Creating perfect welds is a fantastic skill. However, many welders struggle to minimize distortion and create visually appealing welds. The backstep welding technique enables you to cope with this issue and achieve strong and smooth welds.
What is the Backstep Welding Technique?
Backstep welding, also known as skip welding, is a specialized technique that involves welding in the reverse direction of the joint’s progress.
Unlike regular welding, where a welder starts welding at one end and progresses to the other, backstep welding starts involves the deposition of each bead segment from the ending point and moves toward the starting point. According to the American Welding Society, backstep welding is a distortion-reducing method where you deposit the welds in opposite direction to the regular welding.
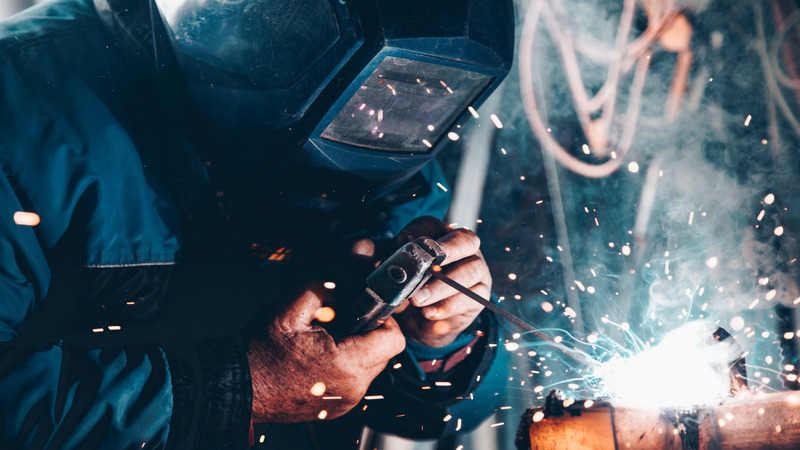
In backstep welding, welders divide the welding process into smaller bead segments. As you place each bead segment, the heated edges expand. It temporarily separates the plates that you are welding.
The plates return to their original position as the heat spreads across the plates. The plate expansion is more prominent when you place the first bead segment. The plates expand less as you move forward and lie successive beads due to the restricted separation of prior welds.
Benefits of the Backstep Welding Technique
The backstep welding technique offers the following advantages over traditional welding methods:
1. Reduced Distortion
One of the primary advantages of the backstep welding technique is its ability to reduce distortion in welded components significantly. Distortion occurs during the welding process due to the uneven heating and cooling cycle. It results in misalignment or structurally compromised weld joints, leading to potential quality issues and increased rework.
Backstep welding minimizes distortion by alternating the direction of welding. Instead of creating weld from start to end, it works backward, gradually reducing localized heating and cooling. It results in a more uniform distribution of heat and minimizes distortion.
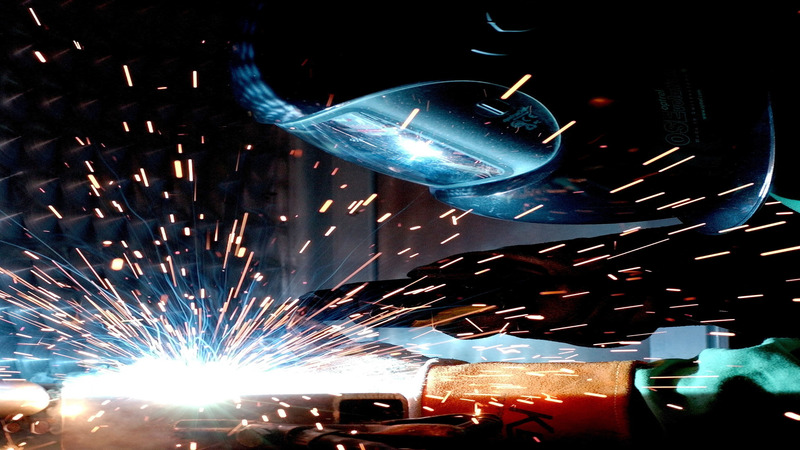
2. Controlled Shrinkage
Controlled shrinkage is another remarkable advantage of this technique. Welding involves the expansion and contraction of metal as it is heated and then cooled. This expansion and contraction can lead to undesirable distortions, cracks, and weakened welds if not managed. Back-step welding distortion control manages it by allowing uniform shrinkage of the metal.
By progressing backward from the endpoint of the weld, each weld bead counteracts the shrinkage of the previous one, resulting in a more even distribution of stresses and a reduced likelihood of material distortion.
This precise control over the shrinkage process ensures that the welded components maintain their intended dimensions, alignment, and structural integrity. This aspect is crucial in industries where precision engineering is paramount.
3. Improved Penetration
Backstep welding also improves the penetration of the weld. In traditional welding, achieving deep weld penetration can be a challenging task, especially when working with thick materials or complex joint configurations. However, backstep welding allows the deep penetration of weld in adjacent base metal. It creates a strong bond between the metals.
4. Minimized Residual Stresses
Residual stresses include various issues, like distortion, cracking, and reduced structural integrity. The backstep welding also minimizes residual stresses. According to Weldcor, the distribution of deposited weld metal prevents the accumulation of stress. It reduces the chances of weld failures and ensures great weld results.
Do You Have Any Questions?
Let Us Solve Your Problem
Cons of the Backstep Welding Technique
While there are many benefits to using the backstep welding technique, it also has some limitations. Here are some of the cons associated with this method:
1. Complexity
This welding method demands a higher level of skill and expertise from welders compared to other traditional techniques.
Welders carefully plan and execute each step in reverse order. It ensures that the following bead effectively prevents the shrinkage and distortion caused by the previous one. Beginner welders may find it perplexing to work on such a complicated technique. It can lead to poor weld quality and increased risks of failure.
2. Time-Consuming
Another significant drawback of backstep welding is its time-consuming nature. In this method, each weld pass builds upon the accurate formation of the previous one. It can significantly slow down the welding process. This time-consuming aspect significantly affects your project, especially when working on a larger scale.
3. Equipment Constraints
One notable drawback of the backstep welding technique is its equipment constraints. To effectively utilize this method, welders need specialized welding tools to help weld metals in reverse order. Many professional welding setups can be adapted for this technique. However, small businesses and workshops can’t afford such tools.
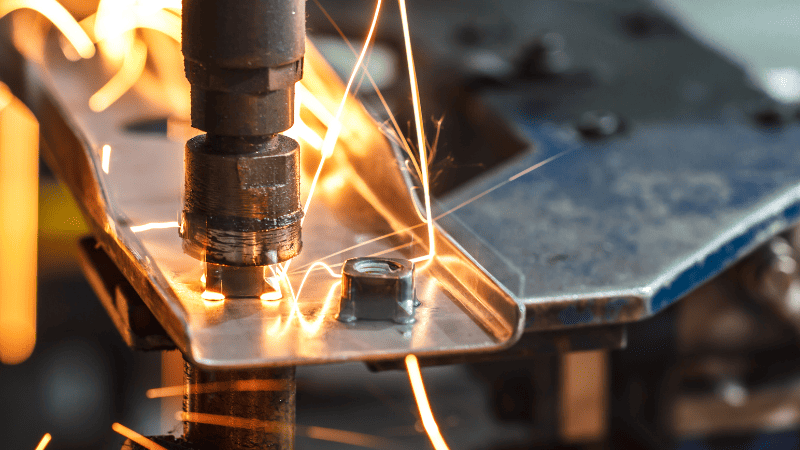
Back Step Welding Sequence and Process
Like intermittent welding, backstep welding is also a discontinuous welding process. The following is a step-by-step guide to the backstep welding process:
I. Cleaning
Like other welding techniques, backstep welding also requires thorough cleaning. Before welding, the surfaces of the metal pieces need to be free from debris, oil, rust, and any other contaminants that can affect the welding quality. Dirty metal surfaces or welding leads to poor weld quality. You get a weak bond, which can risk the weld joint’s structural integrity.
II. Preheating
Preheating the base metal is also required for the backstep welding process. You can use infrared lamps, torches, and ovens for this step. Preheating reduces the thermal shock and the chances of cracking. Moreover, preheating facilitates even heat distribution during welding, promoting better fusion and a smoother bead appearance.
According to the American Institute of Steel Construction, you can apply continuous heating during the welding process. Frequent heating also works well for the welding process. However, be careful, as excessive preheating can lead to issues such as grain growth and workpiece distortion.
III. Interpass Temperature Control
Interpass temperature control involves controlling the temperature between subsequent welding passes. It maintains the structural integrity of the weld joint. However, this control can be demanding, especially in thick materials or during prolonged welding sequences.
If the interpass temperature is allowed to drop too low, it can lead to rapid cooling and create stresses within the weld that may result in cracking. In contrast, excessive interpass temperatures can lead to problems such as over-tempering and softening of the material. It can affect the mechanical properties of the weld.
IV. Welding
Thin-sheet welding occurs in this step. Before starting the welding sequence, tack welds the metals. Now, begin welding by moving from one point to another. After completing the first segment, start welding backward along the joint. Keep welding in this pattern.
This step is challenging as you have to maintain a consistent travel speed and arc length. In addition, the backstep process may require frequent starts and stops, which can introduce discontinuities in the weld bead.
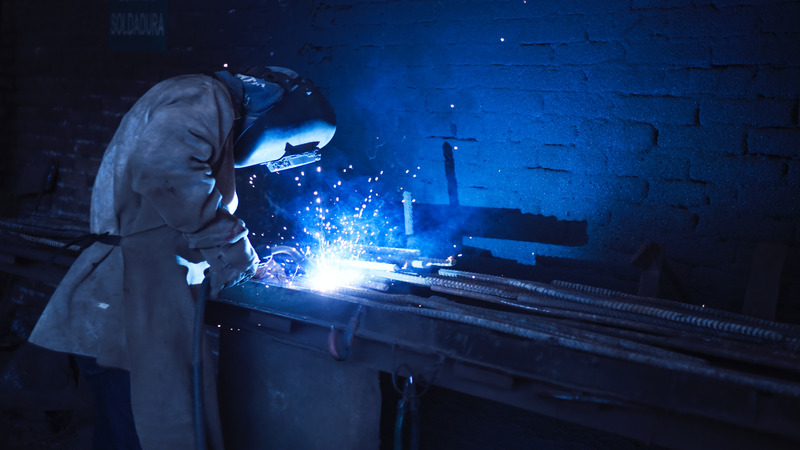
V. Cooling
After completing the welding, let the metals cool gradually. Avoid rapid cooling, as it can cause undesirable stresses and potential cracking. Too slow cooling is also challenging as it can affect the mechanical properties of the material.
Moreover, the cooling phase can also cause post-weld distortion. In post-weld distortion, metal wraps or bends due to uneven cooling. Carefully plan and monitor this step to prevent such issues.
VI. Post-Weld Heat Treatment
In some cases, post-weld heat treatment (PWHT) may be necessary for backstep welding to relieve residual stresses. It is also necessary for the improvement of the mechanical properties of the weld and to meet specific code or material requirements.
However, it requires additional time and cost, which can extend project timelines and increase expenses. Moreover, the high temperatures and thermal cycles associated with PWHT can potentially introduce challenges, such as the risk of distortion, cracking, or changes in material properties.
VII. Final Inspection
The final inspection ensures the quality and integrity of the weld joint. However, it can also be a time-consuming and resource-intensive aspect.
Comprehensive inspections involve a range of techniques, including visual examination, non-destructive testing (NDT), and destructive testing where necessary. These inspections are necessary to detect any defects or discontinuities in the weld. They ensure it meets the required standards and specifications.
Do You Have Any Questions?
Let Us Solve Your Problem
Applications of the Backstep Welding Technique
The backstep welding technique has found widespread use in various industries. However, you can’t use it for automatic welding. Here are some of the common applications of the backstep technique:
1. Aerospace Manufacturing
Aerospace is a complex field that requires durability and precision in every step and component. For assembling aircraft and spacecraft, extraordinary welding techniques are required to avoid any damage. The aerospace industry utilizes the backstep welding technique to ensure strong welds. By utilizing it, you can control distortion and improve the weld quality.
By welding the metal plates in the reverse direction of the joint’s progression, you can prevent materials from warping or weakening. Moreover, this technique allows you to secure confined spaces like the interior of engine components, ensuring the integrity of aerospace machinery. If you’re in search of a laser welder for aerospace welding purposes, fiber laser solutions by Baison Laser are highly recommended.
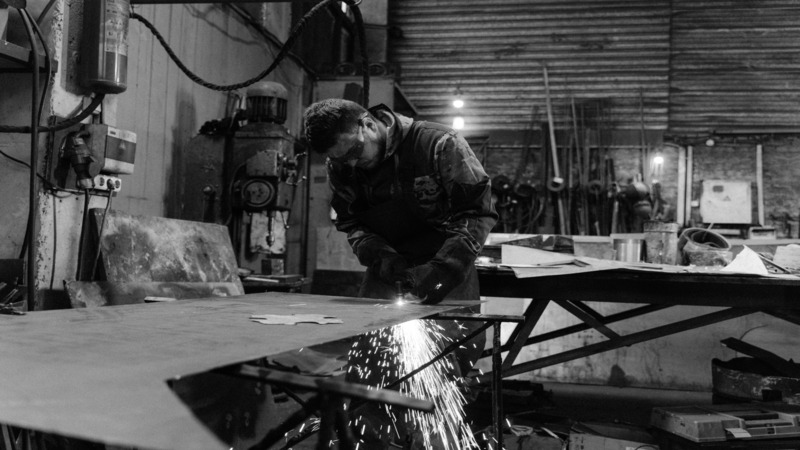
2. Automotive Industry
The automotive industry also needs long-lasting welds. The backstep technique ensures the durability of bodywork and frame construction. By precisely controlling heat input and reducing distortion, this approach minimizes the need for additional welding processes. It offers automotive better quality and cost-effectiveness in production.
3. Ornamental Metalwork
The backstep welding technique is also significant for manufacturing ornaments. Ornamental metalwork needs durability and attractive features. Various ornamental metalwork, such as gates and sculptures, employ this reverse welding process to create sleek welds.
Control distortion by managing heat input to create clean welds without affecting the aesthetic value of the final product. It ensures the aesthetic value of metal ornaments. This approach also offers design flexibility, allowing you to make intricate shapes and unique patterns with minimum distortion.
Tips for Effective Backstep Welding
The following tips can help you achieve the best results when using the backstep welding technique:
- Break the backstep welding into smaller segments. It enables you to maintain control and precision throughout the process. Smaller segments also help distribute heat evenly and reduce the risk of distortion or warping.
- Consistent heat input is critical for producing high-quality welds. Adjust your welding speed and angle to maintain a steady heat input throughout the process.
- Maintaining the correct torch angle is essential for successful backstep welding. An optimal torch angle of around 10 to 15 degrees from the vertical position is recommended for most welding applications. It allows the heat to penetrate the joint evenly, resulting in a strong and clean weld.
- Avoid adding too much filler metal at once, as it can lead to overlaps and irregularities in the weld bead. Instead, gradually add filler metal in small increments to maintain an even and consistent weld bead.
- Like any skill, you must practice backstep welding to refine your technique and achieve better results. Use scrap pieces of metal to test and improve your skills before working on important projects.
Do You Have Any Questions?
Let Us Solve Your Problem
Conclusion
Backstep welding is an efficient technique that makes your weld more reliable and aesthetically pleasing. It’s an intricate process that might take some practice to master, but the results are well worth it.
By following these tips and techniques, you can achieve high-quality backstep welds that will enhance the strength and appearance of your welded joints. With proper training and experience, you can use this technique to create strong and durable welds on various materials, from simple steel plates to complex structures.
Master Welding Technique With Baison Laser!
Having the right tool is as crucial as the right technique for welding. Thanks to Baison Laser, which provides a wide range of laser solutions to enhance your welding process. So, contact us today to learn more about our laser welding machines and get one for your welding projects.