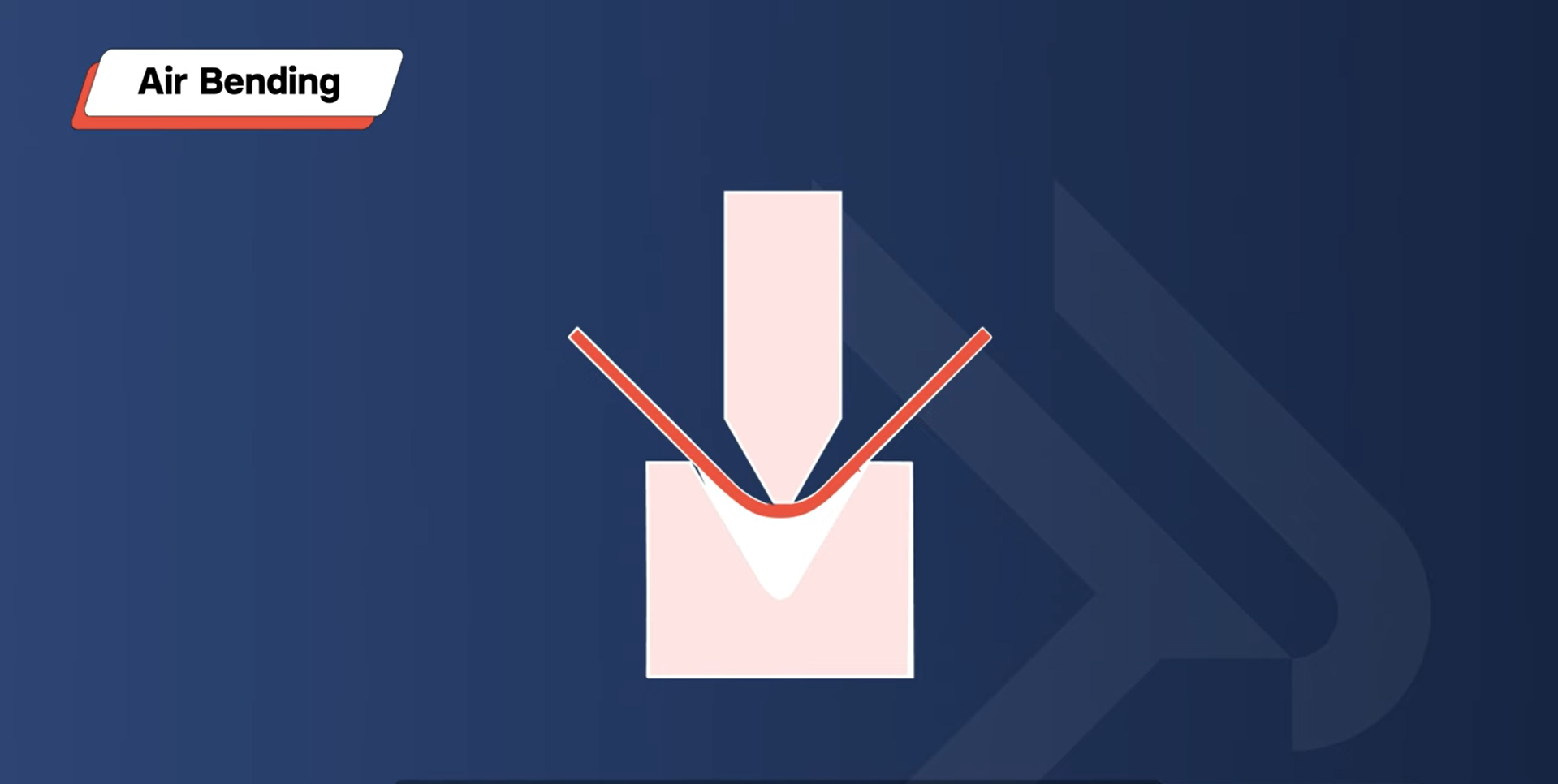
Air bending gives you more options and needs less power than bottom bending. You can make different angles using the same tools. But it’s not as exact as bottom bending, and the metal might spring back. Air bending works well to create many angles and tricky shapes in stainless steel sheets.
Key Considerations
When selecting a bending technique, determine the required bend angle to choose the appropriate method and tooling. Consider the minimum bend radius for stainless steel to avoid cracking or material failure. Calculate the bend allowance to account for material stretching and ensure accurate dimensions.
Design Considerations for Metal Sheet Bending
- Bend Radius: Make sure the bend radius matches or exceeds the material’s thickness. This will help you avoid cracks. Each material needs its own minimum bend radius. Stainless steel often requires a bigger radius because it’s stronger.
- Bend Length: Your press brake or bending machine should be able to handle the bend length. Keep the length the same to stop changes in the final product.
- Bend Distance: Leave enough space between bends to stop tools from getting in the way and to get accurate bends. Think about the order of bends to avoid crashes and to make handling easier.
- Hole to Edge Distance: Put holes at least two times the material’s thickness away from the bend. This stops the areas around the holes from changing shape. Make sure holes aren’t too close to where the bend will be to keep the structure strong.
- Springback: Keep in mind springback, which is how materials try to bounce back to their original shape after you bend them. To get the angle you want in the end, tweak the bend angle a bit. Each material springs back differently. For instance, stainless steel bounces back more than aluminum does.
- Processing Tolerances: Specify tolerances that match the capabilities of your bending process. Always make sure that these tolerances are consistent across all parts to maintain uniform assembly.
- Material Properties: Understand the tensile strength of your material. Higher tensile strength requires more force to bend and may need specialised tooling. More ductile materials can handle greater deformation without cracking.
Safety Precautions and Best Practices
Safety comes first when you’re working with sheet metal. Here’s a detailed look at how to stay safe and follow best practices:
1. Protective Gear
Put on cut-resistant gloves to guard your hands from sharp edges. Wear safety glasses or goggles to protect your eyes from flying bits and metal shavings. If you’re in a loud place, use earplugs or earmuffs to save your hearing. Cover up with long sleeves and pants made of tough fabric to shield your skin from cuts and burns.
2. Work Area Setup
Make sure you have good airflow to avoid breathing in fumes when you weld or cut metal. Good lighting plays a key role in precision and safety. Light up your work area well to steer clear of accidents. Keep your workspace tidy and free of mess to stop trips and other dangers.
3. Lifting and Handling Techniques
To lift heavy materials, rely on your legs instead of your back. Bend at the knees while keeping your back straight. Ask a coworker to help you with large or heavy sheets to prevent strain and injury. Handle sharp or hot materials using suitable tools such as clamps and tongs.
4. Machine Safety
Make sure you get proper training on how to use all machines and tools. Check and fix equipment often to keep it working well. Learn where emergency stop buttons are on all machines and how to use them.
5. General Best Practices
Keep your mind on what you’re doing and don’t let things distract you. Follow all safety rules that apply to your workplace. Tell your boss right away if you see anything unsafe or if the equipment isn’t working right.
Calculating Bend Allowance for Sheet Metal
You’re right! Calculating the bend allowance for sheet metal is crucial for accurate fabrication. Here’s a breakdown of the formula you mentioned:
Bend Allowance (BA) Formula:
BA=(π/180) x B x (IR+K x MT)
Where:
- ( BA ) = Bend Allowance
- ( B ) = Bending Angle (in degrees)
- ( IR ) = Inner Radius of the bend
- ( K ) = K-Factor (a constant that represents the location of the neutral axis)
- ( MT ) = Material Thickness
Steps to Calculate Bend Allowance:
- Determine the Bending Angle (B): Measure the angle to which the sheet metal will be bent.
- Measure the Inner Radius (IR): This is the radius of the inside curve of the bend.
- Find the K-Factor (K): This factor depends on the material and the bending process. It typically ranges from 0.3 to 0.5 for most materials.
- Measure the Material Thickness (MT): This is the thickness of the sheet metal.
Example Calculation:
Let’s say you have a sheet metal with the following properties:
- Bending Angle (B) = 90°
- Inner Radius (IR) = 5 mm
- K-Factor (K) = 0.3
- Material Thickness (MT) = 2 mm
Plugging these values into the formula:
BA = (π/180) x 90 x (5+0.3 x 2)
BA =1.5708×(5+0.6)
BA =1.5708×5.6
BA ≈8.8 mm
So, the bend allowance would be approximately 8.8 mm.
Bending Stainless Steel Sheet with a Press Brake
Bending stainless steel sheets with a press brake needs close attention to some main factors to get good results.
To start, you must work out the right amount of force, or tonnage, since stainless steel is tougher and harder to bend than other metals. A formula can help you figure this out:

The material factor for SS sits around 1.6.
After that, picking the right tooling and die matters a lot. The width of the V-die should be about 8 times as wide as the sheet is thick. So, for a sheet 1 mm thick, you’d use a die with an 8 mm opening.
You can bend metal in different ways, like air bending bottom bending, and coining. Air bending is the most common way. It lets you change the angle more because the punch doesn’t push the sheet all the way into the die.
Stainless steel has special qualities such as work-hardening. This means it becomes tougher as you handle it more. This can make bending harder, so it’s crucial to know the material well.
To wrap up, using a CNC-controlled press brake can boost accuracy and make it simpler to do bends over and over with precision when dealing with more intricate shapes.
Edge Bending and Hemming Techniques
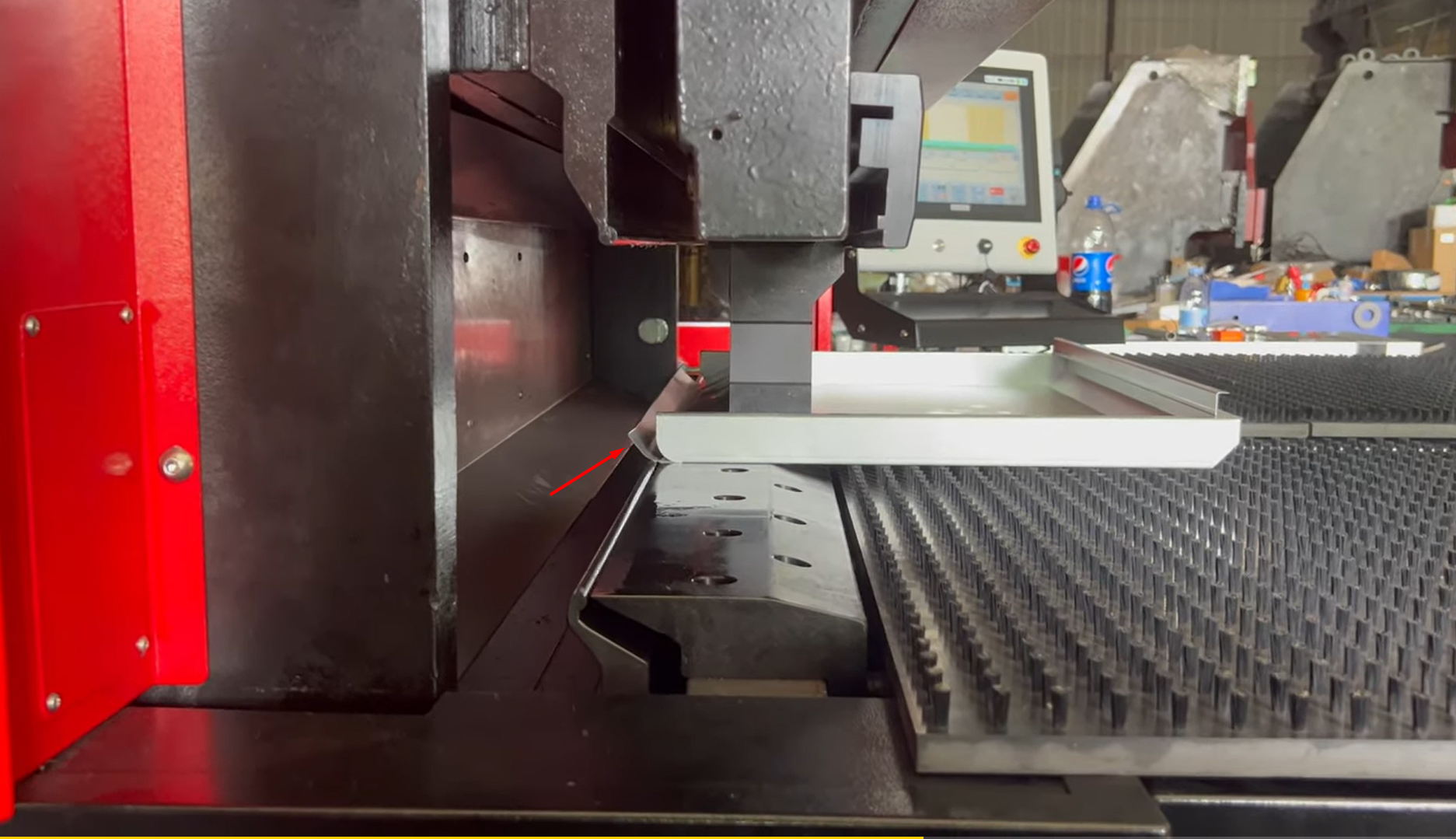
Edge bending helps shape the edges of metal sheets. You put the metal sheet in a press brake or bending machine. A punch then applies pressure to bend the edge to the needed angle. People often use this technique to make flanges and seams in metalworking.
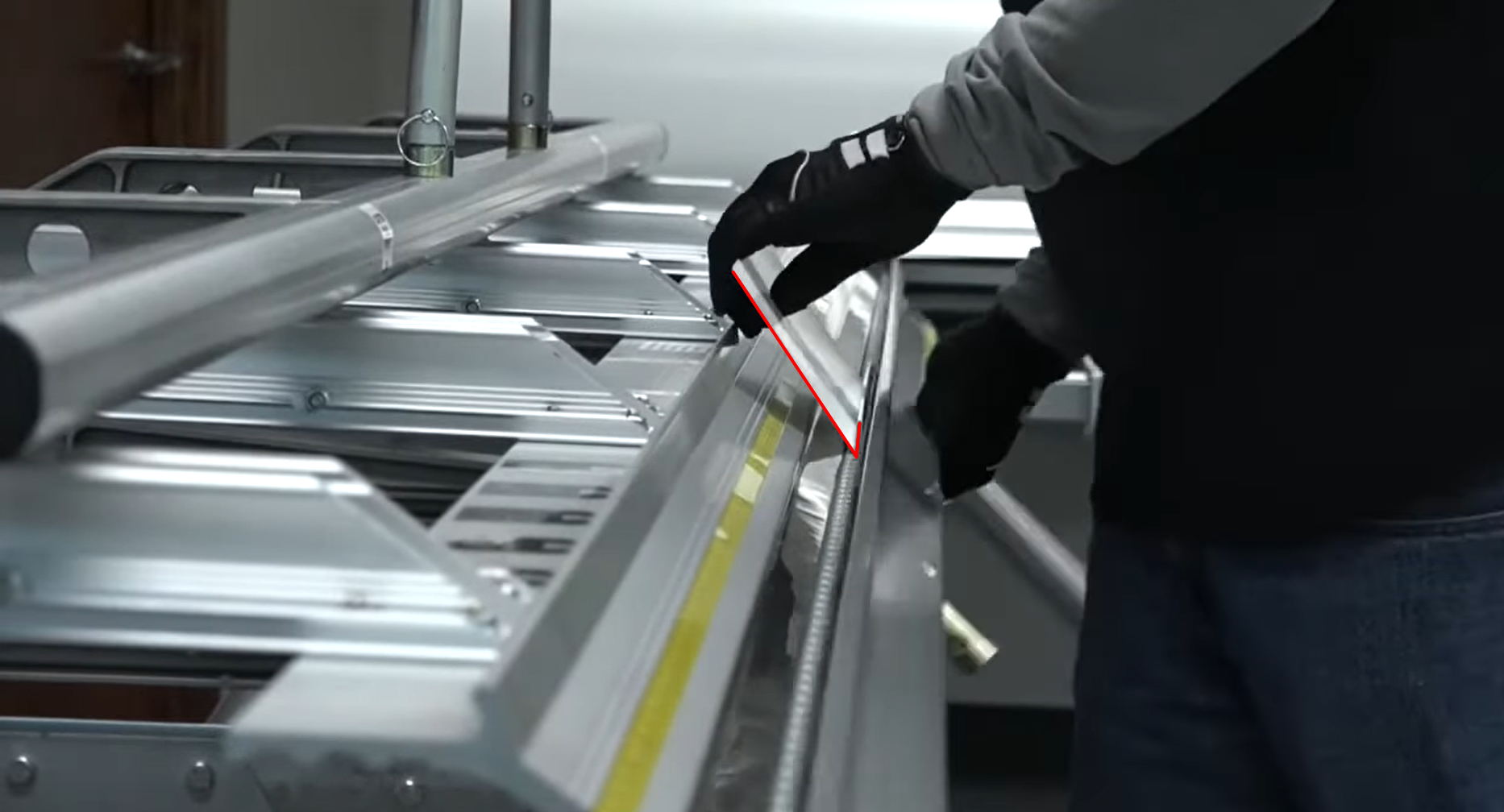
Hemming folds the edge of a metal sheet over itself. This creates a smooth, rounded edge. You start by bending the sheet to a right angle. Then, you fold it over to form the hem. You can do this in one step or several. Car and appliance makers often use hemming. It gives metal parts safe finished edges and makes them stronger.
Conclusion
If you’re planning to bend a stainless steel sheet, you must maintain careful planning and execution. Understanding the basics of sheet metal bending and choosing the right tools and techniques is crucial for achieving the desired results. Consider the material properties, bending technique, and design considerations when bending stainless steel sheets.
For high-quality, custom laser-cut products tailored to your large machine needs, trust BaisonLaser. Whether you need precision bending, press brake services, or other custom solutions, BaisonLaser has the expertise and technology to deliver exceptional results. Contact BaisonLaser today to discuss your project and see how they can help you achieve your goals!
FAQ Section
What is sheet metal bending?
Sheet metal bending is a manufacturing process that deforms flat metal sheets into desired shapes with force. The process uses tools like punches and dies. Commonly, laser-cut sheet metals are bent using press brakes or benders.
What is the difference between air bending and bottom bending?
Air bending bends a metal without fully pressing it into the die. You’ll get more flexibility in angle adjustments, but there’ll be more springback. In contrast, bottom bending pushes the metal completely into the die. It generates precise angles with less spring back but requires different tooling for each angle change.
What is the minimum bend radius for stainless steel sheets?
The minimum bend radius for stainless steel sheets typically ranges from 1 to 2 times the material thickness, depending on the specific grade and temper of the stainless steel. For instance, a common guideline is to use a bend radius of at least 1.5 times the thickness for optimal results.
What is the importance of bend allowance in sheet metal bending?
Bend allowance accounts for material stretching during the bending process. Accurate calculation of bend allowance helps prevent issues like gaps or misalignments in assembled parts.
Can you heat stainless steel to bend it?
Yes, heating stainless steel can make it more malleable and easier to bend, especially for thicker materials. However, overheating steel can lead to changes in material properties or surface oxidation.